RTM de vitesse avec capteurs de flux de chaleur
Représentant 3 à 5 % du poids d'un avion, les trains d'atterrissage ont longtemps été ciblés pour une réduction de poids afin d'améliorer l'efficacité de l'avion. Cela est devenu encore plus critique avec le passage imminent à des systèmes de propulsion électriques à réduction d'énergie et d'émissions.
Par exemple, Safran Landing Systems (Vélizy, France) permettra un roulage électrique sans moteur via des moteurs électriques intégrés dans les roues des trains d'atterrissage des avions, réduisant les NOx, le CO2 , les émissions de CO et d'hydrocarbures imbrûlés de 51 %, 61 %, 73 % et 62 %, respectivement. C'est une énorme victoire pour une aviation plus durable, mais les moteurs électriques nécessitent de l'énergie et les batteries nécessaires pour fournir cette énergie sont lourdes.
Ainsi, la demande de structures de trains d'atterrissage légères semble parfaitement adaptée à l'application de composites, à un seul problème près. « Parce que le train d'atterrissage est une structure à trajectoire de charge unique, la défaillance d'un composant structurel pourrait entraîner une situation d'atterrissage d'urgence grave », explique Peet Vergouwen, technologue chez GKN Fokker Landing Gear (Helmond, Pays-Bas). GKN Fokker Landing Gear a travaillé pendant plus d'une décennie pour démontrer la faisabilité technique des structures de trains d'atterrissage composites, y compris le développement de renforts de traînée en polymère renforcé de fibres de carbone (CFRP) pour le F-35 Lightning II . "En raison de leur criticité, les structures de trains d'atterrissage sont parmi les plus conservatrices des avions commerciaux." Par conséquent, ils ont principalement été fabriqués à partir de métaux à haute résistance.
Ce vent commence cependant à tourner. Clean Sky 2 poursuit une réduction de poids de 30%, mais via des composants CFRP dans le projet HECOLAG (High Efficiency Composites Landing Gear), pour deux applications. Dans la première application, une alternative CFRP a été développée pour le étai de traînée supérieur existant en aluminium pour le train d'atterrissage avant de l'A350-1000, initialement développé et fabriqué par Liebherr-Aerospace (Lindenberg, Allemagne). Les partenaires HECOLAG Royal Netherlands Aerospace Center (NLR, Marknesse) et GKN Fokker Landing Gear ont conçu ce hauban en CFRP selon les exigences de Liebherr. À l'aide d'une technologie de préformage automatisée développée en interne, NLR a construit des prototypes fonctionnels de l'étai de traînée CFRP, qui ont été testés par GKN Fokker Landing Gear.
Dans la deuxième application en cours d'évaluation par HECOLAG, NLR et GKN Fokker Landing Gear ont également développé un étai latéral inférieur en CFRP en collaboration avec Safran Landing Systems pour le train principal électrifié. CW fera rapport spécifiquement sur les résultats globaux du projet HECOLAG plus tard en 2021, mais ici, l'accent est mis sur le sous-projet INNOTOOL 4.0, guidé par le responsable du sujet GKN Fokker Landing Gear pour faire progresser la production hautement automatisée de structures de trains d'atterrissage en CFRP à l'aide de moulage par transfert de résine (RTM) . Plus précisément, INNOTOOL 4.0 cherche à démontrer un outillage intégré aux capteurs qui ouvrira la voie à des outils plus petits avec moins de masse pour des cycles de production plus rapides, une manipulation plus facile et une consommation d'énergie réduite, ainsi qu'une automatisation accrue pour un coût inférieur et un contrôle des processus intelligent des composites 4.0. Le projet INNOTOOL 4.0 est financé par l'entreprise commune Clean Sky 2 dans le cadre du programme de recherche et d'innovation Horizon de l'UE sous le GAP n° 821261.
Objectifs INNOTOOL 4.0
Le démonstrateur de cette deuxième partie d'HECOLAG (voir image d'ouverture) est plutôt une partie générique, explique Vergouwen. « Il s'agit de démontrer des méthodologies de conception, de simulation et de fabrication de pièces qui fourniront les performances, le taux de production et le coût nécessaires pour les avions monocouloirs. » Fin 2017, le consortium HECOLAG avait défini la première pièce de démonstrateur CFRP et l'outil de production, analysé le comportement thermique de l'outil et réalisé des essais de performances. Ce produit volumineux et complexe a passé l'examen de conception préliminaire et a atteint un niveau de maturité technologique (TRL) de 4 plus tard dans l'année. « Sur la base des problèmes et des enseignements tirés de ce premier démonstrateur, nous recherchions des partenaires pour développer la technologie d'outillage RTM afin d'optimiser et de raccourcir le cycle de durcissement », explique Vergouwen. Un appel à partenaires Clean Sky 2 a été lancé en 2018 et a été attribué au consortium INNOTOOL 4.0, composé du fournisseur d'équipements et d'automatismes Techni-Modul Engineering (TME, Coudes, France) et du spécialiste de l'injection de résine Isojet Equipements (Corbas, France). Ils ont commencé à travailler en avril 2019 et ont franchi les étapes initiales en mars 2021.
