Révolutionner le paradigme des coûts des composites, Partie 2 :Formage
Le sous-programme RAPM du programme Tailorable Feedstock and Forming (TFF) de la DARPA a compilé des données analytiques de la production actuelle/passée ainsi que des données empiriques de ses propres essais de formage pour plusieurs pièces afin de générer ces courbes. L'objectif est de mieux comprendre l'espace commercial des pièces et procédés composites.
Source de toutes les images :The Boeing Co., DARPA
Le programme Tailorable Feedstock and Forming (TFF) a été lancé par la Defense Advanced Research Projects Agency (DARPA, Arlington, Virginie, États-Unis) en 2015 pour permettre une fabrication rapide, peu coûteuse et agile de petites pièces composites de forme complexe pour la défense. avion. Ce programme de 48 mois visait à accroître la compétitivité-coût des composites afin d'exploiter leurs gains de poids et leur résistance à la corrosion et à la fissuration par rapport à l'aluminium usiné. Dans la partie 1 de cette série, CW a exploré la vision de TFF et son sous-programme Tailorable Universal Feedstock for Forming (TuFF), qui a développé un matériau en feuille à fibres courtes avec des propriétés mécaniques élevées et une formabilité semblable à celle du métal.
Dans cet article, l'accent passe de la matière première au formage avec le deuxième sous-programme de TFF :RAPid high-Performance Manufacturing (RAPM, prononcé « wrap-em ») dirigé par The Boeing Co. (Chicago, Illinois, États-Unis). Le programme a débuté en juillet 2016 et a présenté ses résultats dans de nombreuses publications, dont 6 articles et deux présentations au SAMPE 2019. L'objectif du RAPM, comme expliqué par les chercheurs techniques et chercheurs principaux de Boeing, Gail Hahn et Tom Tsotsis, est de « révolutionner le paradigme des coûts pour petites pièces composites, permettant une utilisation omniprésente dans les applications de défense. »
« Nous avons commencé avec cette vision d'atteindre des performances aérospatiales avec une efficacité automobile », explique Hahn. Le programme a travaillé avec des fabricants de matériaux composites et de pièces automobiles, notamment Solvay Composite Materials (Alpharetta, Géorgie, États-Unis) et SGL Composites (Ried et Ort im Innkreis, Autriche), mais l'obtention de propriétés aérospatiales n'a pas toujours été simple. « Bien que les époxydes à basse température et à durcissement rapide soient facilement disponibles pour les applications automobiles, ils ne répondent pas aux exigences de l'aérospatiale », explique Tsotsis. RAPM a utilisé de nouveaux époxydes à deux composants à durcissement rapide ciblant les pièces d'infusion de résine de qualité aérospatiale. Cependant, au départ, le système de moulage chez SGL ne pouvait pas dépasser 130°C, ce qui empêchait d'atteindre l'objectif de 30 minutes de temps sur outil.
"Notre objectif était d'atteindre un temps maximum de 30 minutes sur l'outil pour permettre l'utilisation d'une cellule de travail à haut débit afin de réduire les coûts au niveau du système afin d'être compétitif avec l'aluminium usiné", explique Tsotsis. « Au sein de Boeing, nous avons décidé que cela satisferait tout ce que nous voyions pour les applications de défense », ajoute Hahn. « Pourquoi le mettre ici quand on peut avoir 2 à 6 minutes avec des thermoplastiques ? Parce que les thermoplastiques nécessitent un traitement à des températures encore plus élevées avec des contraintes d'outillage correspondantes, et notre objectif est de donner à notre chaîne d'approvisionnement de nombreuses options. »
Au fur et à mesure que le programme avançait, il s'est ouvert aux matériaux et fabricants aérospatiaux et même aux systèmes expérimentaux, tels que le XEP-2750 de Solvay. « Au départ, nous pensions que nous serions en mesure d'évaluer pleinement ce système, comme nous l'avons fait avec CYCOM 5320-1 dans notre travail avec le programme DARPA ‘Non-Autoclave Manufacturing Technology’ de 2007 à 2012 », explique Hahn. Bien que le même degré d'évaluation n'ait pas été possible, le XEP-2750 a maintenant été commercialisé par Solvay sous le nom de CYCOM EP-2750 (voir l'encadré en ligne « Novel prepreg for compression moulage in RAPM ”) et a bénéficié des nombreux essais de pièces RAPM et des enseignements tirés.
"Tout ce que je veux, ce sont quelques processus pour les petites pièces composites qui peuvent gagner contre l'aluminium dans une étude commerciale", déclare Jeff Hendrix, consultant pour l'industrie des composites et le programme TFF, à propos de ses objectifs pour RAPM. Alors, le RAPM a-t-il réussi ? CW explore les efforts du programme pour fabriquer des centaines de pièces, en comparant plus d'une douzaine de configurations de pièces aérospatiales à travers plusieurs matériaux et processus, tout en recherchant des méthodes pour réduire le temps et les coûts.
Cadre du programme
En collaboration avec des partenaires clés de l'industrie, RAPM a testé des pièces dans trois domaines principaux :
- Infusion de résine avec HITCO Carbon Composites (Gardena, Californie, États-Unis) et SGL Composites
- Préimprégné thermodurci formage avec Solvay Composite Materials (Heanor, Royaume-Uni et Anaheim, Californie, États-Unis), Fibre Dynamics (Wichita, Kan., États-Unis) et Reinhold Industries (Santa Fe Springs, Californie, États-Unis)
- Formage thermoplastique avec ATC Manufacturing Inc. (Post Falls, Idaho, États-Unis) et TxV Aero (Bristol, R.I., États-Unis)
Les essais de formage se sont déroulés en deux phases :une phase initiale de « développement de la fabrication » (Fig. 1) suivie des parties suivantes « Défi et transition » (C&T) (Fig. 2) pour défi développements initiaux et transition candidats ayant le potentiel de gagner contre l'aluminium usiné.
