Fourniture d'énergie innovante pour une fabrication de composites plus efficace
Ceci est mon deuxième blog dans cette série pré-CAMX 2019 qui met en évidence les technologies clés qui ont été réellement exposées au CAMX 2018. Ce blog se concentre sur le nouveau black.infrared d'Heraeus Noblelight. système, un nouveau type de système pour le traitement des composites, et son humm3 technologie, qui remplace les radiateurs laser et infrarouges dans les machines de placement automatique de fibres (AFP).
Innover avec la lumière
Heraeus Noblelight innove une large gamme de procédés industriels en utilisant la puissance de la lumière. Pour donner un aperçu, toute la lumière est un rayonnement électromagnétique (EMR) et a une longueur d'onde et une fréquence inhérentes, comme on peut le voir dans le diagramme ci-dessous. Heraeus Noblelight développe des appareils qui utilisent la lumière sur une grande partie de ce spectre, allant des émetteurs infrarouges (IR) aux lampes LED et aux systèmes ultraviolets (UV), ainsi qu'aux lampes à arc et flash.
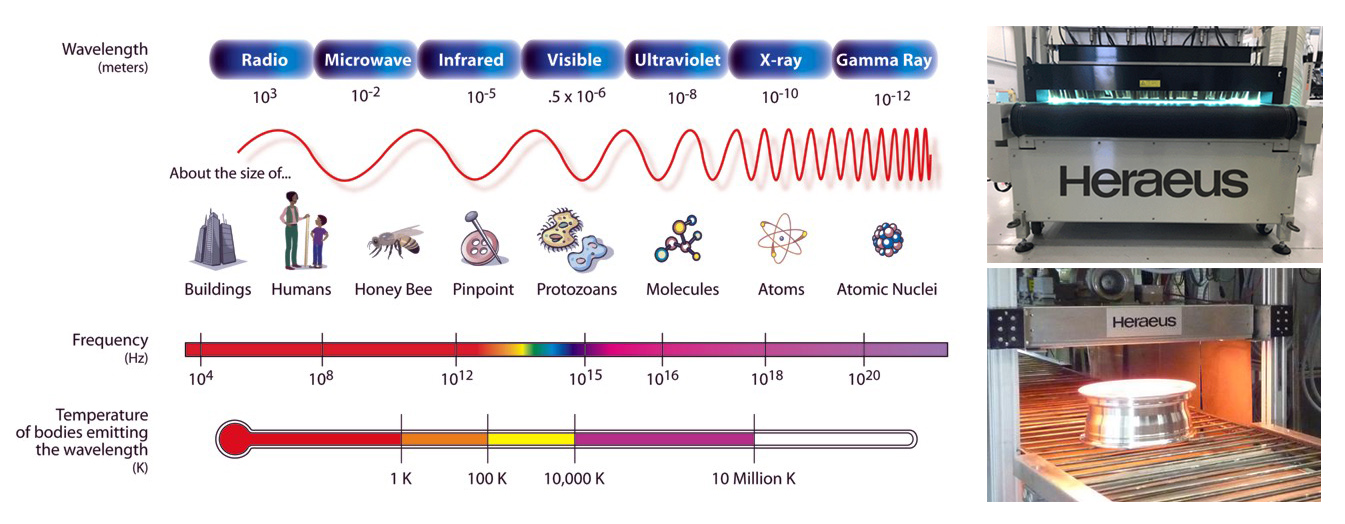
La lumière le long du spectre électromagnétique est utilisée pour le chauffage et le traitement.
SOURCE | https://mynasadata.larc.nasa.gov/basic-page/electromagnetic-spectrum-diagram (à gauche) et Heraeus (à droite).
Dans les composites, les systèmes UV et infrarouge (IR) sont utilisés depuis des décennies, comme on peut le voir dans l'exemple ci-dessous. Le système infrarouge noir, cependant, est une nouvelle technologie.
- Sunrez a développé une technologie de polymérisation aux UV pour l'infusion de résine et la réparation de composites dans les années 1990.
- Les revêtements époxydiques durcis aux UV sont la norme dans de nombreuses industries.
- La résine époxy durcie aux UV est également utilisée par les pionniers de l'impression 3D à fibre continue tels que Continuous Composites et moi composites.
- Le chauffage infrarouge est très courant dans les lignes de production automatisées de composites où les ébauches sur mesure 2D doivent être préchauffées avant le préformage et/ou les préformes doivent être préchauffées avant l'emboutissage et le surmoulage.
