Hitachi Powdered Metals adopte l'automatisation robotique et augmente son volume de 400 % sur un marché du travail tendu
La métallurgie des poudres (PM), ou frittage, est le processus de compactage de mélanges personnalisés de poudres élémentaires ou d'alliages dans des matrices préfabriquées pour fabriquer efficacement des pièces de machine de complexité variable. Une fois compactées, les formes sont chauffées dans un four à atmosphère contrôlée pour lier les particules et durcir les pièces.
Également connu sous le nom de compactage vert, le processus produit des composants presque nets qui utilisent généralement plus de 97 % de la matière première initiale dans la pièce finie. Les mélanges d'alliages de poudre personnalisés permettent de produire des pièces complexes, voire complexes, qui répondent aux spécifications de résistance et de tolérance requises pour les applications très exigeantes.
L'usine Hitachi Powdered Metal (USA) Inc. à Greensburg, Indiana, est l'une des neuf usines Hitachi dans le monde. Elle est spécialisée dans la production de composants de train de soupapes et de transmission pour les fournisseurs automobiles de premier rang aux États-Unis, avec une présence croissante parmi les fabricants de motos et d'équipements paysagers.
Motivation initiale
Hitachi Powdered Metals (HPM) a commencé à investir progressivement dans des robots industriels à l'usine de Greensburg en 2005, poussé par l'émergence d'un marché du travail tendu et la possibilité de fabriquer un produit extrêmement fragile.
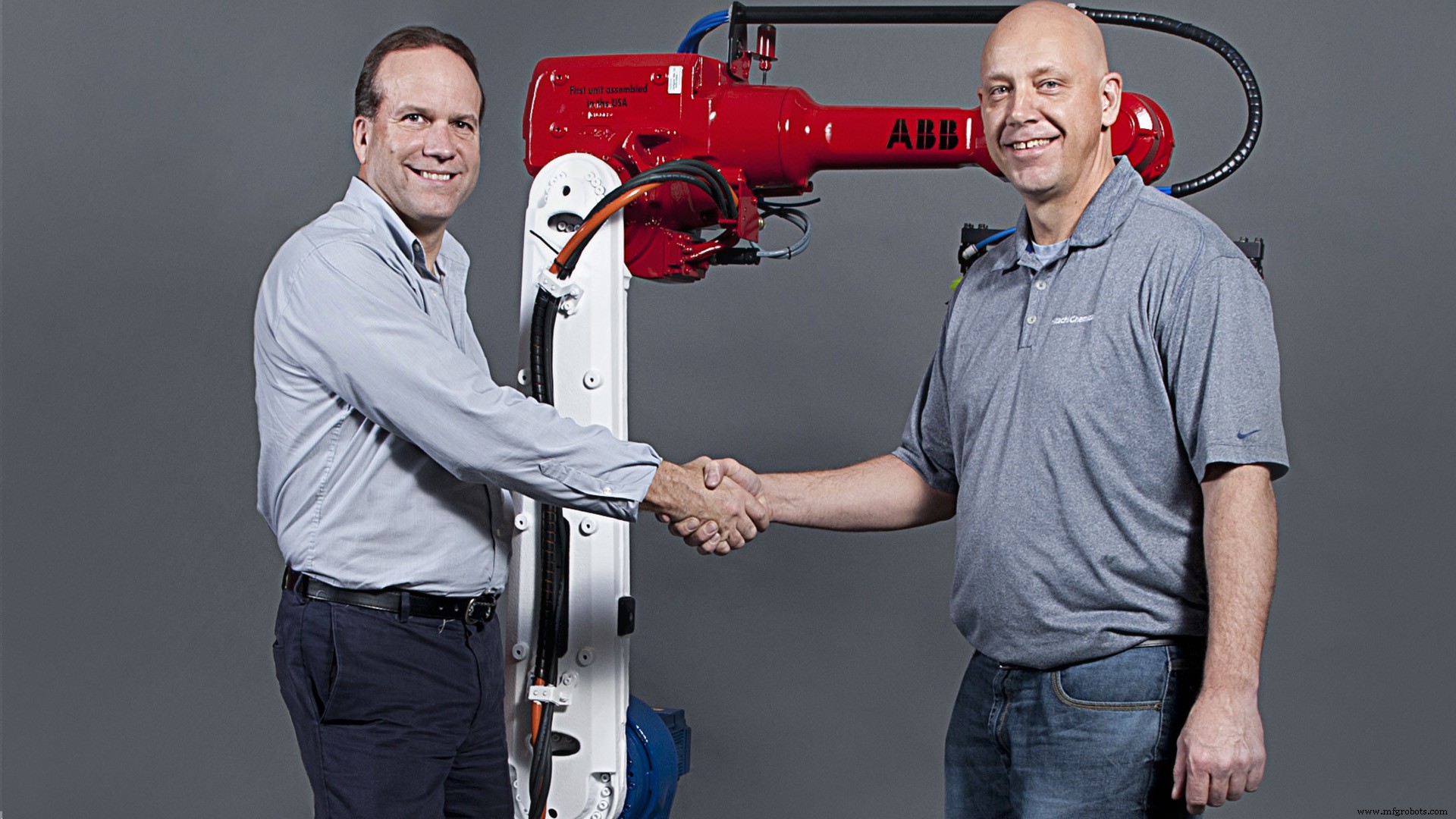
"Nous avons commencé avec des robots parce que nous avions une pièce à fabriquer pour un client qui avait de petites dents fragiles qui ne pouvaient pas être manipulées manuellement, et à ce moment-là, toutes nos presses de compactage étaient entretenues à la main", a déclaré Gregory Owens, président de l'usine HPM de Greensburg. "La réduction des coûts de main-d'œuvre a également été un facteur, mais peu de temps après la première installation, un important équipementier automobile a ouvert une usine de fabrication en ville, et notre problème de coût de main-d'œuvre est passé à un problème de disponibilité de la main-d'œuvre car il est devenu extrêmement difficile d'embaucher et de conserver des employés. "
