Impression 3D de fibre continue sur le bureau
Le nouveau système d'impression 3D de bureau à fibre continue de Desktop Metal Source | Métal de bureau
Desktop Metal (Burlington, Mass., États-Unis), une société spécialisée dans l'impression 3D métallique pour le développement de produits et la production de masse, a annoncé qu'elle étendrait sa technologie pour inclure la communauté des composites. Desktop Metal a été fondée en 2015 avec pour mission de « rendre l'impression 3D accessible à tous les ingénieurs, concepteurs et fabricants ». -Imprimante 3D en métal du système de production en volume, capable d'imprimer à des vitesses allant jusqu'à 12 000 cm 3 /heure. Aujourd'hui, la société dévoile ce qu'elle dit être la première véritable imprimante de bureau à fibre continue au monde.
« Nous élargissons maintenant notre offre pour intégrer l'impression 3D à fibre continue sur le bureau de chaque ingénieur et concepteur », déclare Ric Fulop, PDG et fondateur de Desktop Metal.
Les progrès récents de la fabrication additive ont vu son utilisation se généraliser pour le prototypage, ainsi que pour les gabarits, les montages et l'outillage. Desktop Metal prédit que la technologie connaîtra une croissance de 10 à 50 fois au cours de la prochaine décennie en tant que moyen de fabrication de pièces d'utilisation finale. L'entreprise a reconnu une opportunité sur le marché d'apporter l'impression 3D dans une zone mal desservie :l'automatisation de la fabrication de petites pièces composites. Débutant son entrée dans le secteur des composites, Desktop Metal a récemment acquis Make Composites Inc. (Boston, Mass., États-Unis), une start-up fondée par Konstantine Fetfatsidis. Fetfatsidis a récemment été nommé SAMPE Young Professional of the Year 2019 et était auparavant responsable de la R&D en fabrication de pointe chez Aurora Flight Sciences (Manassas, Virginie, États-Unis), une société Boeing.
Fetfatsidis, maintenant vice-président des produits composites pour Desktop Metal, explique son inspiration pour le démarrage de Make. « Sur la base de mon expérience dans la R&D sur les composites et également dans le développement commercial d'aérostructures avec les clients, j'ai pu voir et travailler avec ce qui était accessible et les différentes technologies de fabrication disponibles, et franchement, j'étais un peu frustré par le fait que la pose à la main était toujours à la pointe de la technologie. -l'art, en particulier pour les petites pièces », dit-il.
Il fait valoir que pour les petites pièces – moins de 20 livres – les fabricants comptent toujours principalement sur le drapage manuel. Ces processus à forte intensité de main-d'œuvre nécessitent des techniciens, un outillage coûteux et beaucoup de temps, ce qui augmente le coût global de fabrication d'une pièce.
« Tout au long de ma carrière, il y a eu tellement d'applications où nous aurions aimé utiliser la fibre de carbone - en particulier chez Aurora lorsque je travaillais sur les concepts eVTOL - pour ses propriétés légères, sa rigidité et sa résistance, mais les coûts ne s'additionnaient tout simplement pas, ", dit Fetfatsidis. « Je me suis dit qu'il devait exister un meilleur moyen d'automatiser, de consolider le nombre d'étapes de processus impliquées dans la fabrication traditionnelle, de réduire l'outillage et les délais de livraison, tous les coûts qui y sont associés. »
Bien que des tentatives aient été faites pour automatiser la fabrication de petites pièces composites, les propriétés atteignent rarement la qualité à laquelle les utilisateurs industriels sont habitués avec le drapage manuel, et certainement pas dans un processus de bureau. Dans la plupart des impressions 3D composites aujourd'hui, les résines ne sont souvent pas les mêmes que celles utilisées dans les processus traditionnels, et de nombreuses imprimantes utilisent des matériaux propriétaires qui n'offrent pas les mêmes performances élevées que les matériaux qualifiés, ce qui entraîne une non-uniformité et une variabilité de la qualité. Les pièces résultantes ont généralement une teneur en volume de fibres plus faible et une porosité plus élevée que les pièces fabriquées à la main.