"La pièce composite doit être compétitive par rapport à l'acier forgé et à l'aluminium", note Vergouwen chez GKN Fokker Landing Gear. « Cela n'est possible qu'avec l'automatisation, permettant un très faible nombre d'heures de travail et des matériaux plus abordables que le CFRP actuel de qualité aérospatiale, durci à l'autoclave. »
Ainsi, INNOTOOL 4.0 a cherché à intégrer des capteurs dans l'outillage RTM qui surveilleront et géreront les processus d'injection et de durcissement, y compris la détection du front d'écoulement de la résine. « L'objectif est d'être complètement automatisé — chargez la préforme, appuyez sur un bouton et l'équipement de moulage gérera la température, la pression, le vide et le durcissement », explique Stéphane Besson, directeur commercial chez TME. Cependant, c'est la première fois que GKN Fokker Landing Gear et TME travaillent avec la surveillance de la guérison. « Nous avons déjà travaillé avec des capteurs de température et de pression », explique Besson, « mais pas avec des capteurs pour le débit et la polymérisation de la résine. »
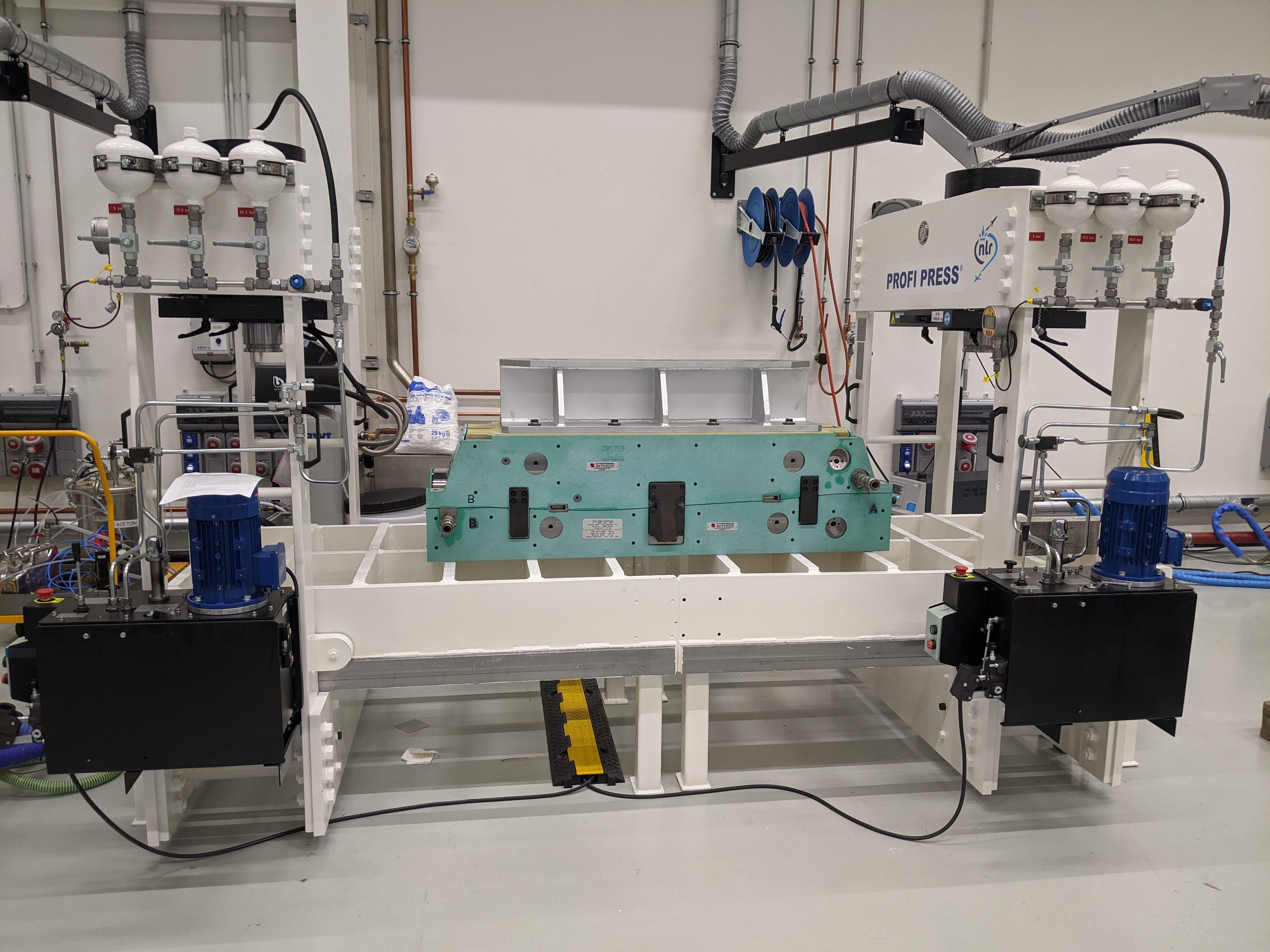
Les premières étapes du projet INNOTOOL 4.0 ont obligé TME et Isojet à livrer à NLR un outil de moulage et un système d'injection équipés de capteurs qui seraient utilisés pour produire des pièces de démonstrateur en mars et avril 2021. En parallèle, TME utiliserait un outil existant pour la production de Plaques CFRP - dimensionnées 600 x 600 millimètres avec une épaisseur de 1 à 8 millimètres - modifiées avec les mêmes capteurs pour les essais de contrôle de processus dans leur installation. « C'est quelque chose que vous préférez faire à petite échelle la première fois plutôt que directement sur un grand outil avec une pièce coûteuse », explique Vergouwen. Ainsi, TME a utilisé un outil différent, mais les mêmes capteurs pour montrer leurs capacités et leur profondeur. Une fois ces tests terminés, NLR réutiliserait ensuite l'outil principal HECOLAG pour produire une nouvelle série de démonstrateurs CFRP afin d'optimiser davantage le contrôle du processus sur les pièces réelles.
Conception d'outils de production RTM
