Composites imprimés en 3D avec 60 % de fibres, moins de 1 % de vides
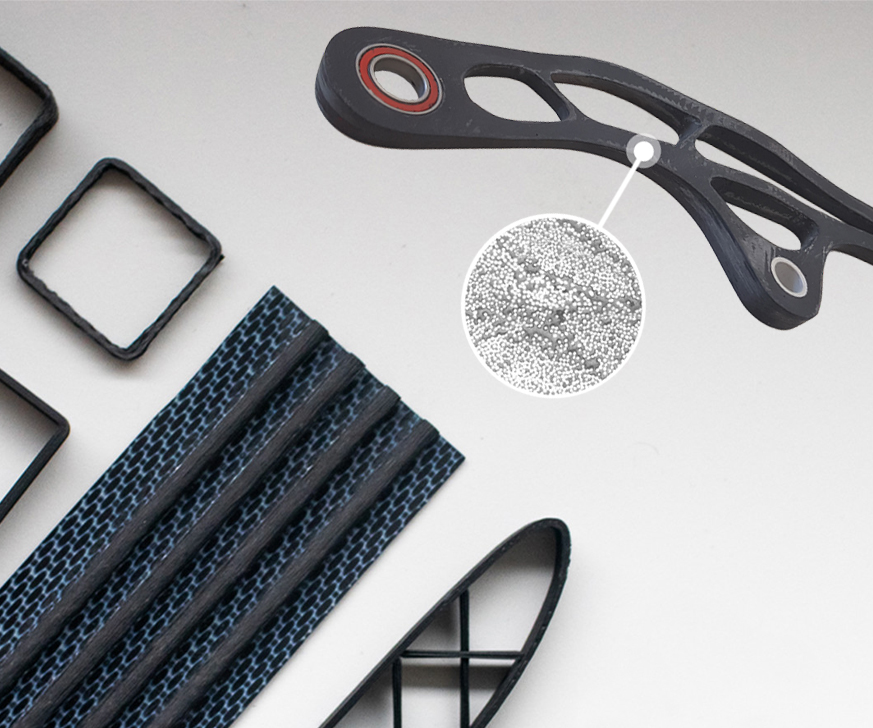
« Notre objectif principal est de produire des composites structurels à fibres continues pour l'industrie », déclare Giovanni Cavolina, co-fondateur de 9T Labs (Zurich, Suisse). « Si vous parlez à des personnes qui fabriquent des pièces en CFRP (polymère renforcé de fibres de carbone), la plupart ne croient pas qu'il soit possible d'obtenir une teneur en vide très faible ou une bonne résistance au cisaillement interlaminaire (ILSS) entre les couches avec une impression 3D en fibre continue. » 9T Labs, cependant, a développé un post-processus breveté qui élimine les vides. « Nous pouvons désormais imprimer en 3D des composites à fibres continues avec une grande adhérence entre les couches et une teneur en vide inférieure à 1 %, ce qui est en concurrence avec les composites fabriqués de manière conventionnelle. »
Début à l'ETH Zurich
9T Labs a commencé avec un projet de recherche dans le Laboratoire de matériaux composites et structures adaptatives (CMAS) de l'Ecole polytechnique fédérale de Zurich (ETH Zurich). Les co-fondateurs de Cavolina et 9T Labs Martin Eichenhofer et Chester Houwink avait développé une tête d'impression composite, "que nous avons montée sur un bras robotique et fabriqué des noyaux en treillis pour des structures sandwich ultra-légères, ciblées pour les applications aérospatiales", explique Cavolina.
