Faire progresser la fabrication additive pour exploiter l'anisotropie
Fondée en 2014 par le PDG Fedor Antonov, Anisoprint (Esch-sur-Alzette, Luxembourg) fait partie d'un nombre croissant d'entreprises technologiques faisant progresser l'impression 3D de composites avec fibre continue . Il préfère cependant être connu comme un pionnier dans l'éloignement de la fabrication additive (FA) des métaux aux composites.
« Les propriétés directionnelles des composites sont un avantage, pas un inconvénient », déclare Antonov. « Les composites unidirectionnels en fibre de carbone sont plus solides et plus légers que les métaux. La fabrication conventionnelle et la FA à base de métaux considèrent l'anisotropie directionnelle des composites comme un inconvénient qui doit être atténué. Mais l'approche d'Anisoprint exploite cette anisotropie, en orientant et en plaçant les fibres pour répondre avec précision aux charges structurelles, réduisant considérablement le poids des pièces tout en conservant une résistance et une rigidité élevées. »
Permettre des composites plus efficaces
Antonov souligne que la fabrication de composites conventionnels a généralement utilisé les pratiques de l'industrie des métaux, y compris les stratifiés quasi-isotropes, le perçage de trous et les fixations mécaniques. « Ces derniers annulent les avantages en termes de poids et de performances des composites », explique Antonov. « La technologie d'anisoimpression offre une méthode de production automatisée beaucoup plus rapide et plus flexible. » Il offre également un moyen d'obtenir les structures plus efficaces actuellement produites par l'optimisation de la topologie et la conception générative logiciel.
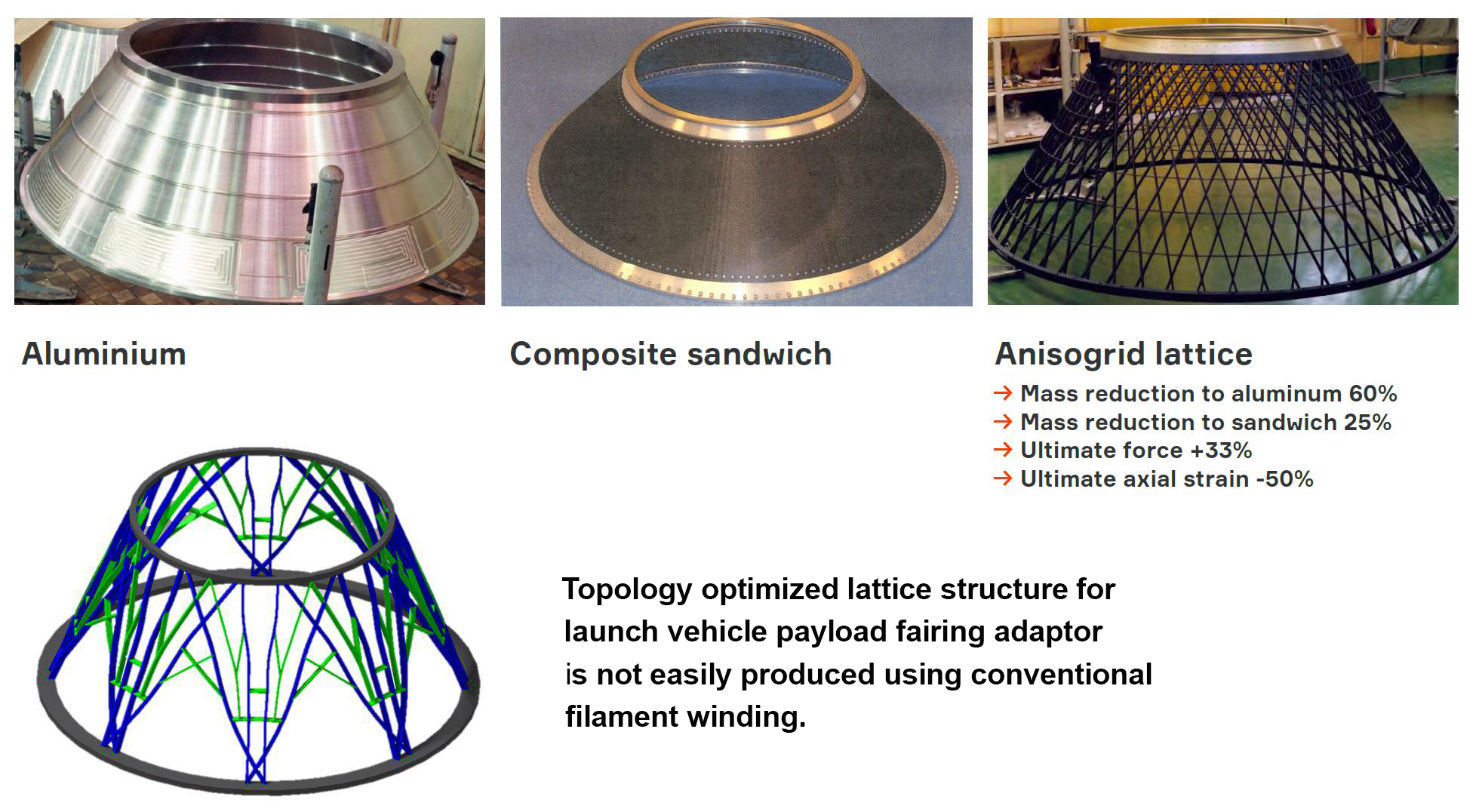
« Les structures les plus efficaces de la nature, comme les arbres et les os, exploitent les propriétés directionnelles, orientant les matériaux porteurs principalement le long des chemins de charge », affirme Antonov. Cependant, ces types de structures optimisées en topologie sont difficiles à produire. Par exemple, les structures en treillis qui ont permis des adaptateurs de carénage de charge utile solides et légers pour les engins spatiaux, sont généralement produites à l'aide d'un enroulement filamentaire. Cependant, une version optimisée pour la topologie , offrant une économie de poids supplémentaire de 30 % , n'est plus facile à produire avec les procédés composites conventionnels, ni avec le placement automatisé de fibres (AFP) plus récent.
« Les structures enroulées de filaments anisogrilles classiques sont obtenues à l'aide de rainures dans l'outillage, et une fraction volumique de fibres relativement faible dans les nervures permet de les croiser », explique Antonov. « Ces types de structures anisogrilles étaient notre objectif initial. Mais cela ne fonctionne pas avec l'AFP car votre contenu en volume de fibres est toujours constant, et il n'est pas possible de croiser des nervures sans couper les fibres ou des variations d'épaisseur locales. »
(Remarque :pour une étude plus approfondie à ce sujet, voir https://www.researchgate.net/publication/321081593_Anisogrid_Payload_Adaptor_Structure_for_Vega_Launcher)
Direction fibre
L'orientation des fibres est une technique actuellement appliquée à la production de composites à l'aide de l'AFP qui permet d'appliquer des fibres dans des chemins curvilignes - l'AFP a traditionnellement utilisé des chemins linéaires droits. L'orientation des fibres permet d'optimiser le chemin des fibres, et donc la réponse mécanique du panneau composite, pour présenter des performances supérieures à celles des stratifiés conventionnels. Dans un exemple, cette approche produit un panneau de substrat composite pour un panneau solaire de vaisseau spatial qui a une première fréquence naturelle supérieure de 44 % (minimise l'amplitude des vibrations et permet un amortissement plus rapide) qu'un panneau conventionnel équivalent avec des chemins de fibres rectilignes et la même masse. Alternativement, un panneau de poids inférieur peut être obtenu pour les mêmes performances de fréquence.
