Composites thermoplastiques :sur le point d'aller de l'avant
Les composites thermoplastiques (TPC) ne sont pas nouveaux dans le secteur aérospatial, mais au cours des deux dernières années, l'utilisation des thermoplastiques dans les avions commerciaux a atteint un point critique. Alors que les TPC sont utilisés depuis un certain temps pour des pièces plus petites telles que des clips et des supports, ou des composants intérieurs plus petits, les thermoplastiques ont progressivement fait leur chemin dans les structures d'avions plus grands et semblaient maintenant prêts à jouer un rôle plus important dans l'avenir des avions commerciaux.
En mars 2018, Toray Industries Inc. (Tokyo, Japon), le plus grand fabricant de fibre de carbone au monde, a acquis TenCate Advanced Composites (Morgan Hill, Californie, États-Unis et Nijverdal, Pays-Bas) pour 930 millions d'euros (TenCate a depuis changé son nom en Toray Advanced Composites). Cette décision semblait être un effort pour renforcer les capacités thermoplastiques de Toray en vue de la prochaine vague de développement d'avions commerciaux. Peu de temps après cette annonce, Hexcel (Stamford, Connecticut, États-Unis) et Arkema Inc. (Roi de Prusse, Pennsylvanie, États-Unis) ont annoncé une alliance stratégique pour développer des solutions composites thermoplastiques pour l'aérospatiale, combinant les compétences d'Hexcel dans la fabrication de fibres de carbone avec le polyéthercétonecétone d'Arkema. l'expertise des résines (PEKK). Et au cours de l'année, plusieurs autres pièces du puzzle des thermoplastiques ont semblé se mettre en place.
En avril 2018, Premium Aerotec GmbH (Augsbourg, Allemagne) a dévoilé un démonstrateur pour une cloison sous pression A320 d'Airbus (Toulouse, France) qu'elle avait développée et fabriquée en utilisant de la fibre de carbone dans une matrice thermoplastique. Le démonstrateur, qui se compose de huit segments soudés, illustre comment la soudabilité des thermoplastiques a le potentiel de permettre des composants d'avion plus gros. (En savoir plus sur le démonstrateur de cloison sous pression A320 de Premium Aerotec).
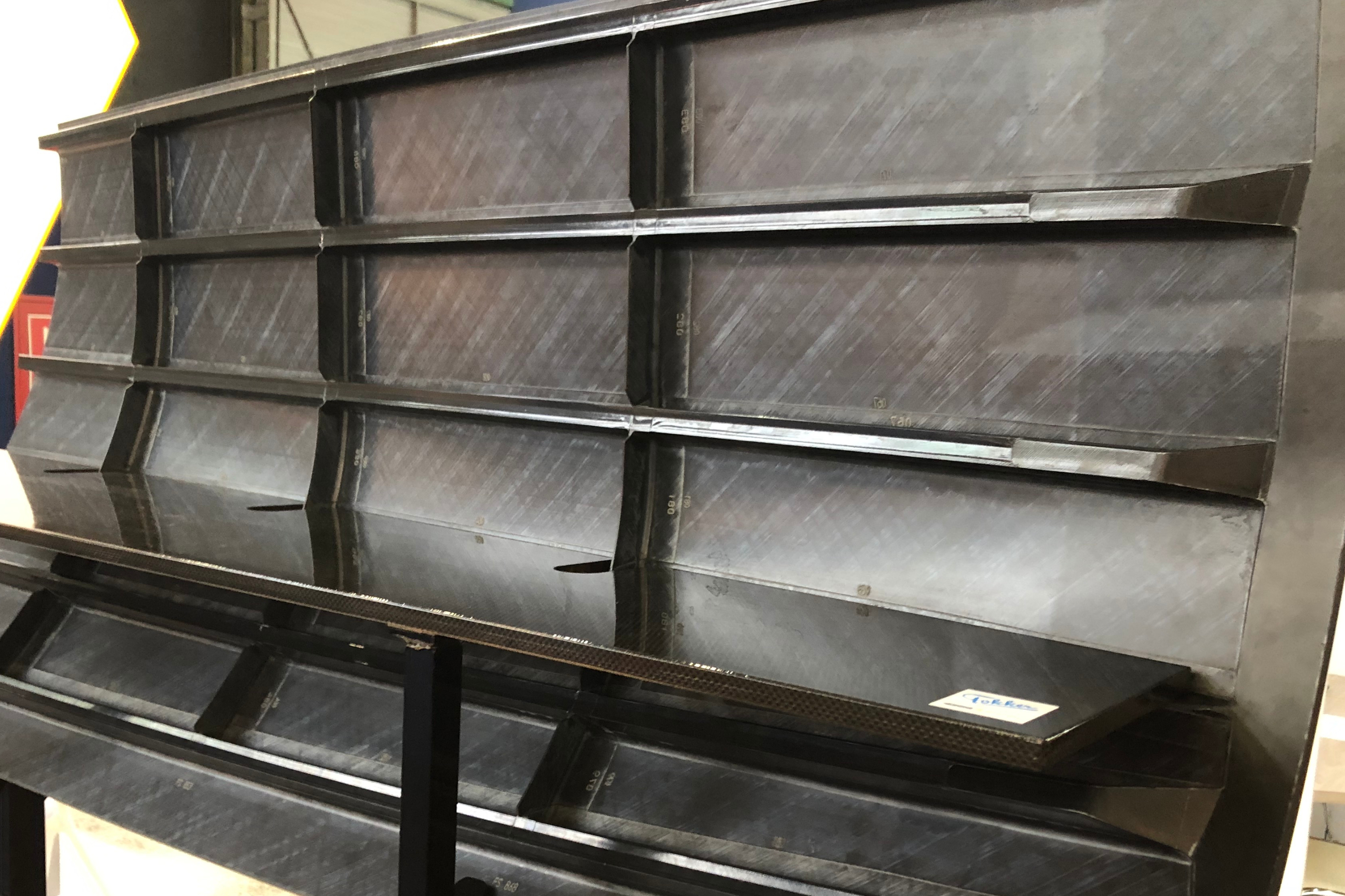
