Impression 3D magnétique de la prochaine génération de composites sur mesure
Fortify (Boston, Massachusetts, États-Unis) a été fondée en 2016, sur la base de la recherche sur l'impression 3D composite par Josh Martin (PDG de Fortify) et Randall Erb, directeur du DAPS Lab de la Northeastern University de Boston. (Erb est également co-fondateur de Boston Materials et de Fortify.) Leur objectif était de permettre une production rapide de composites avec des microstructures optimisées. La technologie brevetée Fluxprint qu'ils ont développée utilise des champs magnétiques et un traitement numérique de la lumière (DLP) - mais avec des systèmes de résine hautement chargés - pour produire des microstructures personnalisées dans des pièces composites imprimées en 3D haute résolution.
Fluxprint contre DLP
Le DLP et la stéréolithographie (SLA) sont actuellement considérés comme les technologies d'impression 3D offrant la complexité et la précision des pièces les plus élevées. Les deux reposent sur l'utilisation de la lumière - généralement ultraviolet (UV) - pour durcir une résine photosensible qui comprend généralement des monomères époxy ou acryliques et méthacryliques. La lumière est dirigée numériquement pour éclairer la résine dans le réservoir du système afin de créer les formes ou les motifs pour chaque couche. La plate-forme de fabrication est déplacée après chaque couche, permettant à la couche suivante d'être imprimée et de procéder à une pièce finie et solide.
Les projecteurs DLP et SLA remontent au début de l'impression 3D dans les années 1980. Les imprimantes DLP ont tendance à être plus grandes car elles abritent le projecteur de lumière réel. La plupart des machines SLA et DLP utilisent des polymères thermodurcissables, mais EnvisionTEC fabrique une imprimante qui peut également utiliser des thermoplastiques. Les deux ont traditionnellement utilisé des polymères purs sans renforcement.
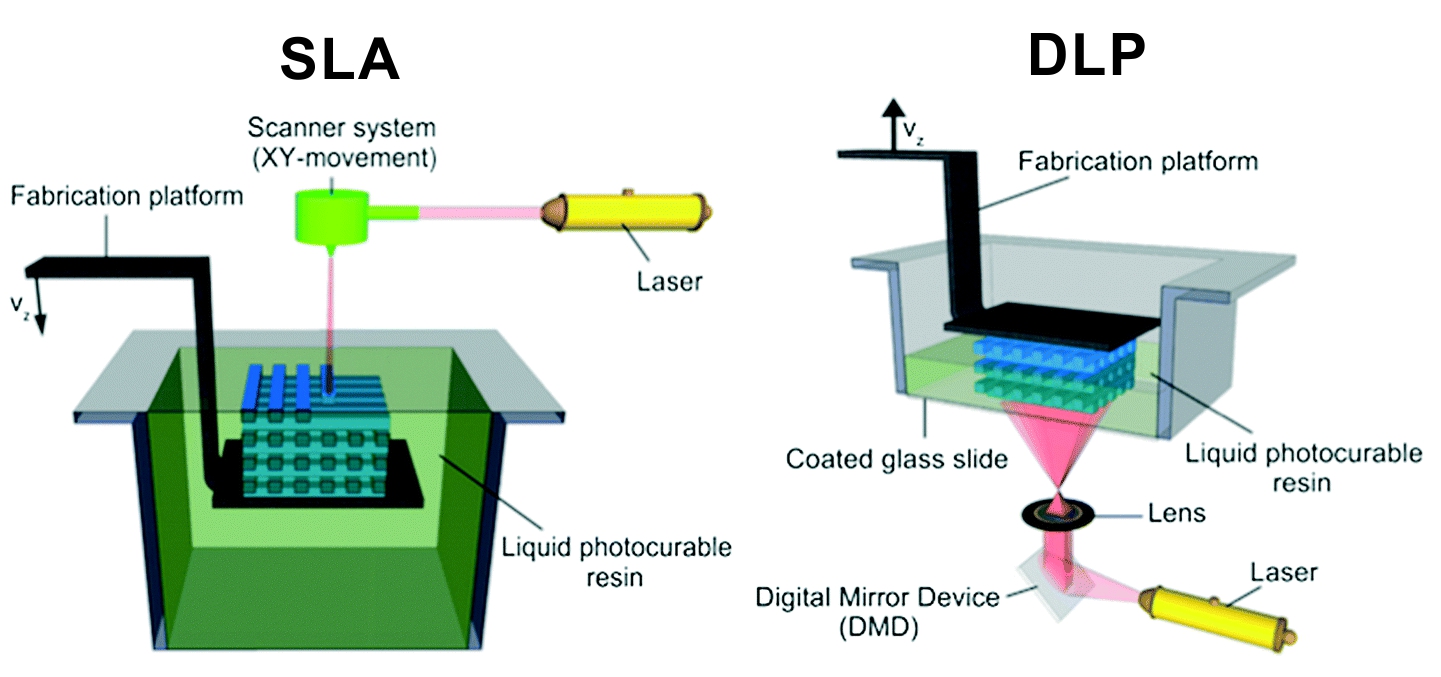
« Les plates-formes DLP sont capables de taux de production et de qualité suffisants », déclare Josh Martin, PDG de Fortify, « mais les propriétés mécaniques ont toujours été un défi. Notre thèse principale est qu'un changement radical de performance ne sera pas accompli par la seule chimie des polymères. Cependant, l'exploitation des propriétés uniques des composites dans l'industrie des additifs haute résolution changera la donne. »
Il explique que Fortify est spécialisé dans le séchage UV de résines techniques hautement chargées en utilisant des additifs uniques et en contrôlant l'orientation de ces additifs améliorant les propriétés dans l'impression. Les charges comprennent des fibres de verre, de carbone et de céramique ainsi que des particules. Les résines techniques comprennent les résines à base d'acrylate et de méthacrylate (PMMA) ou à base d'époxy, à base de cations - qui, explique Martin, sont plus conventionnelles pour l'industrie des revêtements. Les principaux fabricants de résines dans le monde (BASF, DSM, Dupont et autres) investissent massivement pour améliorer les propriétés de leurs additifs. Fortify est en mesure de sélectionner le meilleur de ces avancées pour ajouter leur technologie de renforcement.
Le contrôle de l'orientation des fibres est obtenu en utilisant un champ magnétique. Comme Fortify 3D imprime une pièce à l'aide de sa technologie Fluxprint, les fibres sont magnétiquement alignées voxel par voxel pour répondre aux exigences de charge de la pièce. (Voir le processus en action dans la vidéo ci-dessus.) Pour les matériaux de renforcement non magnétiques, tels que les particules et les fibres de céramique et de verre, des techniques exclusives d'étiquetage magnétique sont utilisées pour enrober les charges d'une manière qui les rend magnétiquement sensibles et compatibles avec la résine.