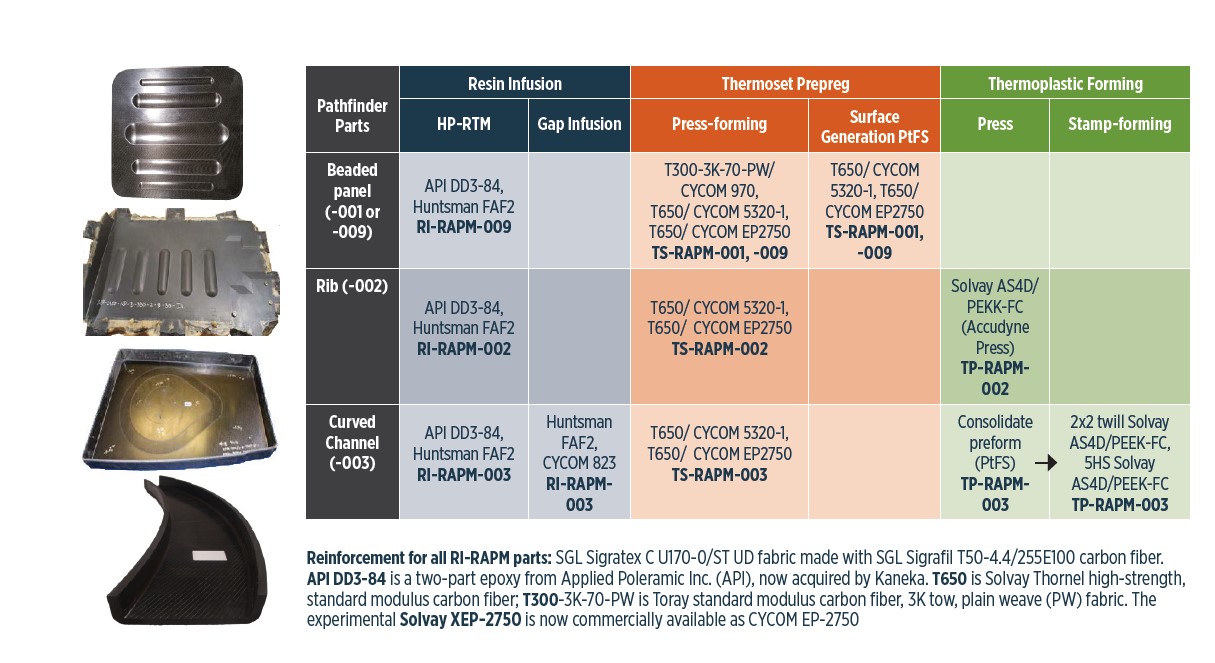
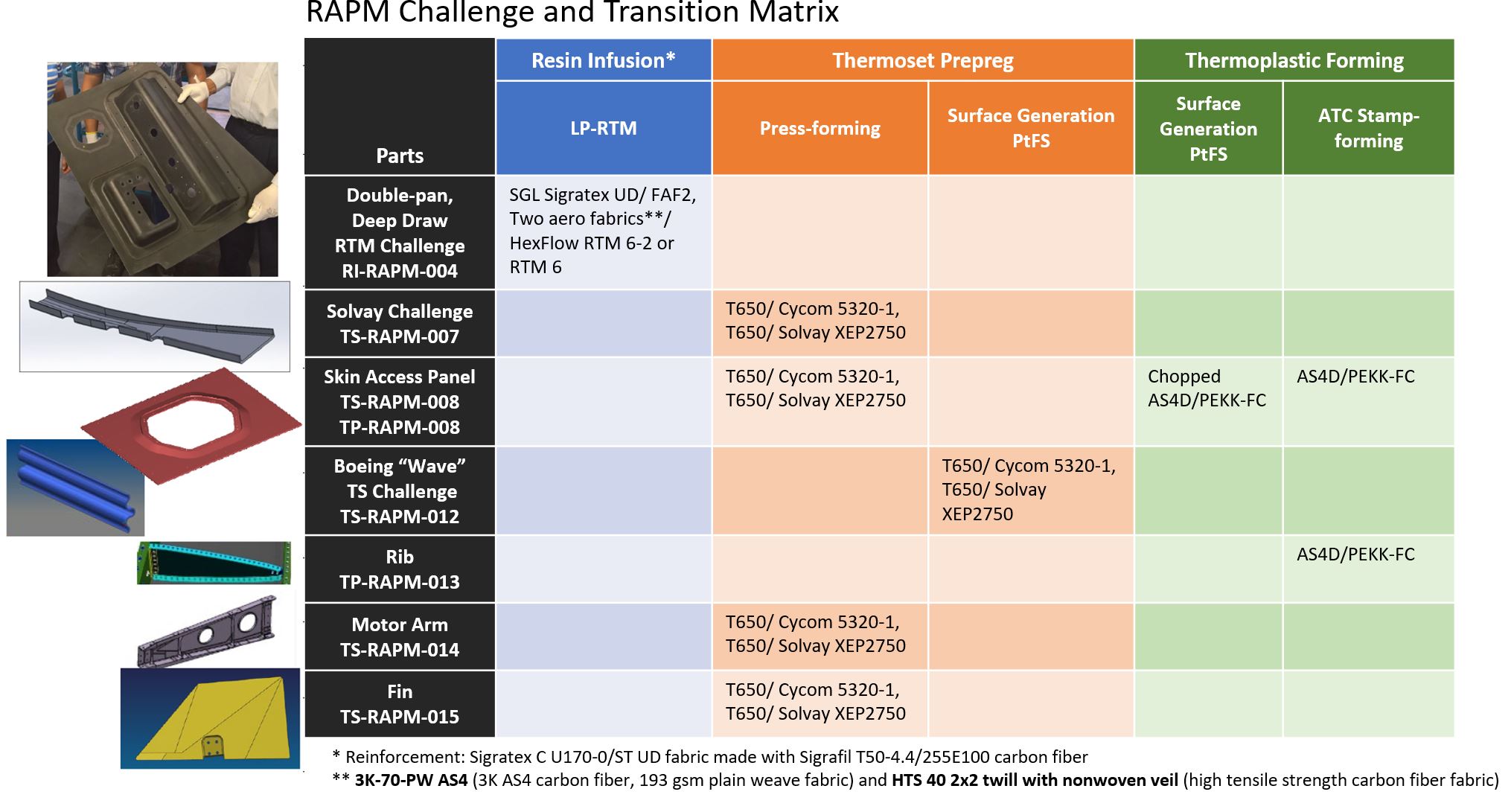
Développement de la fabrication les essais ont utilisé trois configurations de pièces principales :des panneaux à billes (il y en avait deux types), une nervure avec des rembourrages (accumulations de plis) et un canal en C incurvé. Ces caractéristiques incorporées communes aux pièces aérospatiales qui peuvent poser des problèmes de fabrication :le panneau perlé avait plusieurs caractéristiques hors du plan plus des rembourrages, des rembourrages et un bord vertical; le panneau nervuré avait un rembourrage avec plusieurs bords à 90 degrés ainsi qu'un joggle dans l'un des bords ; et le profilé en C avait un rayon intérieur et extérieur différent, une courbure variable dans les ailes et des chutes de pli importantes dans l'âme.
