Les grandes couvertures composites protègent beaucoup de l'eau
Le stockage et la livraison de l'eau à Bogotá, en Colombie, comme pour toute grande zone urbaine, sont compliqués. Le défi n'est pas celui de l'approvisionnement, car la ville de quelque 9 millions d'habitants reçoit 32 pouces (824 millimètres) de pluie chaque année, et la rivière Bogotá traverse la ville. L'enjeu est de capter cette eau, de la traiter puis de la stocker pour qu'elle reste potable et disponible selon les besoins des habitants et des entreprises. Pour ce faire, Empresa de Acueductos y Alcantarillados (Société d'aqueducs et d'égouts, EAAB, Bogotá) a, au fil des ans, construit une série de 59 réservoirs dans toute la ville pour stocker l'eau traitée et assurer l'approvisionnement des clients.
Certains de ces réservoirs sont de véritables réservoirs - entièrement fermés pour protéger l'eau des éléments extérieurs. D'autres, pour beaucoup plus anciens, sont des bassins massifs en béton protégés des intempéries par une série de couvercles amovibles. L'un de ces réservoirs, appelé Casablanca et situé dans le quartier de Ciudad Bolivar dans la partie sud de Bogotá, dessert une population d'environ 3 millions de personnes. Casablanca, le plus grand réservoir d'eau du réseau EAAB et le plus grand réservoir d'eau de Colombie, mesure 144 mètres (472 pieds) de long x 110 mètres (361 pieds) de large x 9 mètres de profondeur et a une capacité de stockage de 143 000 mètres cubes ( 38 millions de gallons) d'eau. Le réservoir est coupé en deux par une cloison en béton qui coule en son milieu de sorte que l'eau soit stockée en deux sections égales.
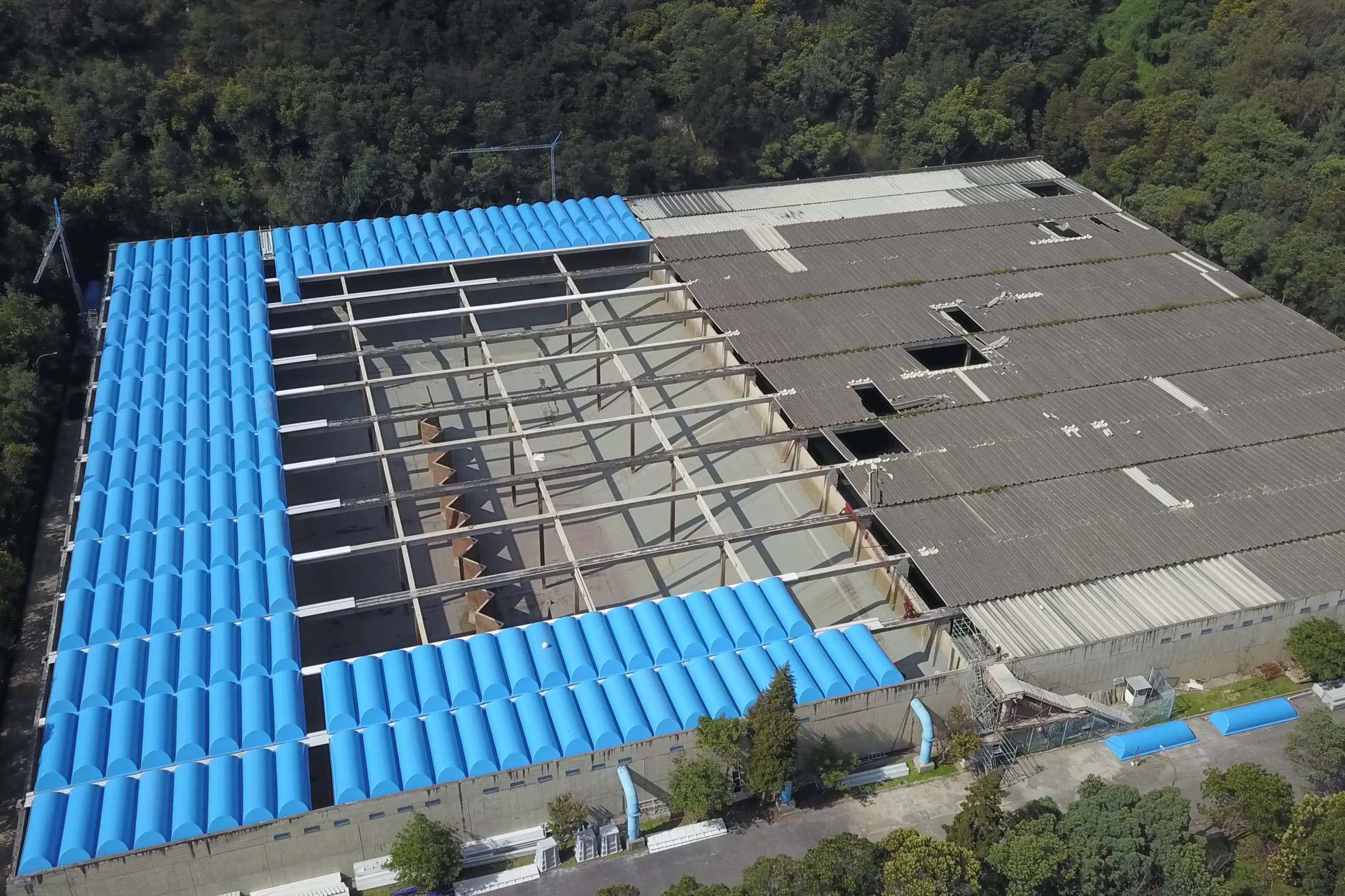
