Aiguiser le point d'attaque de l'automatisation dans l'atelier
Sur la machine, près de la machine, entre les machines :l'IIoT n'est jamais loin
La flexibilité est venue à l'automatisation, peut-être comme jamais auparavant. Et pour les industries qui nécessitent un usinage, un assemblage et une mesure de précision, les technologies d'automatisation n'ont jamais été aussi disponibles.
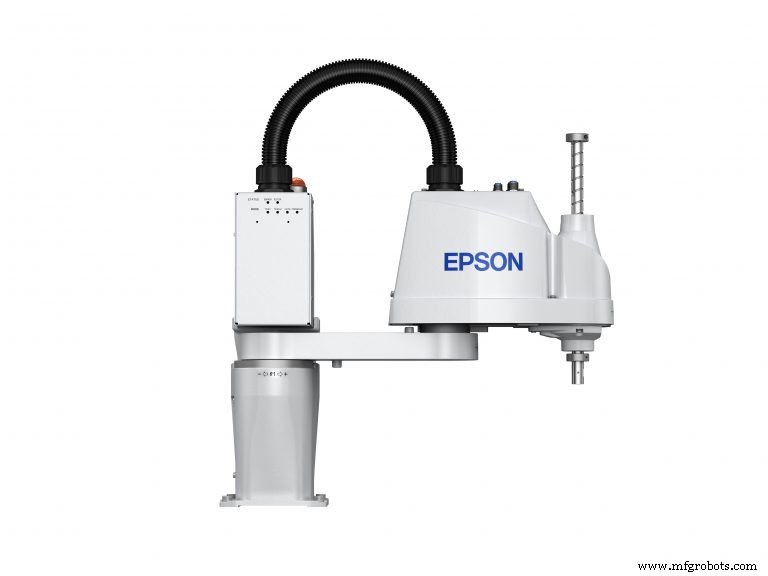
Les solutions d'automatisation vont de la plus haute précision à la fiabilité et à la vitesse testées en production. Les technologies ne sont presque jamais présentées comme étant tout pour tout le monde, ou plus exactement toutes les solutions à tous les problèmes. Il ne s'agit pas de choisir son poison, il s'agit plutôt de sélectionner la technologie la plus appropriée et de pouvoir justifier le retour sur investissement. L'automatisation éprouvée comme les ravitailleurs de barres, les chargeurs à portique, les options simplifiées de prélèvement et de placement ne sont jamais trop loin de l'avant-garde, mais elles sont rejointes et éclipsées dans de nombreux cas par de nouvelles technologies robotiques plus rapides qui bénéficient de la polyvalence que l'IIoT numérique la communication peut apporter à la fabrication.
La précision dans l'horlogerie a conduit à des dizaines de robots
Selon Rick Brookshire, chef de produit du groupe, robots pour Epson America Inc. (Carson City, Californie), lorsque sa société mère, Seiko Epson Corp., a développé des robots pour fabriquer ses propres montres il y a environ 35 ans, la précision était primordiale. Aujourd'hui, Epson allie vitesse et précision dans son offre de plus de 300 robots dans des tailles allant de 175 à 1000 mm de portée, avec des charges utiles jusqu'à 20 kg et une répétabilité jusqu'à 5 μm. Les premières applications typiques comprenaient des pièces pouvant tenir dans votre main pour l'automobile, le médical, l'électronique et des fonctions telles que l'assemblage, l'entretien des machines, la mise en kit, l'inspection et les tests, et la palettisation dans pratiquement tous les types d'industrie.
Le plus récent ajout au portefeuille de robots Epson, le SCARA d'entrée de gamme Synthis T3 All-in-One (bras de robot articulé à conformité sélective), a été introduit à un prix et avec des capacités de vitesse et de précision destinées à étendre davantage les applications d'Epson dans automobile, électronique, dispositifs médicaux et produits de consommation.
