CSIRO :développement de fibres de carbone de meilleure qualité, plus résistantes et moins coûteuses
« Le travail du CSIRO est centré sur les premières étapes de la production de fibre de carbone, y compris la polymérisation de l'acrylonitrile en poly l'acrylonitrile, puis le filage et le traitement ultérieur du PAN pour produire une fibre précurseur de meilleure qualité et moins chère », explique Abbott. La production de PAN représente 50% du coût de la fibre de carbone mais 70-90% de ses propriétés. "La technologie de l'Université Deakin implique les dernières étapes de la production de fibre de carbone, y compris l'oxydation et la carbonisation", poursuit-il. "La technologie qu'ils ont concédée sous licence à LeMond Composites (Oak Ridge, Tennessee, États-Unis) est destinée à l'oxydation rapide visant à réduire le coût de ces étapes finales."
Pour atteindre ses objectifs en matière de fibre de carbone de nouvelle génération, le CSIRO utilise un ensemble d'outils stratégiques :la polymérisation RAFT, les procédés chimiques FLOW et la métrologie CarbonSpec. "Notre objectif est de produire une fibre de carbone de qualité aérospatiale avec une résistance supérieure de 20 %", a déclaré Abbott, notant que l'équipe espère obtenir les premiers résultats d'ici la fin de 2020.
Équipe fibre de carbone CSIRO
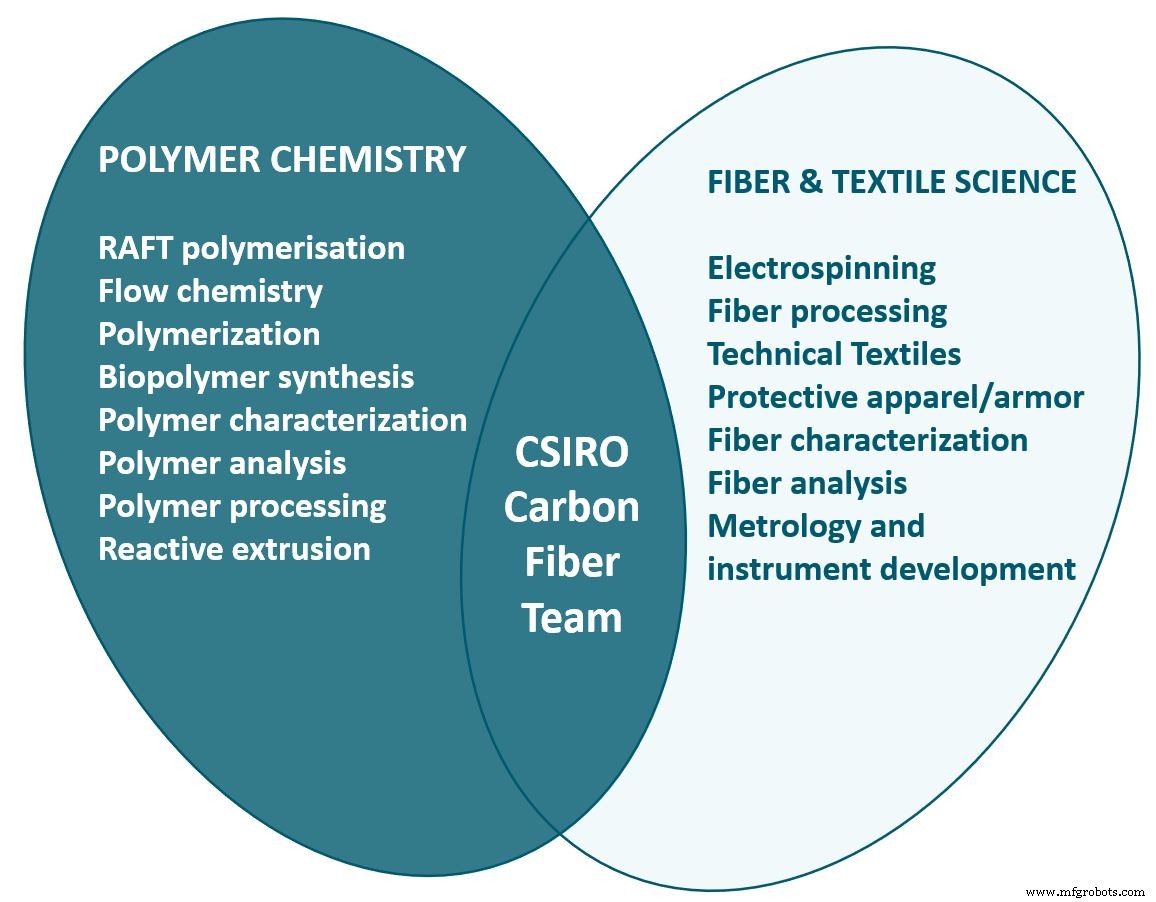