"Vraiment, il n'y a pas eu de solution de bout en bout pour le faire au niveau du bureau avec les matériaux que les gens sont habitués à utiliser, jusqu'à présent", explique Fulop. « Nous combinons les avantages de l'impression 3D avec des matériaux à fibres continues qualifiés pour des applications hautes performances. »
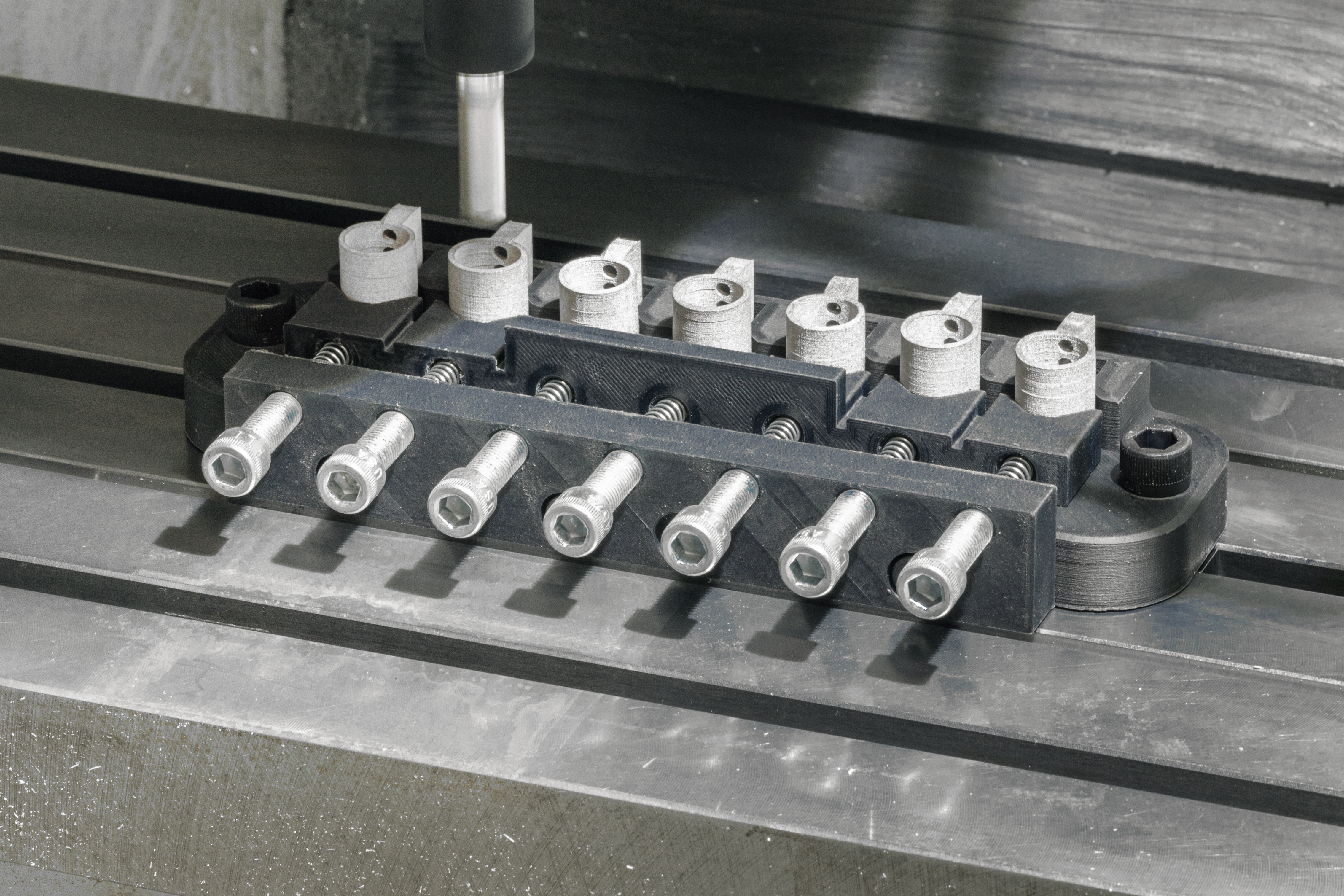
Montage CNC : En imprimant en 3D ce montage CNC en tant que composite à fibres continues sur le système Fibre, la pièce peut être rendue extrêmement rigide, permettant aux barillets de verrouillage d'être fermement maintenus en place pendant que les opérations d'usinage sont effectuées. Le ruban en fibre de carbone peut être posé de manière sélective pour ajouter de la rigidité dans les sections du luminaire qui subissent la charge la plus élevée. Les montages d'usinage doivent souvent supporter des températures extrêmes et l'utilisation d'un PEEK renforcé de fibres de carbone assure la stabilité à haute température. En imprimant en 3D sur le nouveau système Fibre, les ingénieurs d'atelier d'usinage pourront utiliser une conception de montage optimisée qui aurait autrement pris trop de temps et serait trop coûteuse à usiner. Origine | Métal de bureau
Basé sur des bandes
La nouvelle imprimante de bureau de Desktop Metal adopte la technologie de placement automatisé des fibres (AFP) pour produire des pièces composites thermoplastiques renforcées de fibres de haute qualité. La technologie s'appuie sur les mêmes lignes de fabrication qui fabriquent les bandes préimprégnées commerciales, puisant ainsi dans une chaîne d'approvisionnement existante et profitant de la croissance déjà en cours sur le marché des bandes unidirectionnelles (UD). Essentiellement, la technologie prend AFP et la réduit pour une imprimante de bureau. En fait, la société a tiré le nom de son projet d'origine du système d'extrusion cinématique Micro AFP (Make).
L'imprimante, que la société appelle Fiber, est conçue comme un système de changement d'outils modulaire à utiliser dans un bureau ou un environnement de production et est capable de fournir des gabarits de fabrication, des mâchoires, des outils et des montages de qualité industrielle, ainsi que l'utilisation finale les pièces. L'opérateur peut utiliser une tête Micro AFP pour disposer le matériau, puis le garer et passer à une tête de fabrication de filaments fondus (FFF) si nécessaire.