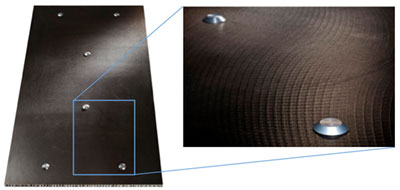
La direction par fibre permet la conception et la fabrication de pièces comme des panneaux structurels pour satellites ou des composants de machines à grande vitesse avec de très hautes performances. Il s'agit d'un processus reproductible, permettant d'obtenir une qualité élevée et constante et permettant de nouvelles conceptions innovantes. Il peut également être utilisé pour réduire le poids pour la même conception géométrique. SOURCE | "Fibre-Steering technology for advanced composite panels" (le lien original est donné ici mais n'est plus disponible via le serveur esa-tec :http://www.esa-tec.eu/space-technologies/from-space/fibre-steering -technologie-pour-panneaux-composites-avancés/)
« L'anisoimpression est une combinaison de structures en treillis et d'orientation des fibres utilisées pour obtenir des pièces optimisées en termes de topologie », explique Antonov. « Il s'agit d'une technologie clé pour les composites imprimés. Par exemple, comment construisez-vous un panneau de fuselage pour un avion commercial qui a des découpes ou des trous ?
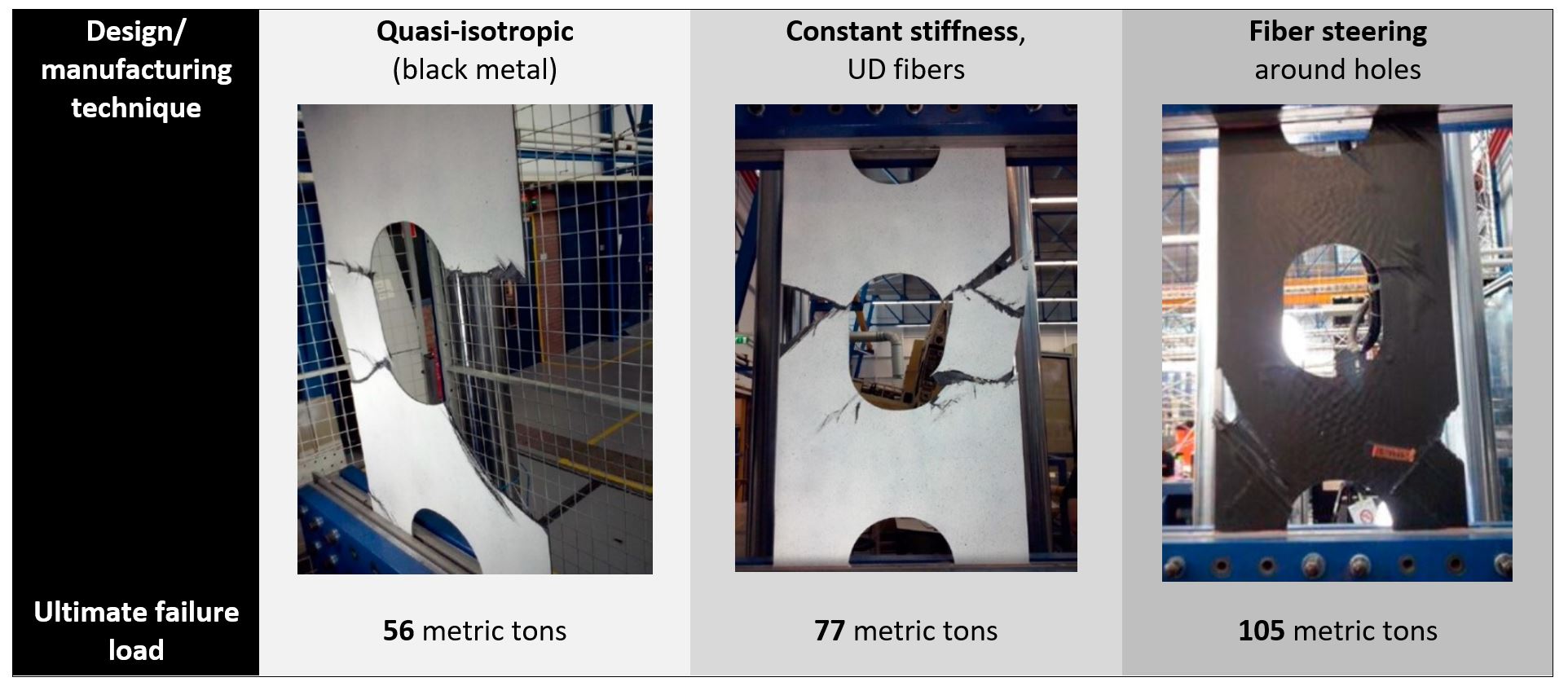
Il donne trois techniques différentes, qui sont utilisées pour produire des échantillons composites de même épaisseur et poids, chacun avec des trous usinés CNC (voir tableau ci-dessous). Il note que lors des tests de compression, l'échantillon fabriqué avec la direction des fibres a une charge de compression ultime deux fois supérieure à celle d'un composite quasi-isotrope (« aluminium noir ») et 30 % supérieure par rapport à un stratifié UD à rigidité constante. « Ainsi, la direction par fibre est un outil puissant », explique Antonov. « L'anisoprint s'orientera vers le pilotage de la fibre AFP à mesure que nous augmenterons le volume et la productivité de la fibre, et l'AFP évoluera vers nous avec plus de flexibilité.
La « flexibilité » à laquelle Anotov fait référence est une mesure de la possibilité de placer une fibre le long de n'importe quel chemin dans un espace tridimensionnel. Arevo, une autre entreprise qui commercialise l'impression 3D à fibre continue, affirme disposer de ce type de flexibilité. « La technologie d'Arevo n'est pas très différente de celle des sociétés AFP comme Coriolis, Automated Dynamics, Electroimpact, etc. », explique Antonov. «Ils l'ont simplement miniaturisé et au lieu d'utiliser un ruban fin et large, ils en utilisent un épais et étroit avec une tête AFP laser. C'est tout pareil." Notez que la technologie d'impression 3D d'Arevo est basée sur un robot depuis le début. Comment la technologie d'Anisoprint évoluera-t-elle à mesure qu'elle passera aux plates-formes robotiques ?