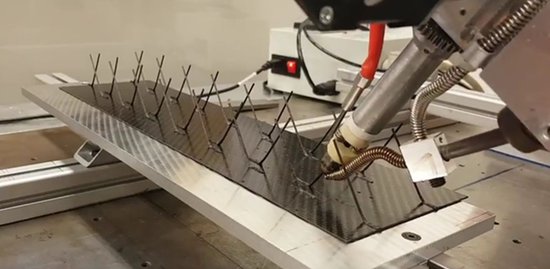
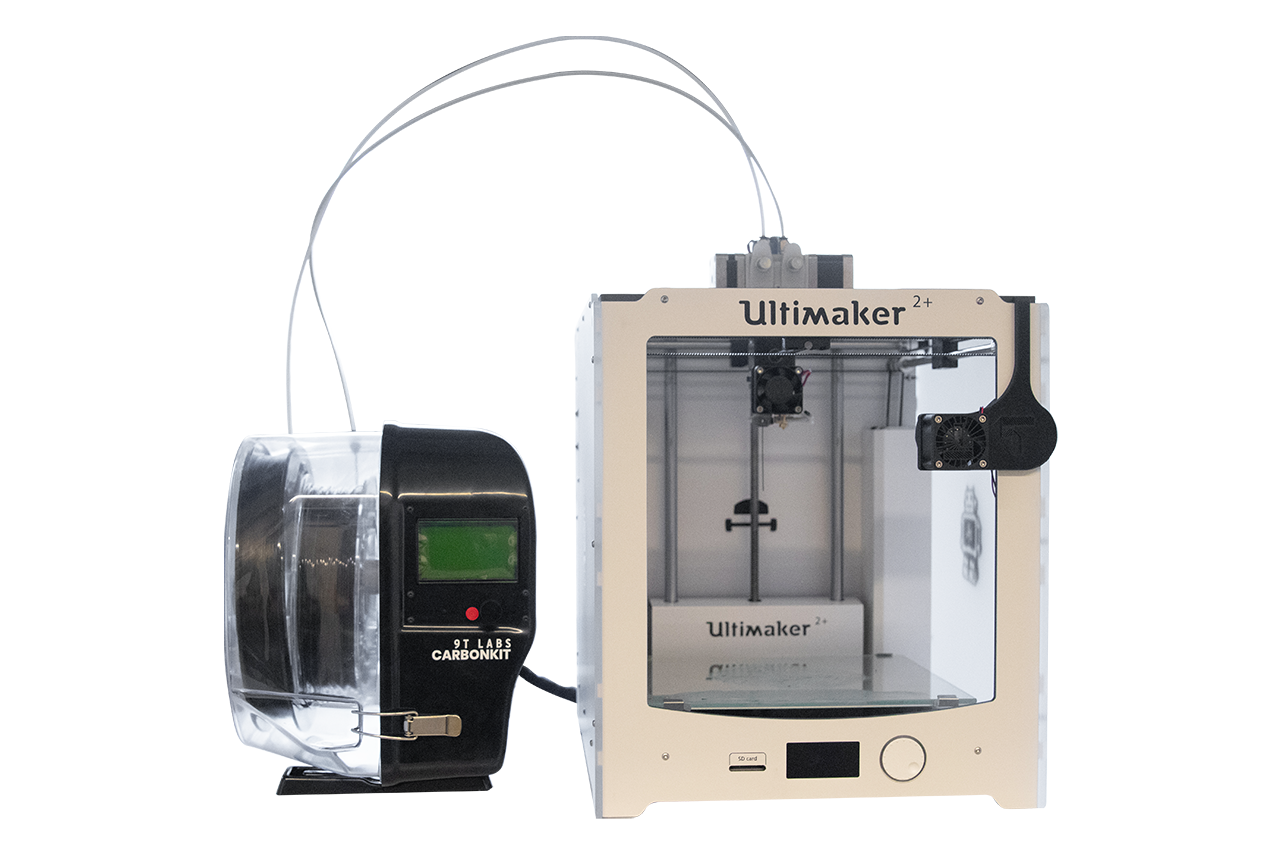
CarbonKit était un produit à diffusion limitée qui permettait aux imprimantes FDM standard d'utiliser de la fibre de carbone continue, mais n'était pas encore la bonne solution pour produire des pièces structurelles en CFRP à un prix compétitif. SOURCE | Laboratoires 9T.
Kit Carbone
Ainsi, 9T Labs a été créé début 2018 pour prouver le concept d'impression 3D de stratifiés CFRP monolithiques qui pourraient répondre aux exigences des clients potentiels. « Notre prochaine étape était le CarbonKit », explique Cavolina. C'est le produit présenté dans CW L'article de mars 2019 « Passer l'impression 3D à fibre continue en production ». Le CarbonKit transforme les imprimantes 3D Ultimaker ou Prusa en un système capable d'imprimer avec de la fibre de carbone continue. « Cela vous permet d'utiliser vos imprimantes existantes en combinaison avec notre tête d'impression, nos filaments et notre logiciel pour placer des fibres continues, selon le cas de charge, avec une teneur en volume de 50 % de fibre de carbone - et non 30 %, ce qui était la norme dans l'impression 3D CFRP. », ajoute-t-il.