Dans un effort pour réduire les coûts et minimiser toute exposition au cours de la période d'essai initiale, HPM a acheté un robot ABB S3 d'occasion de 1993 de CIM Systems Inc. à Noblesville, Ind. James Adams, qui avait rejoint HPM plusieurs années plus tôt en tant que un ingénieur en développement de fabrication, connaissait CIM, le fournisseur de valeur ABB Robotics le plus ancien (c'est-à-dire l'intégrateur de systèmes) aux États-Unis, grâce à son travail avec des robots chez son ancien employeur.
"CIM avait un robot d'occasion qui nous permettrait de nous frayer un chemin dans l'automatisation robotique, limitant notre exposition initiale au cas où il ne fonctionnerait pas comme prévu", a déclaré Adams. "Ils nous ont également fourni une assistance indispensable pour la programmation et l'intégration du système dans l'opération existante."
Réduction des rebuts, meilleure répartition de la main-d'œuvre
Lorsque les pièces métalliques en poudre sortent de la presse, avant d'être durcies au four, elles peuvent facilement s'effriter au moindre contact. Avec le robot nouvellement installé, doté d'une pince magnétique électrique pour manipuler la pièce, le taux de rebut du nouveau produit est passé de 11 % alors qu'il était manuellement tendu à 0,5 %.
«Lorsque les pièces étaient retirées manuellement de la presse, il y avait des dommages de manutention considérables. La pièce pourrait être imperceptiblement déformée, mais vous ne le sauriez pas jusqu'à ce qu'elle sorte du four cinq heures plus tard. Correctement programmés et équipés, les robots sont beaucoup plus doux dans la manipulation des pièces », a déclaré Adams.
Le nouveau système a permis à HPM de déplacer plusieurs des manipulateurs de machines manuelles vers des postes moins banals dans l'usine, réduisant ainsi le stress d'une tâche répétitive et réaffectant la main-d'œuvre de manière plus efficace.
La production augmente de 400 %
Au cours de l'année suivante, HPM a ajouté cinq autres robots S3 d'occasion, appliquant ce qu'il avait appris du système initial pour automatiser d'autres presses compactes. Au bout de 18 mois, HPM avait suffisamment économisé sur la ferraille et la main-d'œuvre pour investir dans son premier nouveau robot.
