Capteurs diélectriques CC pour la production de composites industriels
Alors que les fabricants cherchent simultanément à réduire les coûts et à augmenter le taux de production de pièces composites, la capacité de voir l'intérieur des processus de moulage en temps réel et de surveiller le flux de résine, la viscosité, la température, la pression et la Tg/l'état de durcissement devient un différenciateur. Synthesites (Uccle, Belgique) a développé cette capacité. Sur la base des résultats rapportés par le Centre aérospatial allemand (DLR, Stade) et le Centre national des composites (NCC, Bristol, Royaume-Uni), cette technologie a le potentiel de réduire les temps de cycle jusqu'à 50 %, avec des décisions de durcissement basées sur la Tg et le degré. de durcissement par résine et pièce par rapport aux périodes de temps conservatrices basées sur des études de matériaux génériques. Il s'agit en fait d'un progrès vers la production de Composites 4.0, utilisant les données des capteurs pour contrôler les processus et les équipements, et également pour améliorer la simulation et la conception.
J'ai d'abord fait un reportage sur Synthesites via le projet OPTO-Light (voir « thermosets surmoulés thermoplastiques , cycle de 2 minutes, une cellule »). En fait, la possibilité de joindre des thermoplastiques aux thermodurcissables en OPTO-Light sans les surfaces soumises à l'ablation laser ont été rendues possibles grâce à l'utilisation de capteurs dans le moule pour la pression, la température, la résistivité au courant continu (DCR) et l'analyse diélectrique (DEA). Les capteurs DCR ont été fournis par Synthesites et ceux pour DEA ont été fournis par Netzsch (Selb, Allemagne). Les deux sont des capteurs diélectriques qui mesurent les propriétés électriques de la résine. Je vais discuter de l'histoire et des différences de ces technologies ci-dessous.
La technologie que Synthesites a développée avec une gamme de clients commerciaux est impressionnante, y compris la production industrielle de pales d'éoliennes et les ailes infusées de résine pour la série C, maintenant Airbus 220. Elle a également été démontrée pour une gamme de matériaux et de procédés, y compris l'autoclave -préimprégné durci, infusion de résine et moulage par transfert de résine haute pression (HP-RTM).

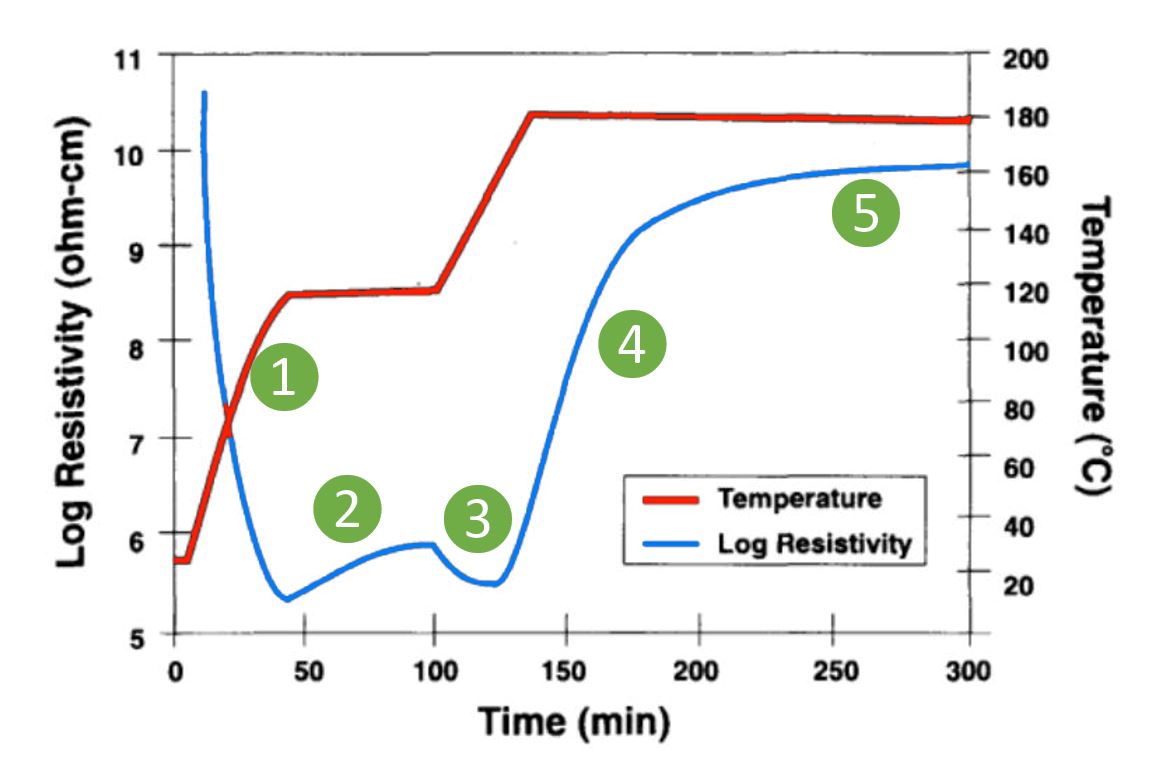
- La diminution initiale de la résistivité reflète la diminution de la viscosité de la résine pendant la rampe jusqu'à ≈ 120 °C.
- Pendant ce séjour à 120 °C, la résistivité augmente à mesure que la viscosité de la résine augmente en raison de la réaction de la résine et de la perte de substances volatiles.
- La résistivité diminue à nouveau et atteint un minimum lorsque la résine est chauffée à 177 °C.
- La résistivité augmente ensuite rapidement à mesure que la réaction de guérison progresse rapidement.
- L'augmentation de la résistivité ralentit au fur et à mesure que la réaction de durcissement ralentit, atteignant une pente proche de zéro au bout de 300 minutes lorsque la réaction de durcissement est presque terminée.
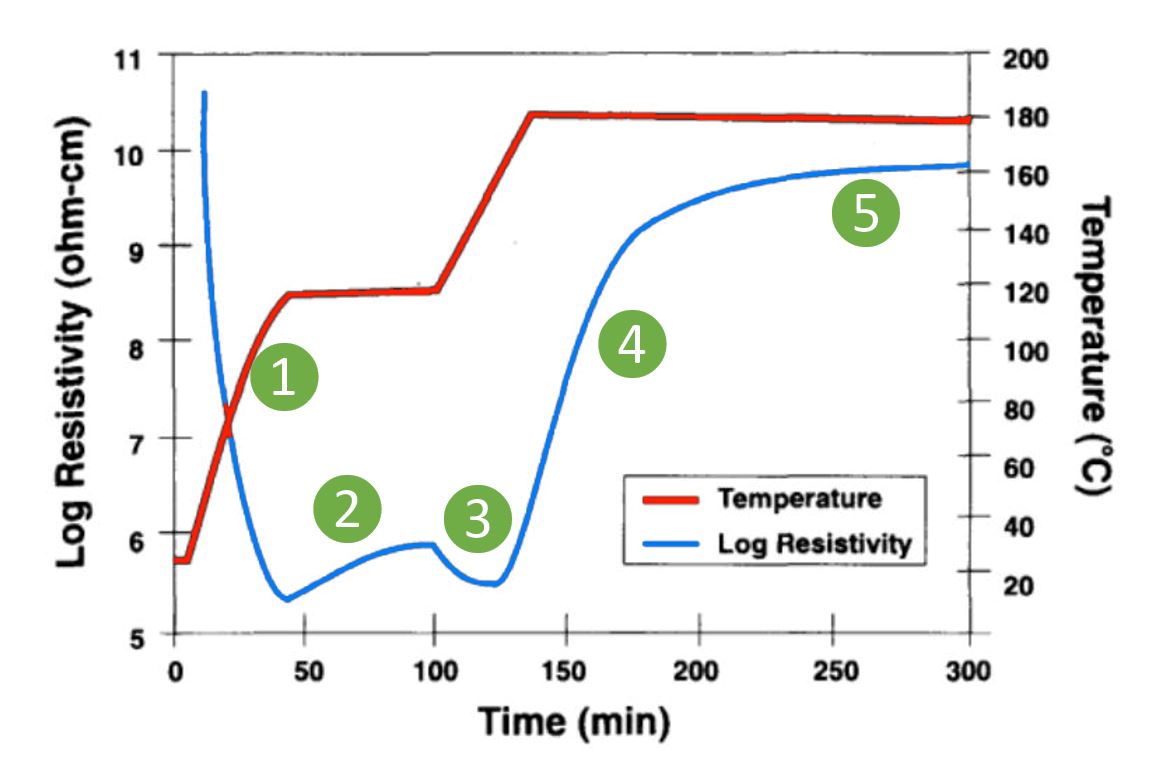
SOURCE | Caractérisation non destructive des matériaux VIII édité par Robert E. Green, p. 385.
La conductivité ionique est inversement liée à la viscosité de la résine avant gélification et à la rigidité après gélification (mobilité ionique élevée, faible viscosité de la résine et faible rigidité). L'inverse de la conductivité ionique, la résistivité, est donc directement lié aux changements de viscosité/rigidité dans la résine de la matrice.
Il a été démontré que l'augmentation de la résistivité est corrélée à l'augmentation de la Tg. C'est la base de la résistivité au courant continu (DCR), qui n'est qu'un DEA utilisant le courant continu (DC), et la description initialement donnée au procédé développé par Synthesites.
Comme expliqué ci-dessus, cette technique d'utilisation de la tension continue pour le DEA est basée sur des corrélations entre la résistivité et l'état de durcissement. Ceux-ci ont été rapportés en 1962 par R.W. Warfield dans "Properties of Crosslinked Polymers as Evidenced by Electrical Resistivity Measurements", Makromoleculare Chemistry, Vol. 58. (Voir en bas les références utilisées dans cette section.)