En août 2018, Solvay (Alpharetta, Géorgie, États-Unis), Premium Aerotec et Faurecia Clean Mobility (Columbus, Ohio, États-Unis) ont lancé IRG CosiMo (Industry Research Group :Composites for Sustainable Mobility), un consortium axé sur le développement de matériaux et des technologies de processus visant à permettre la production en grand volume de composites thermoplastiques pour les marchés de l'aérospatiale et de l'automobile. Le consortium associe des entreprises tout au long de la chaîne de traitement des composites thermoplastiques, des matériaux aux machines en passant par les applications dans l'automobile et l'aérospatiale. (En savoir plus sur le consortium IRG CosiMo ici).
Solvay s'est associé à GKN Fokker (Hoogeveen, Pays-Bas) pour faire progresser la technologie et poursuivre l'adoption des TPC pour les grandes structures aérospatiales depuis juin 2017. La société a lancé la production de polymères PEKK en septembre 2017, puis a doublé sa capacité de ruban thermoplastique UD qualifié en 2018. Plus tôt en 2019, Solvay a mandaté un laboratoire de recherche TPC dédié à Alpharetta, Géorgie, États-Unis, visant à développer des matériaux de nouvelle génération. Solvay prévoit de commencer la qualification d'une nouvelle ligne de ruban UD fin 2019.
Teijin Ltd. (Tokyo, Japon) a annoncé en janvier 2019 que son ruban pré-imprégné unidirectionnel unidirectionnel en fibre de carbone et fibre de carbone/thermoplastique (TENAX TPUD) avait été qualifié par Boeing (Chicago, Illinois, États-Unis) pour une utilisation en tant que produit intermédiaire avancé. matériau composite pour les pièces structurelles primaires (lire l'article complet ici).
À mesure que ces technologies et matériaux et des matériaux similaires progressent, une image de ce à quoi l'industrie aérospatiale pourrait commencer à ressembler dans les années et les décennies à venir se dessine progressivement. Le rôle des TPC devient de plus en plus une partie de cette image.
Les fabricants souhaitent profiter des avantages de fabrication et des temps de traitement rapides des thermoplastiques, et utiliser les TPC pour commencer à fabriquer des structures plus grandes telles que des panneaux de fuselage et des nervures. De plus, les thermoplastiques présentent une ténacité élevée à la rupture; bonnes propriétés mécaniques; recyclabilité; faible flamme, fumée et toxicité (FST) et peut être conservé à température ambiante. Et à mesure que les équipementiers et les fournisseurs de niveau aérospatial se familiarisent avec les thermoplastiques, ils sont utilisés pour des pièces plus complexes, des assemblages soudés et des structures primaires.
