La structure composite thermoplastique remplace les métaux sur les pédales de frein critiques pour la sécurité
L'industrie automobile a converti les pédales d'accélérateur des métaux en thermoplastiques à verre court moulés par injection dans les années 1990. Cependant, les pédales de frein - étant des composants critiques pour la sécurité avec des exigences de rigidité, de résistance et de charge de torsion difficiles - ont pris beaucoup plus de temps à convertir. Le fournisseur automobile de rang 1 Boge Rubber &Plastics Group (Damme, Allemagne) affirme qu'il est le premier fournisseur à atteindre les objectifs exigeants de performance et de coût des OEM pour les pédales de frein en composites thermoplastiques. Une conception unique, trois matériaux différents et un processus de production sur mesure permettent à l'entreprise de produire des pédales plus solides, plus rigides, plus légères et à moindre coût.
Trouver un créneau qui compte
Boge est un développeur et producteur de produits pour l'amortissement des vibrations et le montage du groupe motopropulseur/châssis ainsi que des modules en plastique léger et des pédaliers (y compris des combinaisons de pédales de frein, d'embrayage et d'accélérateur) pour l'industrie automobile. Elle produit des composants automobiles en feuille organique à fibres continues avec des composés de surmoulage de verre court depuis 2008. Elle a ajouté des rubans thermoplastiques unidirectionnels (UD) au mélange en 2018. Grâce à l'innovation continue des processus, la durée du cycle et les coûts ont été réduits et l'activité a augmenté.
« En 2015, mon patron est venu me voir et m'a dit :'Ces changements que vous avez apportés sont sympas, Daniel, mais ce serait bien si vous pouviez trouver un marché plus important avec des volumes de production qui comptent vraiment' », se souvient le Dr-Ing. . Daniel Häffelin, senior manager/chef de l'équipe des poids légers au Boge Global Innovation Center. Une équipe d'ingénieurs de Boge a accepté le défi et a réfléchi à la manière d'augmenter l'efficacité de la fibre pour réduire les coûts et augmenter le chiffre d'affaires.