L'objectif était de développer des directives de conception et de fabrication pour chacune des trois pistes. "Cela n'avait pas l'air sexy de faire ces premiers essais", se souvient Hahn. "Mais ils ont aidé à déterminer des rayons acceptables et des géométries de pièces qui produiraient des pièces sans distorsion indésirable des fibres ainsi que des combinaisons optimales de paramètres tels que la tension appliquée, la température, la pression et le temps sur l'outil."
Les trois pistes de matériaux et de processus RAPM comprenaient des essais utilisant un système de contrôle et d'outillage de chauffage pixélisé PtFS (Production to Functional Specification) de Surface Generation (Rutland, Royaume-Uni) (voir l'encadré en ligne « Développement RAPM avec PtFS "), situé chez Boeing R&T à St. Louis, Missouri, États-Unis. « Nous avons pu explorer différentes approches et coûts de contrôle de la température. » La cellule Boeing PtFS a une température maximale de 440°C, une force de serrage de 150 tonnes et un volume de pièce effectif de 750 par 750 par 100 millimètres.
Bien que la vision originale était d'utiliser des matériaux en feuilles à fibres courtes TuFF, car ils n'étaient pas disponibles au début, RAPM a utilisé des matériaux de substitution. Ceci est en fait bénéfique pour l'industrie des composites car les substituts couvrent des matériaux qui reflètent davantage ce qui est utilisé et développé en dehors de ce projet :feuilles organiques automobiles et préimprégnés qualifiés pour l'aérospatiale, époxydes expérimentaux, thermoplastiques semi-cristallins et composés préimprégnés hachés. Ainsi, les résultats et conclusions concernent tous les types de fabricants de composites, pas seulement ceux de la défense.
Piste 1 :Infusion de résine/fabrication RTM
Les essais de développement de fabrication dans cette filière ont commencé avec des matériaux et des procédés de type automobile. Les pièces ont été fabriquées par SGL Composites en utilisant un moulage par transfert de résine haute pression (HP-RTM, 300 bars) et un module standard C T50, des tissus non frisés en fibre de carbone 50K (SGL Carbon à Wackersdorf, Allemagne) dans des configurations en trois parties :RI-RAPM-009 , RI-RAPM-002, RI-RAPM-003 (Fig. 1). Ceux-ci ont été utilisés pour identifier les paramètres de préforme nécessaires pour des pièces finies de haute qualité. L'infusion d'espace (compression RTM ou C-RTM) a également été testée pour le RI-RAPM-003 par Boeing St. Louis à l'aide de son système PtFS.
La modélisation informatique des flux a été utilisée pour mieux comprendre comment infuser ces pièces, en analysant le comportement du processus pour optimiser les matériaux et les paramètres de processus et pour évaluer les scénarios d'injection.
Des approches d'outillage ont été évaluées pour savoir comment et quand appliquer une tension à différents types de géométries de préformes afin de minimiser la distorsion des fibres. Ces modifications de conception ont été validées pour une géométrie modifiée du canal C, suivies d'analyses de tomodensitométrie (CT). Les enseignements tirés ont été appliqués dans la phase de C&T suivante, passant au RTM basse pression (LP-RTM) pour réduire les coûts.
Au cours de ces essais de pièces éclairantes, des délaminages ont été trouvés dans plusieurs des rayons d'emboutissage profond. Tsotsis pense que ceux-ci ont été causés par une combinaison d'un durcissement initial insuffisant de la résine dans l'outil - parce que le système de chauffage à la vapeur de SGL limitait les températures dans l'outil à 130 ° C - et des contraintes thermiques/mécaniques hors plan lors du retrait des pièces. « Parce que la résistance de la résine n'avait pas encore été suffisamment développée, ces anomalies auraient probablement pu être éliminées avec un durcissement complet de l'outil, suggère-t-il. "SGL n'a pas pu répondre à la fois sur l'outil et propriétés aérospatiales jusqu'à ce que le chauffage à l'huile (par rapport à la vapeur uniquement) soit ajouté à l'outil, permettant un durcissement au-dessus de 130 °C », note Hahn. Cela a été ajouté après les essais de développement de fabrication.