Selon Steve Mead, directeur général de Toray Advanced Composites (anciennement TenCate), "[les grands avionneurs] recherchent vraiment une solution matérielle qui a les capacités de taux de l'aluminium et les capacités de poids des matériaux à base de fibre de carbone - type de pont thermoplastique cet écart."
Processibilité des TPC
Une grande partie des raisons pour lesquelles les TPC trouvent leur place dans les programmes d'avions est leur aptitude au traitement. Parce que les thermoplastiques sont déjà entièrement polymérisés, ils ont des taux de production plus rapides que les thermodurcissables, qui doivent subir un durcissement.
« Quand vous regardez le temps qu'il faut pour fabriquer une pièce thermodurcie aujourd'hui et que vous le comparez au temps qu'il faut pour fabriquer une pièce en composite thermoplastique, [le thermoplastique] est environ 10 fois plus rapide », déclare Mike Favaloro, président et PDG de CompositeTechs LLC (Amesbury, Mass., États-Unis), une société de conseil dans l'industrie des composites.
Un grand avantage du placement automatisé des fibres thermoplastiques (AFP) par rapport à l'AFP thermodurcissable - en particulier compte tenu de l'absence de cycle de durcissement - sont des taux de production plus élevés en raison d'un temps de traitement plus rapide. Des économies de coûts peuvent être réalisées grâce au laminage in situ et à la post-consolidation hors autoclave (OOA). De plus, le fait de retirer l'autoclave de l'équation permet le développement de structures plus grandes.
David Leach, directeur du développement commercial pour ATC Manufacturing (Post Falls, Idaho, États-Unis), reconnaît que le coût unitaire des thermoplastiques dépasse le coût des thermodurcissables, mais soutient que les prix des matériaux TPC vont baisser. De plus, dit-il, l'efficacité du traitement offre une opportunité de réduire les coûts aujourd'hui. Le consensus général dans l'industrie des composites est que les procédés thermoplastiques OOA, à l'heure actuelle, offrent des économies de coûts de plus de 30 pour cent par rapport aux thermodurcissables.
« Les thermoplastiques trouvent leur place dans les programmes même après la mise en production des avions », souligne Leach. « Cela témoigne des avantages économiques des thermoplastiques. »
Le potentiel des polymères matriciels haute performance s'étend au-delà de ce qui est actuellement disponible sur le marché. Doug Brademeyer, responsable des matériaux ultra-polymères chez Solvay, déclare que la société travaille à la fois en interne et avec des partenaires pour développer des polymères sur mesure adaptés aux différents processus de fabrication.
« Nous sommes enthousiasmés par ces solutions PAEK personnalisées et pouvons rapidement les commercialiser dans nos actifs à l'échelle mondiale, en fonction des besoins des clients », déclare Brademeyer.
PAEK à bas point de fusion
Avec les équipementiers et les fournisseurs d'avions qui se bousculent pour des taux de production plus élevés et des temps de cycle plus courts, la capacité de traitement est la clé. Le polyétheréthercétone (PEEK) a longtemps été le polymère thermoplastique privilégié car il possède la plus grande base de données et est le plus largement qualifié. Mais selon Favaloro, la polyaryléthercétone à bas point de fusion (LM PAEK) offre certains avantages, en particulier pour les méthodes de traitement automatisées comme l'ATL.
« Le PEEK peut être traité par estampage et moulage en continu, mais le LM PAEK est traité à une température plus basse, a une viscosité de travail plus faible qui permet un meilleur traitement automatisé et a un degré de cristallinité inférieur qui réduit les contraintes de moulage résiduelles », dit-il.« Le but ultime est d'utiliser une machine ATL pour déposer [la bande] et d'en finir avec elle - vous avez besoin du bon degré de cristallinité, d'une bonne fenêtre et de bonnes vitesses de dépôt. »
LM PAEK a une large fenêtre de traitement de 350-385ºC. À titre de référence, les températures de traitement du sulfure de polyphénylène (PPS) vont de 330 à 350 °C, tandis que les températures de traitement du polyéthercétonecétone (PEKK) et du PEEK sont respectivement de 380 °C et 400 °C.
