Les plaques flexibles en fibre de carbone permettent des chaussures hautes performances
Les plaques de semelle intermédiaire en fibre de carbone, les tiges et d'autres composants améliorent les performances et réduisent le poids des chaussures de sport de haut niveau depuis des années. Cependant, explique Junus Khan, fondateur et président de Carbitex Inc. (Kennewick, Wash., États-Unis), même avec les composites, les développeurs de chaussures doivent généralement faire des compromis lorsqu'il s'agit de choisir le matériau pour les plaques de semelle intermédiaire :le choix est entre un matériau suffisamment rigide pour soutenez le pied pendant l'activité requise, même s'il peut être rigide et lourd, ou un matériau léger et flexible, mais n'offre pas autant de soutien. Soit le choix, soit un matériau de compromis qui se situe quelque part entre les deux, rend la chaussure - et le porteur - intrinsèquement inefficaces, quelque chose que Carbitex dit avoir été capable de surmonter grâce au développement de sa gamme de produits de matériaux composites flexibles en fibre de carbone/thermoplastique.
Cependant, note Khan, il n'avait pas initialement pour objectif de transformer l'industrie de la chaussure. Il y a un peu plus de 10 ans, Khan, qui a une formation en économie mais qui a découvert les composites en fibre de carbone en travaillant dans l'industrie automobile, s'est penché sur le marché des bagages et s'est demandé pourquoi les fabricants de bagages essayaient d'imiter l'esthétique de la fibre de carbone. en utilisant du nylon balistique et d'autres tissus, au lieu d'utiliser de la fibre de carbone réelle. Incapable de trouver une entreprise qui fabriquait un produit en fibre de carbone souple et souple adapté au marché des bagages, il a décidé de s'essayer à le fabriquer lui-même.
En 2010, Khan a commencé à étudier divers matériaux en fibre de carbone dans son garage pendant son temps libre, et en 2011, ses premiers matériaux et processus ont été testés au laboratoire national du département de l'Énergie des États-Unis, Pacific Northwest. À ce stade, dit-il, « j'avais un concept viable et une meilleure compréhension de l'espace matériel », et il a décidé de transformer ce concept en une entreprise, dans le but de poursuivre le développement et finalement de vendre le matériau. Carbitex Inc. a été fondée en février 2012.