Depuis son introduction fin 2017, le T3 a été accepté par le marché au-delà de nos attentes les plus folles », a déclaré Brookshire. "Le T3 a un contrôleur contenu à l'intérieur du bras, une connexion à un PC pour la programmation, le tout au prix de 7495 $. Il intègre le même logiciel que celui que nous utilisons dans nos robots haut de gamme à six axes de la série G. »
Comme les autres robots SCARA d'Epson, le T3 est un robot à quatre axes qui passera d'une surface plane à une surface plane et a été positionné comme une alternative aux glissières linéaires dans l'atelier. "Les glissières linéaires doivent être ajustées en permanence pour les changements", a déclaré Brookshire. Le T3, avec un bras de 400 mm et une charge utile maximale de 3 kg, répond à ce besoin de flexibilité avec une vitesse pour un fonctionnement efficace, une intégration dans une conception compacte et le logiciel de programmation RC+ d'Epson.
Efficacité des robots dans des packages compacts
Erowa Technology Inc. (Arlington Heights, IL) a une histoire de développement de systèmes de palettisation et de robots pour manipuler des outils et des pièces pour le traitement EDM, ainsi que des applications d'entretien de machines pour la fabrication de puces en tandem ou en combinaison avec des machines EDM. « Un job shop fait quelque chose de différent chaque jour. C'est notre point fort :placer une pièce sur une palette et dans un magasin et laisser un robot la déplacer à l'intérieur de la machine pour la traiter, que ce soit pour une, deux ou cinq pièces », a déclaré Chris Norman, président et directeur de l'exploitation. "Nous sommes sur un marché de niche et notre automatisation est conçue pour les ateliers de travail, les ateliers de moulage de matrices et les ateliers de fabrication aérospatiale à court terme, pour n'en nommer que quelques-uns."
La demande pour les produits d'automatisation d'Erowa a été forte. « Aujourd'hui, les ateliers acceptent mieux les solutions d'automatisation. Nous avons connu une croissance des ventes d'automatisation de 10 à 20 % par rapport à 2017, soit une hausse d'environ 30 % par rapport à 2016 », a déclaré Norman. « Nous ne sommes plus seulement les gars de l'EDM, bien que nous fassions encore beaucoup dans la fabrication et la manipulation d'électrodes. Notre outillage est utilisé dans de nombreuses facettes différentes de la fabrication. Notre système de changement rapide entre nos palettes et nos mandrins et changeurs d'outils pour outils de coupe et changeurs d'électrodes sur une EDM est une forme d'automatisation à laquelle beaucoup d'entreprises ne pensent pas."
La programmation de ses robots a été simplifiée, selon Norman. « Nos robots ne sont pas difficiles à programmer. Il existe différents niveaux d'intégration. La plus basique est que le robot est l'esclave de la machine. Nous avons effectué tout le travail d'interface et avons des interfaces avec tous les principaux équipementiers. Lors de l'installation, nous appelons la palette dans la machine de la même manière que vous appelez une broche dans la machine. Il s'agit essentiellement d'une ligne de code. Nous avons un logiciel de contrôle de cellule qui gère la machine et le robot plutôt que le contrôle de la machine. En règle générale, nous n'avons besoin que d'environ une journée de formation avec les clients », a déclaré Norman.
L'atelier est un endroit très fréquenté
Les derniers EDM de Makino Inc. (Mason, OH) sont dotés d'une automatisation pour un fonctionnement sans surveillance. L'assistance provient d'HyperConnect, la suite d'applications de l'Internet industriel des objets (IIoT) de Makino pour les GED qui améliore l'expérience et l'efficacité de l'utilisateur et réduit les temps d'arrêt des machines. Disponible sur tous les EDM Makino équipés de systèmes de contrôle Hyper-i, HyperConnect permet aux responsables d'atelier et aux opérateurs de surveiller et de contrôler les processus EDM à partir de n'importe quel PC, appareil intelligent ou autre système de contrôle Hyper-i sur le réseau.
Les opérateurs EDM sont déjà confrontés à trop de choses dans l'atelier. La dernière chose que l'on souhaite, c'est qu'ils fassent des allers-retours entre les machines et les espaces de bureau. HyperConnect offre à ces opérateurs un accès à ce dont ils ont besoin pour optimiser leur efficacité, qu'ils soient à la machine, dans leur bureau ou à distance.
