Résistance à l'abrasion personnalisée :protections de longboard
Le skate est un sport rude, à la fois pour le rider et pour la planche. Les longboards (un sous-ensemble de skateboards plus longs) et les skateboards de rue (le type que vous avez probablement l'habitude de voir) souffrent de carres qui se fendent à l'impact ainsi que d'un phénomène appelé « queue de rasoir ». La queue de rasoir se produit parce que les queues de kick (les deux extrémités de la planche) sont claquées contre le sol à plusieurs reprises et, étant plus molles que la chaussée, elles s'usent jusqu'à devenir tranchantes avec le temps. Sur mon longboard, le résultat ressemble à ceci :
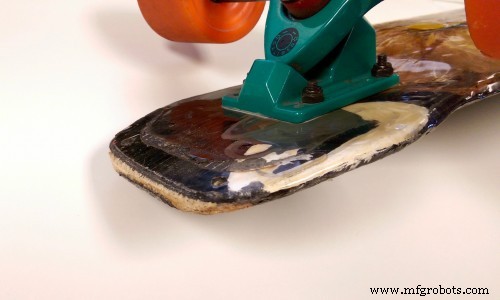
Ce que vous voyez à la fin, c'est le noyau en bois et les bords exposés en fibre de carbone. Cela s'est produit assez rapidement, alors je savais que j'avais besoin d'une couverture pour que les kick tails fonctionnent comme une plaque de protection. Des options commerciales sont disponibles mais elles sont épaisses, lourdes et incompatibles avec la forme de ma planche, donc je suis resté à l'écart de cette option. J'ai fabriqué de fines feuilles de Delrin à boulonner au fond, mais elles se sont rapidement usées et se sont cassées. Ce dont j'avais vraiment besoin, c'était de quelque chose de léger et résistant à l'abrasion qui pourrait s'enrouler les tails de ma planche, j'ai donc décidé d'utiliser le Mark Two pour imprimer en 3D des protections infusées de Kevlar, adaptées à mon longboard. Le flux de travail pour y arriver était étonnamment facile et pouvait être utilisé pour créer des housses personnalisées et durables pour tout, des bateaux aux EPI, alors j'ai pensé partager mon processus ici.
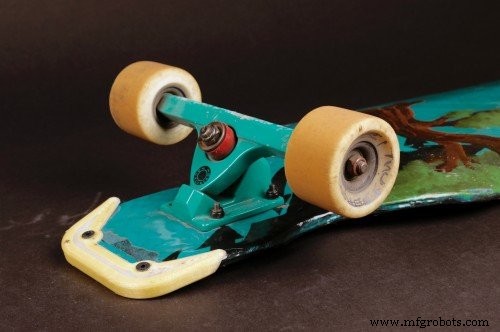
Étape 1 : tracer et photocopier un modèle Comme je n'avais pas de version numérisée de la forme de la queue de mon longboard, je l'ai tracé sur un morceau de papier d'imprimante et l'ai scanné afin d'avoir une copie propre sur mon ordinateur. Prendre une photo peut également fonctionner si l'objet est trop difficile à tracer, mais vous risquez une inexactitude dimensionnelle en raison du raccourcissement des objets si vous ne prenez pas la photo directement.
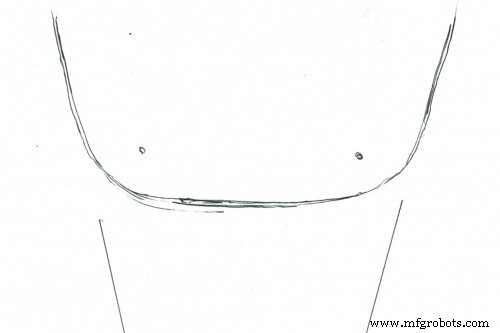
Étape 2 :Importer vers CAD et Trace Ouvrez le programme de CAO avec lequel vous êtes à l'aise (j'ai utilisé Fusion 360 dans ce cas) et importez l'image afin de pouvoir la tracer. Assurez-vous d'avoir une dimension sur le dessin que vous pouvez utiliser pour le mettre à l'échelle avec précision.
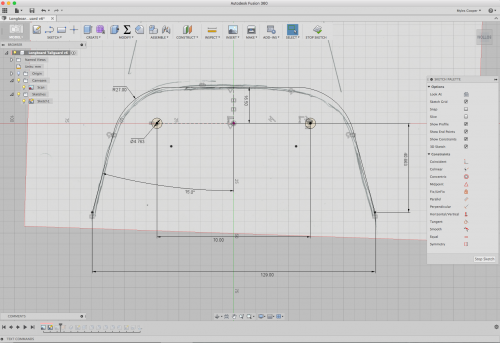
Étape 3 : Modélisez le reste De la manière qui vous convient, CAD votre couverture. Pour moi, cela signifiait créer une plaque inférieure adaptée à mes trous de boulons, puis extruder un mur pour envelopper les extrémités de la planche. Ce mur protégera la planche des chocs et des éraflures frontales avec le sol.