Des bagages aux chaussures
Khan explique que d'autres sociétés ont développé des tissus en fibre de carbone semi-flexibles en suspendant un seul pli de tissu entre deux films thermoplastiques. "Cependant, lorsque vous tirez ce matériau sous tension, le mode de défaillance est que les films arrachent la surface du carbone", dit-il, ce qui signifie qu'une tendance au délaminage peut entraver la quantité de flexibilité réelle disponible pour le stratifié.
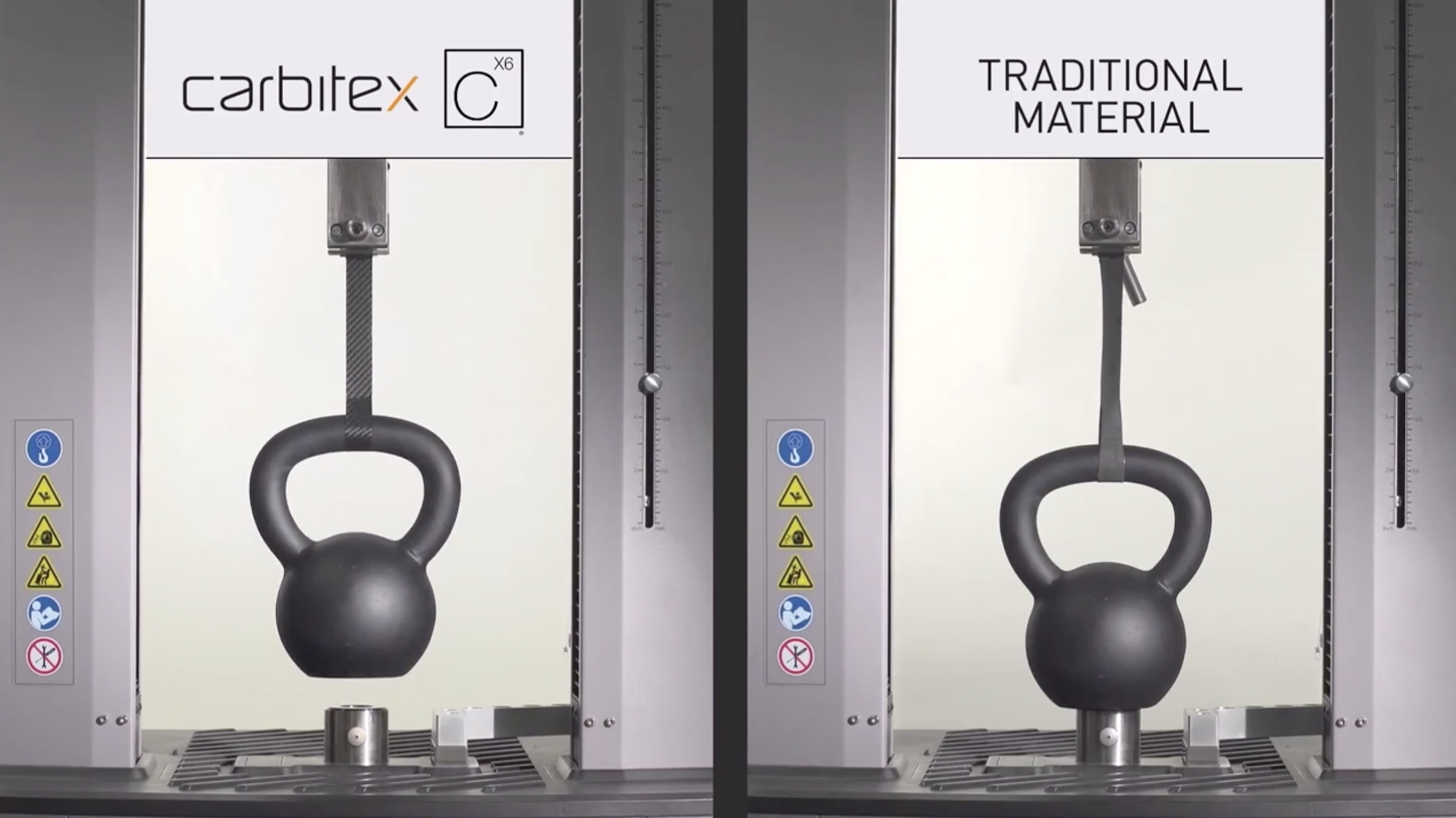
Le produit CX6 de Carbitex, son offre de produits originale, est également un simple pli de tissu en fibre de carbone laminé entre des films thermoplastiques. Mais, dit Khan, le tissu est d'abord traité avec un liant spécialement développé qui, selon un brevet américain Carbitex déposé en 2015, confère au tissu laminé "une flexibilité similaire au tissu non laminé avec des films polymères, ainsi qu'une adhérence et une résistance à la traction améliorées". Il ajoute : « Lorsque vous tirez notre matériau CX6 en tension, le mode de défaillance est la rupture des fibres, pas le délaminage du film. Vous obtenez vraiment cette force de marque de la fibre de carbone. Le matériau aurait également des propriétés d'étirement très faibles par rapport à d'autres matériaux composites, pour lesquels Carbitex a trouvé une utilisation dans des composants de chaussures fabriqués avec précision avec un transfert de puissance amélioré.
Carbitex a commencé à vendre son premier produit CX6 dans l'industrie des bagages et des sacs à main à des entreprises comme Tumi (South Plainfield, N.J., États-Unis), comme Khan l'avait initialement prévu de le faire. Rapidement, cependant, Carbitex a commencé à recevoir des demandes de renseignements d'une variété d'autres industries, telles que l'électronique grand public. Alors que la croissance était passionnante, dit-il, "En même temps, nous avons commencé à réaliser que nous nous éparpillions très légèrement." Il y a environ trois ans, l'entreprise a pris la décision de se concentrer sur un marché qui présentait le plus de potentiel :les chaussures.
