Accélérer les composites thermoplastiques dans l'aérospatiale
Les composites thermoplastiques renforcés de fibres (TPC) continus ont été cités comme une technologie habilitante pour l'avenir des avions durables, offrant des taux de production accrus de pièces légères et très résistantes qui peuvent être assemblées sans trous ni attaches dans des assemblages soudés économiques.
CW a publié une série d'articles en 2018 sur les rubans TPC, la consolidation in-situ et le soudage et a présenté deux webinaires en 2019 sur les TPC dans les applications automobiles et les développements de TPC pour l'aérospatiale. La plupart de mes les articles et les présentations à ce jour font référence aux fabricants de pièces détachées et aux fournisseurs d'équipements TPC en Europe, ainsi qu'à la division Automated Dynamics de Trelleborg aux États-Unis. Mais j'ai malheureusement oublié un autre fabricant de pièces TPC ici aux États-Unis qui fait discrètement avancer l'enveloppe de la technologie et de la production depuis 15 ans. ATC Manufacturing, situé à Post Falls, dans l'Idaho, juste à l'extérieur de Spokane, dans l'État de Washington, produit un million de pièces par an, toutes des thermoplastiques renforcés de fibres continues et toutes destinées à l'industrie aérospatiale. Ayant développé une expertise unique dans le formage rapide de pièces 3D, ATC est également un partenaire clé du programme de recherche RAPid high-Performance Molding (RAPM) avec Boeing Co. (Chicago, Ill., US) et la Defense Advanced Research Projects Agency (DARPA, Arlington, Virginie, États-Unis) pour le département américain de la Défense (DoD).
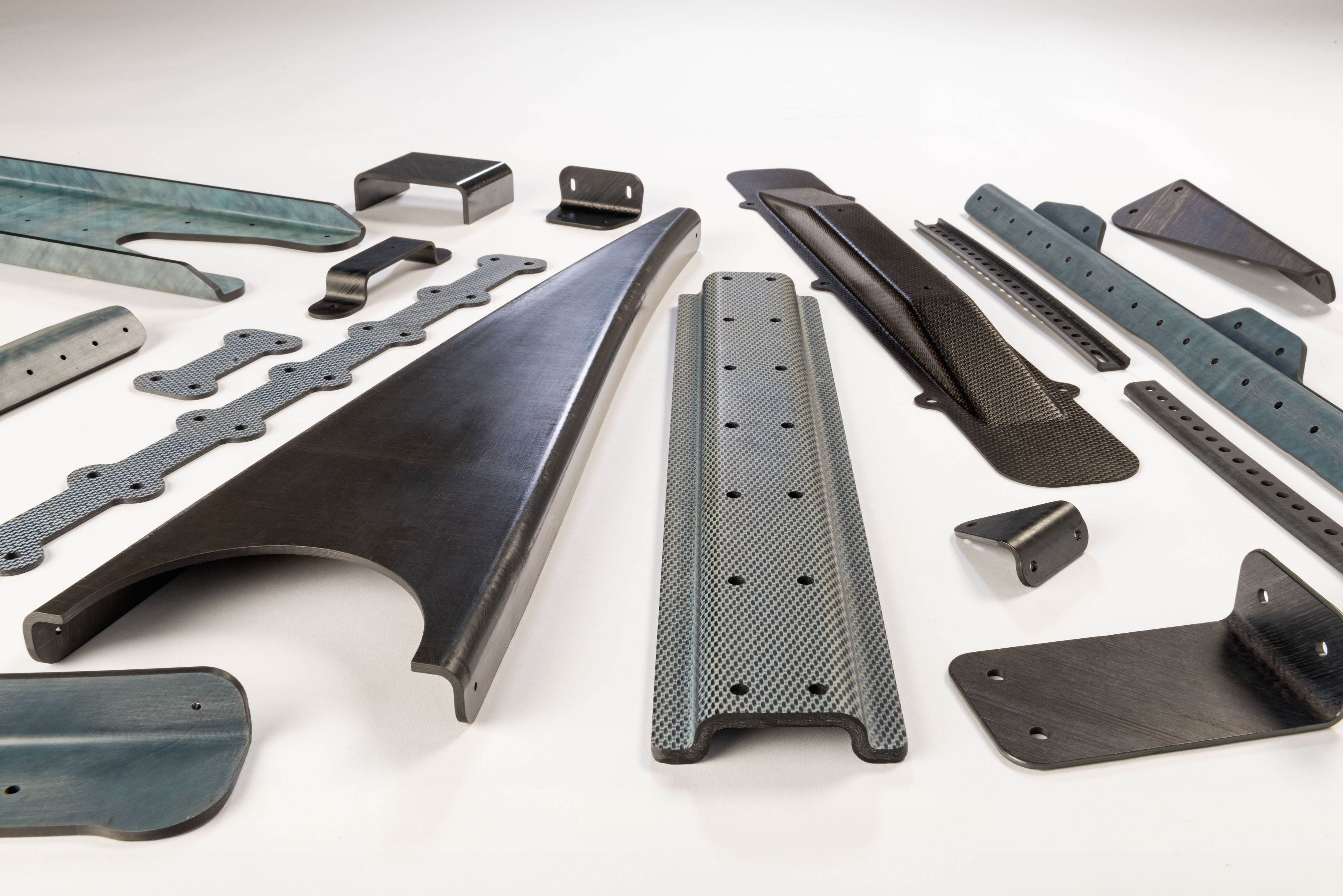
ATC Manufacturing produit un million de pièces composites thermoplastiques par an pour les applications aérospatiales, notamment des nervures, des clips, des supports et des raidisseurs. SOURCE | Fabrication ATC