Entretenir le Casablanca de 66 ans n'est pas une tâche facile. En 2009, il a été découvert que des fissures dans le sol en béton du réservoir permettaient à 360 000 litres (95 000 gallons) d'eau de s'échapper chaque heure . Les réparations du béton avec un revêtement de polyurée ont réduit les fuites à zéro. Casablanca, cependant, avait encore un problème au-dessus du béton. L'eau contenue dans le réservoir était protégée par une série de couvercles constitués d'un mélange de béton et d'amiante, ce qui représentait une menace importante pour la qualité de l'eau et la santé humaine. Les anciennes couvertures étaient également sujettes à l'échec et étaient coûteuses à entretenir. EAAB avait besoin de remplacer les anciennes couvertures par une alternative plus sûre, plus légère et plus durable.
De grandes couvertures, et beaucoup d'entre elles
EAAB a décidé de rechercher une solution composite pour les couvertures, mais a été immédiatement mis au défi par l'ampleur du projet. Casablanca est traversé par une série de piliers en béton qui soutiennent un réseau de poutres sur lesquelles reposent les couvertures. Ces poutres étant espacées d'environ 7,2 mètres (23,6 pieds), les nouvelles couvertures devraient donc être autoportantes et couvrir cette portée pour utiliser l'infrastructure existante. L'EAAB a proposé que ces couvercles soient fabriqués par moulage par transfert de résine légère (LRTM). Le défi? Les structures composites de cette taille requise pour cette application n'avaient jamais été fabriquées via LRTM en Colombie. De nombreux fabricants n'ont tout simplement pas pu prendre en charge le projet.
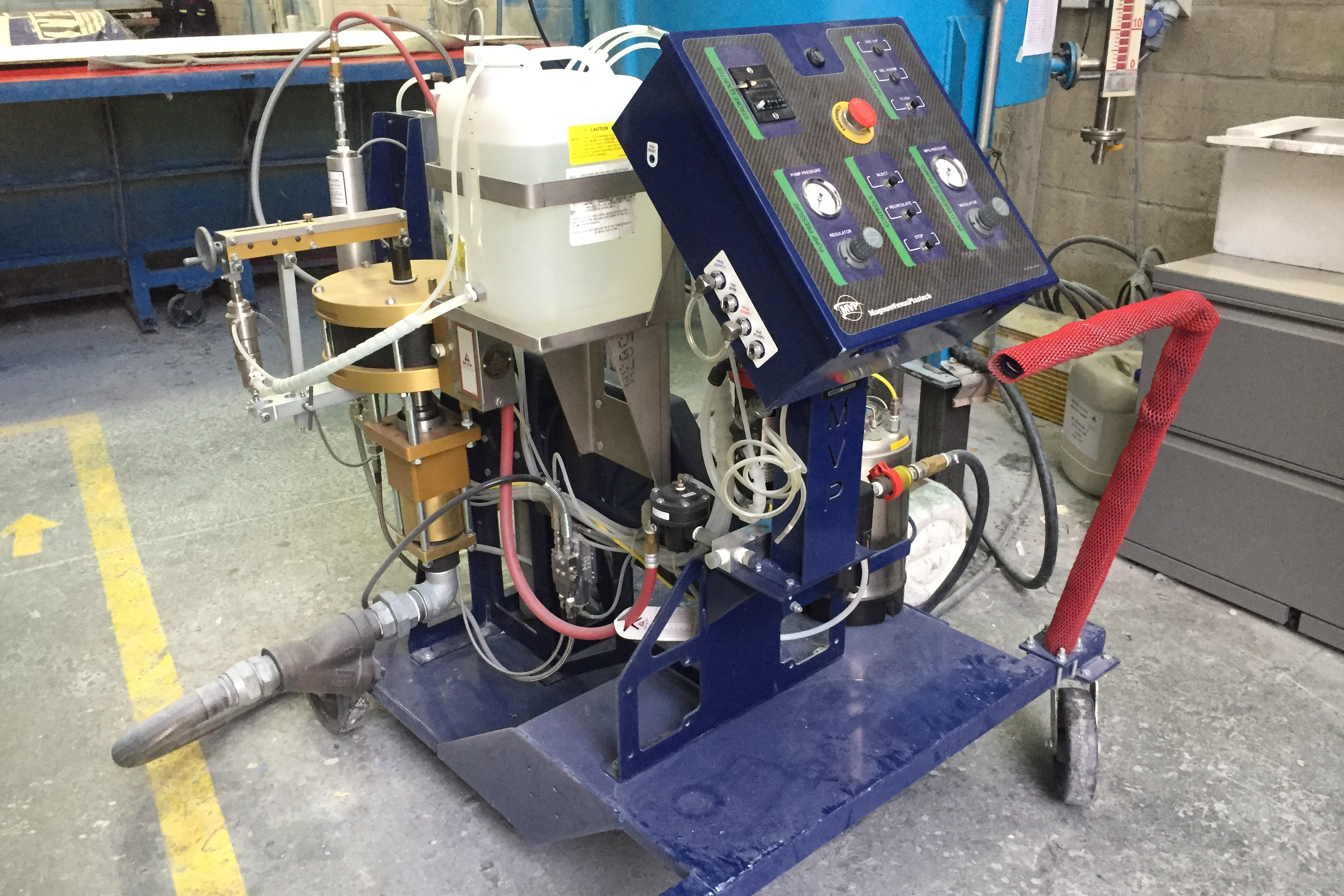