« Pour la première fois, les imprimantes à fibre combinent les propriétés matérielles des matériaux à fibres continues AFP hautes performances avec l'abordabilité et la vitesse d'une imprimante 3D de bureau », déclare Fulop.
La technologie utilise les mêmes bandes UD qualifiées pour les applications hautes performances. Alors que l'imprimante est capable de traiter des rubans UD avec une grande variété de systèmes de matrices en fibres et thermoplastiques, les matériaux initialement disponibles pour le système comprendront du polyamide 6 (PA6) avec des renforts en fibre de carbone et en fibre de verre, ainsi que du polyétheréthercétone (PEEK) et polyéthercétoncétone (PEKK) avec renfort en fibre de carbone. Les rubans, proposés dans un format de 3 millimètres de large, comportent généralement des fibres de remorquage 12K et sont enroulés sur des bobines exclusives. Un seul câble de 3 millimètres de large est acheminé à travers la tête jusqu'à ce qu'il descende jusqu'à la zone de pincement, où un élément chauffant sans contact obtient la température du thermoplastique au-dessus de sa température de fusion, et un rouleau de compactage applique une pression pour la consolidation de l'entrée du ruban adhésif sur le substrat en dessous. Un cutter dans la tête coupe le ruban à la fin de chaque passe. Selon Fetfatsidis, les rubans offrent une solution de meilleure qualité mais plus de 10 fois moins chère au litre qu'une bobine de filament de remorquage 1K utilisée dans certaines imprimantes 3D basées sur l'extrusion qui utilisent de la fibre continue. De plus, la qualité supérieure des rubans associée à la possibilité d'ajouter de la pression à la pièce via le processus AFP se traduit par une résistance plus élevée.
« Nous avons des bandes de très haute qualité qui sont utilisées dans les processus AFP/ATL qui ont une charge de volume de fibre très élevée - 60 % de fibre de carbone - et nous les combinons avec une matrice haute température PEEK ou PEKK », explique Fetfatsidis.