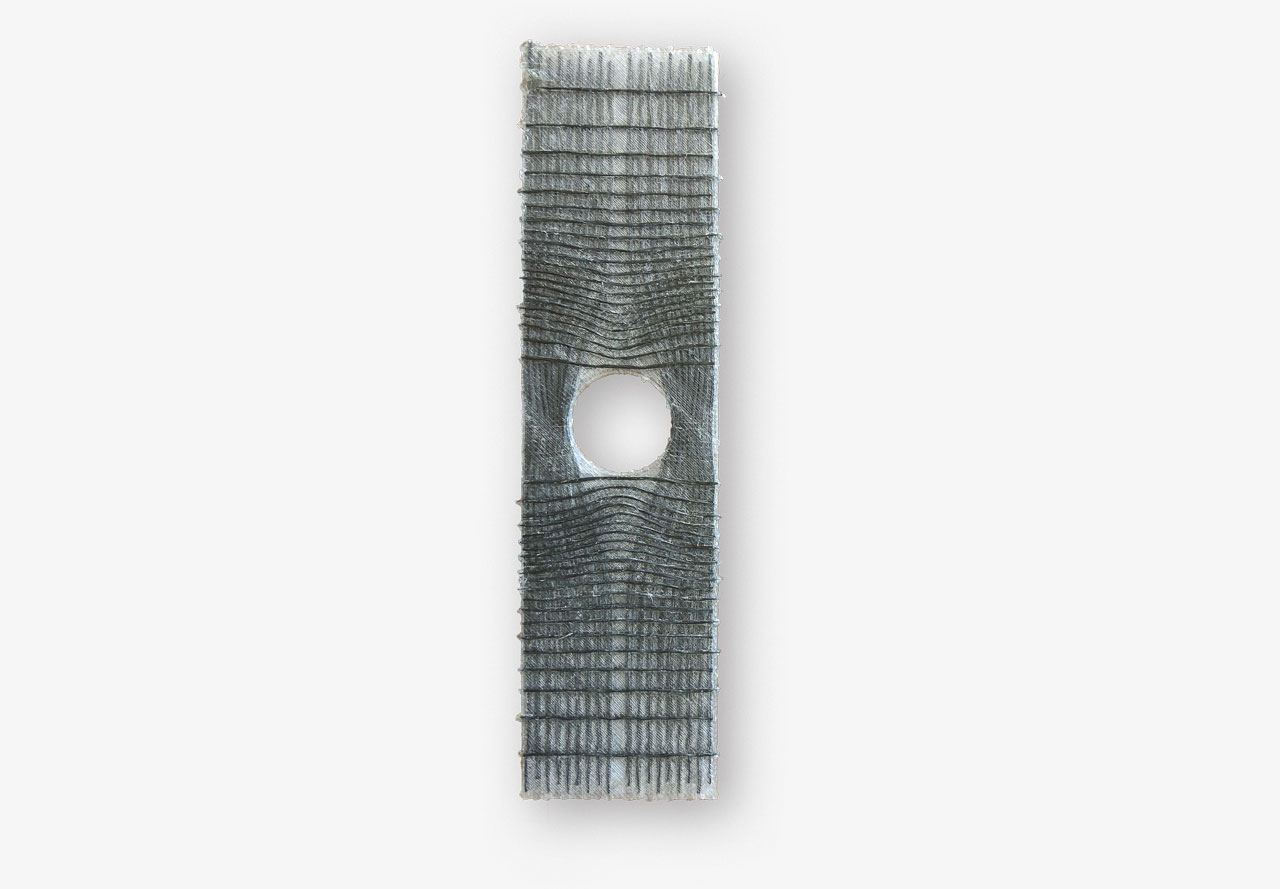
Exemple d'échantillon composite imprimé en 3D Anisoprint à l'aide de la direction de fibre.
Historique d'Anisoprint et approche TS-TP
Antonov et ses co-fondateurs (Andrey Azarov, Alexey Khaziev, Mikhail Golubev et Zafer Gürdal) étaient dans une nouvelle université dans la partie ouest de Moscou appelée Skolkovo Institute of Science and Technology (Skoltech), qui a été créée en 2011. En 2014, Antonov travaillait à la construction du nouveau centre de technologie des composites de Skoltech et a commencé à développer l'impression 3D. Le directeur du centre des composites à l'époque était Zafer Gürdal, qui est parti en 2015, retournant au McNair Center de l'Université de Caroline du Sud. Ce dernier est aujourd'hui connu pour sa R&D dans les composites et l'impression 3D en fibre continue.
« Nous avons décidé de nous séparer de Skoltech lorsque Zafer Gürdal est parti », explique Antonov. « Nous avions développé un prototype de tête d'impression CFC à l'été 2015. Notre prochain objectif était de développer une imprimante de bureau. »
Anisoprint a lancé son imprimante de bureau Composer en 2017. Semblable aux imprimantes à fibres continues Markforged, Composer d'Anisoprint utilise deux buses d'impression :une pour le renforcement des fibres continues et une pour la matrice plastique. Installé dans une chambre d'impression en verre, le lit d'impression en verre de Composer peut être chauffé jusqu'à 120 °C, ce qui permet de minimiser les effets du rétrécissement. Actuellement, il est disponible en deux tailles :
- A3 (420 par 297 par 210 millimètres)
- A4 (297 par 210 par 147 millimètres)
Avec un diamètre de buse standard de 0,4 millimètre, la vitesse d'impression de Composer est de 10 à 80 millimètres/seconde sans renforcement et de 1 à 20 millimètres/seconde avec un renfort en fibre continue. Anisoprint peut extruder de nombreux plastiques, notamment le PLA, le PETG, l'ABS, le nylon et le PC. Elle peut les renforcer avec ses matériaux composites en fibre de carbone (CCF) et a récemment lancé un matériau d'impression composite en fibre de basalte (CBF).
