Technologie de finition de surface des alliages de magnésium
Cet article présentera les propriétés de base et les applications des alliages de magnésium et 5 techniques de finition de surface couramment utilisées pour les alliages de magnésium.
Propriétés des alliages de magnésium
Les alliages de magnésium désignent des alliages à base de magnésium puis d'ajout d'autres éléments. Parmi eux, les alliages magnésium-aluminium sont les plus utilisés, suivis des alliages magnésium-zinc-zirconium et des alliages magnésium-manganèse.
Application d'alliage de magnésium
Les alliages de magnésium ont une faible densité et une résistance élevée. Les alliages de magnésium sont largement utilisés dans les appareils photo reflex numériques, les automobiles, l'aérospatiale et d'autres domaines.
Application sur les appareils photo reflex numériques
Les alliages de magnésium ont une faible densité, une résistance élevée et certaines propriétés anticorrosion. Par conséquent, il est souvent utilisé comme squelette de l'appareil photo reflex. Dans des circonstances normales, les appareils photo reflex numériques milieu à haut de gamme et professionnels utiliseront un alliage de magnésium comme squelette. Le squelette en alliage de magnésium est durable et agréable au toucher.
Application en voiture
(1) Tels que le carter d'embrayage, le tableau de bord, le corps de la boîte de vitesses, le capot avant du moteur, la culasse, le carter du climatiseur, etc.
(2) Tels que volant, support de frein, cadre de siège, etc.
Application dans l'aérospatiale
Les alliages de magnésium sont les matériaux de structure métalliques les plus légers utilisés dans les industries de fabrication d'avions, d'engins spatiaux, de fusées et de missiles.
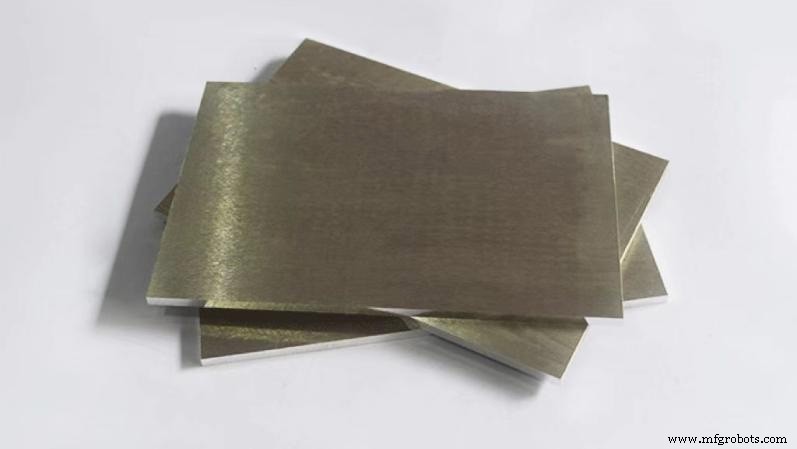
Finition de surface des alliages de magnésium
Les alliages de magnésium sont largement utilisés dans les transports, la technologie des fusées et d'autres domaines en raison de leur faible densité, de leurs bonnes performances spécifiques, de leur bonne absorption des chocs, de leur bonne conductivité électrique et thermique et de leurs bonnes performances de traitement.
Avec le développement de l'économie, le niveau de la science et de la technologie s'est amélioré. Une variété de technologies de traitement de surface sont appliquées au processus de traitement de surface des alliages de magnésium, ce qui peut élargir efficacement la gamme d'applications des matériaux en alliage de magnésium, prolonger la durée de vie des matériaux en alliage de magnésium et jouer efficacement le rôle des alliages de magnésium.
La faible résistance à la corrosion est devenue la principale raison limitant l'application ultérieure des alliages de magnésium. La principale raison de la corrosion des alliages de magnésium est qu'un film protecteur efficace ne peut pas se former à la surface des alliages de magnésium et qu'il agit comme une anode lorsqu'il est en contact avec d'autres matériaux métalliques.
Afin de prévenir efficacement la corrosion des alliages de magnésium, nous pouvons réaliser des traitements de surface sur les alliages de magnésium. La technologie de traitement de surface est non seulement efficace dans la protection des alliages de magnésium, mais aussi simple et économique. Un revêtement dense et uniforme avec une bonne adhérence peut jouer un bon rôle protecteur et réduire efficacement le taux de corrosion des matériaux en alliage de magnésium.
À l'heure actuelle, les technologies de traitement de surface en alliage de magnésium couramment utilisées comprennent la galvanoplastie, le placage autocatalytique, le revêtement par conversion chimique, l'anodisation et l'oxydation par micro-arc.