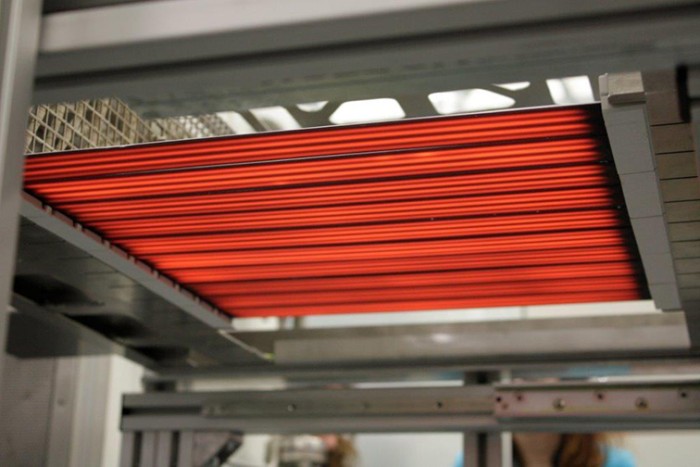
Système de chauffage infrarouge noir de Heraeus Noblelight pour composites. SOURCE | Heraeus Noblelight
Noir.infrarouge
Heraeus Noblelight a exposé son nouveau noir.infrarouge système au CAMX 2018. « C'est un émetteur infrarouge à ondes moyennes qui fournit beaucoup de puissance dans un petit volume », explique Bruce Fricks, directeur des ventes principal pour les systèmes infrarouges, Heraeus Noblelight America, LLC. Bien que Heraeus Noblelight ait son siège à Hanau, en Allemagne, sa division américaine pour les systèmes de lampes IR et flash est basée à Buford, en Géorgie, tandis que sa division américaine pour les systèmes UV est basée à Gaithersburg, dans le Maryland.
« En général, pour un émetteur infrarouge à ondes moyennes, vous vous dirigez plutôt vers une densité de puissance de 60 kW/m 2 ", explique Fricks, " mais " Black IR " atteint 200 kW/m 2 . L'IR est un moyen beaucoup plus efficace d'amener de l'énergie dans un substrat que de chauffer tout l'air qui l'entoure, mais Black IR est trois fois plus efficace qu'un four à convection. Pour le traitement en ligne, cela signifie qu'un convoyeur peut fonctionner trois fois plus vite ou être raccourci pour prendre moins de place. Par exemple, un convoyeur avec un four de 30 pieds de long pourrait être réduit à un four de 10 pieds en utilisant Black IR. »
À ce jour, les applications des systèmes à infrarouge noir comprennent le soudage de plastiques et le chauffage de films photovoltaïques minces (de microns d'épaisseur) pour les cellules solaires. « L'IR, en général, fonctionne très bien pour le dépôt au niveau atomique », note Fricks, « par exemple, l'application de couches de gallium ou de motifs en silicium pour les semi-conducteurs. Attention, toutes ces opérations se font dans le vide. Black IR fonctionne également bien dans le vide et à haute température. »
Il explique que les émetteurs infrarouges noirs ont été conçus pour fonctionner avec une température de surface de 1000°C. "Ces émetteurs sont tous à semi-conducteurs, vous pouvez donc en mettre un dans un four fonctionnant à 700-800°C et il n'en souffrira pas. Cependant, si un processus nécessite des températures beaucoup plus élevées que cela, disons 1 500 °C ou plus, l'IR à ondes courtes conviendrait mieux. »
Fricks explique que Black IR est également une technologie de ligne de visée. « C'est mieux pour les surfaces plates ou simples convexes/concaves. Le plus gros problème concerne les pièces ou les matériaux ayant des zones internes ou externes où quelque chose projettera une ombre. »
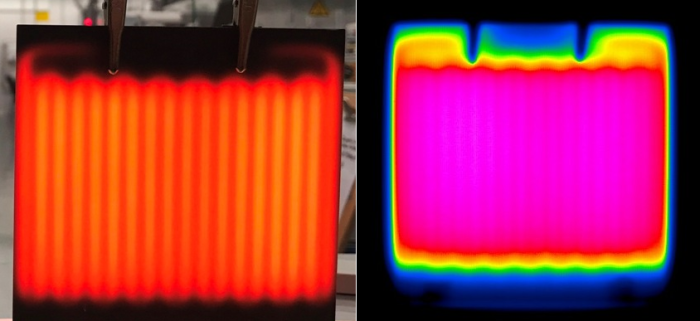
Un module noir.infrarouge (gauche ) et image thermique montrant l'uniformité de la température (à droite ).
