Dépôt physique en phase vapeur (PVD)
L'application de revêtements sur les matériaux est l'une des stratégies les plus utilisées dans l'industrie pour améliorer leurs propriétés. Par dépôt de revêtements , un large éventail de caractéristiques d'un matériau peut être amélioré, d'un point de vue tribologique à un point de vue esthétique.
Dans le blog d'aujourd'hui, nous présentons une technologie qui a un grand potentiel dans l'application de revêtements. Cette technologie est le dépôt physique en phase vapeur (PVD) .
Qu'est-ce que le dépôt physique en phase vapeur ou PVD ?
L'origine dudépôt physique en phase vapeur (PVD) naît de la combinaison de l'électricité, du magnétisme et de la connaissance de la chimie à l'état gazeux.
Le concept de dépôt physique en phase vapeur est apparu lorsque les revêtements appliqués dans une atmosphère sous vide étaient à la hausse. Au cours de ces années, différents développements dans des technologies telles que la pulvérisation cathodique ou le plasma ont été réalisés, impliquant des réactions chimiques à l'état de vapeur, des évaporations thermiques et le contrôle des sources d'énergie.
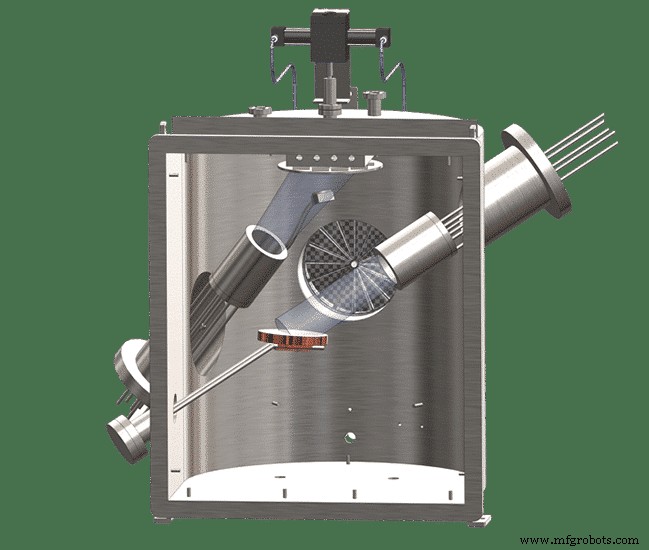
La technique PVD est un processus dans lequel un dépôt de couche mince se produit sur la surface d'un matériau, croissant atome par atome sur le substrat . Le dépôt physique de vapeur consiste en un processus de collision physique-thermique qui transforme le matériau à déposer, appelé la cible, en particules atomiques, qui sont dirigées vers les substrats à l'état de plasma gazeux à travers une atmosphère sous vide, générant un revêtement physique par condensation des atomes projetés.
Les revêtements déposés par PVD ont tendance à avoir de fines épaisseurs, qui peuvent aller de couches atomiques (moins de 10 angströms (Å) à 0,1 nanomètre (nm)) à des revêtements de plusieurs microns (épaisseur d'une fibre capillaire).
Quelles sont les technologies PVD les plus utilisées ?
Malgré le fait que le processus d'évaporation et d'ionisation de la cible, qui constituera finalement le revêtement sur le substrat, sera toujours de nature physique (d'où le nom de dépôt physique en phase vapeur), il existe différentes technologies qui utilisent le PVD pour le application. de revêtements.
Les technologies PVD les plus importantes et les plus utilisées sont :
-
Dépôt cathodique ou pulvérisation
Dans ce type de technologie PVD, l'accélération des ions au moyen de plasma permet l'impact de ceux-ci avec la surface de l'objectif pour en produire le dégagement de particules. Les ions transfèrent leur énergie cinétique à la surface de la cible et se vaporisent. Ce type de PVD se caractérise en permettant le dépôt de composés qui apparaissent lorsque la cible réagit avec le gaz présent dans le plasma. L'exemple le plus caractéristique est le dépôt de nitrure de titane (TiN), dans lequel le gaz présent est de l'azote et la cible est du titane, les deux réagissant pour donner naissance à un revêtement de TiN.