La suite HyperConnect dispose de quatre fonctionnalités de connectivité principales permettant au personnel de l'atelier de surveiller, de planifier et de dépanner leurs opérations EDM. Parmi les quatre fonctions, les fonctions EDM Mail et PC Viewer sont les plus couramment utilisées. EDM Mail relaie les informations sur l'état de la machine aux opérateurs par e-mail pendant le fonctionnement sans surveillance pour aider à réduire les temps d'arrêt et prendre en charge les capacités multitâches. Il peut fournir des mises à jour périodiques à intervalles réguliers des conditions de fonctionnement d'une machine ou alerter les opérateurs d'un arrêt de la machine à toute heure.
Interconnexion des processus à une idée près
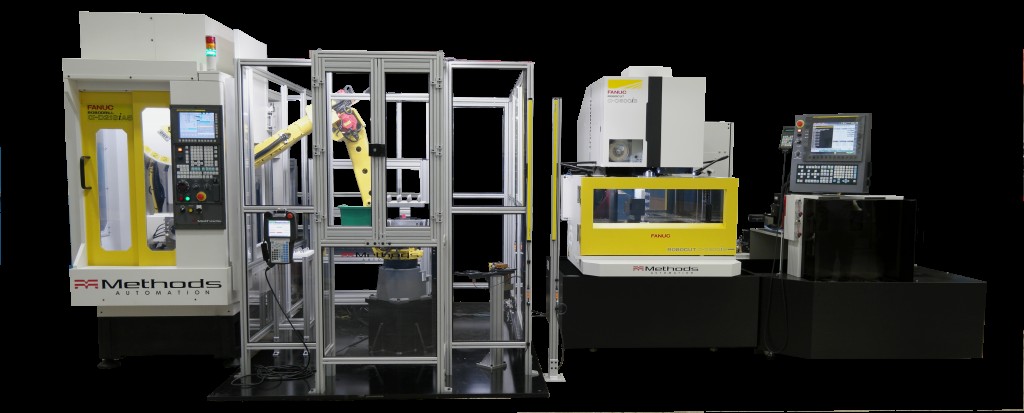
Lorsque la technologie proposée par un constructeur de machines-outils s'étend à des processus autrement sans rapport, l'automatisation peut fournir le lien productif inattendu. Methods Machine Tools Inc. (Sudbury, MA), un fournisseur de machines-outils, de technologie d'impression 3D et d'automatisation, a fait un « saut quantique » en combinant les processus pour augmenter la production dans la fabrication 3D. La cellule d'automatisation combine la fabrication additive avec la robotique et les processus soustractifs dans le but de fournir un post-traitement pour une production de pièces 3D finies rapide et très efficace.
Le 20 pieds. (6-m) La cellule de méthodes comprend une station d'alimentation de produits imprimés en 3D, qui transporte les pièces 3D sur des plaques de construction dans un FANUC C600 EDM qui effectue une coupe pour séparer partiellement les pièces des plaques de construction. Dans la station suivante, un robot FANUC extrait les plaques des pièces imprimées et transfère les pièces à un FANUC RoboDrill pour une opération d'usinage finale. Les Robodrills sont particulièrement appréciés dans les environnements d'atelier pour leur empreinte d'automatisation autonome et compacte. Conçue pour la fabrication en continu, la cellule réduit le temps global de réalisation des pièces, de l'impression 3D au post-traitement final, quadruplant le débit total des pièces tout en éliminant le travail manuel. Le partenaire d'impression 3D de Methods Machine est 3D Systems Corp. (Rock Hill, SC), à l'origine de l'impression 3D.
La fabrication intelligente signifie la connectivité IIoT
Deux constructeurs de machines-outils, Mazak Corp. (Florence, KY) et Murata Machinery USA Inc. (Charlotte, NC), ont collaboré pour développer un système de fabrication intelligent en combinant l'usinage, l'automatisation et les technologies intelligentes de Mazak avec le stockage automatisé haute densité Muratec et système de récupération. Le SMS Mazatec (système de fabrication intelligent) qui en résulte offre une fabrication sans surveillance et sans éclairage et un rendement élevé ainsi qu'une connectivité IIoT.
