L'état de la fibre de carbone recyclée
Le cas de la fibre de carbone recyclée est compliqué. L'industrie est fondée sur l'espoir de résoudre les problèmes, à savoir le désir de garder les déchets de fibre de carbone hors des décharges et de combler un écart potentiel entre l'offre et la demande de fibre de carbone. On estime généralement qu'environ 30 % de la fibre de carbone produite finit en déchets. Pendant ce temps, alors que les matériaux de valeur finissent dans les décharges, la plupart des analystes s'accordent à dire que la demande annuelle de matériaux pourrait dépasser la capacité de production annuelle actuelle au cours des prochaines années. La demande mondiale moyenne estimée de fibres de carbone est d'environ 65 000 à 85 000 tonnes métriques par an, avec une capacité nominale mondiale (qui est supérieure à la capacité réelle) d'environ 150 000 tonnes métriques, selon les estimations présentées par Brett Schneider, président, fibres mondiales, Hexcel (Stamford, Connecticut, États-Unis) et Dan Pichler, directeur général de CarbConsult GmbH (Hofheim am Taunus, Allemagne) lors de la conférence Carbon Fiber de décembre 2018. Tel que rapporté par CW contributeur Amanda Jacob en mars, certains analystes estiment que la demande de fibre de carbone pourrait dépasser l'offre d'environ 24 000 tonnes métriques d'ici 2022. (voir « Construire la confiance dans la fibre de carbone recyclée. »)
Et tandis que les fournisseurs commerciaux de fibre de carbone recyclée (rCF) désignent les matériaux récupérés et réutilisés comme une solution potentielle à cet écart entre l'offre et la demande, l'industrie du rCF a ses propres défis. Alors que la technologie de recyclage des composites en fibre de carbone existe depuis plusieurs années et est capable de produire un produit avec des propriétés mécaniques très proches de celles du matériau vierge, l'industrie du recyclage des composites est relativement jeune et n'en est encore qu'aux premiers stades de développement des marchés pour les matériaux. il produit à partir de recyclage. Au fur et à mesure que la confiance dans la qualité de la fibre produite par les recycleurs augmente, les questions de coût et de disponibilité sont venues au premier plan. Le plus grand défi pour l'industrie est peut-être la préoccupation concernant la sécurité de la chaîne d'approvisionnement.
« Les technologies sont en fait là, et elles existent depuis un certain temps, mais la chaîne d'approvisionnement n'a tout simplement pas été vérifiée », déclare Andrew Maxey, PDG de Vartega (Golden, Colorado, États-Unis). « Sans les bonnes pièces réunies, vous pouvez disposer de la meilleure technologie au monde, mais vous n'aurez pas de matériau à recycler et vous n'aurez aucun produit dans lequel le mettre. »
Les fournisseurs commerciaux considèrent souvent l'industrie aérospatiale comme une source de déchets de production et de matériaux en fin de vie à utiliser comme produits de recyclage, mais alors que la quantité de déchets créés par l'industrie aérospatiale est importante en termes de ce qui va à la décharge, de nombreux équipementiers et fabricants ont hésité à s'y fier comme source d'approvisionnement stable pour une gamme de produits à grand volume.
D'un autre côté, des progrès sont en cours. En décembre 2018, Boeing a annoncé qu'elle fournirait au spécialiste du recyclage de la fibre de carbone ELG Carbon Fiber Ltd. (Coseley, Royaume-Uni) des déchets de fibre de carbone durcis et non durcis à recycler pour être utilisés dans des produits secondaires pour d'autres applications de fabrication de composites. L'accord est la première relation formelle d'approvisionnement en matériaux entre un recycleur de fibre de carbone et un grand constructeur d'avions et semble être de bon augure pour l'industrie.
Il ne s'agit pas seulement de préoccupations environnementales
L'argument en faveur de l'utilisation du rCF va au-delà de la durabilité. La réduction des coûts est également un avantage. Par exemple, le rCF d'ELG Carbon Fibre coûte environ 40 % de moins que la fibre de carbone vierge de qualité industrielle. D'autres fournisseurs commerciaux affirment que leur matériau est de 20 à 40 % moins cher que la fibre de carbone vierge. De plus, pour de nombreuses applications, il existe un besoin pour des formats de fibres discontinus - ce qui suggère une opportunité où le rCF pourrait offrir une alternative plus durable et économique au matériau vierge.
« Partout où l'industrie utilise de la fibre de carbone discontinue ou hachée, la [fibre] recyclée devrait être la première considération », déclare Maxey. « Nous dépensons tout cet argent pour fabriquer de la fibre de carbone vierge dans un format continu… pourquoi prenons-nous cela et allons-le hacher pour le mettre en thermoplastique ? Si nous avons déjà un format discontinu dans ces chutes, c'est le meilleur matériau à utiliser, à mon avis, pour ces composés de moulage où vous allez juste le hacher de toute façon."
De plus, la qualité du rCF produit s'est avérée, dans certains cas, comparable à celle de la fibre vierge. La fibre de carbone ELG, qui récupère les fibres de carbone par pyrolyse, affirme que sa fibre conserve généralement au moins 90 % de sa résistance à la traction sans changement de module. Vartega utilise un processus de recyclage chimique et prétend que sa fibre présente les mêmes propriétés mécaniques que la fibre de carbone vierge. Shocker Composites (Wichita, Kan., États-Unis) utilise un processus de solvolyse en ligne pour récupérer la fibre et revendique une haute qualité sans aucun dommage apparent aux fibres.
