Fraunhofer IPT développe des composites thermoplastiques pour le stockage d'hydrogène, les aubes de moteur et plus encore
Le développement de Fraunhofer IPT comprend (dans le sens des aiguilles d'une montre à partir du haut à gauche) des pales de ventilateur de moteur d'avion en composite thermoplastique, des structures hybrides composite-métal utilisant la structuration laser et l'AFP, la surveillance de la santé structurelle (SHM) des composites et des systèmes de traitement de bandes composites thermoplastiques, tels que les systèmes PrePro 2D et PrePro3D commercialisé par Conbility. Crédit photo :Fraunhofer IPT
En décembre 2020, j'ai publié un article sur la façon dont l'Institut Fraunhofer pour la technologie de production (IPT, Aix-la-Chapelle, Allemagne) développe une pose et un formage de ruban entièrement automatisés pour les aubes de ventilateur de moteur d'avion en polymère thermoplastique renforcé de fibres de carbone (CFRP). Il s'avère que la consolidation in situ (ISC) du ruban composite thermoplastique est un sujet que Fraunhofer IPT connaît bien, ayant piloté cette technologie à ses débuts avec les pionniers d'ISC Accudyne Systems Inc. (Newark, Del., États-Unis) et Automated Dynamics, maintenant Trelleborg Sealing Solutions Albany (TSS Albany, Niksayuna, NY, États-Unis). [Pour en savoir plus sur ces pionniers de l'ISC, voir « Consolidation des aérostructures thermoplastiques en place, Partie 1 et Partie 2 ».] », explique le Dr Henning Janssen, ingénieur en chef et chef du département des plastiques renforcés de fibres et de la technologie des systèmes laser chez Fraunhofer IPT. Il note que la technologie LATW a beaucoup changé, en particulier au cours des 10 à 15 dernières années. Ce blog donne plus de détails sur le développement par Fraunhofer IPT du LATW et des composites thermoplastiques en général, ainsi que sur la direction que prend la technologie à l'avenir.
Évolution de l'enroulement de ruban laser
« Lorsque nous avons commencé il y a 30 ans, la technologie laser n'était pas prête pour le traitement à grande vitesse des composites thermoplastiques », explique Janssen. « Vous pouvez imaginer que, surtout du côté des commandes, vous n'aviez qu'une caméra analogique. Maintenant, nous avons une bien meilleure technologie. Par exemple, lorsque nous avons développé une tête de bobinage laser compacte en 2008, ce qui a abouti à la création de l'AFPT Allemagne (Dörth, Allemagne), nous avons dû utiliser une caméra de 16 pixels x 16 pixels, qui offrait une fréquence d'images de seulement huit images par seconde. Désormais, nous avons facilement 640 x 480 pixels et un traitement de 50 images ou plus par seconde. Il explique que c'est important, « car avec l'enroulement de ruban laser que nous avons développé, l'un des principaux avantages est que vous pouvez examiner le processus et également modifier la puissance de traitement en quelques millisecondes. Cela vous donne un bon avantage, par exemple, lorsque vous contournez des géométries complexes, comme le dôme des récipients sous pression, où la vitesse d'enroulement ralentit, et vous devez réduire la puissance de chauffage du laser. Vous devez alors réajuster au fur et à mesure que l'enroulement reprend de la vitesse le long du cylindre du réservoir. Cela n'était pas possible il y a 15 ans, car les technologies laser, système de contrôle et d'imagerie thermique n'étaient pas prêtes ou étaient trop chères et pas aussi puissantes que ce que nous avons aujourd'hui.
Janssen poursuit : « Donc, beaucoup de choses se sont développées du côté numérique. Maintenant, par exemple, nous fournissons quelque chose comme un jumeau numérique, où vous pouvez mapper toutes les informations de votre capteur sur le récipient sous pression, afin que vous puissiez comparer la pièce telle qu'elle est fabriquée par rapport à la conception numérique pour évaluer la qualité de la pièce et prédire les performances. L'utilisation de capteurs et de modèles de processus virtuels nous permet également de prédire la résistance du stratifié telle que définie par son historique de traitement. Ceci est important car le LATW utilisant du ruban thermoplastique utilise un chauffage et un refroidissement rapides où les propriétés du matériau et de la pièce sont déterminées pendant le processus d'enroulement lui-même, en raison de l'absence d'étape de post-traitement thermique, note-t-il. Il est donc essentiel de pouvoir contrôler rapidement les processus.