1. Revêtement de conversion chimique
Le revêtement de conversion chimique est une réaction entre les atomes sur la surface métallique et les anions dans le milieu pour former une couche de séparation avec une bonne adhérence sur la surface métallique. Cette couche de couche d'isolation composée est appelée revêtement de conversion chimique.
Les revêtements de conversion chimique des alliages de magnésium comprennent les revêtements de conversion organiques et les revêtements de conversion inorganiques, parmi lesquels il existe de nombreux revêtements de conversion inorganiques. Les revêtements de conversion inorganiques comprennent les revêtements de conversion au chromate, les revêtements de conversion au phosphate, les revêtements de conversion aux sels de terres rares, les revêtements de conversion au stannate et les revêtements de conversion au permanganate de potassium.
Les films de conversion organiques comprennent les films de conversion de composés organométalliques, les films de conversion d'acides organiques et les monocouches auto-assemblées. Le revêtement de conversion chimique de l'alliage de magnésium est relativement mince et doux, il est donc rarement utilisé seul et est généralement utilisé comme processus de protection intermédiaire.
(1) Film de conversion inorganique
Parmi eux, la conversion du chromate est relativement mature. Les revêtements de conversion au chromate peuvent retarder l'apparition de la rouille et améliorer la résistance à la corrosion.
Bien que l'effet anti-corrosion du revêtement de conversion contenant du chrome soit meilleur, il peut être utilisé dans un environnement à température plus élevée. Cependant, le Cr(VI) qu'il contient est toxique, le coût de traitement des déchets liquides est élevé et il pollue l'environnement. Il a donc été progressivement remplacé par une méthode de conversion chimique sans chrome et respectueuse de l'environnement.
Le traitement de conversion chimique sans chrome comprend principalement le phosphate, le manganate, le molybdate, le stannate, le sel d'acide organique, la passivation des terres rares et les méthodes de conversion composite.
(2) Film de conversion composé organique
Le traitement de la matière organique des alliages de magnésium est un nouveau procédé de traitement de conversion sans chrome qui peut améliorer la résistance à la corrosion des alliages de magnésium. Le film de conversion présente les avantages d'une bonne résistance à la corrosion, du respect de l'environnement, de matières premières non toxiques et inoffensives, facilement disponibles et d'un faible coût. Les revêtements de conversion de composés organiques de magnésium et d'alliages de magnésium peuvent être divisés en trois catégories :les revêtements de conversion de composés organiques métalliques, les revêtements de conversion de composés acides organiques et les monocouches auto-assemblées.
- Revêtement de conversion composé organométallique
Une fois que le composé organique a réagi avec l'atome de métal, il a un bon effet protecteur sur le substrat en alliage de magnésium, ce qui peut améliorer considérablement la résistance à la corrosion de l'alliage de magnésium.
- Film de conversion composé d'acide organique
Le procédé de revêtement par conversion d'oxalate présente les caractéristiques d'une faible toxicité et d'une faible pollution de l'environnement. Dans les conditions de processus optimisées, le revêtement de conversion d'oxalate est composé de particules uniformes, petites et relativement denses, avec une bonne adhérence et une bonne résistance à la corrosion, et ses performances peuvent répondre à la norme d'utilisation.
- Monocouches auto-assemblées
Une monocouche auto-assemblée fait référence à une monocouche ordonnée bidimensionnelle étroitement disposée formée par l'adsorption spontanée de molécules organiques sur une surface solide en solution ou en phase gazeuse. Il a une bonne résistance à la corrosion, un ordre et une orientation élevés, un garnissage à haute densité, de faibles défauts et une structure stable. La structure et les propriétés des films auto-assemblés sont affectées par de nombreux facteurs, tels que les propriétés de la solution (concentration, pH, etc.), les propriétés moléculaires assemblées, le temps d'immersion du substrat dans la solution, le solvant, etc.