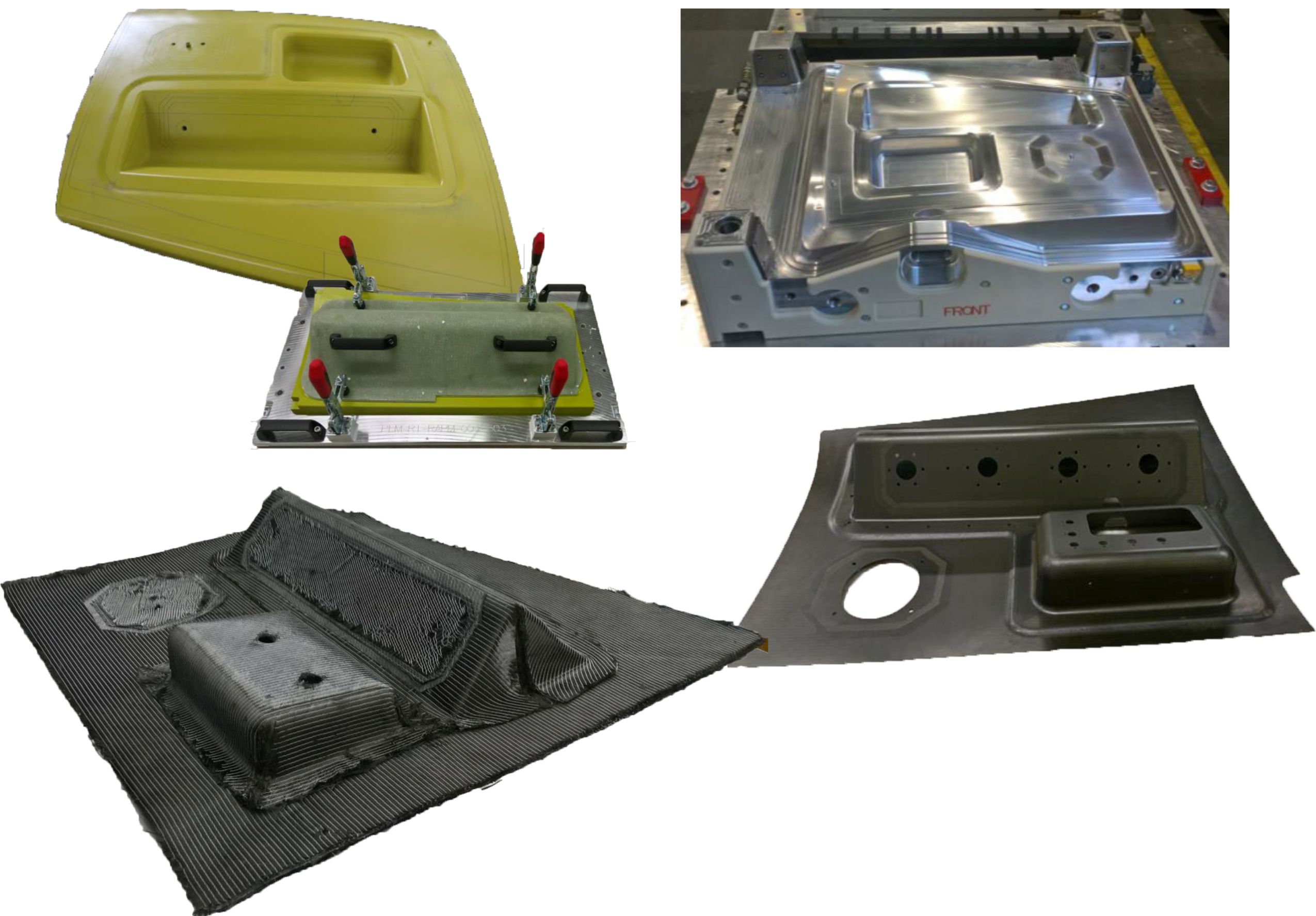
Partie défi emboutissage
Les résultats des essais de développement de fabrication ont ensuite été utilisés pour développer des essais de défi et de transition. La modélisation a également été réalisée pour la partie défi d'emboutissage profond RI-RAPM-004 (Fig. 3), qui comporte deux emboutissages profonds :une région rectangulaire de 5 centimètres et une région de 10 centimètres qui passe d'une forme rectangulaire à une forme en V. Inspiré d'un assemblage de bacs de production, sa géométrie complexe assurait un chemin d'écoulement de la résine non uniforme. Huntsman (Bâle, Suisse) a réalisé la modélisation de l'écoulement avec le logiciel PAM RTM (Groupe ESI, Paris, France) pour un procédé LP-RTM utilisant de l'époxyde en deux parties FAF2 (Huntsman, The Woodlands, Tex., US) et SGL Carbon NCF 150 -grammes par mètre carré de renforts biaxiaux et de 190 grammes par mètre carré unidirectionnels (UD).
RI-RAPM-004 comprend une préforme pour la peau, une pour chacune des sections d'emboutissage, ainsi que deux zones de reconstitution (Fig. 3). Différentes couches ont été utilisées pour ces éléments de préforme afin de répondre aux épaisseurs de panneaux conçues (voir « Fabrication des pièces à géométrie complexe de RAPM ”).
"Le préformage basse pression et le LP-RTM ont permis d'utiliser des outils économiques (par rapport à l'acier) :Allemagne) ; l'outil de durcissement a été fabriqué en aluminium 5083.
Les premiers essais RI-RAPM-004 ont montré une anomalie inattendue dans l'écoulement près de la sortie qui a soulevé les plis de surface, provoquant une distorsion des fibres. L'inversion de l'entrée et de la sortie a résolu le problème. Après infusion et durcissement initial dans un outil à 130°C, les pièces ont été post-polymérisées à 180°C pendant 60 minutes, puis usinées pour obtenir une forme nette. Dix pièces de haute qualité ont été livrées à Boeing pour les analyses C du système à ultrasons automatisé (AUSS).
Les pièces de défi finies ont montré une consolidation complète, un excellent alignement des fibres et une bonne qualité. Les pièces présentaient une température de transition vitreuse de 197°C et une fraction volumique de fibres (FVF) de 49,5%, typiques pour le NCF utilisé. Le nombre de pièces de superposition de pièces a été réduit de plus des deux tiers par rapport au processus de préimprégnation actuel, et le travail tactile a chuté d'environ 90 %. RAPM a également relevé le défi avec des résines et des tissus qualifiés pour l'aérospatiale - pour tester l'adaptabilité des outils et des processus qu'il a développés - et a fabriqué des pièces qui ont satisfait aux exigences de production pour les essais non destructifs (END).
