Avancer sur le démonstrateur multifonctionnel de fuselage (MFFD)
La réduction des émissions de carburant et de la consommation d'énergie, ainsi que la capacité de produire des avions commerciaux monocouloirs à un rythme d'au moins 60 par mois, sont le moteur du développement technologique du partenariat européen Clean Sky 2 pour la prochaine génération d'avions qui décolleront en 2035 et au-delà. . Des composites légers et des processus de fabrication plus rapides et plus respectueux de l'environnement font de ces objectifs une réalité, en particulier pour le projet Multifunctional Fuselage Demonstrator (MFFD).
Le principal livrable de ce projet, mené par Airbus (Hambourg, Allemagne) avec des partenaires du monde universitaire et de l'industrie aéronautique, est un démonstrateur de canon de fuselage d'avion commercial monocouloir en composite thermoplastique de 8 mètres de long, qui sera produit par 2022. Le MFFD est l'une des trois sections de fuselage à grande échelle produites au sein de la plate-forme de démonstration d'avions innovants (IADP) des grands avions de ligne (IADP) de Clean Sky 2.
Lancé en 2014, les objectifs du projet MFFD sont les suivants :
- Activer des taux de production de 60 à 100 avions par mois
- Réduire le poids du fuselage de 1 000 kg
- Réduire les coûts récurrents de 20 %.
Pour atteindre ces objectifs, des dizaines de projets individuels et de lots de travaux sont en cours de réalisation, avec deux structures principales en cours de production :une coque supérieure de fuselage et une coque inférieure de fuselage, qui seront soudées ensemble pour former le démonstrateur final. En fait, l'assemblage sans poussière (sans attaches ni trous) par soudage est une composante majeure du programme. Les deux moitiés sont fabriquées à partir du préimprégné thermoplastique en fibre de carbone polyaryléthercétone (PAEK) Toray Cetex TC1225 à bas point de fusion de Toray Advanced Composites (Morgan Hill, Californie, États-Unis). Selon le Dr-Ing. Lars Larsen, responsable des technologies d'assemblage et d'assemblage au Centre aérospatial allemand (DLR ; Augsbourg, Allemagne), les deux moitiés testeront l'utilisation de différentes techniques de fabrication.
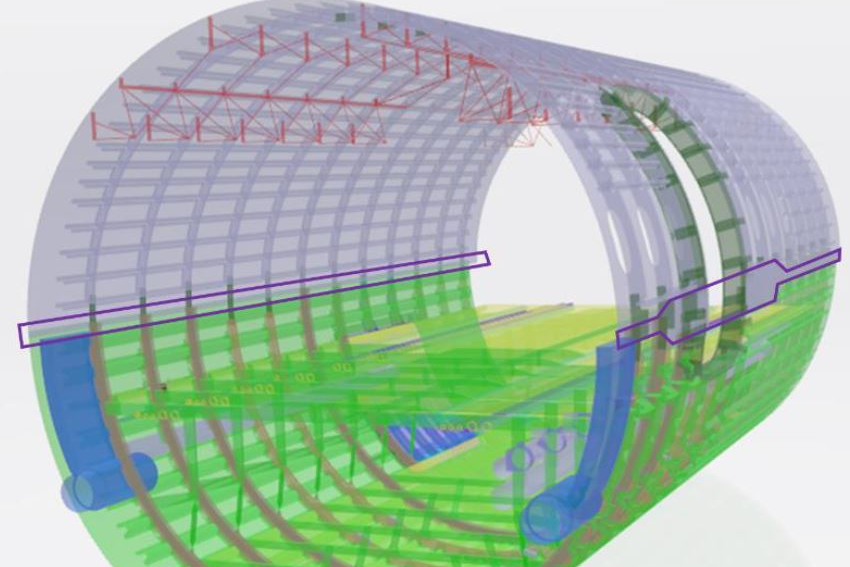
La partie inférieure du fuselage du MFFD est réalisée dans le cadre du projet STUNNING (SmarT mUlti-fuNctionNal and INtegrated thermoplastique fuselaGe), qui a lui-même de nombreux projets en dessous (comme MECATESTERS, axé sur le soudage par induction). La section inférieure comprendra la coque inférieure du fuselage avec des longerons et des cadres soudés, la structure de la cabine et du plancher de chargement et les éléments intérieurs et système pertinents.
STUNNING est dirigé par GKN Fokker (Papendrecht, Pays-Bas) avec des partenaires clés Diehl Aviation (Laupheim, Allemagne), Netherlands Aerospace Center (NLR; Amsterdam, Pays-Bas) et l'Université de technologie de Delft (TU Delft; Delft, Pays-Bas). Le projet vise à développer davantage les processus d'assemblage automatisés, les technologies de fabrication et de soudage thermoplastiques, la conception intégrée et le développement de la fabrication et les architectures de systèmes électriques avancées.
