Spar arrière VBO hors autoclave, nervures thermoplastiques cible Wing of Tomorrow
Airbus (Toulouse, France) est au milieu d'un vaste effort pour travailler avec les fabricants d'aérocomposites sur le développement de structures hors autoclave (OOA) pour le programme Wing of Tomorrow (WOT) de l'entreprise. Ces structures seront livrées à Airbus en 2021 et seront assemblées dans une aile de démonstration qui sera testée et évaluée pour une utilisation potentielle dans un avion monocouloir de nouvelle génération. On ignore quand un tel programme pourrait être annoncé et fait l'objet de nombreuses spéculations, mais l'ensemble de la chaîne d'approvisionnement en aérocomposites se positionne pour faire partie de la prochaine génération de fabrication d'avions, que ce soit pour Airbus ou Boeing, ou les deux.
CW a déjà rendu compte d'une partie de cette activité WOT dans des articles sur le revêtement inférieur de l'aile produit par Spirit AeroSystems (Wichita, Kan., États-Unis) et les nervures thermoplastiques produites par GKN Aerospace (Hoogeveen, Pays-Bas). L'avionneur et fournisseur d'aérostructures Daher (Paris, France) se joint à l'effort WOT, qui a développé, fabriqué et livré un longeron arrière OOA et cinq nervures thermoplastiques pour le programme.
« Daher est fier de participer à ce programme WOT. Ce développement confirme la position de Daher comme l'un des leaders mondiaux des technologies thermoplastiques et des structures à fonctions intégrées thermodurcissables, ainsi qu'un partenaire fort pour les avionneurs et un Tier 1 pour les pièces complexes », déclare Dominique Bailly, VP R&D chez Daher.
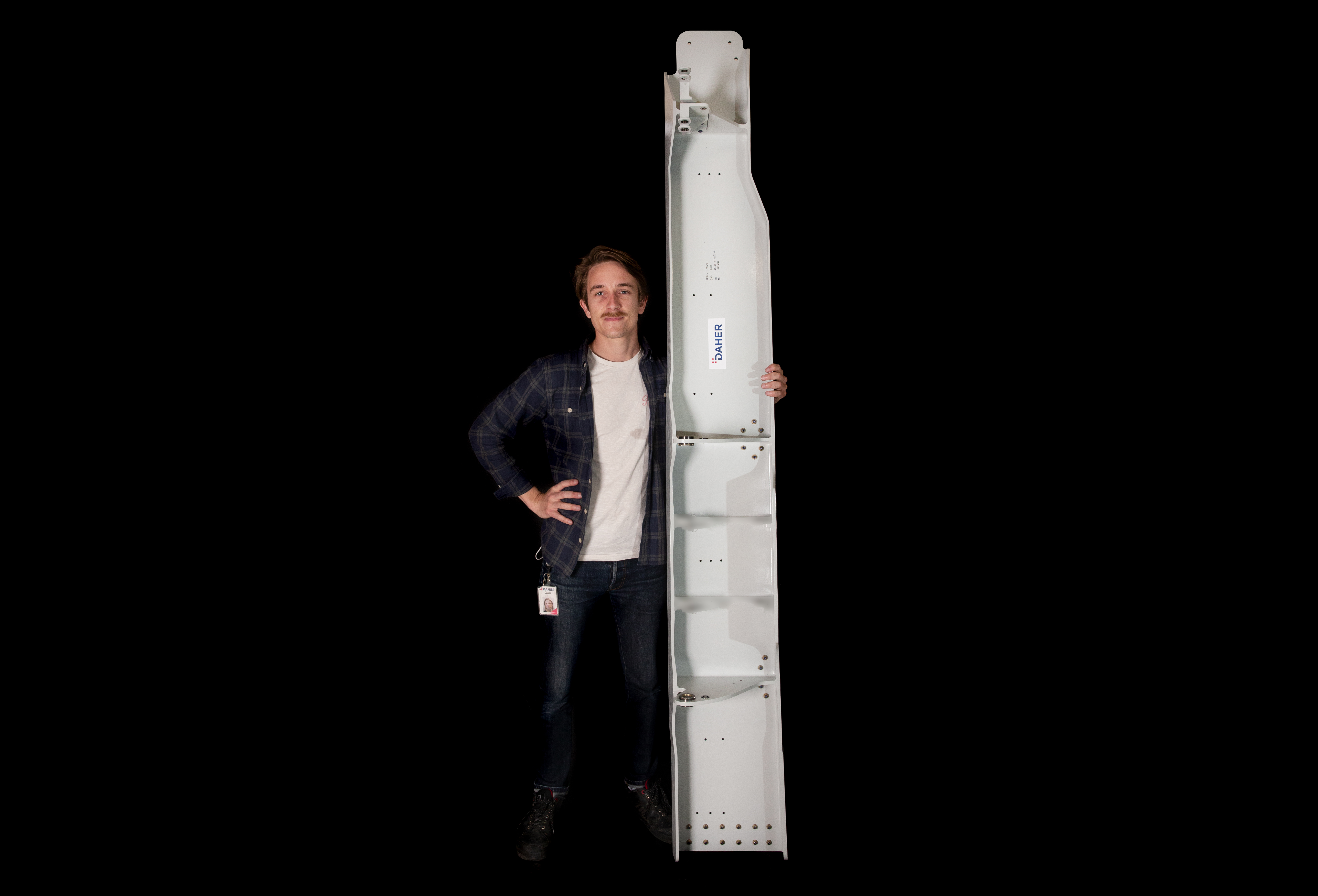
Spar haute performance