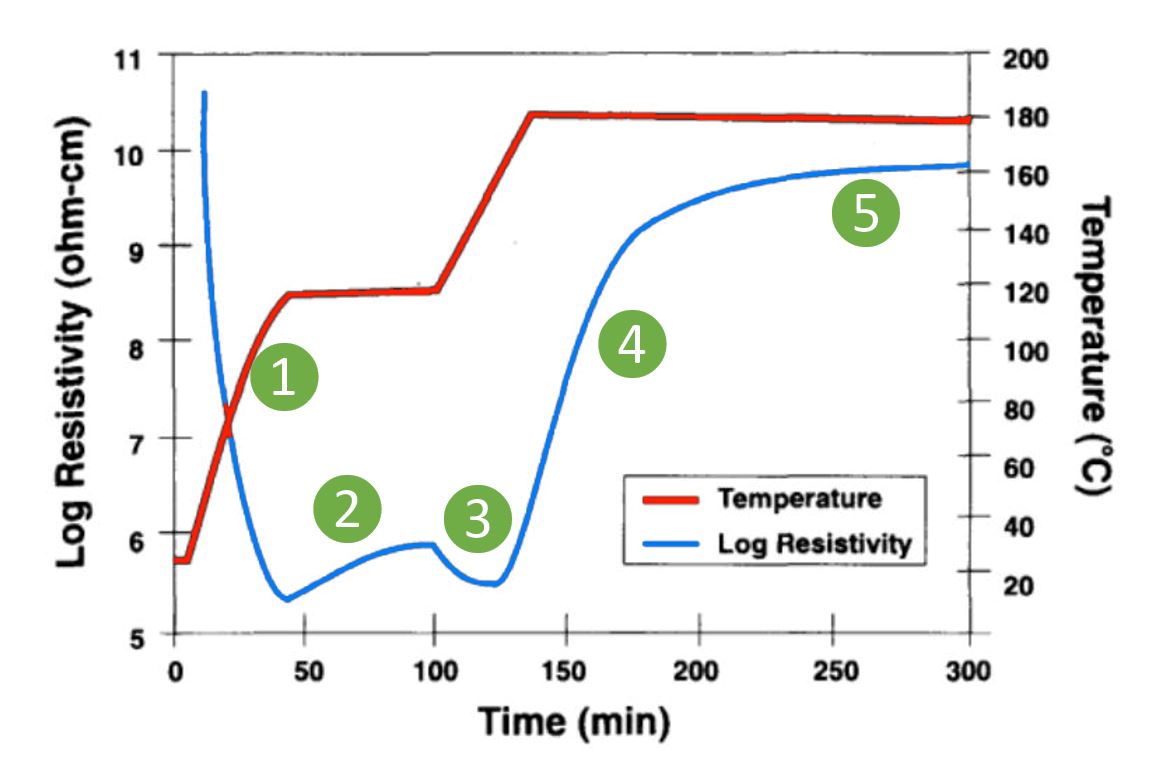
Historique des capteurs DEA et AC vs DC
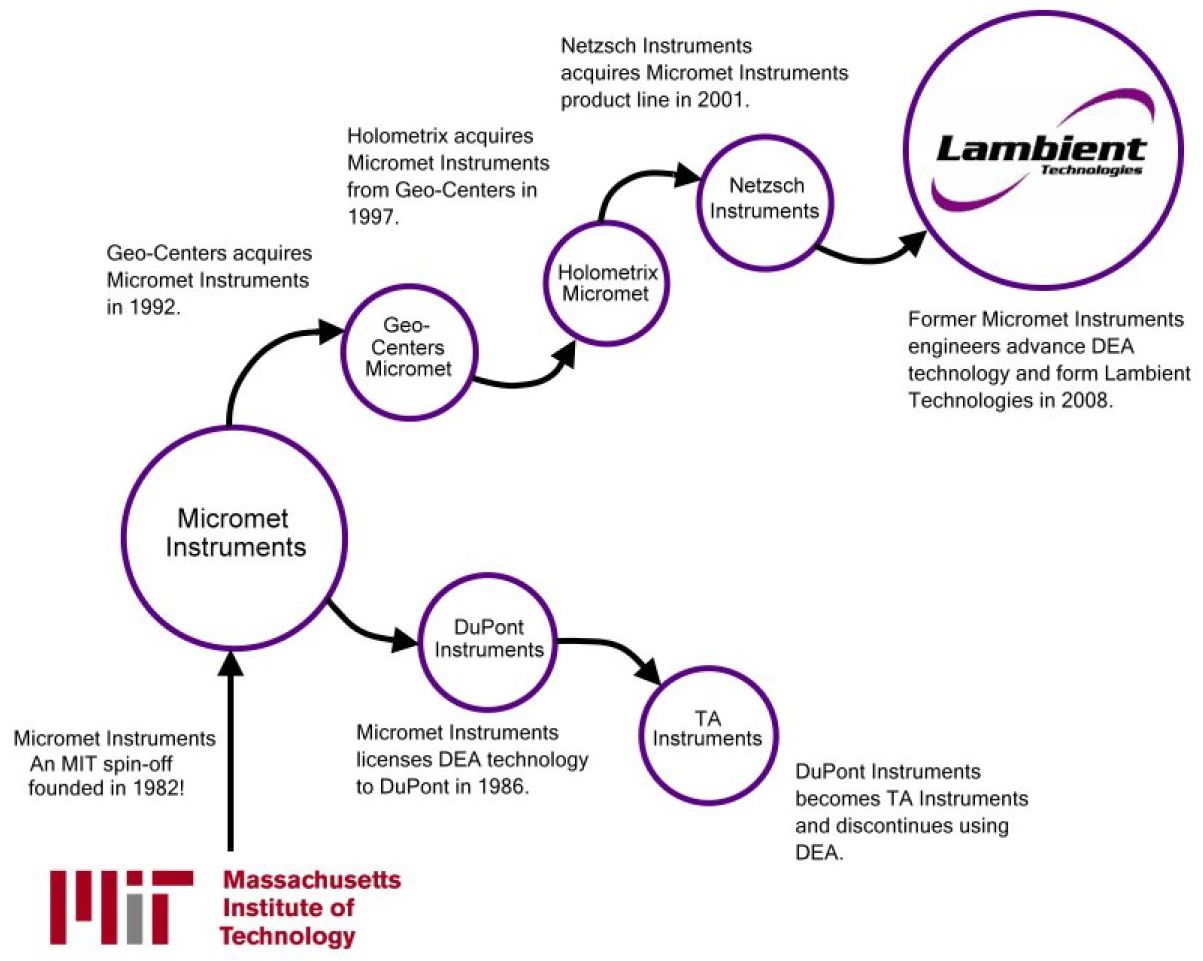
« L'idée de la surveillance de la guérison est assez ancienne, explique le Dr Nikos Pantelelis, directeur de Synthesites. « Dans les années 1980, la méthode de détection diélectrique était considérée comme plus mature que d'autres, comme les fibres optiques. Le MIT (Massachusetts Institute of Technology) a travaillé dessus et a essayé de le mettre en œuvre en production. Cette technologie est ce que Netzsch a acheté et utilise aujourd'hui. »
Synthesites a été créé en 2008. « Nous avons développé notre technologie à partir de zéro en utilisant des capteurs électriques à courant continu, et non à courant alternatif », raconte Pantelelis. « Pour nous, l'inconvénient de l'utilisation de capteurs diélectriques alternatifs conventionnels est la nécessité d'exciter la résine à une gamme de fréquences, puis de mesurer la réponse d'impédance pour divers signaux. Il n'est pas seulement difficile de traiter toutes ces données, mais à mesure que la résine passe du liquide au solide, vous devez vous concentrer sur différentes fréquences de signal afin d'obtenir les bonnes informations. »
Pantelelis dit que les capteurs DC de Synthesites peuvent mesurer une très faible conductivité et une résistivité élevée, "ce qui est nécessaire pour mesurer la transformation des résines pendant le durcissement". Il affirme que l'utilisation de la DEA conventionnelle à une seule fréquence pour la simplifier ne donne pas des données précises. « Nous n'avons pas plusieurs fréquences mais appliquons simplement une tension constante. L'inconvénient est que cette approche est très étroite, ce qui signifie qu'elle fonctionne bien pour des applications très spécifiques telles que le durcissement de la résine, mais pas pour tout. Cependant, lorsque l'on compare les performances de notre équipement au DEA conventionnel, le nôtre peut mesurer toute la gamme de durcissement même à des températures plus basses. Les entreprises fournissant des instruments et des services en dehors des composites n'aiment pas notre approche car elle a des paramètres limités à régler. »
Ce n'est pas un problème pour Synthesites car il a spécifiquement ciblé les composites. « Notre approche fonctionne bien sur une large gamme de résines composites et de procédés, y compris les thermodurcissables, les RTM, les préimprégnés et même les thermoplastiques réactifs comme Elium. » (Elium est le thermoplastique basse viscosité d'Arkema (Colombes, France) qui peut être traité par infusion de résine.)
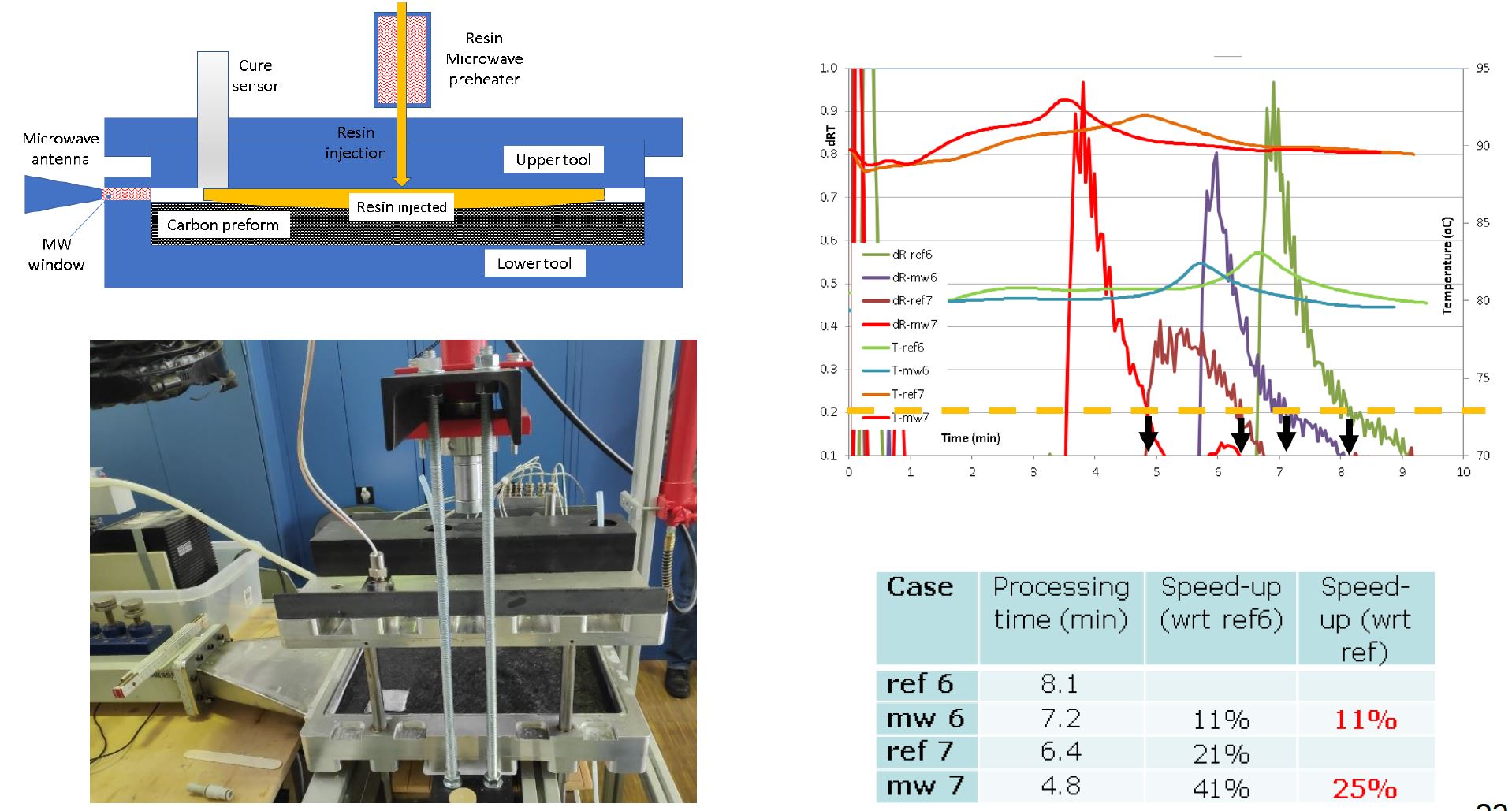
Si la DEA utilisant le courant continu était connue dans les années 1960, alors pourquoi les capteurs AC ont-ils été privilégiés dans les années 1980 et à l'avenir ? « Il y a trente ans, la technologie de DEA utilisant des capteurs CC n'était pas aussi développée », souligne Pantelelis. « Mais nous avons avancé notre approche pour fournir des mesures très fluides et précises pour la production industrielle. Nous avons démontré et continué à développer nos systèmes avec des clients comme GE Aviation (Batesville et Ellisville, Mississippi, États-Unis) et Bombardier qui traitent de grandes pièces avec moulage de résine liquide. Nos systèmes sont également utilisés quotidiennement dans la production de pales d'éoliennes et ont démontré leur capacité à produire industriellement des stratifiés préimprégnés durcis à l'autoclave. »
Contrôle des processus
Pantelelis explique comment les capteurs DC de Synthesites ne sont qu'une partie d'un système intégré pour surveiller le traitement et le durcissement des composites. « Nous mesurons directement la résistance et la température, et à partir de là, nous calculons en ligne la viscosité, le degré de gélification et le degré de durcissement. Nous utilisons des capteurs durables dans le moule, mais également des capteurs de porte et des capteurs en ligne pour les entrées, les sorties et les lignes d'alimentation de résine, ainsi que des capteurs jetables sur les pièces. Vous n'utilisez les capteurs que là où vous en avez besoin. »
Les capteurs de température sont des détecteurs de température à résistance de platine (RTD), qui offrent une précision beaucoup plus élevée (à moins de 0,1 °C) que les thermocouples ainsi qu'une stabilité pendant des années par rapport à la dérive de mesure possible avec les thermocouples. Les RTD sont des équipements standard dans de nombreuses applications industrielles. Les capteurs de porte (voir le schéma de contrôle de processus ci-dessous) sont binaires, signalant le flux de résine comme activé ou désactivé, bien qu'il existe une deuxième version qui peut également signaler la viscosité. Synthesites a développé des capteurs pour une utilisation avec de la fibre de carbone sans risque de corrosion galvanique, des capteurs qui peuvent être utilisés à travers un sac sous vide et des capteurs moulés pour s'adapter à la géométrie du moule.