-
Évaporation thermique
Ce type de méthodologie PVD se caractérise par le fait que la cible s'évapore par un processus de chauffage sous vide et forme un flux de vapeur qui frappe le substrat dans la chambre de traitement, entraînant l'adhérence du revêtement. Dans ce processus, l'atmosphère sous vide joue un rôle particulier car elle empêche la contamination du revêtement formé.
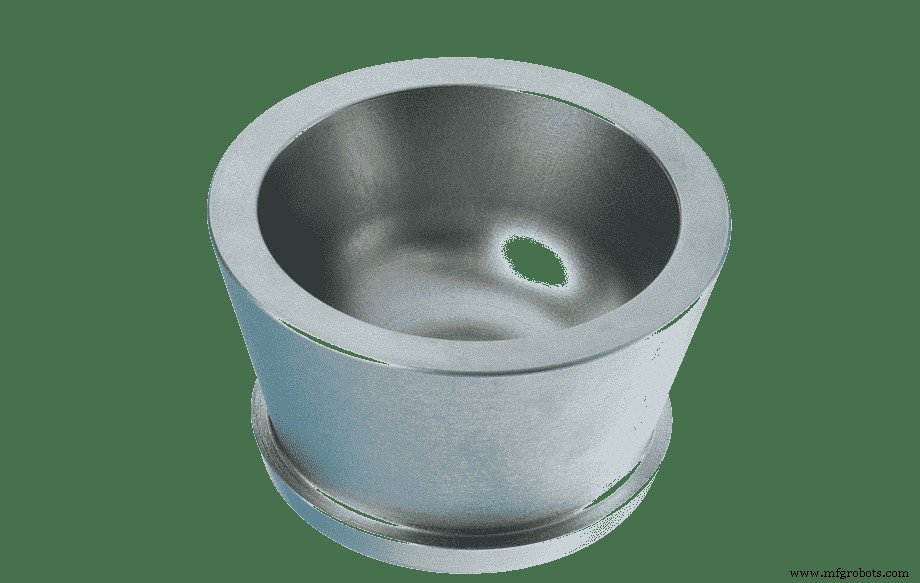
-
Dépôt d'arc
Dans cette technologie PVD, un arc de courant électrique de haute intensité et basse tension est appliqué, élevant la température jusqu'à ce que les particules de l'objectif se subliment, s'évaporant hautement ionisées dans la chambre à vide. Les particules ionisées sont dirigées vers le substrat en appliquant un potentiel. Dans le dépôt à l'arc, la cible peut jouer le rôle de cathode (arc cathodique) ou d'anode (arc anodique), selon sa nature et le revêtement à obtenir. Comme le dépôt par pulvérisation, les revêtements avec certaines compositions peuvent être obtenus en faisant réagir les ions cibles avec un gaz réactif.
