Connexions pour le contrôle :interfaces de communication pour les capteurs de position et de mouvement
Les interfaces de communication constituent le lien essentiel entre les capteurs (les « nerfs » d'un système de contrôle) et les contrôleurs (le « cerveau »). Une variété impressionnante de technologies de communication a été introduite pour fournir ce lien, généralement avec des fonctionnalités et des capacités adaptées à un certain type de système de contrôle. Examinons quelques technologies de communication largement utilisées pour le contrôle de mouvement.
Solutions spéciales pour cas particuliers
Pour certains capteurs qui fournissent une rétroaction pour le contrôle de mouvement, la technologie de mesure dictera l'interface de communication. Les encodeurs incrémentaux délivrent un flux continu d'impulsions de signal - une pour chaque fois que l'arbre de l'encodeur tourne d'une certaine quantité. Ils excellent dans le contrôle de la vitesse, car le contrôleur peut déterminer avec précision le taux de rotation à partir de l'intervalle entre les impulsions.
De nombreux codeurs incrémentaux transmettent deux signaux de sortie, appelés A et B, avec une différence de phase de 90°, permettant au contrôleur de déterminer le sens de rotation. Certains émettent également un signal Z une fois par rotation à un angle de rotation défini. Cela fournit un point de référence précis.
La connexion entre un codeur incrémental et son contrôleur doit être point à point, avec un câble dédié reliant chaque codeur à son contrôleur. Les communications sont généralement basées sur un signal différentiel transmis sur un câblage à paires torsadées, le nombre de paires de conducteurs dans le câble dépendant du nombre de signaux (A, B et Z).
Les pilotes de sortie des encodeurs doivent être compatibles avec l'interface du contrôleur — les pilotes de sortie Push-Pull (HTL) ou RS-422 (TTL) sont couramment utilisés. Ces normes spécifient la tension du signal.
Capteurs de position absolue

Le reste de cet article se concentrera sur les capteurs de position absolue tels que les codeurs et les inclinomètres. Ces appareils signalent une position mesurée à un instant précis, soit sous forme de niveau de tension/courant (codeurs analogiques), soit en transmettant un mot numérique ou « télégramme » (codeurs numériques). Ces dispositifs sont idéaux pour les applications de contrôle de position.
Les capteurs analogiques ont une longue histoire, avec des systèmes de contrôle antérieurs utilisant des potentiomètres (résistances variables). Plus récemment, des capteurs numériques avec convertisseurs N/A intégrés ont été introduits. Ceux-ci sont disponibles avec des sorties de tension (par exemple, 0-5 V) ou de courant (par exemple, 0-20 mA). Ils comportent des convertisseurs N/A programmables de sorte qu'une plage prédéterminée de mouvement mécanique (allant d'une fraction de tour à plusieurs révolutions) peut être réglée pour couvrir la plage de sortie électrique complète du système (par exemple, 0-5 V, 0-20 mA ). Cela améliore la précision et la résolution sur la plage de mouvement la plus importante. Les capteurs analogiques nécessitent des connexions point à point, souvent avec un fil de relativement gros calibre pour limiter la résistance électrique.
Les codeurs absolus avec des interfaces parallèles de bits rapportent les mesures sous la forme d'un mot numérique, avec un conducteur séparé pour chaque bit. La réponse est pratiquement instantanée. La connexion est point à point, généralement via un câble de type ruban. Comme ce type de câble est relativement encombrant et peu flexible, les systèmes parallèles fonctionnent mieux sur de courtes distances.
Câblage point à point numérique

Avec un câblage point à point, un câble dédié relie le contrôleur à chaque capteur individuel. Les interfaces SSI (Serial Synchronous Interface) et BiSS (Bidirectional Serial Synchronous) pour codeurs absolus utilisent des systèmes de câblage point à point. Ce sont des interfaces numériques qui peuvent se connecter directement à des automates ou à d'autres contrôleurs. Les connexions SSI offrent une bonne vitesse (fréquences d'horloge jusqu'à 2 Mhz), une haute résolution, un câblage flexible et une communication fiable jusqu'à quelques centaines de mètres (bien que les débits en bauds soient réduits pour les distances plus longues). Les protocoles SSI fournissent une détection d'erreur de base (câble rompu, court-circuit, cohérence des données).
BiSS est une version avancée de SSI qui prend en charge les communications en temps réel entre les dispositifs de contrôle et les capteurs/actionneurs des servomoteurs, robots et autres systèmes d'automatisation. L'interface permet également au contrôleur de définir des paramètres opérationnels dans les appareils esclaves. Il existe plusieurs variantes de BiSS, notamment BiSS C (communications continues) et BiSS Line (conçu pour des configurations combinant alimentation électrique et transmission de données dans un seul câble). Les normes d'interface open source SSI et BiSS ne sont pas propriétaires, avec des licences gratuites.
