Spécialiste des applications :fusées imprimées en 3D et l'avenir de la fabrication d'engins spatiaux
L'impression 3D est en passe de devenir une technologie passionnante pour la fabrication d'engins spatiaux, et de fusées en particulier. Les startups et les fabricants établis adoptent l'impression 3D pour créer des composants de fusée avec une conception et des performances améliorées à moindre coût et avec des délais d'exécution plus rapides.
Cette semaine, nous continuons notre série Application Spotlight en examinant les avantages de l'impression 3D pour des pièces de fusée, voire des fusées entières.
Regardez les autres applications couvertes dans cette série :
Impression 3D pour échangeurs de chaleur
Impression 3D pour roulements
Impression 3D pour la fabrication de vélos
Impression 3D pour la dentisterie numérique et la fabrication d'aligneurs transparents
Impression 3D pour implants médicaux
Impression 3D pour la fabrication de chaussures
Impression 3D pour composants électroniques
Impression 3D dans l'industrie ferroviaire
Lunettes imprimées en 3D
Impression 3D pour la production de pièces finies
Impression 3D pour supports
Impression 3D pour pièces de turbine
Comment l'impression 3D permet des composants hydrauliques plus performants
Comment l'impression 3D soutient l'innovation dans l'industrie de l'énergie nucléaire
Pourquoi l'impression 3D est-elle utilisée pour fabriquer des composants de fusée ?
La course aux satellites dans l'espace est de plus en plus féroce.
Pour cette raison, les fabricants d'engins spatiaux sont confrontés au défi d'accélérer le développement et la production de fusées, tout en réduisant les coûts et en augmentant l'efficacité.
Cependant, dans la fabrication de fusées conventionnelles, les cycles de prototypage et les étapes de production multiples rendent le processus long et très coûteux.
Par exemple, cela peut prendre entre 10 et 14 mois pour fabriquer une chambre de combustion conventionnelle (un composant structurel de fusée où un mélange de carburant et d'air comprimé est enflammé).
Pour produire ces chambres de combustion, les fabricants doivent couler et forger des composants séparés. Les canaux de refroidissement doivent alors être usinés autour la chambre — un processus très long, laborieux et coûteux.
Face à ces enjeux, les grands constructeurs de fusées commencent déjà à produire des chambres de combustion avec fabrication additive. Une fois conçue, une chambre de combustion imprimée en 3D peut être fabriquée en quelques semaines, permettant aux fabricants de réduire considérablement les délais et les coûts de production.
La fabrication de matériel destiné à être lancé dans l'espace requiert des performances et une précision exceptionnelles. Pour assurer un lancement réussi, chaque partie doit fonctionner ensemble de manière transparente.
Avec la fabrication traditionnelle, les ingénieurs sont confrontés à des limites lors de la conception de pièces de fusée très complexes. L'impression 3D en métal permet aux ingénieurs de surmonter certaines des limitations des processus traditionnels et de développer plus rapidement des composants de fusée plus complexes.
Les technologies d'impression 3D utilisées pour fabriquer des composants de fusée
À ce jour, les entreprises d'engins spatiaux ont, dans l'ensemble, adopté des technologies d'impression 3D métalliques à base de laser telles que la fusion sélective au laser (SLM) pour produire des pièces de moteur de fusée telles que des chambres de combustion, des injecteurs, des buses, des pompes et des soupapes. SLM applique un laser puissant et affiné sur une couche de poudre métallique, fusionnant les particules métalliques entre elles. Le processus est répété sur des centaines de couches jusqu'à ce qu'une pièce soit créée.
SLM offre une haute précision (peut imprimer des couches aussi fines que 20 microns) et est optimisé pour fonctionner avec une large gamme de métaux haute performance , du titane aux alliages de nickel. Cette technologie est généralement utilisée pour les petites pièces.
En plus de la SLM, certaines sociétés d'engins spatiaux utilisent la technologie de dépôt direct d'énergie (DED) pour créer des composants de grande taille. Les imprimantes 3D DED fonctionnent en faisant fondre un matériau métallique avec un laser ou un faisceau d'électrons lorsqu'il est déposé à travers une buse sur la plate-forme de construction.