Aujourd'hui, Carbitex fournit ses plaques en fibre de carbone à l'ensemble de l'industrie de la chaussure, où elles sont utilisées dans le snowboard, le cyclisme, les sports nautiques, la course à pied, la randonnée, les produits de mode et plus encore. L'une des applications de chaussures les plus récentes et les plus performantes de l'entreprise est une chaussure de football lancée par Adidas à l'automne 2020.
AFX et DFX :Transformer les chaussures
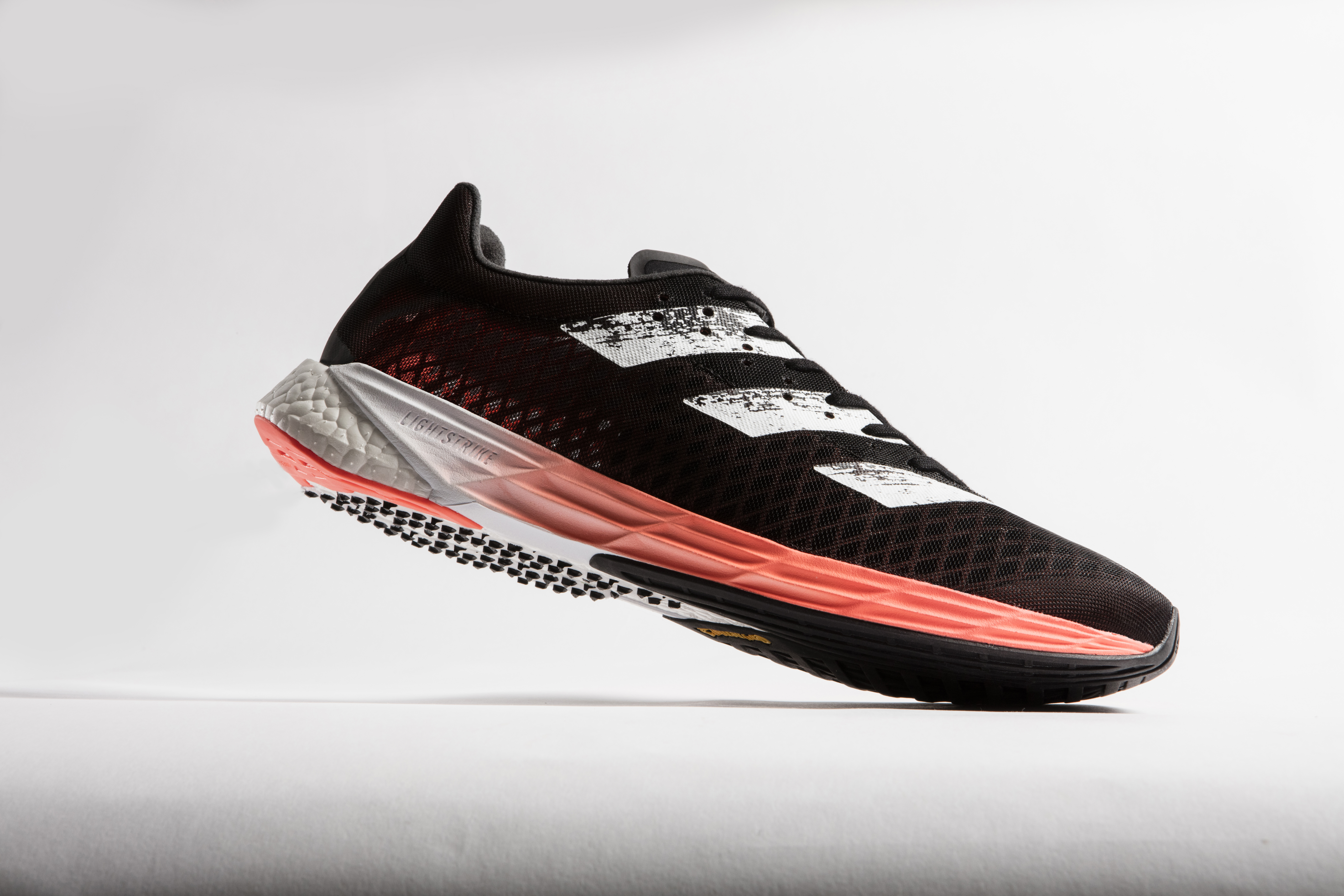
Au cours des dernières années, Carbitex a lancé deux nouvelles technologies composites, appelées AFX et DFX. Selon Khan, contrairement aux « composites typiques » dont la rigidité est contrôlée par l'orientation des fibres et la longueur du pli, la rigidité d'une feuille de fibre de carbone Carbitex est uniforme sur toute sa longueur. Là où d'autres composites peuvent être constitués d'un type de système de résine et de fibres, dit-il, les matériaux de Carbitex sont plus complexes, impliquant des couches complexes de feuilles de polymères et de couches de tissu, pour obtenir les propriétés de flexibilité souhaitées. « Une version très simple de notre matériau AFX pourrait avoir deux types différents de fibre de carbone pris en sandwich entre deux ou trois autres types de polymères différents », dit-il. "C'est un système de superposition complexe, et vous devez comprendre comment ces couches doivent se réunir pour les propriétés [requises]."
Généralement, le processus de fabrication commence par la superposition de tissus, qui peuvent être traités avec des liants ou d'autres traitements de tissus, et des feuilles de polymère dans un panneau. Une variété de fibres provenant de différents fournisseurs sont utilisées, bien que Khan affirme que la plupart des produits de Carbitex comprennent des fibres de Toray Composite Materials America (Tacoma, Wash., États-Unis) et étendent souvent des tissus de remorquage de Hexcel (Stamford, Connecticut, États-Unis). Les polymères varient également selon l'application, mais sont généralement thermoplastiques pour la flexibilité et la formabilité, "bien que parfois ce ne soit pas complètement thermoplastique, selon l'application", ajoute-t-il.
Ces panneaux sont consolidés dans des presses chauffées; une fois retirées, les pièces individuelles sont découpées au jet d'eau et formées. La fabrication en panneaux plutôt que la pose de pièces individuelles conduit à un rendement plus élevé que les poses traditionnelles, explique Khan.