Qui est l'ATC ?
ATC Manufacturing a été fondée en 2004 par l'ancien ingénieur de Boeing Dan Jorgenson, qui reste le coprésident de la société. « Nous avons toujours eu une forte concentration technique et d'ingénierie », déclare David Leach, directeur du développement commercial pour ATC Manufacturing. La société a également une longue histoire avec Boeing, reconnu comme fournisseur de niveau Argent au cours des cinq dernières années consécutives et nommé fournisseur Boeing de l'année en 2016 et 2017. supports et pièces estampées plus petites », explique Leach. "Mais ces dernières années, nous avons progressé vers des assemblages plus complexes, ainsi que des pièces beaucoup plus épaisses et plus grandes - jusqu'à 60 pouces de longueur - et des pièces destinées aux structures primaires." Ces derniers comprennent des composants structurels d'extrémité d'aile, de longues poutres avec des couches sur mesure dans une variété de sections transversales ainsi que des structures de fuselage et d'empennage.
L'entreprise compte 150 employés avec plus de 20 ingénieurs. Sa fabrication est concentrée dans une seule installation de 67 000 pieds carrés, construite à cet effet en 2015 et conçue pour un flux de travail optimisé avec de la place pour s'étendre. (Remarque, 52 500 pieds carrés d'espace sont déjà pré-planifiés pour une croissance future.) « Tout est sous un même toit », note Leach, « ce qui simplifie les opérations. » Cela comprend neuf presses de formage de tampons avec des capacités allant de 30 à 150 tonnes et des surfaces de platine jusqu'à 60 pouces sur 30 pouces. « Nous installons une presse supplémentaire de 200 tonnes qui sera pleinement opérationnelle d'ici fin 2019 », ajoute-t-il. ATC dispose de 10 stations d'usinage CNC capables de traiter des pièces jusqu'à 12 pieds de longueur et de découpe au jet d'eau pour des pièces jusqu'à 30 pieds de longueur.