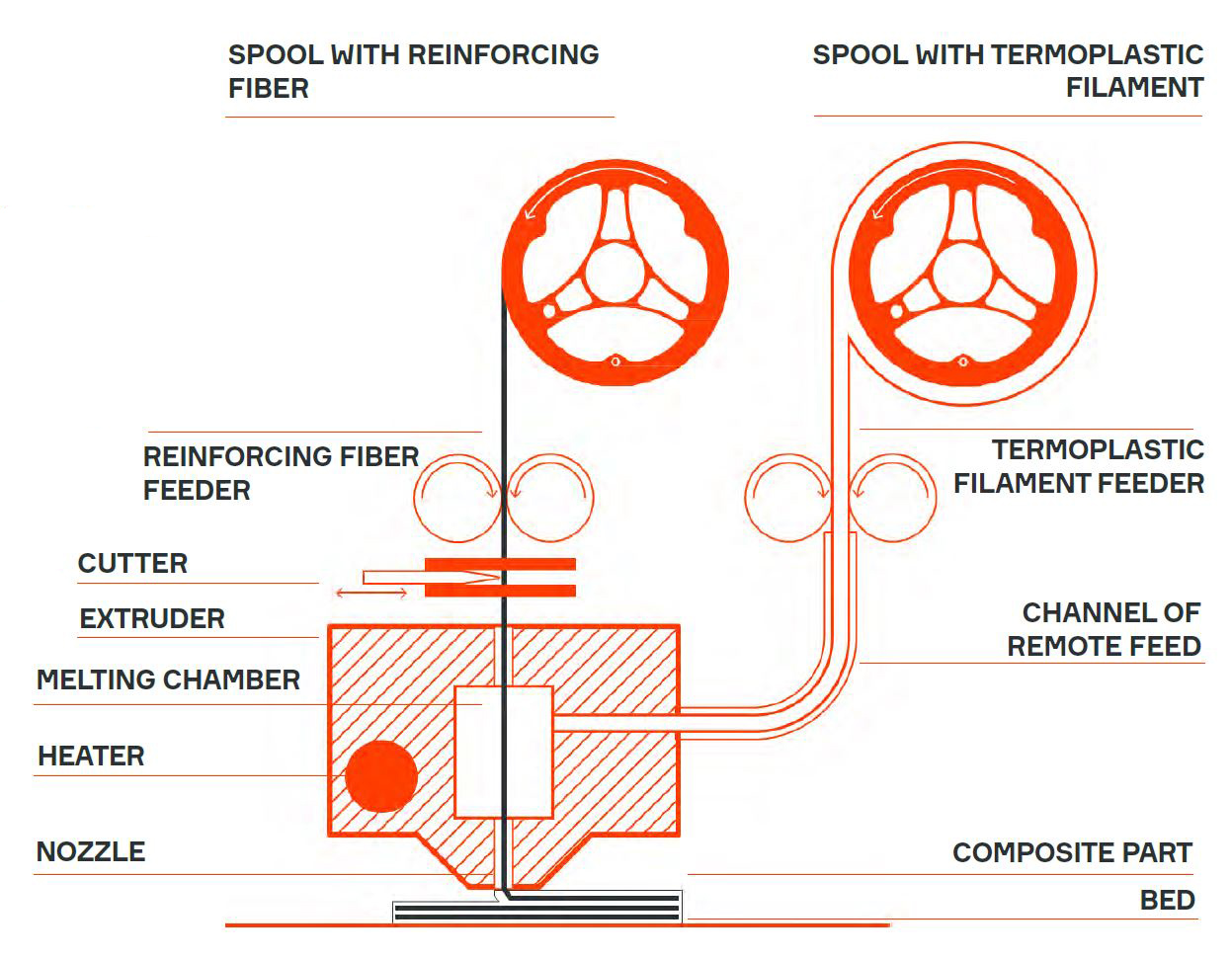
Cependant, Anisoprint est assez différent des autres technologies d'impression 3D à fibre continue car il imprègne d'abord le renforcement de fibres continues avec un thermodurci polymère et l'extrude ensuite dans le filament thermoplastique fondu pendant l'impression. "Cette approche à deux matrices garantit une faible porosité, une bonne adhérence de la fibre au polymère et d'excellentes propriétés mécaniques," affirme Antonov.
Il poursuit :« L'inventeur de l'anisogrille à enroulement filamentaire pour l'adaptateur de charge utile du lanceur Proton M, V.V. Vasiliev, qui fait partie de notre comité consultatif, a en fait montré que cette idée d'utiliser une double matrice thermodurcissable-thermoplastique Les matériaux (TS-TP) présentent des avantages par rapport à l'utilisation d'une seule matrice thermodurcissable ou thermoplastique. Les matériaux de matrice thermodurcissables ont des problèmes de fragilité, de sorte que la matrice commence à se fissurer beaucoup plus tôt que la fibre ne se rompt. Vasiliev a prouvé qu'il pouvait atténuer cela avec une approche à double matrice. »