L'exception était Innovative Engineering Solutions, ou Soling, un fabricant de composites situé à La Estrella, Antioquia, Colombie, juste au sud de Medellín. Soling a été fondée en 2014 par Javiar Moreno, qui possède et exploite plusieurs entreprises de fabrication de composites en Colombie et dans ses environs. Rodrigo Vergara, coordinateur de l'ingénierie chez Soling, affirme que la taille des couvertures était un échec pour de nombreux fabricants. "Personne n'avait d'expérience avec cela en Colombie en raison de la taille de la pièce", note-t-il. « C'est la plus grande pièce composite fabriquée en Colombie. Pour Moreno, cependant, la taille des couvertures était un défi intéressant. « Pour notre propriétaire [Moreno] », dit Vergara, « c'était un rêve devenu réalité. "Impossible" est un mot qu'il ne comprend pas. Il a dit :« Nous allons le faire ! » J'ai dit : « OK ! » »
Soling a proposé une solution spécifique pour le projet Casablanca :Une série de 840 structures composites rectangulaires en forme de dôme, mesurant chacune 7,6 mètres de long et 2,4 mètres de large (24,9 x 7,9 pieds). La conception du dôme semi-circulaire a été choisie, dit Vergara, car «la forme géométrique qui a la plus grande résistance mécanique est une circonférence. C'était le principal facteur pour garantir que les couvertures étaient autoportantes. D'un autre côté, nous devions trouver le moyen le plus simple de les expédier du site de fabrication au point d'installation, qui se trouvait à 260 milles. »
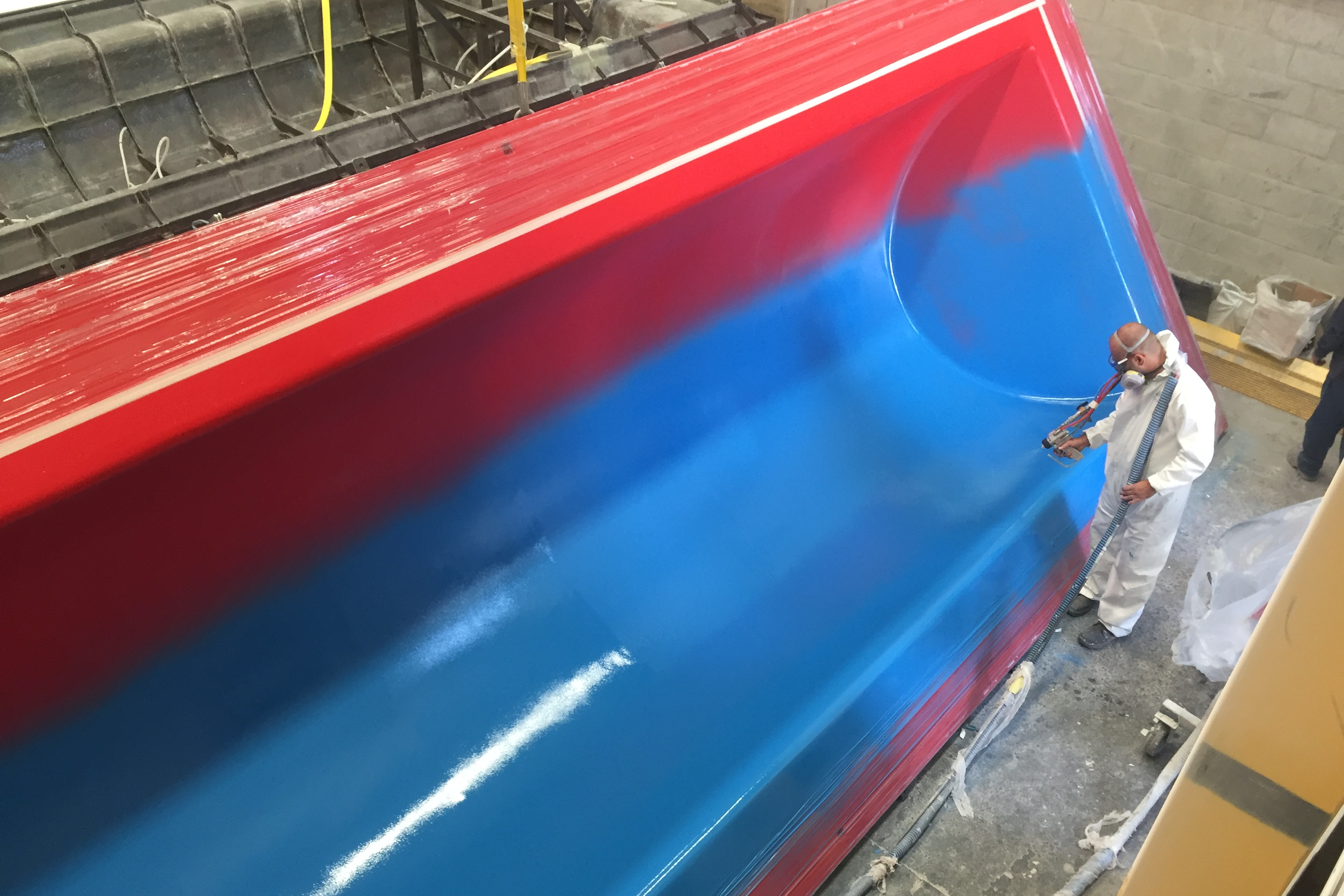
Les couvertures seraient fabriquées via LRTM avec, selon la spécification EAAB, un gelcoat bleu sur la surface extérieure et un gelcoat blanc sur la surface intérieure. Constituée de tissus en fibre de verre et d'une résine polyester, la couverture, d'une superficie de 28,5 mètres carrés (207 pieds carrés), pèserait 320 kilogrammes (705 livres), dont 208 kilogrammes en résine. Avec une conception en main et un engagement à livrer les couvertures, Vergara et Soling se sont mis au travail.