Avec 5 000 employés, 55 sites, huit unités commerciales et un budget d'environ 1 milliard de dollars, les projets du CSIRO couvrent un large éventail de sujets - par exemple, l'impression 3D, les biopolymères, les implants médicaux, les vêtements intelligents, l'astronomie/l'exploration spatiale - et impliquent plus de 2 800 partenaires chaque année. « Le CSIRO a inventé et breveté le réseau local sans fil », explique Abbott, « et utilise ces revenus pour financer d'autres recherches. »
L'un de ses 55 sites se trouve dans la Silicon Valley, en Californie. CSIRO US met en relation des chercheurs australiens avec des projets américains pour accélérer les avancées scientifiques dans des domaines tels que l'espace, l'agriculture, la conservation de l'eau, les incendies de forêt et les villes intelligentes. L'objectif est un partenariat d'innovation ouverte qui rassemble des compétences de recherche approfondies ainsi qu'une expérience avec un large éventail de problèmes du monde réel.
« Dans les composites, le CSIRO développe de nouvelles résines et techniques de traitement », poursuit-il. « Nous travaillons également beaucoup sur la modélisation des composites et des simulations de procédés ainsi que sur la mesure des propriétés des fibres de carbone. Par exemple, nous avons développé de nouveaux instruments pour mesurer le module transverse de la fibre de carbone, que nous avons ensuite saisis pour améliorer notre modélisation et nos simulations. »
« Le CSIRO entretient une relation stratégique de 30 ans avec Boeing », déclare Abbott. « Nous avons été nommés fournisseur technologique de l'année de Boeing en 2016 et 2017. » L'équipe de fibre de carbone du CSIRO collabore également avec l'Université du sud du Mississippi (Hattiesburg, Mississippi, États-Unis).
