Arevo en 2018 :Industrialisation de la production de pièces imprimées en 3D en fibre continue
SOURCE pour toutes les images :Arevo.
CW couvre Arevo (Santa Clara, CA, États-Unis) depuis 2014. Connu pour son utilisation de polymères thermoplastiques haute performance, y compris le polyétheréthercétone (PEEK), le polyaryléthercétone (PAEK), le polyétherimide (PEI) et le sulfure de polyphénylène (PPS), la société était également un leader dans le développement de contrôle robotique en boucle fermée pour l'impression 3D , permettant le placement de la fibre dans la direction z et le long de courbes 3D. L'entreprise a une liste de nouveaux développements, y compris son procédé de dépôt d'énergie directe (DED) utilisant le chauffage au laser pour une vitesse de production 100 fois supérieure.
Nouveau PDG et financement de la série B
Jim Miller a rejoint Arevo en tant que PDG il y a trois mois. Il a été l'un des premiers employés d'Amazon et a passé huit ans chez Google, plus récemment en tant que vice-président des opérations mondiales. « En fait, j'ai passé la majeure partie de ma carrière à aider de jeunes entreprises à monter en puissance », déclare Miller, « j'étais enthousiasmé par l'approche d'Arevo en matière d'impression 3D de composites et j'y voyais une énorme opportunité de changer la façon dont le monde conçoit et fabrique des structures complexes dans une myriade de candidatures."
La société vient également de finaliser son financement de série B, levant 12,5 millions de dollars avec Asahi Glass Co. (AGC, Tokyo, Japon) en tête du tour. « Ils sont le plus grand producteur de verre automobile au monde », déclare Miller. « Ils ont de bonnes relations dans l'industrie automobile et voient une grande opportunité pour les nouvelles technologies composites dans les applications automobiles . " Les autres investisseurs incluent In-Q-Tel (Arlington, VA, États-Unis), Sumitomo Corporation (Tokyo, Japon) et Leslie Ventures. Miller dit que Sumitomo , l'un des plus grands conglomérats japonais et leader des technologies pétrolières et gazières, souhaite appliquer la technologie d'impression 3D d'Arevo à l'ensemble de ses activités industrielles , qui comprennent la construction, les transports, les infrastructures et l'énergie.
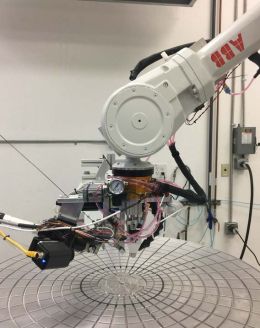
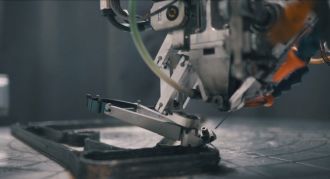
Les cellules de fabrication de dépôt d'énergie directe (DED) d'Arevo comprennent un robot industriel, une tête d'impression avec chauffage laser et une plate-forme de fabrication rotative. La tête d'impression (vue à droite pendant la coupe et le redémarrage automatisés) comprend un équipement de gestion thermique et des systèmes de vision pour l'inspection in situ. SOURCE :Arevo.
