Visite de l'usine :STELIA Aerospace, Méaulte, France
Avec 7 000 collaborateurs dans le monde et un chiffre d'affaires 2018 de 2,2 milliards d'euros, STELIA Aerospace (Toulouse, France) affirme clairement ses principaux produits et sa position industrielle :N°1 en Europe/N°. 3 mondial pour les aérostructures, n° 1 mondial pour les sièges pilote et équipage et n° 3 mondial pour les sièges passagers de première et classe affaires.
L'utilisation des composites par STELIA Aerospace s'étend aux sections avant du fuselage de l'Airbus A350, aux ailes des avions à turbopropulseurs ATR, à diverses structures d'hélicoptères et à certains produits de sièges, dont son tout nouveau siège OPAL. Les installations de production de composites comprennent les sites français de Méaulte (grandes sections de fuselage) et de Salaunes (pièces composites plus petites), des pièces de détail et d'assemblage au Maroc et en Tunisie et une large gamme de pièces composites pour l'aéronautique, la défense et l'espace sur l'ancien site Composites Atlantic à Lunenburg, Nouvelle-Écosse, Canada.
STELIA Aerospace est née de la fusion en 2015 de deux anciennes filiales d'Airbus, Aerolia et Sogerma. Son site de Méaulte - à 1h30 de route au nord de Paris - s'étend sur 49 hectares avec 150 000 mètres carrés d'espace de production, 1 500 employés et 500 sous-traitants, et est un élément clé de la chaîne d'approvisionnement d'Airbus. Son emplacement dans une petite ville dément une puissance de production, "livrant 860 sections de fuselage avant pour l'A320, l'A330, l'A350, l'A380 et l'A400M en 2018", explique le responsable de la communication de STELIA Méaulte, François Fournier. Il est mon guide à travers la production du fuselage avant de l'A350 « Usine du Futur » du site et l'installation R&T de STELIALAB, accompagné d'Olivier Canal, responsable R&T fabrication, assemblage &automatisation, fabrication, assemblage &automatisation, composites &numérique de STELIA Aerospace Méaulte, et Simon Maire-Vigeur , responsable fabrication R&T composites, STELIALAB.
« Usine du futur »
Lors d'une présentation introductive dans le bâtiment du siège du site, Fournier explique que STELIA Aerospace a investi dans les technologies du futur, telles que la fabrication numérique et l'automatisation dont la réalité augmentée/réalité virtuelle utilisée pour augmenter l'efficacité de la production et les robots/cobots pour un assemblage plus efficace.
« L'avenir, ce sont les composites et structures métalliques », note Canal. « Nous essayons de définir des solutions futures non pas pour remplacer nos travailleurs, mais pour les rendre plus efficaces. »
Cette recherche d'efficacité est peut-être mieux illustrée par l'initiative « Usine du futur » lancée il y a cinq ans pour répondre aux rampes de production de l'A320 et de l'A350. « Nous avons adopté une nouvelle stratégie industrielle pour ce site », se souvient Canal, qui était chef de projet pour l'initiative. « Nous voulions pouvoir répondre à des cadences de production variables et développer un outillage flexible que nous pourrions réutiliser d'un programme à un autre. »
Un autre résultat de cette refonte a été de consacrer des bâtiments à des programmes spécifiques. "Chacun aurait une ligne et une équipe", explique Canal, "et serait conçu avec une approche de fabrication au plus juste qui se concentre sur l'élimination des déchets dans la main-d'œuvre, les mouvements, les matériaux et les processus." STELIA Aerospace a également repensé la ligne A320 et gagné 10 à 20 % de productivité, « ce qui est en fait une amélioration significative », déclare Canal. « Nous y sommes parvenus en 2,5 ans, en modifiant plus de 50 % de l'empreinte de la fabrication de ce site tout en maintenant la production et Livraison à 100 % dans les délais sans perte de qualité. Ce succès est attribué au soutien de la direction de haut niveau, « mais nous avons également travaillé dur pour que les travailleurs soient propriétaires », note-t-il.
Canal explique que la conception du bâtiment de production de l'A350 de 30 000 mètres carrés a été dictée par le flux, illustré par sa forme en U, avec des matières premières entrant à une extrémité et des sections de fuselage finies sortant de l'autre. « Tout pour la production de nos structures A350 se trouve dans ce bâtiment, du début du laminage à l'assemblage final. C'est important, par exemple, pour permettre d'identifier et de traiter rapidement et facilement tout problème de qualité », dit-il.