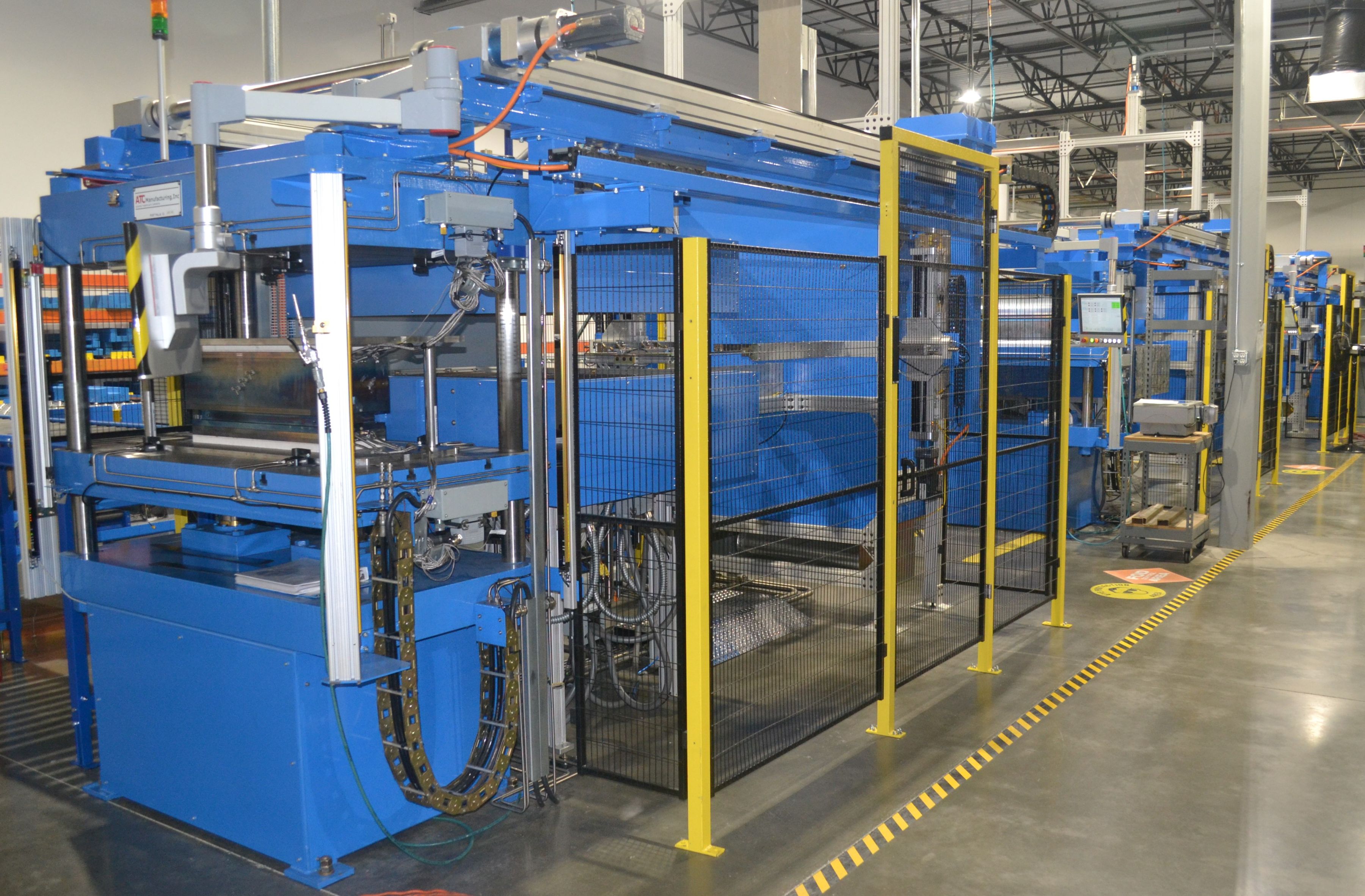
ATC Manufacturing exploite 9 presses de formage de tampons, y compris la presse de 80 tonnes illustrée ici, avec des capacités allant jusqu'à 150 tonnes et des surfaces de platine jusqu'à 60 x 30 pouces.
SOURCE | Fabrication ATC
L'inspection non destructive (NDI) est également intégrée dans la conception des opérations et du flux de travail de l'installation, y compris cinq systèmes de réservoirs C-scan fournissant un écho d'impulsion et des tests de transmission pour des pièces jusqu'à 9 mètres de long. L'autre expertise interne comprend toute la préparation de surface et la peinture. « Nous avons développé une préparation de surface très efficace pour les composites thermoplastiques, qui peuvent être difficiles à peindre et à coller », explique Leach, notant qu'ATC a également travaillé sur le traitement plasma des pièces en TPC. L'entreprise peint 200 000 pièces/an et scelle les bords 70 000 pièces par an.