Construire la couverture parfaite
Soling, bien sûr, n'a pas repris le projet de Casablanca sans aide. Travailler avec l'entreprise était un réseau d'approvisionnement qui comprenait un distributeur, un fournisseur de matériel et un fournisseur d'équipement. Le distributeur, Minepro SAS (Medellín, Colombie), a fourni un support technique et a travaillé avec le fournisseur d'équipements Magnum Venus Products (MVP, Knoxville, Tennessee, États-Unis), qui a fourni des pompes et des équipements auxiliaires pour le processus LRTM. Les fournisseurs de matériaux sont Andercol (Medellín), qui a fourni la matrice en résine polyester, les gelcoats et le support technique, et Jushi (Tongxiang City, Chine), qui a fourni les tissus en fibre de verre E.
La fabrication, naturellement, commence par l'outillage. La question était de savoir combien de moules le projet nécessitait. Pour déterminer cela, Vergara dit que Soling a d'abord dû établir le rythme de fabrication pour répondre aux exigences de livraison de l'EAAB. Ceci, à son tour, a été affecté par les exigences du chantier. Pour éviter de contaminer potentiellement l'approvisionnement en eau lors de l'installation des nouvelles couvertures, EAAB a accepté de vider la moitié de Casablanca sur laquelle les couvertures étaient en cours de livraison et de mise en place. Réduire de moitié la capacité de stockage d'eau de Casablanca pose des défis, c'est pourquoi l'EAAB avait besoin que la livraison et l'installation se fassent le plus rapidement possible.