Production industrielle de composites thermoplastiques
« Nos nouvelles cellules de fabrication utilisent un robot industriel standard , une plateforme de construction rotative et un laser pour le chauffage », explique Miller. « Nous appelons le processus dépôt d'énergie direct (DED)." À l'intérieur de la cellule de fabrication sécurisée pour le laser, le robot dispose d'un effecteur de tête d'impression avec gestion thermique propriétaire équipements, électronique personnalisée et systèmes de vision qui permettent l'inspection in situ . « Le processus est principalement sans intervention/hors service », explique Miller. "Ces nouvelles cellules produisent une vitesse de production plus de 100 fois supérieure." Le directeur technique Wiener Mondesir ajoute :« Le laser fournit une énergie illimitée. Nous pouvons contrôler cela et aller plus vite pour atteindre des cadences de production industrielles. » Mais Miller souligne :« Ce n'est pas une question de vitesse à laquelle les machines peuvent se déplacer ou de quantité de matériau pouvant être appliquée, car nous construisons des composites structurels complexes à un quart du coût des composites traditionnels. »
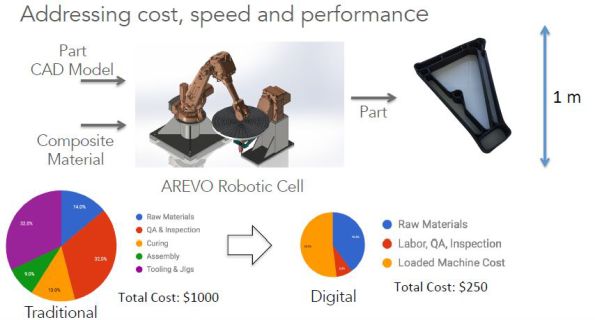
Fabrication de composites non traditionnels — Le processus DED d'Arevo permettrait la production de pièces composites thermoplastiques renforcées de fibres continues à ¼ du coût des composites traditionnels. (Calculs basés sur une pièce de 1 m.)
« Nous poursuivons la fabrication économiquement viable de pièces composites thermoplastiques à grande échelle , dit Miller. « Nous abordons cette fabrication du point de vue des composites non traditionnels. » Cependant, la tête d'impression intègre une capacité de compactage et les pièces sont toujours conformes aux exigences de qualité traditionnelles des composites. « Nous pouvons réaliser des pièces composites thermoplastiques avec un teneur en vide bien inférieur à 1 % », atteste Miller. « Arevo continue d'améliorer son procédé et satisfera aux propriétés mécaniques des exigences de structure primaire dans un avenir proche. »
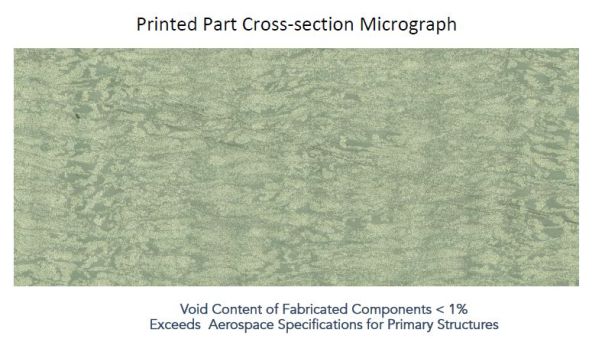
Logiciel Pathfinder
L'investissement d'Arevo dans les logiciels de conception et de processus numériques fait partie des références de Miller à la «perspective des composites non traditionnels». « Nous avons réduit tout un flux de travail dans le logiciel », explique Miller. « Il peut fournir une analyse 3D complète de la pièce et développer l'orientation optimisée des fibres à l'aide de Additive FEA modules (AFEA). Une grande partie de notre succès repose sur le logiciel et la simulation de production de pièces. Nous exécutons la conception générée par ordinateur via notre logiciel de simulation de processus et il montre les paramètres de processus, y compris les températures, le chemin d'impression, le gauchissement et rétrécissement du matériel imprimé , ainsi que les contraintes résiduelles. Cela nous permet de vraiment comprendre et optimiser le processus afin de produire des pièces de très haute qualité. »
Il dit que le témoignage du logiciel d'Arevo est que les propriétés des pièces fabriquées se situent à moins de 5% des propriétés simulées, ce qui, selon Miller, est essentiellement inférieur au niveau de la marge d'erreur de mesure des tests. Il ajoute qu'Arevo utilise également l' machine learning. d'une manière unique.