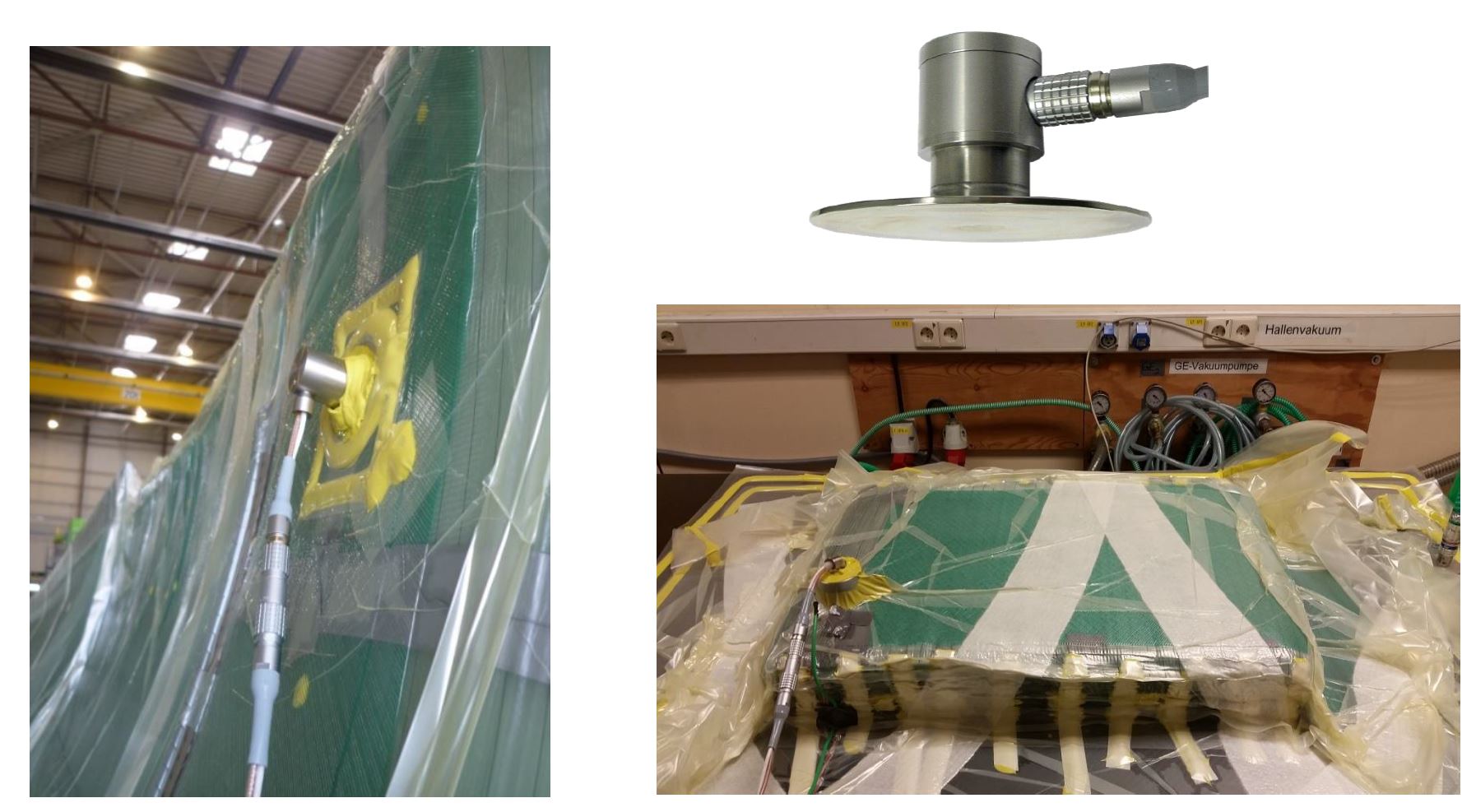
Les composants suivants sont les unités d'acquisition de données OPTIFLOW et OPTIMOLD. OPTIFLOW permet un suivi in situ et en temps réel de l'arrivée et de la température de la résine pour le moulage des composites liquides. Il vérifie et enregistre le flux de résine et peut identifier les écarts de production lors de l'infiltration de la résine. OPTIMOLD utilise des mesures de température et de résistance de la résine pour effectuer des calculs et surveiller l'état de la résine, notamment le rapport de mélange, le vieillissement chimique, la viscosité, la Tg et le degré de durcissement. Il peut être utilisé avec des procédés de préimprégnation et de moulage liquide.
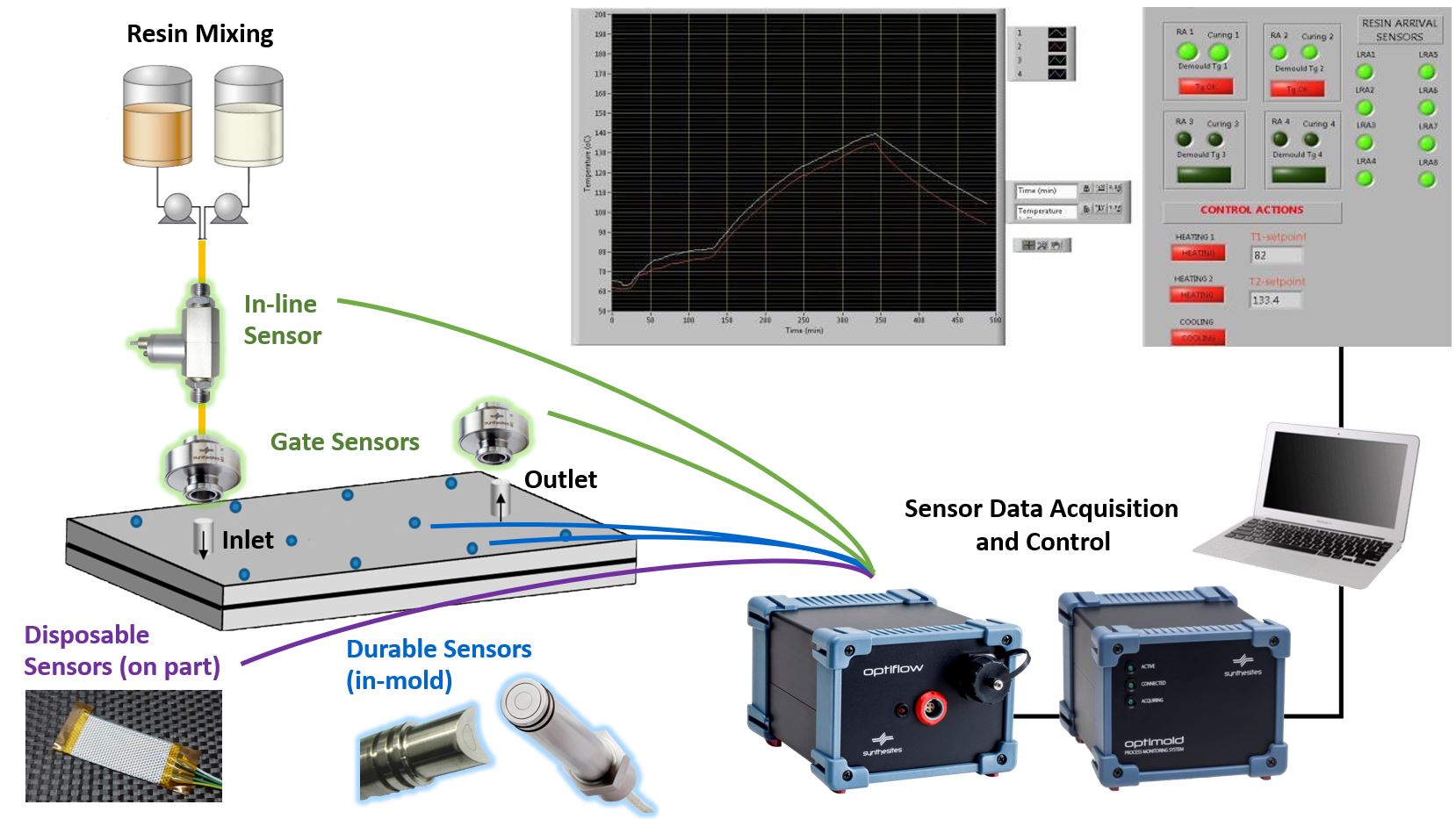
Les unités OPTIFLOW et OPTIMOLD sont pilotées par le logiciel OPTIVIEW. « Ce logiciel permet l'acquisition et le stockage des données et est fourni gratuitement avec notre équipement », explique Pantelelis. « Nous proposons également le logiciel Online Resin State (ORS), une option plus avancée que les clients peuvent acheter en supplément. Il collecte les données d'entrée, effectue des calculs en ligne et envoie des données de sortie pour un contrôle de processus intelligent. »
Les systèmes OPTIFLOW et OPTIMOLD vérifient en permanence que les capteurs sont connectés et que les lectures sont dans la plage. « Lorsque vous comptez sur ces capteurs pour le contrôle des processus, il est impératif que les systèmes déclenchent une alarme si un capteur ne fonctionne pas ou si ses lectures dépassent les limites prescrites », explique Pantelelis. Les deux systèmes ont également des sorties relais pour contrôler l'équipement de traitement. Par exemple, les vannes des conduites d'alimentation peuvent être ouvertes ou fermées en fonction des données d'arrivée de résine, et l'équipement de chauffage/refroidissement peut être géré en fonction de la viscosité de la résine. « Vous pouvez alimenter la sortie des capteurs de pression dans OPTIMOLD », note Pantelelis, « et ainsi contrôler la pression dans le moule en fonction des données de viscosité. »
Mesures et courbes de données typiques
Les captures d'écran ci-dessous montrent les mesures OPTIMOLD des essais RTM de compression haute pression (HP-CRTM) à NCC (Bristol, Royaume-Uni). La première série, issue d'un simple essai à 115 °C, montre comment les mesures en temps réel de la résistance électrique et de la température de la résine sont converties en viscosité et Tg estimées par le logiciel ORS.