« Nous avons également beaucoup investi dans la recherche, comme le programme RAPM pour la DARPA, et nous sommes membres du Centre de recherche sur les composites thermoplastiques (TPRC, Enschede, Pays-Bas) », poursuit-il. ATC participe à la conférence du 10e anniversaire du TPRC intitulée « L'avenir des composites thermoplastiques » qui se tiendra le 8 octobre à l'Université de Twente aux Pays-Bas. « Corbin Chamberlain, vice-président de l'ATC, participera à une session de groupe et nous présenterons également des pièces structurelles aérospatiales que nous avons fabriquées lors d'une exposition organisée conjointement avec la conférence », a déclaré Leach.
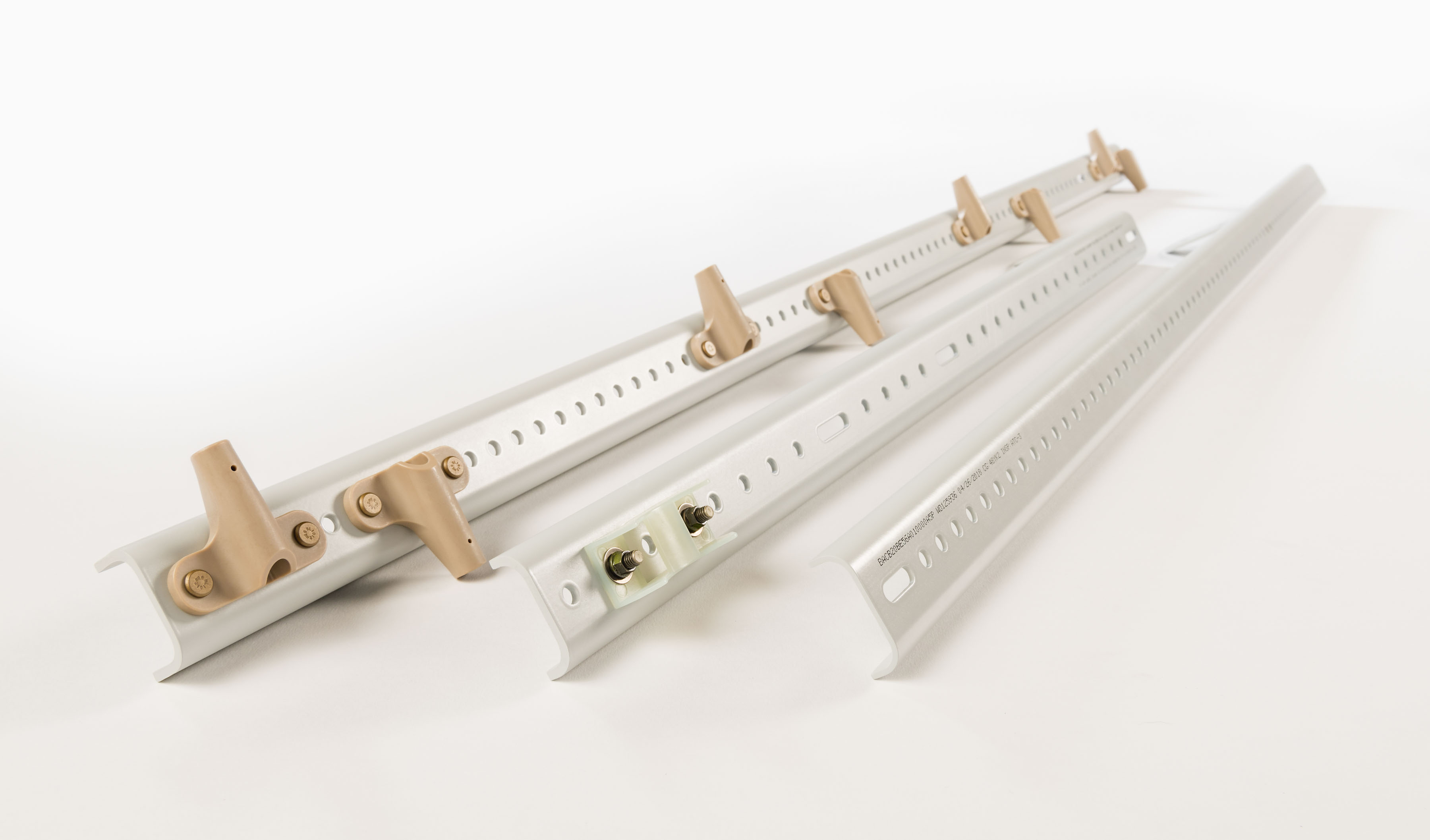
Canaux composites thermoplastiques peints avec raccords installés. SOURCE | Fabrication ATC
Tissus sur ruban UD, formage et temps de cycle rapides
Bien que la fabrication par ATC de supports et de clips TPC ait commencé avec des renforts en tissu, ils ont maintenant migré vers l'utilisation de ruban unidirectionnel (UD). « Nous avons ensuite évolué vers des pièces structurelles plus grandes car nous avions déjà acquis une bonne expérience de la formation de pièces 3D avec du ruban UD », explique Leach. « Ces pièces, dont l'épaisseur varie de 1 à 2 millimètres à 6,5 millimètres, doivent s'adapter à