"Notre impact sur l'industrie est double :le niveau d'automatisation que nous appliquons à l'assemblage du démonstrateur et le développement de méthodes durables pour produire des pièces", explique le Dr Bas Veldman, responsable de programme chez GKN Fokker.
Selon un article de Veldman publié en février 2020, l'assemblage modulaire du bas du fuselage est essentiel pour atteindre l'objectif de délais de production rapides. Pour fabriquer la peau principale du fuselage, de grandes préformes en fibre de carbone/préimprégné thermoplastique sont posées par une machine automatisée de pose de ruban (ATL) chauffée par ultrasons ou laser, mais non consolidées in situ. Les détails sont posés par une machine automatisée de placement de fibres (AFP). Des robots placent ensuite les préformes dans un moule de consolidation femelle, et après ensachage, la peau est consolidée dans un autoclave. Selon Veldman, les procédés hors autoclave sont également à l'étude. Les longerons et cadres seront soudés à la peau.
« À l'origine, le plan était de faire fabriquer toutes les pièces cette année », a déclaré Veldman, mais en raison de retards liés au coronavirus, « il est également en train de passer à l'année prochaine. Mais nous avons un certain nombre de pièces qui sont maintenant terminées », y compris de nombreuses petites pièces formées à la presse telles que des clips, des entretoises et des supports qui seront utilisés pour fixer les sièges d'avion et d'autres composants. Mettant l'accent sur la fabrication durable, Veldman ajoute que certains des clips sont fabriqués à partir de chutes réutilisées d'autres pièces du démonstrateur, dans le cadre d'un projet Clean Sky 2 appelé ECO-CLIP.
À partir du début de 2020, le consortium produisant la coque supérieure de 8 mètres de long comprend Airbus, Premium Aerotec (Augsbourg, Allemagne), qui est le responsable de la conception industrielle et structurelle ; DLR, en charge du développement de la technologie de drapage et de soudage; et Aernnova (Vitoria-Gasteiz, Espagne), qui produit les longerons.
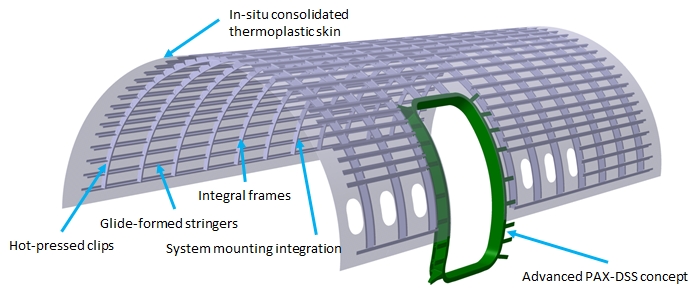
Pour que l'industrie aérospatiale passe à des matériaux thermoplastiques plus coûteux, Larsen déclare :« Nous devons montrer que nous pouvons réduire les coûts pendant la production. » La moitié supérieure du consortium développe une nouvelle technologie avancée de placement de fibres (AFP) avec, notamment, la consolidation in-situ pour le drapage de la peau en fibre de carbone/PAEK, ainsi que l'industrialisation du soudage par ultrasons continu et du soudage par résistance pour l'intégration des longerons, cadres et d'autres composants, améliorant la sécurité et réduisant les coûts. Le DLR construit d'abord une coque de test de pré-démonstrateur de 1 mètre de long pour valider les technologies avant la construction du démonstrateur grandeur nature, et prévoit de fabriquer la peau de la coque de pré-démonstrateur d'ici fin 2020. les longerons est prévu pour début 2021.
Les versions à grande échelle des deux moitiés devraient être terminées d'ici la fin de 2021. Une fois terminées, elles seront soudées dans le démonstrateur final à l'Institut Fraunhofer pour la technologie de fabrication et les matériaux avancés IFAM (Stade, Allemagne).
Résine
- Aller au-delà des bases :apprentissage automatique et AM
- Les avantages de la conception d'avions composites dans des avions de toutes tailles
- Pourquoi l'automatisation est la seule voie à suivre pour la fabrication
- 5 applications robotiques dans l'industrie aérospatiale
- Trois avantages de la migration de la gestion des dépenses vers le cloud
- La première section de fuselage composite pour le premier jet commercial composite
- Au service du monde des composites en Israël et aux États-Unis
- Quelle est la tension directe de la diode ?
- Génération d'azote dans l'industrie aérospatiale