Pour l'A350, STELIA Aerospace réalise la partie avant du fuselage 11, qui est entièrement métallique pour mieux résister aux impacts d'oiseaux, ainsi que l'ensemble hybride métal/composite complexe pour la partie 12 et l'unité inférieure de la partie 11/12, qui comprend la pointe avant. baie de train d'atterrissage. Fournier montre la vidéo « Factory of the Future » de STELIA Aerospace, en montrant la ligne pulsée, comme celle utilisée pour l'assemblage automobile. "Nous avons mis en place une ligne de démonstration pour permettre aux travailleurs de former et de démystifier cette ligne mobile, qui fonctionne à un temps de cadence spécifique pour répondre à une production à plein régime", explique Canal.
Un autre aspect était la technologie numérique. « Les solutions numériques nous ont permis de mettre tous les schémas et étapes techniques sur une tablette et de garantir l'accès à la dernière maquette 3D pour chaque section », explique Canal. Les travailleurs sont ainsi tenus informés des détails et des changements cruciaux tandis que les gestionnaires sont facilement informés des problèmes potentiels. « Nous avons également développé la réalité augmentée pour faciliter l'assemblage, par exemple la projection sur les coques du fuselage montrant quelles pièces et où les fixations doivent être réalisées », note Canal. Il ajoute que l'inspection des cobots sont utilisés pour effectuer des numérisations 3D de sections finies qui sont ensuite comparées à la maquette numérique, identifiant les objets étrangers ou les pièces manquantes, les problèmes de qualité, etc.
Notre visite a commencé dans la salle blanche du bâtiment de production de l'A350, où les machines de placement automatisé de fibres (AFP) de Coriolis (Quéven, France) déposent de grandes coques de fuselage en polymère renforcé de fibres de carbone (CFRP) pour l'unité inférieure de la section 11/12 et la couronne et deux coques latérales pour la section 12. Ces coques sont ensuite couplées à des longerons préfabriqués, emballées sous vide et durcies dans un autoclave. Après durcissement, ils sont coupés et chargés sur des outils de manutention qui permettent un transport facile tout au long de toutes les étapes de l'assemblage, qui comprend le perçage robotisé et l'installation des fixations. Chaque panneau est inspecté à l'aide de tests non destructifs automatisés (CND). Les assemblages terminés sont livrés à la ligne d'assemblage du fuselage d'Airbus à Saint Nazaire, en France.
STELIALAB
Le prochain arrêt est le centre de R&T STELIALAB de 2 000 mètres carrés, qui occupe la moitié gauche d'IndustriLAB, un centre régional de technologie et de formation situé juste au sud du complexe fermé STELIA. Les activités de STELIALAB sont dédiées aux composites, à l'assemblage et aux technologies numériques.
Ici, la visite recommence dans la salle blanche (salle blanche), une pièce assez grande et ouverte avec des fournitures d'ensachage et des outils de drapage. Simon Maire-Vigueur explique que la mission du groupe est d'identifier l'avenir de la production à faible coût et à haut volume pour la plupart des pièces de grande taille et complexes. L'industrialisation des composites thermodurcissables comprend des procédés d'AFP et d'infusion de résine liquide (LRI) à grande vitesse, y compris le moulage par transfert de résine (RTM), pour les grandes structures fermées telles que les composants d'aile, les empennages horizontaux et les empennages verticaux.
En quittant la salle blanche, nous entrons dans la salle AFP occupée par une machine Coriolis pouvant poser des pièces jusqu'à 4 mètres de longueur. Dédié à la R&T, Maire-Vigueur constate qu'il est occupé plus de 200 jours par an. STELIALAB a développé un procédé d'intégration de raidisseurs secs créés par AFP et de peaux durcies en autoclave (OOA) à l'aide d'un four ou d'outils auto-chauffants. « Nous préférons le LRI avec une pression d'injection plus faible car nous pouvons utiliser des outils moins chers », explique Maire-Vigueur.