« La feuille d'organo est un excellent produit, mais vous devez l'utiliser de la bonne manière, uniquement là où c'est nécessaire », explique Häffelin. « Nous avions déjà simplifié notre processus de production, nous ne gagnerions donc pas grand-chose à essayer de réduire davantage les temps de cycle. Nous avons pensé que le meilleur moyen de réduire les coûts était de réduire la quantité de fibre sans fin que nous utilisions en utilisant cette fibre plus efficacement. »
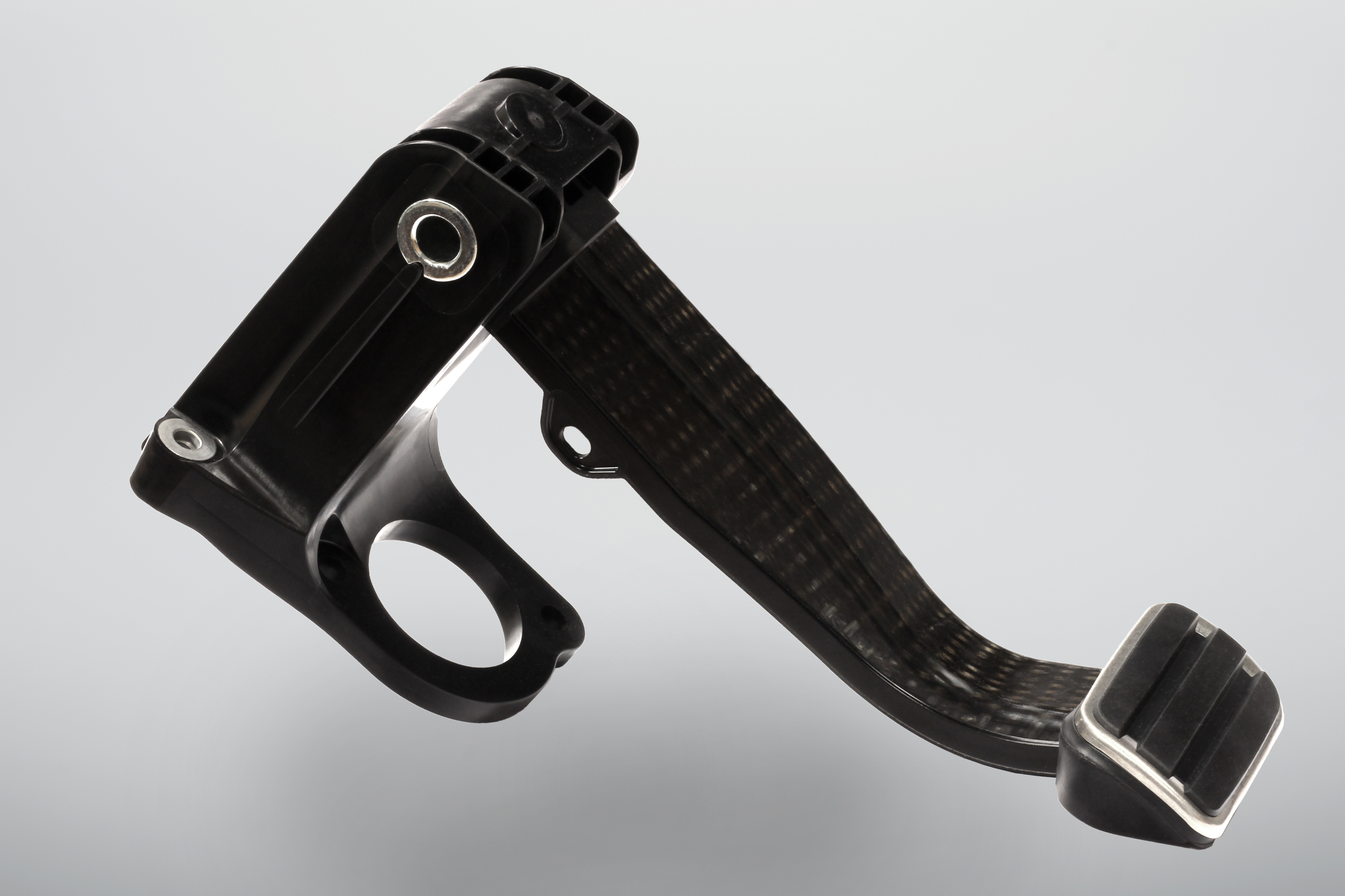
Le simple fait de rendre les pédales plus petites ou plus fines ne fonctionnerait pas non plus car il existe des contraintes pratiques sur la taille et la forme des pédales de frein, sans parler des spécifications de performances difficiles en raison de sa nature critique pour la sécurité. Ce qui était le plus logique était de trouver des moyens de mieux contrôler l'orientation des fibres pour optimiser les propriétés locales dans les zones de la pièce qui ont connu les charges de pointe les plus élevées, offrant des opportunités de réduire l'épaisseur de paroi dans les zones moins critiques.
« Nous avons cherché un moyen de « diriger » localement les fibres afin de pouvoir les placer exactement là où nous en avions besoin pour maintenir la rigidité et la résistance», ajoute le Dr Torsten Bremer, PDG de Boge Rubber &Plastics Group. « Nous savions, en principe, que cela était possible parce que nous avions déjà envisagé des machines pick-and-place utilisées dans les articles de sport et médicaux, mais elles étaient trop chères. C'est à ce moment-là que nous avons décidé que nous avions besoin d'un nouveau processus."
