Réduire le coût des matériaux d'impression 3D à fibre continue
Le DLR Institute of Composite Structures and Adaptive Systems (Braunschweig, Allemagne) est un institut de recherche de premier plan dans le domaine de la construction légère, qui poursuit de nouvelles technologies dans quatre domaines stratégiques :de la conception à la certification, la numérisation et l'industrie 4.0, le recyclage et les structures composites additives. CW a rendu compte plus tôt cette année du laboratoire d'innovation EmpowerAX de l'institut pour accélérer, renforcer et élargir le transfert de l'extrusion d'additifs vers l'industrie pour les composites imprimés en 3D. termine également une série de projets de R&D, notamment la simulation de l'extrusion d'additifs, la modification des thermoplastiques pour améliorer les performances de l'impression 3D et la production de filaments d'imprimante à fibre continue.
Ce dernier projet, intitulé ENDLOSEFFEKT (« effet sans fin »), est conçu pour améliorer la productivité, la qualité et le coût des matériaux renforcés de fibres de longueur infinie. « La disponibilité des filaments d'impression à fibres continues pré-imprégnés est limitée », explique Maik Titze, responsable de la fabrication additive au DLR Institute of Composite Structures and Adaptive Systems à Braunschweig. « Cette disponibilité limitée et la variété des matériaux utilisables, ainsi que les prix des matériaux, constituent un obstacle à l'application. Nous voulions concevoir une buse d'imprégnation afin que le même équipement utilisé pour produire des filaments standard remplis de fibres coupées pour le FDM [modèle de dépôt par fusion] puisse également produire des filaments continus renforcés de fibres. Cet équipement serait destiné aux entreprises qui fabriquent des filaments d'imprimante 3D, dans le but de réduire le coût de l'impression 3D avec des matériaux continus renforcés de fibres. »
Actuellement, la plupart des filaments d'imprimante 3D renforcés de fibres continues sont fabriqués par les mêmes sociétés qui vendent des machines d'impression à fibres continues, chaque matériau étant développé et optimisé pour un système d'impression particulier. Ces matériaux ont tendance à être quelque peu coûteux.