Le Mazatec SMS associe plusieurs centres d'usinage horizontaux et/ou machines multitâches Mazak avec un système de type stockeur orienté verticalement Muratec qui comprend des palettes, un godet de matériau et une grue de stockage à grande vitesse. Pour répondre aux besoins spécifiques de production et d'espace au sol de chaque fabricant, le système modulaire peut avoir jusqu'à 150 stockeurs (de différentes tailles) dans une configuration à six niveaux qui augmente considérablement l'efficacité de l'espace.
La technologie SmartBox IIoT de Mazak et le logiciel de gestion de production Smooth PMC sont des composants clés du SMS. Le système automatisé de Muratec contrôle toutes les interconnexions et se synchronise avec l'hôte ERP/MRP et le MES d'un fabricant. En conséquence, le Mazatec SMS est conçu pour devenir une solution d'usine intelligente pour le contrôle, la surveillance et l'optimisation des processus afin de produire une variété de pièces, même en petits lots, avec une grande efficacité. Le Mazatec SMS peut intégrer différentes tailles et types de machines-outils dans le même système de fabrication automatisé. L'équipement périphérique du Mazatec SMS comprend des stations individuelles pour le chargement et le centrage, le chargement par inclinaison, le levage et l'abaissement du chargement, la configuration du travail et le lavage des pièces. En plus de maintenir les machines-outils alimentées en travail, la grue de stockage du système gère l'entrée globale Mazatec SMS des pièces brutes et la sortie des pièces finies.
L'automatisation dépend du logiciel, focus IIoT
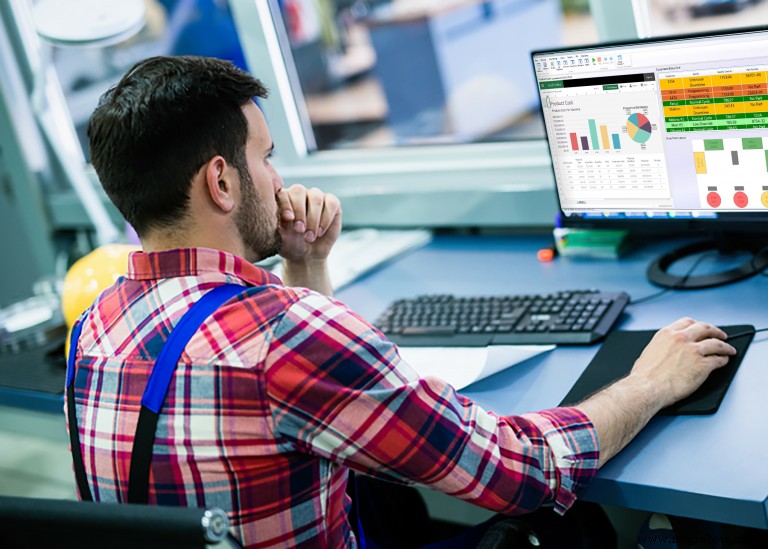
Shop Floor Automations (SFA ; La Mesa, CA) est spécialisé dans les logiciels d'automatisation de la fabrication qui fournissent aux ateliers la surveillance des machines, la mise en réseau CNC (logiciel DNC), le suivi des outils et la gestion des données de production. « Nos technologies avancées fonctionnent avec des protocoles tels que MTConnect, OPC UA, Okuma Thinc, Modbus et FANUC FOCAS », a déclaré Guy Barrow, directeur de compte. "Nos solutions sont efficaces pour les ateliers d'usinage CNC, les ateliers de fabrication, les ateliers de fabrication de moules et tout atelier lié au processus de fabrication. Les ateliers comprennent ceux qui fabriquent [des volumes élevés de pièces aérospatiales, de pièces médicales, d'armes à feu et de pièces automobiles, ainsi que des ateliers de production/travail combinés."
Selon Barrow, les clients de SFA souhaitent éliminer les anciens supports dans l'atelier sans remplacer leurs machines. Ils passent au sans fil et remplacent les lecteurs de disquettes. « Alors que les transferts de programmes et le contrôle des révisions CNC sont nécessaires, je dirais que la surveillance des machines est très appréciée pour nous en ce moment. L'efficacité de la machine est très importante pour les clients. Nous avons des ingénieurs sur place pour personnaliser les solutions qui répondent aux besoins des préoccupations de production du client. Les magasins veulent investir dans les normes de l'industrie 4.0 et de l'IIoT, ce qui a un effet positif sur notre gamme de produits. Nous testons toujours de nouvelles solutions pour résoudre les problèmes des clients en matière de méthodes alternatives de communication/gestion de transfert de programmes, d'augmentation de l'utilisation des machines, de contrôle des révisions, de suppression du papier et d'une meilleure préparation des audits. Cela les aide également à atteindre d'autres objectifs, tels que la certification ISO, la fabrication en continu et l'intégration avec d'autres solutions, comme le logiciel ERP."