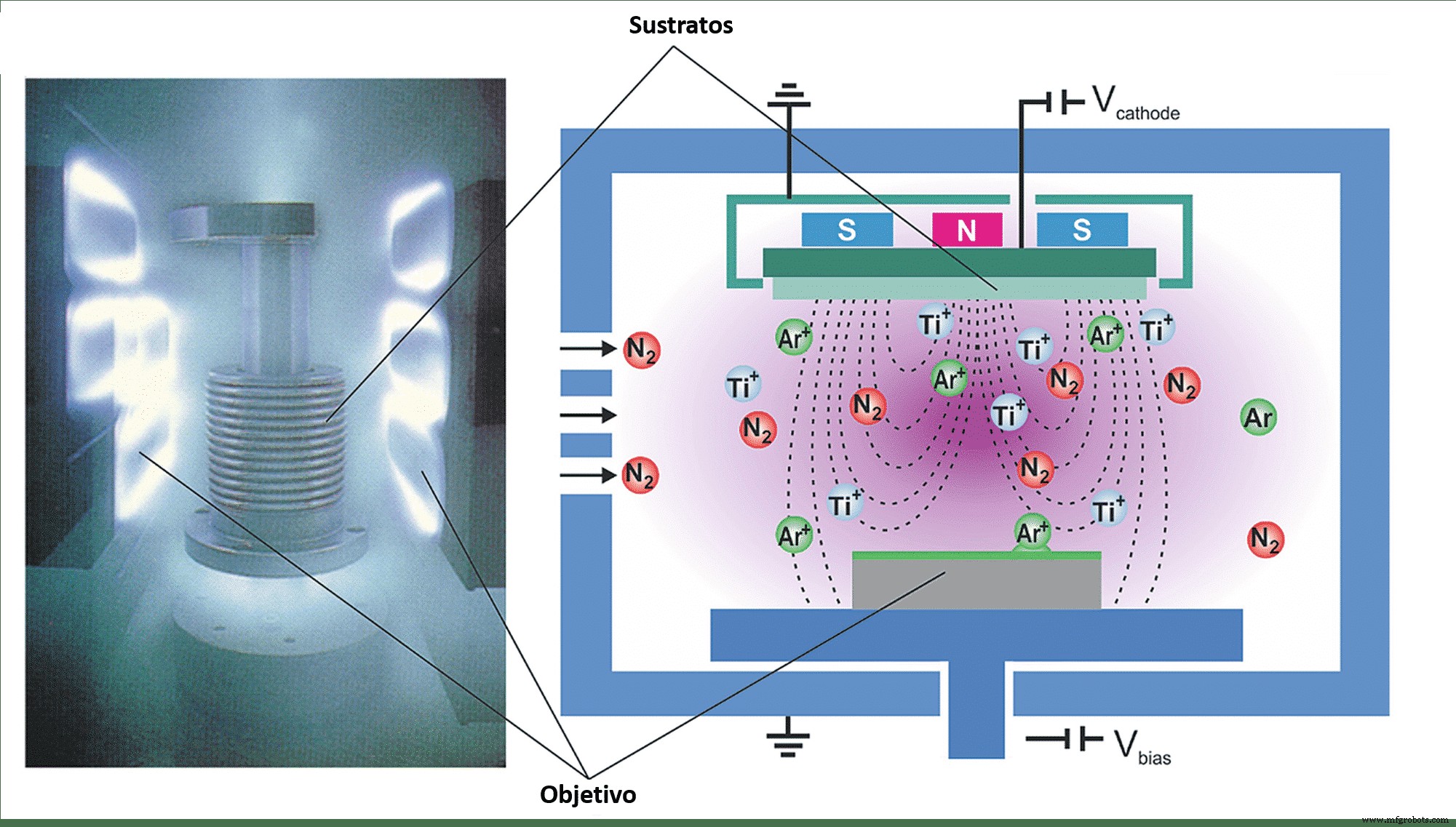
-
Dépôt d'ions (e-beam)
Dans cette technique PVD, l'évaporation de la cible se produit avec les mêmes processus que ceux vus précédemment (pulvérisation, évaporation thermique ou arc électrique). La différence réside dans l'utilisation d'un bombardement d'ions inertes à haute énergie (couramment Argon) pour contrôler et modifier le revêtement obtenu sur le substrat. La principale caractéristique de cette technique est qu'elle permet d'obtenir des revêtements métalliques purs sans contamination atomique.
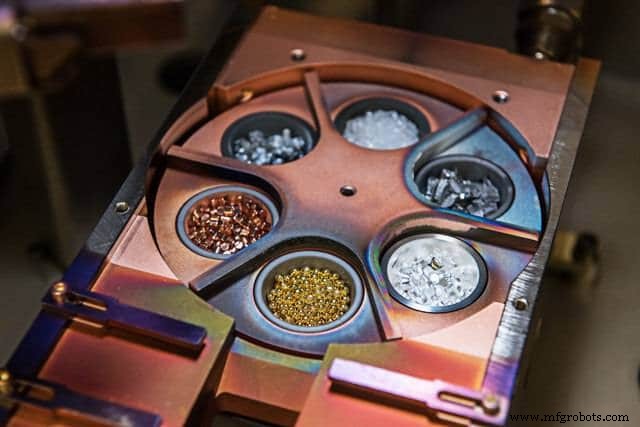
Avantages et inconvénients du PVD
Nous disposons aujourd'hui d'un large éventail de techniques de dépôt de revêtements. Chacun d'eux a des applications spécifiques, avec leurs avantages et leurs inconvénients.
Ensuite, nous présentons les principaux avantages de dépôt physique en phase vapeur.
- Il ne nécessite pas l'utilisation de réactifs chimiques ou de post-traitements de nettoyage, il a donc un impact environnemental très faible.
