5 façons dont l'impression 3D complète la fabrication traditionnelle
Il est prévu que l'impression 3D remplacera les technologies de fabrication traditionnelles. Cependant, la véritable puissance de la technologie peut résider non pas dans la concurrence, mais dans le complément et l'augmentation des méthodes de fabrication conventionnelles.
Pour étayer cette affirmation, nous explorons ci-dessous 5 façons clés de la façon dont l'impression 3D peut prendre en charge la fabrication traditionnelle.
1. Impression 3D de moules d'injection plus performants
Le moulage par injection implique le processus de fusion et d'injection de matière plastique dans un outil de moulage spécial, façonné selon l'objet souhaité. Lorsque le plastique durcit, il prend la forme de la cavité du moule. Le moulage par injection est le meilleur moyen de produire en série des produits et des pièces très précis et complexes.
Cependant, le processus présente également certains défis. Par exemple, les pièces moulées par injection sont refroidies en construisant des canaux - essentiellement des passages situés près de la surface du moule - à travers les moules. Ces canaux sont généralement des lignes droites, ce qui peut parfois entraîner un refroidissement inégal, augmentant le risque de déformation de la pièce.
Un refroidissement efficace peut être obtenu avec des canaux de refroidissement conformes, qui épousent la forme de la pièce. Cependant, ces types de canaux sont difficiles à produire en utilisant des méthodes conventionnelles, faisant de l'impression 3D une alternative intéressante pour la création de moules d'injection.
La création de moules avec des canaux de refroidissement conformes contribue non seulement à augmenter la qualité des pièces moulées, mais contribue également à réduire considérablement le temps de refroidissement.
L'impression 3D permet d'optimiser la ligne de moulage par injection
Un exemple est Alfred Kärcher GmbH &Co. KG, une entreprise qui vend chaque année des millions de ses nettoyeurs haute pression K2 dans le monde. En essayant de répondre à une telle demande, l'entreprise a été confrontée à un goulot d'étranglement dans la production, ce qui l'a obligée à augmenter la production de boîtiers de lave-glace.
Au lieu d'acheter plus de machines de moulage par injection, Kärcher a commencé à chercher des moyens d'augmenter la productivité des machines existantes. L'entreprise a trouvé la solution dans l'impression 3D métal.
Kärcher s'est tourné vers LBC Engineering, filiale de Renishaw GmbH, qui a découvert que la durée du cycle de moulage était affectée par l'inefficacité du processus de refroidissement. Les moules de tubage comportaient des systèmes de refroidissement traditionnels, percés en lignes droites, créant des points chauds qui augmentaient le temps de cycle.
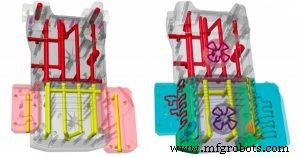
LBC Engineering a modifié la conception du moule en créant deux noyaux imprimés en 3D pour fournir un refroidissement conforme aux points chauds identifiés.
Les canaux de refroidissement conformes imprimés en 3D ont permis de réduire la température des parois des moules de 100 °C à 70 °C, réduisant ainsi le temps de refroidissement de 22 à 10 secondes, soit une réduction de 55 %.
Avec quelques ajustements des composants périphériques, tels que le système d'alimentation et de manutention du matériau, le temps de cycle pour les boyaux est passé de 52 à 37 secondes. L'impression 3D a fourni la part du lion de cette réduction, permettant à Kärcher d'augmenter la productivité de sa ligne et d'atteindre les objectifs de production de boyaux.
Dans un autre exemple, le professionnel du moulage par injection, Pat Zaffino, a développé une technologie de dépôt robotique multicouche qui imprime en 3D des canaux de refroidissement conformes sur la surface des moules d'injection.
Plus tôt cette année, Zaffino a lancé une nouvelle société, Conformal Cooling Solutions Inc. (CCS), pour promouvoir les avantages de l'utilisation de canaux de refroidissement conformes.
'Créer des canaux de refroidissement conformes qui suivent la forme de la cavité et du noyau favorise l'uniformité de la température dans les matières plastiques moulées, et les mouleurs qui utilisent cette technologie obtiennent des résultats frappants :des temps de cycle raccourcis, une meilleure qualité des pièces en plastique et, surtout, des réductions de coûts", a-t-il déclaré. dans une interview avec canplastics.com.