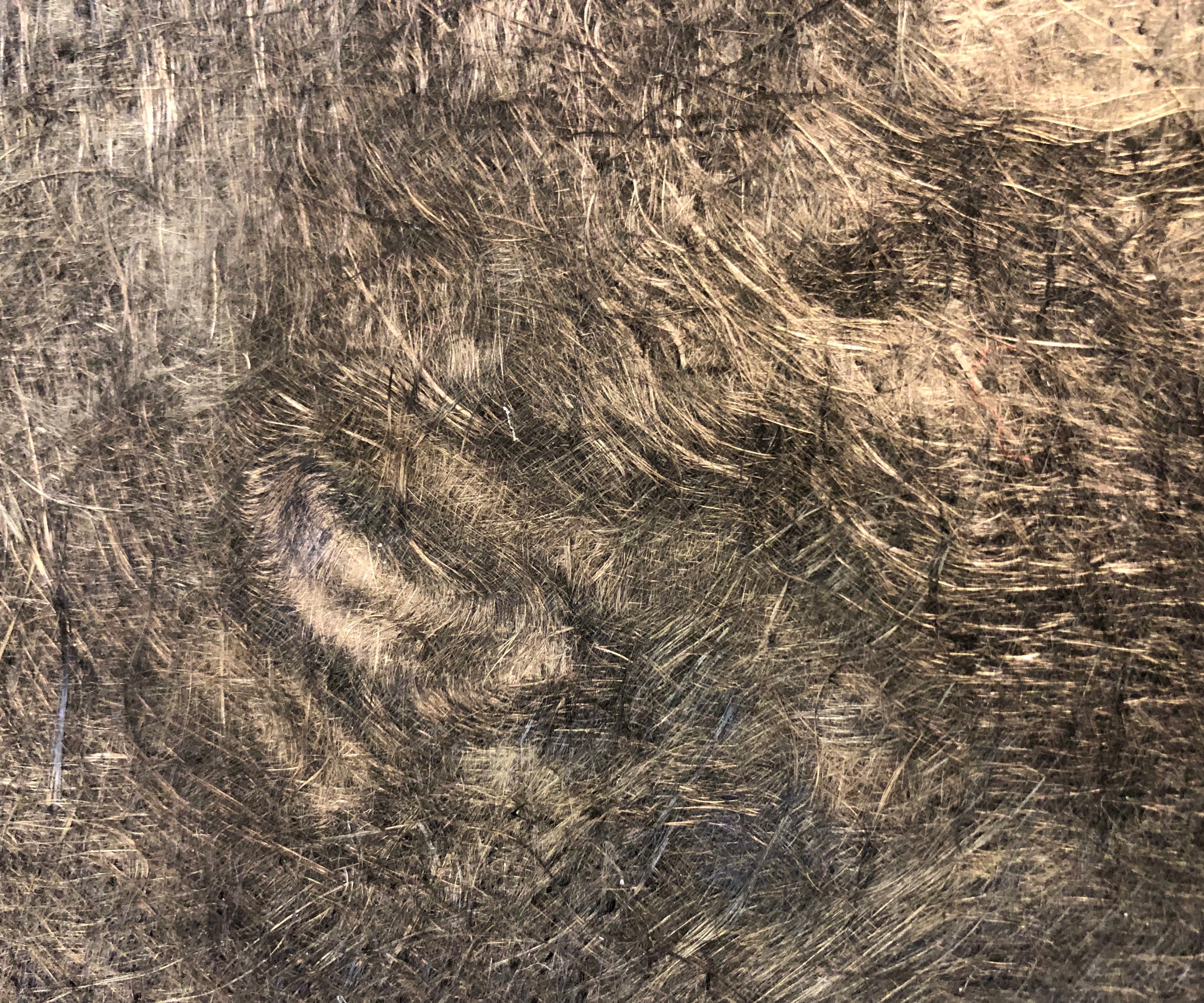
Tapis non tissé en fibre de carbone recyclée à partir de fibre de carbone ELG.
Photo CW | Scott Francis
Selon Vamsidhar Patolla, Ph.D. de l'Université d'État de Wichita. étudiant et fondateur de Shocker Composites, le défi consiste à ramener le coût à un niveau comparable à celui d'autres matériaux comme l'aluminium. « La transformabilité doit correspondre à l'échelle de production à haut volume », dit-il. Le processus de Shocker Composites offre cet avantage car il s'agit d'un processus en ligne et non d'un processus par lots. (En savoir plus dans l'article « Recyclage durable et en ligne de la fibre de carbone. »)
Compte tenu des améliorations récentes apportées au cours des dernières années au traitement du rCF et à la qualité de la fibre, les fournisseurs commerciaux ont commencé à se concentrer davantage sur le recyclage du rCF vers des produits moins performants et davantage sur la recherche d'applications appropriées qui bénéficient des propriétés du matériau.
« Nous ne remplacerons jamais complètement la fibre vierge, en particulier dans l'aérospatiale où les exigences de résistance et de rigidité sont élevées, mais les gens commencent à penser que la fibre recyclée n'est pas seulement une fibre recyclée à faible potentiel », déclare Benjamin Andrews, responsable technique sur le terrain. ingénieur de services chez ELG Carbon Fibre. « Il a ses propres avantages qui sont supérieurs aux fibres vierges dans certaines applications. La drapabilité et la finition de surface sont toutes deux meilleures que celles de la fibre vierge… ce n'est pas seulement un matériau réutilisable; c'est un matériau qui a ses propres avantages. »
Quoi de neuf avec l'automobile ?
En ce qui concerne les marchés, l'industrie automobile semble être celle qui devrait détenir le plus de potentiel pour l'utilisation du rCF. La capacité du matériau à combiner légèreté et bonne finition de surface en fait un ajustement naturel pour les panneaux de carrosserie, sans parler de divers composants intérieurs. Les fournisseurs commerciaux de rCF ont longtemps regardé l'industrie avec impatience, espérant une adoption généralisée, mais un point de basculement n'est pas encore arrivé. Le temps de traitement et le coût continuent d'être des pierres d'achoppement pour l'industrie.