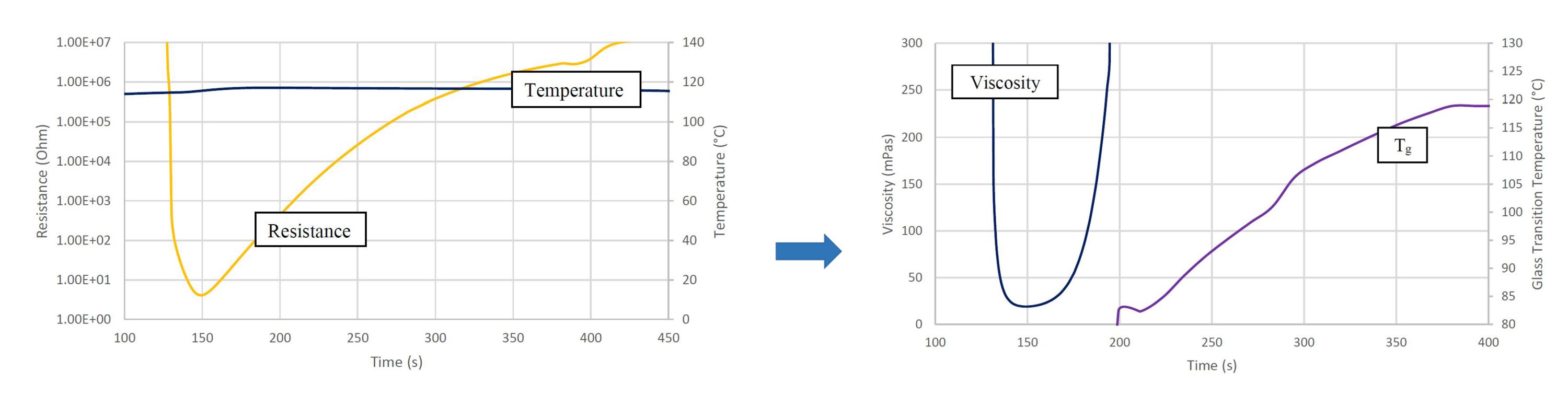
Dans les graphiques ci-dessous, résistance électrique et température (graphiques du haut) ont été enregistrés à 110° (gauche) et 120°C (à droite). Au-dessous des lectures de résistance (R) et de température (T) se trouvent les graphiques montrant la viscosité calculée et la Tg à 110°C (gauche) et 120°C (à droite) . Ces mesures provenaient de deux capteurs OPTIMOLD situés dans la moitié supérieure du moule (Sn.1 et Sn.2, photo du bas ) tandis que la pression de la cavité a été enregistrée à l'aide de deux capteurs de pression Kistler 6162A (Sn.3 et Sn.4).
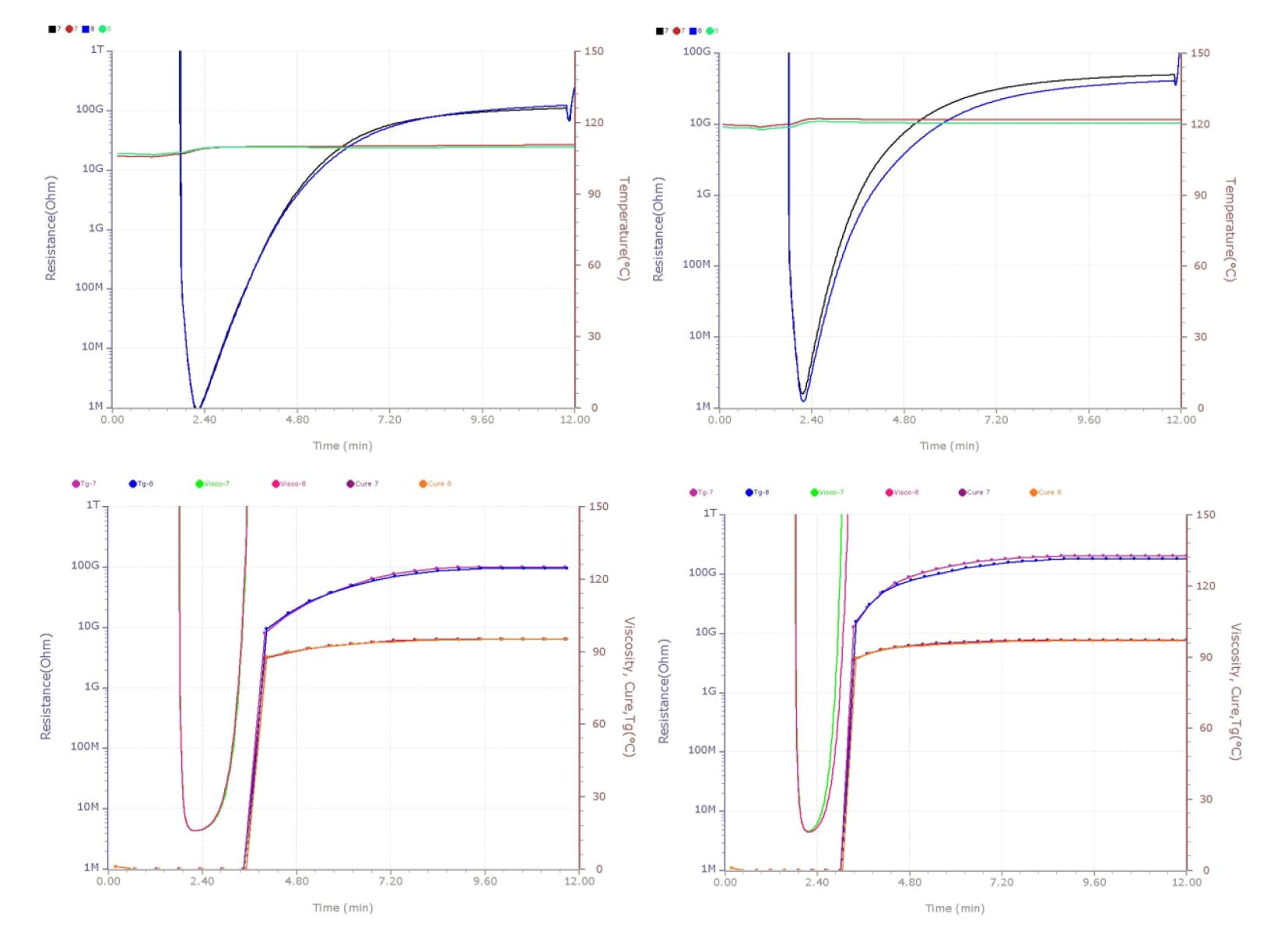
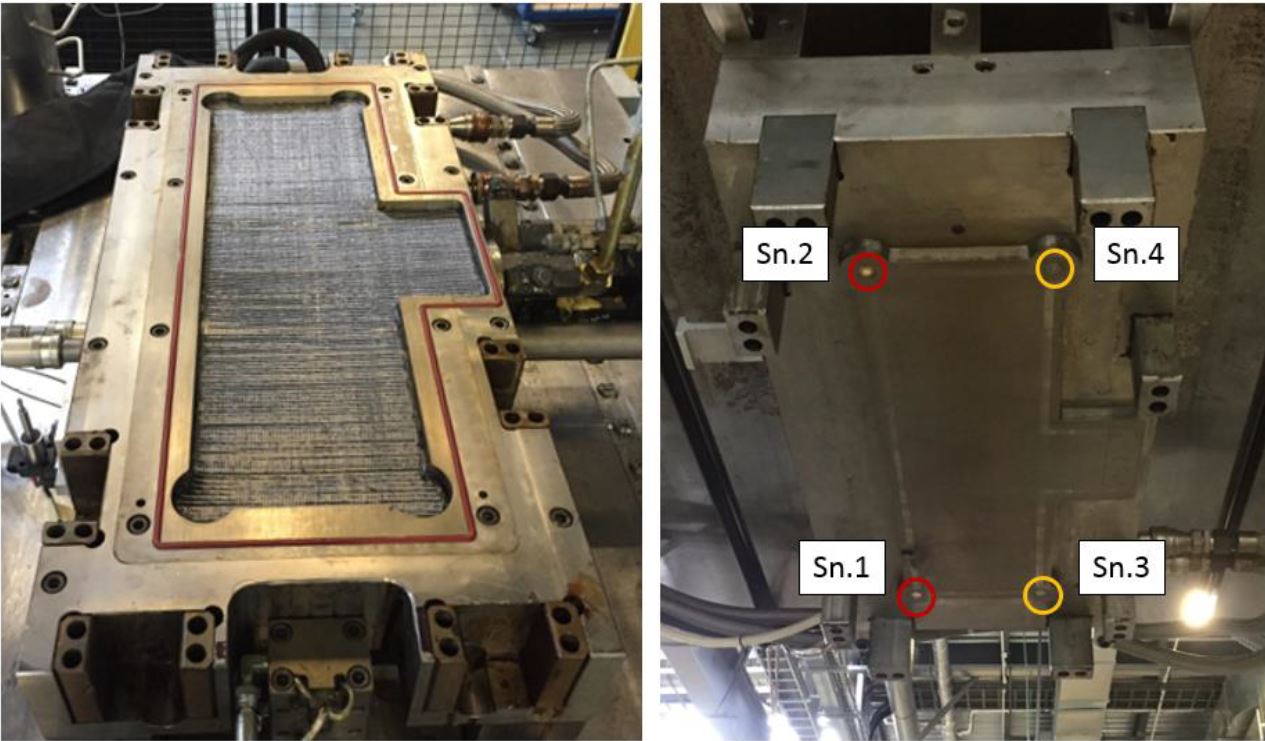
Toutes les données enregistrées par les capteurs dans le moule ainsi que la presse et l'équipement d'injection peuvent être rassemblées dans un seul fichier journal, permettant une image détaillée du processus de fabrication pour chaque composant créé.
Réduction du temps de durcissement
« Nous avons le potentiel de réduire le temps de durcissement de plus de 30 % car le fabricant peut voir la Tg en temps réel, ce qui lui permet de décider quand arrêter le cycle de durcissement », explique Pantelelis. « Ils n'ont pas à attendre pour terminer un cycle d'héritage plus long que nécessaire. Par exemple, le cycle hérité du RTM6 est de 2 heures à 180 °C pour un durcissement complet. Nous avons vu que dans certaines géométries, cela peut descendre jusqu'à 70 minutes. »
Le but alors, est-il d'arrêter le processus une fois la guérison terminée ? "Il ne s'agit pas d'une guérison complète, mais d'atteindre le niveau de guérison dont chaque composant a besoin", explique Pantelelis. « La guérison complète prend trop de temps. La clé est de pouvoir voir quand un durcissement suffisant est atteint. Les fabricants de pales d'éoliennes ont une cible Tg. Quand ils atteignent cela, ils peuvent commencer à se refroidir. Il faut donc un capteur qui puisse donner des mesures très précises de la Tg en temps réel. »
Synthesites a terminé un projet de démonstration avec Hutchinson (Paris, France) pour produire une lame de suspension automobile en fibre de verre/époxy et RTM pour le projet ECOMISE financé par l'UE (Enabling Next Generation COmposite Manufacturing by In-Situ Structural Evaluation and Process Adjustment, 2013 -2016). L'objectif de ce projet était d'optimiser le cycle RTM sur la base d'un suivi des processus en temps réel :
- La première rampe de chauffe serait déclenchée par l'achèvement de l'infiltration de résine à l'aide de capteurs.