TME a commencé la production de la conception de l'outil RTM en utilisant le logiciel CATIA V5 de Dassault Systèmes (Vélizy-Villacoublay, France) pour la conception mécanique et électrique, et ANSYS (Canonsburg, Pennsylvanie, États-Unis) pour la simulation thermique et mécanique. Cet outil serait associé au système 1K-2K à piston d'Isojet (pour les résines à un et deux composants) pour injecter Hexcel (Stamford, Connecticut, États-Unis) HexFlow 2K RTM 6 et Solvay (Alpharetta, Géorgie, États-Unis) 1K PRISM EP 2400 résines époxy monocomposant de qualité aérospatiale à une pression d'injection allant jusqu'à 20 bar.
« La forme de cet outil de moulage est très complexe », note Besson, « combinant des épaisseurs variables dans la préforme sèche 3D avec une forme tubulaire fermée. Cela crée des transitions d'épaisseur complexes, avec des problèmes concernant l'assemblage des préformes, la précision des extrémités de pli, les gradients de température internes et le retrait de la résine, ainsi que la manière d'optimiser la méthode de chauffage et la capacité de chauffage du mandrin interne pour permettre un temps de cycle court. Pour permettre des temps de cycle courts, tous les éléments de l'outil doivent être simples à utiliser, robustes et permettre un chauffage et un refroidissement rapides. Même si le projet INNOTOOL 4.0 a brièvement demandé des solutions de moules non métalliques, un ensemble typique de moules en acier supérieurs et inférieurs a été conçu en raison des pressions nécessaires pour minimiser les plis et assurer l'alignement des fibres pendant le formage.
Les moules supérieurs et inférieurs et le mandrin appariés sont chauffés et refroidis. « Les moules assortis utilisent un circuit d'eau intégré tandis que le mandrin est chauffé électriquement », explique Besson. "La circulation de l'eau fournit un chauffage et un refroidissement rapides pour réduire le temps de cycle partiel et le chauffage électrique permet d'obtenir la même chose dans le mandrin où l'espace est limité."
« Un autre défi était le nombre de pièces dans le mandrin », explique Besson. « En raison de la forme complexe et de la nécessité de retirer le mandrin après moulage, il comprenait six composants auto-chauffants et deux éléments de support où passent les capteurs pour contrôler la température interne des pièces du mandrin. A l'usage, ces éléments sont assemblés à la main à l'aide d'un support de base qui guide l'opérateur. Le travail avec un mandrin gonflable comme solution sera réalisé dans le cadre du projet HECOLAG plus vaste, mais cela n'était pas inclus dans le sous-projet INNOTOOL 4.0.