"Notre idée est de commencer avec n'importe quelle taille de fibre sèche, par exemple un câble de fibre de carbone 1K jusqu'à 50K, puis d'utiliser l'imprégnation directe par fusion à partir de granulés ou de granulés thermoplastiques de base par extrusion car c'est très rentable", explique Titze. « Vous n'avez pas besoin de produire de poudre ou de feuilles de polymère, ni d'utiliser des presses coûteuses ou des centaines de rouleaux pour réaliser l'imprégnation de la fibre. Ainsi, le traitement devient beaucoup plus accessible et abordable. »
Au lieu de presses, de bandes et de rouleaux, DLR a conçu un système utilisant des ultrasons. « Nous utilisons une sonotrode de 19,5 kilohertz qui dirige les vibrations dans le thermoplastique fondu qui entoure la fibre », explique Titze. « Ceci la matrice et le renforcement à 19 500 fois par seconde, ce qui donne une très bonne imprégnation."
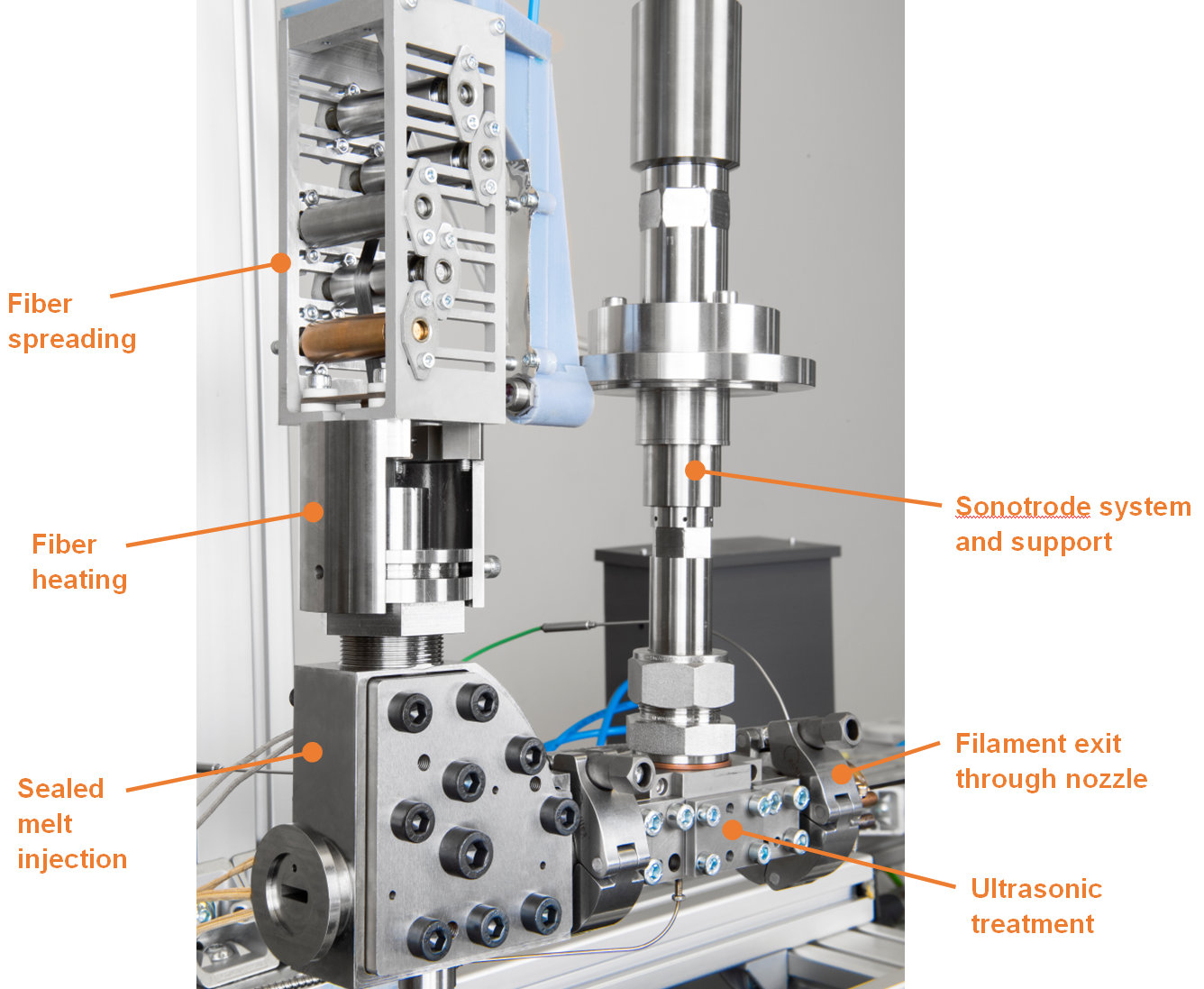
Le processus commence par l'étalement et le chauffage des fibres (Fig. 1). Ce renfort est ensuite introduit dans une enceinte étanche dans laquelle le polymère fondu est injecté. Lorsque la fibre traverse cette chambre, la résine fondue recouvre la fibre. "La fibre et le polymère passent ensuite dans une chambre à ultrasons, qui, avec une longueur de 80 millimètres, est très petite et compacte", note Titze. « La sonotrode émet des vibrations du filament de polymère renforcé de fibres, qui sort ensuite de la buse sous la forme que vous souhaitez. Par exemple, la buse peut être circulaire ou plate."
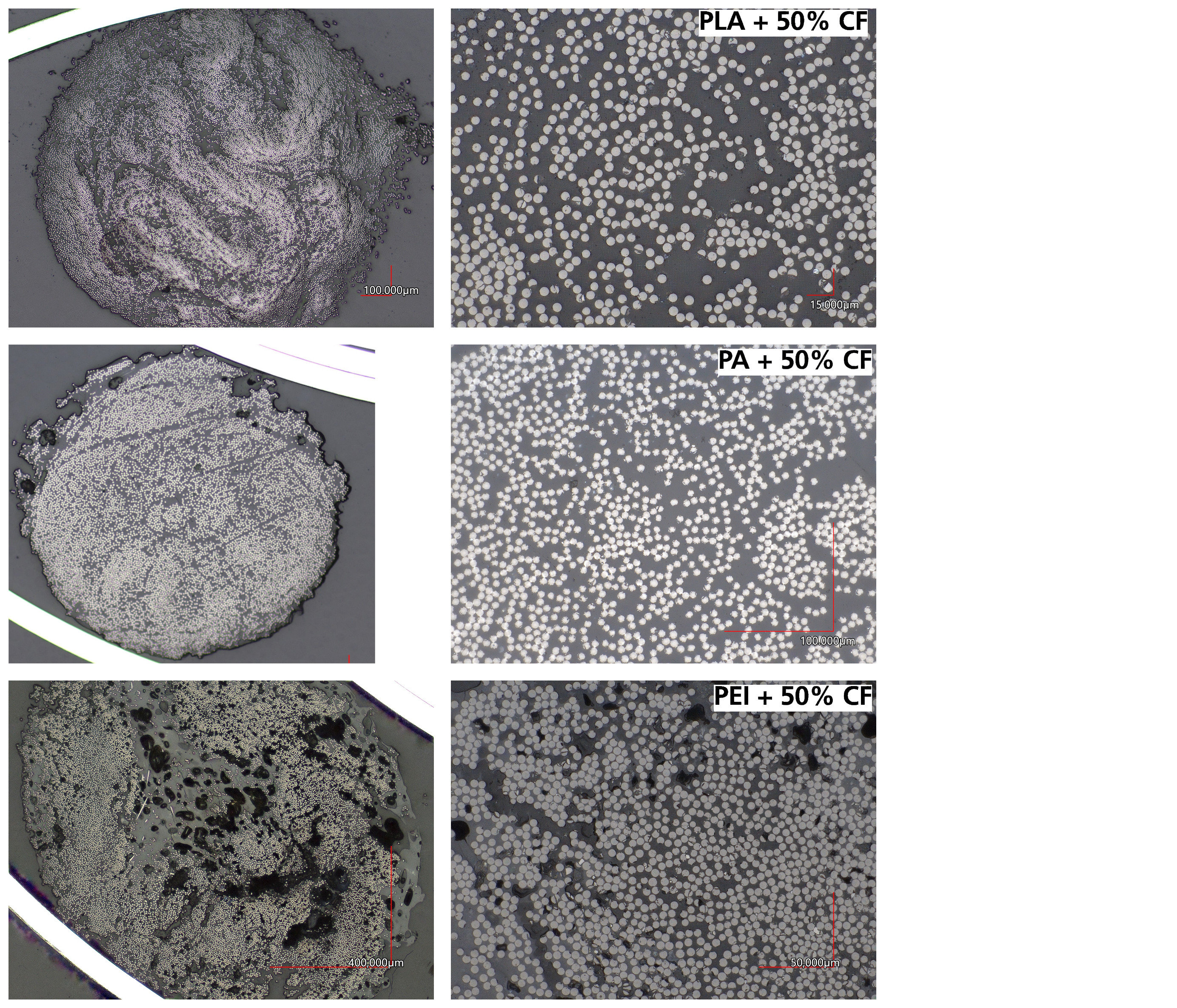
Les micrographies de la figure 2 montrent une fibre de carbone 12K imprégnée d'acide polylactique (PLA), de polyamide (PA) et de polyétherimide (PEI) à 50 % de volume de fibre. Le volume de fibre est réglable (30-50%) grâce à la conception de la buse de filière, explique Titze. «Nous pensons que jusqu'à 60% sera possible. Dans l'ensemble, plus de travail est nécessaire sur le processus, mais nous avons montré qu'il fonctionne avec de bons résultats initiaux et une vitesse de ligne de 5 millimètres/seconde. Il concède que c'est lent et pas économique, mais une nouvelle conception d'équipement devait être testée en juin, visant déjà à atteindre 3 mètres/minute.