- La deuxième rampe de chauffage serait déclenchée à la fin du durcissement basé sur le calcul de Tg.
- Le refroidissement serait déclenché par la fin de la post-polymérisation basée sur le calcul de la Tg.
Le système Synthesites comprenait deux (2) in-mold capteurs pour le durcissement (CS1, CS2), un (1) dans le moule capteur pour le débit et la température de la résine (Flow Sensor 1) et huit (8) jetables capteurs de débit/température de résine — quatre (4) intégrés dans la pièce d'essai et quatre (4) fixés à la surface de l'outil.
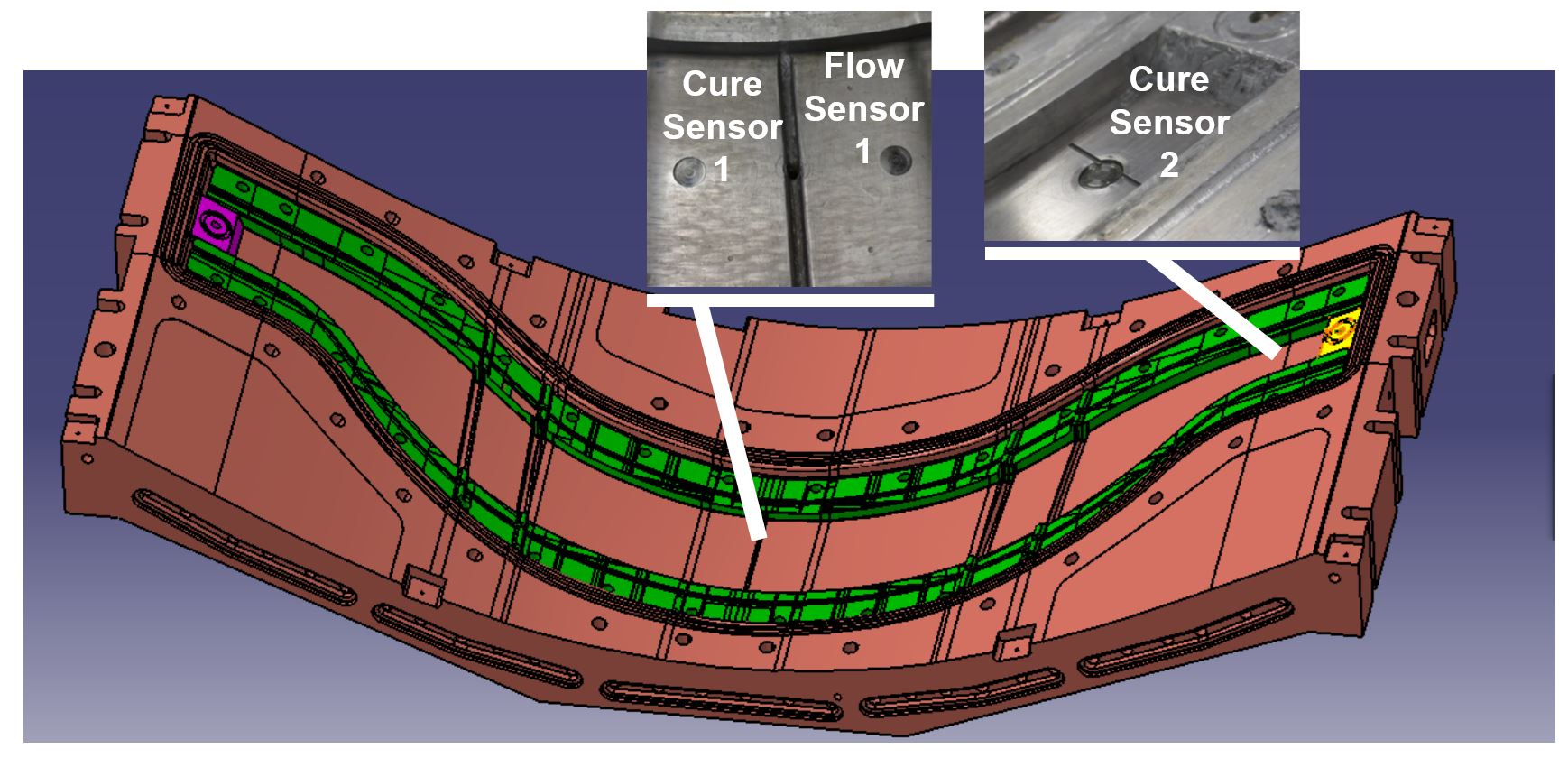
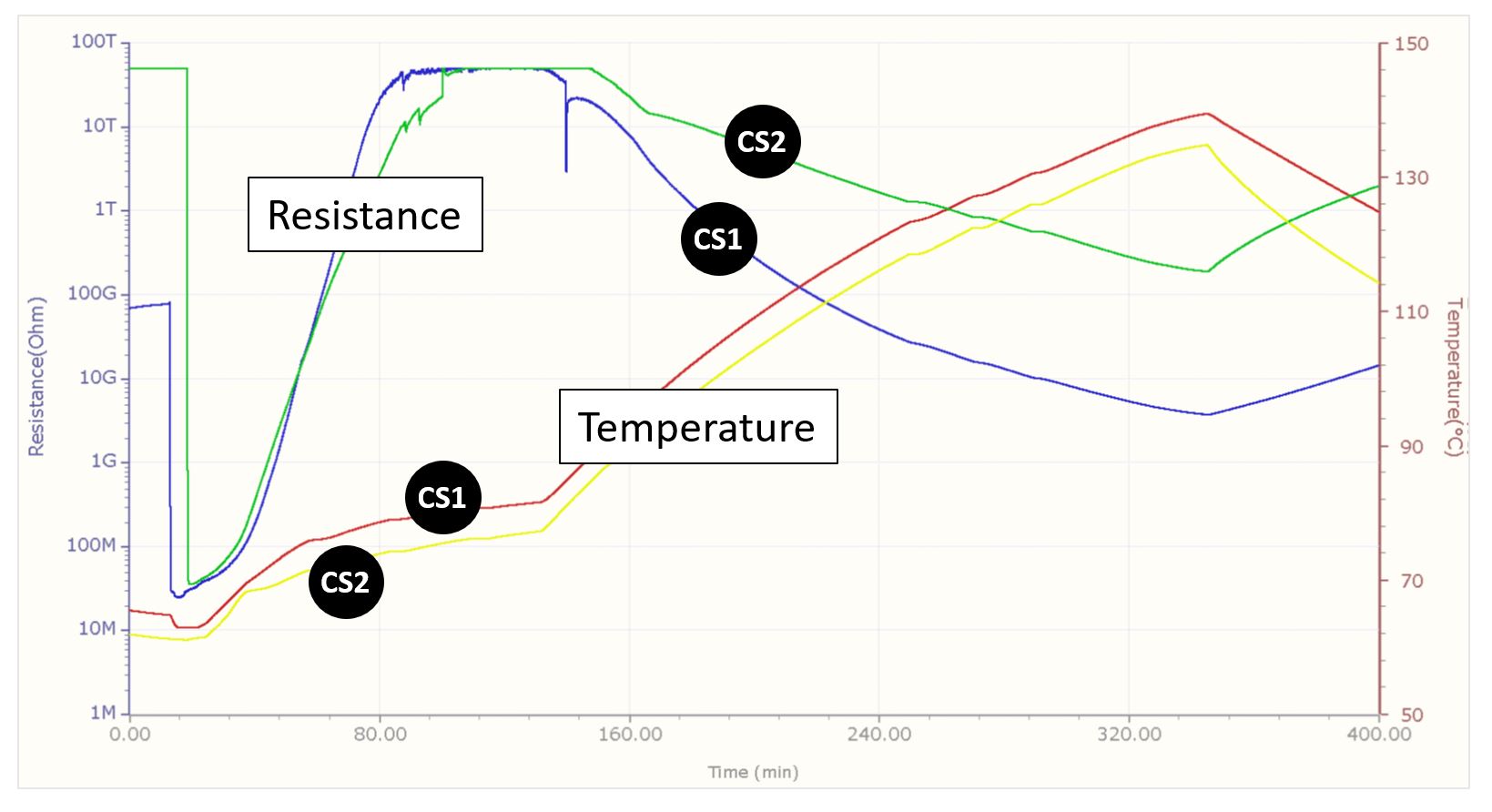
« Les unités OPTIMOLD et OPTIFLOW peuvent être connectées ensemble via Ethernet afin que tous les capteurs puissent être enregistrés dans une session Optiview », explique Pantelelis. "Ainsi, CS1 et CS2 ont été connectés à deux unités OPTIMOLD, le capteur de débit dans le moule 1 et les huit capteurs de débit jetables ont été connectés à trois unités OPTIFLOW."
Ce système de capteurs, d'unités d'acquisition de données OPTIMOLD/OPTIFLOW et de logiciels OPPTIVIEW/ORS a ensuite été appliqué lors d'essais de moulage RTM pour établir des cibles pour différentes étapes de processus, notamment l'injection/l'infiltration de résine et deux cibles Tg. « Il s'agissait d'une pièce épaisse fabriquée à l'aide de fibres unidirectionnelles et de résine époxy Huntsman », explique Pantelelis. "Dans ce cas, nous avons utilisé des capteurs à fil de flux pour vérifier le flux dans ces plis UD, qui sont généralement très compacts et peuvent créer des problèmes lors de l'infiltration de résine."