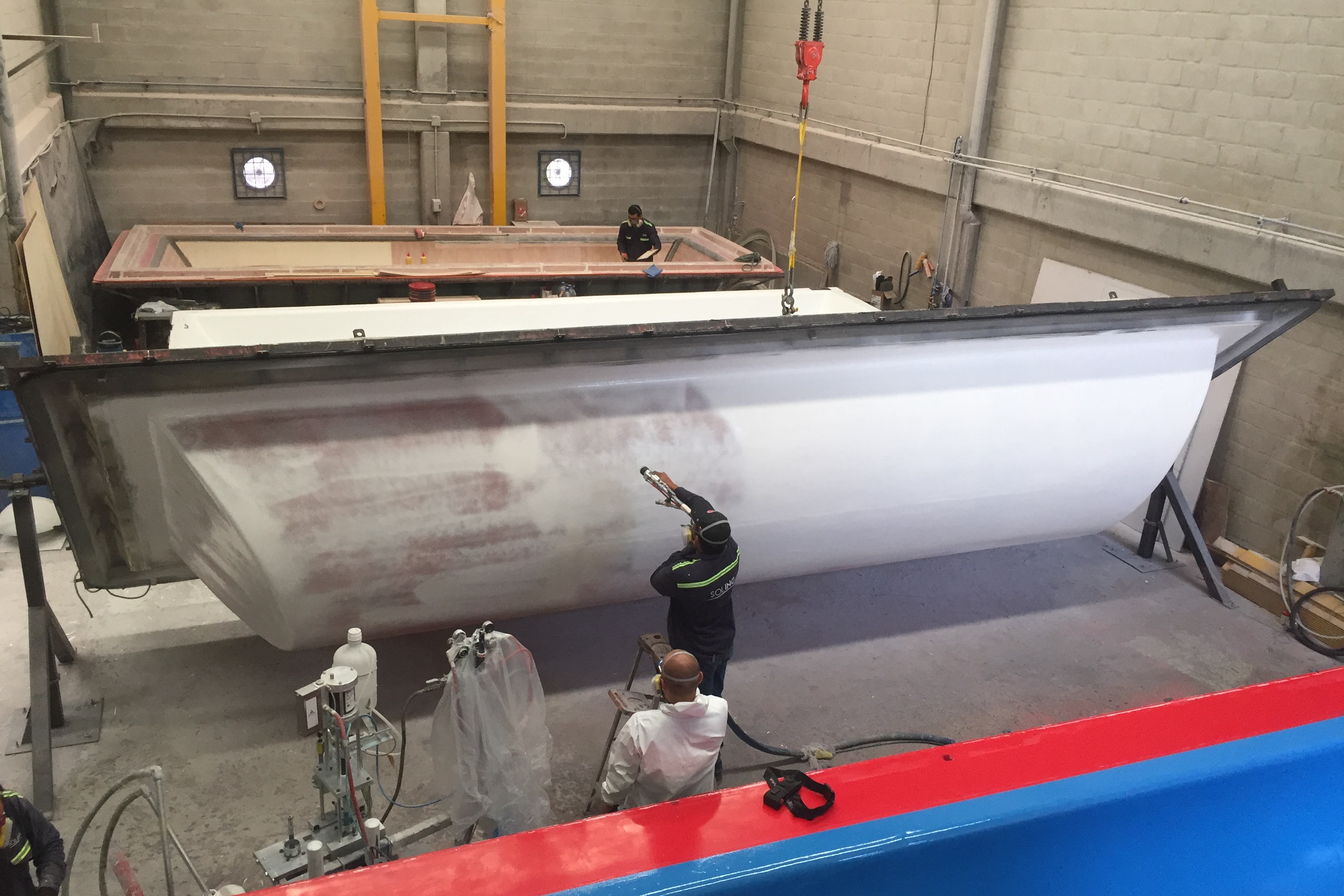
Soling, en collaboration avec EAAB, explique Vergara, s'est fixé un calendrier de production qui livrerait six couvertures par jour. Dans une usine exécutant trois équipes de huit heures par jour, cela nécessitait deux moules, chacun capable de fabriquer une couverture par équipe. Les moules, dit-il, ont été construits en interne et étaient composés d'un modèle mâle/femelle en composite de fibre de verre soutenu par une structure de support en acier.
Une fois les moules construits, Soling a ensuite commencé à établir comment, spécifiquement, les dômes seraient fabriqués. En collaboration avec Minepro et MVP, Vergara a déclaré qu'il avait été décidé que chaque moule serait alimenté par deux ports d'injection de résine, avec un port à vide. Pour l'injection de résine, MVP a recommandé l'utilisation de son unité de pompe de moulage par transfert de résine (RTM) Patriot Innovator, capable de fournir le grand volume de résine requis par chaque couvercle. MVP a également fourni ses vannes Turbo Autosprue, ainsi que des coupleurs universels, des joints et des accessoires de moule.
Pour lancer la production d'un couvercle, explique Vergara, la moitié femelle du moule a été vaporisée de gelcoat blanc et la moitié mâle du moule a été vaporisée de gelcoat bleu. Comme indiqué, les deux gelcoats ont été fournis par Andercol. Ensuite, les tapis et tissus en verre E fournis par Jushi ont été posés à la main dans la moitié femelle du moule. Cela a été suivi par l'abaissement, via une grue, la moitié mâle du moule dans la moitié femelle, avec les deux moitiés serrées ensemble. Après que le vide a été tiré, l'injection de résine a commencé. Vergara dit que l'injection de chaque couverture a été réalisée en 40 minutes environ, suivie d'un durcissement à température ambiante. Après que chaque couvercle a été démoulé, il a été coupé aux dimensions finales et des canaux d'alimentation pour l'atténuation de l'eau de pluie ont été coupés dans la surface de la bride du couvercle.