Le démonstrateur WOT, comme toute aile d'avion commercial, possède plusieurs structures de longeron. Le longeron arrière Daher développé pour WOT est à l'extérieur du réservoir et le deuxième le plus proche des deux longerons immédiatement adjacents au fuselage, situé juste au-dessus du train d'atterrissage. Il mesure plus de deux mètres de long et 10 millimètres d'épaisseur, et doit répondre à des exigences importantes de résistance et de rigidité - quelques tonnes appliquées sur les éléments et plusieurs dizaines de tonnes pour le cisaillement et la traction dans le sens de l'envergure ", explique Bailly - étant donné sa proximité avec le fuselage et au système de train d'atterrissage.
En outre, explique Alexandre Condé, ingénieur en chef chez Daher qui a travaillé sur le longeron, Airbus recherchait le développement d'un processus de fabrication hautement automatisé qui permettrait à l'entreprise de réduire le poids des avions et de répondre de manière rentable aux taux de production d'avions de 60 à 100 ensembles de navires. par mois. Daher a proposé une conception capable de remplacer 15 composants métalliques et attaches qui étaient d'origine pour la conception de base du longeron composite. "L'idée était d'intégrer le plus de fonctionnalités pour être rentable et économiser du poids", explique Condé.
La structure de longeron qui en a résulté est un sous-produit d'un longeron thermodurcissable à sac sous vide uniquement (VBO) développé par Daher en 2018 pour un avion d'affaires Dassault Aviation (Paris, France). Bailly dit que le longeron Dassault a été fabriqué avec du préimprégné à base de résine époxy Hexcel (Stamford, Connecticut, États-Unis) M56, durci OOA VBO. Par la suite, lorsque Daher s'est impliqué dans le programme Airbus WOT, la société a décidé d'adapter la conception, les processus et la justification du longeron Dassault et de l'appliquer à la nouvelle structure Airbus WOT, en sélectionnant l'époxy Hexcel M56 350°F cure OOA, préimprégné dans Tissu en fibre de carbone Hexcel AS4 et fibre de carbone IM7 UD.