Ligne pilote de filage humide
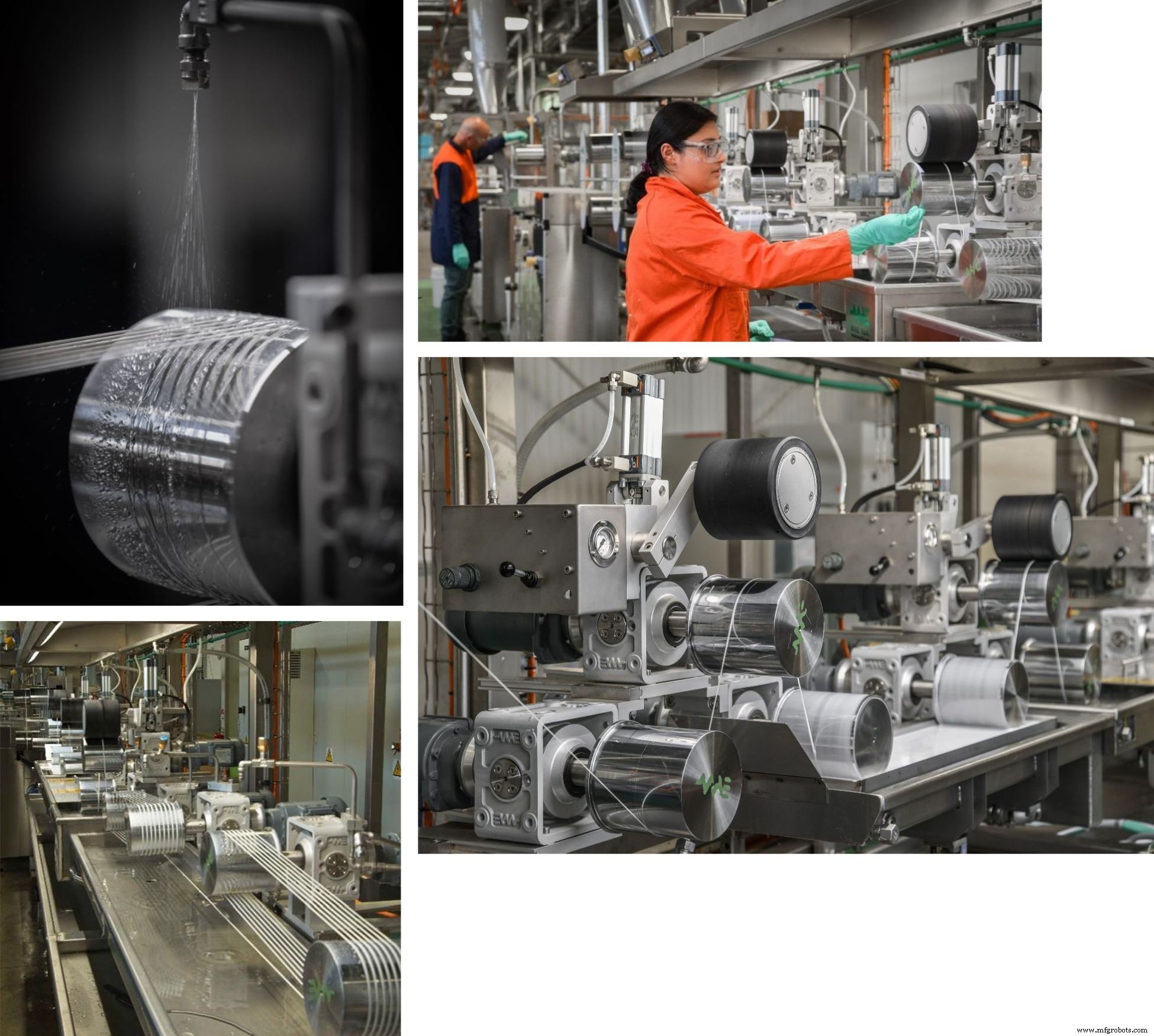
Afin de compléter les recherches nécessaires sur les précurseurs de la fibre de carbone, le CSIRO a d'abord dû établir sa propre ligne de filature humide. "La fibre de carbone n'est fabriquée que par une poignée de fabricants dans le monde, chacun d'eux détenant ses propres recettes secrètes et brevetées", a expliqué le directeur général du CSIRO, le Dr Larry Marshall, lors du lancement en 2017 de la nouvelle gamme. La ligne pilote a été construite sur mesure par MAE (Fiorenzuola d'Arda, Italie), un fabricant de machines spécialisé dans les équipements de traitement des polymères et des fibres. « Elle est conçue comme une ligne commerciale mais à plus petite échelle », explique Abbott.
Dans un blog du CSIRO, le fonctionnement de la ligne est décrit en utilisant l'analogie de la fabrication de pâtes. Semblable à la pâte utilisée pour faire des pâtes, une solution de polymère appelée dope est utilisée pour filer la fibre précurseur de PAN. Tout comme la pâte à pâtes est pétrie puis pressée dans une matrice pour faire de longs et minces brins de spaghetti, la dope est mélangée puis coagulée et filée à travers une filière à plusieurs trous pour produire 500 à 12 000 brins séparés de fibre PAN - tous plus fins que des cheveux humains . Ces fibres sont lavées, étirées sur rouleaux, stabilisées dans une série de solutions, étuvées et séchées avant d'être enroulées pour la ligne de carbonisation chez Carbon Nexus.