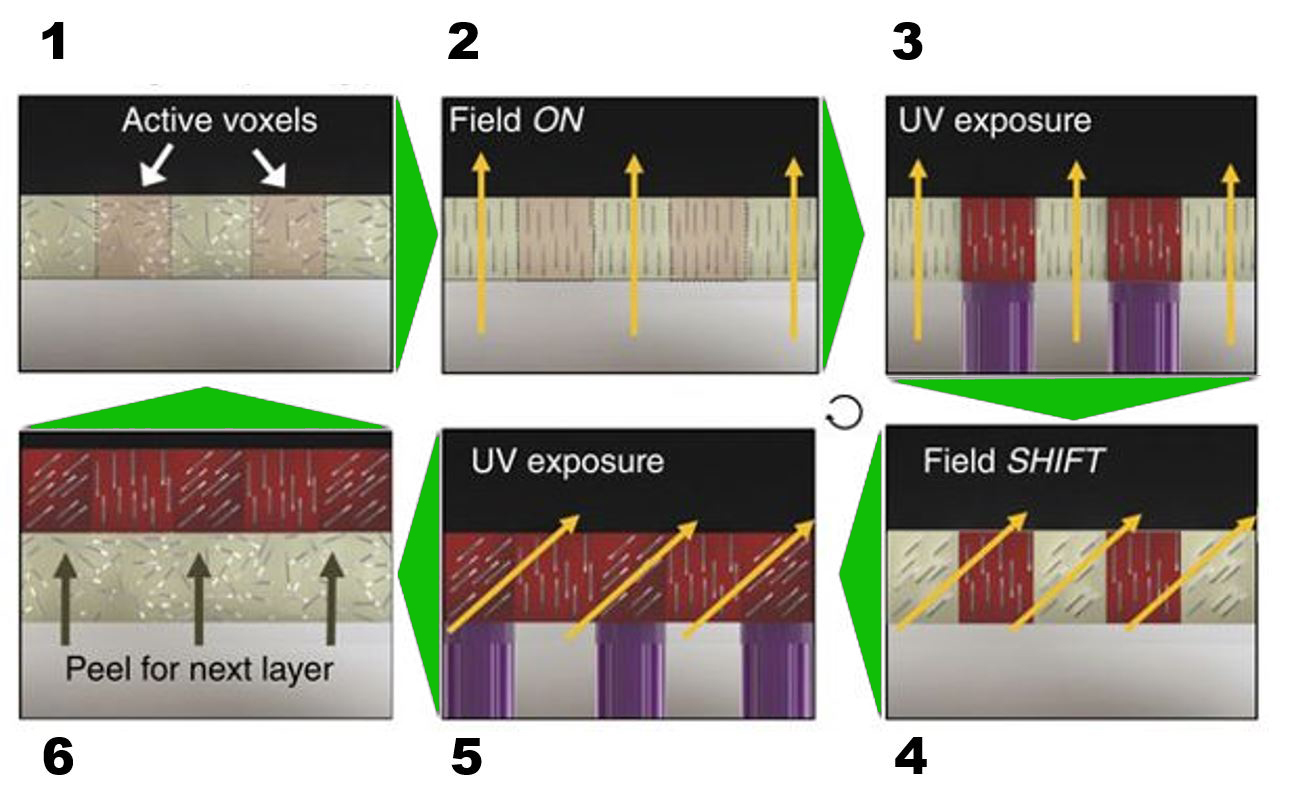
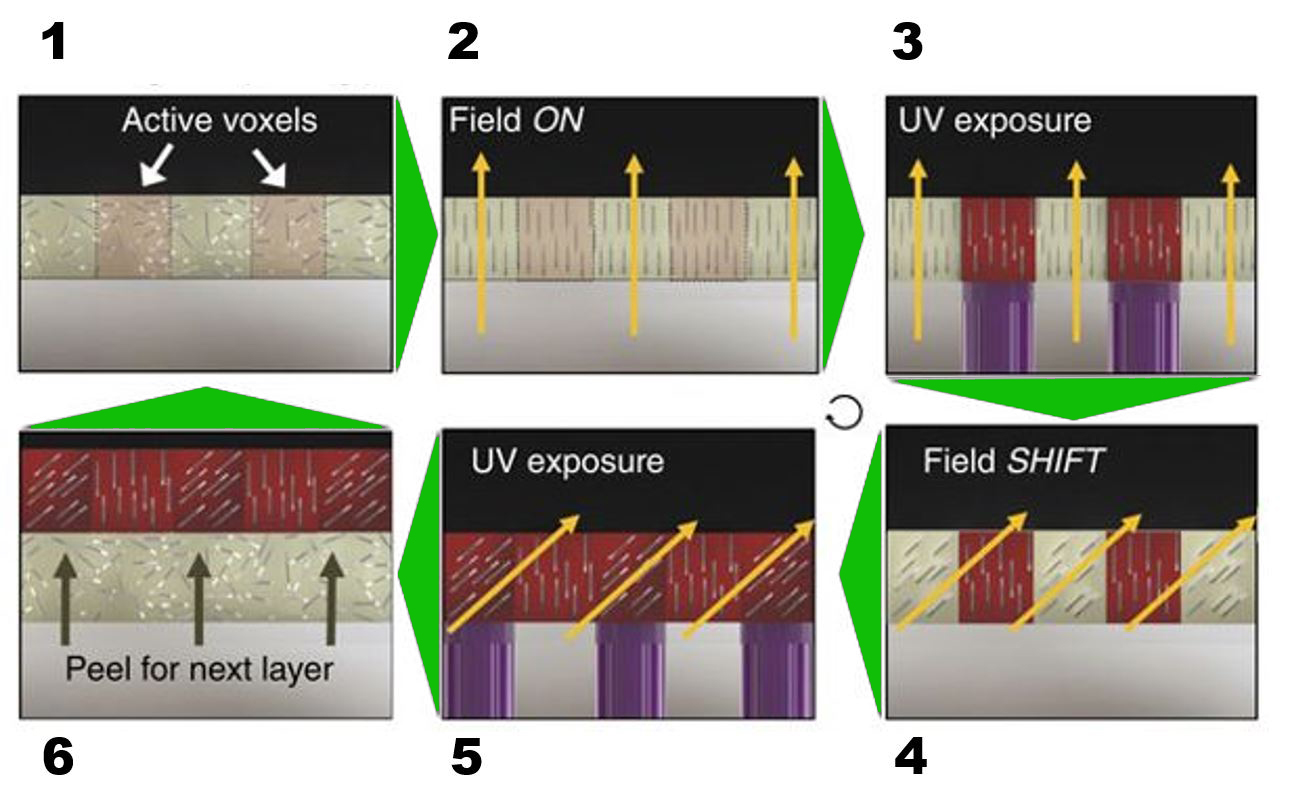
Le processus Fluxprint est illustré dans l'image ci-dessus et décrit comme suit :
- Une couche de matériau d'alimentation est fournie à la zone de construction avec des renforts alignés de manière aléatoire.