Piste 2 :Formage du préimprégné TS

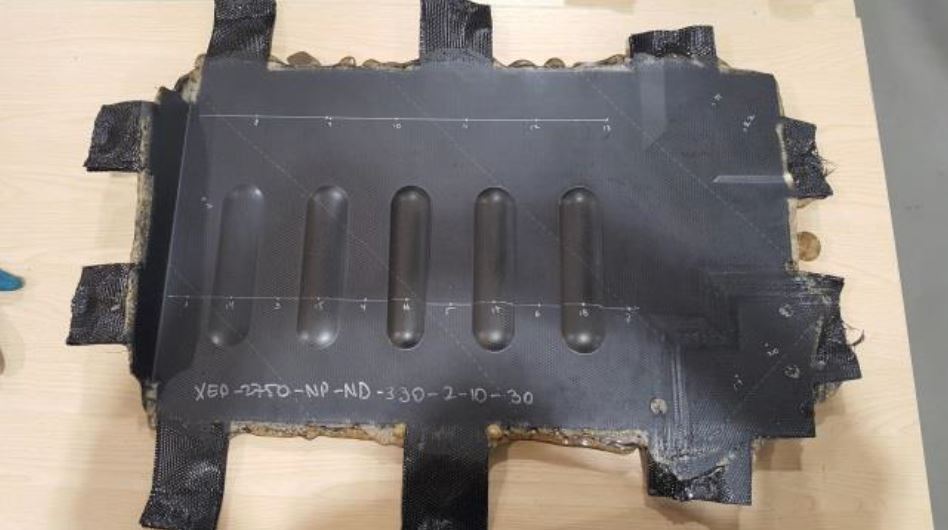
Trois pièces préimprégnées thermodurcissables (TS) de développement de fabrication ont été fabriquées au centre d'applications de Solvay à Heanor, au Royaume-Uni, à l'aide d'un emboutissage à ressort et/ou d'un formage à double diaphragme (DDF). Les trois pièces ont été fabriquées à l'aide de préimprégnés époxy à base de résines Solvay, notamment CYCOM 5320-1, CYCOM 970 et le système aérospatial CYCOM EP-2750. « CYCOM 5320-1 est notre référence pour les pièces hors autoclave (OOA), mais il est également utilisé comme système qualifié pour l'autoclave », explique Hahn. « CYCOM 970 est une option de préimprégné à base de solvant par rapport à un préimprégné thermofusible, et [CYCOM] EP-2750 est notre système de formage à la presse car il est optimisé pour la physique et la cinétique du processus, qui, nous l'avons montré, produit les meilleures pièces. »
L'estampage à ressort et le DDF sont des procédés de moulage par compression isotherme dans lesquels des préimprégnés thermodurcissables sont coupés, assemblés et consolidés en une préforme 2D. La préforme est ensuite préchauffée, transportée dans des outils métalliques assortis et moulée dans une presse à platine hydraulique conventionnelle. La préforme peut être maintenue en tension par un cadre à ressort (Fig. 4), ce qui réduit le plissement induit par les zones de compression du matériau lors du formage. Alternativement, le DDF prend en sandwich la préforme entre deux diaphragmes, éliminant ainsi le besoin de nettoyage et de démoulage du moule. La préforme est collée sur l'un des diaphragmes, la maintenant essentiellement en tension, mais pas aussi directement ou adaptable comme avec un cadre à ressort. Dans RAPM, le type de ressort, les emplacements et les tensions ont été optimisés pour chaque pièce à l'aide de la simulation, tout comme le cadre du ressort. Par exemple, le panneau perlé TS-RAPM-009 a utilisé un cadre qui peut être actionné de haut en bas pour adapter la formation de la charge en parallèle avec la fermeture de la presse.
RAPM a minimisé le temps pièce sur outil en retirant les pièces dimensionnellement stables après un durcissement initial de 15 à 30 minutes, puis en post-durcissement par lots pour augmenter la capacité de cadence. Les familles de pièces ont également été étudiées à l'aide d'un seul ensemble d'outils - par exemple, un canal en C avec trois angles de bride variables le long de la longueur d'une aile - pour maximiser l'utilisation de la cellule. D'autres objectifs guidant l'approche RAPM TS comprenaient :
- Rassemblement et formage automatisés pour minimiser le travail manuel
- Performances mécaniques aérospatiales avec durcissement à 177 °C
- Outillage en acier capable de>1 000 pièces par ensemble d'outils.
Développement de la partie challenge « vague »
Des pièces de développement de fabrication de préimprégnés thermodurcissables ont été formées, en indexant une variable à la fois, jusqu'à ce que la qualité des pièces soit suffisante. Des variables telles que la vitesse de fermeture de la presse, la position de fermeture et la pression de fermeture ont été évaluées, dans le but de consolider le matériau au bon point de la courbe de rhéologie pour créer une pression hydrostatique interne, minimiser le saignement de la résine et empêcher le durcissement d'avancer trop loin, pour éviter les fissures induction. Une fois les paramètres de formage définis, trois à cinq pièces ont été fabriquées pour vérifier la répétabilité du processus, puis testées pour la qualité. Les panneaux perlés ont montré une porosité <0,5% en raison des pressions de consolidation élevées (20,7 bars). Des côtes reproductibles de haute qualité ont également été produites.
Les enseignements tirés ont ensuite été appliqués à la partie défi « vague » ondulée, TS-RAPM-012, pour démontrer le moulage par compression de stratifiés UD épais (6,3 millimètres d'épaisseur nominale) dans des formes avec un rayon de courbure serré (12,7 millimètres). Pour répondre aux exigences, la pièce a utilisé une couche quasi-isotrope de ruban UD en fibre de carbone à module intermédiaire (IM7 ; Hexcel ; Stamford, Connecticut, États-Unis). Les couches extérieures de tissu en fibre de verre style 108 et de fibre de carbone à module standard Solvay THORNEL T650 dans un tissu satiné à 8 faisceaux protègent les fibres UD et empêchent la corrosion galvanique du côté qui s'accouple à une pièce métallique. L'utilisation de la résine époxy Solvay CYCOM 5320-1 a permis des cycles de durcissement isothermes plus courts (≤ 30 minutes) avec un post-durcissement autonome de 2 heures à 177°C.
La partie du défi des vagues a été moulée à l'aide de la cellule de travail PtFS de Boeing et des faces de moule en acier P20 avec des joints intégrés sous vide et en résine. La cavité de l'outil était plus fine que l'épaisseur nominale du stratifié pour tenir compte de la variation de la teneur en résine du matériau, maintenant la pression hydrostatique interne pour les pièces de haute qualité.
Trois paramètres de procédé ont été testés, dont le formage à froid (plis de préformage sans chaleur), le pré-consolidation à chaud et le préchauffage de la préforme. Le formage à froid a été rejeté car il prend du temps et n'est pas utile. Pour la pré-consolidation, les stratifiés ont été ensachés sous vide sur une plaque avec un reniflard en fibre de verre tissé et dégonflés sous vide complet dans un four à 116°C pendant 40 minutes. Bien qu'un préchauffage infrarouge automatisé soit standard pour la production industrielle, dans ces essais, le préchauffage consistait à placer la préforme dans le moule chaud (179°C) et à fermer autant que possible sans toucher pendant 3 minutes. La pièce a ensuite été moulée par compression.
L'essai 8 sur les neuf terminés (#0-8) a produit la pièce de la plus haute qualité, principalement attribuée à la pré-consolidation. Les échantillons prélevés sur celui-ci présentaient une épaisseur (un problème avec d'autres pièces) et une qualité de stratifié avec un volume de fibres de 59 à 63 % et une teneur en vides de 0 à 0,6 %.
Piste 3 :nervure TP en forme de vessie et canal C
RAPM a choisi la nervure TP-RAPM-002 des essais de développement de fabrication pour démontrer le moulage par compression en une seule étape de la matière première à la pièce complexe finie, et le canal incurvé TP-RAPM-003 pour une approche en deux étapes. Boeing St. Louis a moulé la nervure -002 à l'aide d'une presse Accudyne Systems (Del., États-Unis) et consolidé les ébauches pour le canal C -003 à l'aide de l'équipement PtFS. Dans une deuxième étape, ATC Manufacturing a estampé les ébauches du canal C en pièces.