Processus de fabrication
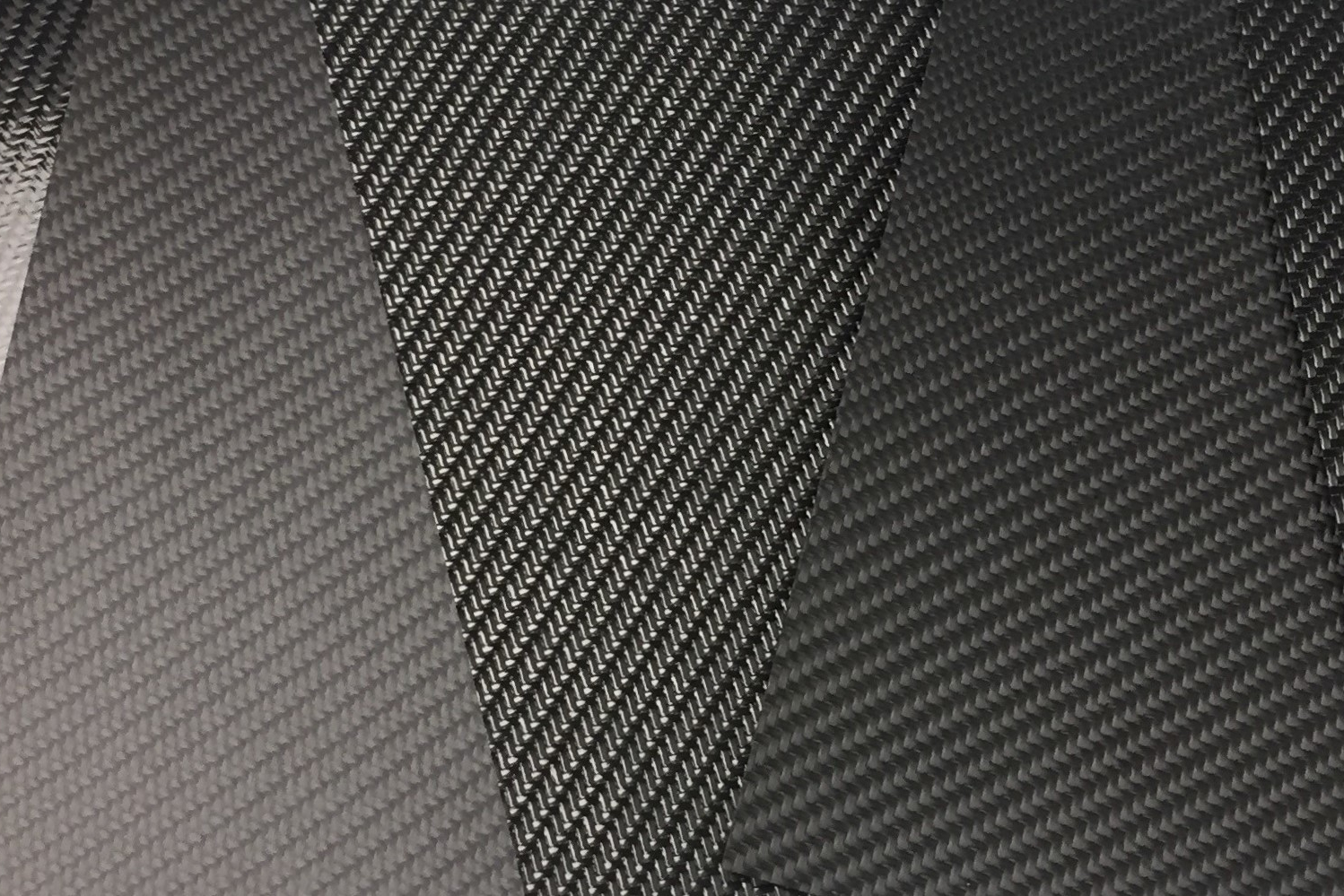
Tout d'abord, des couches spécifiques de tissus tissés, de préimprégnés et de films polymères sont empilées ensemble dans un panneau.
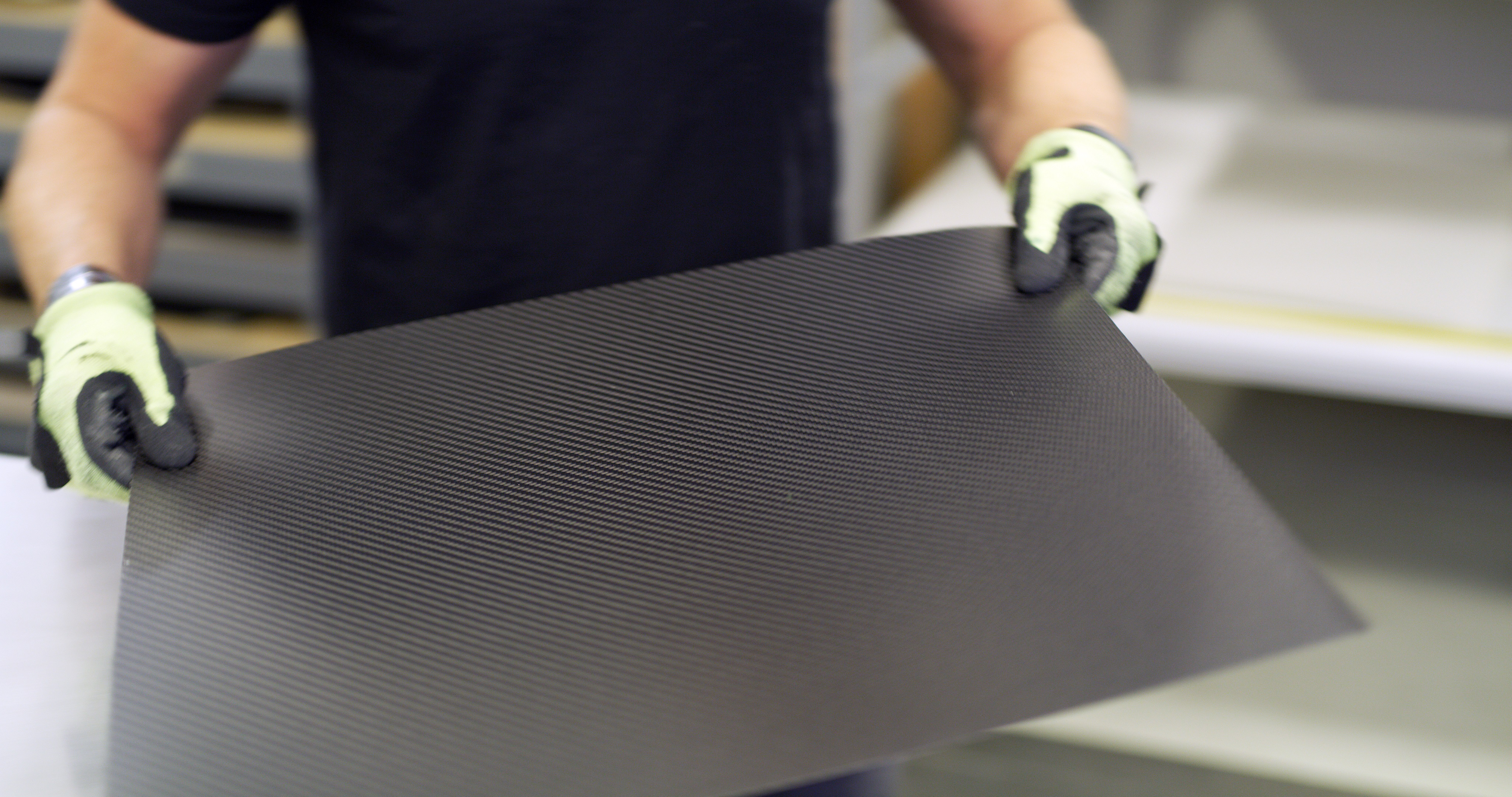
Ensuite, le panneau est consolidé dans une presse chauffée.