- Le PVD peut être appliqué à tout type de matériau inorganique.
- Les revêtements obtenus par PVD ont une grande adhérence, résistance et durabilité.
- La technique PVD permet un grand contrôle de la composition et de l'épaisseur des revêtements.
Les principaux inconvénients de PVD sont :
- Le procédé PVD utilise des équipements complexes, avec un coût très élevé
- La vitesse de production des revêtements PVD est lente par rapport aux autres procédés de dépôt de revêtement.
- La technique PVD est limitée dans les substrats aux géométries complexes
Applications PVD
Comme nous avons présenté le PVD au début de ce blog, il convient de souligner la précision et la pureté offertes par le dépôt physique en phase vapeur pour obtenir des revêtements. Les principales applications PVD actuellement utilisées sont les suivantes :
- Revêtements métalliques pour fournir des semi-conducteurs propriétés à un substrat qui ne le sont pas initialement.
- Magnétique pelliculage.
- Revêtements pour décoratif fins, largement utilisé dans le domaine de la joaillerie.
- Revêtements pour verres ou miroirs solaires, qui agissent comme optiques barrières d'interférence ou réfléchissantes barrières.
- Couches conductrices de palladium ou de carbone, pour les échantillons de microscopie électronique.
- Revêtements à haute dureté de matériaux composites,résistants à l'usure et corrosion , largement utilisé pour l'amélioration des outils mécaniques.
Projets réalisés avec la technologie PVD par ATRIA
Ci-dessous, nous allons vous montrer quelques-uns des projets réalisés par l'équipe ATRIA où les revêtements obtenus ont été utilisés par PVD :