Capteurs de flux thermique
TME avait initialement prévu d'utiliser des capteurs diélectriques pour surveiller le flux et le durcissement de la résine (voir « Combiner les mesures diélectriques AC et DC pour la surveillance du durcissement des composites »), mais est passé aux capteurs de flux thermique de TFX (Boncourt, Suisse). « Au fur et à mesure que nous avancions dans le développement, nous voulions des capteurs qui permettaient de contrôler la mesure sans contact direct avec le polymère et les matériaux composites », explique Jorge Lopez Torres, chef de projet chez TME. « Les capteurs TFX ont permis cela car ils mesurent le flux de chaleur, qui se propage à travers les matériaux. » Il souligne qu'il s'agit essentiellement de la même mesure utilisée dans la calorimétrie différentielle à balayage (DSC), une technique de laboratoire qui analyse l'état de durcissement d'un polymère ou d'un composite. Notamment, les capteurs TFX et les tests DSC mesurent tous deux la chaleur libérée pendant la polymérisation/durcissement et donnent une courbe du flux de chaleur en fonction de la température et du temps.
Pour les capteurs TFX, les données de température proviennent d'un capteur de température interne dans les capteurs de flux thermique. Bien que les capteurs diélectriques soient également équipés d'un capteur de température interne, les deux capteurs sont très différents. « Des capteurs diélectriques mesurent directement les propriétés du polymère pendant le durcissement », explique le directeur de TFX, le Dr Fabien Cara. « Les capteurs de flux thermique ne donnent pas l'état du matériau à un instant donné. Cependant, la mesure de la chaleur générée pendant l'écoulement de la résine et la polymérisation fournit une bonne vue sur le comportement du processus et sur la répétabilité du cycle de durcissement pour chaque pièce produite. Et comme DSC, nous devons voir toute la courbe du processus de durcissement, mais notre capacité à surveiller le durcissement est très fiable. »
Des décennies d'expérience
Fondée sous le nom de Thermoflux en 2000, les capteurs TFX ont été utilisés dans des essais dans des centres de R&D et dans des applications industrielles par plus de 100 clients dans le monde. « Nous avons commencé à travailler avec RTM il y a plus de 15 ans, explique Cara, d'abord avec BMW pour les pièces automobiles et aussi pour le centre technique désormais connu sous le nom d'Institut de Soudure [(Saint-Avold, France)]. En 2006 et 2012, nous avons démarré deux grands projets de suivi du durcissement d'aubes de soufflantes de moteurs d'avions réalisées à l'aide de RTM et de préformes tissées en 3D. Safran dispose d'un système d'acquisition de données que nous avons développé pour eux dans leur laboratoire de composites près de Paris. Ils peuvent enregistrer jusqu'à 100 signaux simultanément [(flux thermique, température et pression]) et les analyser pour le durcissement et la surveillance des cycles de processus. TFX a également travaillé avec Hexcel dans son laboratoire des Avenières, en France, pour surveiller la qualité et les cycles de traitement des résines thermodurcissables injectées dans des préformes sèches. Des capteurs TFX ont également été utilisés dans un projet avec l'IRT-M2P (Porcelette, France) pour démontrer la compression RTM (En savoir plus). « Nos capteurs sont très efficaces pour les processus rapides tels que le moulage par compression, y compris avec les composés de moulage SMC et BMC », note Cara. « Nous avons également remporté un prix JEC Innovation en 2016 avec Huntsman Advanced Materials [(Bâle, Suisse)] pour un développement intitulé « Pièces en époxy structurelles avec une qualité d'autoclave en moins d'une minute. » »
TFX dispose de capteurs pour chaque type de processus de moulage des composites, basés sur la méthode de transfert de chaleur vers le capteur :conduction (RTM, compression et moulage par injection), convection (autoclave, four) et rayonnement (enroulement filamentaire, AFP). Les capteurs utilisés dans le projet INNOTOOL 4.0 étaient conducteurs, conçus pour être intégrés dans des moules métalliques RTM. « Ils fournissent un signal exceptionnellement reproductible à une distance allant jusqu'à 1 millimètre de la surface de l'outil et du matériau composite », note Cara.