Avance rapide jusqu'en 2019. Aujourd'hui, avec plus de 200 robots installés, l'usine de Greensburg compte le même nombre d'employés qu'il y a 10 ans, mais produit quatre fois plus de volume, livrant facilement plus de pièces avec moins de personnel que n'importe quelle usine Hitachi PM mondiale. .
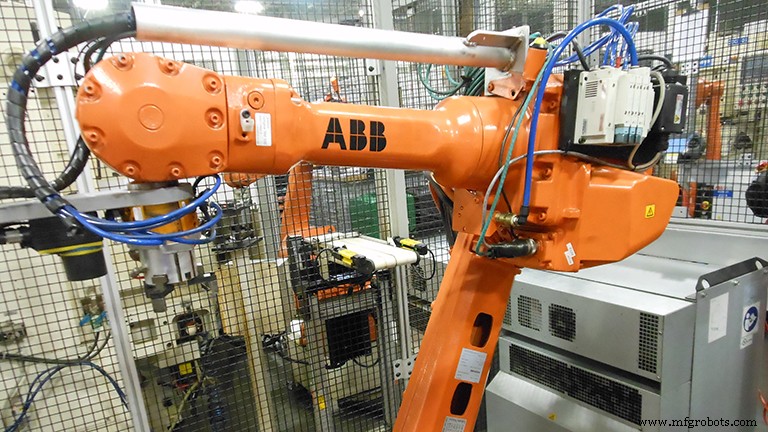
"Une fois que le premier robot a été installé pour la partie fragile, il est devenu très évident que nous pouvions vraiment tirer parti d'autres robots automates", a déclaré Owens. "Les robots ont largement dépassé nos attentes initiales, et avec les pénuries de main-d'œuvre auxquelles nous continuons de faire face, je crois franchement que les robots nous ont évité de ne pas exister."
Avec le succès du premier robot, le rythme des installations suivantes a été soutenu. Il a fallu dix ans pour atteindre 100 robots installés, puis, à mesure que les affaires et l'économie continuaient de s'améliorer, il n'a fallu que quatre années pour atteindre le 200 e récemment installé. robot.
Lorsque les opportunités se sont présentées, HPM a continué à acheter des robots ABB d'occasion en bon état, même si de plus en plus de nouveaux robots ont été ajoutés à la flotte. En fait, chaque robot ajouté depuis le #147 en 2015 était nouveau.
La base d'installation de HPM comprend une gamme de robots ABB à six axes de petite et moyenne gamme, un robot Delta et plusieurs modèles SCARA récemment ajoutés. Avec 350 employés, l'investissement en automatisation est bien utilisé, avec trois équipes cinq à six jours par semaine.
"Notre siège social est au Japon", a déclaré Adams. "Une fois qu'ils ont vu les performances des robots et le retour sur investissement rapide, ils ont été très favorables à notre programme robotique."
Certains des robots, neufs et d'occasion, sont ABB Foundry Prime d'ABB Robotics, Auburn Hills, Michigan. Ce sont des modèles classés IP67 qui ont des connexions bien scellées qui protègent le fonctionnement interne des robots du métal fin et tranchant. poudres qui flottent dans l'atmosphère de la plante. Les nombreux modèles de robots standard classés IP65 sur le sol de HPM sont robustes et ont été capables de résister à l'environnement poussiéreux.
Développement continu
La prolifération des robots chez HPM a été soutenue par la réplication des applications existantes et l'extension de l'automatisation à d'autres fonctions de l'installation.
Après l'installation du premier robot s'occupant de la presse compacte pour le produit le plus fragile, Adams et son équipe ont automatisé séquentiellement le retrait des compacts des autres presses. Une partie de ce processus consistait à placer chaque pièce sur une échelle pour vérifier son intégrité. Une fois vérifiée, la pièce était placée sur un convoyeur menant au four.
Des gains de main-d'œuvre supplémentaires en ont résulté et, grâce à l'habileté du robot, le taux de rebut des pièces les moins fragiles est passé de 7 % au même 0,5 % de la pièce initiale.
À la fin du convoyeur, les pièces sont déposées sur des plateaux de frittage qui, une fois remplis, sont placés dans des fours pour le processus de durcissement. Ce processus de chargement du four est devenu la deuxième fonction majeure à être automatisée.