- Un champ magnétique est appliqué pour aligner le ferraillage.
- Les voxels actifs sont exposés à la lumière UV, fixant l'orientation du renforcement dans ces voxels (maintenant affiché en rouge).
- Le champ magnétique est déplacé pour définir une nouvelle orientation du renforcement.
- Répétez l'étape d'exposition aux UV pour corriger l'orientation du prochain ensemble de voxels (répétez si nécessaire).
- La plaque de construction s'ajuste pour apporter une matrice de matériau d'alimentation non durcie pour la couche d'impression suivante.
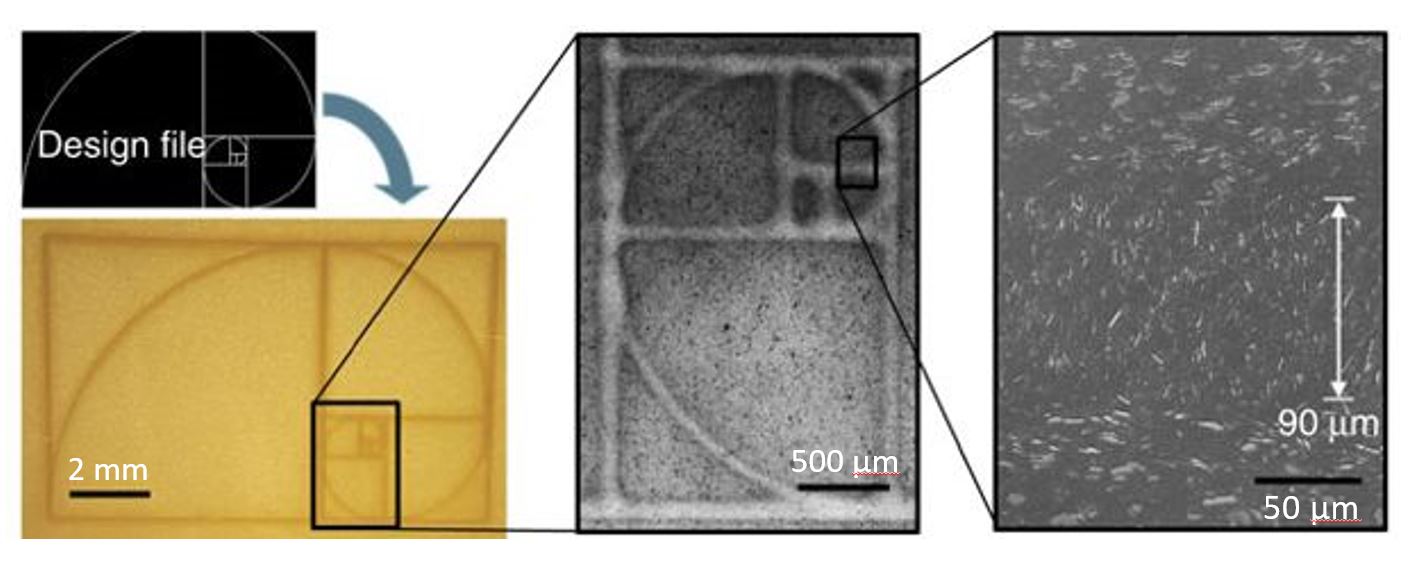
La technologie Fluxprint permet un contrôle du niveau de voxel sur l'orientation des fibres pendant le processus d'impression. Origine | « Conception d'architectures de renforcement composite bioinspirées via l'impression magnétique 3D » par Joshua J. Martin, Brad E. Fiore et Randall M. Erb, Nature Communications volume6, numéro d'article :8641 (2015).
Pourquoi voxel par voxel ?
« Chaque géométrie a des états de déformation et de contrainte uniques », explique Martin. « La plupart des composites sont fabriqués à la main pour tenir compte de cela. Nous numérisons le processus. Par exemple, si vous pouvez renforcer correctement un cadre de drone, vous pouvez utiliser moins de matériau. Toute application qui fonctionne contre la gravité en bénéficiera fondamentalement. »
L'impression voxel par voxel est également intrinsèquement haute résolution. « Il s'agit du processus de fabrication de composites à la plus haute résolution à ce jour », déclare Martin, notant que la modélisation par dépôt par fusion (FDM) - où un filament de plastique renforcé de fibres