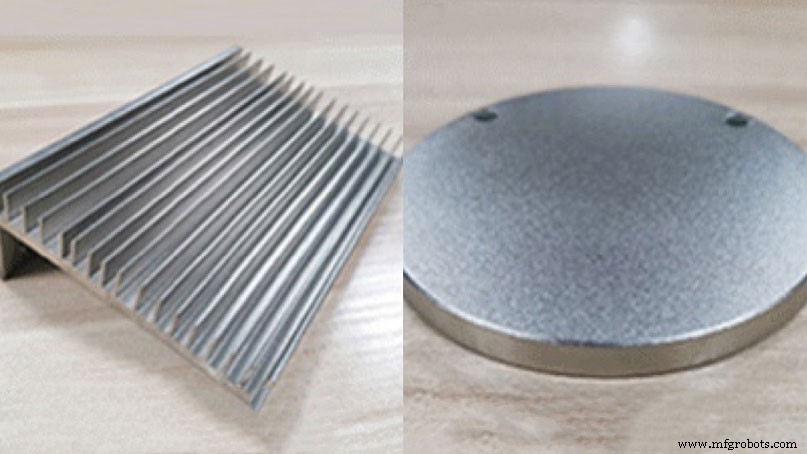
2. Revêtement Cermet
Une couche d'autres couches métalliques est formée à la surface des alliages de magnésium par pulvérisation thermique, dépôt en phase vapeur, etc. pour atteindre l'objectif d'anti-corrosion et de décoration.
(1) Dépôt de vapeur
Les techniques de dépôt en phase vapeur sont divisées en dépôt chimique en phase vapeur et dépôt physique en phase vapeur. Il fait référence à l'utilisation de processus physiques et chimiques en phase gazeuse pour modifier la composition de la surface de la pièce et former un revêtement métallique ou composé avec des propriétés spéciales (telles que des couches ultra-dures résistantes à l'usure ou des propriétés optiques et électriques spéciales) sur la surface. Le dépôt en phase vapeur est l'une des nouvelles technologies de renforcement de surface de moule, qui joue un rôle important dans l'amélioration de la résistance à l'usure et à la corrosion des pièces mécaniques.
Le dépôt en phase vapeur recouvre généralement la surface de la pièce d'une couche d'éléments du groupe de transition (titane, vanadium, chrome, zirconium, molybdène, tantale, niobium et hafnium) et de composés de carbone, d'azote, d'oxygène et de bore d'une épaisseur d'environ 0,5 à 10 μm
(2) Projection Thermique
La technologie de pulvérisation thermique est une méthode consistant à utiliser une source de chaleur pour chauffer le matériau pulvérisé à un état fondu ou semi-fondu, puis à le pulvériser et à le déposer sur la surface du substrat prétraité à une certaine vitesse pour former un revêtement.
La technologie de pulvérisation thermique crée une surface de travail spéciale à la surface des matériaux courants. Selon différents matériaux de revêtement, une ou plusieurs propriétés de résistance à l'usure, à l'oxydation, à la corrosion et à la chaleur peuvent être obtenues.
Le traitement de surface par pulvérisation thermique d'un alliage de magnésium se produit lorsqu'un revêtement métallique, céramique ou polymère pulvérise de petites gouttelettes de revêtement sur la surface du substrat à l'état fondu ou semi-fondu pour former une couche de dépôt par pulvérisation.
3. Alliage de surface au laser
L'alliage au laser fait référence au processus de fusion, de solidification et de formation rapides de nouvelles substances d'alliage à la surface des matériaux pour modifier leurs propriétés physiques et chimiques par l'effet thermique de l'interaction entre le laser et les substances en phase solide. La technologie de modification de surface au laser pour le traitement de résistance à la corrosion des alliages de magnésium a été largement utilisée.
4. Implantation ionique
L'implantation ionique est l'implantation d'ions accélérés de haute énergie dans un matériau sous vide sous l'action d'un champ électrostatique. Les ions implantés sont dans des positions de substitution ou interstitielles dans la solution solide, formant la couche de surface de la structure d'équilibre.
5. Diffusion Thermique
La méthode d'obtention du revêtement sur la surface de l'alliage de magnésium en mettant en contact l'alliage de magnésium avec la poudre de revêtement pour le traitement thermique est la technologie de diffusion thermique.
Conclusion
JTR peut vous fournir une variété de technologies de finition de surface pour répondre à vos exigences. Nous fournissons des solutions de fabrication de haute qualité qui peuvent réaliser votre conception en quelques heures et sommes équipés de divers équipements d'usinage CNC de précision pour garantir que nous pouvons répondre aux différents besoins des différents clients dans les étapes de développement d'échantillons, de production d'essai et de production de masse. .
Technologie industrielle
- Défauts à la surface des alliages de titane
- Votre guide des solutions de finition de surface d'impression 3D
- AMRC stimule l'innovation dans la technologie et l'économie circulaire
- 5 cas d'utilisation uniques pour les machines de finition
- Le guide que vous devez connaître sur la finition de surface
- Application de la technologie de finition de surface sur le moule
- Qu'est-ce que le revêtement de passivation et de conversion | CNCLATHING Services de finition de surface
- Technologie de montage en surface - De quoi s'agit-il ?
- Que savez-vous des différents types de finition de surface de PCB -II