« Nous travaillions déjà avec un équipementier allemand pour trouver des moyens de fabriquer des pédales de frein tout composite répondant à leurs exigences de performances et de coûts », se souvient Burkhard Tiemann, vice-président exécutif du groupe Boge Plastics &Rubber, leader de la gamme de produits – Plastiques. « Nous avons dit à notre client : « Nous allons développer un nouveau processus en utilisant des rubans UD et des feuilles organiques. » Ils nous ont dit : « Si vous pouvez réduire davantage la masse et les coûts, nous le ferons. » C'était notre point de départ. Nous avons fait une grande promesse en 2015 que nous pourrions fournir une pédale de frein tout composite moins chère, plus légère et pouvant être produite en grande quantité. Il nous a fallu trois ans pour peaufiner les détails et livrer nos premiers produits. »
Direction fibre
Les pédales de frein composites doivent répondre aux mêmes spécifications de performance que les pédales en acier ou en aluminium existantes. Cela inclut des exigences spéciales en matière de mode de défaillance avec des charges pouvant atteindre 3 000 newtons et une déflexion semblable à celle de l'acier à charge maximale. Compte tenu de ces exigences et de l'espace restreint disponible pour l'emballage, la structure de coque principale de la pédale, qui supporte les charges maximales, nécessite un renforcement continu en fibres. Par conséquent, l'équipe a décidé d'utiliser une feuille organique pour former l'épine dorsale de la pédale. Des rubans UD seraient ensuite utilisés pour augmenter localement la rigidité/résistance et renforcer les parois intérieures lors des pics de contraintes dans la zone de la pièce qui serait ensuite pliée dans un canal en U lors du préformage. Et dans les zones où une géométrie fonctionnelle comme des nervures était nécessaire, un composé de surmoulage de verre haché a été spécifié. L'équipe a estimé que cette approche hybride augmenterait l'efficacité des fibres tout en réduisant l'utilisation des matériaux, l'épaisseur moyenne de la paroi et la durée du cycle.

L'équipe a commencé un travail de simulation intensif pour optimiser les emplacements des fibres pendant la production. Le travail de Boge reposait sur un programme de recherche allemand financé par l'État de 2011 à 2014 appelé SoWeMa (Software, Tools, and Machine Development for a Fully Automatic and Closed Lightweight Manufacturing Chain).
« La recherche SoWeMa a couvert de nombreuses questions que nous poserions un an plus tard pour notre propre entreprise », explique Häffelin. « Parce que la conception fait partie du savoir-faire de base de Boge, nous avons commencé avec les principes fondamentaux du programme SoWeMa et avons construit nos propres capacités de simulation FE (éléments finis) pour les structures de drapage anisotropes. »