Comme la technologie devient moins chère et plus facile à adopter, les moules avec des canaux de refroidissement conformes imprimés en 3D pourraient finalement devenir une nouvelle norme dans l'industrie.
2. Modèles d'impression 3D pour la coulée de précision
Le moulage à la cire perdue utilise des modèles en cire jetables et des coques en céramique pour créer des conceptions de pièces complexes et détaillées. Traditionnellement, ces motifs sont moulés par injection. Cependant, le coût des moules d'injection peut atteindre plusieurs milliers de dollars, avec des délais allant d'une à quatre semaines. Cela rend le processus prohibitif pour les personnes qui pourraient ne pas avoir autant de capital ou avoir des délais courts pour livrer des pièces.
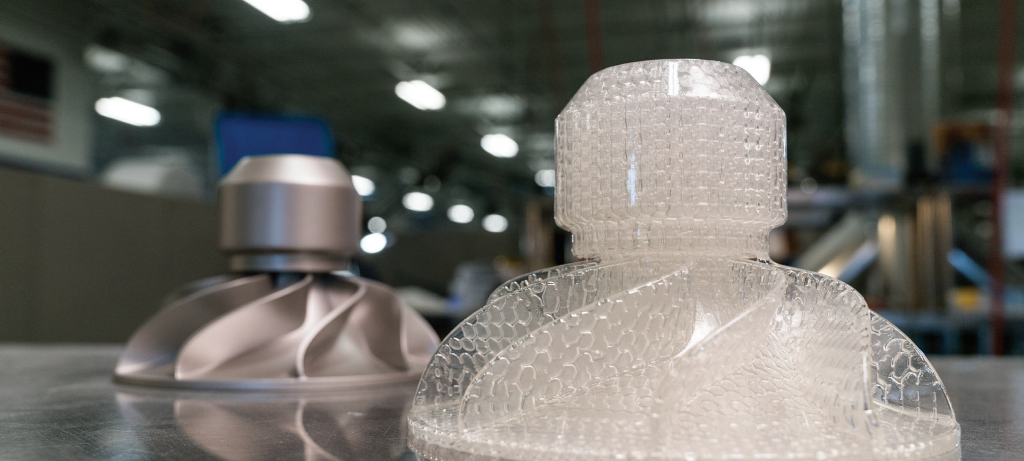
Pour cette raison, les entreprises peuvent choisir d'imprimer des modèles en 3D dans un matériau adapté à la coulée de précision. De nombreux fabricants d'imprimantes 3D ont développé des matériaux imprimables en 3D spécifiquement pour le moulage, notamment de la cire, des résines coulables et certains thermoplastiques, à base de PLA et d'ABS.
Ces matériaux sont généralement utilisés avec la stéréolithographie (résines) et le FDM ( plastiques), créant des modèles très précis avec d'excellentes caractéristiques d'épuisement.
Un autre avantage de cette approche est le risque relativement faible qu'implique son essai. Les motifs peuvent être imprimés en 3D à l'aide d'imprimantes 3D de bureau professionnelles, qui coûtent moins de 5 000 $, une fraction du coût des équipements d'impression 3D industriels plus chers.
Accélération des délais de fabrication des moulages grâce à l'impression 3D
Les modèles de moulage de précision imprimés en 3D sont de plus en plus utilisés pour créer des bijoux personnalisés avec des conceptions complexes et des délais de livraison plus courts. Par exemple, l'entreprise de joaillerie canadienne Vowsmith, spécialisée dans les bagues personnalisées, a pu réduire de 50 % ses délais de production et de livraison en intégrant les imprimantes 3D à cire de 3D Systems dans son flux de travail. En une seule impression, l'entreprise a produit entre 35 et 40 modèles de bagues personnalisés, prêts à être coulés.
La technologie est également de plus en plus appliquée dans les fonderies, pour créer des modèles complexes pour un large éventail d'applications industrielles. Par exemple, Invest Cast, Inc. a récemment intégré la nouvelle solution de fonderie numérique de 3D Systems dans sa production de modèles.
La possibilité de fabriquer des pièces moulées finales sans outiller un moule a donné aux clients d'Invest Cast la liberté de tester plusieurs itérations rapidement et à moindre coût, leur permettant finalement d'arriver à de meilleures pièces finales.