d'autres structures. Nous devons respecter des tolérances dimensionnelles strictes pour les surfaces en contact, par exemple une tolérance de profil de ± 0,010 pouce (0,25 millimètre) et une tolérance angulaire de ± 0,5 degré. »
L'entreprise a alors commencé à développer des profils TPC longs. « Nous fabriquons notre propre stock de stratifié plat en utilisant le moulage par compression continue (CCM) », explique Leach. "Nous avons deux machines CCM pour les stratifiés plats et une qui forme des préimprégnés TPC en un profil 3D continu, produisant des canaux jusqu'à 75 pieds de longueur."
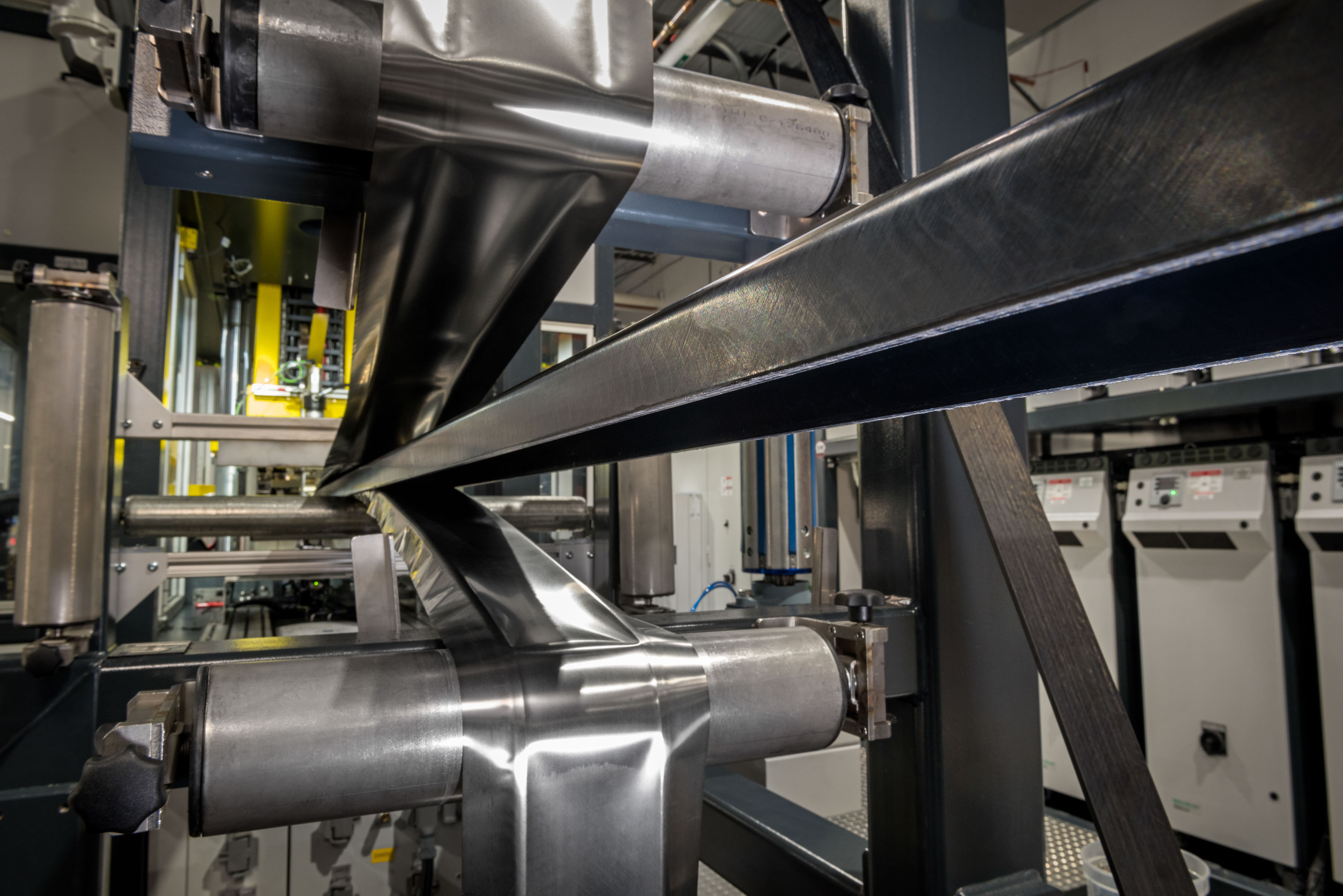
Profil composite thermoplastique formé par moulage par compression continue (CCM). SOURCE | Fabrication ATC
Interrogé sur les défis liés à la formation de profils et de formes 3D, le directeur de l'ingénierie R&D d'ATC Manufacturing, Trevor McCrea, explique qu'avec les tissus, « le tissage lui-même contrôle une grande partie de la déformation qui se produit. Avec UD, il existe différentes dynamiques. Par exemple, 90° par rapport au rayon veut s'éclaircir ou s'épaissir, mais vous ne pouvez pas l'avoir dans une pièce structurelle. Ces problèmes s'aggravent avec des formes plus complexes. Vous avez également plus de difficultés à gérer le processus de formation. »