SOURCE | Heraeus Noblelight
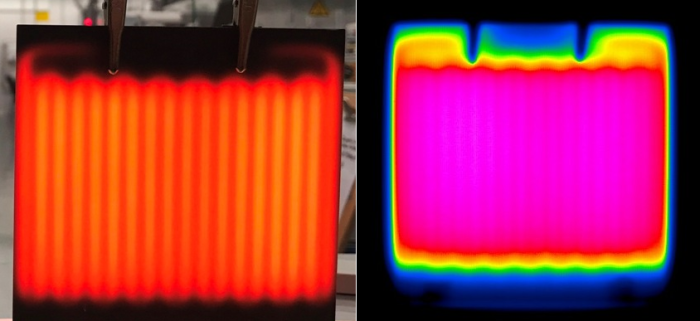
Avantages du Black IR et applications potentielles des composites
Fricks note que black.infrared n'est pas un émetteur infrarouge à filament, qui a tendance à être plus lumineux au centre que sur les côtés. Au lieu de cela, il produit une énergie très uniforme sur la surface plane 2D de l'émetteur, dont la taille peut aller de 40 millimètres sur 400 millimètres jusqu'à 100 millimètres sur 100 millimètres. "Nous pouvons également mosaïquer les émetteurs IR noirs pour créer un appareil planaire jusqu'à 400 mm sur 400 mm", ajoute-t-il.
Parce que black.infrared est un dispositif IR à ondes moyennes, il est relativement daltonien (blanc vs sombre), explique Fricks. « Il ne cuit pas les matériaux noirs et ne surchauffe pas les matériaux jaunes ou blancs. » Et pourtant, il aurait fallu moins de 60 secondes pour chauffer. « Watt pour watt, ce n'est pas très cher par rapport aux autres options IR », déclare Fricks. "L'IR est plus cher qu'un four à convection, mais il offre vitesse et efficacité, ainsi que la capacité de fournir une température très uniforme, c'est-à-dire une variation inférieure à plus ou moins 5 degrés."