« Le matériau a tellement gagné en popularité en raison de sa capacité de traitement », a déclaré Scott Unger, directeur technique de Toray Advanced Composites. Toray Advanced Composites a collaboré avec Victrex (Lancashire, Royaume-Uni) pour produire Cetex TC1225, une bande unidirectionnelle utilisant LM PAEK.
« L'intention avec le développement du TC1225 était de créer un produit qui se transformait facilement à des températures proches de celles utilisées pour le PPS, avait une position de coût favorable pour l'utilisateur final et avait les propriétés de résistance mécanique et fluide du PEEK », explique Unger. "Avec le TC1225 LM PAEK, je pense que nous avons atteint tous ces objectifs."
Cetex TC1225 est actuellement en cours de qualification par le National Center for Advanced Materials Performance (NCAMP, Wichita, Kan., U.S.). En outre, Toray indique qu'il existe deux grandes qualifications basées sur l'avionneur dans les travaux pour le matériel, ainsi que quelques programmes de qualification basés sur les marchés émergents tels que les taxis aériens et la mobilité aérienne urbaine.
Les bandes utilisant le LM PAEK auraient permis d'améliorer les vitesses de dépôt. Tim Herr, directeur de l'Aérospatiale SBU chez Victrex, a déclaré :« Les taux de dépôt que nous pouvons atteindre pour l'AFP in situ et l'AFP consolidée hors autoclave sont sans précédent. » Il indique que 60 mètres par minute peuvent être atteints sur des panneaux consolidés au four; 20 mètres par minute seraient possibles avec la consolidation in-situ.
En termes de qualité, Unger affirme que le PAEK à bas point de fusion offre la possibilité d'obtenir la même qualité de stratifié en utilisant le placement des fibres in situ qu'avec un stratifié placé dans les fibres qui a été soumis à une consolidation au four après le placement des fibres.
Collage de composites
La soudabilité des TPC est un grand avantage du matériau utilisé dans le développement d'avions. Le collage/soudage par fusion offre une alternative à la fixation mécanique et à l'utilisation d'adhésifs, qui sont tous deux des méthodes utilisées pour assembler des pièces composites thermodurcissables.
Stephen Heinz, directeur du développement de produits chez Solvay, déclare :« L'assemblage et le soudage jouent un rôle majeur dans l'avenir de l'assemblage et ont le potentiel de réduire les coûts et d'améliorer la fiabilité des aérostructures. Des entreprises comme GKN Fokker prennent les devants en démontrant le soudage. »