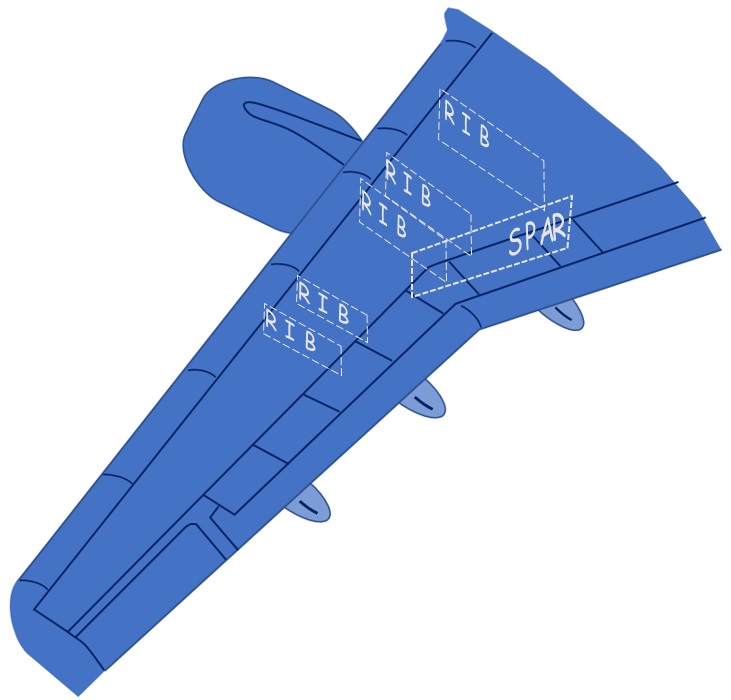
Le processus de fabrication utilisé pour fabriquer le longeron est le placement automatisé des fibres (AFP) à l'aide d'un système Coriolis Composites (Queven, France), qui applique le matériau sur un moule mâle. Le durcissement est effectué sous vide dans une étuve. La pièce résultante, dit Condé, a une porosité de 0,1%.
Condé dit que le préimprégné a été choisi par rapport au moulage de résine liquide pour la même raison que le préimprégné est devenu un incontournable de la fabrication aérospatiale au cours des 30 dernières années :il fournit un volume de résine/fibre cohérent et fiable qui permet la production de pièces ayant des dimensions cohérentes et fiables. et masse. « En utilisant cette nouvelle génération de résine OOA avec uniquement le vide, vous disposez d'une parfaite robustesse de la teneur en fibres dans l'épaisseur du composite après durcissement », explique Condé. "De plus, le poids de la pièce est très stable car vous ne poussez pas la résine à l'extérieur de la fibre."
Daher dit qu'il a été le premier partenaire à livrer, fin 2020, un composant WOT - un longeron à Airbus à Bristol, au Royaume-Uni - pour intégration dans le premier démonstrateur WOT; l'entreprise est en train d'en livrer deux autres. Au-delà de cette phase de démonstration, Daher réfléchit également à l'industrialisation de la fabrication des longerons et travaille sur une analyse de conception du système de fabrication (MSD) qui estime et simule les opérations, les installations, les équipements et les besoins en personnel pour la production à plein régime d'un monocouloir de nouvelle génération. avion.
Plusieurs côtes, plusieurs tailles
L'effort de Daher pour développer les côtes car le programme WOT a été plus complexe et exigeant. La société a conçu cinq nervures de différentes tailles et dimensions à l'intérieur de l'aile ; les autres nervures sont une combinaison de conceptions en aluminium et composites, y compris une nervure composite thermoplastique conçue par GKN Aerospace.
Dans un précédent projet avec Dassault Aviation, Daher avait démontré sa capacité à concevoir et fabriquer des nervures relativement petites à partir de composites thermoplastiques, explique Bailly. Avec WOT, l'entreprise a eu l'opportunité d'étendre ses compétences vers le développement de nervures plus grandes (environ 2 mètres de long), plus lourdes.
De plus, selon les objectifs WOT, Daher vise un niveau de maturité technologique (TRL) de 6 d'ici fin 2023. deux programmes [WOT et Dassault Aviation], nous aurons démontré que nous sommes capables de couvrir toute la portion de côte de l'aile - c'est l'idée », explique Bailly.
« Nous avons profité de ce programme pour examiner différentes manières de fabriquer des pièces et comparer les comportements mécaniques, et également pour examiner l'impact sur la fabrication. En parallèle, nous travaillons sur la simulation pour prédire le comportement des composants comme le retour élastique ou l'effet d'emboutissage. L'objectif est de réduire les essais au cours du développement, donc le coût non récurrent », précise Condé.