Des composants spécifiques sont découpés dans les panneaux durcis par jet d'eau.
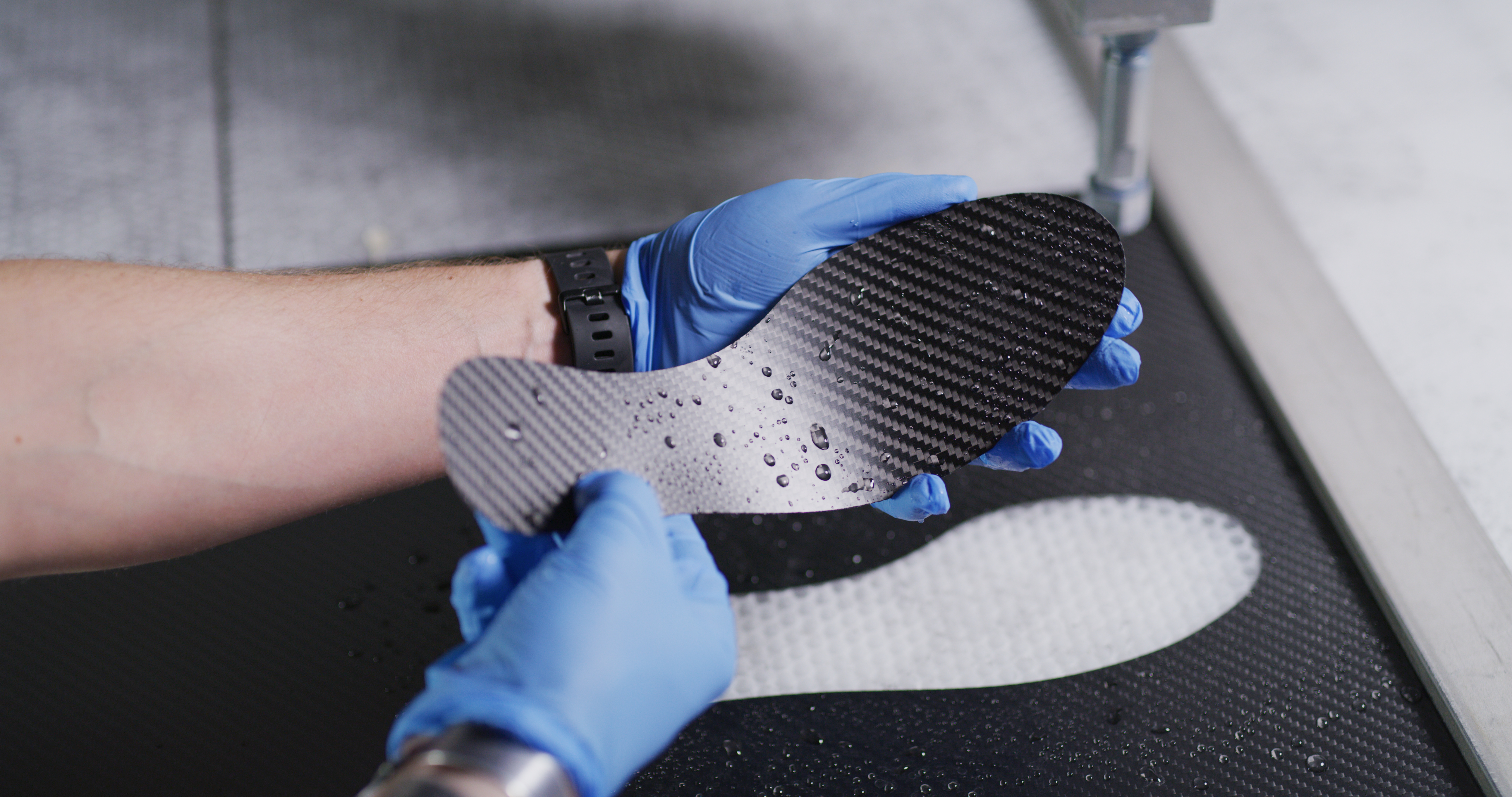
Éviter la superposition de pièces individuelles permet d'obtenir un débit plus élevé, dit Carbitex.