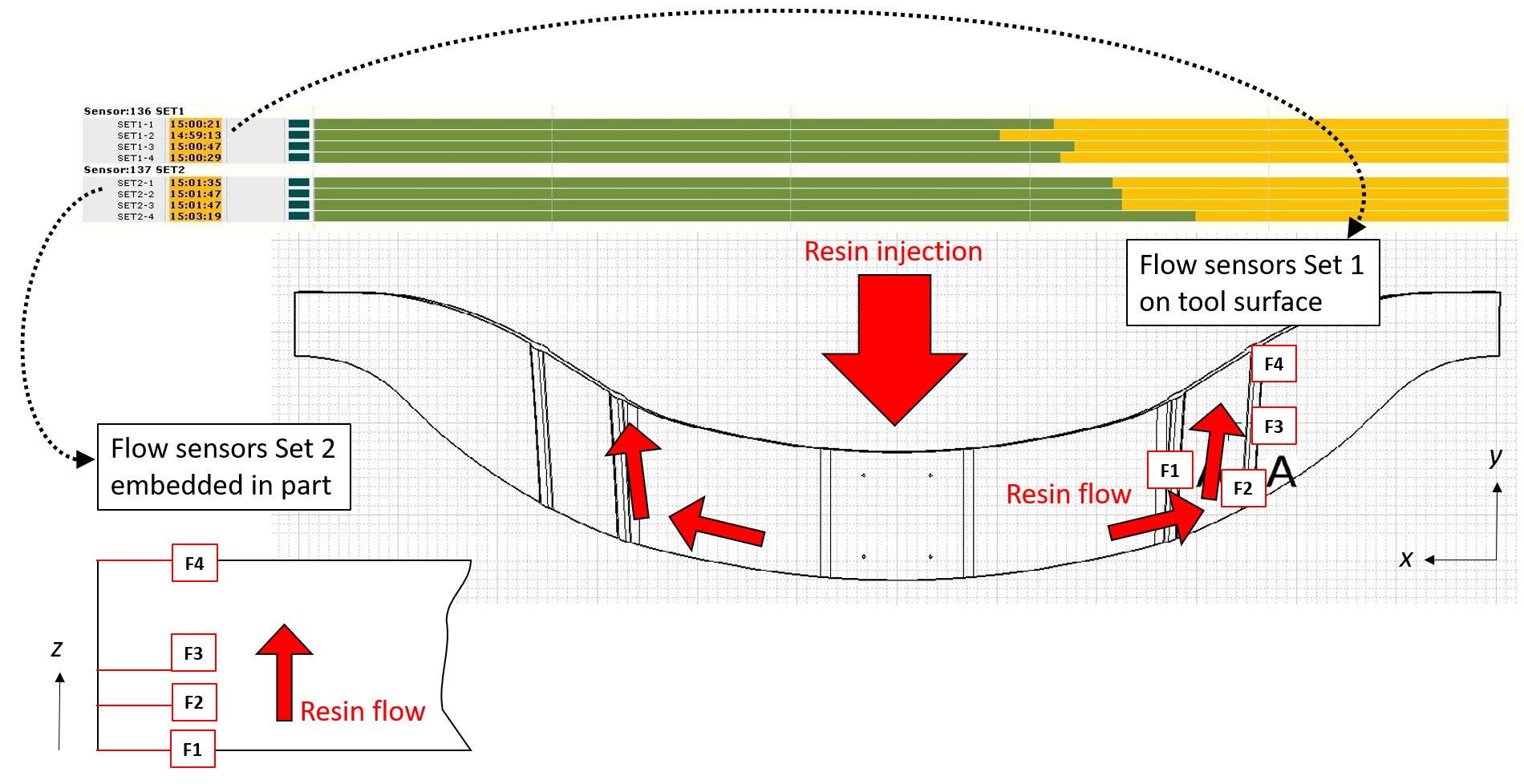
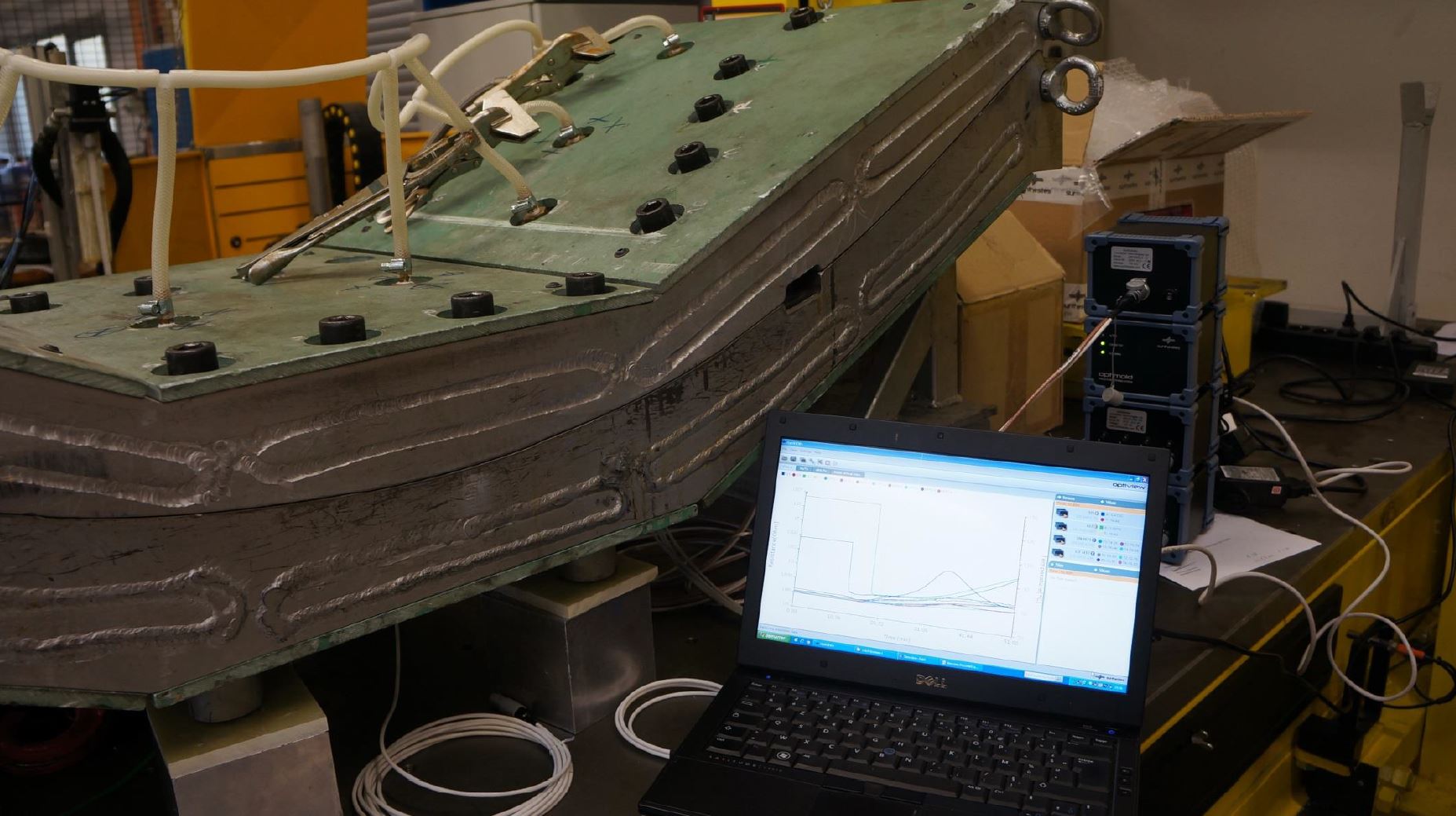
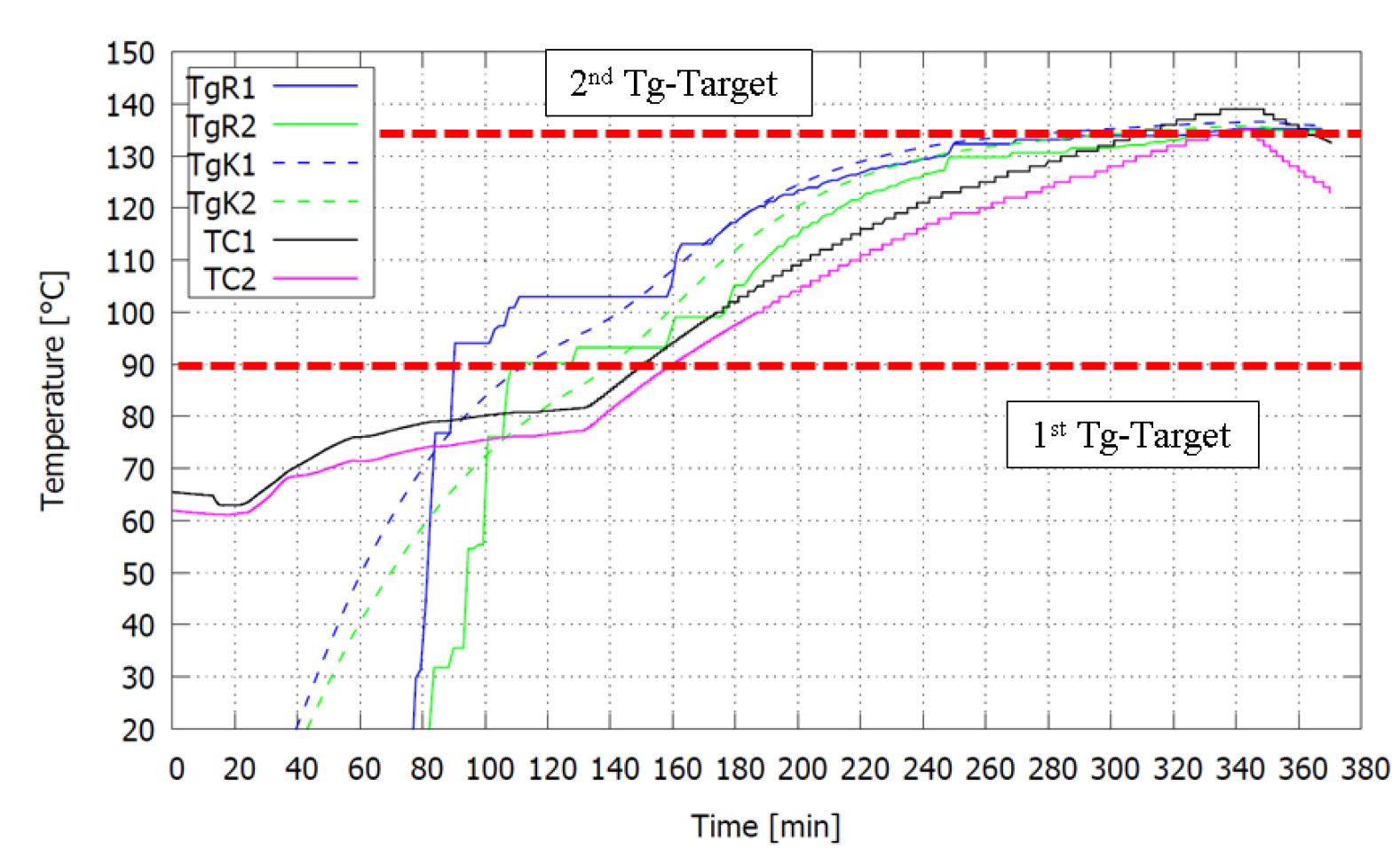
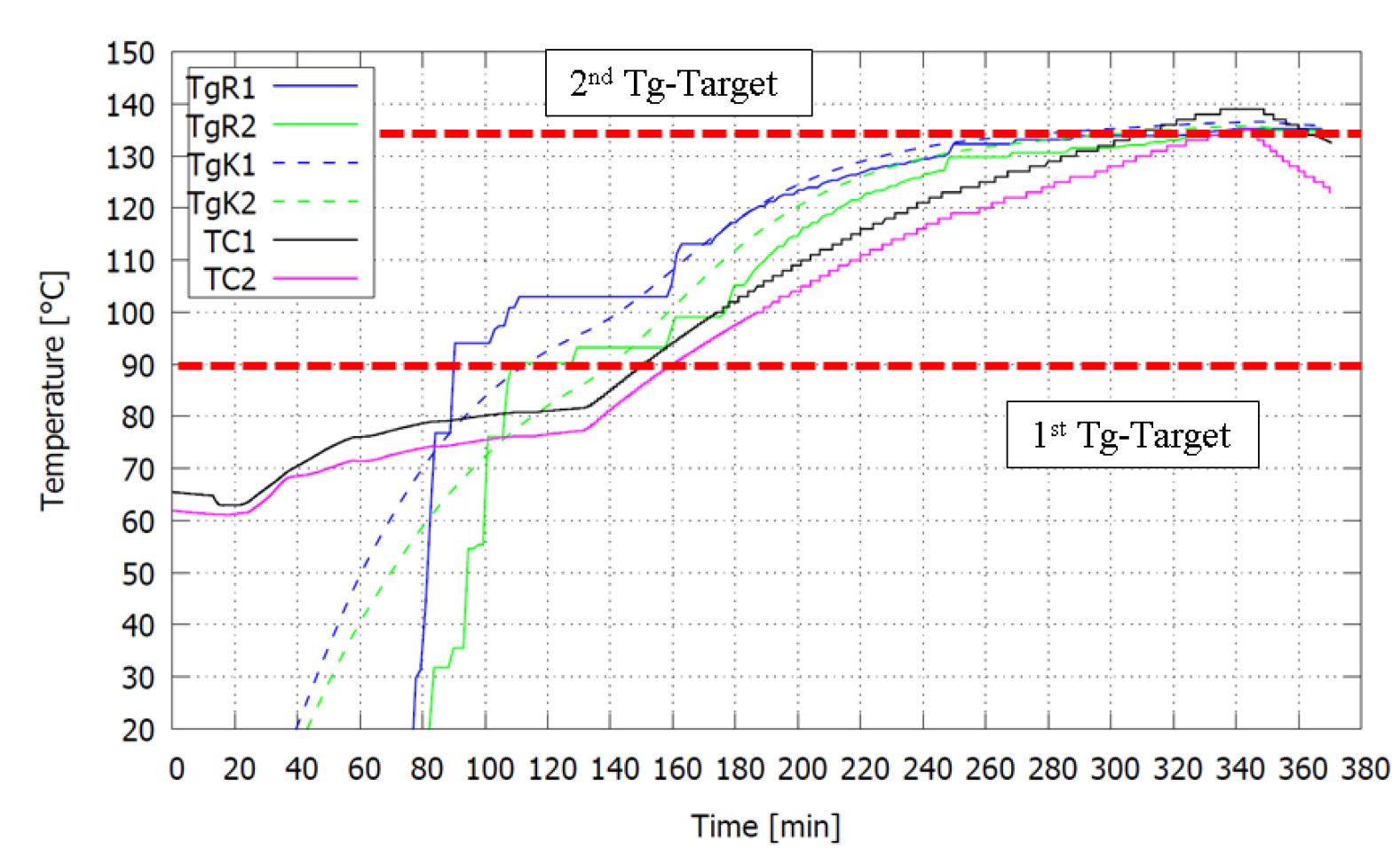
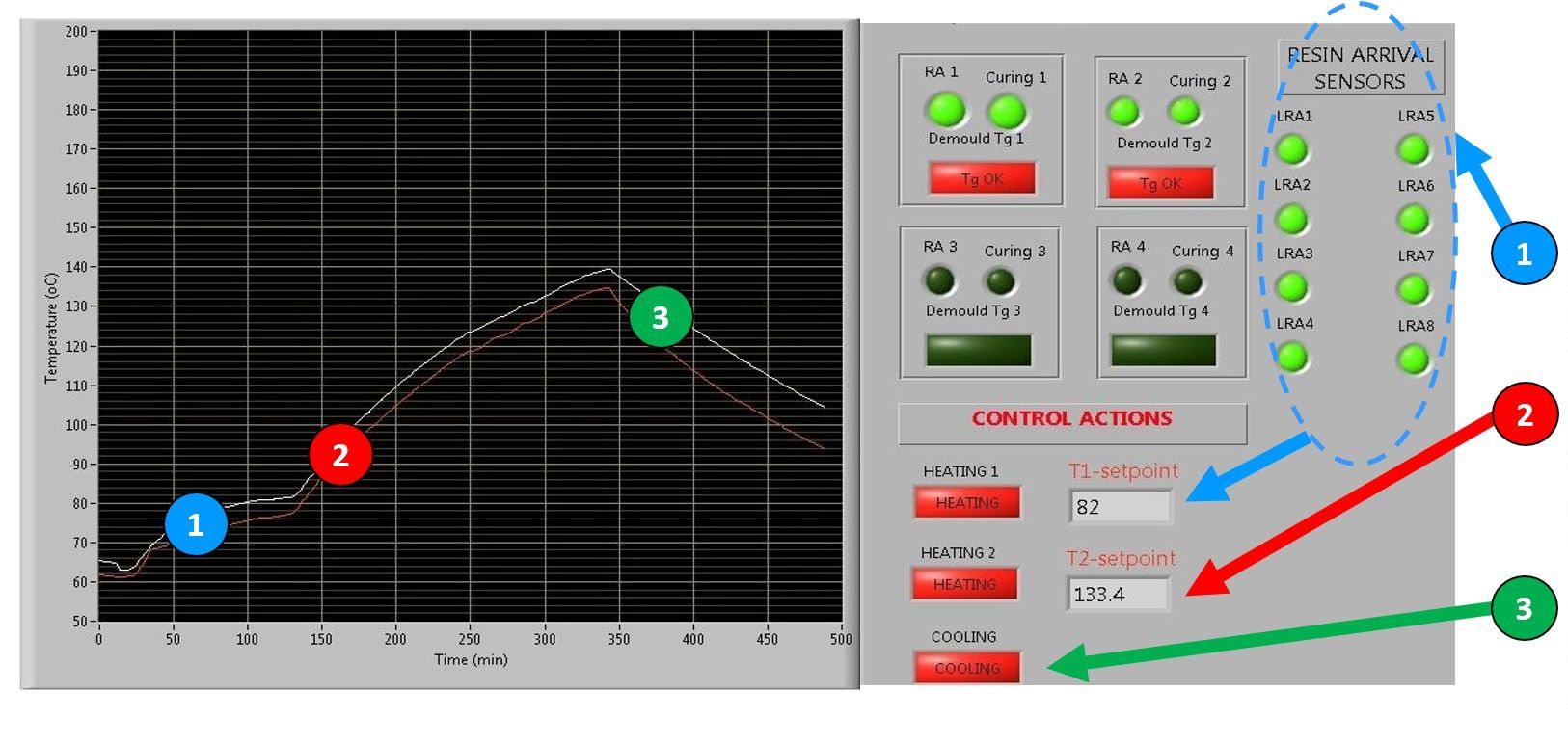
Grâce à ce système de contrôle de processus, le projet ECOMISE à Hutchinson a pu réduire le cycle de durcissement de plus de 30 %.
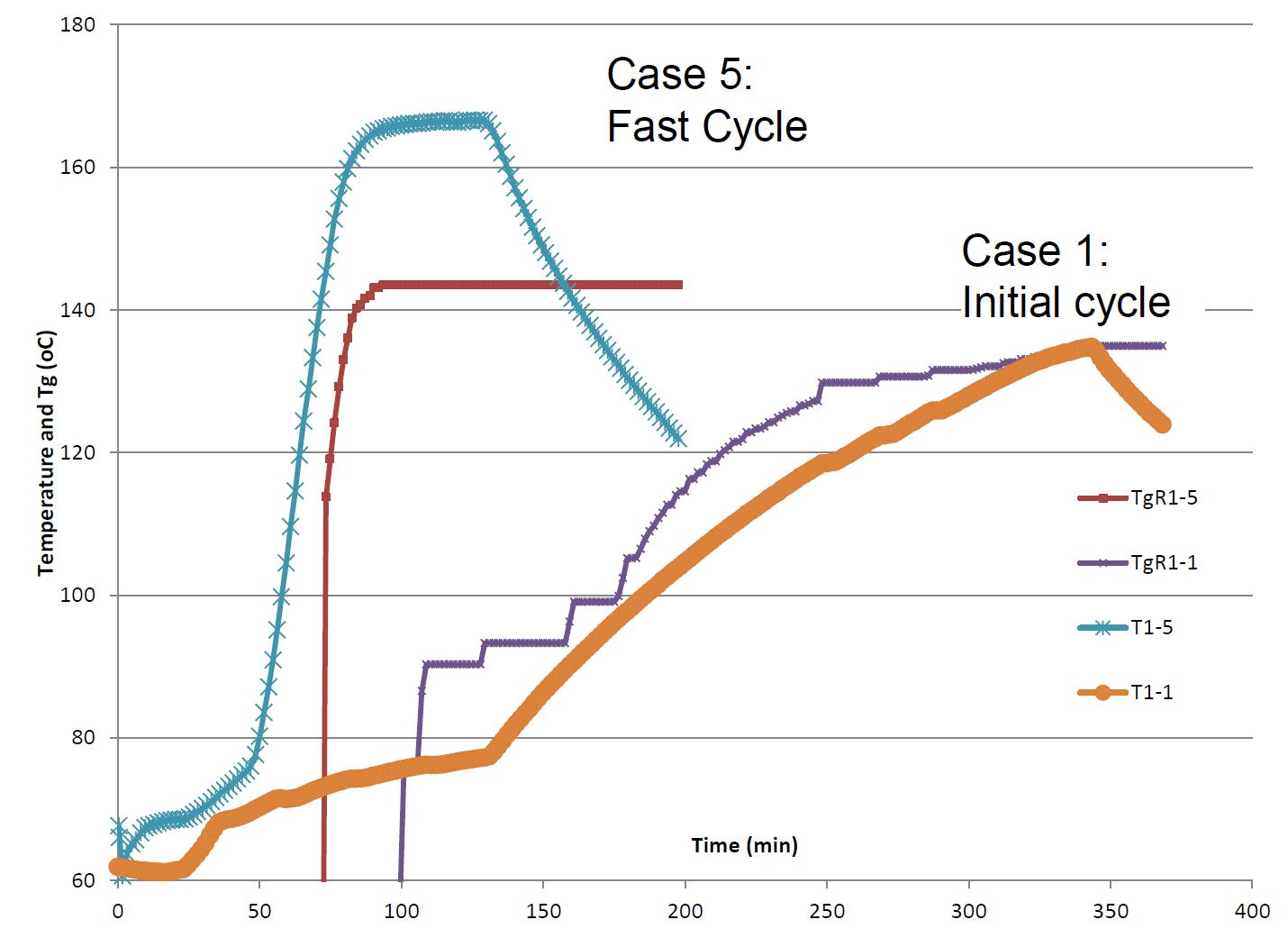
Calibrage
Un étalonnage est requis pour la surveillance en ligne de la Tg. Au fur et à mesure que les mesures sont collectées à partir des capteurs via les unités OPTIMOLD, le logiciel ORS les traduit en viscosité et en Tg en fonction de l'étalonnage pour cette résine spécifique. « Cet étalonnage est un travail effectué avant le traitement pour fournir les corrélations que le logiciel ORS utilisera pour ses calculs », explique Pantelelis. « Nous étalonnons en plaçant la résine dans un rhéomètre et en mesurant la température et la viscosité. En appliquant les formules appropriées, vous calculez ensuite la résistance et la Tg correspondantes. Nous développons le calibrage des résines pour nos clients en fonction de leurs standards, et étudions les différents cycles de durcissement de la résine. Ces données d'étalonnage sont ensuite utilisées par le logiciel ORS lors du traitement de cette résine. »