Généralement, les machines DED ont des taux de dépôt de matériaux élevés et peuvent travailler avec des matériaux métalliques sous forme de poudre ou de fil, créant des pièces très denses avec des formes proches du filet.
Les avantages de l'impression 3D pour les fusées
La capacité d'itération rapidement
L'un des plus grands avantages de l'impression 3D pour les pièces de fusée est la possibilité d'itérer les conceptions très rapidement.
“Avec l'additif, vous pouvez parcourir cinq itérations d'une conception avant même d'obtenir les premières par une méthode traditionnelle, et les cinq ensemble coûteront probablement moins d'une itération traditionnelle ", déclare Scott Killian, directeur du développement commercial aérospatial pour EOS Amérique du Nord dans une interview avec engineering.com.
Une imprimante 3D peut créer des pièces de fusée directement à partir d'un fichier de conception sans avoir besoin d'outillage. Si une pièce nécessite des modifications, les ingénieurs peuvent simplement apporter des modifications à un fichier CAO d'origine et créer une nouvelle conception modifiée beaucoup plus rapidement que les processus traditionnels ne le permettraient.
Flexibilité de conception
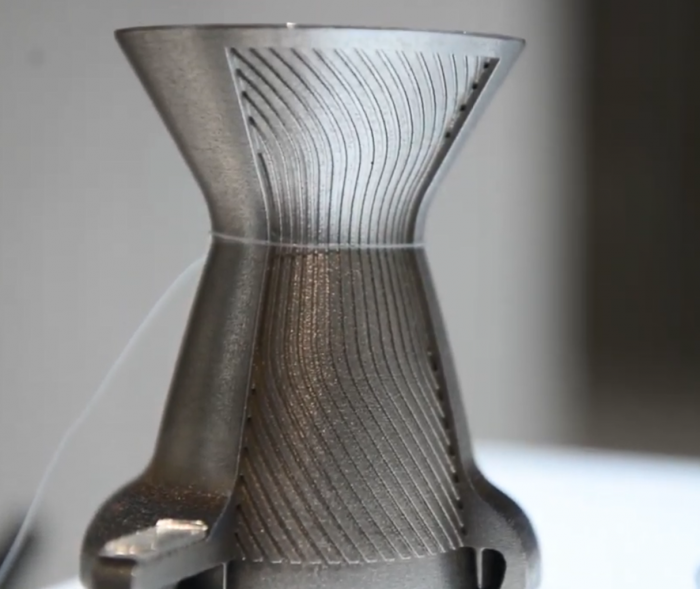
Sans dépendre de l'outillage, l'impression 3D offre aux ingénieurs des engins spatiaux la flexibilité de créer des formes et des géométries complexes impossibles à réaliser avec les processus conventionnels.
Pensez aux chambres de combustion. Composant essentiel de tous les moteurs de fusée, une chambre de combustion doit résister à un environnement hautement pressurisé et à des températures pouvant atteindre 5 000 °F (2760 °C), car les propulseurs se mélangent et s'enflamment à l'intérieur.
Pour fonctionner efficacement, ce composant nécessite des canaux de refroidissement internes complexes qui sont remplis de gaz refroidis à moins de 100 °F (38 °C) au-dessus du zéro absolu.
Traditionnellement, ces canaux de refroidissement sont très compliqués et coûteux à développer. Ils nécessitent un outillage spécialisé pour usiner des canaux de refroidissement CNC et braser la paroi extérieure de la chambre. Ces segments séparés doivent ensuite être soudés en une seule pièce.
L'impression 3D, quant à elle, rationalise le processus en permettant de produire directement l'ensemble de la chambre. De plus, il permet des conceptions de canaux de refroidissement complexes comme le montre l'image ci-dessus, qui seraient impossibles à usiner.