Selon Invest Cast, l'imprimante 3D ProJet MJP 2500 IC de 3D Systems a réduit considérablement le temps du processus de moulage de précision . La technologie permet à l'entreprise de passer du modèle au métal en 2 à 5 jours, ce qui est inférieur au délai moyen d'environ 6 à 12 semaines avec les moules de moulage de précision.
3. Augmenter la productivité avec des outils de coupe imprimés en 3D
L'impression 3D peut être utilisée pour créer des outils de coupe - de petites plaquettes en carbure qui retirent de la matière du parcours d'outil programmé.
Certains matériaux hautes performances, tels que les aciers à très haute résistance, les alliages de titane et de nickel, peuvent être difficiles à usiner et entraîner une usure rapide de l'outil.
Les outils d'impression 3D avec des géométries personnalisées, dotés de canaux de refroidissement intégrés qui peuvent éliminer efficacement l'excès de chaleur généré près de la zone de coupe pendant l'usinage, peuvent augmenter la durée de vie et les performances de l'outil.
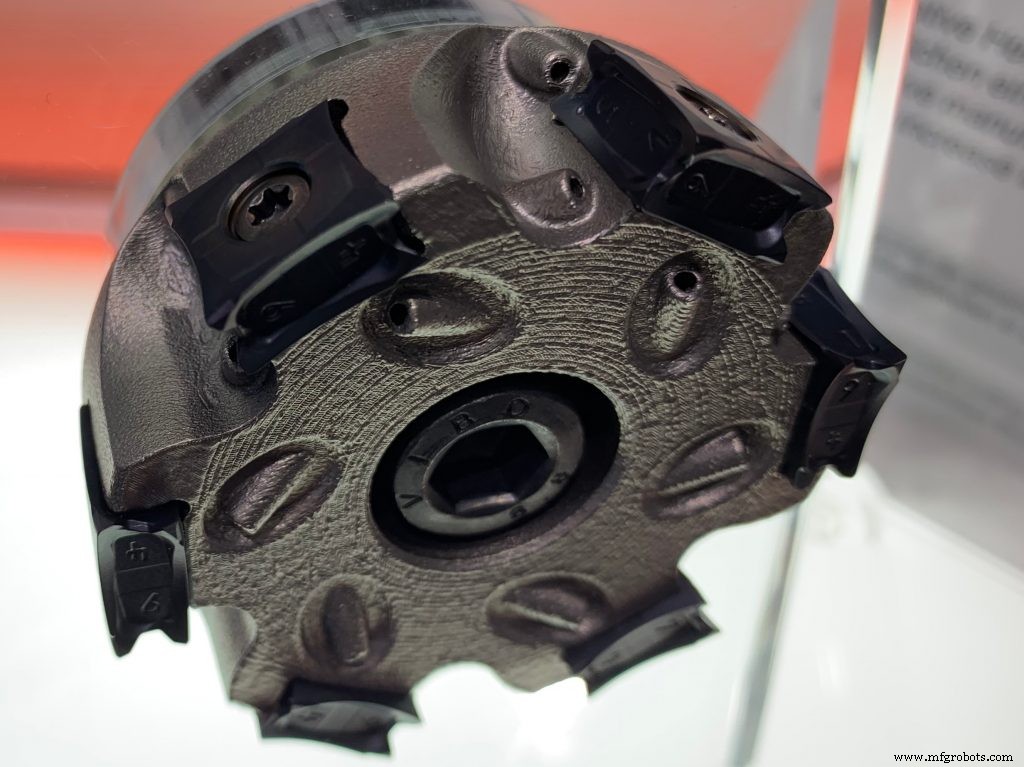
Le spécialiste des outils, LMT Tools Inc., a utilisé la technologie pour créer des passages de liquide de refroidissement internes dans un corps d'outil de fraisage, comportant auparavant des trous droits. La liberté de l'impression 3D de fournir des canaux incurvés permet à l'outil de fraisage de LMT de fournir le liquide de refroidissement précisément là où il est nécessaire. LMT affirme que la coupe d'essai a montré une amélioration de la durée de vie de l'outil de 50 % dans le fraisage du titane, grâce à ce changement de conception.
Komet Group augmente la productivité de ses outils grâce à l'impression 3D
L'un des principaux fournisseurs mondiaux d'outils de coupe de précision, le groupe Komet, applique également l'impression 3D métal à la fabrication d'outils.
En utilisant l'alliage d'aluminium et la technologie laser du spécialiste britannique Renishaw, Komet a pu introduire plus d'arêtes de coupe dans l'outil et optimiser sa géométrie pour augmenter la productivité de l'outil.