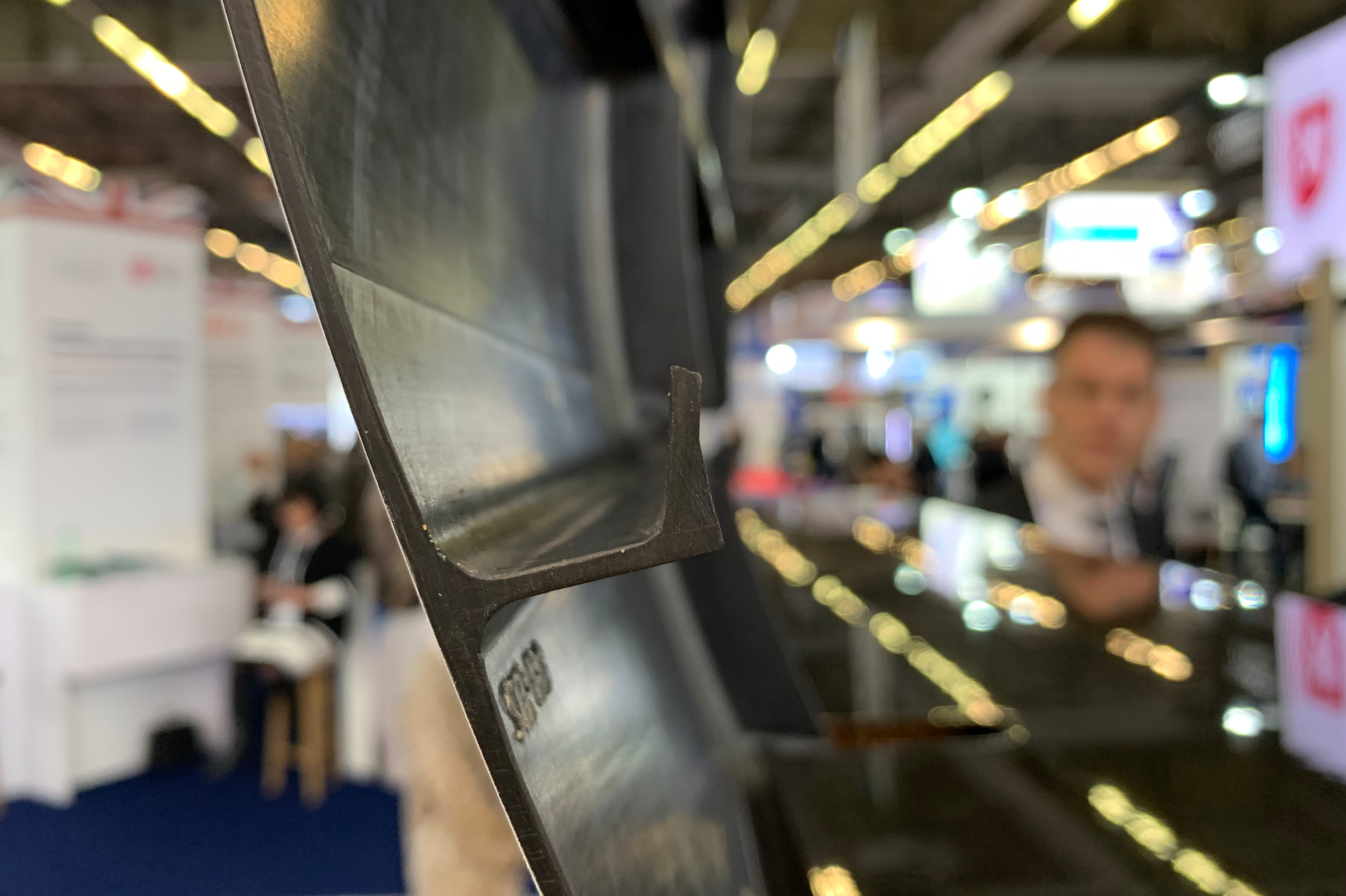
GKN Fokker (Hoogeveen, Pays-Bas) travaille depuis un certain temps au développement du soudage TPC, ayant commencé à expérimenter le soudage par résistance des thermoplastiques dans les années 90. L'entreprise utilise des procédés de soudage thermoplastiques pour assembler des nervures et des peaux internes de pointe. Au JEC World 2019, la société a présenté un panneau de fuselage en composite thermoplastique à règle de surface fabriqué à l'aide du ruban UD APC (PEKK-FC) de Solvay. Le panneau est le résultat d'un projet de R&D conjoint entre GKN Fokker et Gulfstream Aerospace (Savannah, Géorgie, États-Unis). La pièce serait le panneau composite le moins cher, en raison d'un simple raidissement de l'orthogrille « à joint bout à bout » et des cadres entièrement soudés.
« Avec les thermoplastiques, une orthogrille peut être considérablement simplifiée en « joignant bout à bout » la grille à la peau», explique Arnt Offringa, responsable du développement de la technologie des composites thermoplastiques pour GKN Fokker. « La grille est maintenant composée de simples préformes plates qui sont co-consolidées avec le stratifié de la peau pour former une coque à faible coût et intégralement raidie. Les cadres sont soudés sur la grille. Ces soudures sont chargées en cisaillement, ce qui permet d'omettre tous les boulons. »
Alors que les structures thermoplastiques soudées sont utilisées sur les avions depuis un certain temps, la technologie semble désormais bien placée pour être utilisée dans les structures primaires. Mike Favaloro pense que les fabricants de produits aérospatiaux et les équipementiers gagnent en confiance dans les TPC, en particulier dans le contrôle des processus. « À un horizon de 10 ans, nous commencerons à le voir beaucoup plus adopté », dit-il.
En savoir plus sur la technologie de soudage dans l'article de Ginger Gardiner « Soudage des composites thermoplastiques ».
Passer à l'outil sans outil
Une autre innovation à l'horizon qui pourrait permettre d'accélérer l'utilisation des thermoplastiques est la fabrication de composites sans outil. Le concept, comme son nom l'indique, élimine le besoin de moules et d'outillages traditionnels, en les remplaçant par la robotique.