Mark Mauhar, PDG de Carbon Conversions (Lake City, SC, États-Unis), soutient que ces préoccupations sont en quelque sorte une excuse compte tenu des progrès qui ont été réalisés, et il estime que le principal obstacle à l'adoption sur n'importe quel marché est en fait l'aversion au risque. .
« Personne ne veut être le premier à adopter un nouvel écosystème matériel », dit-il. Il souligne également que l'adoption à grande échelle du rCF par l'industrie automobile n'est pas nécessairement même souhaitable, soulignant que l'adoption de l'utilisation par une douzaine de grandes plates-formes automobiles pourrait rapidement consommer l'offre mondiale de rCF. Il dit que l'approche devrait être de cibler des programmes de niche, ce qui, à son tour, rendra la chaîne d'approvisionnement plus robuste d'un point de vue commercial.
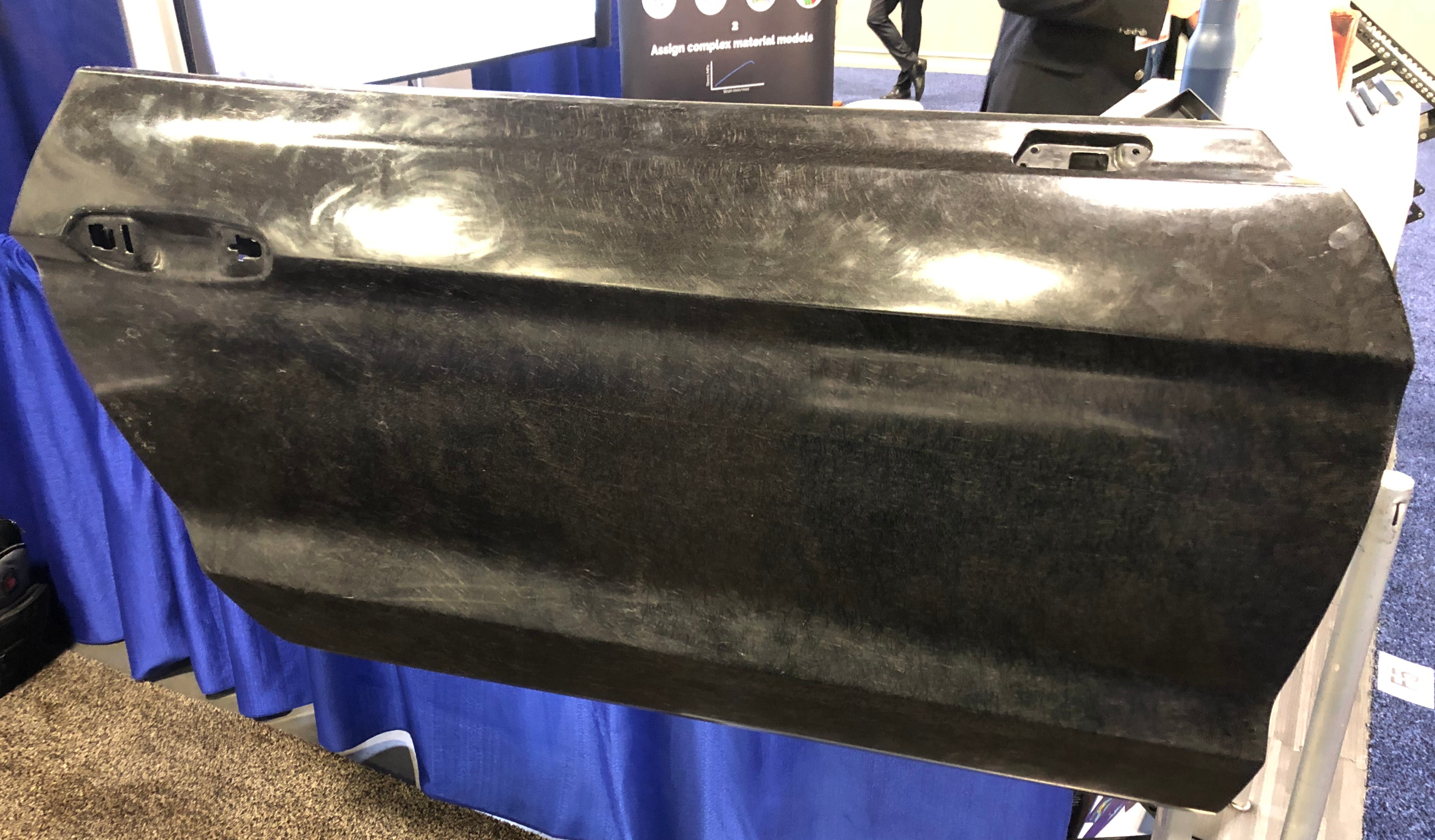
Panneau de porte automobile fabriqué à partir de préimprégné fabriqué à partir du re-Evo MCF de Carbon Conversions.
Photo CW | Scott Francis
« Cela vaut la peine d'être intelligent quant à l'endroit où vous le placez dans l'automobile », dit-il. "Choisir des pièces spécifiques sur des modèles de voitures spécifiques qui ont du sens."
Mauhar espère que l'automobile sera le premier grand marché à consommer une fraction décente de la fibre de carbone recyclée disponible. "Au cours des 24 prochains mois, nous commencerons à voir du mouvement là-bas", prédit-il.
Les composites, en général, pénètrent progressivement dans l'industrie automobile sous la forme de pièces telles que des boîtiers de batterie, des réservoirs sous pression, des ressorts à lames et même des systèmes de hayon élévateur. Il serait logique que rCF suive la même trajectoire.