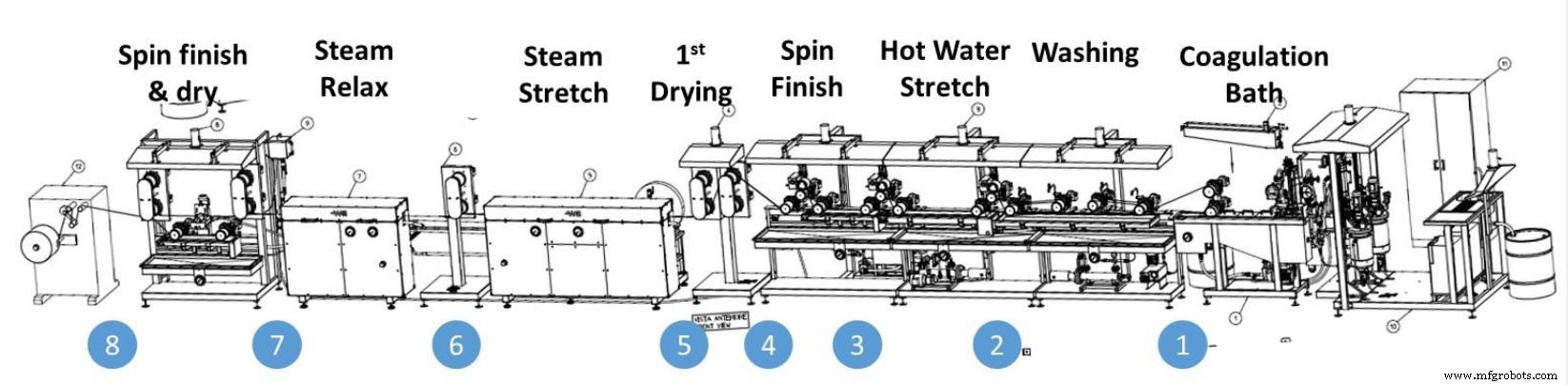
« Il nous a fallu beaucoup de temps pour bien comprendre comment fabriquer de la fibre de carbone et la matière première précurseur », déclare Abbott. « Personne ne voulait vraiment nous aider, nous avons donc dû apprendre principalement par nous-mêmes. Maintenant, cependant, nous avons un contrôle total sur le processus précurseur, qui est la clé, et nous travaillons ensuite avec Carbon Nexus pour la carbonisation. »
Polymérisation RAFT
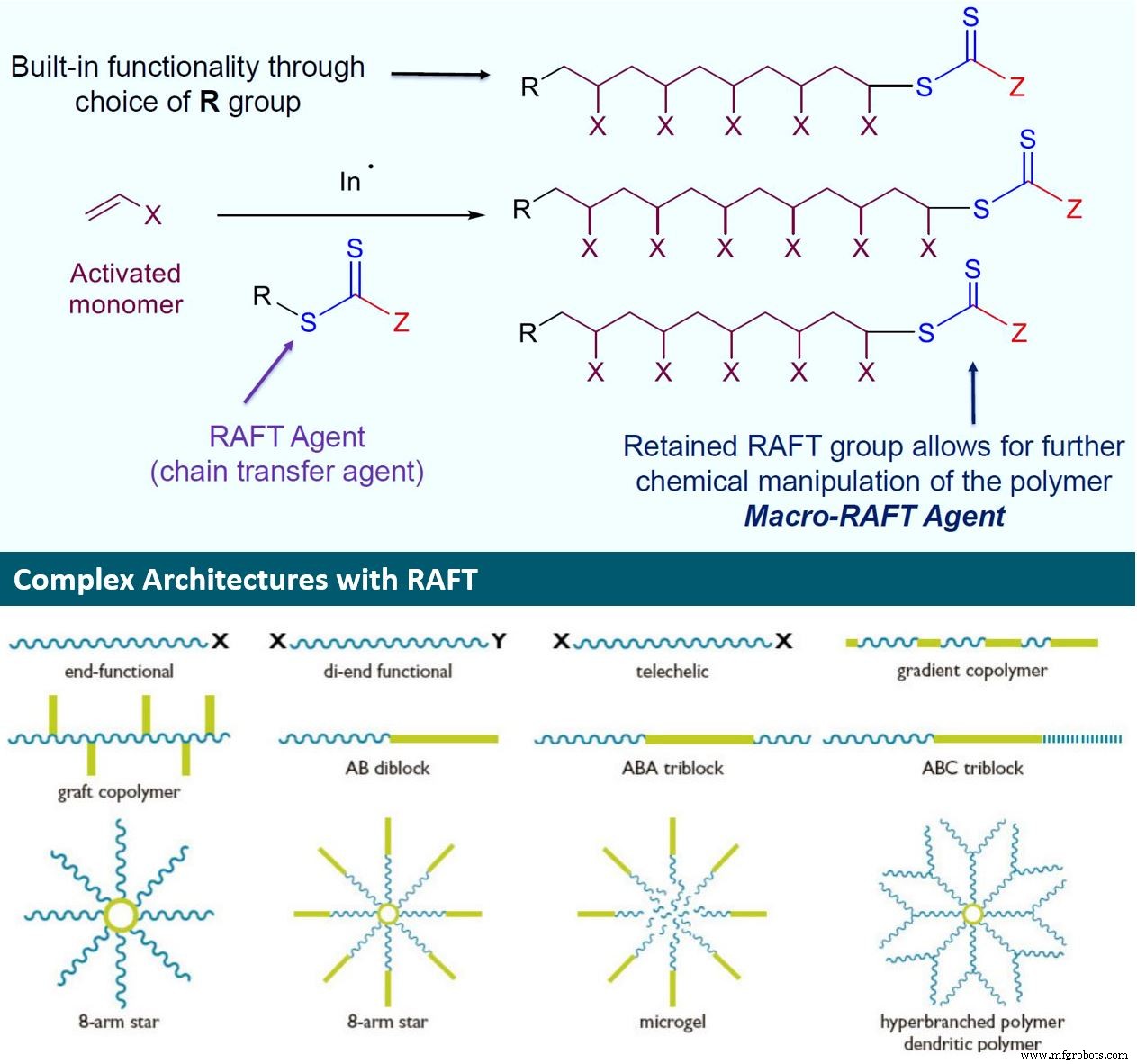
Un autre outil que CSIRO applique est sa technologie brevetée et commercialisée RAFT (Reversible Addition-Fragmentation chain Transfer). RAFT est une forme sophistiquée de polymérisation radicalaire contrôlée qui permet la synthèse de polymères sur mesure avec un contrôle sans précédent sur la composition et l'architecture. Bien que les applications de RAFT s'étendent des nouveaux systèmes d'administration de médicaments aux lubrifiants et revêtements industriels, l'équipe de fibre de carbone du CSIRO l'utilise pour exercer un contrôle sur le processus de polymérisation du PAN.