non renforcé ou broyé est fondu et déposé sur un lit d'impression - a une résolution de plusieurs centaines de micromètres tandis que celle de Fluxprint est à quelques dizaines de micromètres. "Donc, c'est un ordre de grandeur d'amélioration, qui entre dans le territoire au-delà de ce qui est perçu à l'œil nu. Ce type de résolution est très important pour une grande variété de pièces d'utilisation finale. »
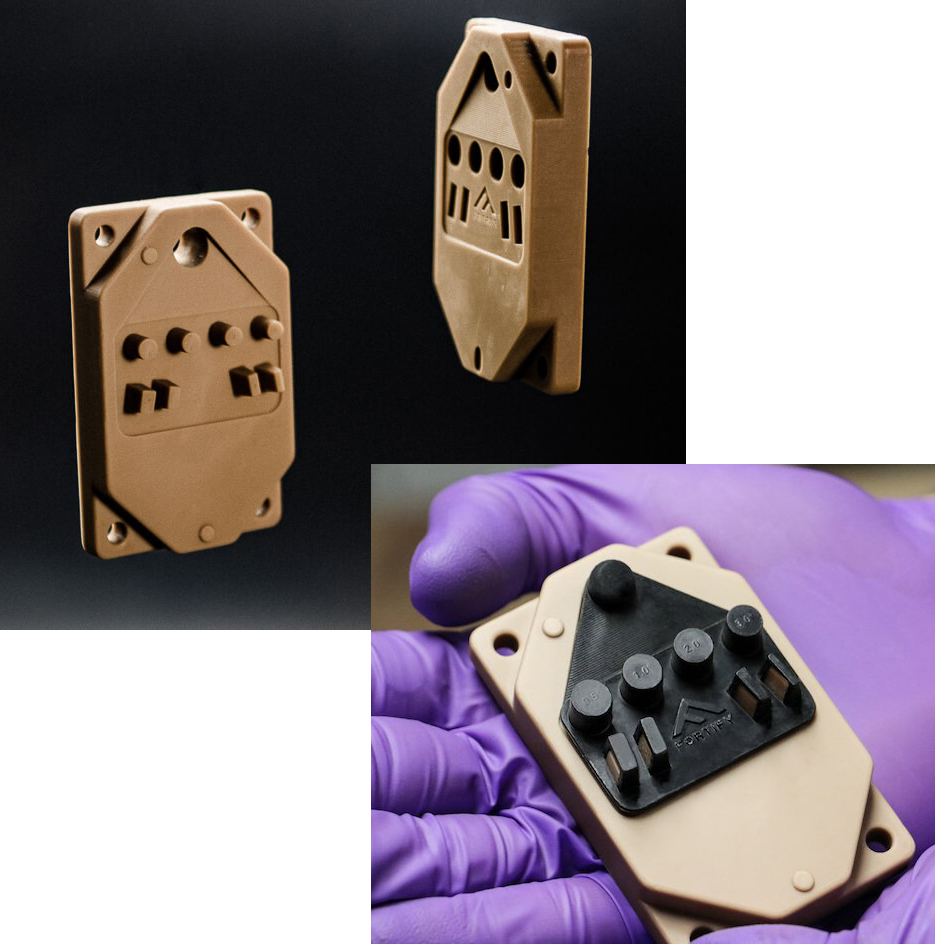
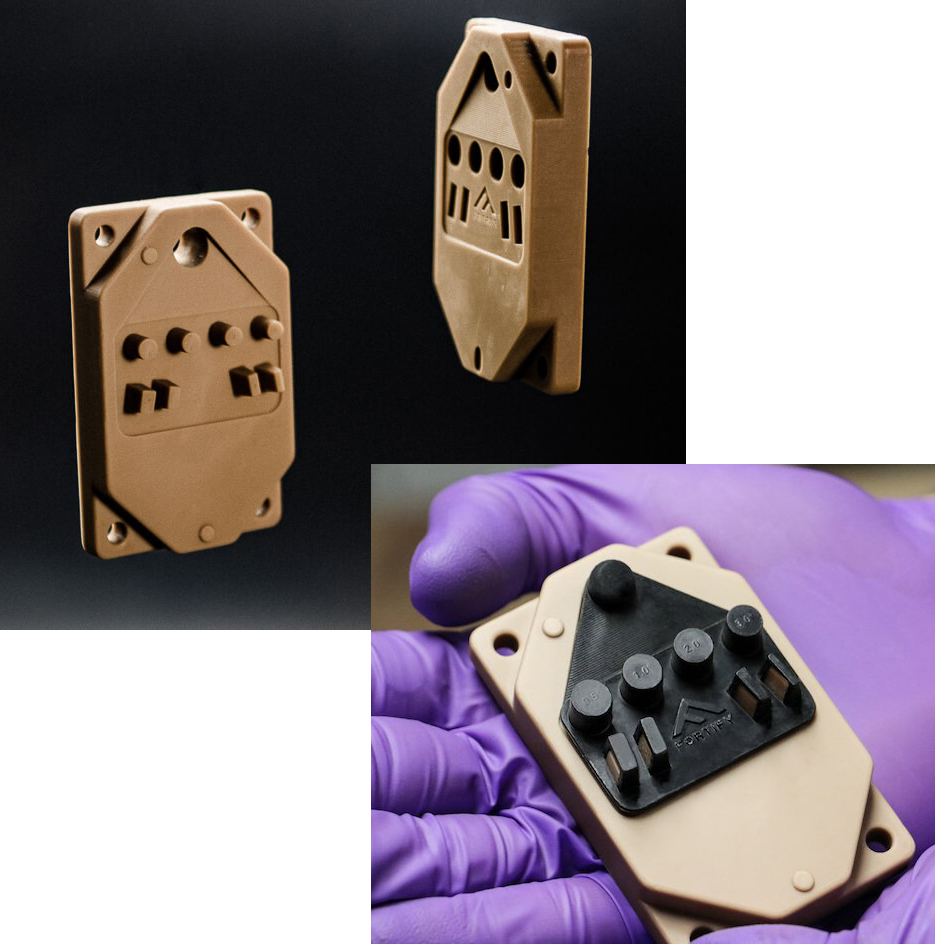
La technologie d'impression 3D magnétique Fluxprint de Fortify peut orienter les fibres pour renforcer les projections de « piquets » sur les outils de moulage par injection. Origine | Fortifier.
"Nous proposons des outils de moulage par injection qui sont nettement moins chers que le métal usiné traditionnellement, peuvent être livrés en une fraction du temps et offrent des fonctionnalités que les pratiques d'usinage conventionnelles ne seraient pas en mesure d'atteindre", poursuit Martin. « Un client parcourrait 12 modèles différents par an usinés à partir d'aluminium. Nous avons considérablement réduit leur temps de mise sur le marché, produisant plus d'une douzaine de modèles en plusieurs mois. Ils peuvent désormais passer de la conception aux pièces en rayon en quelques semaines. » Un autre avantage est la possibilité de renforcer les projections, appelées « piquets ». Ces extrusions à rapport d'aspect élevé se retirent souvent. Le renforcement empêche cela, tout en maintenant des tolérances serrées.
En savoir plus sur les avantages de Fortify dans l'outillage de moulage par injection dans le magazine sœur de CW Additive Manufacturing.