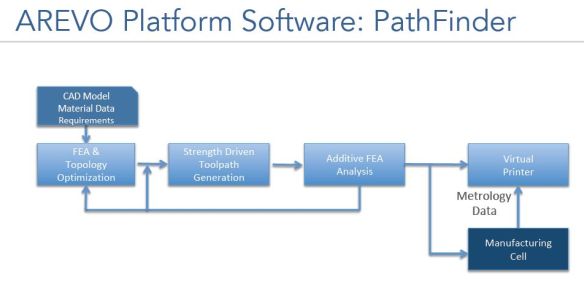
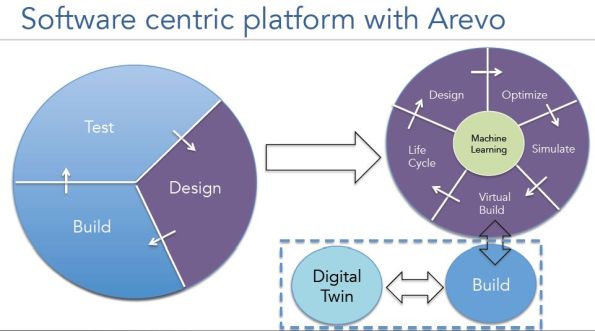
Démontrer les possibilités
Il y a tout juste un mois, Arevo a présenté ce qu'il pense être le premier vélo imprimé en 3D au monde à l'événement Sea Otter (19-22 avril, Monterey, CA, US). « Notre objectif était de démontrer ce que nos logiciels et processus peuvent réaliser », explique Miller. « Nous avons travaillé avec la société de design industriel Studio West basée au Colorado pour développer la conception du cadre de vélo en porte-à-faux . " Il note que Studio West est bien connu dans l'industrie du vélo, travaillant avec certains des meilleurs fabricants. « Ils nous ont initialement donné une conception de cadre très traditionnelle », explique Miller. « Mais nous voulions montrer comment Arevo peut appliquer des fibres continues de nouvelles manières. , nous avons donc continué à travailler avec eux à travers diverses itérations. Il ajoute que l'équipe Arevo souhaitait optimiser la rigidité et la flexion du cadre du vélo, mais aussi démontrer la nouvelle esthétique possible grâce à sa technologie de fabrication additive. « Nous nous sommes retrouvés avec un design de vélo tout à fait unique », explique Miller. Le cadre du vélo est fait de remorquage continu 12K CF et PEEK mais Miller dit qu'il est également possible d'utiliser du nylon.
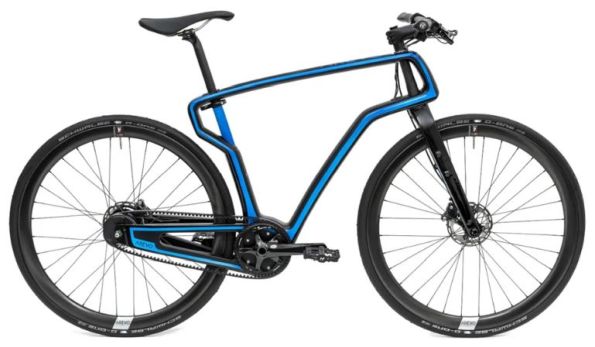
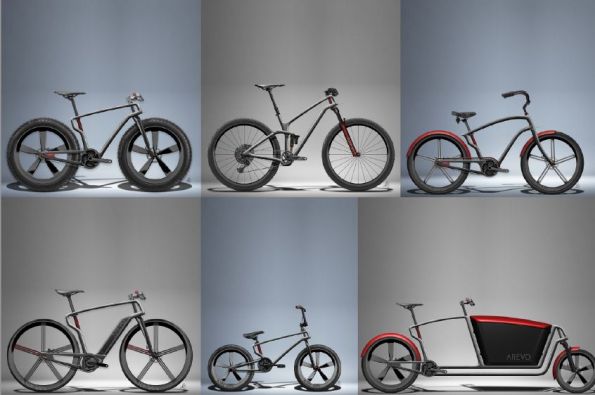
Le cadre de vélo composite CF imprimé en 3D d'Arevo est facilement adapté pour répondre à une large gamme de produits pour le marché du vélo, y compris les vélos électriques, les vélos cargo, les vélos couchés, les vélos à 3 roues, les vélos pour enfants, les gros vélos, le BMX, les cruisers et Suite. SOURCE :Arevo.