Il y a également eu des développements dans les matériaux, dit Janssen. « Il y a vingt ans, il n'y avait qu'une quantité limitée de matériaux de bandes composites thermoplastiques disponibles, comme l'APC-2 de Cytec, qui est maintenant Solvay (Alpharetta, Géorgie, États-Unis) », explique-t-il. « Mais maintenant, beaucoup plus de matériaux sont qualifiés pour les applications industrielles, et vous avez également beaucoup de matériaux de base comme le polypropylène (PP) renforcé de fibre de carbone et également de fibre de verre, ainsi que le polyamide six (PA6), par exemple, qui est beaucoup utilisé dans l'industrie automobile. Il y a aussi maintenant des applications pour LATW qui sont plus vers la production de masse. Par exemple, il y a une poussée vers les manchons de rétention et d'autres pièces dans les moteurs électriques. Ce sont de simples bagues ou tubes composites thermoplastiques, mais dans des volumes de 10 000 à 50 000 par an. »
ambliFIBRE, canalisations pour pétrole et gaz
Une partie de la commande numérique dans LATW que Janssen décrit ci-dessus a été développée dans le projet ambliFIBRE (2015-2018). « Il y avait de nombreux partenaires dans ce projet », dit-il, « mais l'un d'eux était Baker Hughes (Newcastle, Angleterre et Houston, Texas, États-Unis) et nous avons utilisé notre équipement LATW pour leurs tuyaux non métalliques. » Notez que peu de temps après la fin d'ambliFIBRE en 2018, Baker Hughes a annoncé sa joint-venture avec Saudi Aramco (Riyad, Arabie saoudite) pour étendre l'utilisation de tuyaux non métalliques, y compris l'utilisation possible de plastique renforcé de fibres de carbone (CFRP).
Baker Hughes vise désormais à accélérer l'introduction de matériaux non métalliques dans le secteur de l'énergie, et d'autres entreprises utilisent également la technologie laser pour les tuyaux, comme Magma (Portsmouth, Royaume-Uni). (Voir « Tuyau thermoplastique à la hausse dans les grands fonds » et « Magma Global livre une colonne montante composite haute pression…).
« Il est également assez courant d'utiliser un enroulement de ruban laser pour les colonnes montantes et les conduites d'écoulement en composite thermoplastique », explique Janssen. "Bien que ce ne soit pas encore connu dans d'autres industries." Il ajoute qu'une grande partie de l'attention récemment accordée à LATW a été pour les réservoirs de stockage d'hydrogène, mais la technologie a déjà une application beaucoup plus large.