Le constructeur aérospatial General Atomics Aeronautical Systems Inc. (GA-ASI, San Diego, Californie, États-Unis) développe un tel procédé pour la fabrication de structures composites thermoplastiques. Composite Automation LLC (Cape Coral, Floride, États-Unis), utilisant l'équipement Mikrosam (Prilep, Macédoine), a travaillé avec GA-ASI pour développer l'automatisation. Le processus utilise deux robots à 6 axes travaillant ensemble pour placer du ruban thermoplastique. Un robot se compose d'un système de placement de bande unidirectionnel standard qui fournit un chauffage laser pour effectuer la consolidation in situ du matériau thermoplastique. Le second robot fournit un support, travaillant à l'opposé de la couche de bande automatisée (ATL) pour fournir une surface d'outillage mobile contre laquelle l'ATL place la bande. (Pour en savoir plus, voir « General Atomics Aeronautical développant un processus de composites thermoplastiques sans outil. »)
Recyclabilité
Un autre avantage des TPC est la recyclabilité. Étant donné que les polymères thermoplastiques peuvent être refondus et remodelés, plusieurs entreprises se tournent vers les TPC comme moyen de réutiliser les matériaux.
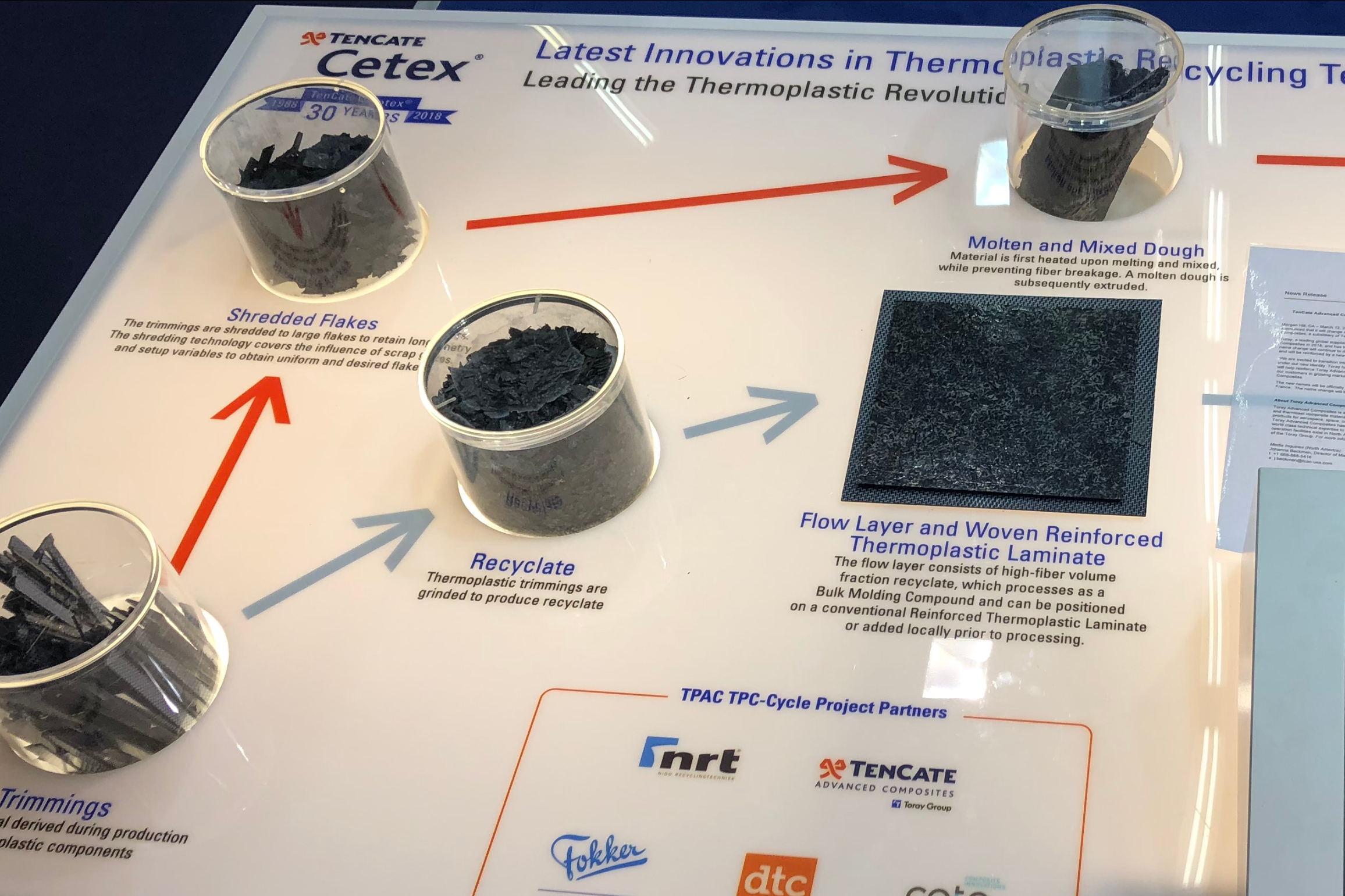
L'une de ces initiatives de recyclage, gérée par le Thermoplastic CompositesApplication Center (TPAC, Enschede, Pays-Bas) et le Thermoplastic Composites Research Centre (TPRC, Enschede, Pays-Bas), est axée sur la réutilisation des déchets de production issus du traitement TPC, de la collecte au déchiquetage et du retraitement jusqu'à l'application. Le projet TPC-Cycle s'efforce de développer une voie de recyclage abordable et respectueuse de l'environnement pour les marchés haut de gamme et à volume élevé, tout