La semelle intermédiaire en composite de fibre de carbone résultante (sur la photo est un composant DFX) sera assemblée dans une application de chaussure finale.
Précédent SuivantParallèlement à l'équilibre entre rigidité et flexibilité, le développement de chaussures présente un défi supplémentaire :le pied humain ne peut se plier que dans une direction sans s'étendre ni se casser, les matériaux de la chaussure doivent donc avoir la polyvalence de se plier dans certaines directions mais pas dans d'autres . Carbitex y parvient, dit Khan, grâce à un flambage ou à une flexion contrôlés du
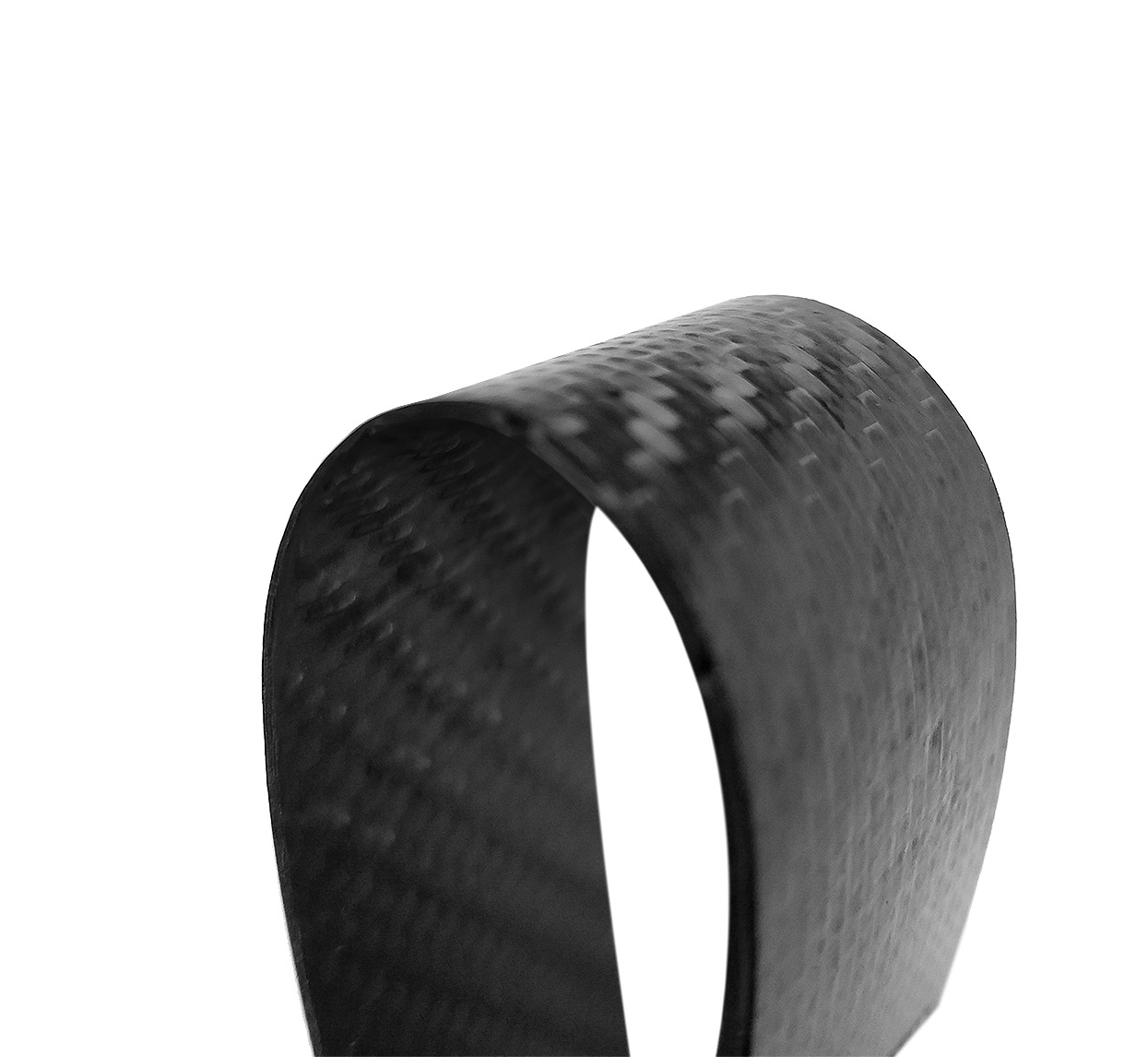
stratifié. "Généralement dans les composites, le mot" flambage "est attribué à une défaillance", dit Khan, "mais nous avons trouvé des moyens de permettre à la fibre de se déformer mais pas de se casser." Cette invention, ajoute-t-il, a été initialement réalisée par accident, car un collègue s'est rendu compte qu'une certaine combinaison de couches de fibres et de polymères avait donné lieu à un matériau qui se déformait dans une seule direction. "Nous avons réalisé qu'il devait y avoir une sorte d'avantage à cela", dit Khan, "nous avons donc commencé à retirer les couches, pour savoir comment cela s'est produit et ensuite comprendre comment nous pouvions le faire exprès."