Gérer le processus ? "Pour nous, c'est très différent du formage dans des thermodurcissables car nous n'avons que 2 secondes pour former", explique McCrea. "Vous pouvez couvrir beaucoup de péchés dans un cycle d'autoclave", ajoute-t-il. « Mais nous utilisons des processus de formage et d'emboutissage très rapides sans cette marge de manœuvre. Il faut aussi gérer la cristallinité. En effet, les structures d'avions fortement chargées utilisent des polymères à matrice thermoplastique semi-cristallins - tels que le polyétheréthercétone (PEEK), le polyéthercétonecétone (PEKK) et le polyaryléthercétone à bas point de fusion (LM PAEK) - qui tirent leurs propriétés mécaniques notables et leur résistance chimique de la structure cristalline qui se développe. comme ils refroidissent. « Vous pouvez cristalliser de manière isotherme, ce qui n'est pas trop difficile pour les plaques plates, mais devient beaucoup plus difficile avec les formes 3D », explique McCrea. « Les matériaux doivent être suffisamment chauffés pour former [notez que les températures de fusion de ces matériaux sont comprises entre 300 et 400 °C], mais ensuite suffisamment refroidis pour être démoulés à chaud afin d'éviter le cyclage thermique des outils tout en gérant la forme, la tolérance, la cristallinité et la finition de surface. ."