La précision des calculs de Tg en temps réel du logiciel ORS a été démontrée lors d'essais menés par le producteur de pales d'éoliennes Carbon Rotec Composite Technology (Lemwerder, Allemagne). La Tg calculée en ligne par le logiciel ORS a été comparée à la Tg mesurée juste après le démoulage en effectuant un calorimètre à balayage différentiel (DSC). Pour le traitement isotherme, la différence moyenne était de 1,61 °C et pour le traitement non isotherme, elle était de 2,15 °C.
"Cette précision a été démontrée à maintes reprises dans des projets privés avec d'autres clients", explique Pantellis.
Les avancées de la production industrielle
Ce contrôle de processus basé sur des capteurs et des données est en effet un grand pas vers la fabrication entièrement automatisée et intelligente de Composites 4.0. Bien qu'il ait été démontré dans ECOMISE et également avec le NCC à Bristol, il n'est pas encore utilisé dans la production quotidienne. « L'idée d'utiliser les capteurs pour voir la Tg et ensuite commencer le refroidissement a en effet été lancée dans la fabrication de pales d'éoliennes », rapporte Pantelelis, « mais elle n'est pas encore entièrement automatisée. Le système émet une alarme lorsque la Tg cible est atteinte, puis l'opérateur arrête le cycle de durcissement. L'automatisation est simple et sera achevée une fois que le fabricant aura validé la précision du système pendant la phase pilote.