Pour la nervure -002, RAPM a utilisé du ruban UD de 12 pouces de large fourni par Solvay :fibre de carbone 12K AS4D (Hexcel, Stamford, Connecticut, États-Unis) renforcée de polyéthercétonecétone (PEKK). Le tissu utilisé à canal C -003 de Cramer Fabrics Inc. (Dover, N.H., États-Unis) :3K AS4 (Hexcel) fibre de carbone non dimensionnée dans un sergé 2x2, enduit de poudre de polyétheréthercétone (PEEK) ; le poids surfacique des fibres est de 250 grammes/mètre carré; la teneur en résine est de 42 %.
Problèmes de formation de thermoplastique (TP)
Les composites TP sont traités à des températures plus élevées que les thermodurcissables, par exemple 390 °C pour le PEEK et 375 °C pour le PEKK, ce qui présente un certain nombre de problèmes. Les matériaux d'outillage pouvant supporter ces températures de processus élevées sont limités. De plus, le grand delta de température entre le traitement et l'enlèvement des pièces rend difficile le maintien d'une température d'outil uniforme. Le remède est des bains de chaleur et/ou des montées et descentes plus lentes, qui allongent les temps de cycle.
Les températures élevées présentent également un problème de coefficient de dilatation thermique (CTE). Le CTE du matériau d'outillage est souvent différent de celui du stratifié TP, ce qui peut entraîner le retrait du stratifié TP de l'outil, réduisant la pression appliquée et empêchant la consolidation complète. De plus, le CTE du stratifié TP est constant le long de la fibre de carbone mais une courbe bilinéale perpendiculaire à la fibre. Cela se traduit par un retrait différent dans le plan et hors du plan lorsque le stratifié TP chauffe et se refroidit et doit également être pris en compte dans la conception de l'outillage.
Les stratifiés TP peuvent également rétrécir par rapport à l'outillage car le volume de résine diminue avec le passage du liquide au solide. C'est pendant cette phase de refroidissement, lorsque la cristallisation critique de la matrice de résine se produit, qu'un contrôle précis de l'uniformité de la température et de la pression du stratifié est requis pour garantir des propriétés de haute qualité dans la pièce finie.
Un autre problème est que les outils doivent être complètement scellés pour contenir le liquide TP fondu pendant le moulage. « Sceller un outil entre 375 °C et 390 °C est difficile car très peu de joints conformables peuvent supporter cette température et TP formant des pressions de 300 à 500 psi ou plus », explique Hahn. « Nous sommes limités à des joints métalliques ou à des outils métalliques assortis pour fournir les caractéristiques d'étanchéité. L'outillage en élastomère serait incroyablement bénéfique, mais tous les élastomères actuels se décomposeront aux températures de formage TP. »
Boeing St. Louis avait besoin d'un nouvel outillage pour créer une pression horizontale sur les éléments verticaux de la nervure lors de la consolidation dans une presse hydraulique qui n'avait qu'un actionnement vertical. Sa solution était une vessie en aluminium mince (un système similaire a été utilisé pour former TP-RAPM-003, Fig. 5). Pressurisée avec du gaz argon inerte à haute température, la vessie s'est dilatée pour appliquer une pression uniforme sur toutes les surfaces des pièces pendant la consolidation.
Les outils supérieurs et inférieurs étaient fabriqués en acier inoxydable 410, ce qui correspondait au CTE dans le plan du stratifié en fibre de carbone UD/PEKK. Pendant le cycle de pressage, l'outil supérieur avec la vessie en aluminium est descendu et a lentement pressé le drapage dans la cavité femelle de l'outil inférieur. La vessie était sous-dimensionnée de 30 % par rapport à l'épaisseur finale de la pièce pour s'adapter à la majeure partie de la préforme de bande non consolidée dans ce processus en une seule étape. Cet outil a été monté dans une presse conventionnelle avec des cartouches chauffantes électriques, câblé dans 12 zones contrôlées indépendamment - plus les six zones principales du plateau de presse - pour contrôler la température de surface de l'outil dans les ailes et l'âme de la nervure.
Ces essais de formage ont produit des pièces composites avec des résultats NDI passables. Cependant, la conception de l'outil de la vessie nécessite un développement supplémentaire pour améliorer la formation du drapage dans les rayons intérieurs serrés de la pièce et également pour maintenir une épaisseur de surface uniforme.
Consolidation des flans de tissu PEEK
Pour le canal C incurvé TP-RAPM-003, le tissu sergé PEEK 2x2 enduit de poudre utilisé avait un facteur d'encombrement relativement élevé. Boeing St. Louis first consolidated the layup, which dropped from 32 to 24 plies along the length of the part, into a flat blank with a tapered cross-section, and then sent the blanks to ATC Manufacturing, which stamped the final part with vertical flanges.
As with the rib, Boeing used a forming bladder and steel top and bottom tools. The bladder was changed to AZ31 magnesium, which better resists rupture versus aluminum. The C-channel tool was designed to operate within the Surface Generation PtFS forming cell to enable more rapid heating and cooling versus the conventional press with cartridge heaters used for the rib.
The C-channel tooling approach was developed to increase flexibility for multiple parts. The layup was placed onto the bottom tool, which was heated to the material’s glass transition temperature (Tg ) to maintain pliability without melting. A volume reducing frame that included a pressure-sealing gasket was placed on top of the bottom tool, leaving a cavity slightly larger than the part layup (Fig. 5). Heat and hydraulic pressure were applied from the top tool through the bladder to the layup. Once at forming temperature, argon gas was applied to the bladder, forcing it down into the frame cavity to apply pressure to the tapered blank. The tool temperature was then increased through the melt phase of the material while maintaining bladder pressure, which prevented material from flowing across the lower tool while in melt phase.