"La polymérisation conventionnelle du monomère au polymère produit une large polydispersité - en d'autres termes, beaucoup de longueurs différentes pour les chaînes polymères", explique Melissa Skidmore, chef d'équipe CSIRO, chimie des polymères. « Si nous ajoutons un agent RAFT, cependant, nous obtenons maintenant des chaînes polymères de presque la même longueur, et donc une distribution de poids moléculaire beaucoup plus étroite. Nous utilisons toujours les mêmes initiateurs, monomères et solvants, mais en ajoutant simplement du RAFT. »
"Le poids moléculaire affecte la viscosité de la solution de filage", explique Skidmore. « Traditionnellement, un poids moléculaire plus élevé dans les solutions de dopage a conduit à des surfaces rainurées sur les fibres précurseurs. L'ajout de RAFT diminue la viscosité des solutions de dopage, ce qui entraîne une charge en solides plus élevée. L'élimination du polymère de poids moléculaire très élevé du polymère peut entraîner un meilleur alignement moléculaire dans la fibre et des propriétés améliorées. Elle ajoute que le faible poids moléculaire a un effet plastifiant sur les fibres. « RAFT produit des polymères PAN qui pourraient produire des fibres précurseurs plus denses et plus uniformes avec moins de défauts structurels. Cela pourrait également aider à accélérer la carbonisation et à réduire les coûts. »
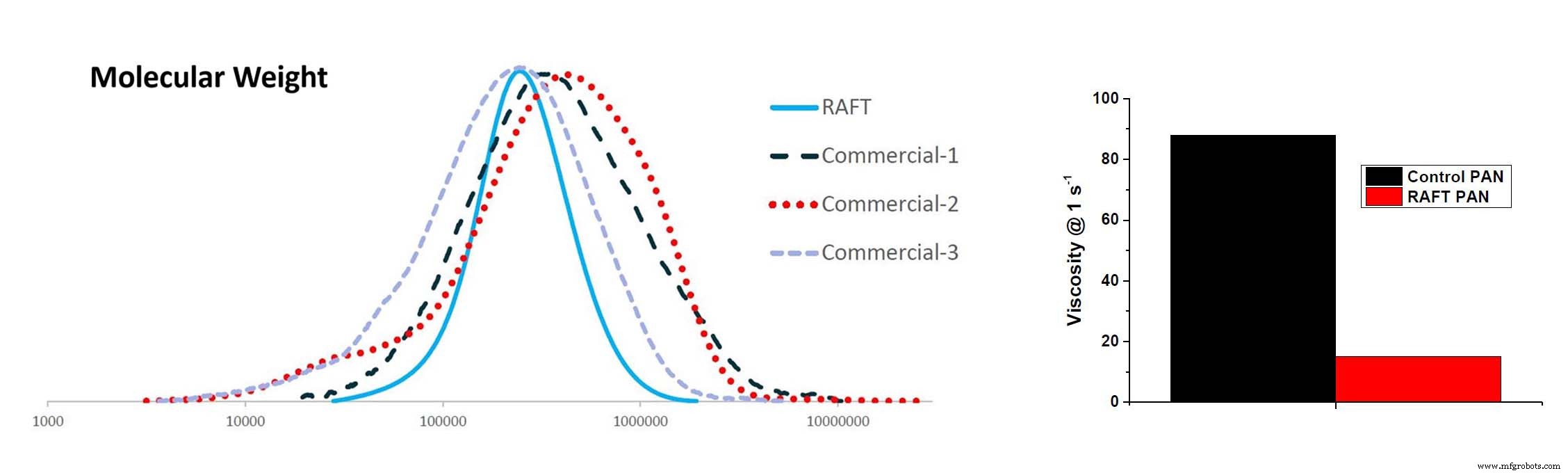
« Cela nous donne également accès à des architectures polymères complexes », note Skidmore. « RAFT permet une manipulation chimique supplémentaire du groupe polymère. » Un exemple d'endroit où cela est utile est lorsque la solution de dope est manipulée pour se coaguler en fibres. « Il existe un équilibre délicat entre les caractéristiques idéales de la solution de dope polymère et les conditions de coagulation », ajoute-t-elle. « Le polymère est composé à 95 % de PAN et à 5 % d'additifs. Étant donné que les polymères RAFT se comportent différemment, nous pensons pouvoir réduire certains des additifs traditionnels et convertir un pourcentage plus élevé en fibres à haute teneur en solides, ce qui entraîne moins de défauts. Nous testons cela maintenant. »
Bien que n'étant pas actuellement l'objectif principal, RAFT est également extrêmement intéressant pour sa capacité à ajouter des fonctionnalités lors de la polymérisation. Par exemple, les chercheurs ont cherché à fabriquer des composites avec une capacité d'adsorption élevée pour la capture du CO2 (c'est-à-dire que le CO2 adhérerait aux surfaces moléculaires du composite). Les composites multifonctionnels sont déjà recherchés par les constructeurs d'avions et de véhicules électriques. De nouveaux types de fibres de PAN et de carbone avec des fonctionnalités supplémentaires pourraient devenir une solution importante pour les futurs composites.
Processus de FLUX continu
«Avec RAFT, nous gagnons le contrôle de la polymérisation», explique Abbott. "Avec FLOW, nous avons plus de contrôle sur la formation des fibres."
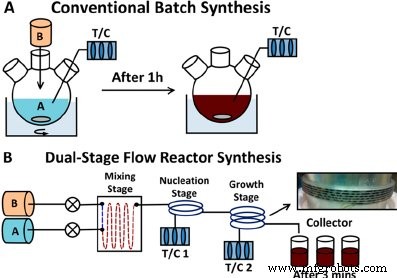
FLOW convertit la polymérisation en un processus continu plutôt qu'en batch. Abbott et Skidmore expliquent que les réacteurs discontinus utilisés actuellement sont bien établis, faciles à installer et efficaces pour mélanger et surveiller la cinétique de la réaction, mais qu'ils nécessitent également un volume plus important que les réacteurs à processus continu, ce qui signifie que l'installation à l'échelle industrielle est coûteuse. Ces réacteurs discontinus de plus grand volume sont également inefficaces en termes de consommation d'espace et d'énergie. Les réacteurs de traitement continu sont plus petits et moins chers, faciles à mettre à l'échelle, plus économes en énergie et offrent un contrôle de processus supérieur et une meilleure reproductibilité par rapport au traitement par lots. Cependant, étant donné qu'il s'agit d'une ligne continue dédiée, ils sont moins flexibles pour basculer entre différents paramètres et produits.