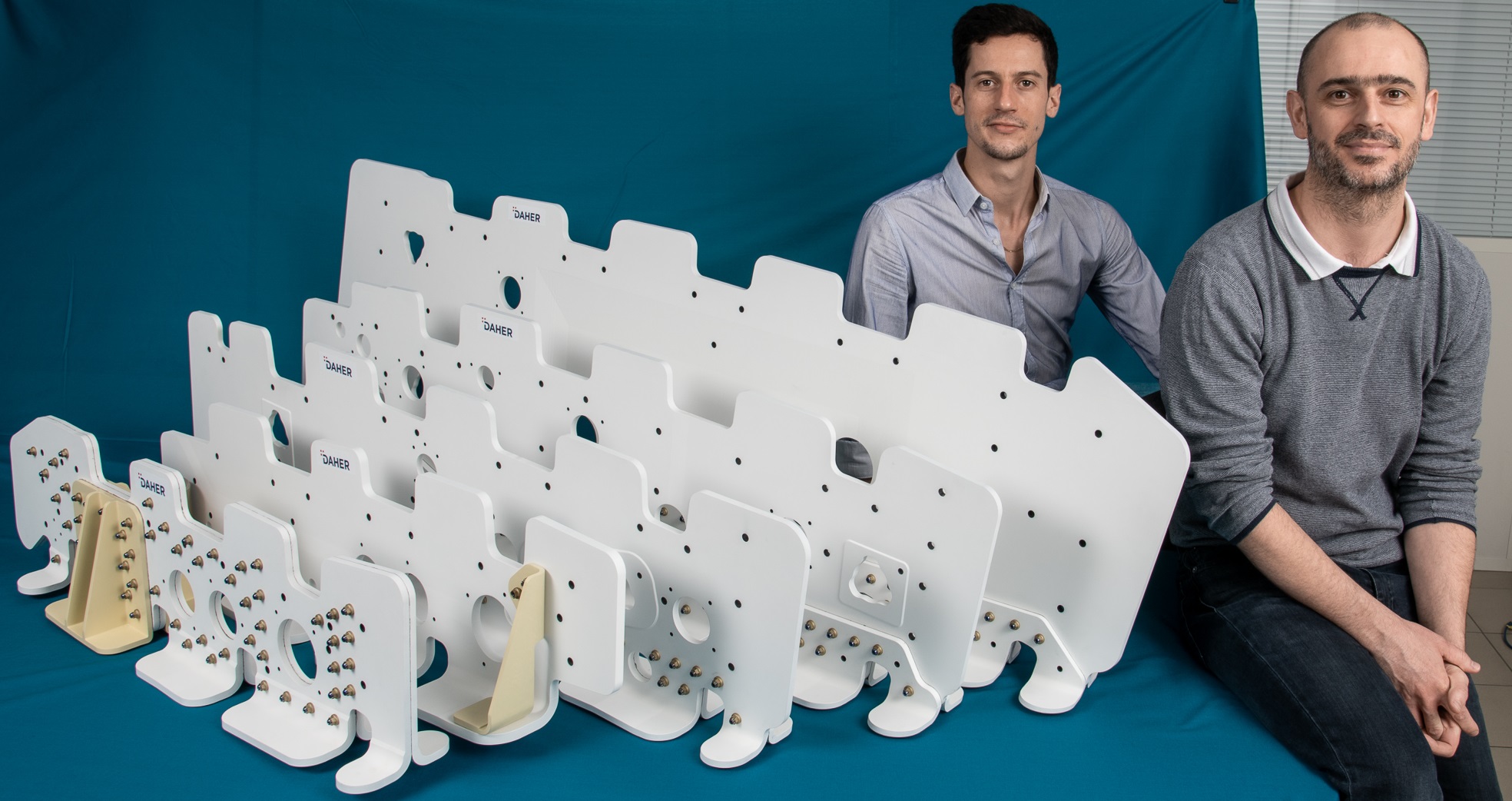
Comme pour le longeron, le développement a commencé au niveau du coupon, de l'élément et du détail, suivi de la fabrication de pièces à l'échelle inférieure avant que les pièces finales de taille normale ne soient construites. Des tests ont été effectués à chaque niveau, note Condé, y compris des tests spécifiques développés par Daher pour les caractéristiques des côtes.
Pour les cinq côtes, Daher a finalement décidé d'utiliser des rubans unidirectionnels (UD) en fibre de carbone/polyaryléthercétone à faible fusion (PAEK) fournis par Toray Advanced Composites (Morgan Hill, Californie, États-Unis) en utilisant une résine fabriquée par Victrex (Cleveleys, Lancashire, Royaume-Uni). ). Pour fabriquer les nervures, des flans plats sont fabriqués à l'aide de l'AFP suivi d'une consolidation au four - dans certains cas, les matériaux sont pré-consolidés avant le formage du tampon. Au besoin, des brides supplémentaires ou d'autres composants sont fixés mécaniquement sur les pièces formées par estampage.