Par exemple, les ingénieurs ont optimisé les canaux d'arrosage de l'outil pour garantir que chaque arête de coupe est alimentée avec précision en liquide d'arrosage via un canal séparé. Grâce à ces améliorations de conception, le temps d'usinage par unité peut être réduit jusqu'à 50 %.
AM offre également la possibilité de réduire le poids des composants, car le matériau ne peut être utilisé que là où il est nécessaire pour la fonctionnalité optimale du composant. Il est également rapporté qu'il surpasse les méthodes de production conventionnelles, en termes de délai de livraison, pour tous les outils spéciaux ou expérimentaux nécessaires aux clients de Komet.
Impression 3D d'une tête de fraisage plus efficace
De plus, le fabricant suédois de systèmes d'outillage, Sandvik Coromant, a récemment introduit une nouvelle fraise avec une tête métallique imprimée en 3D. Une première pour l'entreprise, le composant marque un pas vers l'implication de l'entreprise dans l'impression 3D pour la production finale.
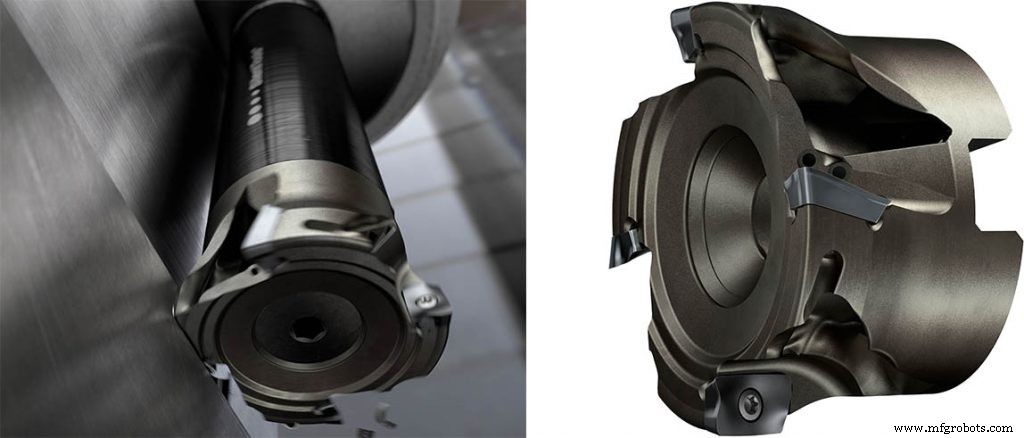
Le nouveau Lightweight CoroMill 390, produit par Sandvik Coromant, est une tête de fraisage du métal basée sur la conception du CoroMill 390. L'outil, produit à l'aide de la poudre Osprey en alliage de titane de marque Sandvik, a été spécialement développé pour surmonter les problèmes de vibration lors du fraisage des métaux avec de longs porte-à-faux.
De telles caractéristiques sont une exigence commune des composants utilisés dans les industries aérospatiale et pétrolière et gazière. Les cavités profondes dans une pièce usinée CNC peuvent être compromises par les vibrations, ce qui entraîne une production plus lente, une durée de vie plus courte et un mauvais état de surface. Lorsqu'il est utilisé en combinaison avec les adaptateurs de fraisage Silent Tools de la société, la société indique que l'outil imprimé en 3D peut augmenter la productivité d'usinage de 50 %.
4. Réparer l'outillage usé et endommagé
L'impression 3D peut non seulement être utilisée pour créer de nouveaux outils et moules, mais aussi pour réparer des outillages endommagés. Les entreprises de l'aérospatiale, de la construction navale et des biens industriels commencent à utiliser des procédés de FA, tels que le dépôt direct d'énergie (DED), pour remettre à neuf les composants dans leur forme d'origine.
Également connu sous le nom de revêtement laser, le DED utilise un laser pour générer un bain de soudure sur la surface du composant. Le matériau est ensuite ajouté au bain de fusion sous forme de poudre ou de fil. Les particules fondues fusionnent et se solidifient, tandis que la buse est manipulée pour ajouter la structure souhaitée au composant.
Plus tôt cette année, un consortium de 7 entreprises et organisations britanniques a lancé un projet de 1,2 million de livres sterling, appelé DigiTool , pour permettre la réparation à faible coût des outils et des matrices en utilisant les technologies de FA.