Les communications SSI et BiSS utilisent des connexions point à point, généralement RS-422. Plusieurs appareils peuvent être connectés en guirlande pour une disposition des câbles plus efficace.
Bus de terrain :systèmes de câblage d'accès partagé

Le câblage point à point fonctionne bien pour les systèmes avec de courtes distances et un nombre limité d'appareils, mais à mesure que le nombre de capteurs augmente, les dispositions de câblage peuvent devenir difficiles à manier. À mesure que les systèmes automatisés devenaient plus sophistiqués et que le nombre d'appareils connectés augmentait, plusieurs fabricants ont introduit des systèmes de bus de terrain. Ces réseaux de fonctions sont basés sur une topologie en bus, avec plusieurs appareils partageant une dorsale de câblage commune. Les systèmes de bus de terrain sont fiables, rapides et relativement économiques. Les applications vont des convoyeurs et des installations de fabrication aux équipements mobiles, aux équipements médicaux, aux éoliennes et aux panneaux solaires.
Le fait que plusieurs appareils partagent un canal de communication commun peut entraîner des problèmes de temps de réponse - lorsque le trafic sur le bus est important, les capteurs individuels peuvent voir leurs messages retardés d'une durée imprévisible. Pour contourner ce problème, la plupart des conceptions de bus de terrain permettent à l'opérateur de classer les appareils par ordre d'importance. Cela permet de garantir que les messages critiques bénéficient d'un traitement prioritaire. La couche physique des systèmes de bus de terrain est généralement basée sur des câbles à paires torsadées (par exemple, EIA-485).
Les normes de bus de terrain populaires incluent Controller Area Network (CAN) de Bosch, CANopen, Profibus (Process Field Bus) de Siemens et DeviceNet d'Allen-Bradley/Rockwell. DeviceNET, largement utilisé en Amérique du Nord, combine la couche physique CAN avec des protocoles de niveau supérieur CIP (Common Industrial Protocol). SAE J1939, qui utilise les normes de transport de données CAN, est optimisé pour les véhicules lourds.
Les réseaux sont constitués d'éléments physiques (fils, connecteurs et composants électroniques qui contrôlent le flux de signaux) et d'éléments logiques (qui adressent des schémas, des protocoles de communication, des profils d'appareils, etc. qui sont implémentés dans un logiciel). Dans le monde des bus de terrain, de nombreux systèmes utilisent les normes CAN pour définir les aspects physiques des réseaux, tandis que les protocoles de niveau supérieur, tels que CANopen, DeviceNet, J1939, etc., fournissent des fonctionnalités de bout en bout.
Ethernet industriel
L'Ethernet industriel utilise les mêmes fondements techniques que l'Ethernet de bureau, mais avec des améliorations qui le rendent mieux adapté aux conditions d'usine difficiles. Les unités de commutation de qualité industrielle peuvent comporter des boîtiers robustes étanches à l'eau et à la poussière, tandis que de nombreux appareils utilisent des connecteurs M12 robustes à la place de connecteurs RJ45 plus vulnérables.
Il existe également des mises à niveau importantes des protocoles de communication. Les applications industrielles, en particulier le contrôle de mouvement, nécessitent souvent que les commandes fonctionnent en temps réel, sans les retards de transmission imprévisibles (latence ou gigue) qui peuvent survenir dans les réseaux Ethernet ordinaires. Les systèmes Ethernet industriels tels que Profinet IRT, EtherNet/IP et Ethernet Powerlink résolvent ce problème via des piles de protocoles modifiées et un matériel spécial qui donne aux messages critiques un accès prioritaire à la bande passante du réseau. Les composants spéciaux nécessaires pour y parvenir peuvent ajouter à la complexité et au coût du système.
Il convient de noter que si Ethernet offre une vision d'un nombre illimité d'appareils et d'options de topologie flexibles, les problèmes de performances du système, en particulier pour les applications de contrôle de mouvement en temps réel, peuvent nécessiter des compromis de conception qui réduisent le trafic local et fournissent des voies de communication directes pour les applications critiques. composants.
IO-Link est un système de communication peu coûteux et facile à mettre en œuvre conçu pour simplifier les connexions entre les réseaux de bus de terrain ou Ethernet industriels et les simples capteurs ou actionneurs situés dans l'usine. D'un côté d'un périphérique de passerelle maître IO-Link se trouve une interface vers le réseau à l'échelle de l'usine, tandis que l'autre côté dispose de plusieurs connexions point à point vers des capteurs individuels.
L'interface IO-Link pour les appareils finaux est relativement simple, éliminant la nécessité de prendre en charge des protocoles de communication complexes au niveau du capteur/actionneur. IO-Link prend en charge une variété de types de données, y compris les données de mesure, les instructions de configuration de l'appareil et les informations sur les paramètres de condition de fonctionnement tels que la température.