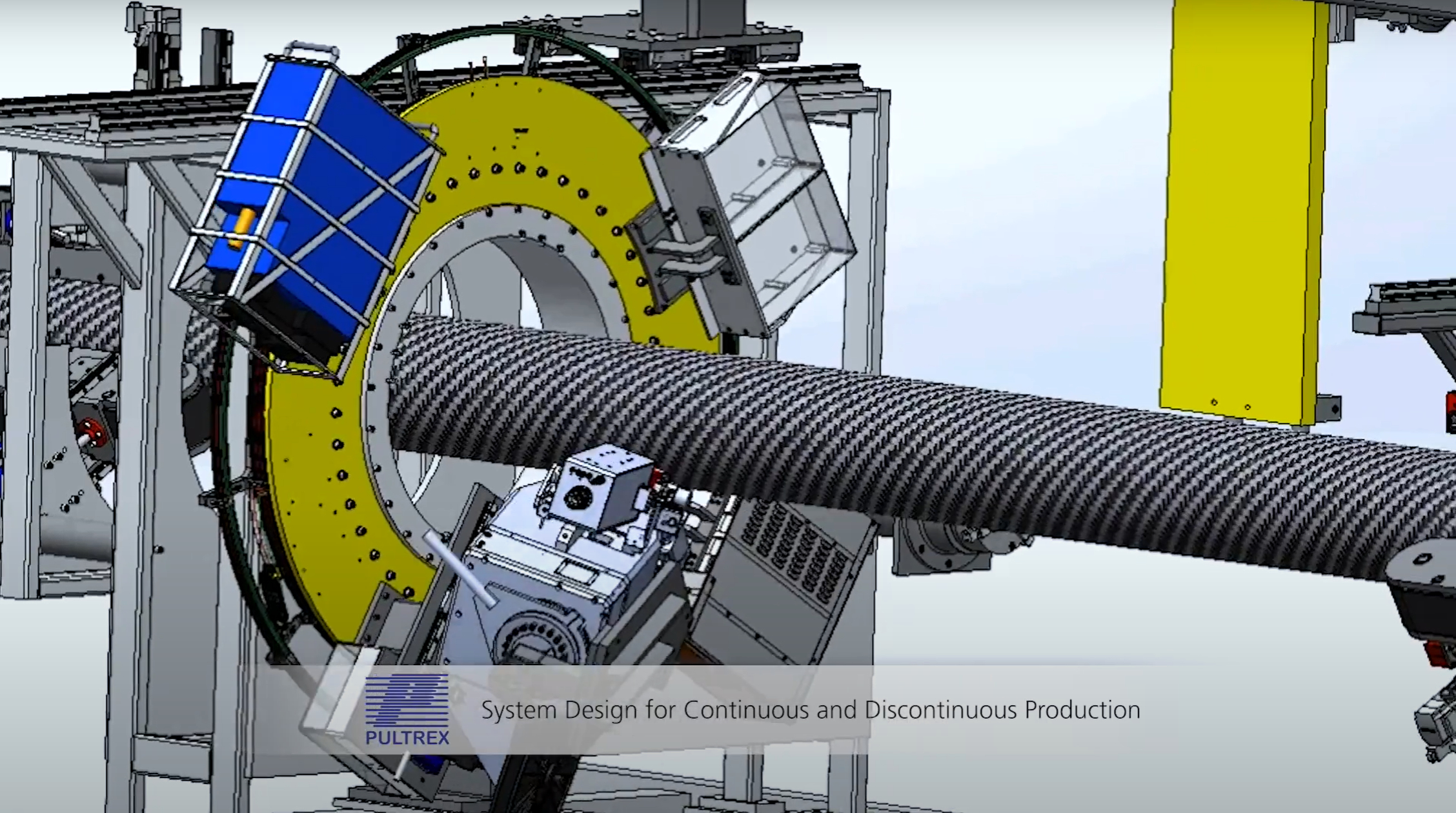
Dans le cadre du projet ambliFIBRE, Fraunhofer IPT a développé des modèles de contrôle de processus numériques pour l'enroulement de ruban discontinu (par exemple, des réservoirs) et continu, par exemple, pour produire des tuyaux de plusieurs kilomètres de long. Crédit photo :vidéo Fraunhofer IPT pour le projet ambliFIBRE
« Et ce que nous proposons chez Fraunhofer IPT pour ces applications est essentiel », déclare Janssen. « De toute évidence, nous n'exploitons pas de ligne de production à grande échelle pour la production de tuyaux en continu ici dans notre institut, mais ce que nous proposons à nos clients, ce sont des tests de matériaux et la qualification de produits. Il y a la pyramide de test, par exemple, basée sur le DNV-GL F114, en commençant par la qualification et le test du polymère et des fibres, puis en passant à la microstructure ou mésostructure du stratifié composite. Nous effectuons donc de nombreux tests au niveau du coupon, puis nous adaptons à des tuyaux plus petits et des tuyaux représentatifs, par exemple, car l'enroulement vous donne des propriétés différentes de celles du pressage ou de la pose automatisée de ruban (ATL)."