Le produit résultant s'appelle AFX, où le "AF" signifie "Asymétriquement Flexible", indiquant qu'il se plie dans une direction mais est complètement rigide dans l'autre. Selon un dépôt de brevet de 2018, le produit AFX de Carbitex comprend une couche de tissu tissé, une couche de préimprégné et, entre les deux, au moins une couche de polymère, qui sont combinées en un assemblage qui est ensuite façonné et durci. "L'agencement en couches a une résistance élevée à la flexion dans une première direction et une faible résistance à la flexion dans une deuxième direction opposée", indique le brevet.
"Notre technologie permet le niveau de rigidité et de protection dans la direction que vous souhaitez", ajoute Khan. Une chaussure de randonnée incorporant une semelle intermédiaire en fibre de carbone AFX, par exemple, comprend le soutien et la rigidité nécessaires pour protéger le pied contre les flexions dans le mauvais sens sur des terrains inégaux ou verticaux, mais « quand vous allez plier le pied pour marcher sur un terrain plat, [ la botte est] tout aussi flexible que, disons, une chaussure de course », dit-il. AFX est également plus léger que la combinaison de matériaux de planche et de caoutchouc qui sont souvent utilisés pour renforcer les chaussures de randonnée.
Le troisième produit de Carbitex s'appelle DFX, un dérivé d'AFX qui signifie « Dynamic Flexible », ce qui signifie que la rigidité du matériau à l'intérieur de la chaussure change au fur et à mesure que le pied bouge. Avec DFX, "vous pouvez avoir [une chaussure] qui va être super flexible à certains angles, puis devenir progressivement ou exponentiellement plus rigide à des angles plus élevés", explique Khan. "Dans les chaussures, cela est directement lié à la performance." Selon son dépôt de brevet en 2020, DFX se compose d'au moins trois couches assemblées et durcies en un seul stratifié :une couche de tissu tissé flexible renforcé par un liant ; une couche de tissu tissé plus rigide ; et au moins une couche de polymère.
Khan note qu'une chaussure de course ou une cale peut être souple et flexible lorsqu'un athlète marche sur une piste ou sur un terrain, puis, une fois que le coureur décolle et que le pied commence à se plier à des angles plus élevés, la chaussure deviendra plus rigide à supporter. le mouvement . "Les entreprises n'ont plus à faire de compromis et à choisir une rigidité spécifique au milieu du pied - nous pouvons identifier les différentes fonctions d'une activité donnée et concevoir la rigidité autour de cela."
« Une autre façon de voir les choses est que DFX augmente les performances du pied, agissant comme des muscles ou des ligaments qui deviennent flexibles ou raides selon la façon dont ils sont étirés. Le matériau AFX agit davantage comme une articulation comme votre coude ou votre cheville - il est conçu pour se plier très bien dans un sens », ajoute-t-il.
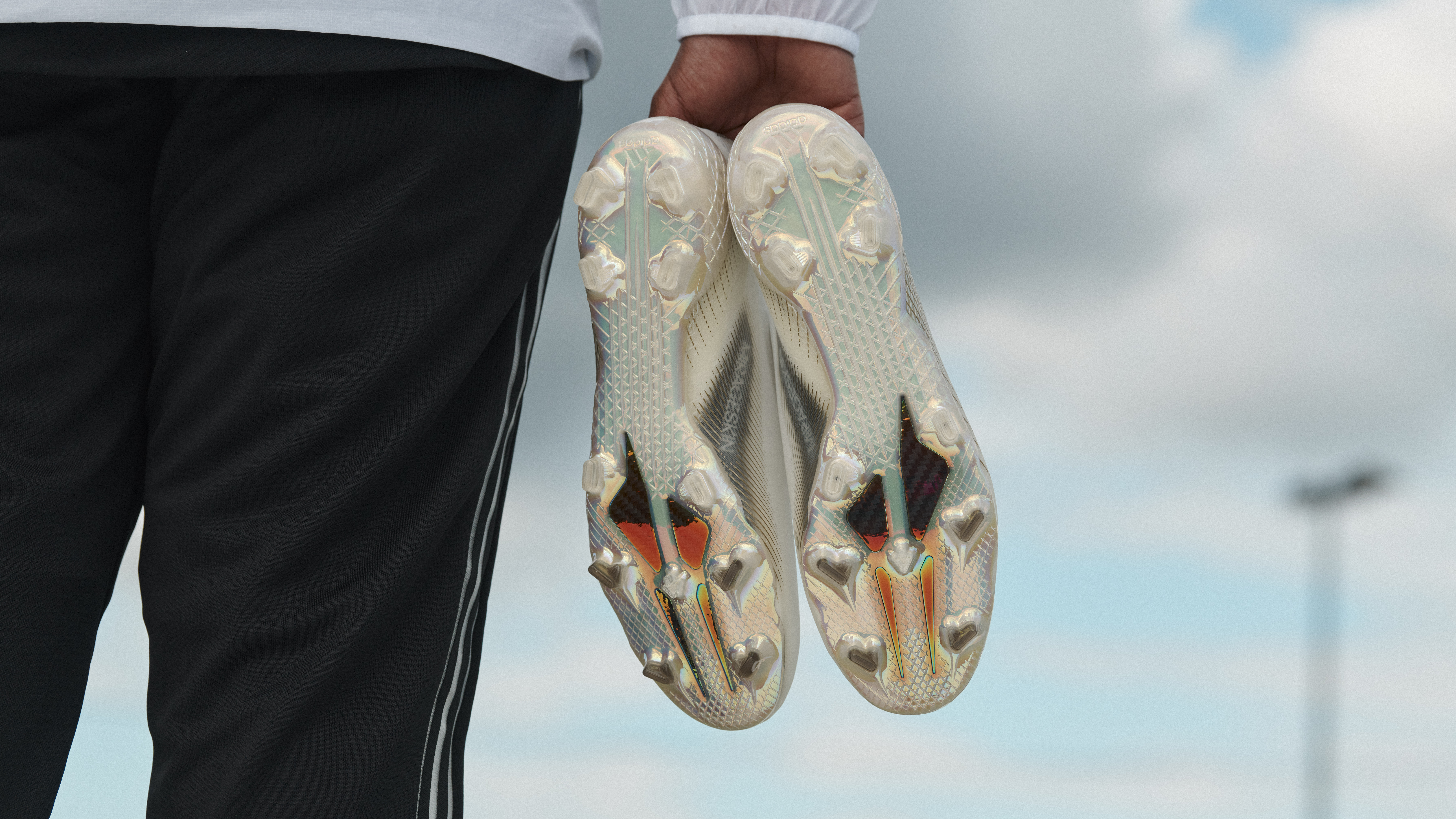