Communications sans fil
Les technologies sans fil permettent des communications avec des machines mobiles (par exemple, des véhicules guidés autonomes) ou des équipements qui doivent être déplacés fréquemment. Wi-Fi (IEEE 802.11) et Bluetooth sont des normes largement utilisées pour les communications sans fil à courte portée. D'autres normes sont disponibles pour les communications à plus longue portée, bien que celles-ci puissent avoir des débits binaires inférieurs. Les réseaux 5G émergents promettent des débits de données élevés et une faible latence.
Les communications sans fil peuvent être moins fiables que les connexions câblées dans des environnements électriquement bruyants et peuvent ne pas convenir aux signaux de retour fortement dépendants du temps. Dans le cas d'un robot d'entrepôt, par exemple, un signal sans fil peut être utilisé pour demander à la machine de récupérer du matériel à partir d'un emplacement particulier. Cependant, les capteurs de direction, de contrôle de la vitesse et d'évitement des collisions sont généralement câblés au système de contrôle pour garantir une réponse fiable et instantanée.
Normes ouvertes pour la compatibilité
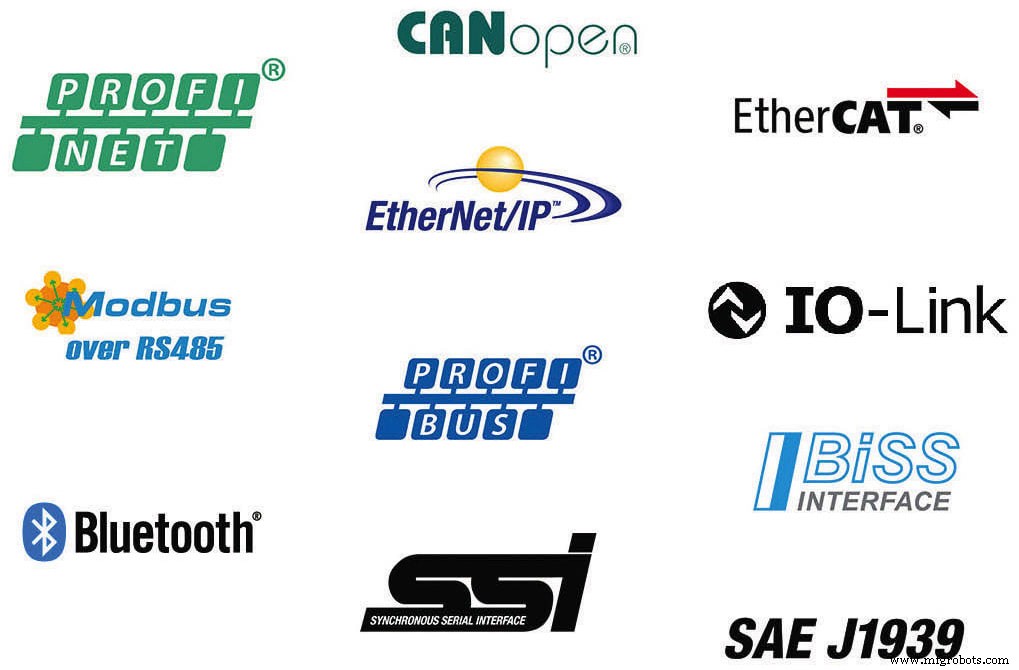
Aucun fournisseur ne peut fournir à lui seul le meilleur équipement de sa catégorie pour chaque partie d'un système d'automatisation complexe et les fournisseurs de technologies de réseau industriel sont passés de systèmes de réseau propriétaires à la prise en charge de normes d'interface et de réseau ouvertes (indépendantes du fournisseur). Grâce à ces normes, les acheteurs d'équipements de contrôle de mouvement peuvent mélanger et assortir des composants certifiés par les normes de différents fournisseurs en s'attendant à ce que tout fonctionne ensemble.
Les organisations de normalisation importantes de l'industrie incluent l'Open Device Vendors Association , sponsors des standards DeviceNet et Ethernet/IP; le CAN dans l'association d'automatisation , sponsors des protocoles CANopen; et Profibus Nutzerorganisation , sponsors des interfaces Profibus et Profinet.
Cet article a été rédigé par Christian Fell, directeur général de FRABA Inc., Hamilton, NJ. Pour plus d'informations, visitez ici .
Capteur
- Capteurs et processeurs convergent pour les applications industrielles
- GE présente un nouveau produit pour les applications de contrôle et de surveillance
- Plages de contrôle pour les planificateurs de maintenance et autres
- Conseils de sélection des contrôleurs et enregistreurs pour les applications alimentaires et boissons
- Le contrôle de mouvement intégré à la sécurité permet à la sécurité et à la productivité de coexister
- Capteur de gaz portable pour la surveillance de la santé et de l'environnement
- Capteur de position inductif sans contact
- Capteurs de déplacement à courants de Foucault pour l'industrie
- Capteur de débit et de température de laboratoire sur puce