L'une des raisons pour lesquelles les pièces TPC se sont développées ces dernières années est leur capacité à offrir des temps de cycle très rapides. "Nous avons fabriqué des nervures pour des démonstrateurs d'avions militaires avec un temps de cycle de 5 minutes, et notre temps de cycle moyen est d'environ 10 minutes", note Leach. « Nous pouvons permettre les taux de production élevés actuellement recherchés par les équipementiers d'avions. » Ce temps de cycle moyen très rapide entraîne en fait un mélange de pièces en constante évolution. « Nous adorerions ne produire qu'une seule pièce pendant des mois, mais notre capacité de cadence dépasse celle de la fabrication d'avions », déclare McCrea. « Donc, nous parcourons toujours différentes parties. » La plupart des activités de fabrication d'ATC se font sur une équipe par jour, 5 jours par semaine. « Nous avons suffisamment de capacité pour répondre à une production accrue », note Leach.
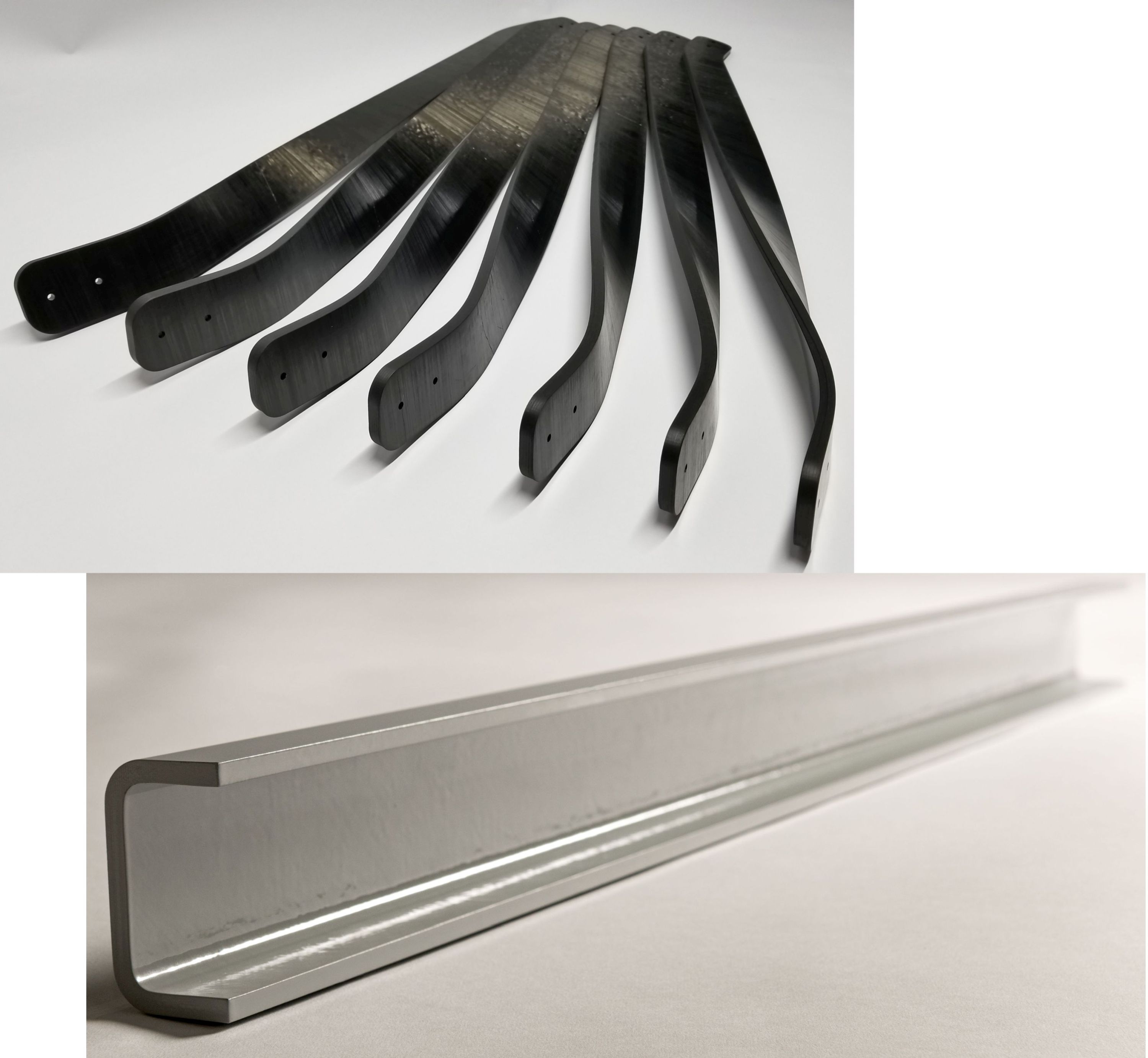
Sangles structurelles en composites thermoplastiques et profil peint. SOURCE | Fabrication ATC
Vision pour l'avenir
ATC offre une valeur significative via sa décennie et plus d'expérience dans la production de TPC. « Nous aidons fréquemment nos clients à concevoir des pièces pour la fabrication », explique Leach. « Nous convertissons souvent des pièces en composite thermodurcissable, par exemple, un raccord de structure primaire de fuselage qui est produit pour conserver l'épaisseur d'origine. Mais il pourrait s'agir d'une pièce beaucoup plus légère si elle était conçue à l'origine pour TPC. Pourquoi? « Parce que ces matériaux de matrice TP semi-cristallins sont plus performants », explique-t-il. « Vous n'avez pas à concevoir pour la microfissuration et la tolérance aux dommages comme vous le feriez avec une matrice thermodurcissable, et il y a également beaucoup moins de précipitations chaudes/humides. En fait, il n'y a pas du tout de précipitation humide en PEEK, PEEK ou PAEK. Il n'y a pas non plus de choc à chaud à moins que vous ne soyez proche de la Tg, qui est généralement ≈150 °C. Pour le test standard de compression à trou ouvert (OHC) pour la tolérance aux dommages, par exemple, où vous évaluez la résistance lorsque vous faites passer l'échantillon de la température ambiante à 120 °C, il n'y a pratiquement pas de renversement du tout. »