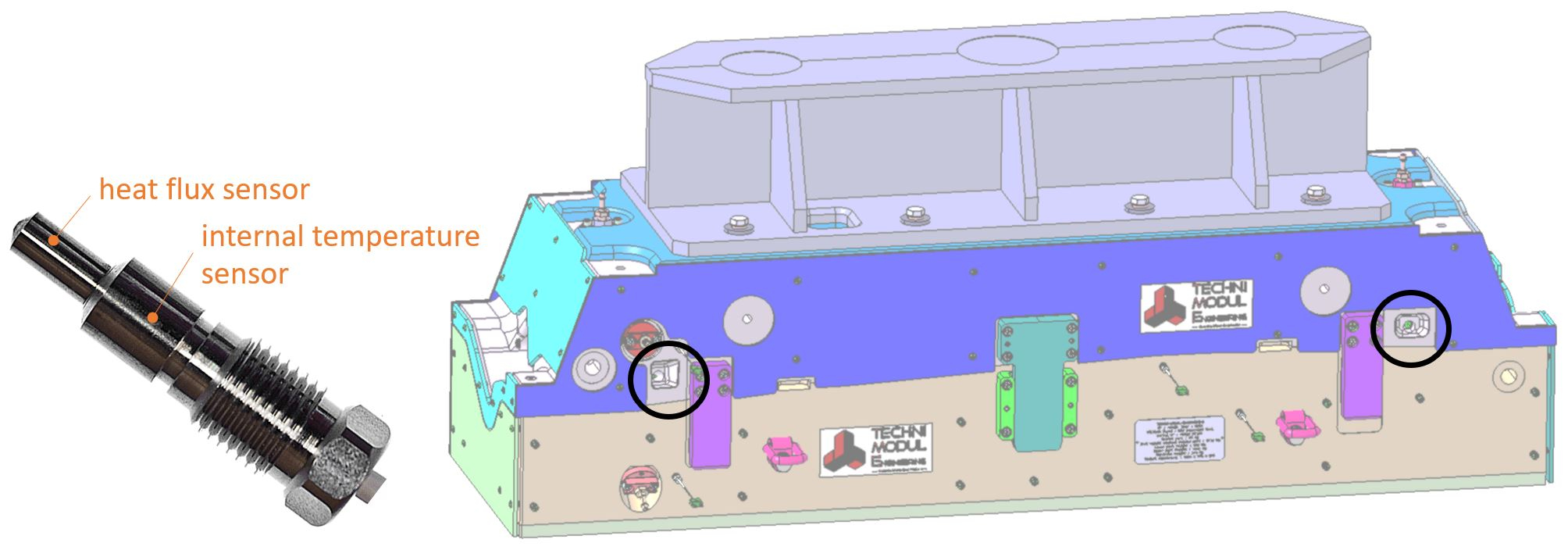
TME a installé deux capteurs TFX-191 - un à l'entrée de la résine et un à la sortie de la résine - dans le moule supérieur de l'ensemble d'outils de production correspondant qu'il a ensuite envoyé à NLR (Fig. 1, 2). NLR a utilisé cet outil de production pour fabriquer des pièces de démonstrateur HECOLAG en mars et avril 2021. Les capteurs TFX-191 sont destinés aux outils métalliques épais.
En parallèle, TME a pris un outil interne plus petit utilisé pour fabriquer des échantillons de plaques CFRP et l'a modifié avec deux capteurs TFX-224, qui sont plus courts, pour des outils plus minces (Fig. 3). Cet ensemble d'outils de plaque RTM a ensuite été utilisé pour effectuer des essais de démonstration de capteurs conformément aux objectifs INNOTOOL 4.0 décrits ci-dessus. "Ces capteurs sont similaires à ceux que nous utilisions pour Safran", explique Cara, "mais sont maintenant améliorés pour être beaucoup plus compacts et sensibles." Les capteurs ont été placés près du centre de la pièce et de la sortie de résine. En plus des capteurs de flux thermique, TFX a développé et fourni deux systèmes d'acquisition de données - l'un livré à Isojet et l'autre utilisé par TME pour les essais de plaques CFRP.