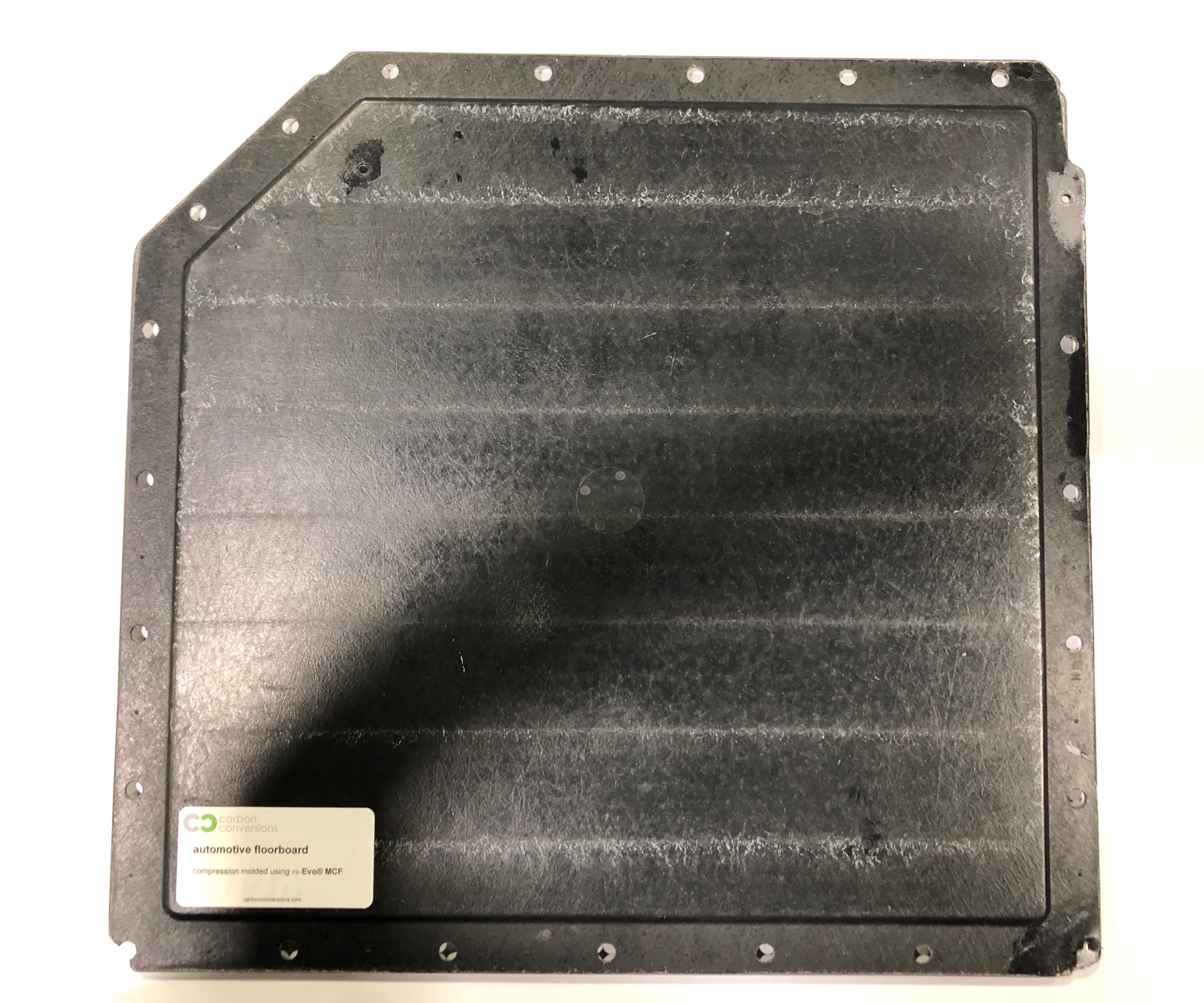
Ce plancher automobile moulé par compression utilise le tapis non tissé re-Evo MCF de Carbon Conversions.
Photo CW | Scott Francis
Un exemple intéressant d'une telle approche de niche est ProDrive Composites (Milton Keynes, Royaume-Uni), fabricant de composites légers avancés pour des applications allant de l'automobile et du sport automobile à l'aérospatiale et la défense. L'entreprise a collaboré avec le Centre de recherche de fabrication avancée de l'Université de Sheffield (AMRC, Sheffield, Royaume-Uni) et ELG Carbon Fiber sur son procédé P2T (Primaire à Tertiaire), un nouveau procédé qui utilise une résine thermoplastique réactive pour fabriquer des composants composites recyclables. Un monomère plastique est mis à réagir avec un catalyseur en présence de fibres recyclées pour produire un stratifié durci, hors de l'autoclave.