Le thermodurcissable utilisé par Anisoprint est un époxy à plusieurs composants et les stratifiés imprimés finaux ont une teneur en fibres allant jusqu'à 45%, selon les tests de l'Université technique de Munich (TUM).
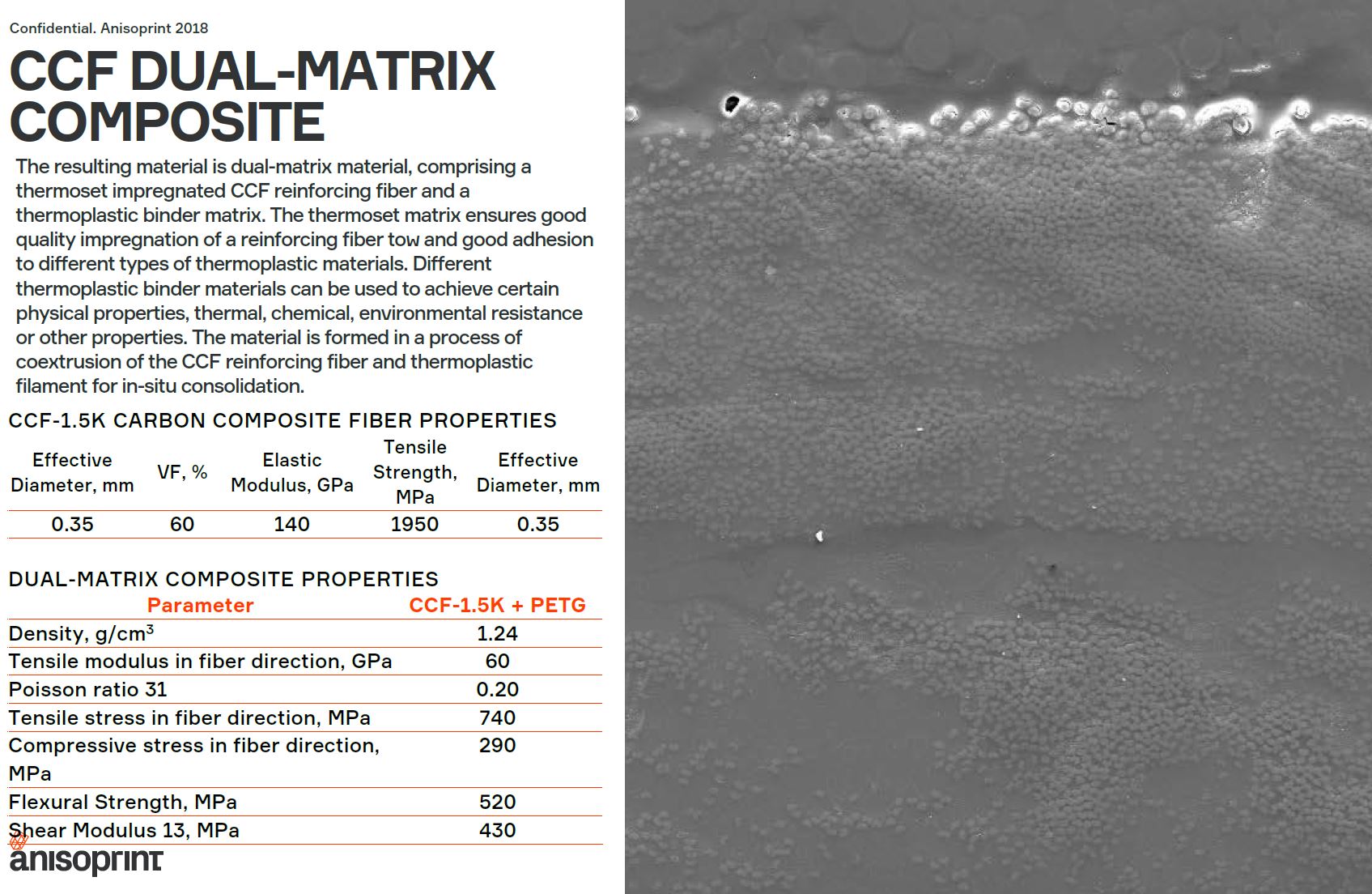
Les offres brevetées d'Anisoprint incluent :
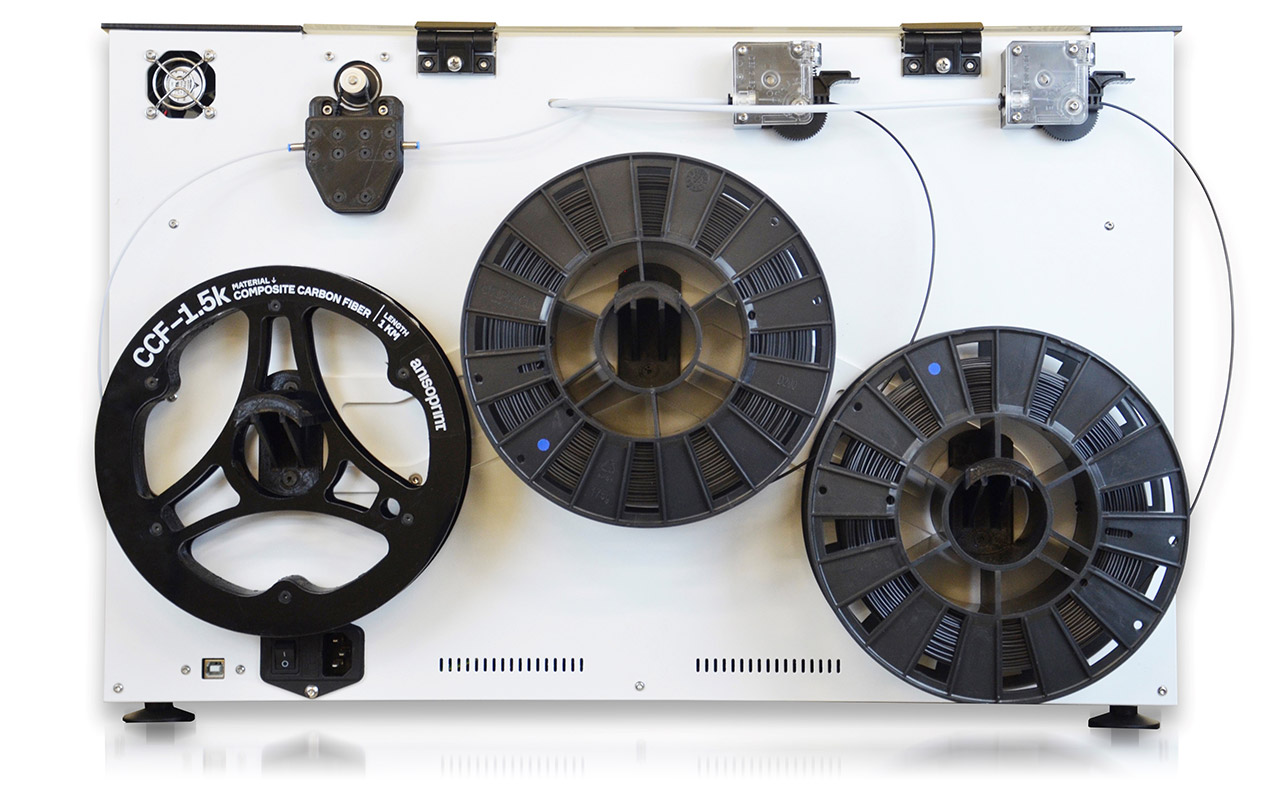
Technologie de coextrusion de fibres composites (CFC) pour la fabrication additive utilisant différents polymères thermoplastiques renforcés de fibres continues (par exemple, le carbone, le basalte) qui sont consolidés et durcis dans un processus automatisé en une seule étape qui ne nécessite ni outillage ni post-traitement.
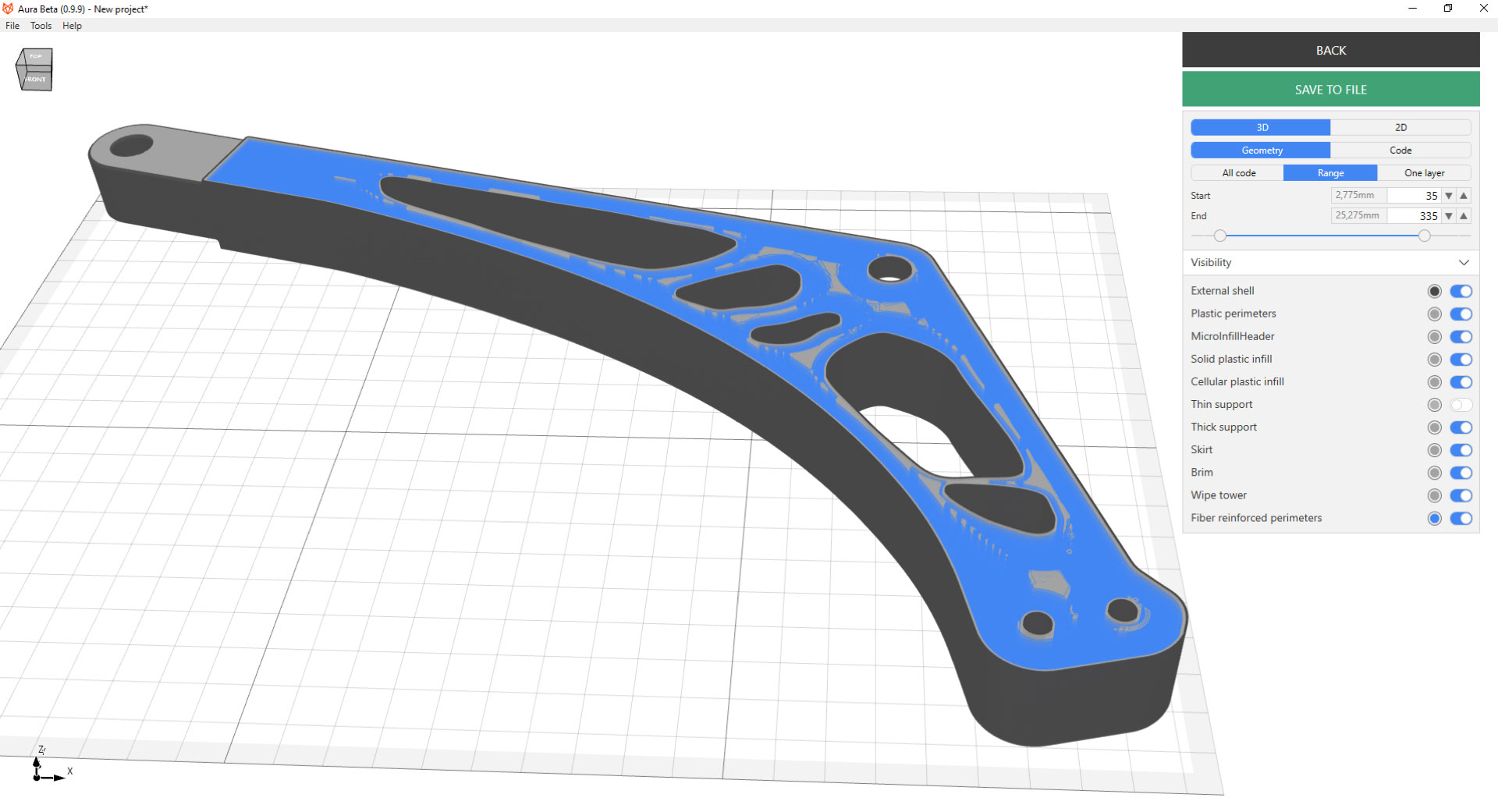
Logiciel Aura slicer qui prépare des modèles 3D pour la fabrication de pièces à l'aide de l'imprimante Composer CFC ainsi que des imprimantes FFF conventionnelles.