Il y a aussi des avantages en matière de sécurité et de durabilité. « À l'heure actuelle, la production de PAN n'est pas durable sur le plan environnemental, en particulier en ce qui concerne la toxicité », déclare Skidmore. « La continuité du processus de polymérisation améliore la sécurité, car les agents réactifs toxiques, odorants et inflammables sont isolés et traités par des équipements automatisés. Cependant, cela augmentera la complexité des lignes, qui nécessitent un degré plus élevé de surveillance et de contrôle. » Bien qu'elle nécessite un développement supplémentaire, Abbott considère la polymérisation FLOW comme un élément positif :« La fibre de carbone est intrinsèquement variable, donc tout ce que vous pouvez faire pour réduire cette variabilité améliore les propriétés. »
CarbonSpec – mesurer à gérer
Le dernier outil de l'approche fibre de carbone du CSIRO est CarbonSpec. « C'est essentiellement de la métrologie que nous avons développée pour tester les fibres que nous produisons et mieux comprendre la relation propriété-matériau », explique Pierlot. « Si vous ne pouvez pas le mesurer, vous ne pouvez pas l’améliorer. Nous sommes également mieux en mesure de prédire les propriétés de la fibre de carbone à partir d'un minimum de mesures de PAN et de fibre de carbone. »
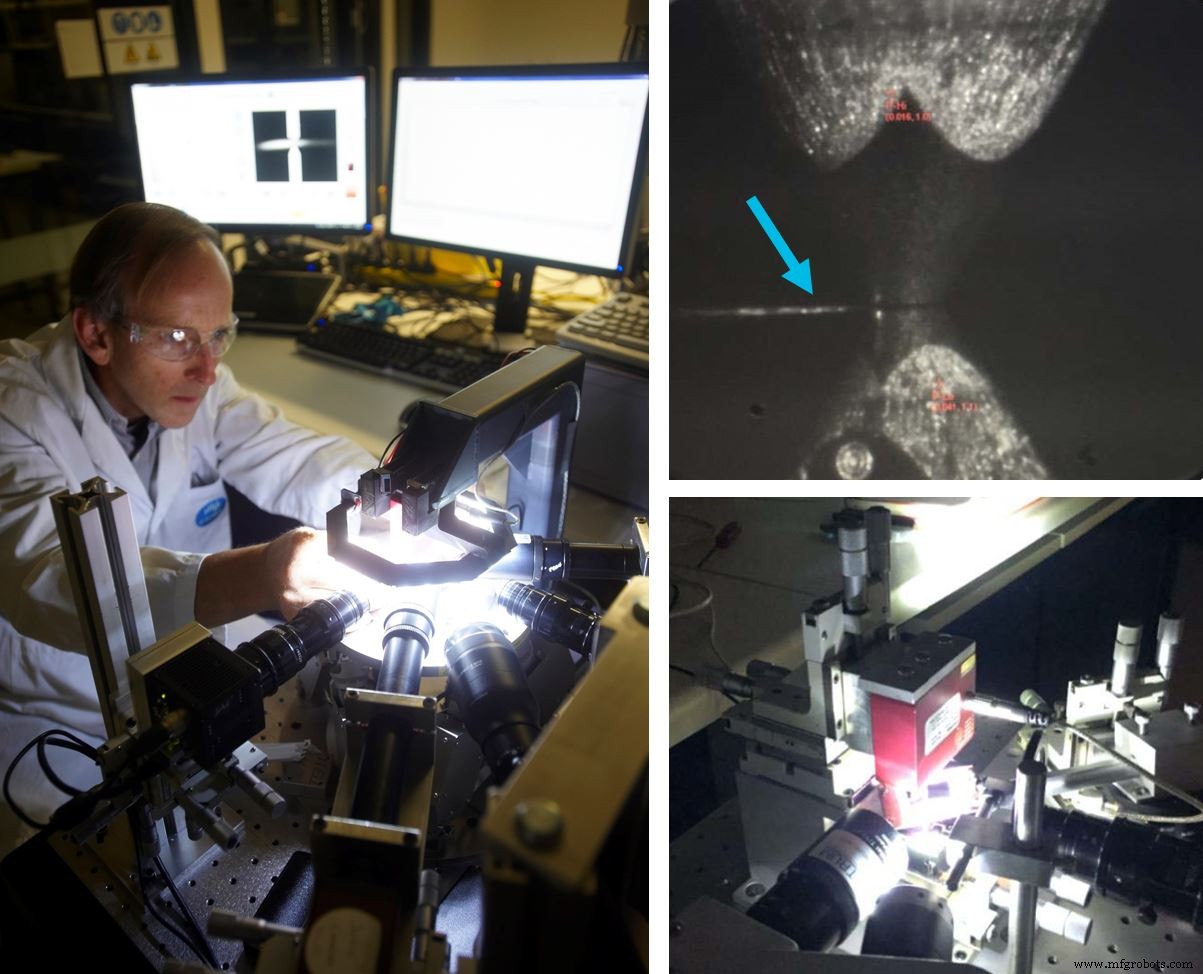
"Dans l'industrie de la fibre de carbone, il est standard d'utiliser des rayons X synchrotron calculés
tomographie (CT) pour déterminer la microstructure de vos fibres », explique Pierlot. (Un synchrotron est un accélérateur de particules de la taille d'un terrain de football qui génère des rayons X très brillants qui sont dirigés vers une ligne de lumière adjacente pour l'imagerie, etc.) « Avec l'aide du personnel de la ligne de lumière du synchrotron australien, un nouveau protocole de caractérisation dédié a a été développé pour scanner la microstructure de précurseurs de PAN individuels et de fibres de carbone. Une carte de la microstructure de fibres individuelles aussi petites que 5 microns de diamètre est réalisée en quelques minutes. Le signal SAXS aide à comprendre le développement des pores dans les fibres tandis que le signal WAXS aide à identifier les paramètres critiques de la microstructure pour optimiser le module des fibres. En utilisant les deux signaux simultanément, nous pouvons surveiller et optimiser la résistance mécanique et la rigidité tout au long de chaque phase du processus de production, du dope PAN à la fibre de carbone. »
Pierlot note qu'au sein de CarbonSpec, l'équipe développe également de nouveaux instruments et méthodes de test. « Par exemple, nous mesurons le module transversal et la résistance en plus des propriétés axiales normalement rapportées des fibres. Nous pensons pouvoir utiliser la nouvelle méthode que nous avons développée pour cela afin de mesurer également la résistance à la compression axiale. Ce dernier a longtemps été un défi car le diamètre d'une seule fibre de carbone ou PAN est très petit (5 à 10 µm), ce qui rend difficile l'application d'une véritable contrainte de compression axiale sans provoquer de flambage.