En outre, note-t-il, « parce que vous avez des contraintes différentes dans votre matériau, beaucoup de ces matériaux composites sont testés dans des tuyaux plus petits, par exemple de 2 à 3 pouces jusqu'à plusieurs mètres de long. Nous effectuons donc ces tests, puis nous appliquons notre compréhension du processus pour la longueur réelle de la pièce, par exemple 2-3 kilomètres. Et c'est très intéressant, car le temps de traitement à cette longueur peut s'étendre sur quelques jours, et vous devez tenir compte du rétrécissement ainsi que d'autres facteurs, tels que les changements de température de l'air ambiant, qui peuvent avoir un impact considérable. »
LATW dans les réservoirs de stockage d'hydrogène
Janssen explique que Fraunhofer IPT travaille avec des sociétés pétrolières et gazières depuis 2000. « Et puis, il y a huit ans, nous avons compris qu'il s'agissait à peu près de la même technologie dont vous avez besoin pour les réservoirs d'hydrogène », se souvient-il. « Et maintenant, nous avons une grande initiative pour la fabrication d'hydrogène ici à l'IPT et également pour les composites en fibre de carbone dans les piles à combustible. Nous mettons en place une installation de 80 millions d'euros pour la fabrication automatisée de piles à combustible et investissons également dans une nouvelle installation de bobinage assez grande afin de pouvoir produire des pièces jusqu'à 7 mètres de long et 2,5 mètres de diamètre, que nous utiliserons également pour les grands récipients sous pression. »
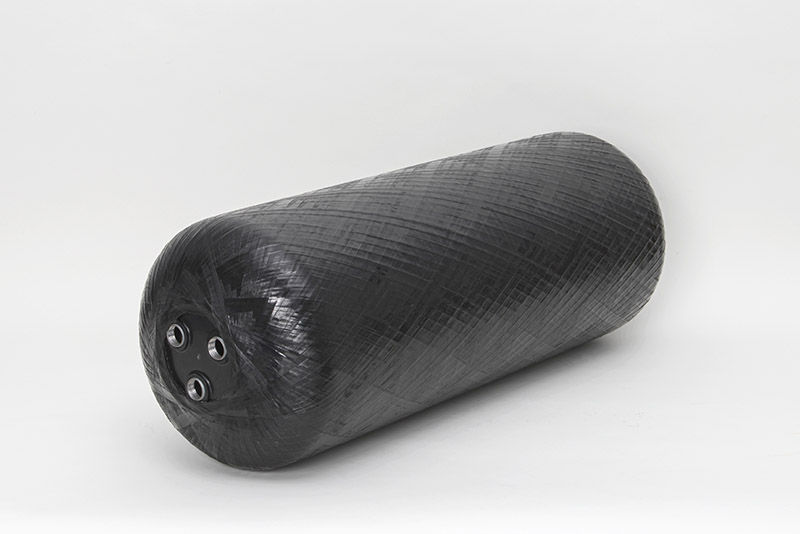
Le LATW utilisant des rubans composites thermoplastiques n'est pas encore à la pointe de la technologie pour la fabrication de récipients sous pression, explique Janssen, « car la chimie des thermoplastiques, ainsi que leur traitement et leur durabilité font encore l'objet de recherches. Mais nous sommes fermement convaincus que la faible perméabilité, la ténacité et la recyclabilité offertes par les thermoplastiques sont importantes. » Il voit également un potentiel pour les thermoplastiques dans les récipients sous pression de type V, qui sont entièrement composites mais n'utilisent pas de revêtement thermoplastique séparé. « Ceux-ci pourraient fournir une solution future pour certaines applications mobiles de stockage d'hydrogène, telles que les camions électriques à pile à combustible. »