Feuille de route TPC
Cette machine AFP a également été utilisée pour la pose de la peau du démonstrateur de fuselage / poutre de queue d'hélicoptère en composite tout thermoplastique (TPC) dans le cadre du programme de développement ARCHES TP. Présenté au salon du Bourget 2017, ainsi qu'au JEC World en 2018 et 2019, il a été réalisé à l'aide de 8 traits de ruban en fibre de carbone/polyéthercétonecétone (PEKK) de 0,25 pouce de large avec chauffage laser. « Nous avons intégré la protection contre la foudre à l'AFP lors du drapage », note Maire-Vigueur. "La peau a été polymérisée par OOA à l'aide d'un film d'ensachage Kapton, ce qui n'est en fait pas très pratique." Les longerons en forme d'oméga ont été fabriqués à partir de panneaux plats en ruban unidirectionnel achetés et formés par estampage par Aviacomp (Toulouse, France). Le même procédé a été utilisé pour les cadres, mais en utilisant des plaques en tissu tissé fournies par Porcher (Badinières, France) et estampées au Cetim (Nantes, France). Bien que les cadres aient été fixés mécaniquement de manière standard, les longerons ont été fixés à l'aide d'un soudage par induction automatisé et dynamique. « Cela permet de réduire les coûts et de nouvelles possibilités de conception », note Maire-Vigueur. « Nous avons également démontré le surmoulage des points d'attache, comme pour les harnais électriques. »
Interrogé sur les défis du programme, Maire-Vigueur cite les drapages, les soudures et le délai de 15 mois. « Même réaliser l'estampage sans trop de distorsion dans le matériau tissé n'était pas facile », ajoute-t-il. Si la conception de la poutre de queue a été réalisée par le bureau d'études toulousain de STELIA Aerospace, l'ensemble de la production a été supervisé par STELIALAB. Cependant, ARCHES TP n'était qu'une étape dans la feuille de route des composites thermoplastiques de STELIA Aerospace. La société continue de développer des technologies TPC pour démontrer la faisabilité d'un fuselage TPC à grande échelle dans les années suivantes.
Repenser les futures aérostructures
En sortant de la salle AFP, la visite se déroule dans un très grand hall ouvert qui est divisé en « cellules de développement » sécurisées par des murs temporaires pour protéger la propriété intellectuelle. En traversant le hall et en tournant à gauche, nous atteignons une zone avec un petit autoclave Scholz (Coesfeld, Allemagne) capable de 450°C, et une machine d'injection pour l'infusion de résine. « Parce que notre feuille de route est de durcir l'OOA, nous utilisons en fait l'autoclave comme un four, durcissant les composites thermoplastiques sans pression », explique Maire-Vigueur. Il y a une salle de garniture avec des rideaux et une zone à côté avec un équipement CND, y compris un petit système C-scan.