en produisant un matériau qui conserve autant que possible les propriétés mécaniques des matériaux thermoplastiques d'origine. Le projet bénéficie de temps de cycle courts, d'une fabrication en forme de filet et est censé permettre la production de formes complexes.
La collaboration comprend plusieurs partenaires industriels dans la chaîne de valeur, du matériau, de la fabrication, de la conception et de l'application, notamment GKN Fokker, Toray Advanced Composites, Cato Composite Innovations (Rheden, Pays-Bas), Dutch Thermoplastic Components (Almere, Pays-Bas) et Nido RecyclingTechniek (Nijverdal , Pays-Bas).
Le bon matériau pour le bon travail
Alors, au milieu du vacarme d'excitation suscité par ces matériaux, la question qui se pose est la suivante :les TPC sont-ils arrivés ? Les fournisseurs aérospatiaux de niveau 1 et de niveau 2 investissent dans les thermoplastiques. Il y a plus d'intérêt et d'investissement de la part des fournisseurs de petite et moyenne taille. Des consortiums comme IRG CosiMo se penchent sur les marchés de l'aérospatiale et de l'automobile pour faire progresser les technologies de processus afin d'atteindre une production en grand volume.
« C'est le Trifecta », déclare Mead, « les équipementiers investissent, les fabricants de machines investissent, le bon matériau a été développé. Tous les composants de la recette sont réunis. »
À plus grande échelle, qu'est-ce que tout cela signifie en ce qui concerne l'utilisation des matériaux sur les avions de nouvelle génération ? Après tout, de nombreux matériaux se disputent une place dans l'avion du futur, et l'innovation ne ralentit pas :les composites thermodurcissables continuent d'évoluer; l'aluminium et le titane continueront de jouer un rôle.