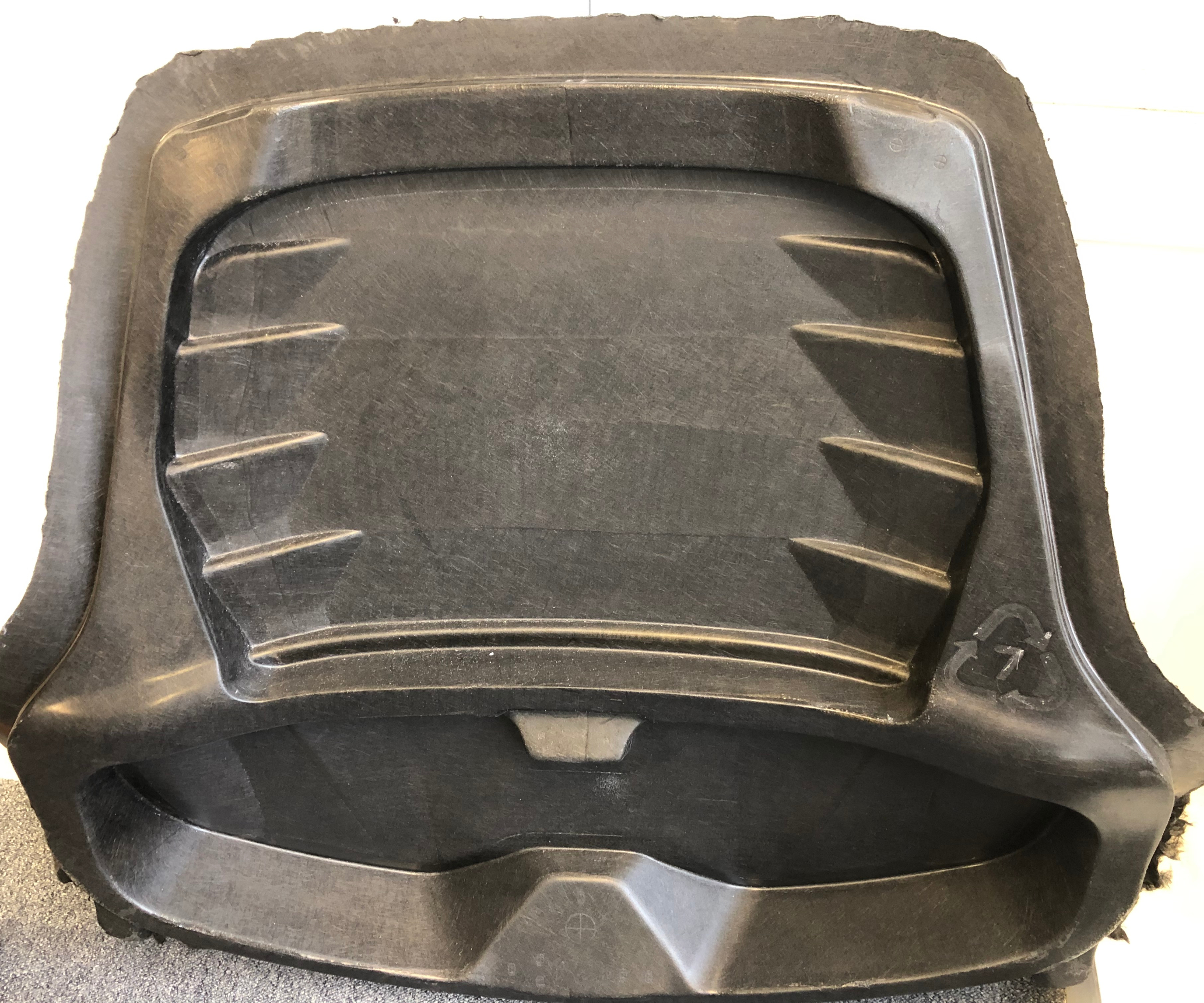
Exemple de pièce tertiaire réalisée selon le procédé P2T de ProDrive.
Photo CW | Scott Francis
« [Nous] avons démontré que les panneaux composites recyclables peuvent être produits à un rythme et à un coût adaptés à de nombreuses industries », déclare John McQuilliam, ingénieur en chef chez ProDrive Composites.
La société affirme que P2T permet à un matériau composite d'être utilisé trois fois ou plus. En fin de vie de la pièce primaire, les fibres et potentiellement la résine peuvent être recyclées, fournissant la matière première pour une pièce secondaire thermoplastique, comme un panneau de carrosserie. Lorsque cette pièce atteint sa fin de vie, elle peut être découpée et remoulée en de nouvelles pièces. (En savoir plus dans l'article « Processus P2T positionné pour le recyclage. »)
Pendant ce temps, Vartega dirige un projet de l'Institute for Advanced Composites Manufacturing Innovation (IACMI, Knoxville, Tenn., États-Unis) axé sur l'industrie automobile. La collaboration technique de deux ans est conçue pour relever les défis de la création de thermoplastiques renforcés de fibres de carbone recyclées cohérentes pour une utilisation dans des applications d'allègement des véhicules. Maxey dit que le projet progresse vers un ensemble de données robuste qui offre une caractérisation complète des matériaux, de l'interface de la fibre aux propriétés de la pièce finie.
Bien sûr, lorsque l'on considère l'industrie automobile, le meilleur pari pourrait être sur les technologies émergentes connexes. Les véhicules électriques, les véhicules autonomes et les aspects de connectivité dans les voitures offrent de nouvelles opportunités de pièces et d'applications où les composites joueront probablement un rôle important.
Maxey propose son évaluation de la direction que prend l'industrie automobile :« Il s'est passé beaucoup de choses au cours des deux dernières années dans l'industrie automobile, où l'accent passera de l'économie de carburant à d'autres priorités en fonction de la réglementation et de la l'administration [présidentielle] dit », dit-il. "[Nous] ne voyons pas de recul majeur sur l'allègement, mais peut-être que la motivation pour cela évolue. Je pense que ce que vous verrez dans l'industrie, c'est l'accent mis sur l'allègement pour les applications de mobilité.
L'aérospatiale peut-elle boucler la boucle ?
L'industrie aérospatiale génère le plus de déchets de fibres de carbone, et les fournisseurs commerciaux de rCF se tournent souvent vers l'industrie aérospatiale comme source de recyclage. Le matériau en excès, généralement un préimprégné composite thermodurcissable non durci, est collecté et la résine est éliminée par la chaleur (pyrolyse) ou un solvant chimique (solvolyse) pour produire une fibre qui est broyée, hachée ou granulée.
Alors que l'industrie s'oriente vers une utilisation accrue des composites thermoplastiques (TPC), ce matériau présente un nouvel ensemble d'opportunités de recyclage. Étant donné que les polymères thermoplastiques peuvent être refondus et remodelés, l'industrie aérospatiale a plus de possibilités de réabsorber une partie de ses propres déchets dans des applications secondaires, en réutilisant potentiellement à la fois la fibre et la matrice. Thomas de Bruijn, chercheur au Thermoplastic Composites Application Center (TPAC, Enschede, Pays-Bas) - un centre de R&D sur les composites thermoplastiques travaillant aux côtés du Thermoplastic Research Centre (TPRC, Enschede, Pays-Bas) au niveau de la recherche appliquée - souligne les efforts de l'industrie étant fait pour recycler le matériau en interne.