« Nous voyons également que le thermoset conventionnel l'enroulement filamentaire est limité en ce qui concerne les angles d'enroulement minimaux », explique Janssen. « Par exemple, il faut faire le tour des dômes en couches hélicoïdales avec un angle de fibre d'au moins 10°. Donc, vous ne pouvez pas mettre un renfort à 0° dans un réservoir à enroulement filamentaire conventionnel. Cependant, soutient-il, « dans le LATW classique, le préimprégné thermoplastique entrant est directement soudé au substrat, vous pouvez donc aller dans n'importe quelle direction, ce qui vous donne beaucoup plus de liberté de conception. Nous menons actuellement des projets avec des partenaires de l'industrie automobile pour développer des récipients sous pression thermoplastiques pour le stockage de l'hydrogène qui sont sûrs, économes en énergie et faciles à recycler. »
Pales de ventilateur en composite thermoplastique
Fraunhofer IPT a une très solide expérience dans le domaine des turbomachines, déclare Janssen. « Nous avons ici à Aix-la-Chapelle le Centre international de fabrication de turbomachines, ou ICTM, une communauté préconcurrentielle où nous travaillons conjointement avec les motoristes et leurs fournisseurs dans le cadre de projets de R&D préconcurrentiels pour développer et améliorer la technologie de fabrication. »
Il note qu'au cours des 20 dernières années, l'accent a été mis principalement sur l'usinage d'alliages à base de titane ou de nickel pour des produits avancés de la section de compression et des turbines, tels que le disque intégré d'aube (blsk). Dans la section froide, des pièces en matériaux composites - telles que des pales de ventilateur en composite de fibre de carbone - ont été développées par GE dans les années 1990 et sont maintenant en service dans le GE90 et le GEnx. "Maintenant, cependant, les composites à matrice céramique (CMC) sont considérés comme des matériaux de nouvelle génération pour la partie chaude des moteurs à réaction", explique Janssen, "permettant des températures plus élevées avec moins de poids pour une plus grande efficacité."
« La fabrication de pièces en composite par rapport au métal est très différente, poursuit-il. « Dans le métal, vous commencez avec une masse de matériau et dérivez la pièce par traitement soustractif, principalement par usinage, de sorte que la conception ne dépende pas autant de la fabrication. C'est tout le contraire dans les composites, qui nécessitent toujours une sorte de processus génératif. Nous avons donc décidé d'aborder les nouvelles stratégies de pales de ventilateur du point de vue de la fabrication. »