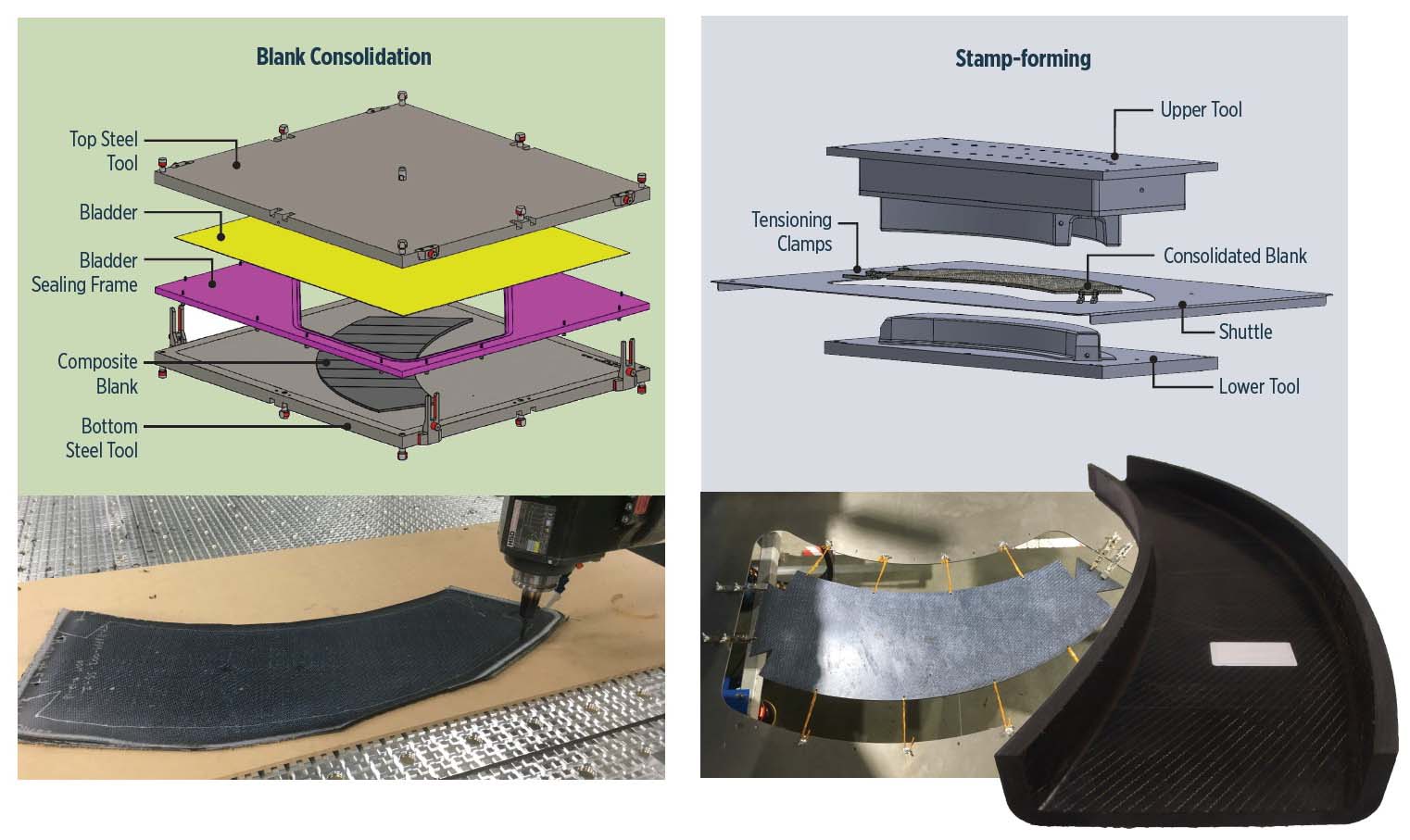
Preforming cycle time comprised 55 minutes for bladder and TP charge to reach process temperature and 30 minutes to cool below the PEEK crystallization temperature. Pressure ranged from 1.4 to 9.7 bar and was maintained manually from a high-pressure tank with a valve. With the recent incorporation of a pressclave system into the PtFS cell, autoclave-like control of vacuum and pressure (±3 psi) in the press mold cavity will be automated in the future.
TP stamp-forming
Consolidated blanks for the -003 C-channel were sent to ATC Manufacturing for stamp-forming, in which the blank is heated sufficiently above melt temperature to ensure polymer flow. It was then transferred to a rapidly closing press to form and cool the part quickly. The forming tool in the press is kept at constant temperature, enabling rapid cycle times by eliminating ramp-up and cool-down. The tool temperature must be between melt temperature and Tg to develop the required level of thermoplastic matrix crystallinity in a short time, yet ensure the part can be removed without deformation. A series of blanks with implanted thermocouples was used to validate the complete thermal cycle for stamp-forming the C-channel.
Forming simulations using Aniform software (Enschede, Netherlands) showed the highly drapable PEEK fabric blank still posed a risk of wrinkling in compression areas, namely the inner (smaller radius) flange. Thus, a tensioning system (Fig. 5) comprising shuttle plate and clips held the blank in tension as the matched metal tools closed to form it. Despite this, the flange face in compression still showed buckling as fiber was pushed inward at the inner radius. “All three RAPM tracks struggled to make this part,” Hahn contends. “Its geometry was extreme, and not so indicative of a real part, but more designed to push what we could achieve in formability.”
The manufacturing development trials led to challenge and transition parts that included multiple versions of the TP-RAPM-008 skin access panel, the TP-RAPM-013 rib with joggles on the flanges and a bladder study using three different geometries of the TP-RAPM-017 panel (Fig. 2). Boeing St. Louis produced all of these except for the TP-RAPM-013 rib, which ATC produced. “Even though this part was made with UD tape, which is typically more challenging to form versus fabric, we were able to form these parts very well,” says Trevor McCrae, R&D director for ATC Manufacturing. Overall, the TP forming trials showed that stamp-forming can produce complex geometries that might not be possible with conventional compression molding.
Learning to cut cost vs. aluminum
RAPM has demonstrated novel forming capability in all three tracks and amassed numerous lessons learned, ranging from how to position pad-ups to prevent slippage during compression molding to guidelines for part geometry to maximize quality and minimize tooling cost. “Understanding the effects of out-of-plane features, radius-to-thickness ratio and distance between geometric details becomes key as you move to small parts,” Hahn observes. “Standardizing features such as radii, curves and flange angles can help mitigate cost drivers, for example, reducing tooling costs, the number of forming trials during development and the need for multiple scans during NDI (nondestructive inspection) by enabling a standard AUSS shoe for a family of parts.”