Matériaux ouverts, nouveaux développements
Fortify poursuit une approche ouverte des matériaux. « Nous ne voulons pas limiter la capacité de croissance et d'exploration de nos clients au sein de l'additif », explique Karlo Delos Reyes, vice-président des applications de Fortify. « Nous garantissons à nos clients la flexibilité et les meilleurs matériaux disponibles en adoptant l'innovation ouverte. »
« Nous travaillons en partenariat avec de grands fabricants de polymères et personnalisons la chimie de surface des additifs », explique Martin. Il note que chaque charge a ses propres avantages et inconvénients en termes de résistance à l'usure, de performances en température, etc. « Pour les fibres, la longueur varie de quelques µm à quelques mm, selon l'application. Lorsque nous avons besoin d'une résolution de surface, nous utilisons un pourcentage plus élevé d'additifs de plus petite longueur. Lorsque nous pouvons nous permettre une surface plus rugueuse, mais que nous souhaitons optimiser la résistance à la traction, par exemple, nous utilisons des additifs pour fibres plus longues. »
L'une des stratégies de Fortify consiste à s'associer avec des leaders de l'industrie et des fournisseurs pour tirer parti de l'expertise et permettre la pollinisation croisée des idées. Fortify a récemment annoncé un partenariat avec DSM Additive Manufacturing (Hoek van Holland, Pays-Bas et Elgin, Illinois, États-Unis) pour développer des matériaux composites hautes performances qui seront utilisés dans les systèmes d'impression de Fortify pour obtenir des performances mécaniques et thermiques accrues. « Ils élargiront notre palette de résines », déclare Martin, « et nous sommes ravis de travailler avec eux pour développer des résines de pointe. »
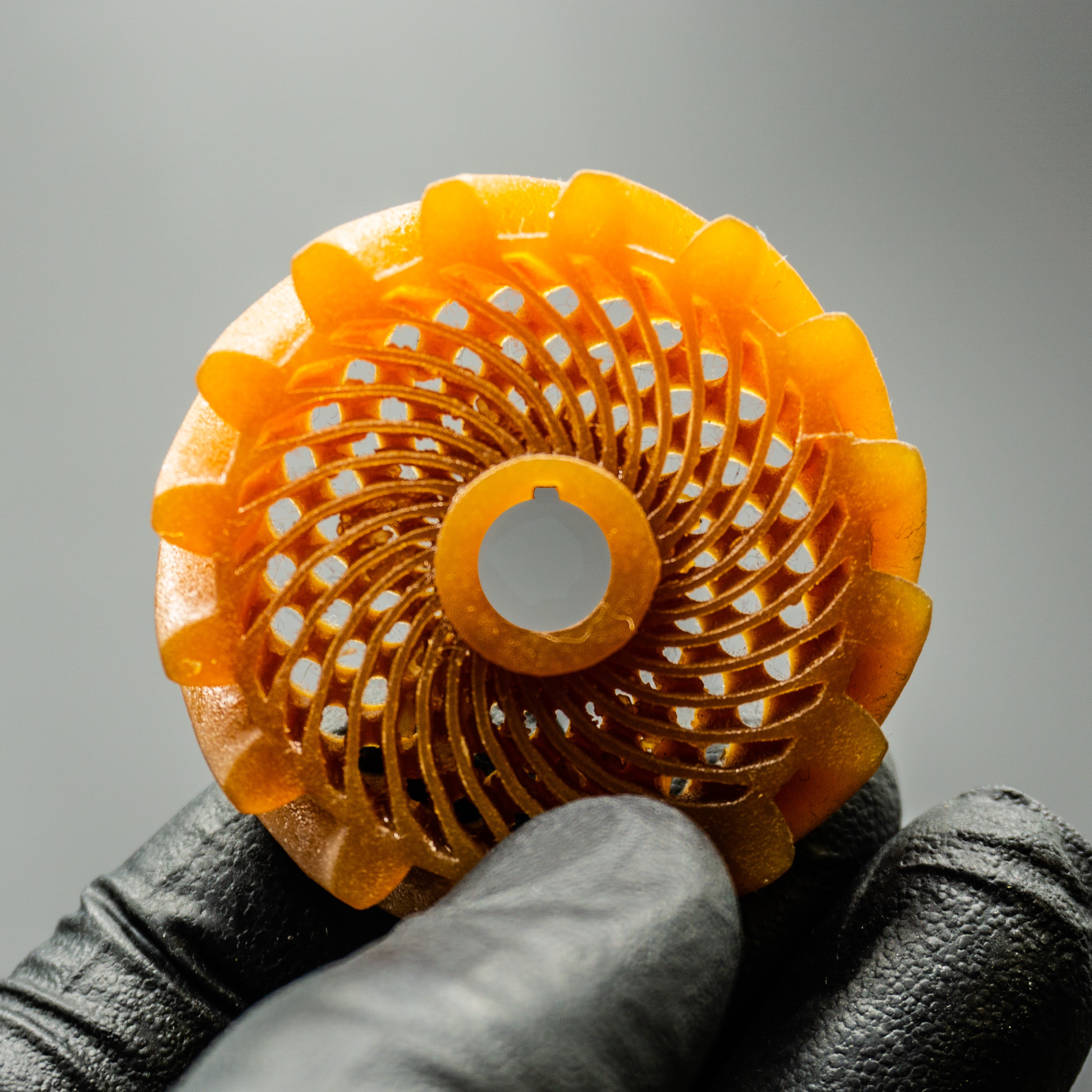
Pièce composite renforcée de fibre de verre réalisée avec Fluxprint. SOURCE | Fortifier.
Renforcement dans la direction Z et applications
Fluxprint imprime toujours par couches. Alors, est-il possible d'obtenir un renforcement dans la direction z ? « Si vous imprimez des fibres de 2 millimètres de long, vous ne pouvez pas les placer dans la direction z », explique Martin. « Mais vous pourriez être plus court fibres dans l'orientation z. Nous envisageons plusieurs échelles de longueur et nous voyons cela se développer à l'avenir pour un transfert de charge optimisé. »
Fortify produit déjà des pièces pour les drones, y compris des hélices, et voit de nombreuses autres applications de ce type dans l'aérospatiale. « Nous avons une petite zone de construction, nous nous concentrons donc sur les applications où nous pouvons facilement répondre à des volumes de pièces plus petits », explique Martin. « Il s'agit d'un écosystème mature, mais nous offrons un nouveau niveau de performances en termes de propriétés mécaniques à des températures et des tolérances élevées. » Il cite la capacité d'améliorer la température de déflexion thermique d'une pièce et explique qu'il existe des dizaines de pièces sous le capot dans l'automobile qui doivent fournir résistance et rigidité tout en étant exposées à des températures de 160 °C. « De telles pièces aux géométries complexes se prêtent bien à l'impression 3D avec notre technologie. Par rapport à la méthode actuelle de moulage et d'usinage de pièces en PEI (polyétherimide), nous offrons des performances plus élevées, un délai de livraison plus court et un potentiel élevé pour un coût inférieur ."