« En règle générale, les vitesses seraient plus proches de 10 mètres/minute », explique Titze. "Cependant, la technologie vise également à permettre une production flexible de nouvelles combinaisons de matériaux, donc une vitesse légèrement inférieure pourrait aider à rendre les petites séries de production abordables.
Le processus que DLR a développé n'est pas sélectif envers un matériau - n'importe quelle fibre ou polymère peut être utilisé, dit Titze. « Ceci est important car les processus continuent de s'hybrider et de nouveaux matériaux sont nécessaires. Les matériaux pour l'impression 3D doivent devenir plus compétitifs, sinon l'impression 3D à fibre continue n'aura pas un grand avenir. En utilisant des pastilles ou des granulés thermoplastiques, nous pouvons réduire considérablement les coûts et l'équipement s'intègre dans un petit espace d'installation afin que même les petites entreprises puissent le mettre en œuvre. »
Le DLR Institute of Composite Structures and Adaptive Systems a lancé ce projet en octobre 2019 et le terminera en janvier 2022. « Notre objectif est de miniaturiser davantage la technologie et de l'intégrer dans une tête d'impression », explique Titze. « Donc, il s'agirait d'une imprégnation directe en ligne avec l'impression. Les deux approches seront transférés dans l'industrie. Il explique qu'en tant qu'association gouvernementale, DLR ne « vendra » rien et donc droits exclusifs. « Notre objectif est d'impliquer les fournisseurs de têtes d'impression afin de faire baisser les prix des matériaux à tous les niveaux et d'élargir l'application industrielle de la fabrication additive de fibres continues. »
Résine
- Les avantages cachés de la réduction des coûts de matériel d'impression 3D
- 6 façons de réduire le coût de l'impression 3D
- 5 tendances qui façonneront le marché des matériaux d'impression 3D en 2019
- Réduction du coût total de possession
- Le coût de la fibre de carbone :pourquoi la qualité en vaut la peine
- Coût de la fibre de carbone :facteurs qui influencent le plus
- La fabrication continue de fibres brouille la frontière entre l'impression 3D et l'AFP
- Impression 3D de composites avec fibre continue
- Les meilleurs matériaux flexibles pour l'impression 3D