L'IR noir pourrait potentiellement être utilisé dans la production de fibres, de préimprégnés, de rubans composites et éventuellement de procédés de dépôt chimique en phase vapeur (CVD) comme ceux utilisés pour fabriquer du graphène et d'autres matériaux nanocomposites. Fricks recherche des discussions avec des fabricants et des fournisseurs de matériaux pour explorer et développer d'autres applications dans les composites.
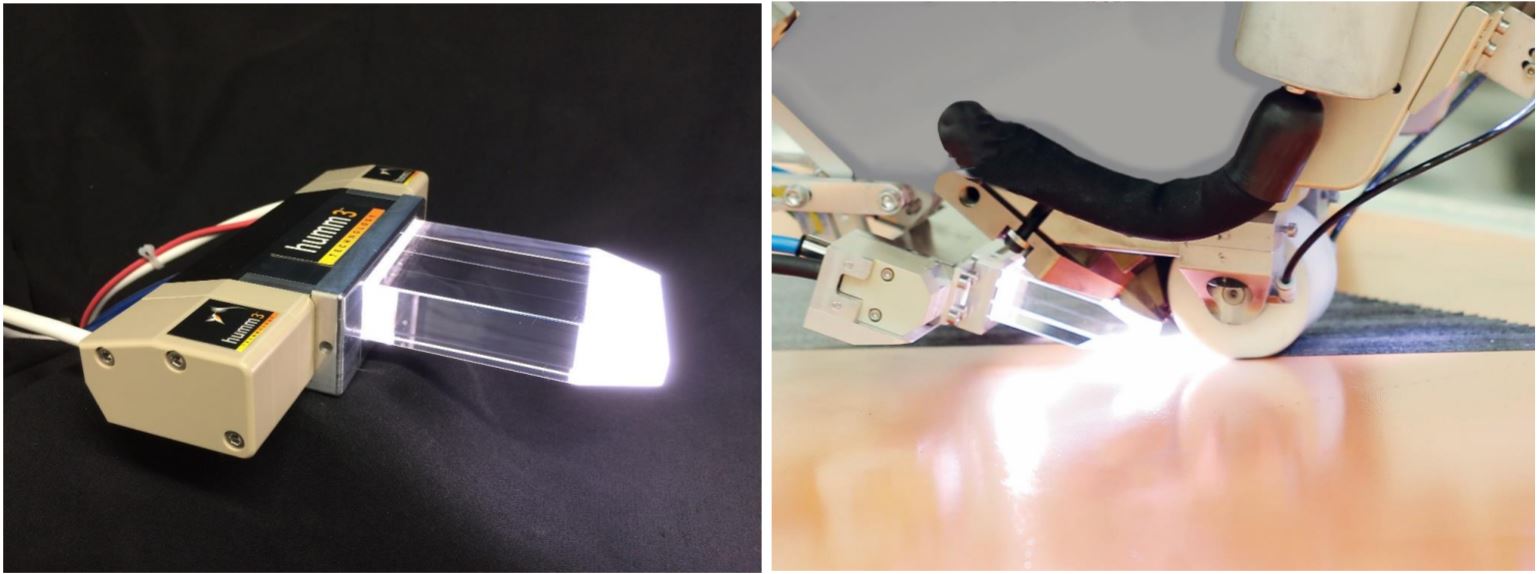
Le système humm3 pour le placement automatisé des fibres de composites thermodurcissables, thermoplastiques et à fibres sèches. SOURCE | Heraeus Noblelight
humm3 remplace les lasers dans l'AFP
L'autre technologie présentée par Heraeus Noblelight au CAMX 2018 était son humm3 système de placement automatisé de fibres (AFP) de rubans thermodurcissables préimprégnés, fibres sèches et composites thermoplastiques. Le système humm3 utilise une lampe flash remplie de xénon qui est pulsée plusieurs fois par seconde. Dans la partie 2 de mon article de 2018 sur la consolidation in situ des composites thermoplastiques, j'ai décrit sur la figure 2 comment les lasers couramment utilisés dans l'AFP thermoplastique peuvent être distingués par leur lumière violette par rapport à la lumière orange des radiateurs infrarouges (IR). utilisé dans le préimprégné AFP thermodurcissable. Notez que la technologie humm3 se différencie des deux par sa lumière blanche et brillante.