L'outillage est également un marché actuel, y compris les matrices, les gabarits et les montages pour le moulage par injection. « Encore une fois, nos pièces sont plus rigides, plus solides et ont une résistance à la température plus élevée, maintenant la précision dimensionnelle en service », explique Martin. « Mais leur vraie valeur réside dans pas nécessitant un post-traitement important, comme ce qui est nécessaire lors de l'utilisation de machines EDM, et pourtant ils correspondent à la qualité des montages fabriqués avec ces méthodes traditionnelles, y compris le fraisage CNC. "
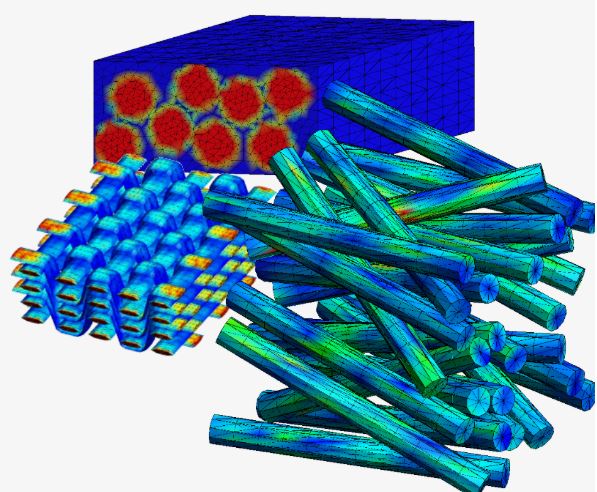
Origine | Multimécanique
Faire progresser la prochaine génération de composites multi-échelles et multifonctionnels
Fortify s'est associé à MultiMechanics (Omaha, Neb., États-Unis), un développeur de logiciels de modélisation et de simulation multi-échelles pour les matériaux avancés. Ce partenariat est intéressant pour plusieurs raisons. Tout d'abord, Fortify utilisera le produit phare de MultiMechanics, MultiMech, pour prédire les performances des pièces et optimiser leur conception et l'orientation des fibres avant leur impression. Ainsi, MultiMech agira pour fournir les commentaires pour la conception itérative en boucle fermée , permettant aux utilisateurs de personnaliser et d'optimiser plus rapidement les pièces composites Fluxprinted. Fortify et MultiMechanics prévoient également d'intégrer MultiMech dans INFORM de Fortify logiciel de conception générative et de contrôle d'impression. Ainsi, de la conception aux tests virtuels en passant par l'impression, toutes les fonctions seront contrôlées au sein d'un seul flux numérique.
Pour le deuxième point, il est important de comprendre ce que propose MultiMechanics à travers son logiciel MultiMech :
- Analyse par éléments finis multi-échelles , y compris la modélisation d'un nombre pratiquement illimité d'échelles (par exemple, nano, micro, pli, stratifié, pièce).
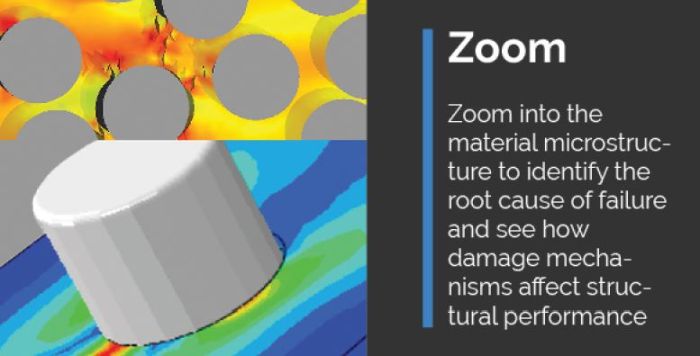
- Génération automatique des microstructures complexes d'éléments finis en 3D et la modélisation de presque toutes les microstructures de matériaux, y compris les fibres continues et coupées, les particules, les vides, les mousses, les tissus, etc.
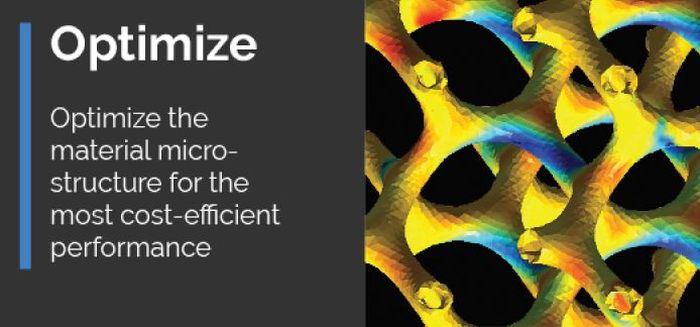
- Modéliser les effets des constituants à micro-échelle, y compris interactions , fractions volumiques, distribution et orientation, plus importation p variation induite par les processus à partir de programmes (par exemple Moldex3D, Moldflow).
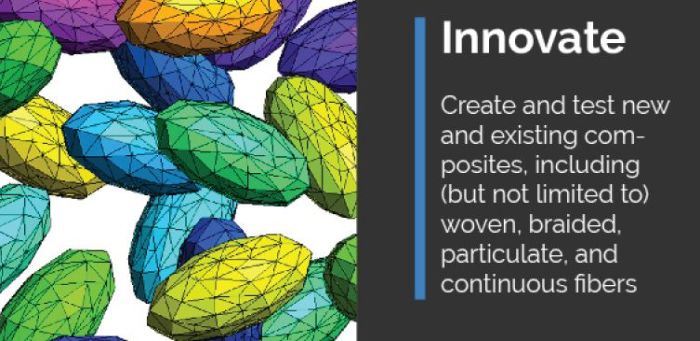
- Analyser comment les variations de fabrication affectent les performances des pièces et effectuez da modélisation de mage y compris la transition à plusieurs échelles de microfissures en macrofissures.
Cela revient à la raison pour laquelle Martin et Erb ont commencé Fortify en premier lieu. Dans leur article de 2015, « Conception d'architectures de renforcement composites bioinspirées via l'impression magnétique 3D », ils déclarent :
Martin et Erb discutent des composites naturels qui utilisent des fibres discontinues et des particules de renforcement organisées en architectures complexes à plusieurs échelles pour obtenir des propriétés supérieures par rapport à leurs constituants. Un exemple donné par Qunfeng Cheng dans un Materials Today de 2017 l'article est de la nacre dans des coquilles d'ormeau. Composée de 95 % en volume d'aragonite inorganique et de 5 % en volume de matrice de protéines organiques, la résistance à la rupture de la nacre est 3000 fois plus que celui de l'aragonite. Cheng note que cela montre un "effet d'amplification" des propriétés mécaniques qui va bien au-delà de la règle des mélanges dans les composites traditionnels .