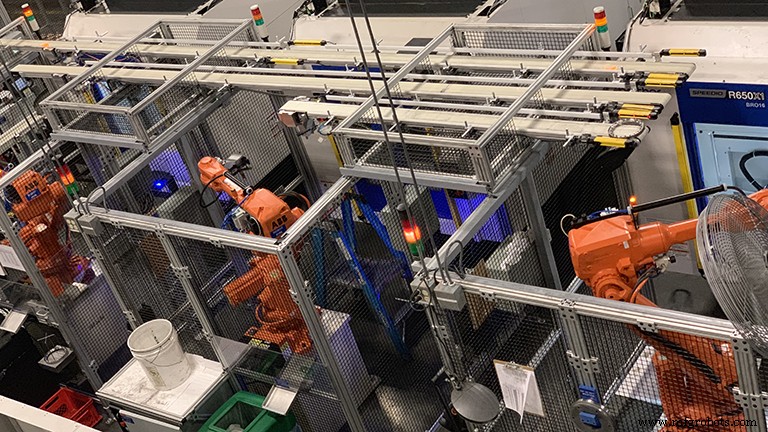
Continuant à un rythme mesuré, des robots ont ensuite été installés pour retirer les pièces des plateaux et les placer sur des palettes, tout en insérant des séparateurs entre chaque couche de palettes.
"Au fur et à mesure que nous nous sommes familiarisés avec les robots, nous avons pris ce que nous avons appris et dupliqué les applications dans l'installation", a déclaré Adams. "La programmation est devenue beaucoup plus facile, et le dernier jour de l'installation de la ligne, nous ajustions les programmes existants, copions et collions et nous étions opérationnels en quelques heures."
RobotStudio, le logiciel de simulation et de programmation hors ligne d'ABB, est devenu un outil précieux pour accélérer l'adoption croissante de la technologie robotique par HPM. Construit sur ABB VirtualController, une copie exacte du logiciel réel qui exécute les robots en production, RobotStudio effectue des simulations réalistes, en utilisant des programmes de robot et des fichiers de configuration identiques à ceux utilisés dans l'atelier. Avec RobotStudio, Adams a pu concevoir la disposition optimale des cellules et vérifier ses performances avant d'intégrer les robots dans une opération particulière.
"C'est le meilleur logiciel jamais développé", a déclaré Adams. "Cela permet d'économiser du temps et de l'argent à la fois en créant des systèmes pour de nouvelles applications et en reproduisant ceux que nous avions déjà installés dans d'autres zones de l'usine."
Présentation de Vision
La simplicité relative de la réplication n'existe qu'après qu'une certaine application a été installée et affinée dans l'usine. Les nouvelles applications sont souvent plus difficiles. Après 18 mois et l'intégration réussie de six robots de pressage, HPM a eu la confiance nécessaire pour adopter la technologie de vision, à ses débuts à l'époque (2006), pour automatiser de manière robotique l'opération complexe de frappe ou de repressage.
Une fois que les pièces sortent du four, elles peuvent souvent se déformer, ce qui nécessite qu'elles soient placées dans une presse qui les ramène à être droites ou plates. De nombreuses pièces ont des rainures de clavette ou des dents qui doivent être placées dans le moule avec tous les aspects alignés avec précision. Avant l'arrivée des robots, les pièces frappées étaient gérées par un système d'automatisation strict qui, avec de nombreuses variantes de produits, nécessitait des changements fréquents et chronophages. Les changements étaient si longs que les sauvegardes de 250 lots de produits, chacun contenant environ 100 pièces, étaient courantes.