Pièces de fusée moins chères
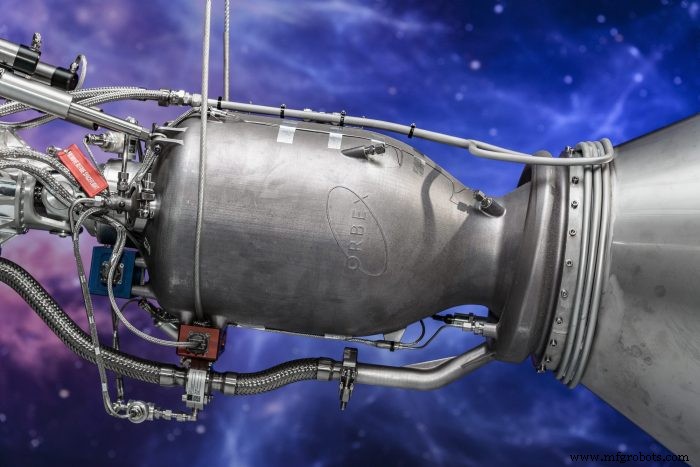
Les moteurs sont la partie la plus chère d'un véhicule de lancement (un véhicule propulsé par fusée utilisé pour lancer des satellites ou d'autres engins spatiaux dans l'espace). Le coût d'un moteur peut représenter jusqu'à 40 % du coût de l'ensemble de la fusée. En utilisant l'impression 3D pour créer des pièces de moteur cruciales, les fabricants de fusées peuvent réduire considérablement les coûts globaux d'un vaisseau spatial.
L'impression 3D permet aux ingénieurs de rationaliser la production de composants de moteurs de fusée, en contournant un certain nombre d'étapes de production. Moins il y a d'étapes, moins d'équipement et de réglages sont nécessaires, ce qui se traduit finalement par des coûts de production inférieurs.
De plus, l'automatisation du processus de production avec l'impression 3D signifie que la plupart des coûts de main-d'œuvre sont éliminés de l'équation .
Par exemple, la société aérospatiale britannique Orbex a utilisé la technologie SLM et un alliage de nickel pour imprimer en 3D un moteur pour son lanceur Prime. L'impression 3D en métal a permis à Orbex de réduire son délai d'exécution de 90 % et de réduire ses coûts de 50 % par rapport aux processus de production plus traditionnels, tels que l'usinage CNC.
L'entreprise spatiale commerciale privée d'Elon Musk, SpaceX, a a également adopté l'impression 3D pour réduire les coûts et offrir une plus grande flexibilité dans le processus de production de ses propulseurs Draco et SuperDraco. La société utilise une imprimante 3D en métal basée sur SLM pour créer des chambres de combustion en Inconel.
Selon Musk, « grâce à l'impression 3D, des pièces de moteur robustes et hautes performances peuvent être créées à une fraction de le coût et le temps des méthodes de fabrication traditionnelles . "
Assemblage simplifié
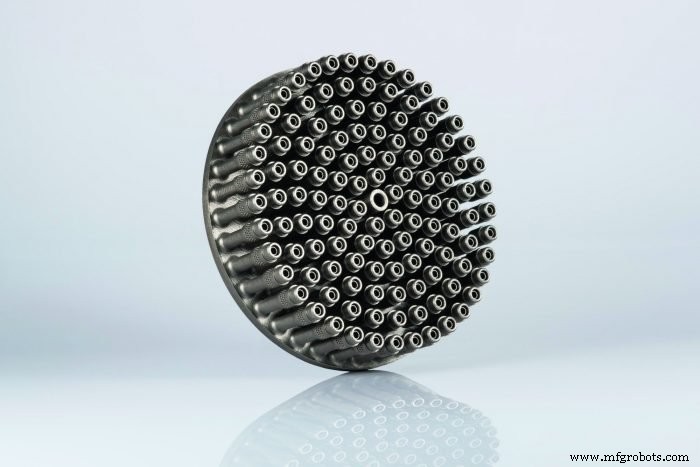
De plus, les ingénieurs peuvent également réduire considérablement le nombre d'étapes du processus d'assemblage. Ceci peut être réalisé en imprimant en 3D des pièces de fusée fabriquées à partir de plusieurs composants en une seule pièce.