Dans les Matériaux avancés 2018 article, "Additive Manufacturing as a Method to Design and Optimize Bioinspired Structures", les auteurs Audrey Velasco-Hogan, Jun Xu et Marc A. Meyers affirment que la structure hiérarchique des matériaux comme la nacre, l'os, le bambou et les coquilles de crustacés sont ce qui permet leur combinaison impressionnante de résistance, de module, de légèreté, de ténacité et de résistance à la fatigue. Leurs particules/filaments constitutifs et leur matrice sont organisés différemment à chaque niveau (par exemple, nano-, micro-, méso-, macro-), variant les propriétés à chaque niveau (c'est-à-dire un composite à plusieurs échelles). Lorsqu'il est combiné avec des interfaces efficaces entre les niveaux, cette structure hiérarchique fonctionne en synergie pour atténuer la propagation des fissures et améliorer la ténacité tout en maintenant la dureté - quelque chose qui n'a pas encore été atteint en céramique après environ un siècle d'essais.
Avenir des composites et INFORM
C'est l'avenir des composites :concevoir des composites hiérarchiques aux propriétés uniques sur mesure pour des applications précises. Et il est déjà avancé, rapidement. Par exemple, l'Institut des structures et de la conception du Centre aérospatial allemand (DLR) de Stuttgart a également établi un partenariat avec MultiMechanics comprendre comment le changement de température affecte la microstructure et le comportement des matériaux des composites à matrice céramique (CMC) . Cette analyse est jugée cruciale pour la future production de composants CMC du DLR, y compris les tuyères pour les fusées et les systèmes de protection thermique pour les véhicules de rentrée, entre autres. « Notre travail chez MultiMechanics au cours des dix dernières années a été consacré à connecter avec précision le comportement microstructural des matériaux avancés à la performance globale de la pièce et sa fabrication », déclare le Dr Flavio Souza, président et directeur technique de MultiMechanics. « MultiMech nous permet de modéliser les fissures microstructurales et de déterminer comment elles affecteraient l'ensemble de la pièce composite », déclare Neraj Jain, chef de groupe au département des composites et structures céramiques du DLR. « L'intégration efficace de MultiMech avec nos autres outils FEA comme Abaqus et ANSYS augmente notre productivité et nous rapproche de notre objectif d'optimiser virtuellement les matériaux CMC . "
Une fois ces composites optimisés virtuellement, ils sont ensuite imprimés, avec MultiMech intégré au logiciel INFORM de Fortify, qui est déjà orienté vers des architectures organiques à charge optimisée via son épine dorsale de conception générative . (Notez que l'unité commerciale Composite Materials de Solvay a également investi dans la technologie MultiMechanics et l'impression 3D.)
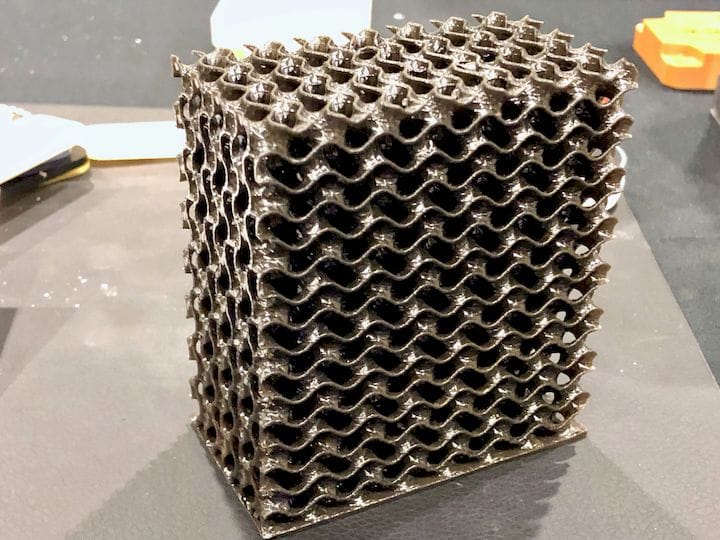
Treillis renforcé de fibres, conception fournie par nTopology. Origine | Fortifier.
« INFORM utilise algorithmes avancés pour optimiser l'orientation des fibres pour chaque pièce », explique Martin. « Là où traditionnellement, le flux de travail d'impression 3D commence par STL pour découper le design, le nôtre commence par FEA (un modèle avec contrainte et déformation), puis décide dans quels voxels séparer cette conception modélisée et comment orienter les fibres. Nous progressons par itérations, alignant les fibres avec les vecteurs de champ de contrainte/déformation, puis simulons le comportement de cette impression et utilisons ces données pour affiner et optimiser la conception, réalisant une conception générative microstructurale ."
Seul le début
A noter que ces futurs composites intègrent une gamme de matériaux. Le Naval Research Laboratory (NRL, Arlington, Va., U.S.) développe des CMC utilisant une matrice céramique avec un renfort céramique secondaire via des nanoparticules et/ou des filaments. Ces CMC peuvent également utiliser un renfort de fibres continues. En d'autres termes, différents constituants et architectures peuvent être utilisés à chaque niveau pour la ténacité améliorée et les propriétés électriques et thermiques adaptées requises (par exemple, en hypersonique, en savoir plus dans mon article de juillet 2019 sur les nanocomposites).
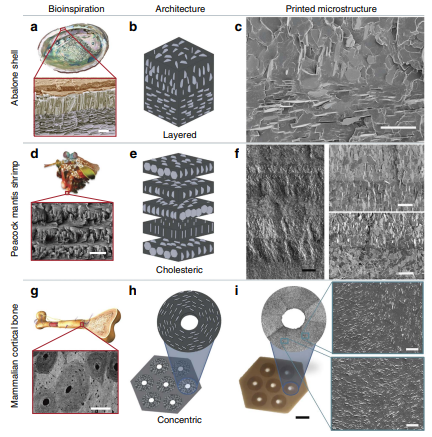
SOURCE | Figure 3, « Conception d'architectures de renforcement composites bioinspirées via l'impression magnétique 3D » par Joshua J. Martin, Brad E. Fiore et Randall M. Erb, Nature Communications, tome 6 (2015).
Des composites hiérarchiques sont également imprimés et testés à l'aide d'encres époxy renforcées et de matrices polymères thermoplastiques. C'est peut-être le plus gros avantage pour Fortify en tant que startup. Il ne s'agit pas seulement de préparer les composites du futur, il les conçoit et les produit déjà. Et même si ce qu'il a déjà accompli est impressionnant, ce n'est que le début.