Augmentation de 20 % de la résistance, fibres de carbone de nouvelle génération
« Nous avons amélioré notre compréhension de la façon de convertir le polymère en fibre et nous fabriquons maintenant des fibres commerciales », déclare Abbott. « Nous appliquons ces outils technologiques à d'autres polymères précurseurs pour fabriquer SIROPAN, qui est la version CSIRO de PAN utilisant RAFT. Nous pouvons produire des kilogrammes de cette fibre maintenant. »
« La prochaine étape consiste à évaluer les avantages de l'utilisation des polymères RAFT », poursuit-il. "Nous produisons toujours du PAN, mais nous contrôlons mieux le poids moléculaire et l'augmentons tout en abaissant la viscosité, ce qui peut produire une fibre de carbone plus résistante." Combien plus fort ? « Nous ne sommes pas encore sûrs, mais notre objectif est 20 % plus élevé », déclare Abbott. « Nous savons qu'une amélioration de 10 % n'est pas suffisante pour rendre financièrement possible le changement de précurseur - 20 % est le minimum nécessaire selon l'industrie. »
- Développer de nouveaux polymères précurseurs via RAFT (polymères de haute qualité ou propriétés différentes)
- Développer des procédés polymères commercialement compétitifs (FLOW)
- Comprendre la conversion du polymère en fibre (filage au mouillé) pour un coût inférieur et des propriétés plus élevées
- Comprendre l'influence des propriétés des précurseurs sur les propriétés de la fibre de carbone, mieux prévoir les propriétés de la fibre de carbone et optimiser le processus en fonction de ces mesures et prédictions (CarbonSpec)
- Produire des fibres de carbone sur mesure pour des applications finales spécifiques en concevant le PAN et la fibre carbonisée
« L'industrie de la fibre de carbone croît de 10 % chaque année », déclare Abbott. "Nous aimerions nous associer à des acteurs de l'industrie bien établis et/ou nouveaux qui souhaitent améliorer la qualité, les performances, les coûts et la durabilité de la fibre de carbone."
« Nous testons six formulations de précurseurs différentes et les carboniserons à Carbon Nexus », ajoute Skidmore. « Nous espérons avoir des résultats d'ici la fin de l'année. Il faut un certain temps pour passer du polymère RAFT à une fibre blanche, puis à travers la carbonisation. »
Abbott ajoute :"Nous voulons des résultats solides d'ici la fin de l'année, mais nous sommes là pour le long terme."
Cette recherche est financée par le Fonds de dotation pour la science et l'industrie.
fibre
- Fibre de carbone
- 5 produits surprenants en fibre de carbone
- La fibre de carbone peut-elle être recyclée ?
- Avantages des chaussures en fibre de carbone
- Utilisations innovantes de la fibre de carbone
- La fibre de carbone dans les applications aérospatiales
- La fibre de carbone dans les applications automobiles
- Comment est fabriquée la fibre de carbone ?
- La fibre de carbone protège contre les pirates