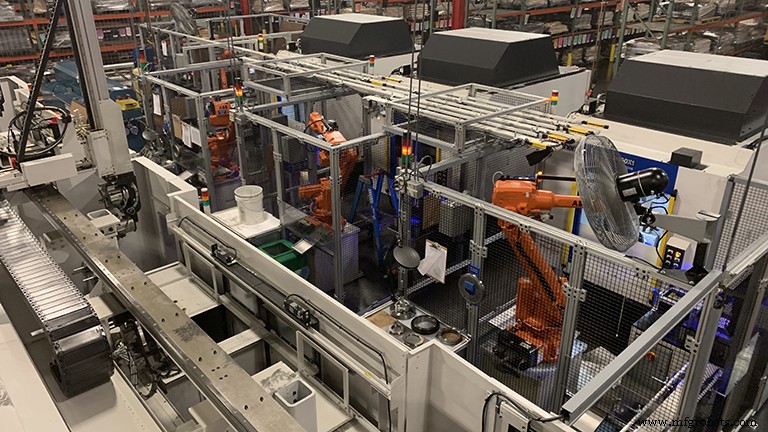
Avec le robot doté de la vision, il n'y a pas de temps d'arrêt. Le robot est capable d'identifier la pièce parmi un groupe de nombreuses pièces différentes, de la saisir, de l'orienter radialement et de la positionner avec précision dans le repress.
Étant donné que le système de vision devait s'interfacer avec la toute dernière technologie robotique, il s'agissait du premier nouveau robot ABB installé sur le site de Greensburg. Peu de temps après sa mise en service, deux nouveaux robots supplémentaires ont été achetés pour la même application.
"Avant l'installation du robot de la station de frappe, le personnel de la répression travaillait tous les jours", a déclaré Adams. "Six mois après l'installation du premier robot de vision, il n'y avait plus de sauvegardes et le personnel avait ses week-ends de congé !"
Autre vision
HPM a de nouveau utilisé la vision plus tard dans le dernier des processus majeurs à être automatisé, la dépalettisation des pièces qui avaient été envoyées pour un traitement thermique spécialisé. Bien que les pièces soient envoyées soigneusement positionnées sur des couches étagées sur une palette, elles reviennent dans un désordre relatif et sont difficiles à désempiler. Un robot ABB avec vision intégrée est capable de trouver les pièces et de les saisir solidement afin qu'elles puissent être dépalettisées en toute sécurité.
"C'est l'une des capacités uniques des robots ABB", a déclaré Dave Fox, président de CIM Systems, qui a aidé à intégrer les différents systèmes de vision. « Les pièces sont vraiment désorientées sur les patins, pas en rangées uniformes, certaines étant à l'envers. Un robot typique à six axes aurait toutes sortes de problèmes de singularité, se mettant dans une position où il ne peut plus bouger. Mais le robot ABB utilisant l'évitement avancé des singularités est capable de trouver les pièces, de les saisir et de les placer en toute sécurité sur un convoyeur sans perdre de temps. »
Robots SCARA pour le contrôle qualité
Sans surprise, une recherche récente d'un système plus efficace pour inspecter les guides de soupapes a ramené aux robots, dans ce cas un groupe de modèles ABB SCARA (Selective Compliance Assembly Robot Arm), qui sont généralement utilisés pour l'assemblage de petites pièces et la manutention. /P>
Le protocole HPM exige une inspection à 100 % de tous les guides de soupapes, ce qui est une entreprise considérable compte tenu de la variété des pièces qui doivent être testées :30 variations de taille différentes et 16 points de détection pour chaque pièce. Le système de test d'automatisation stricte dominant étant incapable de suivre suffisamment le volume, Adams a commencé à rechercher un meilleur système.