Imprimante 3D de bureau Composer disponible en trois tailles (A4, A3, A2).
PROM famille de systèmes d'impression industriels avec options de robot et de portique, disponible dans le commerce à partir de 2020.
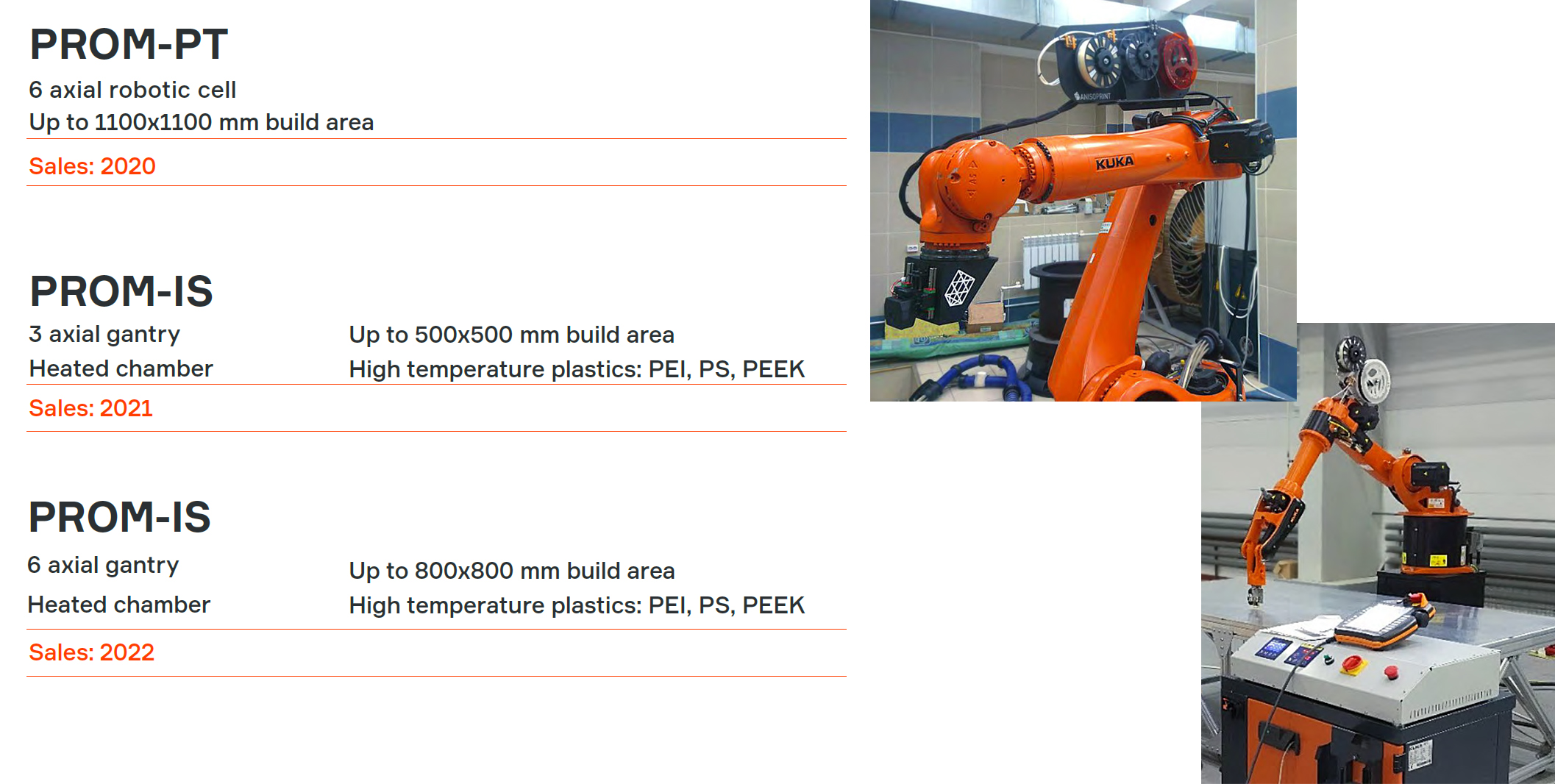
Développement de robots par rapport au bureau
« Le robot a une tête d'impression différente car vous devez déplacer la tête pour s'adapter et atteindre les espaces restreints pendant l'impression », explique Antonov. « Dans un plan 2D, ce n'est pas un problème. Mais dans l'espace 3D, vous devez mettre de la fibre là où il y a déjà une certaine structure. L'accessibilité idéale est obtenue avec une aiguille. Nous avons donc besoin d'un compromis, d'une tête d'impression plus en forme d'aiguille. »
Il note d'autres différences, comme les contrôles industriels. « Les imprimantes de bureau sont basées sur l'électronique grand public, comme Arduino. Mais pour les systèmes robotiques plus grands, vous avez besoin d'un contrôle de mouvement industriel et d'interfaces et de toutes sortes d'assurance qualité in situ, telles que la mesure laser, que Markforged a sur sa plus grande machine. Vous devez également modifier les capteurs et les commandes de chauffage/refroidissement. Il ajoute que tout cela prend du temps et des ressources, et que leur priorité au cours des deux dernières années était de développer la machine de bureau, mais maintenant ils travaillent également sur les systèmes robotiques. »
Logiciel :Aura
Antonov décrit le logiciel d'Anisoprint comme flexible, permettant aux utilisateurs débutants et avancés. « Le logiciel est facile à utiliser, mais il est important que les laboratoires de R&D aient la possibilité de modifier les paramètres d'impression », explique-t-il. En effet, les clients incluent l'institut de recherche MFPA (Weimar, Allemagne), le Brightlands Materials Center (Geleen, Pays-Bas) et l'Université technique de Munich ainsi que des fabricants tels que Schunk Carbon Technology, Airbus et BMW.