Another cost driver RAPM highlighted was the time-consuming pre-consolidation step during TS prepreg compression molding. “Low-bulk and higher resin content prepregs widen the process window and increase repeatability for high-quality parts,” Hahn explains. “Solvay has developed a patent-pending ‘transformer film’ which can be applied to lower-impregnation prepregs before compression molding as a method of guaranteeing hydrostatic pressure in the mold cavity during consolidation.”
Although RAPM won’t officially end until fall 2020, followed by additional published results, findings so far for selected parts, which are based on real defense programs, show that composites can compete with machined aluminum (Fig. 6). Though the selected resin infusion and TP parts reduce recurring costs — e.g., materials, machine time, etc. calculated over total parts per family assuming non-recurring infrastructure is in place — the TS-RAPM-012 wave assembly actually shows a 7% increase vs. machined aluminum. However, it does achieve desired weight savings, and at a premium that is actually within the margin mandated by Hendrix:“No one is going to pay 2X for the weight savings composites offer; they must cost within 10 percent of aluminum.” However, he does concede, “There are still non-recurring time and cost issues to figure out, such as tooling and the development required to successfully form the shape.”
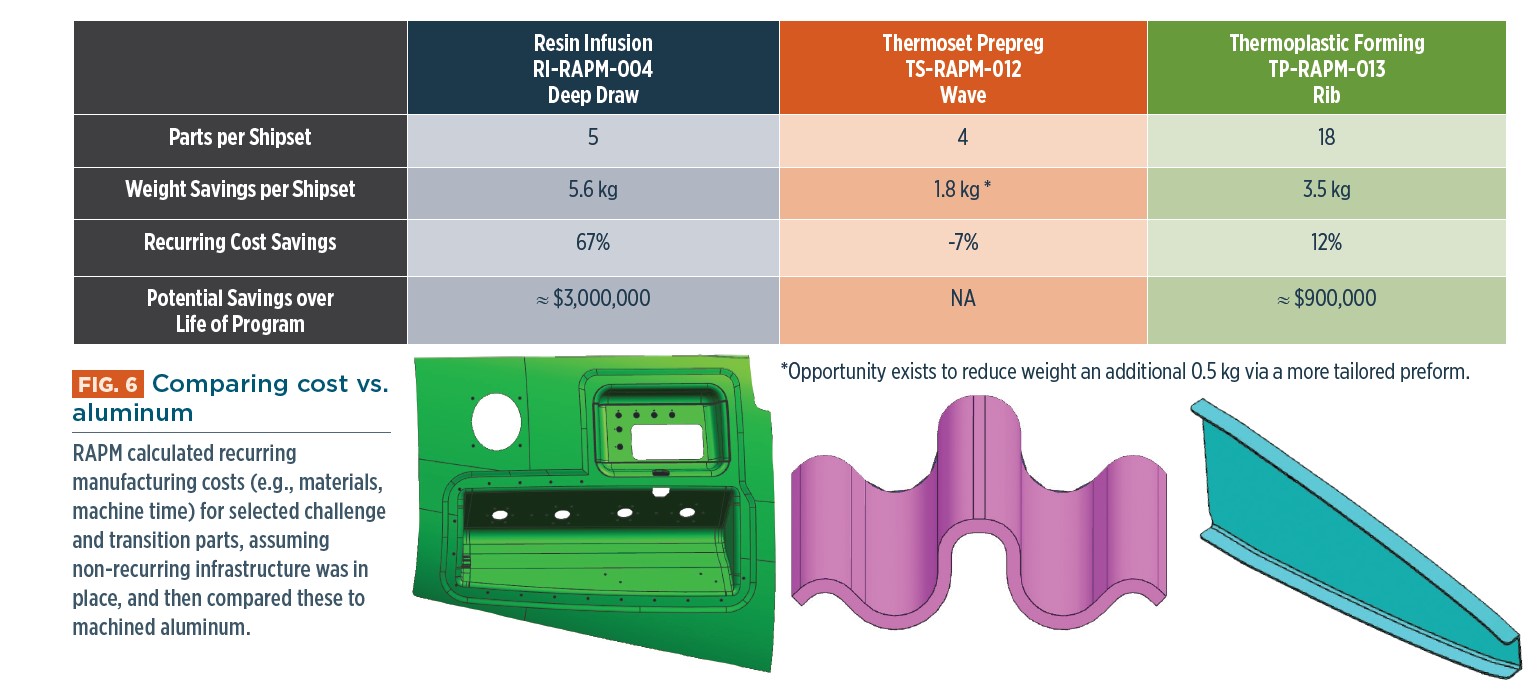
Expanding options
Although resin infusion wins for large parts, says Hahn, TS and TP stamping look pretty good for small parts. “Initial tooling cost for resin infusion is hard to overcome unless the metal parts are very complex, requiring a lot of machining,” she explains.
“Thermoplastics look good for high volume, but a subcontractor for a given program might not be set up to do thermoplastics. However, thermoset stamping might be a very good option, even for low-volume replacement parts. Because defense applications are so wide-ranging, it is important to have more than one material and process in a trade discussion.” Hahn notes that RAPM has opened up new materials and proven aerospace materials can work in automotive-type processes. “We also brought in new manufacturers.”
Hendrix agrees that RAPM’s aerospace and automotive manufacturing exchange was beneficial. Further, he was impressed with Solvay’s and SGL’s ability to form complex shapes without fiber distortion or other defects. “What it takes to make aesthetic auto parts actually has benefits,” he concedes. “You can’t have wrinkles or bad surface finish; they have to be perfect. But it still took multiple trials and significant development for them to form the RAPM parts. I’m not sure defense programs will want to invest in this non-recurring engineering if they’re dealing with small quantities. The economics will be on a case-by-case basis, but tooling and development remain issues we need to address.” Hahn adds, “We are publishing lessons learned, enabling more informed trade studies with expanded options and establishing a reasonably open basis for industry discussion.” CW will continue this discussion with an update once RAPM wraps up later this year.
Résine
- 6 façons de réduire le coût de l'impression 3D
- La question de la maintenance du contrat – Partie I
- Fabrication de composites :la fabrication de matériaux composites
- Retracer l'histoire des matériaux polymères, partie 13
- Les avantages d'un programme de palettes d'entreprise
- L'ACMA publie le programme 2020 de la Conférence sur les composites thermoplastiques
- La keynote SAMPE 2018 se tourne vers l'avenir des composites
- Le coût de l'usinage CNC
- La valeur du moulage de précision (Partie 2)