Avec l'impression 3D, les entreprises du secteur des outils et matrices peuvent surmonter les coûts de remplacement et de réparation des matrices, avec le potentiel d'accélérer le processus de maintenance. Cela aidera les entreprises à économiser sur les coûts et les matériaux, tout en améliorant simultanément leur durabilité avec moins de gaspillage.
Réparation plus rapide d'un insert de moule
La société allemande de fabrication d'outils et de moules, HWF, a utilisé l'impression 3D pour réparer un insert de moule. L'un des défis auxquels HWF a été confronté a été celui de construire une structure, mesurant 300 x 20 x 20 mm, sur un matériau de moule typique.
Dans le passé, des structures comme celle-ci étaient construites à l'aide d'un méthode de rechargement laser manuel alimenté par fil pour éviter les risques de fissures, de déformation et d'altération des propriétés métallurgiques. Cependant, le soudeur peut mettre entre 60 et 80 heures pour terminer la tâche.
Aujourd'hui, HWF utilise la technologie DED de OR Laser, qui lui permet de créer la même structure en appliquant des couches de 250 µm d'épaisseur, à un débit de 5000 mm³ par heure. Le temps de production peut donc être réduit à 24 heures.
Grâce à ce procédé, le matériau de base est également beaucoup moins affecté qu'auparavant, réduisant ainsi considérablement le risque de fissures et de contre-dépouille du matériau, souvent causés par les méthodes de réparation conventionnelles.
5. Gagner en flexibilité grâce aux processus hybrides
La combinaison de capacités additives et soustractives dans un système hybride est une autre façon dont la FA peut compléter la fabrication traditionnelle. Dans ce scénario, les technologies additives et soustractives peuvent ouvrir une gamme d'opportunités pour une fabrication améliorée et à guichet unique.
La fabrication hybride exploite les capacités les plus précieuses des deux technologies :la complexité géométrique de la FA et la haute précision des méthodes soustractives. Cela signifie qu'une pièce peut être créée et usinée de manière additive en une seule opération, accélérant ainsi le processus de production.
Plusieurs systèmes hybrides commerciaux sont maintenant disponibles sur le marché. Par exemple, DMG MORI combine DED avec une capacité CNC à cinq axes dans son système de fabrication hybride.
Pendant ce temps, Matsuura et Sodick ont adopté une approche différente, combinant la technologie Powder Bed Fusion (PBF) et la capacité CNC dans leurs systèmes de fabrication hybrides. Pour suivre la concurrence, DMG MORI a récemment répondu avec son propre système hybride PBF et CNC.
En plus d'un système hybride autonome, il est également possible de moderniser un centre d'usinage CNC existant avec la tête de dépôt laser à poudre Ambit d'Hybrid Manufacturing Technologies.
Les entreprises peuvent également ajouter une combinaison de capacités de dévidage de poudre et de fil à une machine CNC, avec la technologie 3D Hybrid. Cela permet à un système soustractif conventionnel d'être converti en un système de fabrication hybride avec un coût et un effort relativement minimes.
Bien que la promesse de la fabrication hybride soit captivante, nous commençons tout juste à apprendre comment cette technologie peut être appliqué de manière efficace et viable.
L'impression 3D comme technologie complémentaire
L'impression 3D peut devenir un atout précieux pour les industriels qui cherchent à optimiser leurs processus de fabrication traditionnels.
La technologie peut être utilisée pour produire des moules plus performants et des modèles de coulée complexes, ainsi qu'augmenter l'efficacité des outils d'usinage. De plus, les machines hybrides peuvent offrir aux entreprises une liberté et une flexibilité accrues dans la conception et la fabrication.
Par conséquent, au lieu de considérer la fabrication additive comme une technologie concurrente, les fabricants devraient l'adopter comme un autre outil dans la boîte à outils et profiter des avantages qu'elle offre.
impression en 3D
- 5 avantages de l'impression 3D dans la fabrication
- 4 façons dont l'impression 3D transforme l'industrie médicale
- 8 façons dont l'impression 3D industrielle transforme la fabrication
- 6 façons de réduire les coûts de fabrication grâce à l'impression 3D
- L'impression 3D est partout
- 5 façons dont l'impression 3D change l'industrie automobile
- Fabrication additive en médecine et en dentisterie
- L'avenir de l'impression 3D dans la fabrication
- L'impression 3D est-elle l'avenir de la fabrication ?