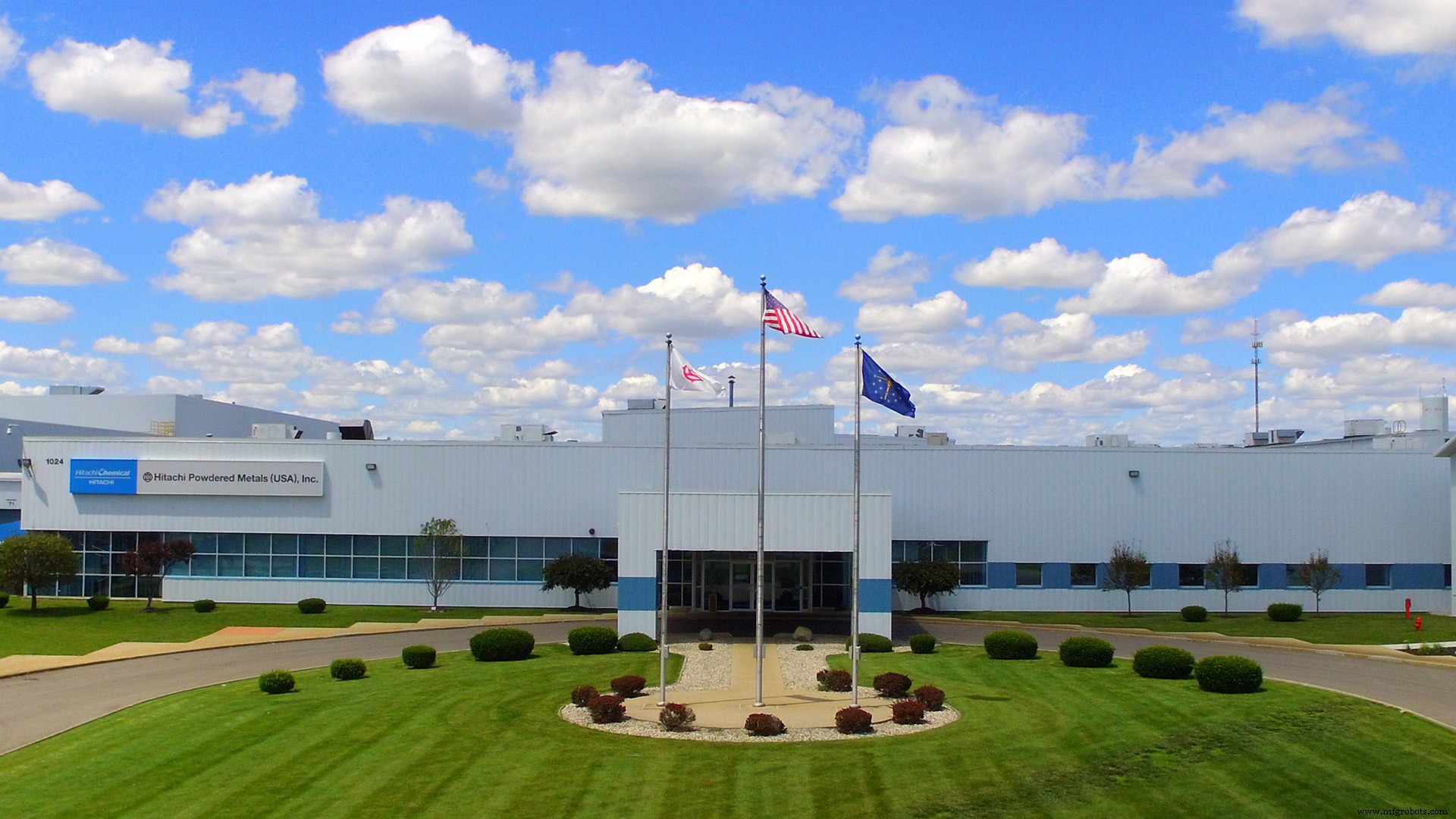
Après avoir examiné diverses options, qui comportaient toutes trop de pièces mobiles et nécessitaient une ingénierie complexe, Fox a suggéré de concevoir un système autour des robots SCARA, qu'ABB a ajoutés à son portefeuille en 2016. Ils étaient certainement assez rapides, avec une grande répétabilité, et avaient un faible encombrement et une forme de montage sans entrave qui s'intègre dans un espace confiné.
Un système relativement simple a été conçu avec trois robots SCARA prélevant des guides de soupape individuels sur un convoyeur à trémie et les présentant à des caméras de vision et à un « comparateur » fixe aux différents angles nécessaires pour accéder aux 16 points de détection. Les pièces qui ont réussi ont été placées sur un convoyeur et celles qui n'ont pas réussi ont été placées dans des bacs de rejet.
Avec la flexibilité de gérer avec dextérité chaque variation de pièce différente avec la même facilité, le système est capable d'inspecter une pièce toutes les deux secondes, 30 % plus rapidement que la méthode précédente. Étant donné que les mouvements sont limités à une courte distance et que les pièces sont très légères, un robot à six axes ne fonctionnerait pas aussi efficacement que l'élégant SCARA à portée limitée.