Prenons l'exemple d'une tête d'injecteur. Une tête d'injecteur est l'un des éléments centraux d'un module de propulsion, qui force le mélange de carburant dans la chambre de combustion.
Traditionnellement, les têtes d'injecteurs sont constituées de dizaines voire de centaines de pièces qu'il faut usiner et souder entre elles. En revanche, l'impression 3D peut produire de tels composants en une seule pièce.
Des chercheurs du Centre aérospatial allemand (DLR) ont utilisé l'impression 3D pour créer une nouvelle conception de tête d'injecteur pour un petit lanceur de satellite.
Le résultat est une pièce monolithique 10% plus légère. En réduisant le nombre de composants de 30 à un seul, l'équipe de recherche a également éliminé les points de défaillance connus sur les sites de fixation. Enfin, la nouvelle conception optimisée améliorerait les performances de la pièce et prolongerait sa durée de vie.
De même, le spécialiste de l'impression 3D métal, EOS, a simplifié l'assemblage d'une tête d'injecteur pour son lanceur Ariane 6 , développé par ArianeGroup, joint-venture entre Airbus Group et Safran.
L'utilisation de la technologie SLM a permis à l'équipe de reconcevoir une tête d'injecteur en un seul composant au lieu des 248 composants requis pour une conception traditionnelle. Parmi les autres avantages, citons une réduction des coûts de 50 % et des délais de livraison trois fois inférieurs.
Exemples de pièces de fusée imprimées en 3D
Moteur Rutherford imprimé en 3D de Rocket Lab
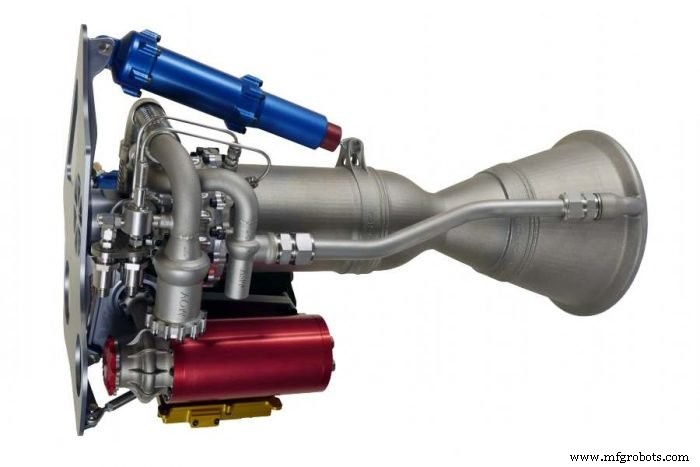
En juillet, Rocket Lab, une société aérospatiale basée en Californie, a achevé le 100e moteur de fusée Rutherford imprimé en 3D. La société utilise l'impression 3D pour tous ses composants de moteur principaux (y compris les chambres de combustion, les injecteurs, les pompes et les soupapes de propulsion principales) depuis 2013.
Neuf moteurs à propergol liquide Rutherford alimentent la fusée Electron de Rocket Lab, qui est fabriqué à partir de composites et peut transporter jusqu'à 225 kg de charge utile. Les pièces du moteur sont imprimées en 3D à l'aide de la technologie Electron Beam Melting (EBM), censée produire des pièces de moteur moins chères que les processus conventionnels.
Récemment, Rocket Lab a une nouvelle fois prouvé la fiabilité des moteurs imprimés en 3D, en lançant avec succès quatre satellites en orbite avec son lanceur Electron.
D'ici 2020, la société prévoit d'effectuer deux lancements par mois. Avec l'impression 3D permettant à Rocket Lab de produire un moteur en quelques jours au lieu de quelques mois, l'équipe est bien placée pour mettre ce plan en action.