«Pour atteindre cet objectif, nous avons développé un nouveau poste de travail pour permettre à l'opérateur de production de superviser le processus automatisé, qui ne nécessite aucune intervention de sa part», poursuit-il. "Nous avons vu dans la fabrication de pales d'éoliennes que l'utilisation d'un seul poste de travail pendant le durcissement de la résine et de l'adhésif peut réduire le temps de cycle d'au moins 2 à 3 heures sans sacrifier la qualité."
Bien que Bombardier Belfast, maintenant Spirit AeroSystems, utilise des équipements Synthesites dans la production de son aile composite infusée de résine pour la série C, maintenant Airbus A220, le contrôle du processus n'est pas automatisé. Cependant, Synthesites a également travaillé avec Bombardier dans ECOMISE, et ce développement se poursuit. Une réalisation clé a été les capteurs qui alimentent la paroi de l'autoclave. Comme expliqué dans mon blog de 2013, « Aile composite C-Series » :
Bombardier injecte après que le drapage a été placé dans son autoclave de 21,3 m de long sur 5,6 m de diamètre, permettant de maintenir la température et la pression au niveau requis pour une viscosité réduite et un mouillage — Cytec 890 est injectable à 80˚C . . . Une fois l'injection de résine terminée, une pression positive est appliquée dans l'autoclave pendant la consolidation, provoquant la fermeture des éléments d'outillage, compactant le stratifié humide et éjectant l'excès de résine de l'entrée de résine dans une décharge de résine spécialement conçue.
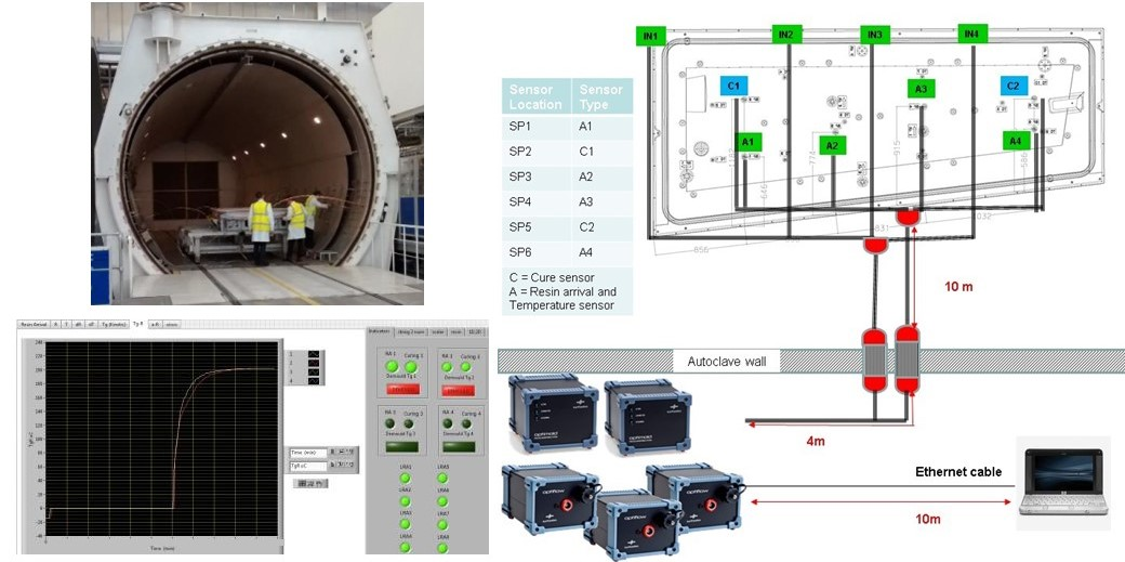
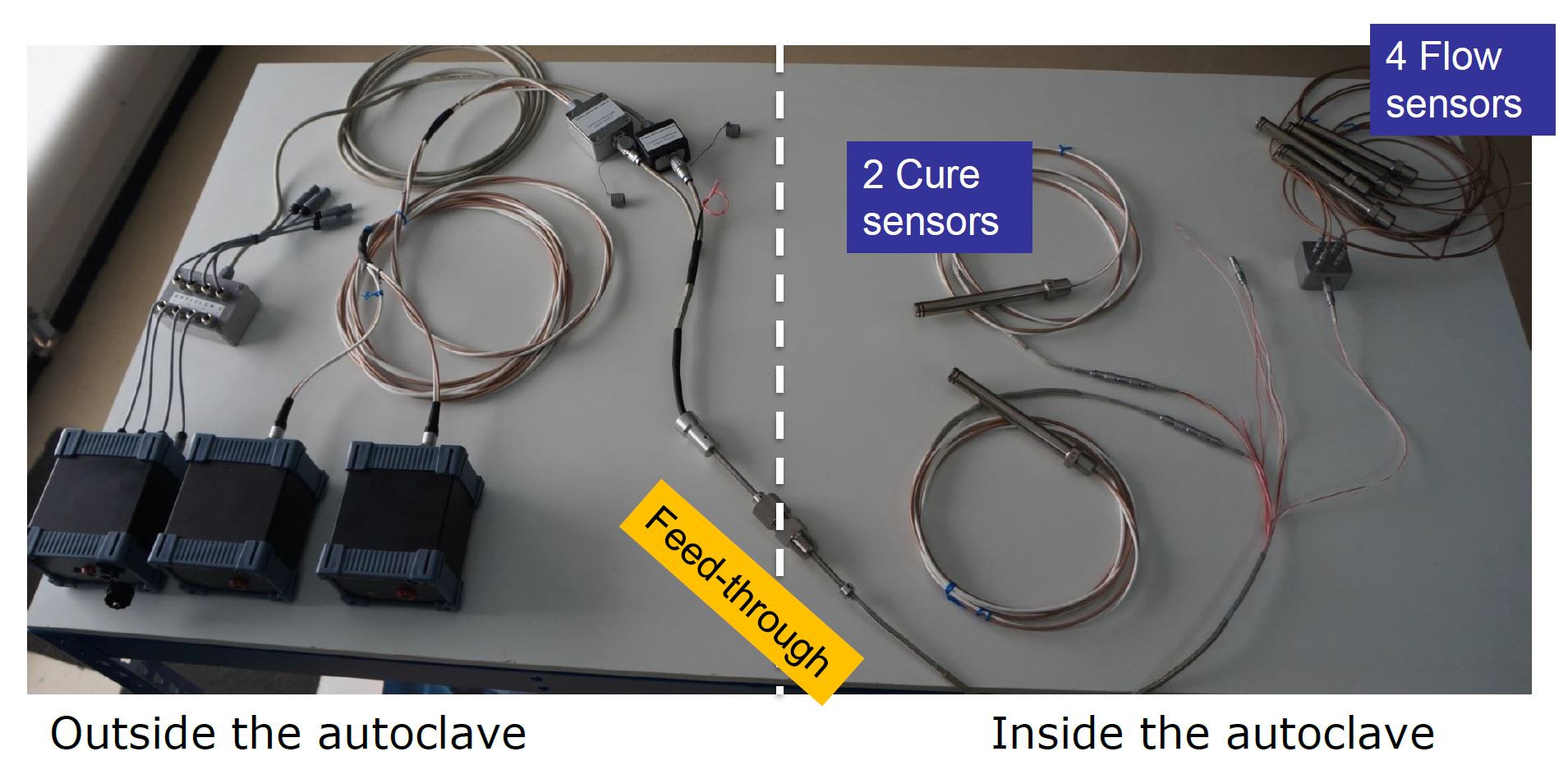
«Comme la plupart des fabricants de l'aérospatiale commerciale, il est intéressé à assurer la qualité et à augmenter le taux», explique Pantelelis. La mise en page ci-dessous et les résultats d'ECOMISE étaient pour un démonstrateur, pas une partie commerciale. Il a utilisé deux unités OPTIMOLD avec deux capteurs de durcissement dans le moule et trois unités OPTIFLOW avec quatre capteurs de débit dans le moule et quatre capteurs en ligne sur les lignes de vide. « OPTIFLOW peut surveiller jusqu'à quatre arrivées de résine et quatre capteurs de température/résistance », note Pantelelis. « Les objectifs de la manifestation ont été pleinement atteints. Nous avons prouvé que les capteurs, le câblage et les systèmes peuvent fonctionner sans aucun problème sous les spécifications aérospatiales les plus exigeantes. Il était intéressant de noter que les mesures d'arrivée de résine ont montré de grandes différences par rapport aux simulations d'écoulement. De plus, la surveillance en ligne de la Tg a montré que le cycle de durcissement suivi pour ce démonstrateur spécifique aurait pu être considérablement plus court. »
« Nous développons actuellement un système de surveillance des lignes de liaison », explique Pantelelis, « principalement pour la production de pales d'éoliennes, mais en fin de compte pour tout processus de liaison. Bien que nous soyons actuellement très occupés par l'industrie éolienne, qui essaie de réduire les coûts, nous voyons de plus en plus d'intérêt de la part du secteur aérospatial alors qu'il s'oriente vers le moulage de composites liquides pour la production de masse. Les fabricants cherchent à mieux comprendre ce qui se passe exactement pendant le moulage et comment ils peuvent stabiliser et optimiser leurs processus. »
Les projets Ecomise et Recotrans ont reçu un financement des programmes de recherche et d'innovation FP7 et Horizon 2020 de l'Union européenne dans le cadre de la convention de subvention nº NMP2-SL-2013-608667 et 768737, resp.
Références pour la section « Analyse diélectrique (DEA), AC vs DC » inclure :
- « Real-time UV cure monitoring » par VINCENTZ, publié dans European Coatings Journal, numéro 11/2003, p. 7.
- « Systèmes de surveillance des processus en ligne – Étude de référence et de test » par Reinhold Meier 1 , Swen Zaremba 1 , Florian Springl 1 , Klaus Drechsler 1 , Fabrice Gaille 2 et Christian Weimer 2 — 1 Institute for Carbon Composites, TU Munich, Garching, Allemagne. 2 Eurocopter Deutschland GmbH, Donauwörth. Flow Process in Composite Materials – FPCM 11, 9-12 juillet 2012, Auckland, Nouvelle-Zélande.
- Caractérisation non destructive des matériaux VIII édité par Robert E. Green, Actes du 8 th Intl. Symposium sur la caractérisation non destructive des matériaux, 16-20 juin 1997, Boulder, Colorado, États-Unis, publié par Springer Science &Business Media, pp. 384-385.
Une autre référence utile est "The Handbook of Dielectric Analysis and Cure Monitoring" de Huan L. Lee, publié par Lambient Technologies.
Résine
- Capteurs et processeurs convergent pour les applications industrielles
- BASF et Toray dans le cadre d'un accord d'approvisionnement pour la production de bandes CFRT pour les applications automobiles et industrielles
- Composites TPE ultra-légers pour chaussures
- Solvay composites sélectionnés pour catamaran de course
- Hexion présente une solution époxy à deux composants pour la production de composites aérospatiaux
- LANXESS étend sa capacité de production de composites thermoplastiques renforcés de fibres continues
- Le consortium des composites thermoplastiques vise une production à haut volume pour l'automobile et l'aérospatiale
- Capteurs de contrainte ultra-minces et sans pile pour bras robotiques industriels
- Capteurs intelligents :avantages et inconvénients pour les machines industrielles