Cavolina explique que même si l'intérêt pour ce produit était assez important, « nous n'avons fourni que 25 clients. Nous avons gardé ce produit limité parce que nous nous sommes rendu compte qu'avec un seul processus FDM [fused deposition modelling] en une seule étape, il n'est pas possible de réaliser des pièces d'utilisation finale structurelles pour des applications aérospatiales industrielles qui sont également compétitives par rapport aux technologies actuelles. P>
Cependant, grâce au CarbonKit, 9T Labs a établi de précieuses relations avec ses clients. « Nous avons pu découvrir ce que les entreprises attendaient et avaient besoin, même si ces pièces n'étaient en fait pas possibles à produire avec le CarbonKit », explique-t-il. « La consolidation in situ est en effet possible avec le FDM, mais cela nécessiterait des machines beaucoup plus complexes et d'un coût prohibitif. Nous avons donc produit un processus en 2 étapes avec une consolidation post-impression. »
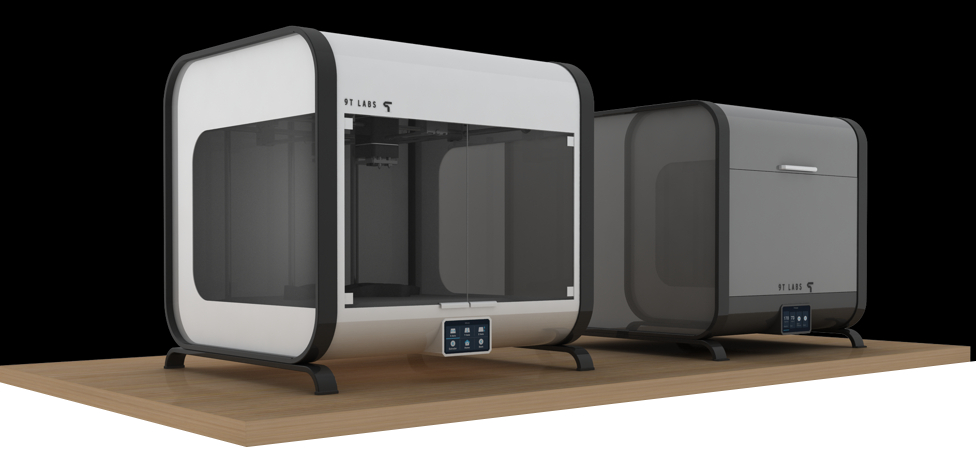
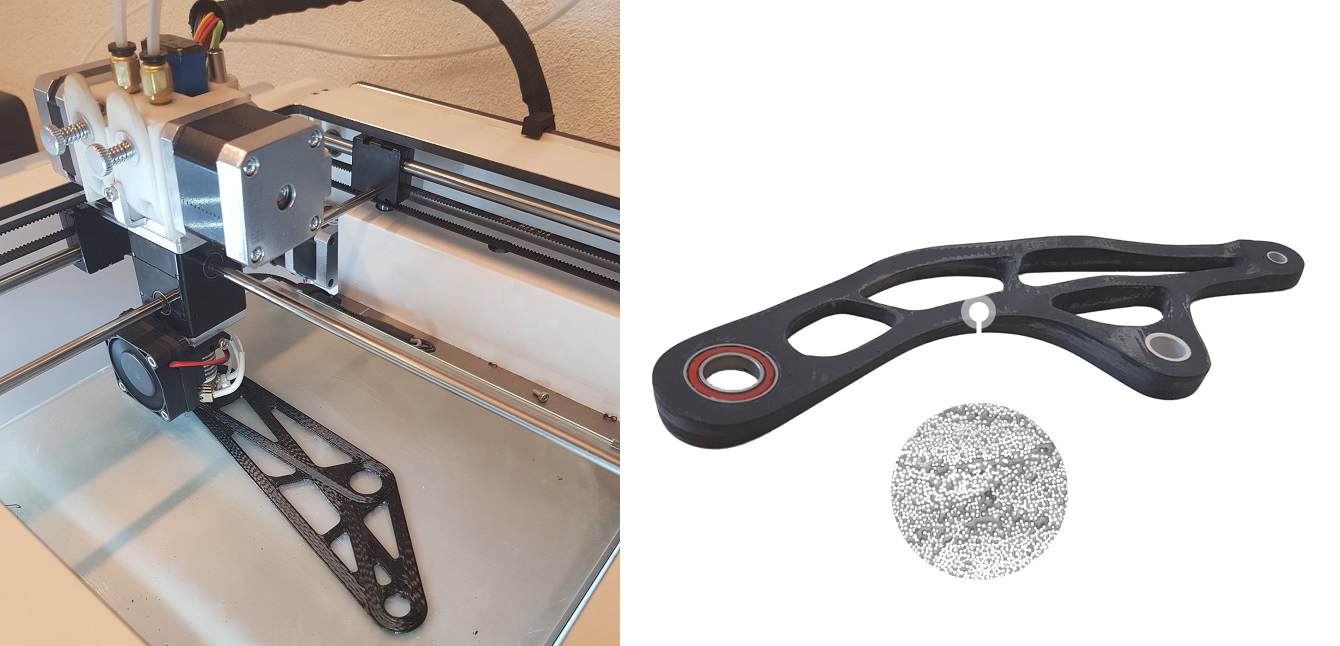
Avec Red Series, 9T Labs a réalisé des structures CFRP imprimées en 3D avec> 50 % de volume de fibres et <1 % de vides à un coût abordable par rapport aux méthodes de production de composites actuelles. SOURCE | Laboratoires 9T.
Série rouge, processus en 2 étapes
Cela nous amène là où 9T Labs est aujourd'hui. « Nous commercialisons la série rouge, qui comprend deux unités :une unité d'impression FDM classique avec une tête d'impression brevetée et une unité de fusion adjacente pour le post-traitement », explique Cavolina. « Nous n'obtenons pas une consolidation in situ complète lors de l'impression, mais au lieu de cela, nous imprimons puis consolidons dans un deuxième processus. Essentiellement, nous imprimons une préforme qui est placée dans l'unité de fusion pour la post-consolidation en utilisant une température et une pression élevées pour atteindre plus de 50 pour cent de volume de fibres avec moins de 1 pour cent de vides. Ce processus en 2 étapes permet d'obtenir une qualité aérospatiale à un coût abordable. »
La Série Rouge utilise pour l'instant des matériaux thermoplastiques. « Nous imprimons de la fibre de carbone avec du PEI, du PEKK, du PA (nylon) et avons également de l'expérience avec le PP », explique Cavolina. La Série Rouge est-elle un système à matériaux ouverts ? « La seule façon d'être compétitif en termes de coûts est d'utiliser des matériaux existants avec un nouveau processus de fabrication », explique-t-il. « Si vous créez votre propre matériau à partir de zéro, vous excluez de pouvoir vous lancer dans la fabrication en série. Pour des raisons de sécurité et de fiabilité de la chaîne d'approvisionnement, les fabricants de séries ne dépendront pas d'une petite entreprise pour leurs matériaux. Ainsi, nous laissons nos clients utiliser leur approvisionnement existant en matériaux, en nous assurant que les matériaux fonctionnent dans notre système. » Il explique que 9T Labs teste les matériaux pour s'assurer que la matière première répond à certaines exigences et détermine les meilleurs paramètres pour l'impression.