« Nous pourrons concevoir des pièces plus minces et également éliminer une grande partie de l'aluminium et du titane qui se trouvent dans les conceptions actuelles de première génération pour les composites [tels que les avions à fuselage large Boeing 787 et Airbus A350] », ajoute McCrea. « Nous continuons à faire progresser la mise en forme de ces matériaux et cela continuera à ouvrir de nouvelles applications. »
Leach pense que cela aura un impact significatif sur les futures applications aéronautiques. « Nous examinons actuellement des pièces que vous ne pouvez tout simplement pas produire à l'aide de thermodurcissables en raison des propriétés et du taux de production exigés. »
Pour plus d'informations, ATC Manufacturing présentera le document technique "Cost Effective Thermoplastic Composites in Aerostructures" des auteurs Corbin Chamberlain, David Leach et Trevor McCrea au CAMX 2019 dans le cadre de la session Thermoplastic Materials and Applications, le mercredi 25 septembre à 16h00. dans la salle 210C.
Il a également présenté un document conjoint avec Boeing lors d'une session à huis clos au SAMPE 2019 (4-7 mai, Charlotte, Caroline du Nord, États-Unis) intitulé :« Rapid High Performance Molding of Structural Thermoplastic Composite Parts ». Voir mon blog :https://www.compositesworld.com/news/darpa-presents-tff-program-for-rapid-low-cost-composites-to-replace-metals-in-small-parts-for-defense- candidatures
Résine
- Comment l'impression 3D a changé l'aérospatiale
- Covestro intensifie ses investissements dans les composites thermoplastiques
- Collins Aerospace acquiert le fabricant de pièces thermoplastiques Dutch Thermoplastic Components
- Composites thermoplastiques chez Oribi Composites :CW Trending, épisode 4
- Dépannage du thermoformage des composites thermoplastiques
- L'ACMA publie le programme 2020 de la Conférence sur les composites thermoplastiques
- Composites thermoplastiques :vue panoramique
- Soudage de composites thermoplastiques
- Le consortium des composites thermoplastiques vise une production à haut volume pour l'automobile et l'aérospatiale