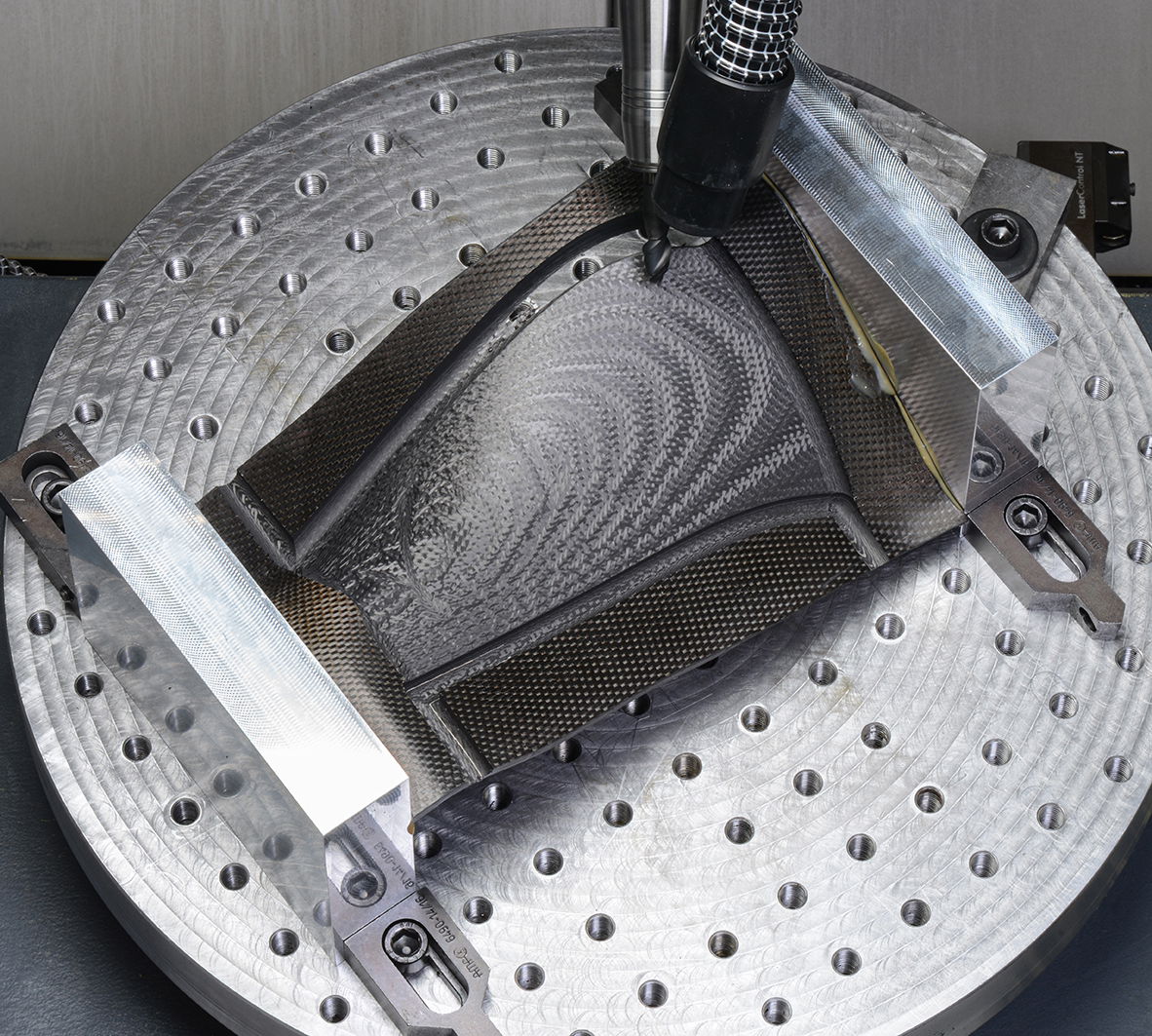
Il note également l'entreprise commune Clean Sky 2, dans laquelle Fraunhofer dirige les activités d'éco-conception. Fraunhofer IPT se concentre sur l'éco-conception des moteurs, qui comprend l'analyse du cycle de vie et l'évaluation de l'impact environnemental. « C'est pourquoi nous avons commencé à nous intéresser aux composites thermoplastiques », explique-t-il. « Jusqu'à présent, nous sommes à un TRL [niveau de préparation technologique] très bas. Pour l'instant, le développement concerne la fabrication et l'essai de différentes voies de processus, telles que la superposition de forme quasi nette et un peu de thermoformage - qui s'apparente plus à une étape d'étalonnage - puis la finition en termes d'usinage. Donc, il y a encore beaucoup de travail devant nous. »
Parallèlement, Fraunhofer IPT étend son expertise dans l'usinage de composants métalliques de moteurs d'avions aux composites, en utilisant sa technologie numérique pour surveiller et évaluer les paramètres d'usinage sur chaque aube. Mais l'objectif des composites n'est-il pas de passer d'une telle fabrication soustractive à une fabrication plus additive pour moins de déchets ? « Oui, mais pour certaines voies de traitement, l'usinage est nécessaire pour respecter les tolérances dimensionnelles », explique Janssen. « Ce sur quoi nous travaillons en ce moment est très proche de la forme nette. »
Il souligne que la conception actuellement développée est un stratifié thermoplastique de 0,75 pouce d'épaisseur à la racine et de seulement 2 millimètres d'épaisseur à la pointe. « Et puis il y a différentes stratégies de conception, dont nous discutons avec les ingénieurs de conception. Aussi, avez-vous un autoclave ou une étape de presse pour ce genre de pièce très chargée ? Cela va aussi jouer un rôle sur les contraintes internes, car on sait que cette pale se tord un peu lors de la rotation. Et, bien sûr, les impacts d'oiseaux sont un problème clé. Pour ce dernier, Janssen considère la ténacité accrue des thermoplastiques comme un catalyseur, soulignant que les composites PPS (sulfure de polyphénylène) sont utilisés dans les bords d'attaque des ailes pour cette même raison.