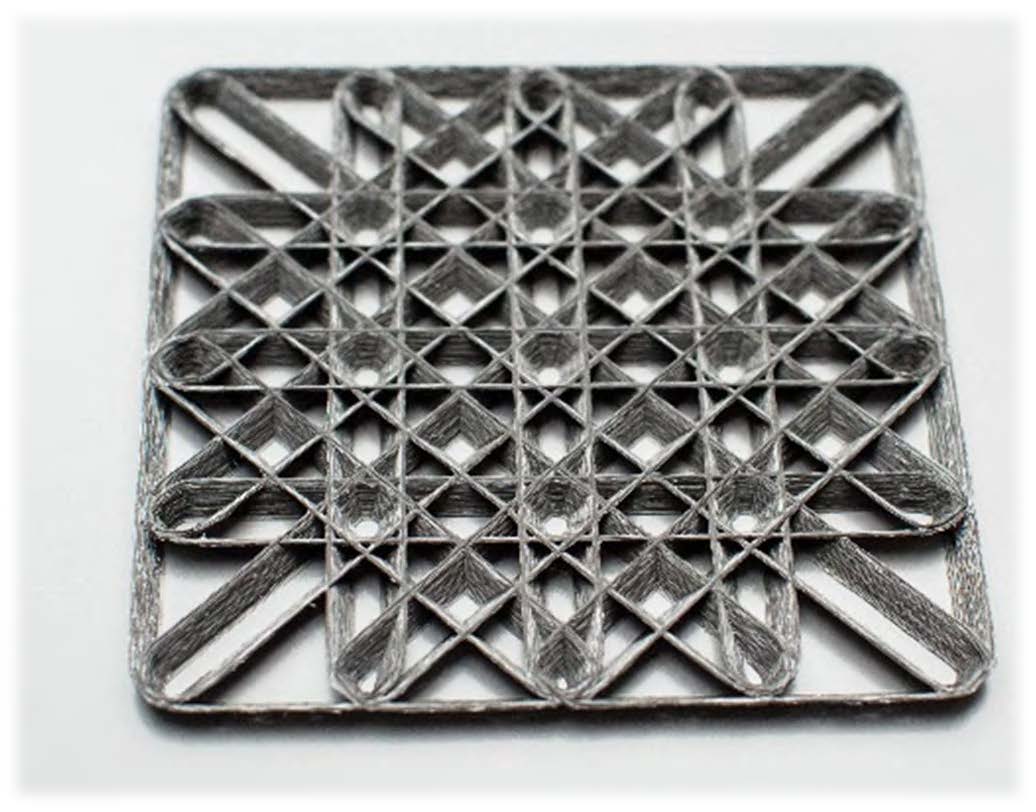
Anisoprint a des pièces microsatellites composites imprimées en 3D avec une réduction de poids allant jusqu'à 45% par rapport aux métaux légers.
Partenariats pour des solutions continues
Anisoprint, qui se présente comme une plate-forme de matériaux ouverte, cherche également à développer davantage de partenariats pour de nouveaux matériaux et pièces d'impression. En juin, elle a annoncé un accord avec la société maltaise Thought3D pour utiliser les adhésifs Magigoo de cette dernière. Ceux-ci collent la première couche d'impression sur le lit d'impression, empêchant le décollement partiel. « Une mauvaise adhérence de la première couche est l'un des problèmes les plus courants qui peuvent ruiner les pièces imprimées, et pas nécessairement au début de la construction », explique Antonov. « Ceci est particulièrement important pour notre système de matériaux ouverts, où le client peut choisir parmi différents types de thermoplastiques. Chacun nécessite des paramètres d'impression différents et c'est pourquoi nous avons introduit plusieurs paramètres de première couche dans notre logiciel de trancheuse Aura. C'est aussi pourquoi nous inclurons des bâtons Magigoo dans chaque boîte Composer pour nous assurer que nos clients auront une solution appropriée en main pour une bonne adhérence de la première couche. »
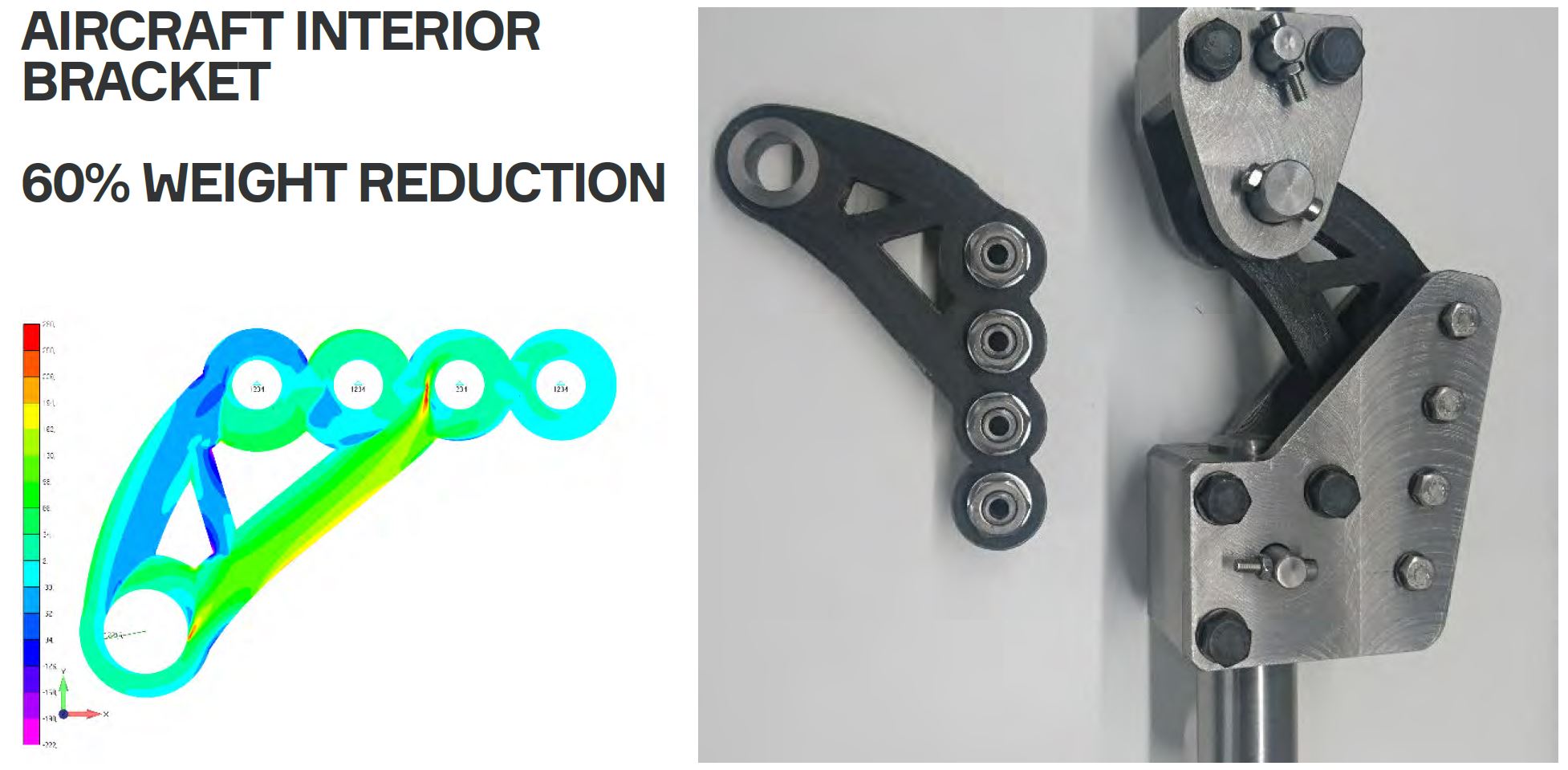
Applications d'anisoimpression
Anisoprint affirme que sa technologie peut être appliquée dans de nombreux domaines, de l'aérospatiale aux produits de consommation et aux soins de santé. Un exemple est un support de siège d'avion qui supporte 1,5 tonne de charge avec une réduction de poids de 40 % par rapport à l'aluminium. Avec 100 appareils de ce type dans un avion de ligne moyen à couloir unique, cette réduction de poids peut se traduire par d'importantes économies de carburant et de coûts d'exploitation globaux.