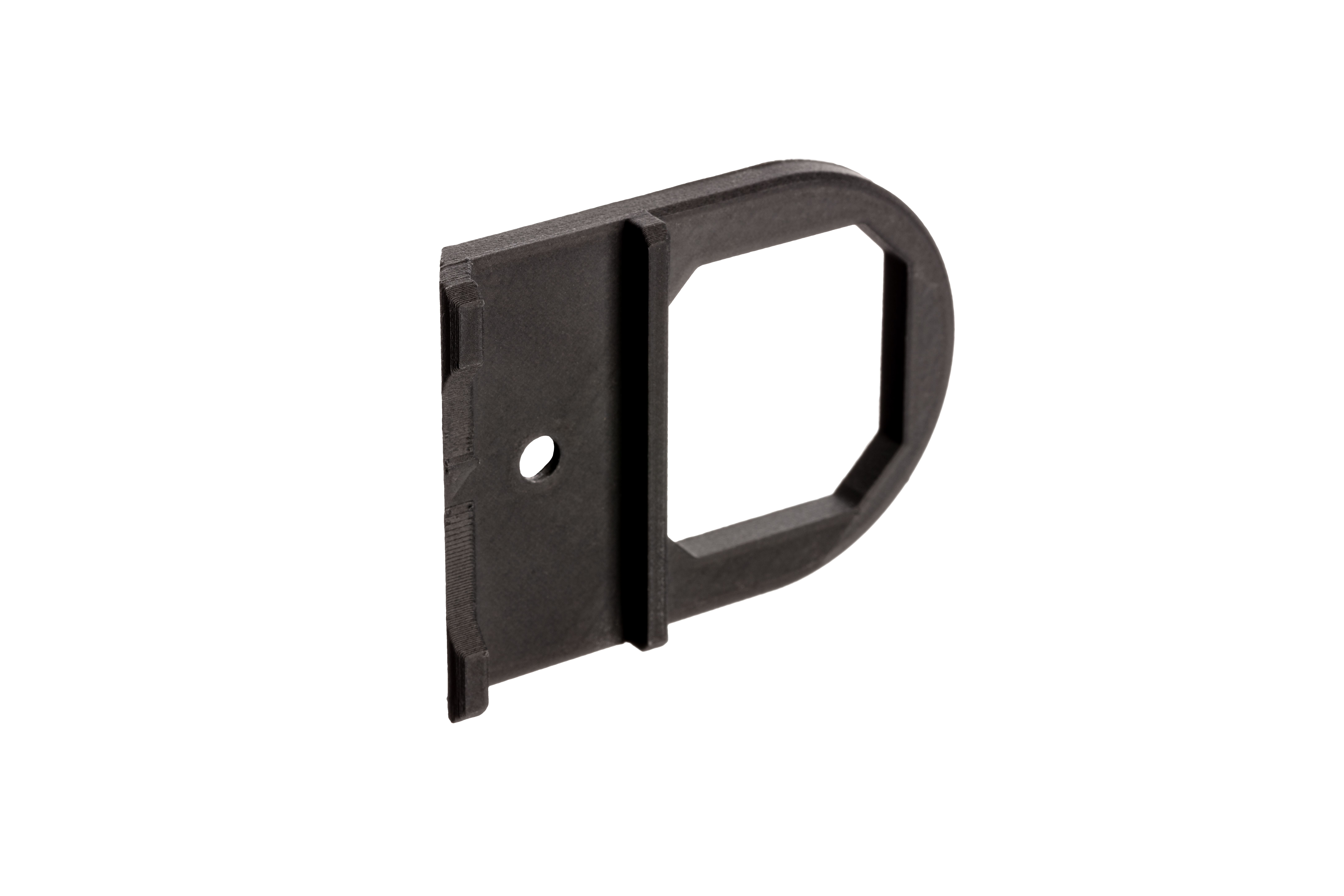
Support de caméra. Le système Fiber permet aux pièces, telles que ce support de caméra, d'être rendues plus rigides et plus légères que si elles étaient imprimées avec d'autres matériaux. Le temps d'impression rapide et les faibles coûts de matériaux permettent au concepteur d'itérer rapidement sur la conception pour obtenir une pièce optimale. Origine | Métal de bureau
On dit que les pièces créées avec le système Fiber sont plus solides que l'acier, plus légères que l'aluminium et peuvent être imprimées sur le bureau. La fibre a un volume de construction de 320 x 240 x 270 millimètres (12,6 x 9,4 x 10,6 pouces). Les avantages incluent un renforcement continu des fibres sur toute la pièce et une très faible porosité. Fetfatsidis dit que les pièces créées avec des bandes PA6 peuvent avoir moins de 5 % de porosité et que les bandes PEEK/PEKK peuvent produire des pièces avec moins de 1 % de porosité. L'opérateur a la capacité de diriger des remorques pour obtenir des formes complexes ou des conditions de charge particulières. Et parce que les résines sont des thermoplastiques, le besoin d'un durcissement à l'autoclave est éliminé, ainsi que le besoin de stocker le matériau dans un congélateur.