Automatisation à petite échelle avec de grandes capacités
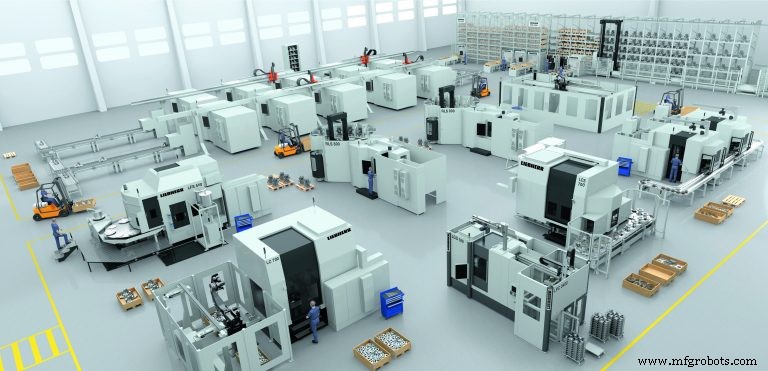
Une combinaison de centres d'usinage avec des systèmes de manutention de palettes s'est avérée bonne pour un système d'automatisation pour les petites séries jusqu'à des tailles de lot d'un seul. C'est pourquoi Liebherr Automation Systems Co. (Kempten, Allemagne et Saline, MI) a élargi son offre de produits d'automatisation avec le PHS Allround. Les objectifs du système d'automatisation intelligent sont une plus grande efficacité et un fonctionnement simple indépendamment de la taille et du poids de la pièce. Le système transfère le réglage des pièces de la machine vers un poste de réglage séparé et stocke les pièces prémontées dans une zone de stockage intermédiaire. Les pièces pré-montées stockées dans le système compensent les temps de fonctionnement courts et longs de la machine et permettent des équipes avec très peu ou même pas de main-d'œuvre, ce qui permet d'optimiser les prix unitaires jusqu'à 20 %.
Liebherr a développé la classe compacte PHS Allround pour les utilisateurs universels. Selon l'entreprise, le PHS Allround comble l'écart entre la solution de système de chargement rotatif d'entrée de gamme RLS de Liebherr et le système de manutention de palettes PHS Pro configurable individuellement. Le système de manutention de palettes PHS Allround permet à un grand nombre d'utilisateurs de passer à une production flexible en combinaison avec des centres d'usinage à quatre et cinq axes. Le nouveau concept modulaire en trois classes de poids pour des charges jusqu'à trois tonnes est flexible et peut être configuré et étendu individuellement. Cela correspond à des tailles de palettes de 500 x 500 mm à 1000 x 1000 mm.
L'automatisation personnalisée cible les opérations secondaires pour la cellule de fabrication de pièces d'extension de canon AR-15
Hydromat, un nom synonyme de production à haut volume dans l'atelier, a conçu et construit une cellule en cours de fabrication personnalisée pour éliminer la manipulation supplémentaire et les opérations secondaires pour une pièce d'extension de canon pour le populaire fusil de style AR-15. Auparavant, cette pièce aurait été produite sur plusieurs machines.
La solution a été fournie avec la technologie de machine EPIC d'Hydromat avec des processus d'automatisation et d'usinage supplémentaires. L'équipe d'ingénieurs d'Hydromat a mis au point un processus qui ferait le travail sans aucune opération en dehors de la cellule, du stock de barres brutes à la pièce terminée.