« Les SCARA sont un excellent ajout au portefeuille d'ABB. Sans cette solution, Hitachi aurait probablement dû rechercher une autre technologie pour l'inspection des pièces », a déclaré Fox. "C'était agréable de pouvoir trouver une autre application pour les robots, même si ce n'était pas la première option qui me venait à l'esprit."
Systèmes CIM toujours présents
Une constante qui a été sur la scène depuis le premier robot installé à HPM jusqu'à aujourd'hui, que ce soit au premier plan ou à l'arrière-plan, est CIM Systems. Toujours disponible en cas de besoin, CIM a configuré HPM avec des robots neufs et d'occasion, aidé à programmer et à dépanner, et peut-être plus important encore, a appris au personnel HPM à faire beaucoup de choses eux-mêmes.
Lorsque HPM a intégré des robots dans une nouvelle application, avec vision ou non, CIM a fait la configuration et la programmation, en étant toujours soucieux de partager son expertise, y compris l'utilisation de RobotStudio. Pendant l'accalmie occasionnelle dans le calendrier d'acquisition de robots de HPM, CIM était disponible pour mettre à jour les programmes, trouver des pièces de rechange insaisissables pour les modèles plus anciens ou offrir des conseils sur le travail avec des robots à travers une gamme de millésimes.
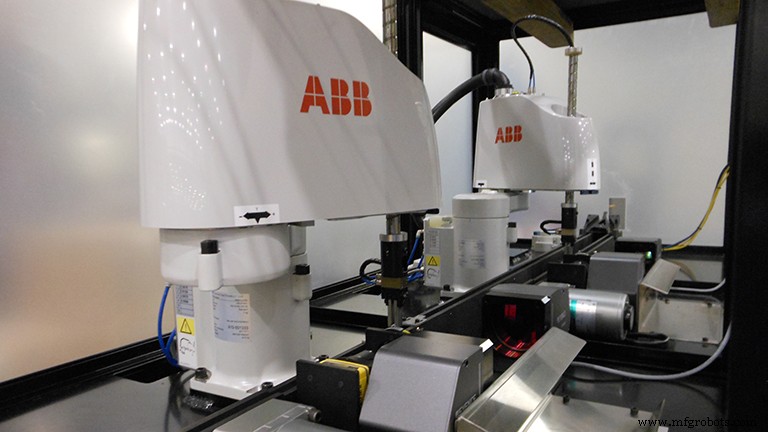
« Au fur et à mesure que nous abordions chacun des différents processus, nous avons demandé à CIM de faire l'intégration et la programmation initiales. Une fois que nous avons commencé à reproduire les processus dans toute l'usine, nous en avions suffisamment appris pour faire beaucoup nous-mêmes », a déclaré Adams. « En raison de sa relation étroite avec ABB, Dave Fox sait toujours quand une nouvelle technologie arrive et quels robots seraient optimaux pour nos diverses applications. L'assistance que nous avons reçue de CIM Systems et le service d'ABB étaient une combinaison idéale. »
Avec une telle relation de longue date, il n'est pas surprenant que lorsque le premier robot est sorti de la chaîne de production de l'usine de fabrication américaine d'ABB à Auburn Hills en 2017, il a été commandé par CIM chez HPM. Le robot IRB 2400, unique en son genre, a été peint sur mesure en rouge, blanc et bleu à l'usine et est placé bien en vue dans les installations de HPM, effectuant des tâches d'inspection et de palettisation.
"Nous sommes ravis d'avoir pu nous procurer le premier robot de fabrication américaine pour HPM", a déclaré Fox. "C'est particulièrement important parce que l'usine d'Indiana possède l'automate le plus flexible des nombreuses installations mondiales de HPM."
Soutien aux autres installations HPM
La direction d'entreprise de HPM au Japon a pris note des importantes améliorations de productivité réalisées par l'équipe de Greensburg grâce aux robots et, en 2017, a chargé Adams et Owens de diriger une initiative « Global Robotics » pour soutenir les autres usines de métal en poudre Hitachi dans le monde à développer leur utilisation des robots. .
Le programme de deux ans a dépassé le point médian et les sociétés affiliées commencent à réaliser des améliorations significatives de la productivité, même avec des coûts de main-d'œuvre inférieurs dans les autres pays.