Jusqu'à présent, chaque itération de matériau a été spécialement conçue pour une plage de performances et un niveau d'intégration de fabrication particuliers identifiés comme applicables à l'industrie, avec une marge de personnalisation, telle que des exigences spécifiques de rigidité ou de durabilité. La société propose également des échantillons personnalisés à des clients potentiels. « Nous recueillons continuellement des données sur nos composites et leur fonctionnement et pourquoi, et avons construit nos propres systèmes de modélisation pour transformer différentes versions selon les besoins assez rapidement. Habituellement, dans un délai d'un jour ou deux après réception d'une demande, nous pouvons faire fabriquer un échantillon personnalisé et le sortir », ajoute Khan.
Au-delà des chaussures
"Pour le moment, notre objectif est de continuer à nous développer dans le domaine de la chaussure et d'essayer de saisir cette opportunité", a déclaré Khan. Cependant, un objectif à long terme est que l'entreprise se développe dans d'autres secteurs, tels que l'aérospatiale et les applications médicales.
« Une industrie qui nous préoccupe vraiment, à la fois en tant que marché où nos produits auraient un réel avantage et en tant que marché qui présente des similitudes avec les chaussures, est le domaine orthopédique et prothétique, et peut-être même le côté robotique. " il dit. La flexibilité dynamique des membres prothétiques, ajoute-t-il, est actuellement obtenue grâce à des systèmes électroniques lourds et coûteux et à des actionneurs hydrauliques. Khan envisage l'utilisation des produits Carbitex dans des applications telles que les genouillères ou les orthèses dorsales, où le matériau pourrait être conçu pour empêcher certains mouvements ou hyperextensions, tout en permettant d'autres mouvements. Il ajoute :« Avec un corset, vous immobilisez généralement une partie du corps de quelqu'un à cause d'un seul mouvement qui serait vraiment mauvais pour lui. La clé serait de fabriquer une attelle qui limite cette direction de mouvement, mais permet à la personne de pouvoir ensuite se déplacer dans d'autres directions. Conformément à cet objectif, Carbitex a récemment commencé le développement d'une application avec une entreprise qui fabrique des appareils orthodontiques destinés aux enfants. Les matériaux de la société ont également été utilisés, dit Carbitex, pour développer un coussin en fibre de carbone pour un manchon de compression conçu pour les randonneurs, et une minerve qui se connecte au casque et aux épaulettes d'un joueur de football pour empêcher le cou de se casser vers l'arrière pendant le jeu.
En poursuivant d'autres applications, Carbitex espère utiliser ses produits pour éliminer les compromis sur les matériaux dans d'autres industries, comme il aspire continuellement à le faire dans le domaine des chaussures. Khan ajoute :« Cela semble plus cool de dire que vous recherchez des produits qui vous rendent plus rapide, meilleur et plus fort, et nous le faisons, mais en fin de compte, nous recherchons toujours l'efficacité. »
Résine
- Fibre de carbone
- 3 avantages d'une montre en fibre de carbone
- Matériau en fibre de carbone dans l'industrie aérospatiale :ce qu'il faut savoir
- Qu'est-ce que la fibre de carbone unidirectionnelle ?
- Le rôle des matériaux composites dans l'industrie automobile
- Pourquoi la fibre de carbone est un excellent matériau de fabrication pour les bijoux
- Plastique renforcé de fibres de carbone (CFRP)
- Avantages des chaussures en fibre de carbone
- Recyclage des composites — plus d'excuses