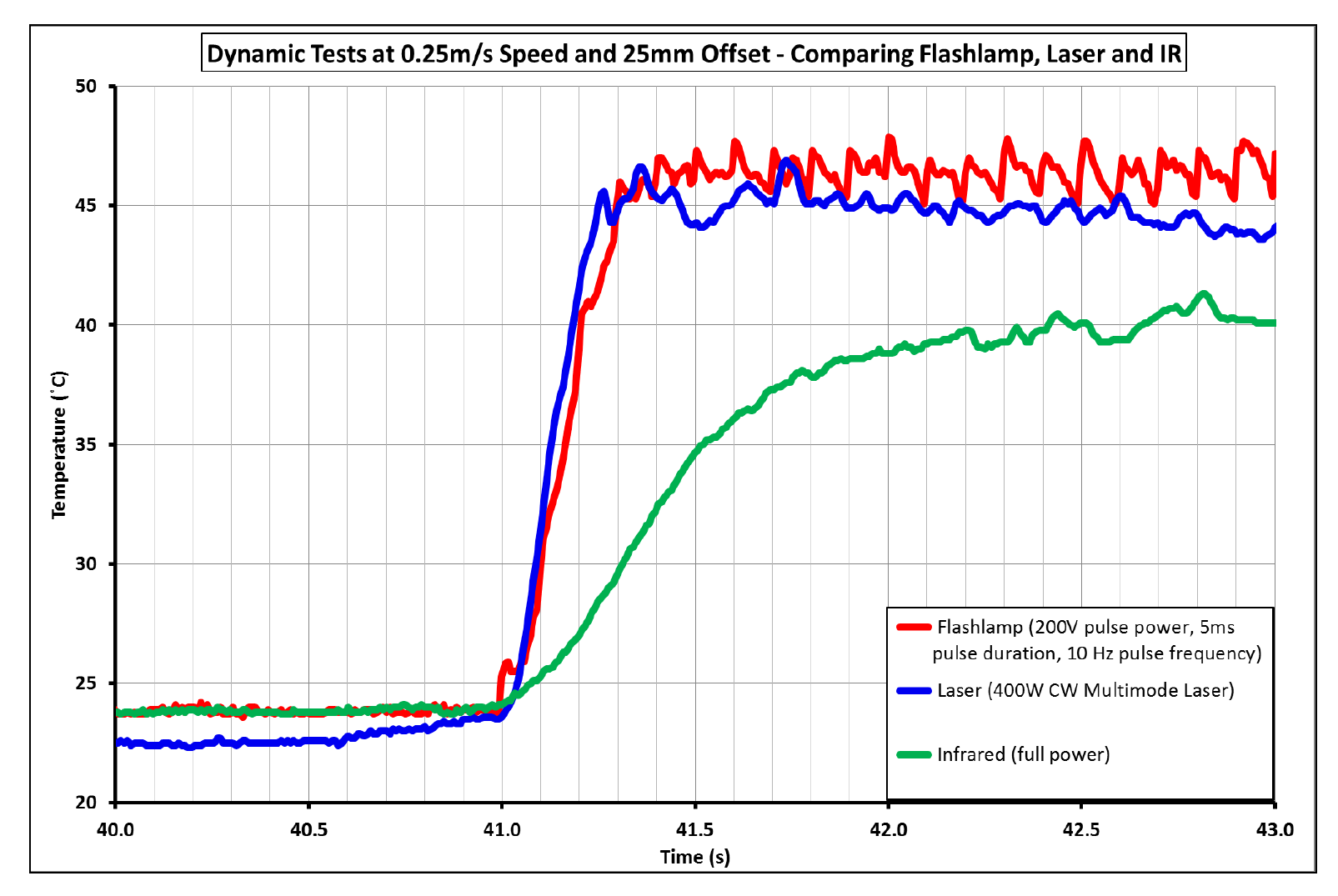
SOURCE | Heraeus Noblelight
« Les lampes infrarouges sont relativement peu coûteuses, mais elles sont lentes et ne peuvent pas atteindre les températures élevées requises par les thermoplastiques aérospatiaux », explique Kyle Hudspeth, directeur des ventes du système humm3 de Heraeus Noblelight en Amérique du Nord et du Sud. « D'un autre côté, les lasers sont très rapides à chauffer et à refroidir, mais ils sont chers et nécessitent des précautions de sécurité importantes. Humm3 comble une lacune sur le marché du chauffage rapide, sûr, compact et économique pour l'AFP. »
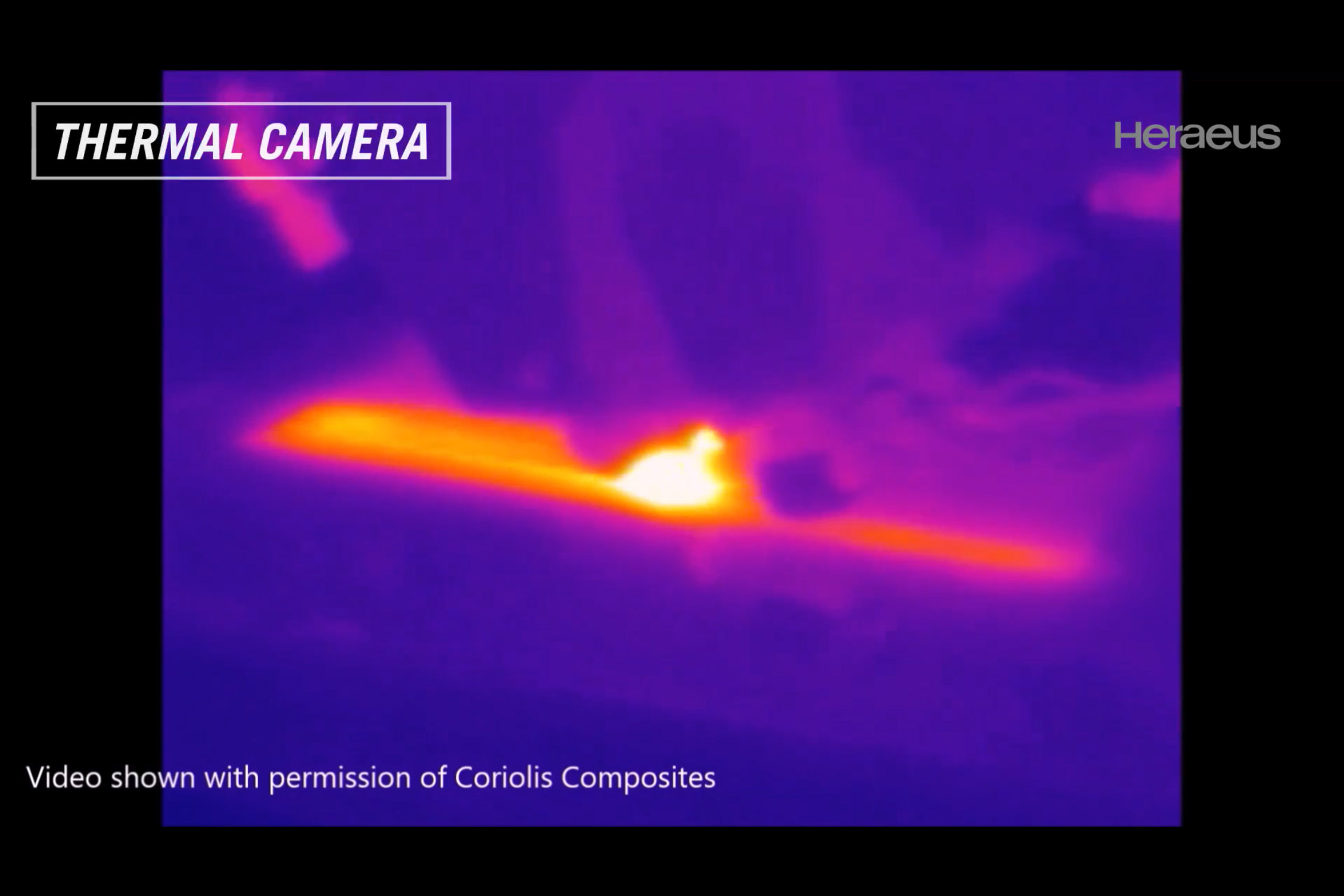
Hudspeth explique que humm3 fournit une chaleur uniforme au point de pincement AFP sur une large plage de températures, allant de 50 °C au maximum actuellement mesuré de 600 °C. Il peut également être contrôlé avec précision à l'aide de trois paramètres programmables :
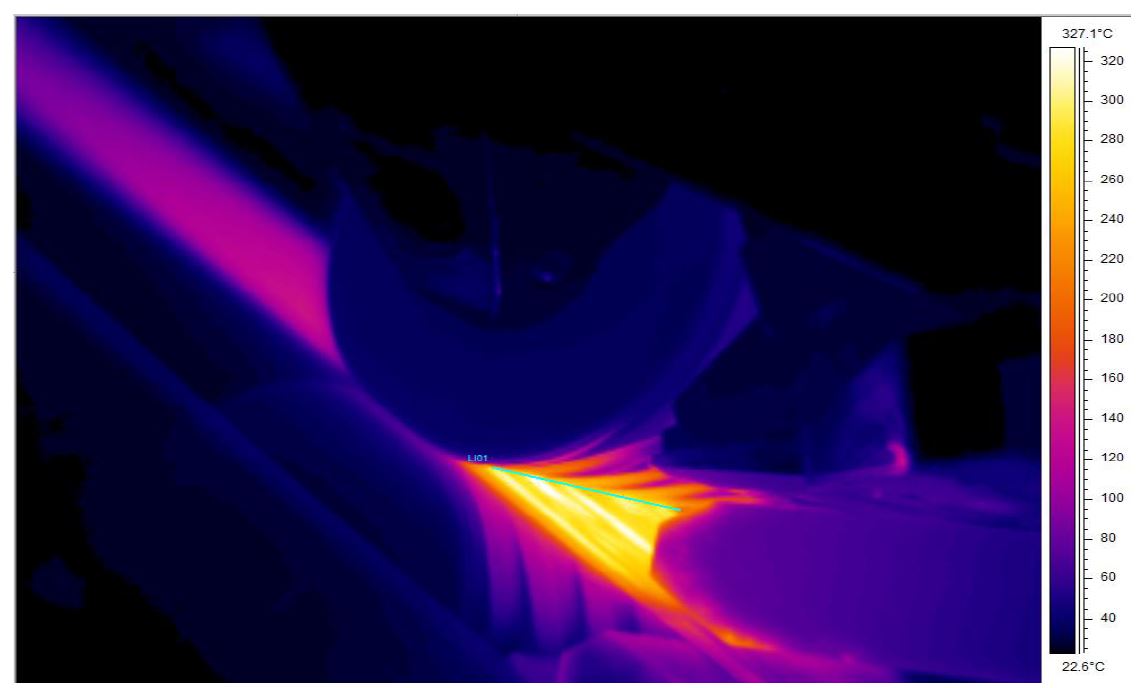
Image thermique du lay-up PEEK sur une machine AFP robotisée. L'optique de distribution du quartz humm3 est visible à droite, pointant vers le point de pincement entre le substrat et le matériau entrant. Des vitesses de 6 mètres par minute ont été atteintes avec des résultats de bonne qualité.
SOURCE | Heraeus Noblelight
- impulsion énergie (quelle taille),
- impulsion durée (combien de temps)
- fréquence d'impulsion (combien de fois par seconde).
Il ajoute que le temps et la température de chauffage sont à peu près les mêmes qu'avec un laser, "mais aucune cabine laser de protection n'est requise, de sorte que les techniciens peuvent être proches du drapage pendant le fonctionnement."
Lors de tests de traitement de stratifiés de polyétheréthercétone renforcé de fibres de carbone (PEEK), Heraeus Noblelight a démontré que humm3 peut produire des stratifiés AFP thermoplastiques de haute qualité avec la cristallinité ≈ 35 % et la porosité <2 % requises pour les structures composites aérospatiales. Dans le cadre du programme européen Clean Sky 2, le Center for Lightweight Production Technology (ZLP, Stade, Allemagne) travaille avec Heraeus Noblelight pour développer humm3 dans le système multi-robot GroFi du Centre aérospatial allemand (DLR) de Stade. Le travail vise à augmenter considérablement les taux d'AFP pour les structures composites thermoplastiques tout en répondant à des exigences de qualité strictes.