Et les logiciels ouverts ? « Notre logiciel d'impression est combiné à un logiciel de simulation structurelle », explique Cavolina. « C'est formidable en tant qu'ingénieur de placer des fibres là où elles sont nécessaires, mais comment pouvez-vous être sûr que c'est bien là où elles doivent être placées ? Notre logiciel donne la liberté de concevoir puis de recouper avec une simulation structurelle. L'autre sens consiste à définir un drapage orienté fibre dans une simulation structurelle, puis à le convertir en chemin d'impression dans notre logiciel. Nous utilisons un partenaire existant, éprouvé et bien connu pour la FEA qui fonctionne en arrière-plan. Vous pouvez également concevoir directement une pièce en CAO, puis télécharger ce fichier dans notre programme. Là, vous décidez où vous voulez la fibre de carbone et où le polymère pur est suffisant. »
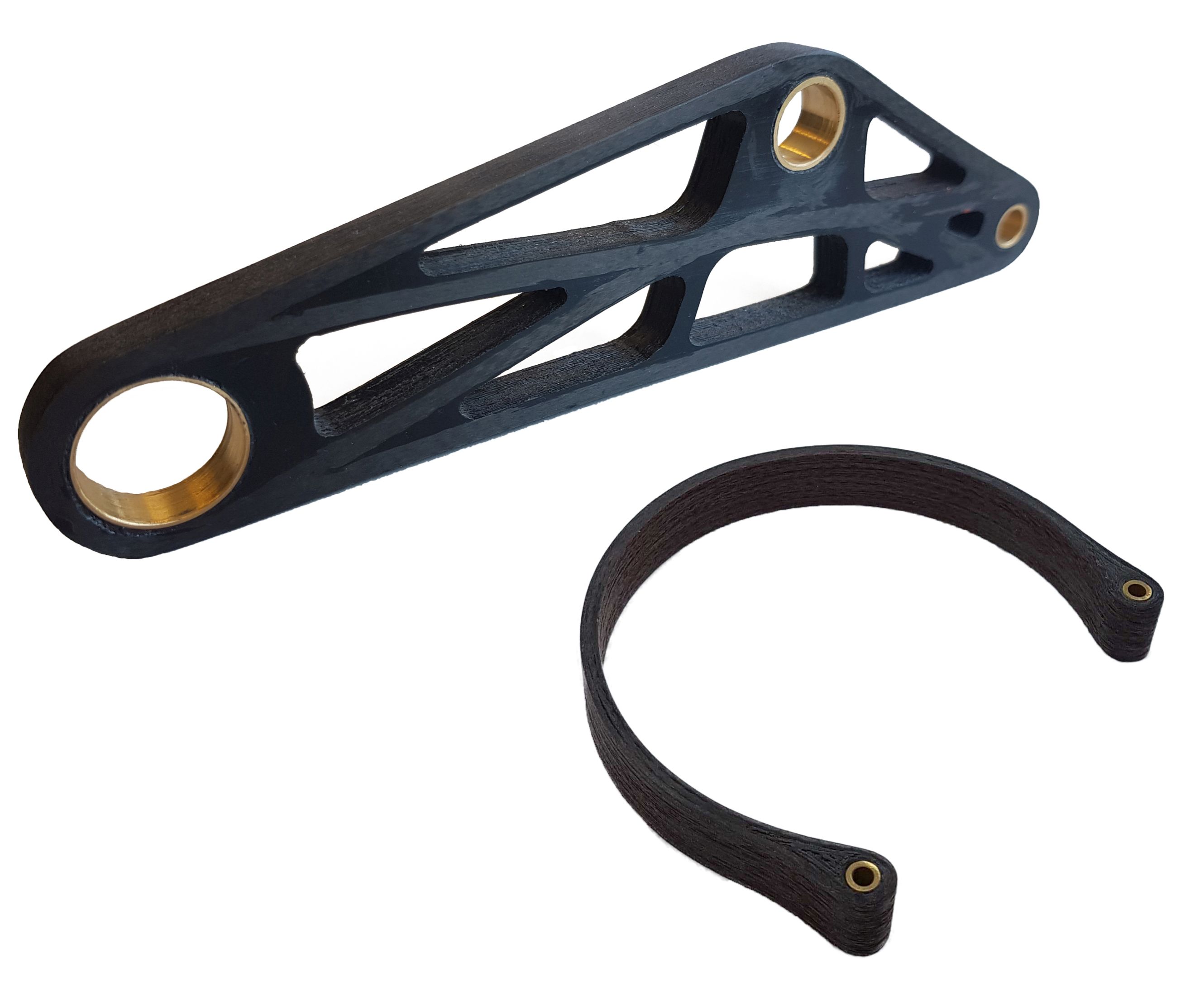
Ce support et culbuteur en PRFC pour les applications non aérospatiales répondent en fait aux exigences des stratifiés aérospatiaux et comportent plus de 40 plis - chaque pli avec une orientation de fibre différente pour exploiter l'anisotropie et optimiser les pièces structurelles qui n'étaient pas possibles auparavant. SOURCE | Laboratoires 9T.