Les cadres de bicyclettes ne sont pas le seul exemple de ce que réalise Arevo dans la fabrication additive de composites. « Les petites entreprises de robotique construisent des robots de grande taille que nous aidons à alléger à une fraction du coût des matériaux traditionnels », explique Mondesir. Arevo met également en évidence les applications d'hélice et d'hélice , où les avantages signalés incluent :
- Production à la demande pour gérer le coût des stocks
- Efficacité supérieure par rapport à la construction métallique
- Résilient à l'environnement de service
- Les géométries complexes ne sont pas possibles avec la fabrication traditionnelle.
Voie vers la production industrielle
Miller indique que le premier objectif pour 2018 est d'installer huit cellules de fabrication DED et de renforcer les capacités pour traiter son arriéré de pièces de production . « Nous allons commencer à expédier des produits en volume cette année », affirme-t-il. La société travaille également avec des clients stratégiques sur des applications clés et le développement de produits. « Notre troisième objectif principal est de continuer à affiner le processus de dépôt pour augmenter la vitesse tout en maintenant la qualité et le rendement », déclare Miller. « Nous ferons également la démonstration de pièces avec différentes fibres et tailles de câble . " Il dit que le processus DED peut gérer une forme et un diamètre de câble variables, jusqu'à un câble de 24K. « Nous pouvons imprimer avec du PEKK, du PAEK, du PPS ainsi qu'avec des fibres continues de verre et d'aramide », ajoute Miller.
Qu'en est-il de l'impression avec fil et fibre optique pour les structures composites multifonctionnelles ? « Ce serait essentiellement une autre fibre pour nous », explique Miller. Les démonstrations de cette capacité ont, jusqu'à présent, été en laboratoire. "Nous étudions la propriété intellectuelle et menons une R&D en cours dans ce domaine", ajoute-t-il.
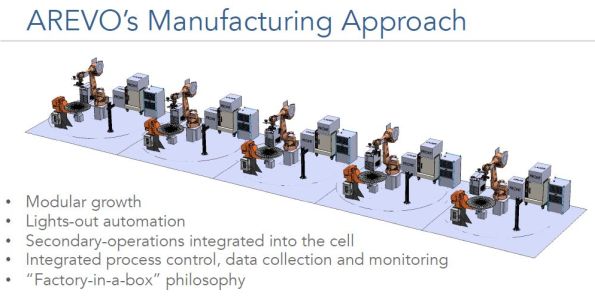
« Rien ne nous empêche d'utiliser plusieurs remorques et/ou rubans », soutient Miller. « Et il n'y a vraiment aucune limite à quelle taille nous pouvons imprimer. Nous fabriquons une pièce de 2,5 m x 1,5 m pour une entreprise aérospatiale et envisageons également d'utiliser plusieurs robots ensemble . L'entreprise a développé ses cellules de fabrication DED pour qu'elles soient modulaires, capables d'intégrer des opérations secondaires telles que la finition pour produire des surfaces de haute qualité.
Nous pouvons également placer nos têtes d'impression sur n'importe quel robot industriel, afin que notre technologie puisse être intégrée dans un processus existant ou des processus complètement nouveaux. Il précise qu'Arevo « n'est pas dans le domaine de l'impression, mais cette adaptabilité ouvre des opportunités. La société possède 55 brevets délivrés, en attente ou demandes en cours.
Qu'en est-il de la conception générative ? Arevo se veut-il un acteur aidant à concrétiser cette nouvelle approche de la conception et de la fabrication ? « La conception générative est très différente de ce que nous faisons, car elle peut aboutir à des conceptions difficiles à fabriquer, ce qui augmente les coûts », répond Miller. « Notre approche consiste à inclure l'optimisation pour la fabrication à l'avant."
Résine
- Production de fibre de carbone et pièces en fibre de carbone :quelles sont les bases ?
- Remplacement des pièces en aluminium par de la fibre de carbone imprimée en 3D
- 2018 :une odyssée IMTS
- AON3D, Astrobotic pour envoyer des pièces imprimées en 3D sur la lune
- Alltec se développe sur le marché nord-américain
- Covestro lance les thermoplastiques à fibres continues Maezio
- Fabrication continue de fibres (CFM) avec des composites moi
- Impression 3D de composites avec fibre continue
- Le logiciel améliore la précision des pièces imprimées en 3D