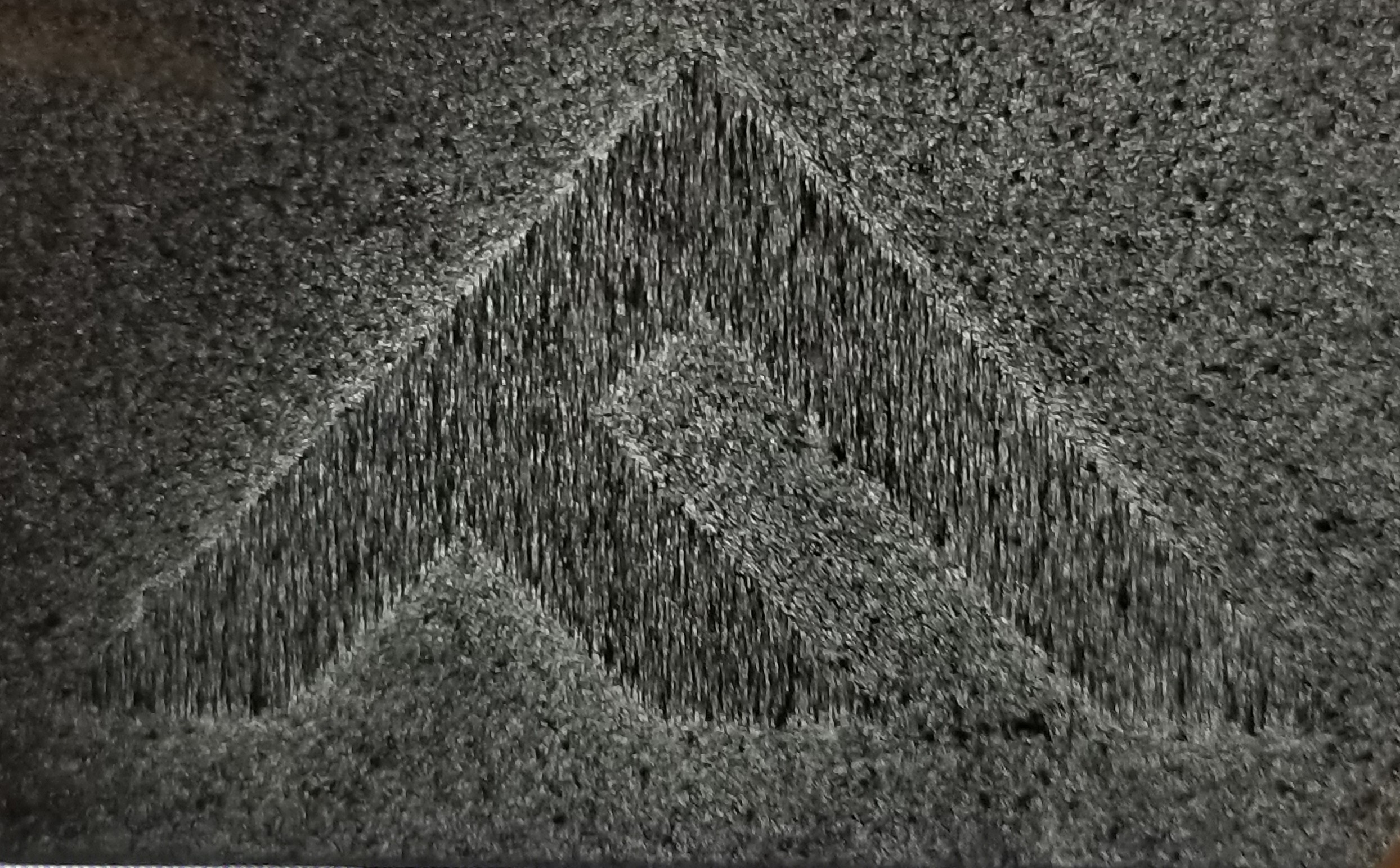
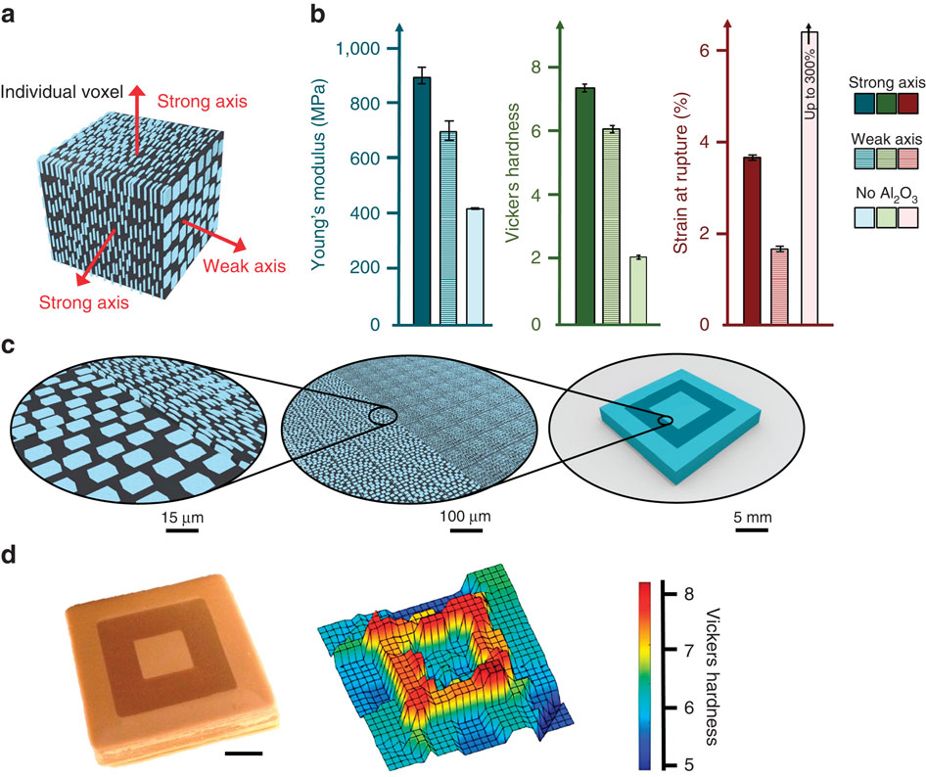
Résine
- Les 3 étapes de base de l'impression 3D
- L'impression 3D multi-matériaux pourrait-elle être la prochaine étape pour la FA ?
- L'ABC de l'impression 3D
- L'évolution de l'impression 3D
- Collèges communautaires :former la prochaine génération de fabricants
- Impression 3D de composites avec fibre continue
- Matériel pour la prochaine génération de capteurs intelligents
- Une source térahertz ultra-mince ouvre la voie à la prochaine génération de technologies de communication
- COVID-19 :Demande pour la prochaine génération d'usines intelligentes