Les applications futures des composites thermoplastiques
J'ai posé des questions sur la possibilité d'utiliser des composites thermoplastiques dans les nacelles des moteurs , ce qui pourrait peut-être aider à fournir une solution à quatre récents incidents de panne de pale, où, comme indiqué dans une Semaine de l'aviation de mars 2021 article :
"… les dommages causés par des fragments d'aubes frappant des sections du capot du moteur, ou nacelle, ont déclenché une série d'événements qui ont causé la rupture de grandes pièces de structure, y compris des parties d'entrées de moteur et de capots de soufflante. un moyen." Dans les quatre accidents, le fuselage de l'avion a subi des dommages, et pour le vol Southwest 1380 en avril 2018, l'une des fenêtres a été délogée, causant la mort d'un passager.
« L'industrie est intéressée à utiliser des composites thermoplastiques dans les compartiments moteur », déclare Janssen, « cependant, il s'agit d'un développement à long terme. » L'un des enjeux d'un tel développement est la certification par les autorités de l'aviation, un autre domaine dans lequel Fraunhofer IPT est actif. « Nous discutons actuellement avec les organismes de certification de la manière d'aider à réduire l'effort de certification en prouvant numériquement que les nouveaux processus de fabrication sont conformes aux normes actuelles et en évolution. C'est donc une nouvelle façon de penser. Dans la fabrication du 21e siècle, il y a tellement de données disponibles, il ne s'agit pas seulement de certifier un processus ou une conception par des tests, puis cela est gelé. » En d'autres termes, l'accent mis aujourd'hui sur l'industrie 4.0 et les composites 4.0 est que les capteurs et les logiciels compatibles avec l'IA recueilleront en permanence des données et développeront des informations qui optimiseront ensuite en continu la fabrication et, à leur tour, renverront ces informations dans le fil numérique pour améliorer les conceptions. C'est en effet très différent de la fabrication d'aujourd'hui.
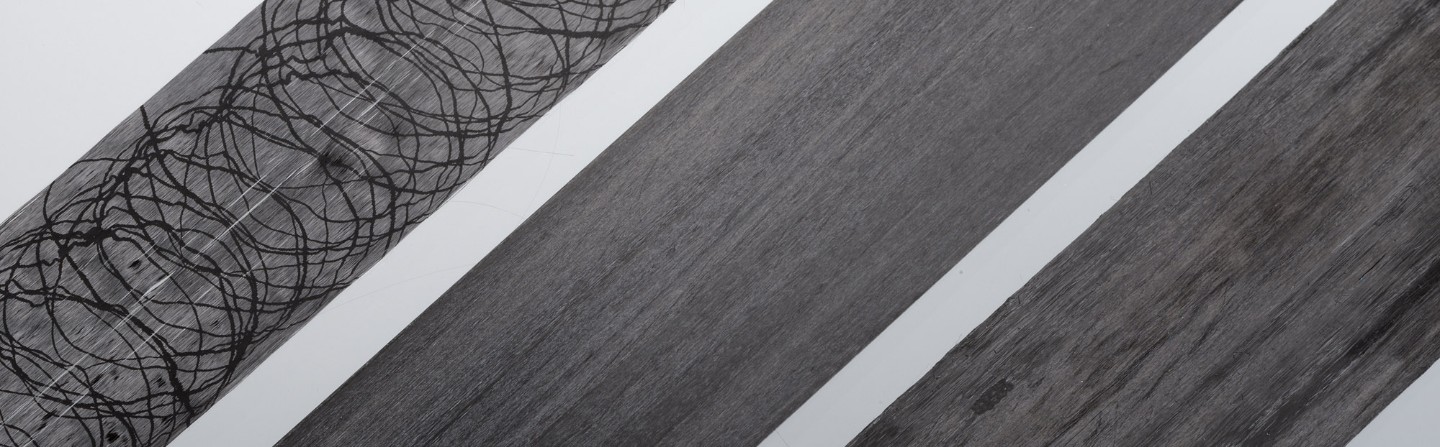