« Alors que les avionneurs développent une base de qualification avec les thermoplastiques, ils ont désormais le choix », déclare Unger. « Et ce choix sera basé sur la sélection du bon matériau pour une application donnée qui répond aux exigences de taux de production et de coût pour le composant ou la structure en question. En regardant l'aviation commerciale à l'avenir, ce que je pense que vous verrez les avionneurs faire, c'est utiliser le bon matériau pour le bon travail. Si un matériau permet la structure la plus appropriée pour le moindre coût et répond aux exigences de taux de construction du programme, il gagnera sa place dans l'avion. »
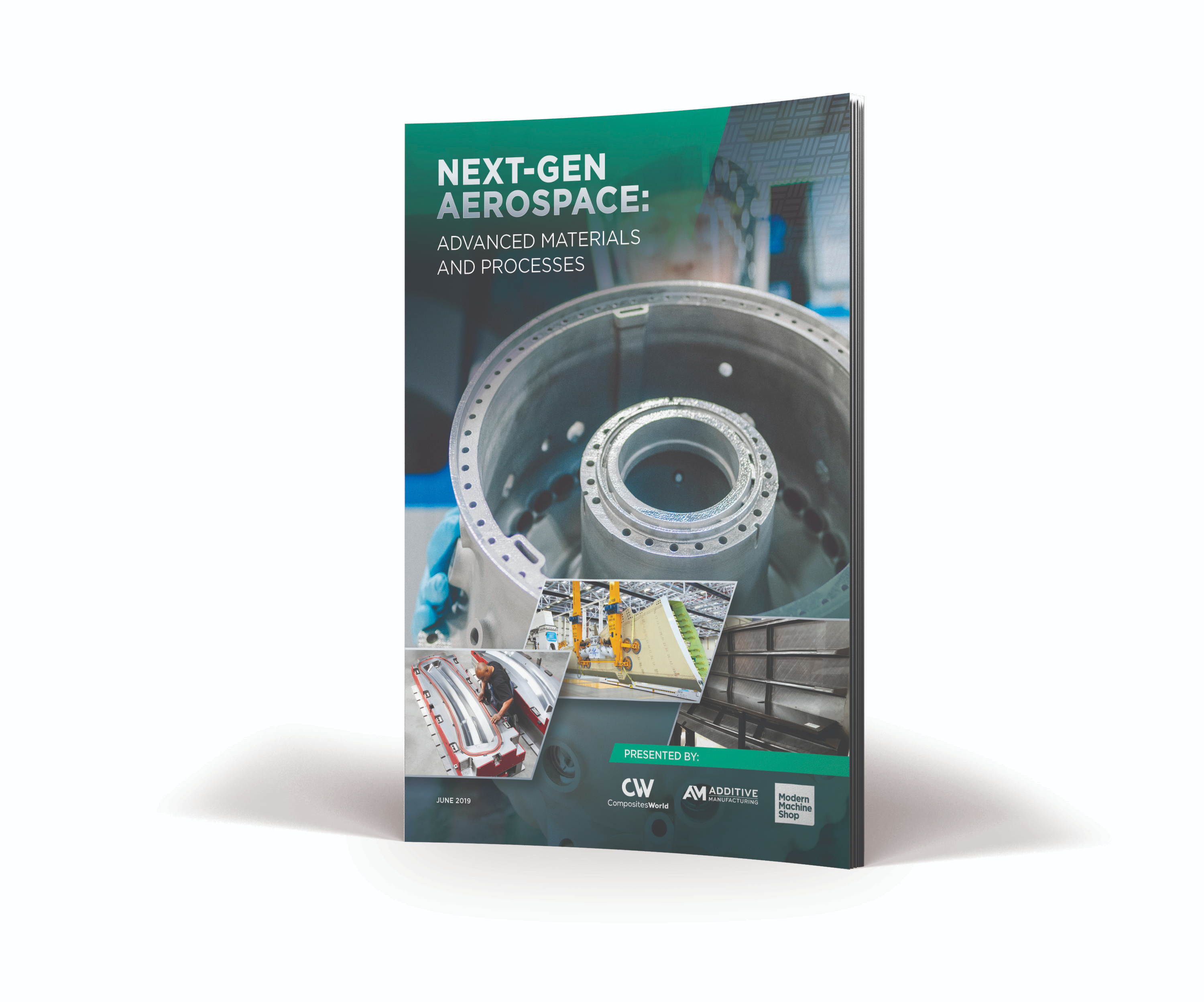
La prochaine génération de fabrication aérospatiale
Le secteur de l'aviation commerciale devant doubler au cours des 20 prochaines années, répondre à la demande d'avions de transport de passagers et de fret nécessitera de nouvelles technologies et des taux de fabrication sans précédent.
Apprenez-en plus sur les matériaux et les processus qui façonneront les avions de nouvelle génération dans une collection d'histoires de CompositesWorld, Modern Machine Shop et Fabrication Additive , disponible pour lire ou télécharger gratuitement . Obtenez-le ici.
Résine
- Covestro intensifie ses investissements dans les composites thermoplastiques
- Composites thermoplastiques chez Oribi Composites :CW Trending, épisode 4
- Dépannage du thermoformage des composites thermoplastiques
- Composites thermoplastiques :support de pare-chocs structurel
- L'ACMA publie le programme 2020 de la Conférence sur les composites thermoplastiques
- Porte thermoplastique une première pour les composites automobiles
- Composites thermoplastiques :vue panoramique
- Aperçu CAMX 2018 :TenCate Advanced Composites
- Soudage de composites thermoplastiques