Pour les stratifiés de fibres sèches qui seront traités par infusion de résine ou moulage par transfert de résine (RTM), Hudspeth affirme que humm3 permet une vitesse de drapage de 1 mètre par seconde et un chauffage uniforme sur huit ou 16 bandes, chacune de 0,25 pouce de large. Le chauffage sur une largeur de 300 millimètres peut être réalisé avec une seule lampe et coordonné avec l'alimentation modulaire et la conception modulaire du humm3 pour personnaliser davantage un système AFP pour des zones chauffées encore plus grandes. L'optique de livraison à quartz humm3 est également personnalisable pour obtenir une forme de zone de chaleur précise.
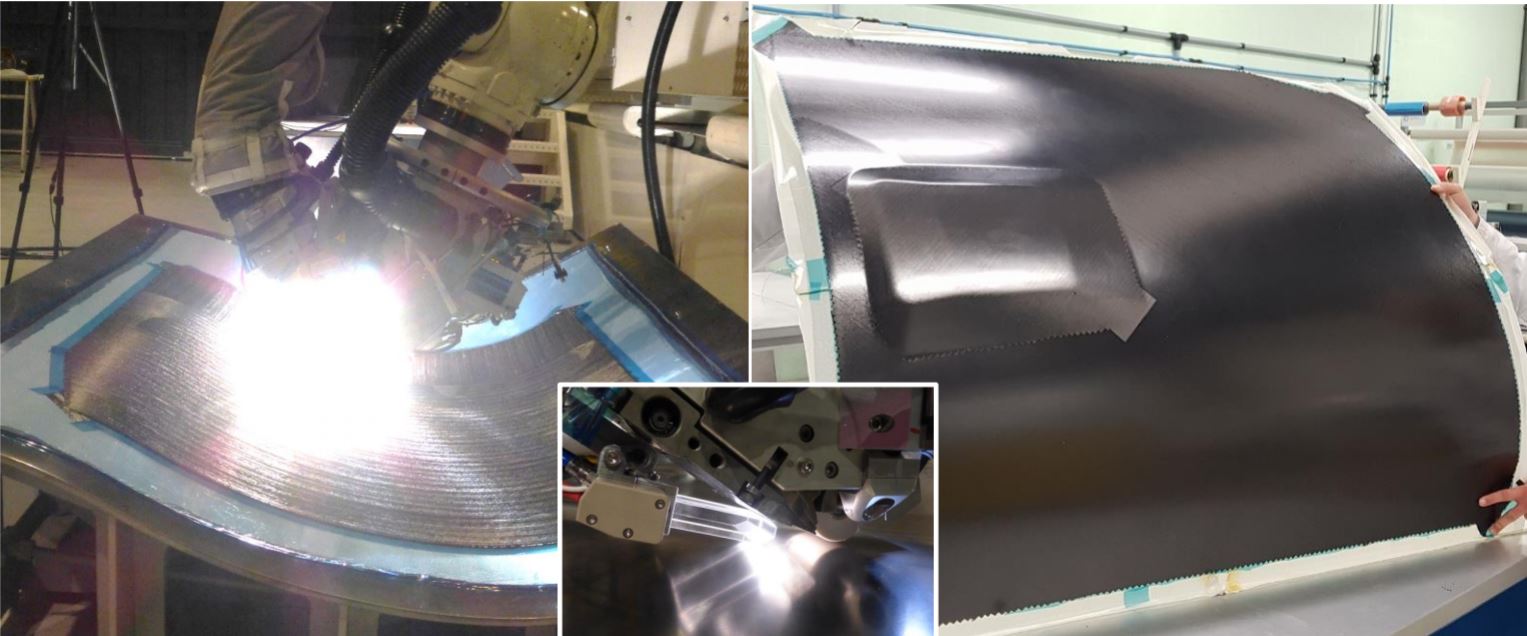
Un démonstrateur de pièces aérospatiales utilisant le ruban à fibres sèches HiTape d'Hexcel (à gauche) et la résine RTM6 (à droite). SOURCE | Heraeus Noblelight
Le système humm3 est en cours de développement pour d'autres traitements de composites, notamment le soudage thermoplastique, l'enroulement filamentaire et le collage de plusieurs couches composites pour les préformes. Hudspeth note que humm3 est une technologie mature et éprouvée, démontrée au National Composites Center (Bristol, Royaume-Uni) depuis 2016 et lauréate du Queen's Award for Innovation au Royaume-Uni en 2015.