Impression 3D de fusées entières
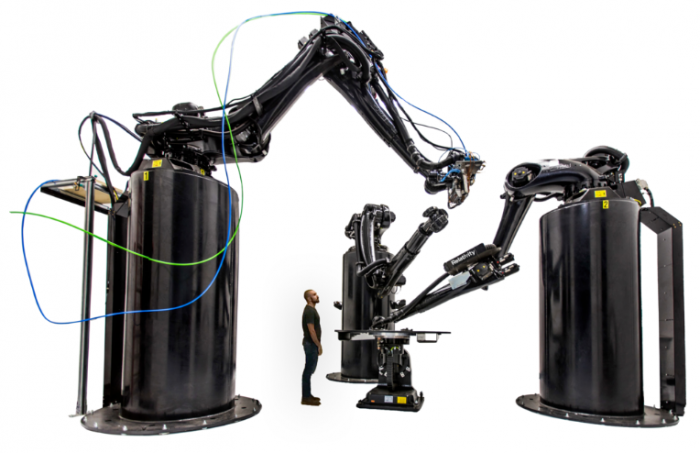
La startup californienne Relativity Space veut aller au-delà des moteurs de fusée imprimés en 3D. L'entreprise développe une fusée terrienne, dont environ 95% des composants seront imprimés en 3D.
Pour y parvenir, la société a développé Stargate, l'une des plus grandes imprimantes 3D métal DED au monde. Avec la possibilité de créer des composants aussi grands que 2,7 m (9 pi) de diamètre et environ 4,5 m (15 pi) de haut, Stargate imprimera tous les réservoirs de carburant et autres composants de grande fusée.
En utilisant l'impression 3D pour fabriquer la quasi-totalité d'une fusée, Relativity Space espère réduire considérablement le poids de la fusée, ce qui peut potentiellement réduire le coût de lancement, tout en augmentant la charge utile.
L'impression 3D réduira également le nombre de pièces à assembler, augmentant ainsi la résistance et la stabilité de la fusée.
Pour les pièces plus petites, l'entreprise utilise la technologie SLM.
Selon Relativity Space, l'impression 3D lui permet de modifier rapidement les conceptions et d'utiliser moins d'outils et de main-d'œuvre que ce qui serait normalement requis pour le développement de fusées. Au final, cela pourrait permettre à Relativity Space de passer de la matière première à une fusée prête à voler en moins de deux mois.
Relativity Space est actuellement la seule entreprise à appliquer les technologies d'impression 3D pour une fusée entière. Son concept de fusée imprimée en 3D sera-t-il un succès ? La réponse résidera finalement dans les tests et le lancement. Le lancement test de la fusée Terran imprimée en 3D est prévu fin 2020.
L'avenir de l'impression 3D dans l'aérospatiale
L'impression 3D a révolutionné la façon dont les fusées et les pièces de moteur de fusée sont conçues et produites. Les principes fondamentaux de la conception des fusées n'ont peut-être pas changé, mais l'impression 3D métallique a ouvert de nouvelles façons d'améliorer les performances des fusées, offrant une plus grande liberté de conception.
La technologie peut aider à réduire le coût de fabrication des moteurs, l'un des composants de fusée les plus chers. Ceci est réalisé en réduisant le nombre d'étapes de production et en permettant des itérations de conception plus fréquentes.
Bien que les capacités de l'impression 3D au-delà des pièces de moteur restent à tester, le potentiel de la technologie pour l'impression 3D entièrement fusées à l'avenir est vraiment excitant.
L'impression 3D est devenue une technologie de fabrication clé pour la production d'engins spatiaux, permettant aux ingénieurs d'innover plus rapidement et de créer la prochaine génération de voyages spatiaux.
Dans notre prochain article, nous aborderons l'impression 3D dans l'industrie de la chaussure. Restez à l'écoute !
impression en 3D
- Conception générative et impression 3D :la fabrication de demain
- La robotique et l'avenir de la production et du travail
- Les avantages du prototypage rapide et de l'impression 3D dans la fabrication
- Automatisation industrielle :un bref historique des applications de fabrication, l'état actuel et les perspectives d'avenir
- L'avenir des machines industrielles en 2020 et au-delà
- Quel rôle la robotique et l'impression 3D joueront-elles dans l'avenir de la fabrication ?
- L'automatisation et l'avenir de la fabrication numérique ?
- L'avenir de l'impression 3D dans la fabrication
- L'impression 3D est-elle l'avenir de la fabrication ?