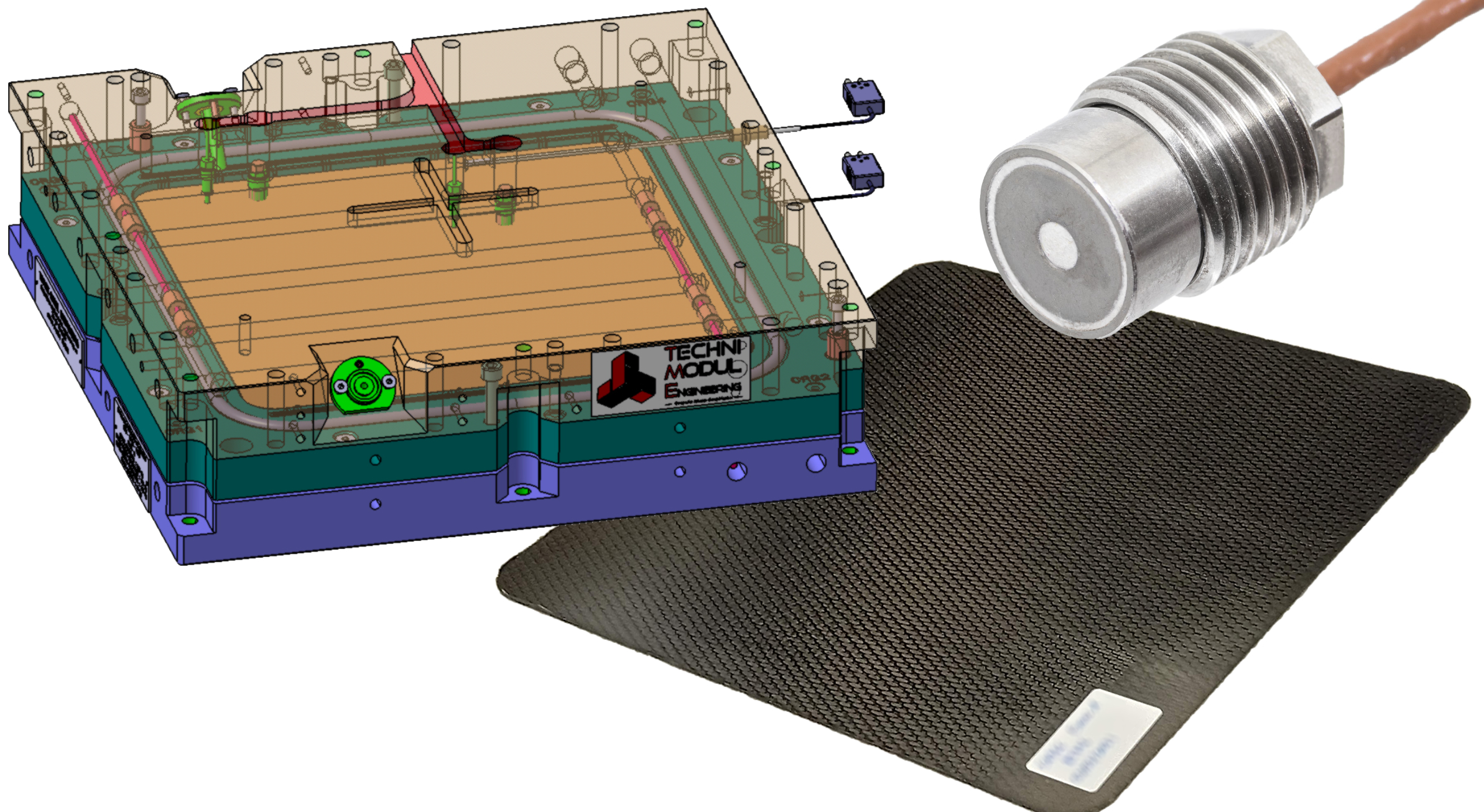
Résultats des tests INNOTOOL 4.0
Les essais menés par TME à l'aide de son outil à plaque modifié avec des capteurs TFX ont testé deux résines différentes - HexFlow RTM 6 et PRISM EP 2400 - ainsi que l'influence de l'épaisseur de la pièce et du temps de durcissement global. « Les capteurs ont fourni de bons signaux pour surveiller le cycle de durcissement », explique Cara. "L'équipe a ensuite analysé les courbes de durcissement et a montré que le temps de durcissement du RTM 6 pouvait être réduit d'au moins 30 minutes par rapport aux deux heures de durcissement prescrites."
Ceci peut être vu dans la courbe ci-dessous, où t=0 heures est le début de l'injection. Notez que le temps de durcissement commence lorsque la température atteint 180°C et la fin du durcissement correspond à 99% du niveau de durcissement relatif (voir l'axe vertical à droite). La fin du durcissement coïncide également avec la stabilisation du flux de chaleur brute.