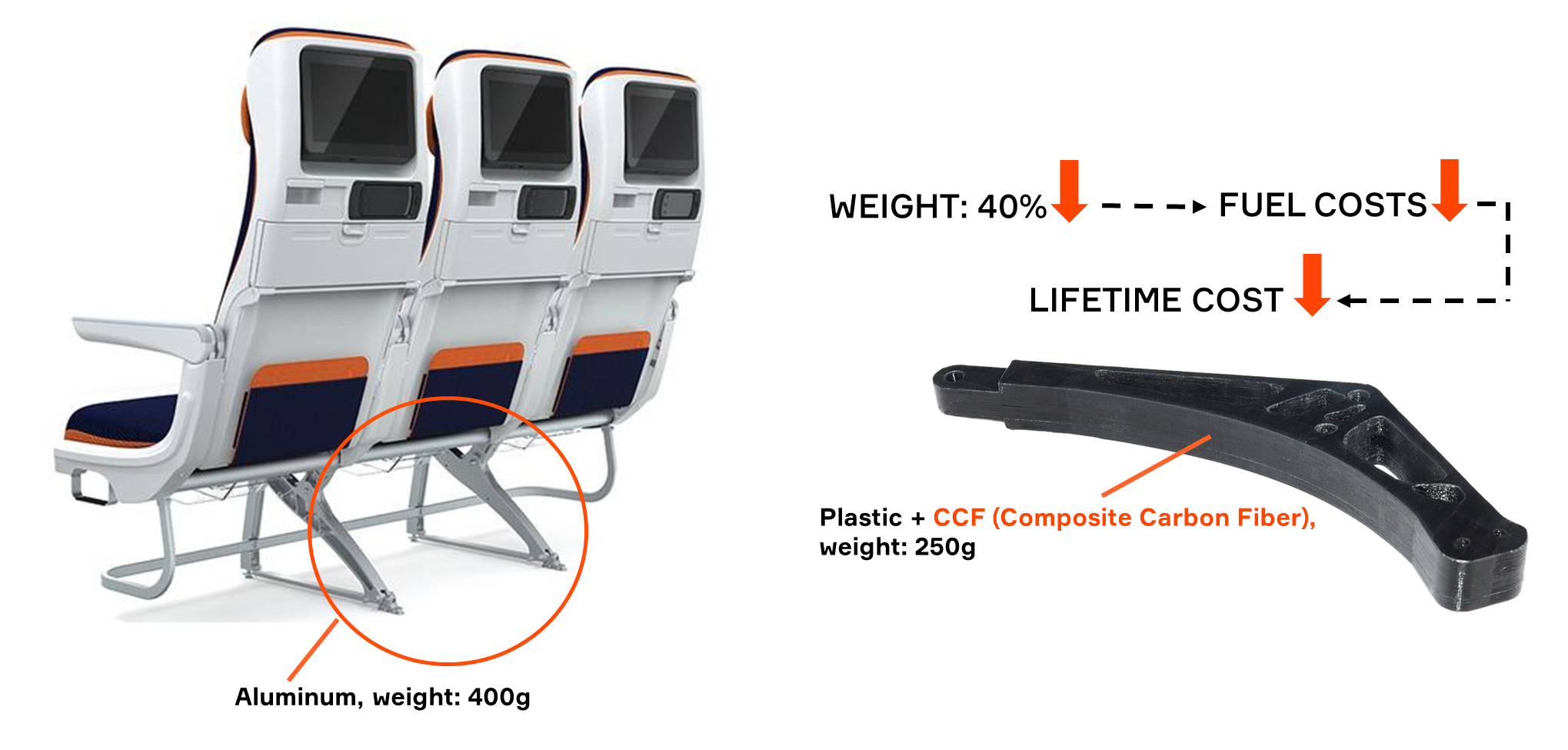
Le support de siège d'avion composite imprimé en 3D Anisoprint permet d'économiser 40 % de poids par rapport à l'aluminium.
Un autre cas est un piston pour former des pots de yaourt, utilisé dans une ligne de production laitière. De tels pistons sont généralement fabriqués à partir de polyamide broyé, mais le remplacement de ces pièces lorsqu'elles sont endommagées prend trois mois, la chaîne de production étant arrêtée pour la durée. La pièce imprimée par un compositeur Anisoprint aurait une durée de vie plus longue et réduirait les temps d'arrêt de la ligne de production de 3 mois à 24 heures.
Anisoprint a répondu aux exigences d'un composant de ligne de production laitière avec son piston composite imprimé en 3D mais avec un temps de remplacement considérablement réduit.
« L'anisoimpression permet la conception et la production de structures composites optimales grâce à la coextrusion de fibres composites », explique Antonov. « Les polymères thermoplastiques sont renforcés avec des fibres continues, consolidés et durcis au cours d'un processus entièrement automatisé en une seule étape, sans post-traitement requis. En conséquence, nous obtenons des pièces plusieurs fois plus solides, plus légères et moins chères que les métaux et plastiques traditionnels et supérieures également aux composites conventionnels. »
Résine
- 5 processus courants de fabrication additive
- Fabrication additive vs fabrication soustractive
- Avantages de la fabrication additive
- Enquête sur les workflows de fabrication additive
- Les 10 principales avancées de la technologie de fabrication des composites
- Fabrication additive avec des composites dans l'aérospatiale et la défense
- Henkel propose une plate-forme de matériaux pour la fabrication additive
- Fabrication additive en électronique
- Fabrication additive dans l'aérospatiale