"C'est vraiment le premier produit dans le domaine de l'impression 3D qui combine la fibre de carbone continue avec le PEEK et le PEKK dans un ordinateur de bureau", déclare Fulop.
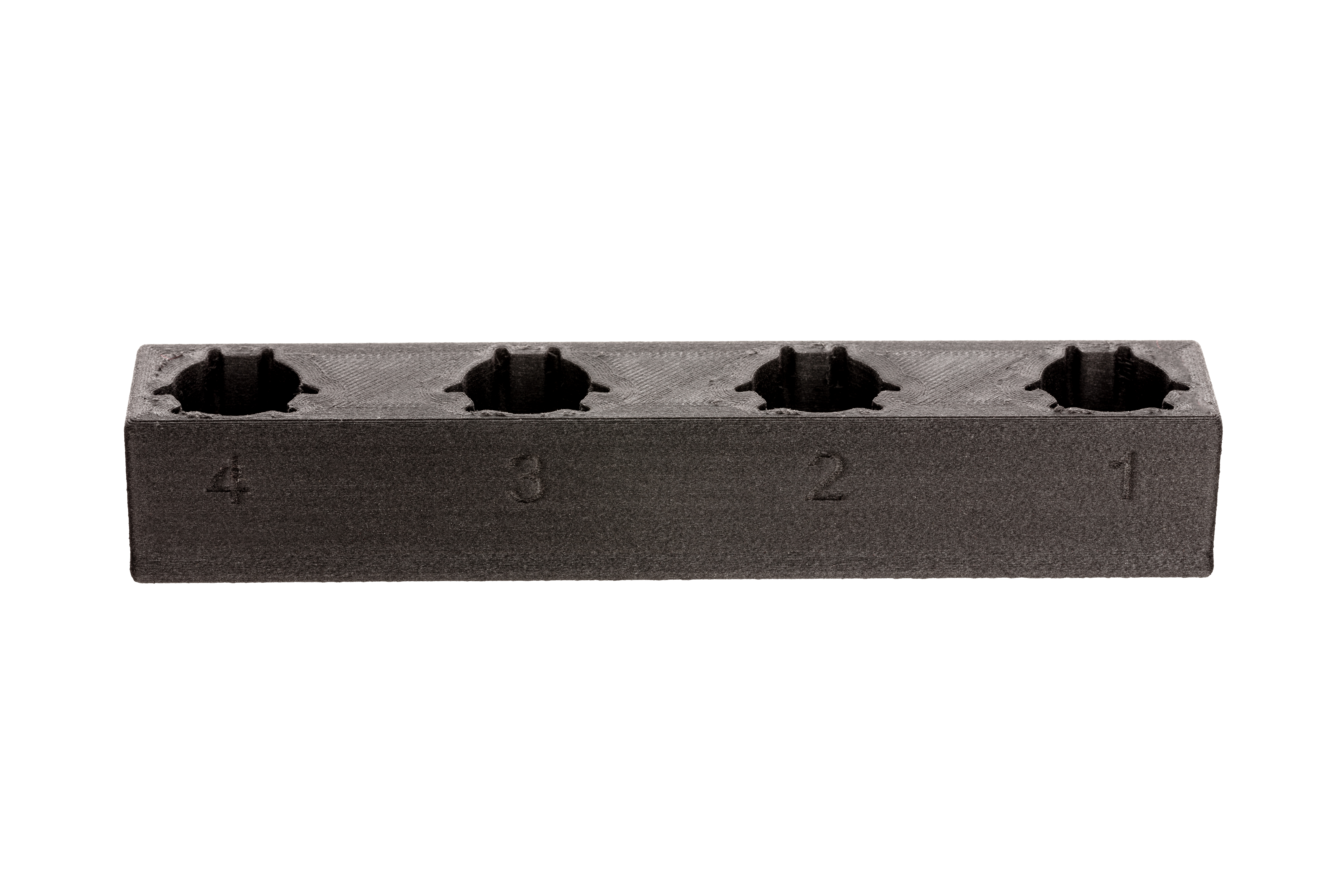
Support de charge de l'enveloppe. Les supports de charge Shroud sont utilisés pour localiser les composants moulés par injection de métal (MIM) afin qu'un effecteur final robotique puisse prélever une pièce avant que les dimensions critiques ne soient usinées. Ce luminaire subit une usure considérable car il est constamment mis à l'intérieur et à l'extérieur du luminaire. L'impression 3D du support de charge du carénage sur le système Fiber permet aux ingénieurs d'atelier d'usinage de réduire le délai de production du dispositif de quelques semaines à quelques heures, tout en réduisant les coûts de fabrication de 95 %. Origine | Métal de bureau
Accessible à tous
Bien que la solution de Desktop Metal présente plusieurs avantages, notamment la possibilité de créer des pièces d'utilisation finale et l'utilisation de thermoplastiques, l'un des aspects les plus intéressants du système Fibre est sans doute son prix abordable. La plupart des systèmes qui utilisent des rubans thermoplastiques à fibres continues pour la fabrication automatisée de pièces composites sont des systèmes à plusieurs millions de dollars. Le système Fibre de Desktop Metal est disponible en deux modèles via un service d'abonnement. Fiber HT est conçu