Nous tournons à nouveau et entrons dans un grand laboratoire d'essais. « Nous pouvons étudier des sections transversales polies pour le contrôle de la qualité et des études sur les matériaux et les procédés », explique Maire-Vigueur. Le laboratoire comprend également un bras Romer (Hexagon Manufacturing Intelligence, Shropshire, Royaume-Uni) pour la mesure des coordonnées et un équipement pour le rapport volumique des fibres, la dureté et les tests chimiques. « Tous les ingénieurs de notre équipe R&T sont capables de contrôler eux-mêmes les matériaux et les procédés », note Maire-Vigueur. « Nous les formons pour qu'ils puissent opérer de la conception à la fabrication, en passant par l'inspection et le test des pièces finales. Ceci est important pour comprendre l'ensemble du processus et permet une évaluation rapide des problèmes suspectés et de leurs causes. La conception n'est pas séparée de la fabrication et des tests de qualité. »
Le dernier arrêt est un grand laboratoire d'automatisation dans l'une des zones fortifiées. Un bref coup d'œil à l'intérieur montre le travail explorant un nouvel assemblage à l'aide de robots et de cobots. « Nous envisageons de poursuivre le développement d'outils plus petits et plus fonctionnels et essayons d'imaginer comment vous pourriez assembler des pièces plus rapidement et à moindre coût », déclare Canal. « Notre culture consiste à repousser les limites et à innover. Nous avons été un leader dans la mise en œuvre de la robotique et maintenant nous sommes un leader dans la promotion de la technologie des composites. Nous avons démontré notre capacité à repenser et à repenser l'avenir et nous ne nous arrêterons jamais. »
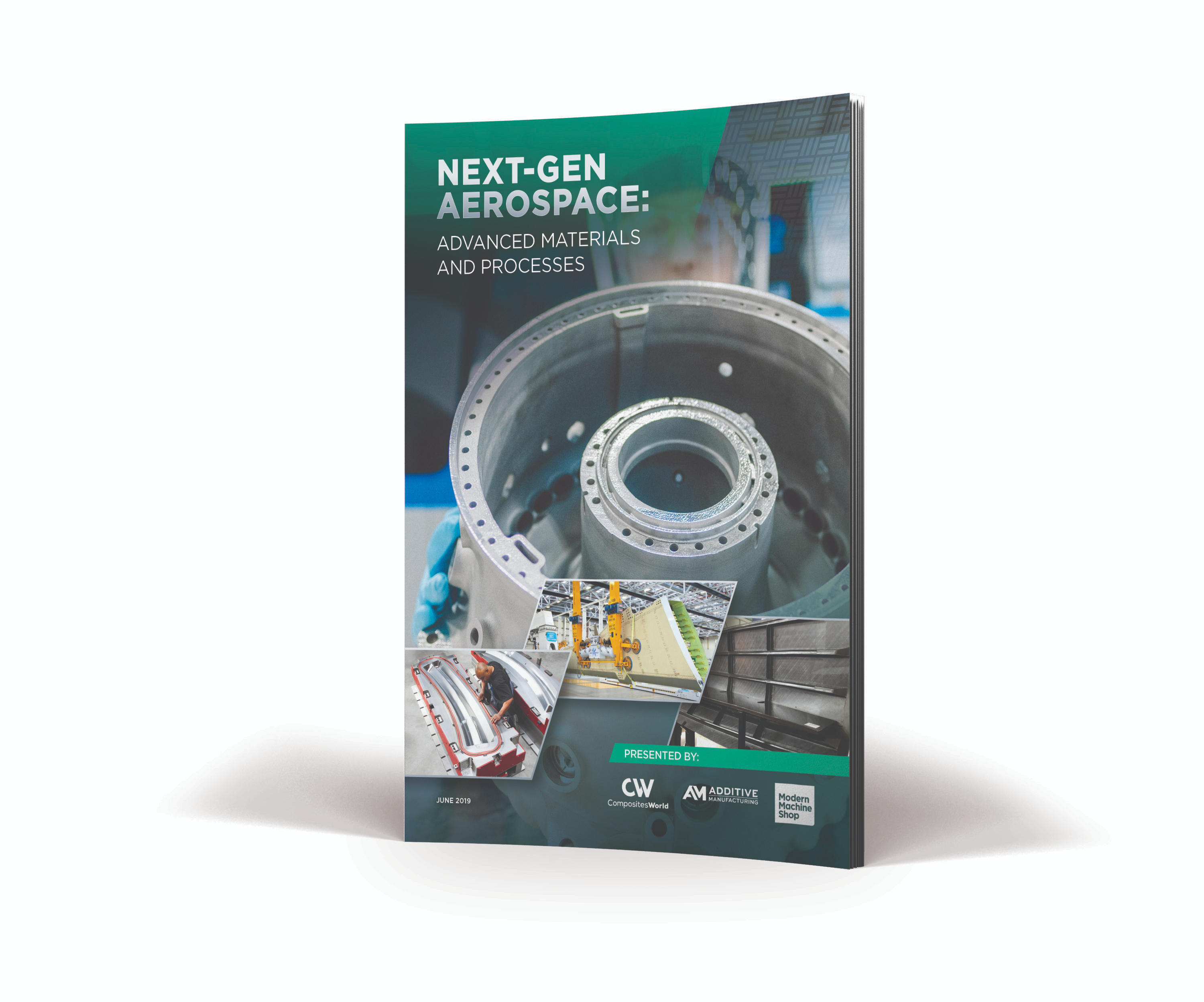
La prochaine génération de fabrication aérospatiale
Le secteur de l'aviation commerciale devant doubler au cours des 20 prochaines années, répondre à la demande d'avions de transport de passagers et de fret nécessitera de nouvelles technologies et des taux de fabrication sans précédent.
Apprenez-en plus sur les matériaux et les processus qui façonneront les avions de nouvelle génération dans une collection d'histoires de CompositesWorld, Modern Machine Shop et Fabrication Additive , disponible pour lire ou télécharger gratuitement . Obtenez-le ici.
Résine
- Vespel® :le matériau aérospatial
- Polyplastics va étendre la production de Topas COC
- Radici augmente considérablement sa capacité de production mondiale
- Polykemi investit dans sa propre usine de compoundage aux États-Unis
- Rethink Robotics obtient un nouveau siège social et une nouvelle usine de production
- Toyota choisit un site en Caroline du Nord pour son usine de production de batteries pour véhicules électriques
- Les fabricants visitent Southco pour une visite de l'usine, une discussion sur les meilleures pratiques d'amélioration continue
- Arkema Inc. construit une usine de production de PEKK aux États-Unis
- Hexion présente une solution époxy à deux composants pour la production de composites aérospatiaux