Applications
9T Labs s'intéresse à l'aérospatiale (intérieurs, pour l'instant), à l'automatisation biomédicale et industrielle (par exemple, machines d'emballage), ainsi qu'aux loisirs/luxe (par exemple, sports motorisés, chaussures de sport, lunettes). Ce dernier marché, dit Cavolina, "est celui où vous avez besoin de composites structuraux, mais les exigences ne sont pas aussi strictes que dans l'aérospatiale". Il cite le culbuteur montré ci-dessus. « Il s'agit d'un support pour une structure non aérospatiale qui représente une application structurelle que vous pouvez produire de manière optimisée en utilisant notre technologie », explique-t-il. « Il provient d'une pièce en aluminium dont la topologie a été optimisée pour gagner du poids en orientant les fibres de carbone en fonction du cas de charge. Vous pouvez réduire les coûts car vous pouvez réduire la quantité de fibre de carbone utilisée par rapport à d'autres processus composites. Vous ne pouvez pas le faire par d'autres moyens car il n'est pas possible avec d'autres méthodes d'orienter chaque fibre comme vous le souhaitez en haute résolution. »
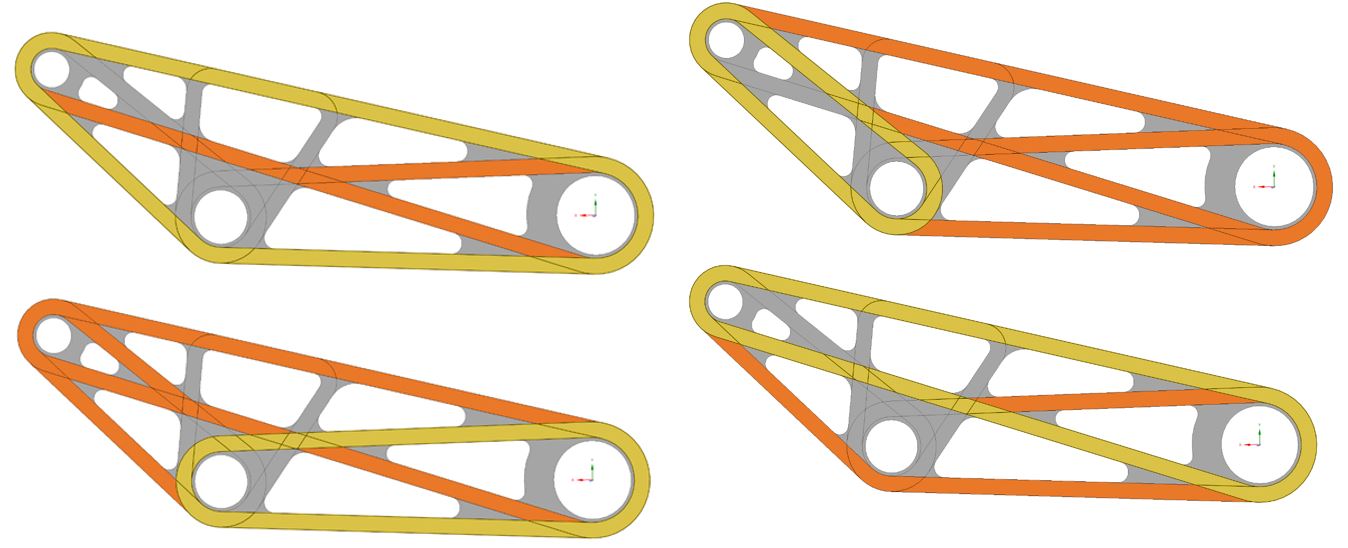
Quatre couches de fibre de carbone continues différentes sont alternées sur toute l'épaisseur du support en CFRP imprimé avec la série rouge 9T Labs. SOURCE | Laboratoires 9T.
Cavolina note que ce culbuteur comprend plus de 40 couches de fibres et de polymères, « et nous pouvons avoir des orientations de fibres différentes dans chaque couche. Nous avons essayé quatre layups différents, non limités au quasi-isotrope. Cette liberté nous permet d'exploiter l'anisotropie des composites pour optimiser davantage la structure d'utilisation finale. Il ne serait pas possible de le faire avec les autres méthodes de fabrication actuelles. »
Il souligne également que l'impression 3D CFRP est un processus automatisé par rapport au drapage manuel. «Notre technologie réduit considérablement le travail manuel grâce à la pose automatisée», explique Cavolina. "Avec notre technologie, il vous suffit d'imprimer, de consolider et le tour est joué."