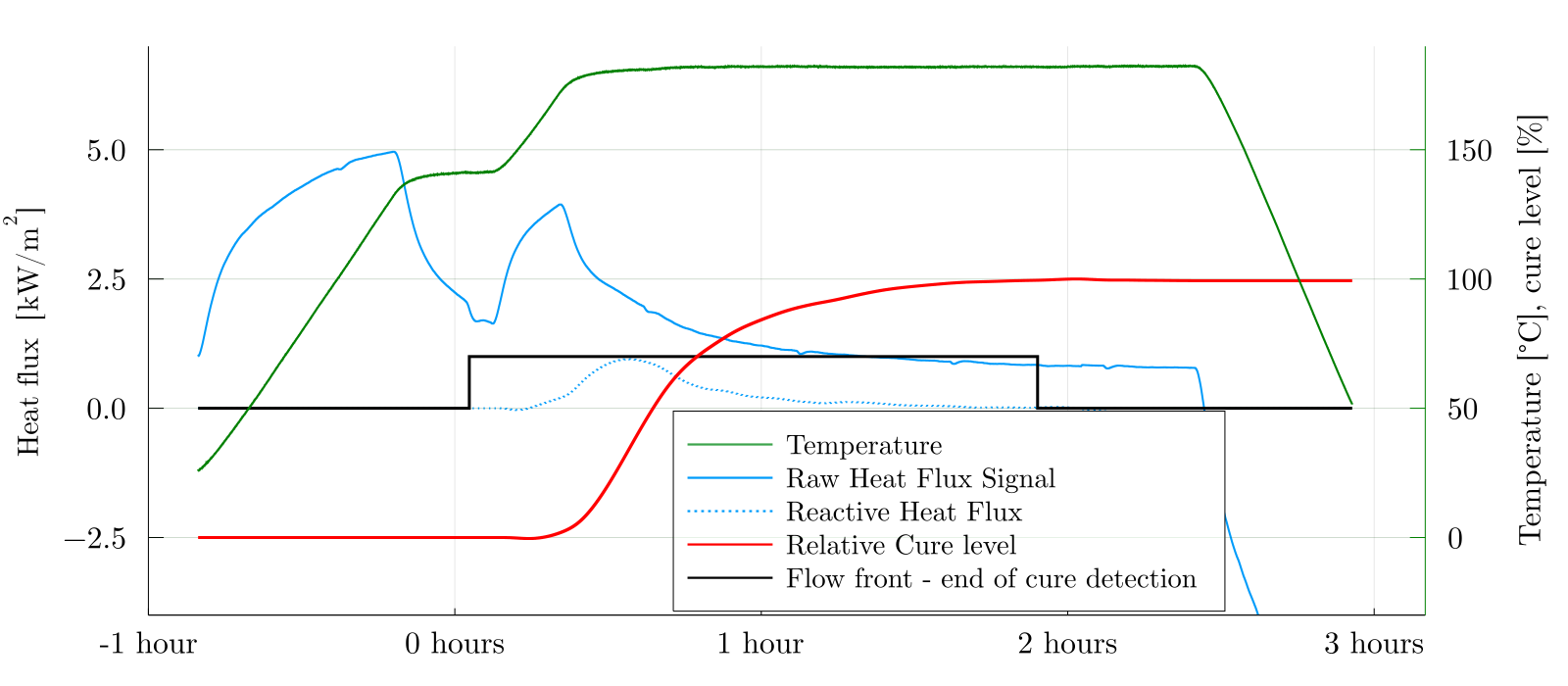
Cela a été vérifié par des mesures de l'état de durcissement des pièces démoulées à l'aide de l'analyse mécanique dynamique (DMA), une technique de laboratoire alternative à la DSC qui mesure la température de transition vitreuse (Tg ) pour les composites. « Les résultats du DMA ont confirmé que pour la résine RTM 6, le Tg reste inchangé après 90 minutes de durcissement à 180°C », ajoute-t-il.
L'effet de l'épaisseur a également été étudié. « Les premières plaques CFRP testées par TME dans leurs essais de démonstration de capteurs avaient une épaisseur inférieure à 2 millimètres », note Cara. « Ces plaques avaient également un volume de fibres élevé (50 à 60 %) et un cycle de durcissement lent pour éviter les dégagements de chaleur et les problèmes potentiels de contrainte thermique et de qualité des pièces. Tout cela est très normal pour les pièces aérospatiales, mais cela signifie qu'il y a très peu de résine, et donc la quantité de flux de chaleur libérée par la réaction de la résine était faible. Nous recherchions donc en fait l'aiguille du flux de chaleur dû au durcissement de la résine dans un océan de chauffage de l'outil et de la pièce. »
En d'autres termes, comme l'explique Cara, « La plupart des cycles de durcissement RTM aérospatiaux impliquent l'injection de résine à une température, puis une montée en puissance pour durcir à une deuxième température plus élevée. Ainsi, lorsque vous avez terminé l'injection, vous chauffez l'outil à la température de durcissement, ce qui génère un flux de chaleur important dans l'ensemble du système. Cependant, comme pour les tests DSC, la clé pour surveiller le durcissement avec des capteurs de flux thermique est de mesurer la chaleur libérée pendant la polymérisation/durcissement et d'afficher ces mesures dans une courbe de flux thermique en fonction de la température dans le système de moulage et du temps. « Nous avons donc inventé une méthode qui nous aide à soustraire la ligne de base de chauffage du moule et la conduction de cette chaleur à la pièce, de sorte qu'il soit possible d'identifier le flux de chaleur de la réaction de la résine. »
Ainsi, même si les conditions de traitement dans les plaques minces initiales étaient très difficiles, dit Cara, « nous pouvions toujours voir le flux de chaleur provenant de la réaction de la résine. Cependant, en fabriquant également des pièces plus épaisses, nous avons pu voir exactement la différence de niveaux de flux de chaleur en fonction de l'épaisseur de la pièce et cela a validé notre suivi de durcissement dans les pièces minces. Notez que la courbe ci-dessus (également montrée sur la photo d'ouverture) a été obtenue en utilisant de la résine RTM 6 dans une plaque de 3,2 millimètres d'épaisseur.