Pour plus de détails, visitez Heraeus Noblelight au stand CAMX Y47.
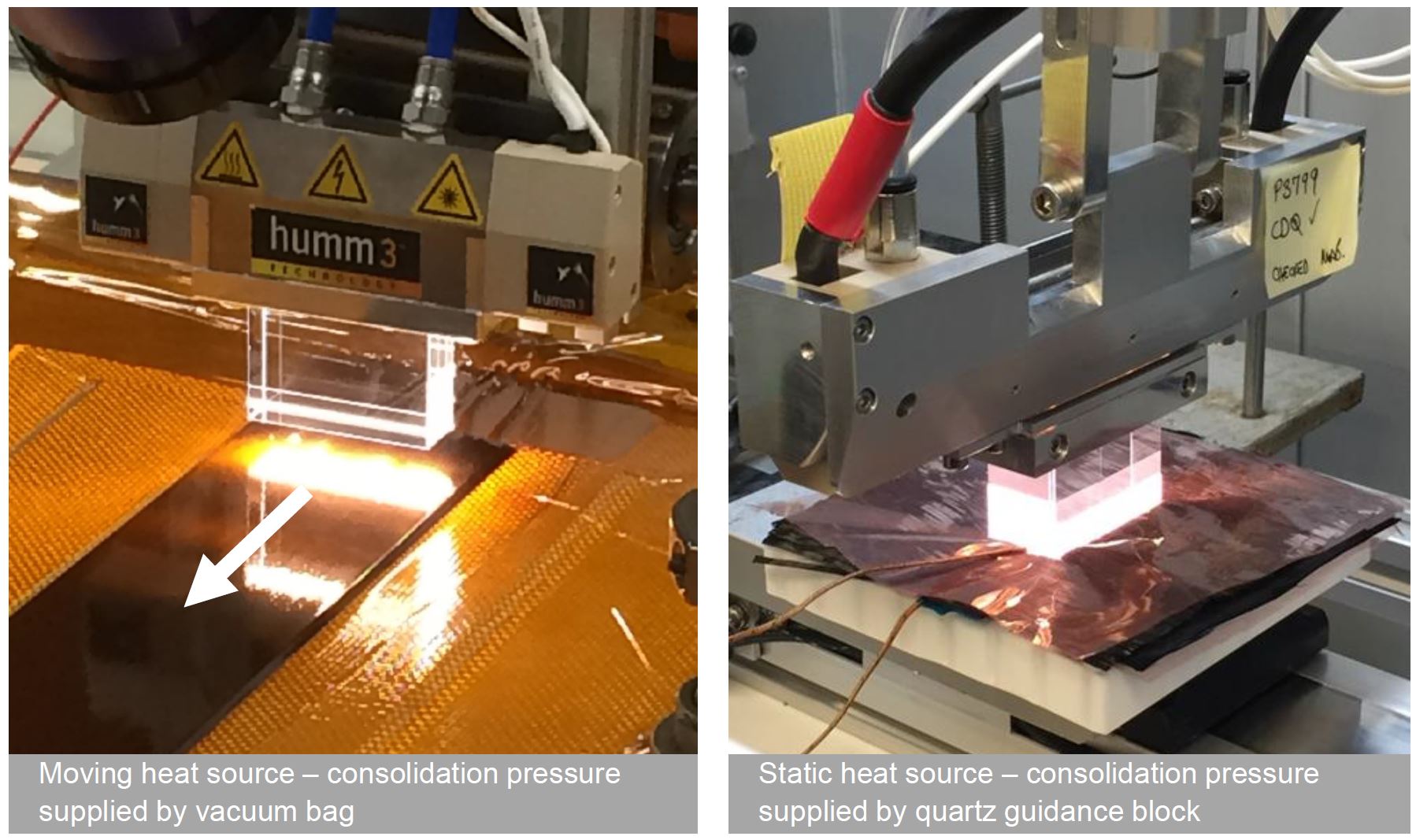
SOURCE | Heraeus Noblelight
Résine
- Les 7 principales tendances de fabrication pour 2020
- Utiliser des listes de contrôle pour une usine plus efficace
- Êtes-vous un fabricant économe en énergie ?
- Le collège communautaire ajoute de la flexibilité pour les étudiants avancés en fabrication de composites
- 10 idées pour des opérations d'entrepôt plus efficaces et plus productives
- Fabrication verte :des idées écologiques pour les usines
- 6 façons dont l'IIoT rend la fabrication plus efficace
- RAPPORT :2016 sera un « point de basculement » pour la technologie de fabrication
- Répondre au grand besoin d'automatisation des composites