pour produire des pièces avec des composites continus avec une porosité <1% et jusqu'à 60% de charge de fibre continue avec une matrice avancée, y compris PEEK et PEKK. Il peut fabriquer des pièces ignifuges UL 94-V0 pour résister à des températures élevées jusqu'à 250°C, en plus des pièces conformes ESD. Le modèle Fibre HT commence à un prix de lancement de 5 495 $ par an. Pendant ce temps, Fiber LT commence à 3 495 $ par an, offrant un moyen abordable de produire des pièces à haute résistance conformes ESD et non marquantes en utilisant une fibre continue avec <5% de porosité avec des thermoplastiques PA6.
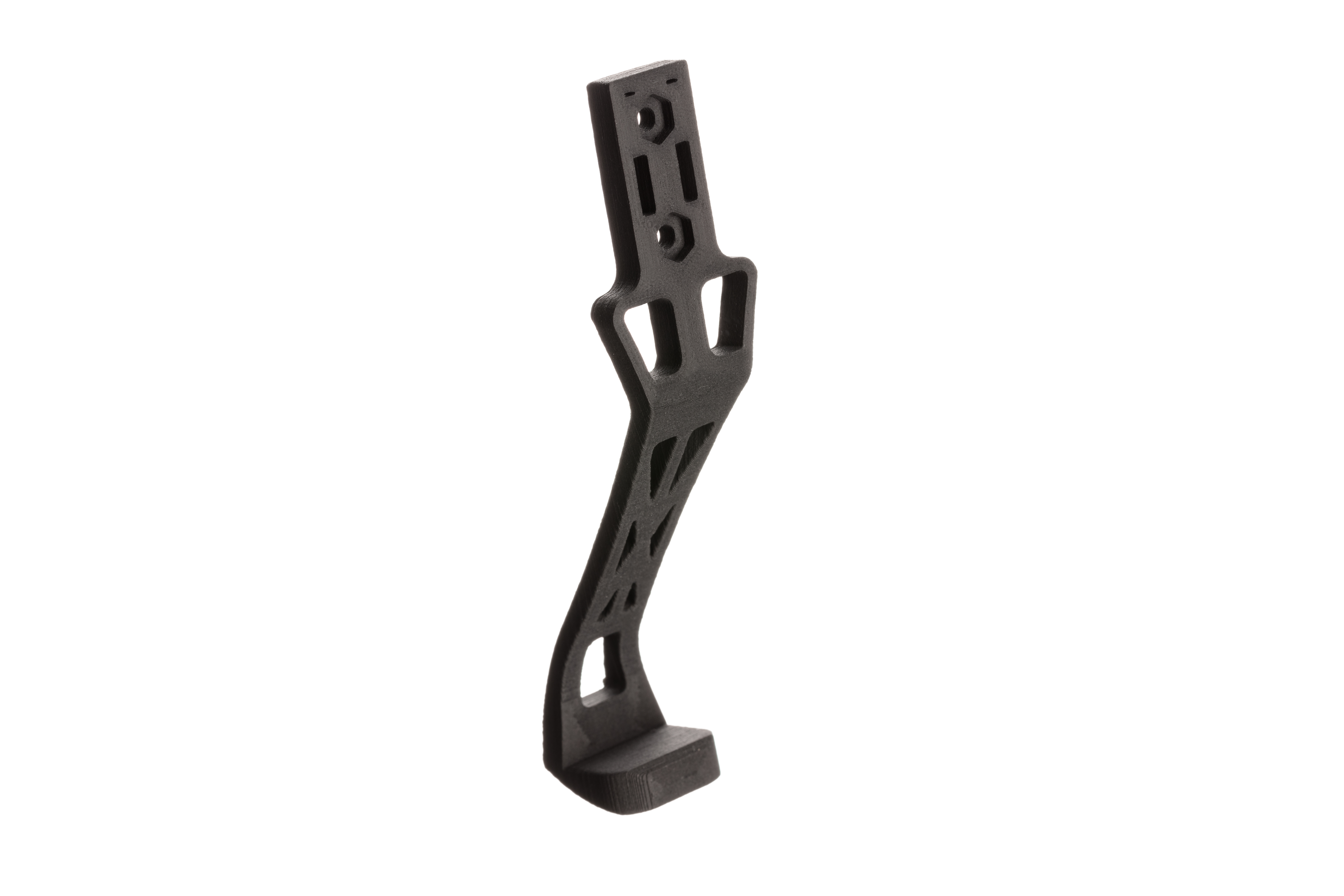
effecteur final ESD. Les effecteurs terminaux sont utilisés pendant le processus de fabrication des cartes de circuits imprimés (PCB). Cette pièce a été fabriquée avec le PA6 renforcé de fibres de carbone anti-décharge électrostatique (ESD) du système Fibre, pour aider à protéger les circuits imprimés contre les décharges électrostatiques dommageables tout au long du processus d'assemblage. Imprimés sous forme de composite de fibre de carbone continue, les effecteurs terminaux sont extrêmement rigides, légers et capables de résister à la charge du processus d'assemblage du PCB. Origine | Métal de bureau
"Nous voulons que les gens puissent acheter le système, l'avoir sur leur bureau à la maison ou au bureau et fabriquer des pièces en PEEK avec de la fibre continue", explique Fetfatsidis.