Un domaine d'intérêt était l'optimisation de la topologie combinée pour la superposition de la bande et la structure des nervures. « Nous avons créé un cycle d'itération pour optimiser le placement des rubans et adapter la structure des nervures en conséquence, car les deux sont liés par la rigidité et la résistance de la pièce », poursuit K. Siebe, ingénieur FEA, CRRC Innovation Center. « Étant donné que la combinaison de matériaux de rubans UD, de feuilles organiques et de matériaux à fibres courtes est unique et que leur application est liée à une fenêtre spécifique d'humidité et de température, nous avons construit nos propres cartes de matériaux pour caractériser plus précisément le comportement de ces matériaux lors des tests physiques. ”
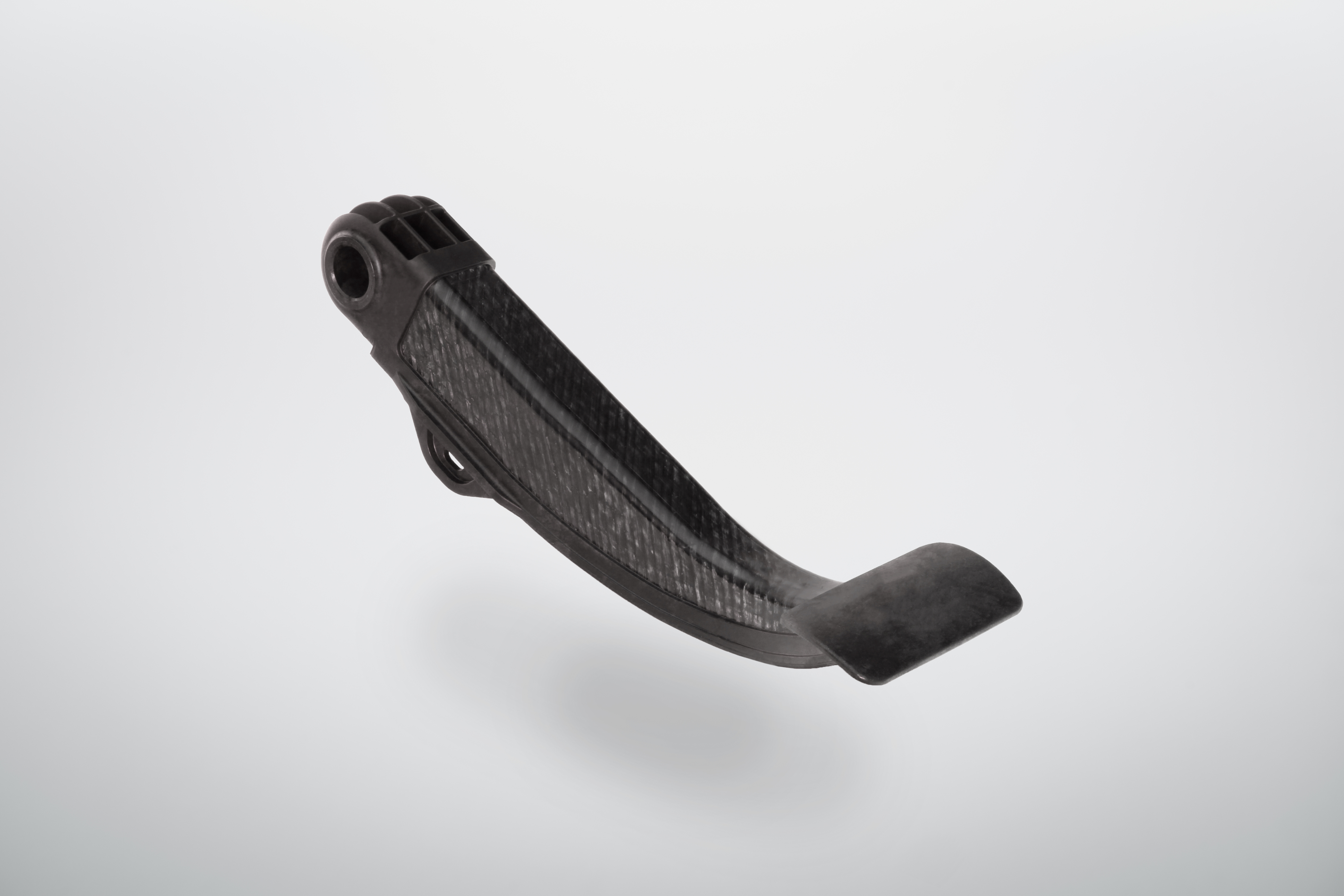
Boge a spécifié la structure des couches et l'architecture des fibres pour chaque matériau sur la base des résultats de la simulation et d'une conception de pédale donnée. Lanxess Deutschland GmbH (Cologne, Allemagne) fournit des feuilles organiques dans des fractions volumiques de fibres (FVF) de 45 à 50 %. Les rubans thermoplastiques UD avec des FVF de 55 à 60 % ont été fournis par Celanese Corp. (Irving, Texas, États-Unis). Les composés d'injection de verre court pour cette application, à 40-60% de fraction en poids de fibres (FWF), ont été fournis par plusieurs sources. Tous les matériaux sont noirs et comportent une matrice polyamide 6 ou 6/6 (PA6, PA6/6). Pour répondre aux spécifications des clients, PA6 est la résine par défaut pour les trois types de composites. Cependant, en fonction des niveaux d'humidité et de température lors de la fabrication, ainsi que des contraintes d'espace et de la géométrie de la pédale, Boge peut également utiliser du PA6/6 pour la résine de surmoulage, car les deux polymères sont suffisamment similaires pour bien adhérer.
Production en trois étapes
Parallèlement à la conception, l'équipe a travaillé sur un processus de production en trois étapes. Dans la première étape, une ébauche de fibre sur mesure est créée en utilisant une feuille organique prédécoupée et préconsolidée comme base stable sur laquelle attacher stratégiquement des bandes de ruban UD alignées sur les chemins de charge pour renforcer la structure de la coque de la pièce. Dans la deuxième étape, l'ébauche est déplacée et séquentiellement chauffée, consolidée et façonnée/drapée. Dans la troisième étape, il est surmoulé avec un composé de verre court pour créer la structure nervurée.
Pour obtenir des temps de cycle rapides, la manipulation robotique était une évidence pour ce système. Une caractéristique clé du processus que l'équipe souhaitait inclure était la flexibilité de placer des bandes de n'importe quelle longueur, dans n'importe quelle orientation et dans n'importe quelle position sur un côté de la coque en feuille organique et de coller ces bandes au laser sur la coque afin qu'elles ne se déplacent pas. dans les étapes suivantes.