- Développement de couleurs dorées à l'aide de la technologie de dépôt physique en phase vapeur . Dans ce projet, l'objectif était d'obtenir différentes nuances de couleur dorée sur des substrats métalliques. Pour ce faire, l'optimisation du procédé PVD de différentes cibles métalliques et gaz réactifs a été réalisée. Comme on peut le voir sur la photo, il a été obtenu d'un or intense à un or plus clair avec des tons roses.
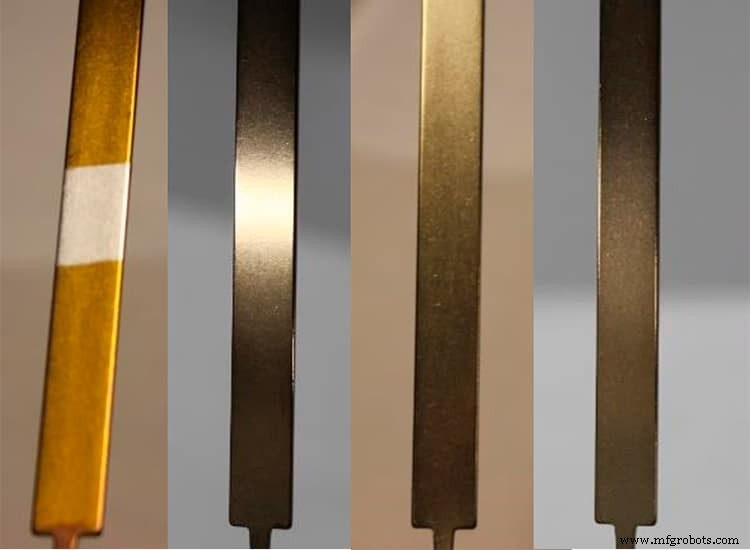
- Développement de films métalliques comme barrières contre la corrosion . Dans ce projet, notre corrosion s'est produite sur un substrat métallique recouvert de différentes couches métalliques lorsqu'il était exposé à certaines conditions environnementales. La solution proposée par ATRIA a été le développement d'un revêtement métallique inerte dans ces conditions environnementales et déposé par PVD. Le but dudit revêtement est de fournir une grande résistance à l'usure et à la corrosion
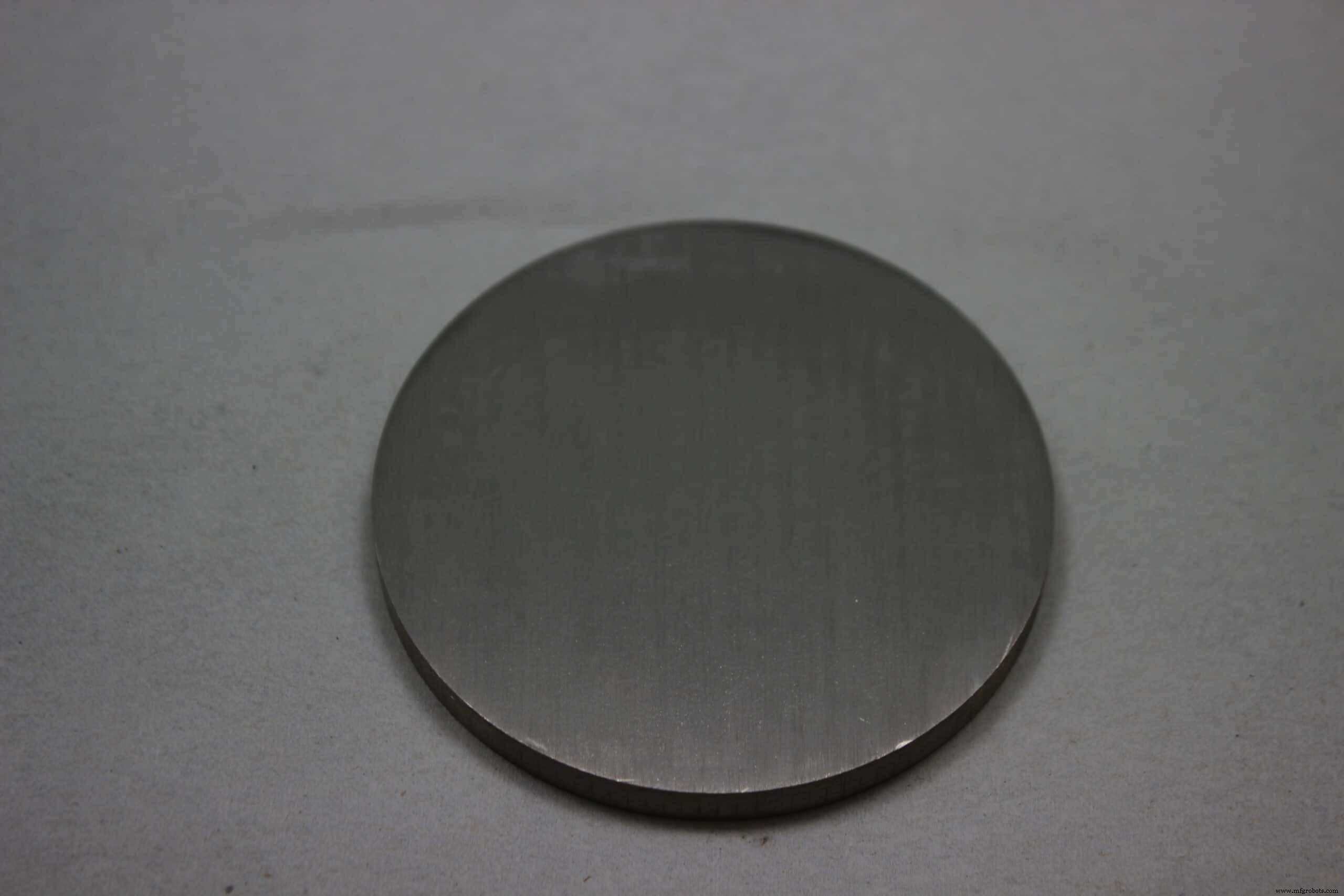
Souhaitez-vous appliquer des revêtements par dépôt physique en phase vapeur dans l'un de vos projets ? Vous souhaitez améliorer les propriétés de vos matériaux grâce à la technologie PVD ? Contactez-nous !
Matériau composite
- Qu'est-ce que le dépôt chimique en phase vapeur?
- Impression vs machines CNC
- pour arrêter de casser les fraises en bout
- pour dépanner un e-stop de machine CNC
- c'est SFM dans l'usinage ?
- es de liquide de refroidissement pour usinage CNC
- Robots d'intelligence artificielle
- La communication M2M ou Machine to Machine, qu'est-ce que c'est ?
- L'automatisation industrielle