« Du point de vue de la faisabilité, pour les composites thermoplastiques, une approche interne est beaucoup plus logique », dit-il.
Selon de Bruijn, les équipementiers d'avions sont plus susceptibles de recycler en interne que de se tourner vers un fournisseur commercial de rCF. La principale raison en est la traçabilité. Faire correspondre les types de polymères à une application donnée devient beaucoup plus difficile lorsque l'approvisionnement est déplacé hors de la maison.
Johan Meuzelaar, spécialiste du stress technique chez GKN Fokker (Hoogeveen, Pays-Bas), pense que la réponse consiste à essayer de trouver autant d'applications que possible dans votre propre environnement de production. « Si je regarde le type de composants thermoplastiques que nous fabriquons à partir de matériaux vierges, ils contiennent de nombreuses pièces que nous pourrions recycler », dit-il. « [Nous pourrions] certainement utiliser une quantité importante de déchets que nous générons. »
« Nous avons déjà les installations, ajoute Guillaume Vincent, ingénieur composites thermoplastiques au TPRC. Il explique que le recyclage en interne s'intègre dans les chaînes de processus normales et que la majorité des équipements sont déjà en place, ce qui en fait l'avenue la plus abordable. "[Il] s'intègre dans les activités que nous avons dans un environnement de production normal."
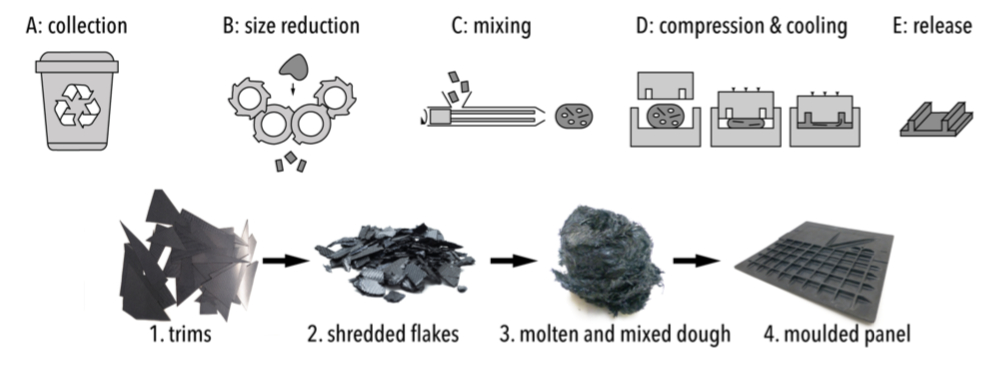
Source | TPRC, TPAC
De Bruijn, Vincent et Meuzelaar sont impliqués dans le projet TPC-Cycle, opéré par TPAC et le TPRC. Le projet vise la réutilisation des déchets de production issus du traitement des composites thermoplastiques pour des applications aérospatiales et à haut volume. L'objectif est de conserver les propriétés mécaniques élevées des composites thermoplastiques et de réduire l'impact environnemental global à un coût abordable. Le TPC-Cycle offre des temps de cycle courts et est censé permettre la production de formes complexes.
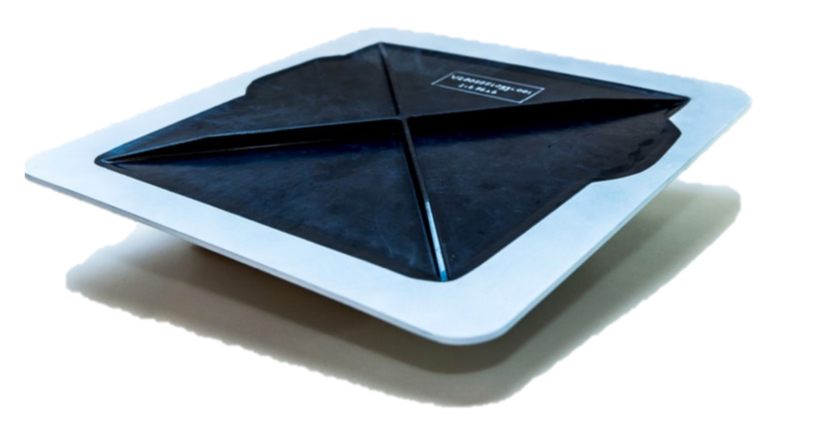
Panneau d'accès au démonstrateur pour giravion développé à l'aide du procédé TPC-Cycle.
Source | TPRC, TPAC, GKN Fokker
Plusieurs partenaires industriels, dont GKN Fokker, Toray Advanced Composites (Morgan Hill, Californie, États-Unis ; Nijverdal, Pays-Bas), Cato Composite Innovations (Rheden, Pays-Bas), Dutch Thermoplastic Components (Almere, Pays-Bas) et Nido RecyclingTechniek (Nijverdal, Pays-Bas) , sont impliqués dans le projet TPC-Cycle, représentant différents segments de la chaîne de valeur depuis les matériaux, la fabrication, la conception et l'application.
Selon de Bruijn, le projet TPC-Cycle cherche maintenant à effectuer des analyses de coûts et des analyses de cycle de vie pour prouver que le processus est économiquement avantageux.
En outre, des programmes tels que l'entreprise commune Clean Sky 2 (qui est financée par le programme Horizon 2020 de l'UE) encouragent la R&D qui vise à boucler la boucle de la ferraille aérospatiale. Les équipementiers envisagent la possibilité d'utiliser des déchets d'usine recyclés pour les pièces intérieures, les panneaux d'accès, les petits composants et même les clips de cellule et les supports de système.