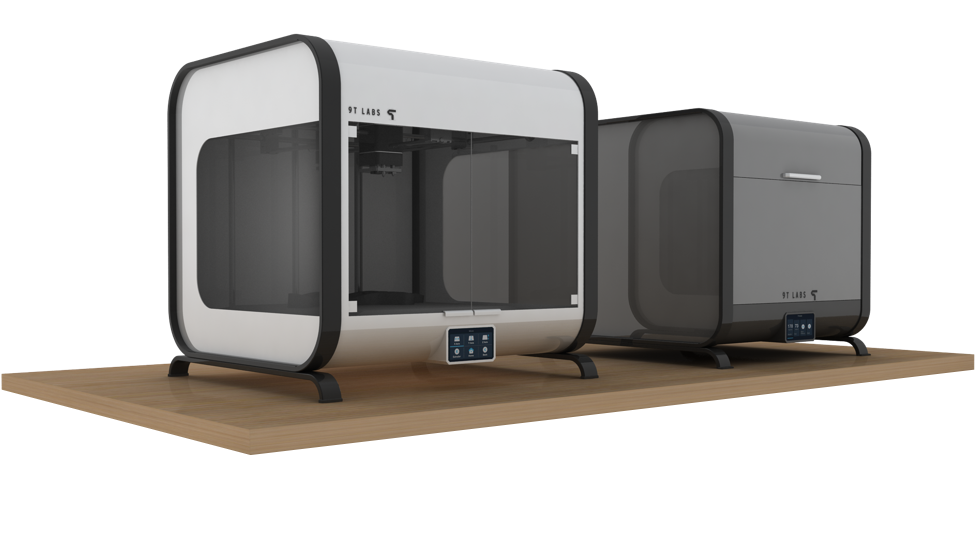
La série rouge imprime des préformes CFRP plus petites, complexes et monolithiques qui sont ensuite consolidées dans une deuxième étape pour une production industrielle en série évolutive. SOURCE | Laboratoires 9T.
Taille d'impression, vitesse et lancement complet de la série rouge
La série rouge est destinée aux pièces monolithiques plus petites pour la fabrication en série dans une zone d'impression de 350 millimètres sur 300 millimètres. « ici, nous voyons actuellement la plus haute valeur ajoutée pour nos clients », explique Cavolina.
Et la vitesse d'impression ? « Nous parlons de manière très concrète de la production au cours des 1 à 2 prochaines années de 4 000 à 8 000 pièces par an pour différents clients, grâce aux unités jumelées de la série rouge », explique Cavolina. « Parce que nous avons découplé la production de préformes complexes et détaillées de la consolidation, il est désormais possible d'augmenter rapidement le volume de production. »
«Nous avons passé beaucoup de temps à analyser la structure des coûts de notre processus, y compris les coûts d'équipement, de main-d'œuvre et de matériaux», répond-il. « Nous avons une structure de coûts d'équipement abordable et avons automatisé le processus de préformage. Nous utilisons les matériaux les plus abordables et les plus efficaces, puis réduisons la quantité de matériau requise en orientant les fibres selon le cas de charge et en utilisant l'optimisation structurelle. Nous travaillons en étroite collaboration avec nos partenaires dans la simulation structurelle et de processus et voyons qu'elle continuera de croître dans le cadre de l'objectif de production consistant à utiliser la technologie de jumeau numérique pour permettre le plug and play avec les lignes et les cellules de production 4.0. »
La série rouge sera lancée en 2020. « Maintenant, nous l'évaluons à travers nos programmes de collaboration avec des partenaires de production. Nous certifions les pièces et les processus avec eux, ils ont donc réservé les premiers emplacements pour les machines de la série rouge et les utiliseront pour fabriquer leurs produits d'utilisation finale. »
Résine
- Renforcer les pièces imprimées en 3D avec un routage de fibre efficace :1ère partie
- Partie de la semaine — Trépied imprimé en 3D avec pieds renforcés en fibre de carbone continue
- Recyclage :composites thermoplastiques renforcés de fibres continues avec polycarbonate recyclé
- TxV Aero Composites est conforme aux normes AS9100
- Hexcel s'associe à Lavoisier Composites, Arkema
- Recyclage des composites — plus d'excuses
- Covestro lance les thermoplastiques à fibres continues Maezio
- Fabrication continue de fibres (CFM) avec des composites moi
- Impression 3D de composites avec fibre continue