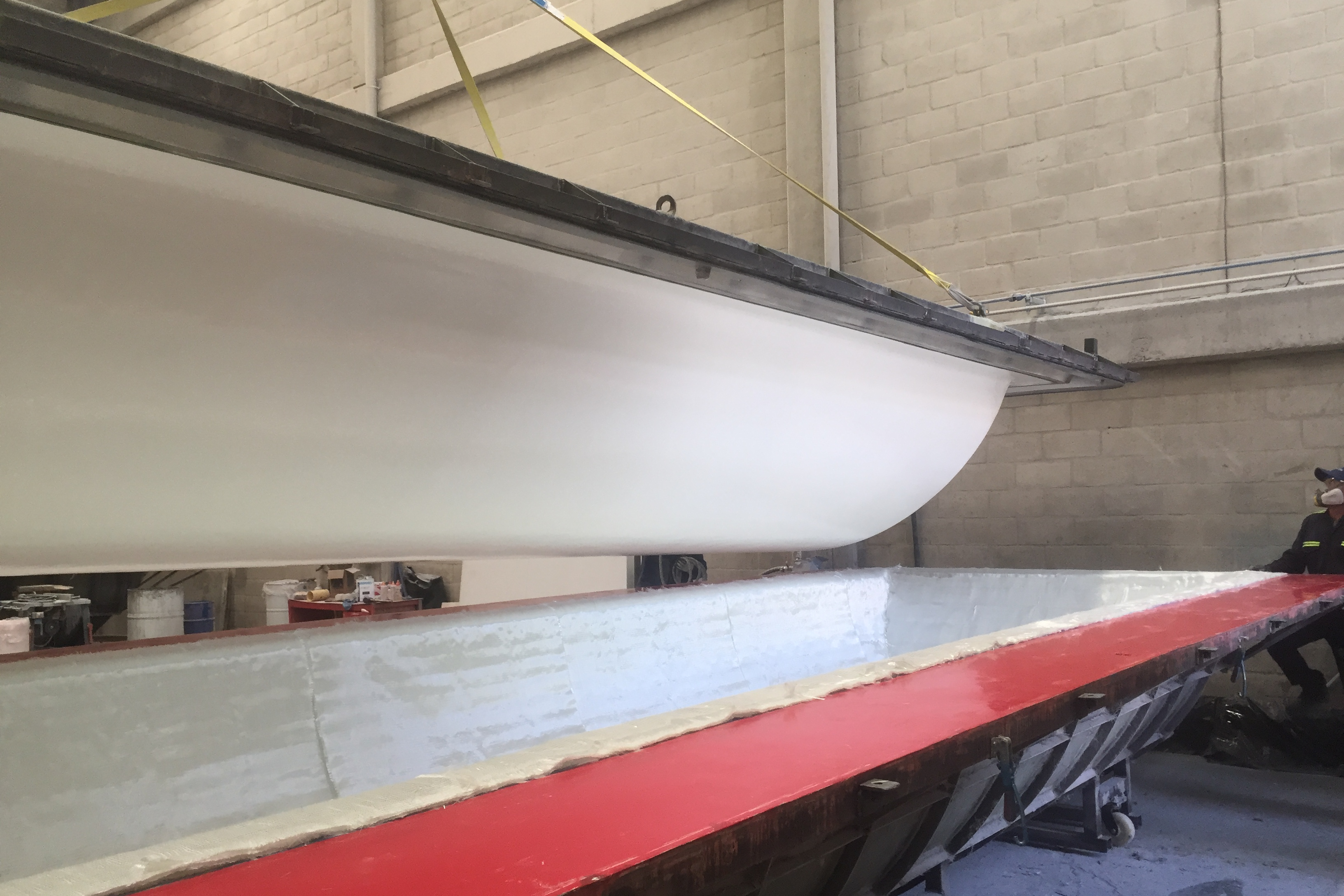
Vergara dit que la taille des couvertures, combinée à des exigences strictes en matière de poids et de dimensions, a posé le plus grand défi à leur fabrication. La détermination de l'emplacement du port d'injection et la gestion du moment de l'injection ont nécessité de nombreux essais et erreurs et la consultation d'experts techniques. Finalement, cependant, Vergara dit que Soling a opté pour un processus de fabrication qui s'est avéré hautement reproductible et fiable.