Chaque nervure a été conçue en fonction de sa position le long de l'aile, des spécifications de taille et des exigences de charge (une tonne à 50 tonnes), chacune est donc unique à plusieurs égards. La plus grande côte mesure 2 mètres de long x 1 mètre de large. Quoi qu'il en soit, chacun commence par une âme plate, qui est estampée en forme de « L » pour créer une bride le long du bas de la partie où elle se connecte au revêtement de l'aile. Pour plus de stabilité, plusieurs des nervures comprenaient deux composants en forme de « L » fixés mécaniquement dos à dos pour former une forme de « T » avec des brides bidirectionnelles.
Les fonctionnalités spécialisées comprenaient un support (fabriqué à partir de composites thermodurcissables) pour la connexion avec le rail de rabat fixé à la nervure, et une série de trous ou de chutes de pli dans certaines nervures pour réduire le poids de la pièce.
« Tout au long de la conception, nous avons dû gérer la complexité par rapport au coût », explique Bailly. « Cela a toujours été dans notre esprit, faire quelque chose de simple mais rentable. » La simplicité était également essentielle du point de vue du taux de production, note Condé. "Si c'est trop complexe, ce ne sera pas compétitif du point de vue du client, aux tarifs très élevés qu'il souhaite avoir."
L'épaisseur relative de chacune des nervures, jusqu'à 12 millimètres pour la plus grande nervure, a été un défi qui a introduit de la complexité dans la conception. Les tissus plus épais ont tendance à se froisser ou à se former de manière incorrecte lors de la formation du tampon, et les pièces plus épaisses peuvent être difficiles à usiner dans la forme finale.
Pour l'usinage, Daher a utilisé un mélange de découpe au jet d'eau et d'usinage mécanique en fonction des besoins des pièces, à la fois pour atténuer les problèmes d'épaisseur des pièces et pour gérer la température. De plus, sur la nervure de 12 millimètres d'épaisseur, l'équipe a conçu une fenêtre de chute de couche au milieu du composant pour réduire le poids global de la pièce. En plus de résoudre ces problèmes potentiels, Condé note que la fenêtre de dépose de pli a également permis à Daher « d'essayer différents types de fonctionnalités de fabrication sur les pièces, afin d'améliorer notre compréhension du comportement des pièces. »
Le processus de formation du tampon s'est avéré un défi encore plus grand. « Nous avons dû imaginer une nouvelle façon d'emboutir pour atténuer le risque de plis », explique Bailly. Daher a finalement développé une méthode propriétaire pour résoudre le problème.
Étapes suivantes
Au-delà de WOT, Daher évalue des méthodes de fabrication alternatives pour la production de nervures thermoplastiques, tout en planifiant le développement d'une ligne de production complète pour une fabrication à cadence élevée à l'avenir.
Par exemple, alors que les démonstrateurs WOT utilisent des fixations, Bailly note que grâce à son acquisition en 2019 des composites thermoplastiques et du spécialiste du soudage par induction KVE Composites (La Haye, Pays-Bas), Daher possède la capacité des composants soudés à l'avenir. « Nous travaillons sur un autre projet distinct pour atteindre un niveau TRL plus élevé sur le soudage de pièces épaisses UD [pour une utilisation sur les avions monocouloirs de nouvelle génération] », dit-il.
Daher travaille également au développement d'une ligne de production complète pour produire à l'avenir des nervures thermoplastiques. "Nous améliorons vraiment le concept et réduisons le nombre de machines nécessaires pour toutes les tâches et réduisons les coûts de processus", déclare Bailly, l'objectif étant d'atteindre les objectifs de production d'avions à haut volume.
Résine
- Covestro intensifie ses investissements dans les composites thermoplastiques
- Lancement des mélanges maîtres thermoplastiques renforcés de graphène
- Solvay augmente la capacité des composites thermoplastiques
- Composites thermoplastiques chez Oribi Composites :CW Trending, épisode 4
- Kordsa étend sa gamme de préimprégnés thermoplastiques
- Composites thermoplastiques LANXESS utilisés dans la coque arrière de l'Audi A8
- Technologie de production de panneaux en nid d'abeille thermoplastique EconCore
- Composites thermoplastiques :vue panoramique
- Soudage de composites thermoplastiques