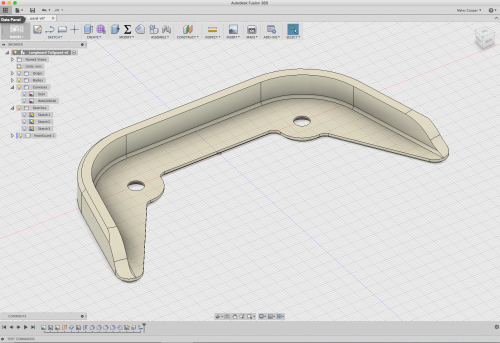
Étape 4 :Envoyer à l'imprimante Dans l'Eiger, j'ai mis du Kevlar supplémentaire dans les couches inférieures ainsi que du Kevlar dans les murs. Cela a donné aux couvertures une résistance à l'abrasion durable sur tous les côtés. En quelques minutes, les couvertures étaient prêtes à être imprimées.
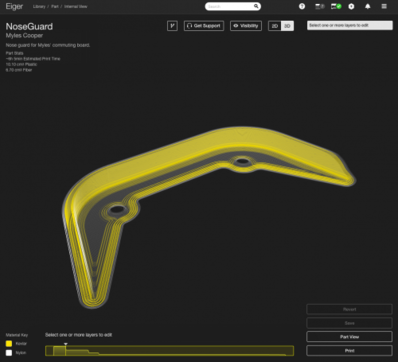
Étape 5 :Attachez-vous et partez Un imprimé, tout ce que j'avais à faire était d'enfoncer des inserts filetés dans le longboard pour lui permettre d'accepter quelques vis à métaux. J'ai boulonné les protections arrière et j'étais prêt à les essayer.
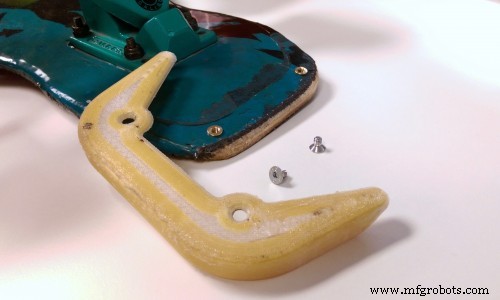
Résultats
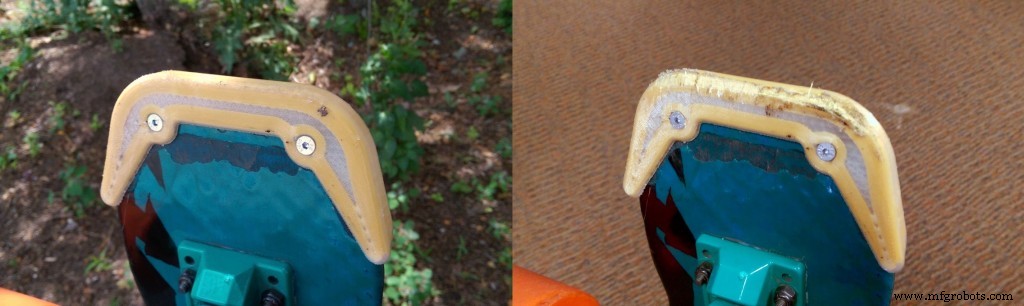
Pour la quantité d'abus que je leur ai fait subir, ces protège-queue ont très bien résisté. Pour leur donner un test sur le terrain approfondi, j'ai frappé les queues contre le sol d'un parking à proximité à plusieurs reprises pour simuler des semaines d'utilisation, mais le Kevlar a à peine montré des signes d'usure (vu à gauche). Finalement, j'ai eu recours à simplement faire glisser la queue contre le trottoir, et après quelques minutes, j'ai finalement commencé à couper les couvertures. Compte tenu de la résilience des protections de ce test, cela pourrait prendre des mois, voire des années de conduite normale pour user ces couvertures.
Le point de défaillance des gardes ne s'est produit que lorsque j'ai commencé à lancer la planche directement dans un trottoir de trottoir. Après quatre ou cinq collisions directes, j'ai réussi à fendre un petit virage et il a commencé à se décoller. Cependant, ces types de collisions frontales sont suffisamment rares pour que je ne m'inquiète pas que cela pose un problème lors d'une utilisation normale.
Alors voilà :un moyen facile d'obtenir une excellente résistance à l'abrasion dans une housse légère et personnalisée à l'aide du Mark Two. Maintenant, pour commencer à réfléchir à quoi d'autre ce flux de travail pourrait être utilisé…
Vous voulez ressentir vous-même la force de ces pièces ? Commandez un échantillon gratuit dès aujourd'hui sur notre site Web !
Vous voulez essayer ces fichiers par vous-même ? Vous pouvez télécharger le NoseGuard STL et le NoseGuard MFP maintenant.
impression en 3D