« Le plus gros défi était le poids des éléments que nous allions installer, car nous ne pouvions pas dépasser la capacité de charge de la structure existante », explique Vergara. « Cela nécessitait que toutes les pièces aient les mêmes caractéristiques, tant en géométrie qu'en poids. La seule façon de garantir ces conditions était d'utiliser un procédé garantissant la répétabilité. »
Les couvertures finies ont été expédiées sur les 418 kilomètres (260 miles) de l'usine de Soling près de Medellín jusqu'au chantier de Casablanca à Bogotá, puis installées par grue, abaissées sur la structure de support et positionnées par des ouvriers debout sur les poutres sur lesquelles les couvertures reposeraient. Bien que les couvercles ne soient pas fixés mécaniquement aux structures de support, Vergara dit qu'ils ne sont pas non plus conçus pour être déplacés ou retirés à moins que "quelque chose de très grave ne se produise".
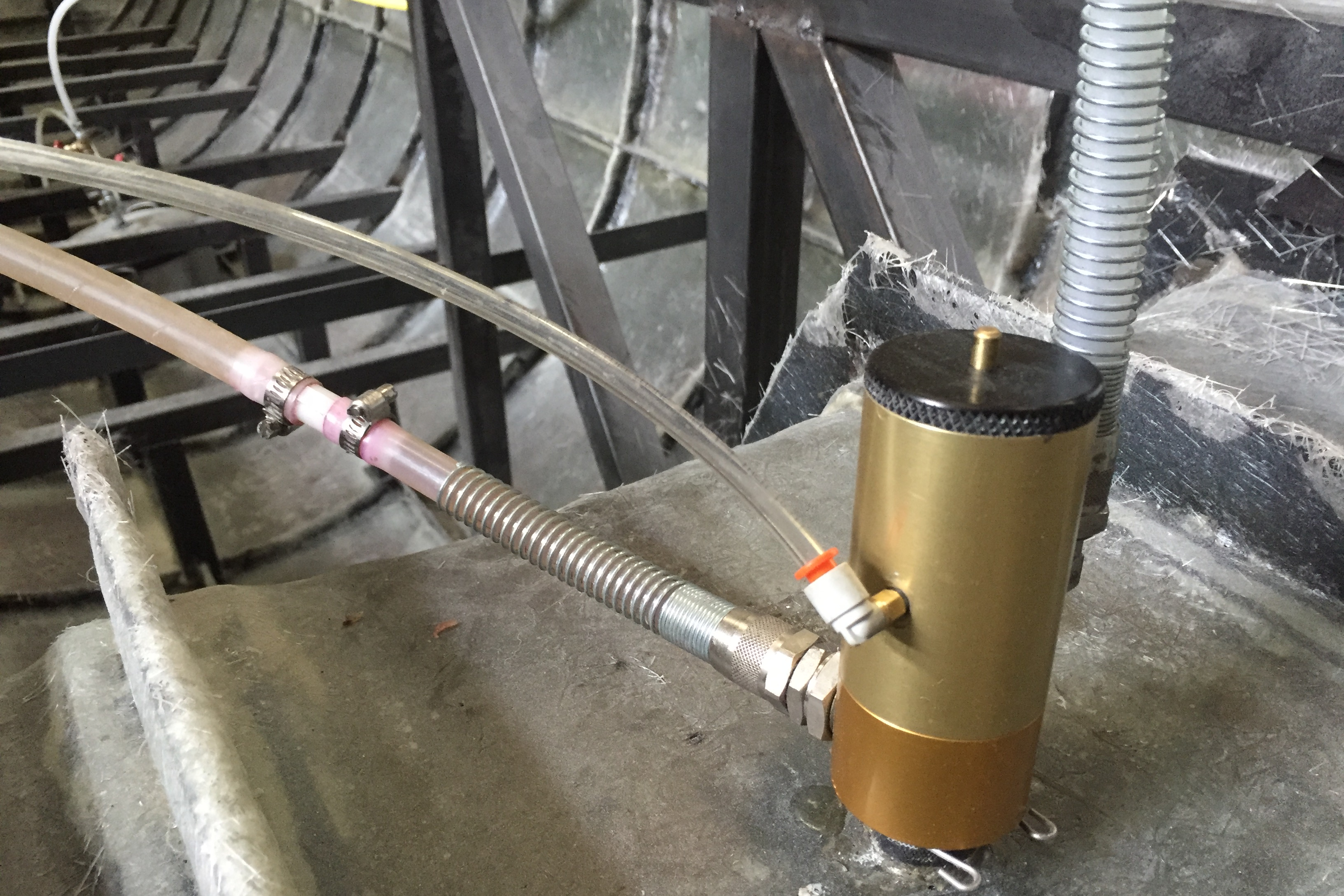
Soling a commencé les travaux de conception sur les couvertures au début de 2019 et a commencé la fabrication des premières couvertures en 2020. La pandémie de coronavirus et les défis mécaniques occasionnels ont provoqué l'arrêt et le démarrage de la fabrication, mais Vergara dit que Soling a achevé la production des 840 couvertures sur une période de 7- 8 mois, se terminant fin 2020. On s'attend à ce que les nouvelles couvertures durent beaucoup plus longtemps et nécessitent beaucoup moins d'entretien que celles qu'elles ont remplacées.