Les résultats pour la détection du front d'écoulement de résine, cependant, étaient plus problématiques. « Pour le capteur près de la sortie, nous pouvions très bien voir l'écoulement, mais pas pour le capteur près du centre, où la résine est arrivée très tard », explique Cara. « La détection de front de flux avec des capteurs de flux de chaleur nécessite que le flux de résine produise un changement dans le champ thermique local. Cela se produit lorsque la résine n'est pas à la même température que la préforme. Il note qu'un T supérieur à 0,1°C est suffisant pour la détection. "Cependant, avec les essais de plaques CFRP minces, la température était très uniforme dans le moule et la résine est arrivée très lentement. Ainsi, le contraste thermique n'était pas suffisant pour détecter l'arrivée de résine par rapport au bruit thermique dans l'ensemble du système. L'arrivée de la résine à la sortie, cependant, était plus rapide en raison des canaux [espaces entre la préforme et le bord du moule, voir « Fabrication des pièces à géométrie complexe du RAPM »], ce qui permet de créer un contraste thermique plus important, plus facile à détecter et à surveiller. ”
Cara suggère que cette surveillance du front d'écoulement de résine pourrait être améliorée avec de nouveaux capteurs actifs que TFX a développés et qui utilisent une capacité de chauffage intégrée au sein du capteur. « Cela permet aux capteurs d'aider à fournir le contraste thermique nécessaire dans les pièces et les processus où cela est intrinsèquement difficile », explique-t-il.
Extension de la capacité de contrôle des processus composites
« Nous sommes satisfaits du travail que nous avons accompli jusqu'à présent », déclare Torres, « mais ce n'est qu'une première étape. L'objectif est d'utiliser ces capteurs de flux thermique pour gérer le traitement des composites dans les environnements de production. Cela est possible, explique Cara, en envoyant automatiquement un signal du système de capteurs à l'équipement d'injection en fonction de l'arrivée de la résine et à la presse en fonction d'une pente nulle dans la courbe de durcissement. Torres ajoute que TME dispose de systèmes de contrôle de processus pour la machine d'injection et la presse RTM qui gèrent la température et la pression. "La prochaine étape", dit-il, "est d'intégrer les capteurs TFX dans ces systèmes de contrôle et de gérer l'ensemble du processus à partir d'un ordinateur portable." Cara note que les capteurs TFX et l'acquisition de données fonctionnent également avec des capteurs de pression (par exemple, Kistler, Winterthur, Suisse) pour faciliter ce contrôle global du processus, et sa société développe un capteur qui mesurera le flux de chaleur, la température et pression dans un seul appareil intégré.
Mais ce contrôle de processus est-il abordable ? Cara affirme que l'investissement initial de 10 000 à 30 000 $ pour le système de surveillance génère généralement un retour sur investissement dans la phase de développement, en réduisant les essais et les erreurs grâce à une meilleure compréhension des processus et des pièces. « Le système permet ensuite de réaliser des économies au cours de la production, en réduisant le temps de cycle, en garantissant la répétabilité et en permettant une détection précoce des dérives ou des non-conformités. »
Chez GKN Fokker, Vergouwen pense qu'une fois la capacité de réduire le temps de cycle et d'améliorer les coûts prouvée, « alors il est possible d'imaginer des composites non seulement dans le type de composant de train d'atterrissage démontré dans les projets INNOTOOL 4.0 et HECOLAG, mais dans tous les types de les pièces. Cela ouvrirait notre espace de conception et nous permettrait de repousser encore plus loin les limites des trains d'atterrissage légers. » Besson voit une application encore plus large :« Ce type de contrôle de processus peut être développé pour toutes sortes de moules et de pièces composites. »
Résine
- Types de capteurs avec leurs schémas de circuit
- ams illuminera Sensors Expo 2019 avec des démonstrations innovantes
- Cartographie du flux de température domestique avec des capteurs bon marché
- Mesure des températures avec un capteur DS18B20 1 fil et Raspberry Pi
- Contrôler un effet avec de vrais capteurs
- Lecture de capteurs analogiques avec une broche GPIO
- Lecture de capteurs analogiques avec Raspberry Pi et Zabbix Supervisor
- Contrôleur d'irrigation Win10 IOT avec capteurs d'humidité
- Améliorer la surveillance de la pollution de l'air avec des capteurs IoT