« Pour quelques milliers de dollars, vous pouvez commencer à fabriquer des pièces composites hautes performances à partir de la même technologie de ruban que celle qui est maintenant utilisée dans les pièces fabriquées par AFP très haut de gamme », ajoute Fulop.
Alors que le rôle de l'impression 3D dans la fabrication continue de croître, les concepteurs et les ingénieurs ont besoin de solutions permettant d'accéder à une large gamme de matériaux. Le système Fiber est un grand pas en avant pour mettre les matériaux composites hautes performances à la portée de tous ceux qui souhaitent profiter de la légèreté, de la résistance et de la rigidité qu'offrent les composites. Desktop Metal présentera son système d'impression 3D de bureau à fibre continue Fibre à l'exposition et conférence sur la fabrication additive Formnext 2019, du 19 au 22 novembre à Francfort, en Allemagne.
Résine
- Les 3 étapes de base de l'impression 3D
- Pourquoi l'impression 3D est à la hausse
- Scalmalloy :le dernier matériau hautes performances pour l'impression 3D sur métal
- Évolution du marché du matériel d'impression 3D en 2020
- L'évolution de la technologie d'impression 3D de HP :du polymère au métal AM
- Les performances de la fibre de verre
- La fabrication continue de fibres brouille la frontière entre l'impression 3D et l'AFP
- Impression 3D de composites avec fibre continue
- Quels sont les avantages de l'impression 3D pour les fabricants de métaux ?