Le Dr Bas Veldman, responsable du programme GKN Fokker pour la moitié inférieure d'un démonstrateur de fuselage multifonctionnel thermoplastique, encourage ce concept en lançant un appel à propositions dans le cadre du programme Clean Sky 2 sur les clips et les supports. Un élément important dans le développement du démonstrateur est de réduire l'impact environnemental grâce à l'utilisation de déchets d'usine pour des produits tels que des clips de cadre et des supports. Le démonstrateur vise également à remplacer les fixations par des soudures, permettant ainsi d'économiser des matériaux, de l'énergie et des coûts tout en contribuant à l'allègement.
Selon Meuzelaar, GKN Fokker étudie comment la technologie de recyclage pourrait faire partie du concept de fuselage de demain de l'entreprise. Il dit que le concept utilisera potentiellement beaucoup de composites thermoplastiques, qui à leur tour pourraient générer beaucoup de déchets qui pourraient être utilisés pour les supports, les raccords et les pièces non structurelles recyclés.
« La raison pour laquelle nous nous penchons sur un fuselage thermoplastique est le coût, et nous pensons qu'il s'agit d'une méthode de production économique, qui intègre également le recyclage », dit-il.
Meuzelaar dit que l'objectif à un niveau élevé est de fabriquer des produits plus abordables et plus durables dans l'aérospatiale. Si des progrès sont faits vers la production en série de thermoplastiques, cela générera également des déchets (comme c'est malheureusement le cas pour les composites en général). Mais il pense que les déchets peuvent être commercialement viables et affirme que le moulage par mélange/compression à faible cisaillement des TPC en fibre de carbone recyclée offre une liberté de conception que ne permet pas le laminage traditionnel avec des fibres continues. « Vous disposez de nombreuses options supplémentaires pour fabriquer des pièces non structurelles très intéressantes telles que des panneaux, de petits carénages ou des supports de système qui, généralement dans l'aérospatiale, ont tendance à être surconçus en termes de matériaux utilisés, d'alliages utilisés et de systèmes de production utilisés » il explique.
Il pense que l'opportunité réside principalement dans les pièces non structurelles de taille moyenne et de complexité moyenne, qui représentent toujours une part importante du coût total des composants plus grands.
« Nous ne fabriquerons pas d'ailes en thermoplastique recyclé dans un avenir proche », déclare Meuzelaar. "Mais à l'intérieur de l'aile, il y a des parties que nous pouvons faire qui ont un sens économique."
Cela dit, il est un peu éloigné de prédire l'impact que les composites thermoplastiques auront sur l'industrie du recyclage.
« Le pourcentage de déchets diminuera probablement en raison de nouvelles méthodes de production telles que le placement de bandes ou de découpes sur mesure, qui produisent probablement moins de déchets que les processus typiques actuels d'imbrication et de formation de tampons que nous voyons », déclare de Bruijn. « Mais en général, je pense qu'il y aura plus de déchets thermoplastiques dans les années et décennies à venir.
Et tandis que cet intérêt pour le recyclage en interne est à la hausse, il y aura toujours des déchets qui ne seront pas utilisables et que les fabricants ne voudront pas ou ne pourront pas recycler en interne. Dans de tels cas, ces matériaux peuvent être récupérés par un fournisseur de matériaux. Le temps nous dira ce que l'utilisation accrue de composites thermoplastiques pourrait signifier pour la chaîne d'approvisionnement. (En savoir plus sur le projet TPC-Cycle et l'initiative Clean Sky 2 dans « Composites thermoplastiques recyclés pour la production. »)
Fabrication additive
La fabrication additive est un autre domaine qui recèle un potentiel pour le rCF. Par exemple, Shocker Composites a transformé sa fibre de carbone recyclée en filament ABS renforcé de 20 à 40 % et a démontré son utilisation réussie avec le processus d'impression 3D de fabrication additive Big Area (BAAM) de Cincinnati Inc. (Harrison, Ohio, États-Unis).
En outre, Vartega affirme tirer parti de sa technologie de recyclage de la fibre de carbone et de son expertise en matière de développement de matériaux pour faire progresser les matières premières polymères pour la fabrication additive par fusion sur lit de poudre. La société a récemment reçu une subvention de la National Science Foundation (NSF, Alexandria, Virginie, États-Unis) Small Business Innovation Research (SBIR) pour mener des activités de recherche et développement (R&D) dans la région.
Vartega prétend également développer un procédé qui permettra de renforcer les poudres thermoplastiques avec de la fibre de carbone tout en garantissant que les matériaux produisent des pièces fonctionnelles dans des systèmes d'additifs infrarouges. Cette avancée permettrait aux fabricants numériques de réaliser tout le potentiel des nouvelles plates-formes matérielles à base de poudre pour produire des pièces qui fonctionnent de manière similaire aux matériaux moulés par injection à des taux de production de volume moyen.
« En proposant des poudres polymères renforcées de fibres de carbone, les fabricants de secteurs tels que les drones [véhicules aériens sans pilote] et les prothèses médicales bénéficieront des avantages d'une impression 3D rapide, complexe et personnalisée, tout en garantissant que leur sélection de matériaux présentera l'intégrité structurelle requise pour leur produit », déclare Alice Havill, directrice de l'exploitation chez Vartega.
Autres applications
Pendant ce temps, d'autres marchés et applications dans lesquels la fibre de carbone recyclée peut jouer un rôle continuent d'émerger.