Le projet de Casablanca, dit Vergara, a démontré les capacités de Soling en tant que fabricant de grandes structures composites de haute qualité et hautes performances et a ouvert la porte à d'autres opportunités. « Ce projet était un défi dans lequel nous avons dû briser les paradigmes qui disaient que des pièces de cette ampleur ne pouvaient pas être fabriquées à l'aide de cette méthode de fabrication, et nous l'avons quand même fait », dit-il. « Pour l'avenir de Soling, quelque chose est très clair :il n'y a aucun projet que nous ne soyons pas capables de réaliser. »
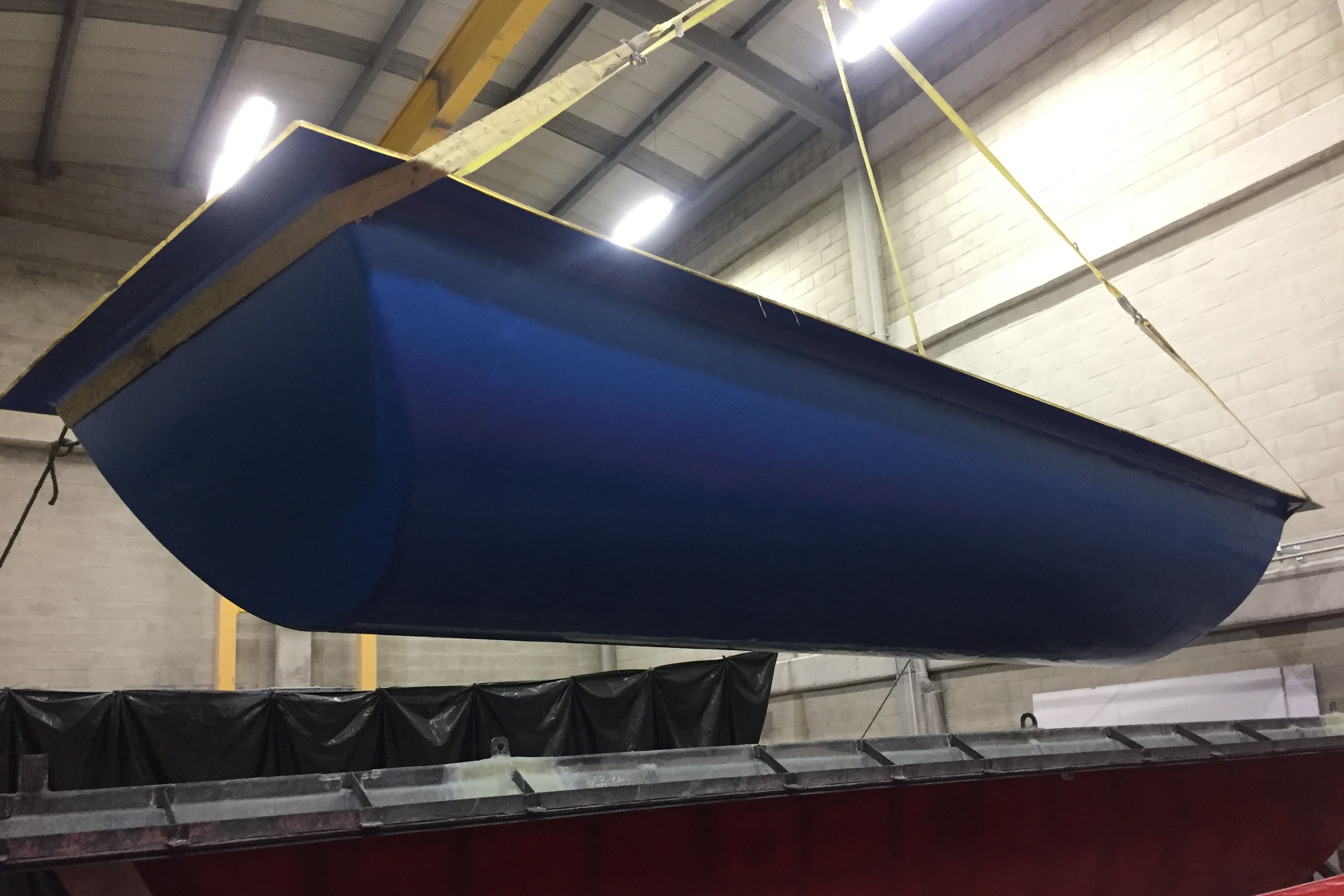
Résine