Une autre décision prise par l'équipe a été de ne pas préconsolider l'ébauche sur mesure immédiatement après le drapage, mais juste avant le drapage/préformage et le surmoulage. L'équipe a estimé que le matériau devrait de toute façon être réchauffé pendant le drapage/le préformage et que pour être rentable, ils devaient maintenir un temps de cycle total proche d'une minute. Par conséquent, Boge chauffe et consolide le flan juste avant le drapage/préformage en utilisant une augmentation rapide de la température combinée à une pression élevée pour créer une forte liaison mécanique entre le ruban et la feuille organique. Le chauffage s'arrête et la température de la pièce commence à baisser à mesure que l'ébauche consolidée encore chaude se déplace dans la cavité de drapage avant d'être à nouveau déplacée et surmoulée avec des nervures et d'autres caractéristiques fonctionnelles dans une deuxième cavité. Des liaisons mécaniques fortes, avec une pénétration vérifiée de la chaîne polymère, sont obtenues entre les trois matériaux. Aucune finition post-moulage n'est requise.
Pour répondre aux exigences de qualité de ces pièces critiques pour la sécurité, l'équipe a également développé un système rapide, précis et conforme à l'industrie 4.0 qui utilise des capteurs de vision, de force, de temps, de pression et de température qui vérifient le matériau à chaque étape du processus de fabrication. Le système stocke ensuite ces données et les associe au numéro d'identification unique de chaque pédale. Cela garantit une traçabilité à 100 % de tous les matériaux, équipes et paramètres de processus impliqués.
Réalisations à ce jour
Le processus sur mesure, entièrement automatisé et contrôlé par Boge est passé du prototype à la production en série à grand volume en 2018. Produisant une nouvelle pédale environ toutes les minutes, la cellule de fabrication actuelle peut fabriquer jusqu'à 1 million de pièces par an. Les pédales entièrement composites utilisent 33% moins d'organosheet que les conceptions précédentes et l'épaisseur nominale de la paroi est passée de 3 à 2 millimètres. Les pédales sont également 50 à 55 % plus légères, mais satisfont ou dépassent les exigences de résistance de l'acier. Les pédales plus légères améliorent l'haptique de conduite pour les consommateurs et l'ensemble du système est 100% recyclable en fin de vie. Avec le procédé actuel, les pédales composites sont à parité de coût par rapport à l'aluminium et un coût légèrement plus élevé que l'acier. D'autres applications automobiles et sportives sont en cours de développement.
Que réserve l'avenir alors que les constructeurs automobiles transfèrent leurs ressources vers l'électrification des flottes ? « Alors que les systèmes d'actionnement électromécaniques [systèmes d'actionnement électromécaniques] et l'électrification du groupe motopropulseur deviennent plus courants, les pédales d'accélérateur pourraient disparaître, mais les pédales de frein resteront", se souvient Häffelin. "Cependant, nous verrons probablement une plus grande intégration de l'électronique, y compris des capteurs, dans les pédales de frein. Cela augmentera considérablement la complexité des pièces, rendant les composites encore plus compétitif que les métaux."
L'utilisation des matériaux, les étapes du processus et les critères d'équipement sont expliqués plus en détail dans CW Article de suivi de janvier 2021 :"Un processus sur mesure produit une pédale de frein composite toutes les minutes."
Résine
- Un composite de nylon renforcé de fibres longues remplace le boîtier de moteur en aluminium
- Composite thermoplastique renforcé de fibres continues entièrement fabriqué à partir de ressources naturelles
- Solvay augmente la capacité des composites thermoplastiques
- Le consortium cible des solutions pour les structures composites thermoplastiques en fibre de carbone
- INEOS Styrolution va construire un site de production pour le composite thermoplastique StyLight
- Xenia présente des composés composites thermoplastiques CF/PP
- Tuyau composite thermoplastique en plein essor en haute mer
- composite thermoplastique TenCate qualifié NIAR NCAMP
- TenCate célèbre l'assemblage d'un consortium de composites thermoplastiques au Brésil