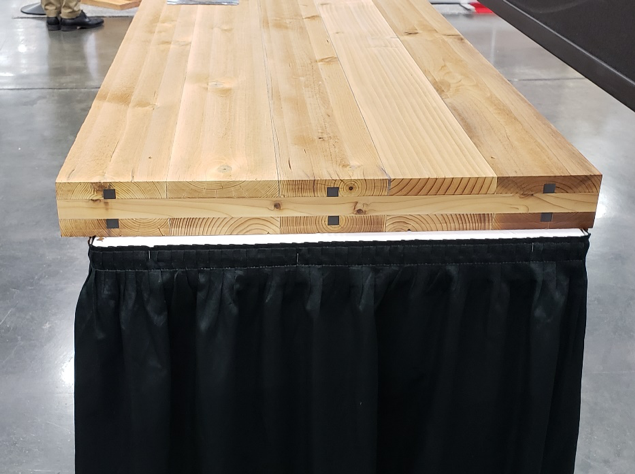
Ce bois lamellé-croisé (CLT) de qualité construction combine du bois modifié thermiquement avec de la fibre de carbone recyclée du Composite Recycling Technology Center.
Source | Le Centre Technologique de Recyclage des Composites
The Composite Recycling Technology Center (CRTC, Port Angels, Wash., U.S.) has been exploring use of recycled carbon fiber in a variety of products, from park benches to high-performance sporting goods to composite tubing. The company works with reclaimed uncured prepreg material from Toray Composite Materials America (Tacoma, Wash., U.S.) as well as rCF from ELG Carbon Fibre.
Dave Walter, CEO of the CRTC, points to the construction industry as an area of potential growth. The company recently developed a construction grade cross-laminated timber (CLT) under a patent-pending process that combines thermally modified lumber with recycled carbon fiber. The thermal modification process cooks off the sugars and lignin, providing rot and termite resistance, and then carbon fiber strips are integrated for strength.
The CRTC also uses recycled carbon fiber to create panels bonded with wood veneer. These panels showcase the beauty of wood with a strong, light and flexible substrate for various interior and exterior applications, as shown in the picture below from a 2019 installation at the Benaroya Hall in Seattle.
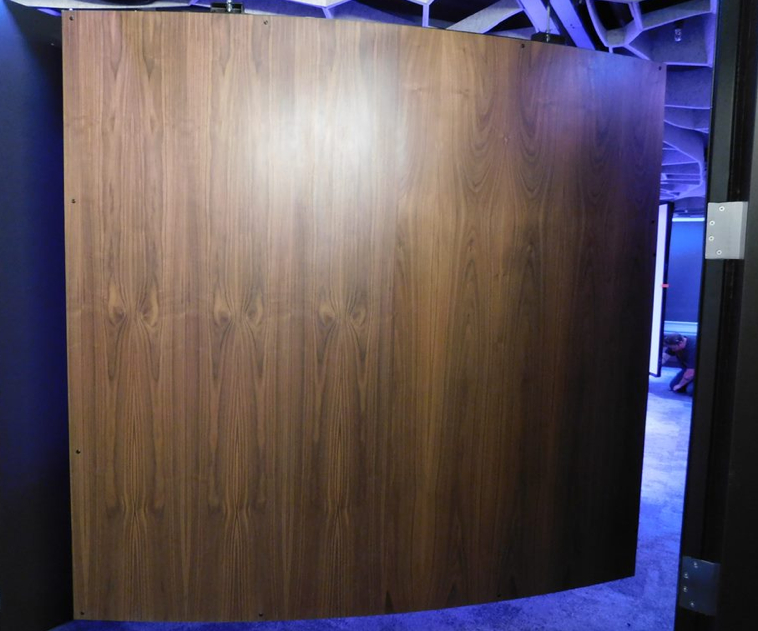
Octave 9 Raisbeck Music Center – Benaroya Hall (Seattle, Wash., U.S.)
Photo | The Composite Recycling Technology Center
A mind change for the industry?
Big changes often happen incrementally, and the relatively young recycled carbon fiber industry continues to slowly push forward. While downcycling of rCF continues, perceptions about the material are beginning to change. Quality of fiber has been proven and processes continue to evolve. Awareness of the necessity to recycle carbon fiber is high and more players are getting involved.
“The ELG and Boeing announcement was a really big deal; it helps everyone move the ball forward [and] to accelerate the supply chain connections,” says Maxey.
“We’re here to enable and connect the dots,” he adds, summing up the industry. “We have this enabling technology that sits in the middle of the supply chain, but its really about connecting that stranded asset in the waste stream to an unmet demand downstream.”
The biggest change, according to Mark Mauhar of Carbon Conversions, is that suppliers now want to be part of the solution. “Prior to two years ago we’d get multiple calls a week from suppliers about getting rid of scrap, but no interest in using the material,” he says. “Now, people are starting to walk the walk. Only recently, we are finally starting to see potential customers of reclaimed carbon fiber spend significant resources in cutting molding tools, building prototypes and mock-ups, solving process issues — all activities that are well down the line in terms of commercial adoption.”
Perhaps what it really boils down to is patience. Detlef Drafz, CEO at ELG Carbon Fibre, points out that it’s helpful to examine the recycling history for other legacy materials.
“For over 50 years, ELG has recycled raw materials for the stainless steel industry. With metal, it’s accepted that you use the scrap even in vacuum furnaces for turbine blades … it’s accepted that recycled metal is a raw material, which properly processed can just be used. That wasn’t common in the aerospace application 25 years ago; however, we established a supply chain in order to give the guarantees that the material performs. We do the same here,” he says.
Résine
- Fibre de carbone
- Comment l'industrie médicale utilise la fibre de carbone
- Les avantages de la fibre de carbone dans l'industrie aérospatiale
- Fibre de verre vs fibre de carbone :quelles sont les différences ?
- Les 5 principales utilisations de la fibre de carbone dans le sport
- Le coût de la fibre de carbone :pourquoi la qualité en vaut la peine
- Innovations en matière de fibre de carbone dans l'industrie médicale
- La fibre de carbone peut-elle être recyclée ?
- Présentation du premier smartphone en fibre de carbone au monde