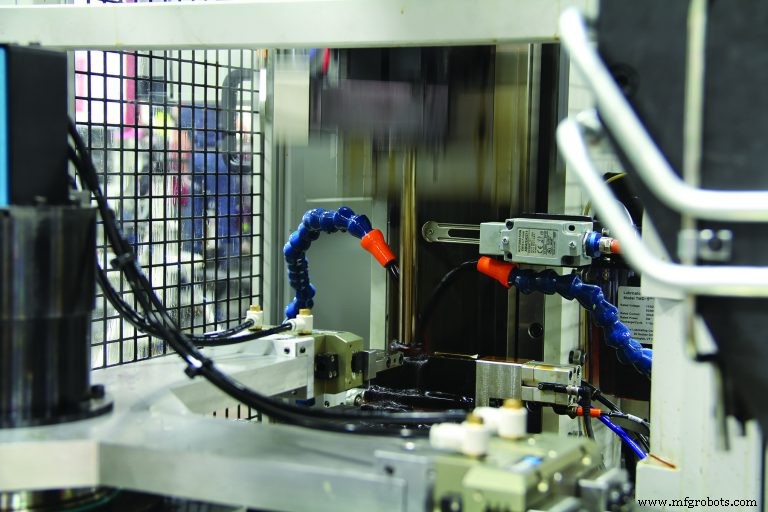
Les ingénieurs d'Hydromat ont proposé un processus de cellule de production Barrel Extension OP 10/20/30. Cette solution comprend une sortie de la machine Hydromat EPIC vers une cellule de processus de transfert à quatre stations de brochage/pièce/ébavurage Op 20 intégrée sur mesure avant de retourner à la machine Hydromat pour l'achèvement de la pièce Op 30. Au cours du processus d'usinage, la pièce est retirée de la machine, brochée dans une cellule séparée, puis renvoyée au processus de transfert rotatif pour être finie. La machine de transfert rotative EPIC 32/45-16 comprend une intégration complète avec l'automatisation du robot et une cellule Op 20.
L'OP 10 commence par un ravitailleur de barres en faisceau qui alimente la barre dans une pince et la coupe au premier poste. L'ébauche de pièce est déplacée des stations deux à huit avec des processus d'usinage spécifiques à chacune pour les caractéristiques du premier côté de la pièce. Au poste 9 de la machine EPIC, la pièce est extraite avec le premier robot FANUC de la pince et placée en position ouverte sur le plateau d'alimentation de la cellule de traitement Op 20. Le deuxième robot saisit la pièce avec l'une des doubles mâchoires Schunk et la place dans la mâchoire à la première position de la table dans la cellule.
Après vérification laser de la position, la pièce est transférée au deuxième poste. La pièce est extraite de la mâchoire par un système de transfert pneumatique et placée dans la position de brochage où la brocheuse fait son travail.
Ty Miles Inc. (Westchester, IL) a fourni la machine à brocher et l'outillage pour l'opération. Une fois le brochage terminé, le système de transfert pneumatique repositionne la pièce dans la mâchoire avant qu'elle ne soit acheminée vers la troisième position pour la frappe.
La pièce est ensuite transférée au quatrième poste pour une dernière étape d'ébavurage avant de revenir au premier poste pour être déchargée et placée en position ouverte dans le bac de déchargement. De cette position, la pièce est renvoyée à la machine Hydromat EPIC pour Op 30 dans les stations 9H à 16H pour l'usinage des caractéristiques sur le deuxième côté de la pièce. Une fois terminé, un autre robot FANUC extrait la pièce d'extension de canon terminée de la pince et la place sur un tapis roulant pour l'enlèvement. Avec un temps de cycle de 15,0 secondes, le processus produit 240 pièces par heure à partir du stock de barres jusqu'à l'achèvement de l'usinage requis de la pièce. Après le traitement thermique, un processus de meulage prépare la pièce pour le marché.
Système de contrôle d'automatisation
- L'atelier de moulage automatisé est là ; Êtes-vous prêt ?
- Le logiciel B&R utilise mieux le potentiel des robots
- L'atelier d'usinage CNC :Un guide complet
- La machine marketing :comment la technologie peut stimuler le succès des fabricants
- L'avenir des tests :automatisation et robots collaboratifs
- L'automatisation et les robots vont-ils changer le monde ?
- Quel est l'avenir de l'automatisation ?
- La machine suisse dans l'atelier d'usinage d'aujourd'hui
- Un tournant pour l'automatisation robotique