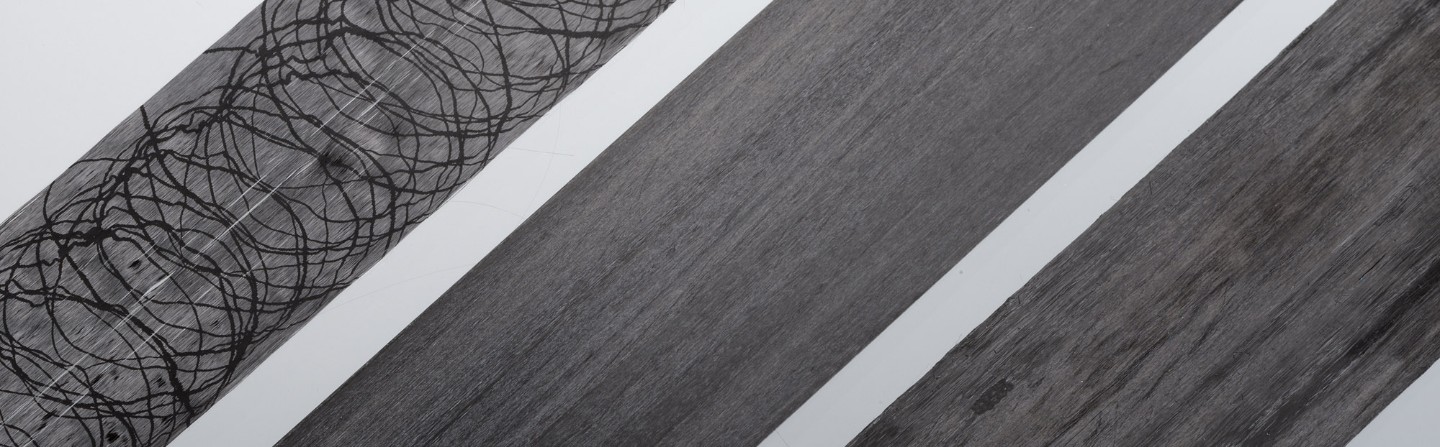
Le travail de Fraunhofer IPT concernant la certification, dit Janssen, "pourrait aider à activer de nouvelles technologies telles que les composites thermoplastiques pour les pièces de moteur, c'est-à-dire une fois que tous les aspects, y compris la technologie, la conception et la gestion des risques, sont pris en compte". Il affirme que les composites thermoplastiques offrent un énorme potentiel pour aider à surmonter les principaux défis d'une variété des secteurs industriels, et note que Fraunhofer IPT s'efforce de surmonter la complexité de traitement des composites thermoplastiques, par exemple en utilisant les nouvelles méthodes de fabrication numérique disponibles. « De plus, le potentiel des composites thermoplastiques ne peut être pleinement exploité qu'une fois que le cycle de vie complet, y compris la réutilisation et le recyclage, est pris en compte », déclare Janssen. « Ainsi, Fraunhofer IPT travaille également sur le recyclage mécanique des composites thermoplastiques. Nous voyons qu'il sera possible d'obtenir des matériaux recyclés de grande valeur en tenant compte à la fois des données générées lors de la fabrication et de celles générées tout au long du cycle de vie des composants composites.
Résine
- Covestro intensifie ses investissements dans les composites thermoplastiques
- Meilleur graveur laser 2021 pour lames et manches de couteaux
- Le projet RECONTRAS valide l'utilisation des micro-ondes et du soudage laser pour obtenir des composites recyclables
- OTOMcomposite développe un logiciel pour la production de Composites 4.0 utilisant le placement et le bobinage de bandes assistés par laser
- Dépannage du thermoformage des composites thermoplastiques
- TPAC et TPRC développent un procédé de recyclage des composites thermoplastiques
- Soudage de composites thermoplastiques
- Le consortium des composites thermoplastiques vise une production à haut volume pour l'automobile et l'aérospatiale
- La société RTP développe des composés thermoplastiques légers et résistants