Adams a mis en place la fonction de surveillance à distance d'ABB chez HPM afin que lui ou les membres de son équipe puissent voir comment les robots fonctionnent et résoudre la plupart des problèmes depuis n'importe où en dehors de l'usine sur un ordinateur portable, une tablette ou un smartphone. Avec les nouveaux robots, HPM espère tirer parti des ABB Ability Connected Services, l'offre numérique unifiée et intersectorielle d'ABB, qui fournit des données en temps réel sur l'état et les performances des robots depuis n'importe quel endroit.
Projets futurs
La mission continue de HPM consiste à améliorer ses opérations grâce à l'automatisation robotique.
"Nous prévoyons une croissance de 10% par an dans un avenir prévisible, et nous devons faire tout ce que nous pouvons pour rester compétitifs", a déclaré Owens. "Nous examinons quelles pièces de transmission nous serons en mesure de fabriquer pour les véhicules électriques, et nous visons à pénétrer des segments non automobiles comme l'équipement lourd, où le métal en poudre peut être en mesure de remplacer les pièces faites d'autres matériaux à moindre coût. ."
"Je prévois certainement que le rythme des installations de robots restera stable, voire augmentera", a déclaré Owens.
Pour plus d'informations sur Hitachi Powdered Metals (USA) Inc., visitez www.hitachi-pm.us ou appelez le 812-663-5058. Pour plus d'informations sur CIM Systems Inc., visitez www.cimrobotics.com ou appelez le 317-773-5600. Pour plus d'informations sur ABB Robotics, visitez www.abb.com/robotics ou appelez le 248-391-9000.
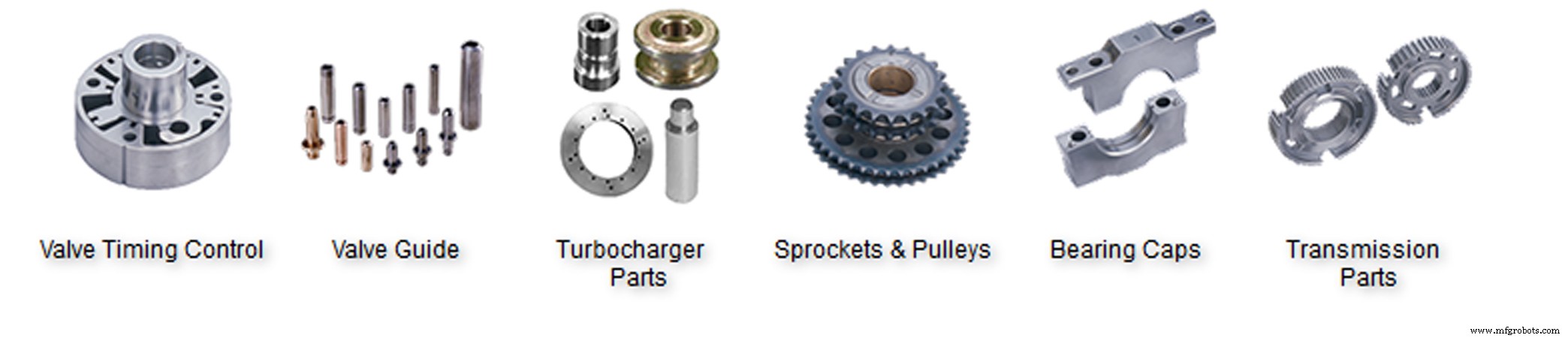
Système de contrôle d'automatisation
- Logistique et automatisation de l'entreposage
- Plus d'automatisation =plus de robots capables
- NPE2018 :les robots et l'automatisation s'attaquent à la complexité croissante
- Automatisation :Lame d'ébavurage conforme pour robots
- ABB prédit les principales tendances qui modifieront l'automatisation robotique en 2022
- Un nouveau type de « cerveau » robotique pourrait transformer les usines modernes
- Hitachi va acquérir l'intégrateur de systèmes robotiques JR Automation pour 1,4 milliard de dollars
- Hitachi finalise l'acquisition de JR Automation
- ATI Industrial Automation lance une nouvelle ponceuse orbitale pour robots