Assemblage automatisé de structures composites hybrides métal-thermoplastique
Permettre l'assemblage hybride à l'échelle industrielle
FlexHyJoin démontre un processus de production de masse pour produire un raidisseur de toit composite thermoplastique avec des supports métalliques soudés pour l'assemblage dans une carrosserie métallique en blanc, comme celui du cas d'utilisation du projet, la Fiat Panda voiture de ville. Origine | IVW
Les structures hybrides métal-composite continuent d'être intéressantes pour les applications automobiles et aérospatiales, offrant un poids réduit et des performances améliorées en plaçant « le bon matériau au bon endroit ». Les composites thermoplastiques (TPC) sont intéressants pour de telles structures multi-matériaux en raison de leur traitement rapide, y compris leur capacité à être soudés et thermoformés. Cependant, jusqu'à présent, l'assemblage de composites à des métaux reposait principalement sur des fixations mécaniques, qui nécessitent de percer des trous qui endommagent les fibres porteuses. Le collage a également été utilisé, mais un certain nombre de thermoplastiques sont difficiles à coller de cette manière; De plus, les adhésifs ajoutent de la matière et du poids. Par exemple, la BMW i3 , qui utilise un châssis en plastique renforcé de fibres de carbone (PRFC) et des panneaux de carrosserie en plastique, utilise 16 kg d'adhésif, ce qui neutralise en partie le potentiel d'économie de poids des composites.
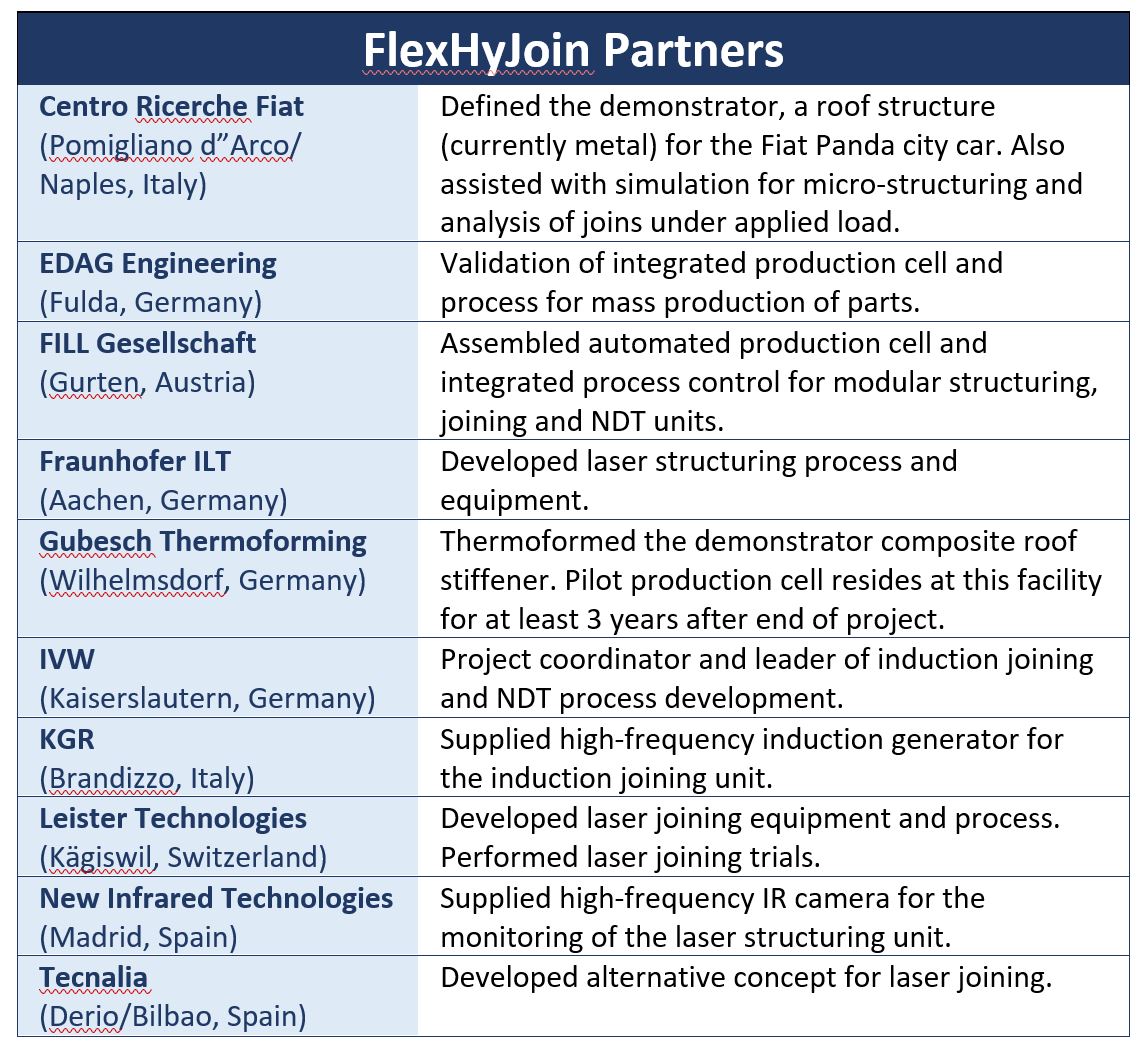
FlexHyJoin est un projet financé par le programme de recherche et d'innovation Horizon 2020 de l'Union européenne, mené d'octobre 2015 à décembre 2018, qui visait à relever les défis de l'assemblage de pièces TPC et métalliques. Coordonné par l'Institut für Verbundwerkstoffe (IVW) - une institution de recherche à but non lucratif de l'état de Rhénanie-Palatinat et l'Université technique de Kaiserslautern, Allemagne - FlexHyJoin a réuni 10 partenaires de toute l'Europe pour développer un processus automatisé permettant un toit automobile TPC structure à assembler en un corps métallique en blanc (BIW). La stratégie consistait à produire un joint à poids neutre et à haute résistance - sans adhésifs ni attaches - en prétraitant au laser des supports métalliques et en les fixant au raidisseur de toit par induction et assemblage au laser. Ceci a été réalisé dans une seule cellule de production automatisée avec contrôle de processus intégré et essais non destructifs (END) en ligne.
Démonstrateur hybride en 140 secondes
Le partenaire du projet Centro Ricerche Fiat (Pomigliano d'Arco/Naples, Italie) a fourni les spécifications pour la partie du démonstrateur — un raidisseur de toit pour la Fiat Panda citadine qui est actuellement fabriquée en acier. Pour FlexHyJoin, la pièce a été thermoformée à partir d'un composite thermoplastique (Fig. 1) par Gubesch Thermoforming (Wilhelmsdorf, Allemagne) en utilisant une feuille d'organo-fibre de verre tissée Tepex Dynalite 102/polyamide 6 (PA6) de 1,5 millimètre d'épaisseur fournie par Bond-Laminates (Brilon, Allemagne). Afin de joindre ce raidisseur de toit TPC dans le Panda 's steel BIW, un ensemble de supports latéraux (gauche et droit) en acier DC04 de 0,7 millimètre d'épaisseur ont été assemblés au laser sur les extrémités. Un support central fabriqué à partir du même matériau a été fixé à l'aide d'un assemblage par induction. FlexHyJoin a montré que les deux méthodes d'assemblage peuvent être utilisées pour la production de structures hybrides industrielles.
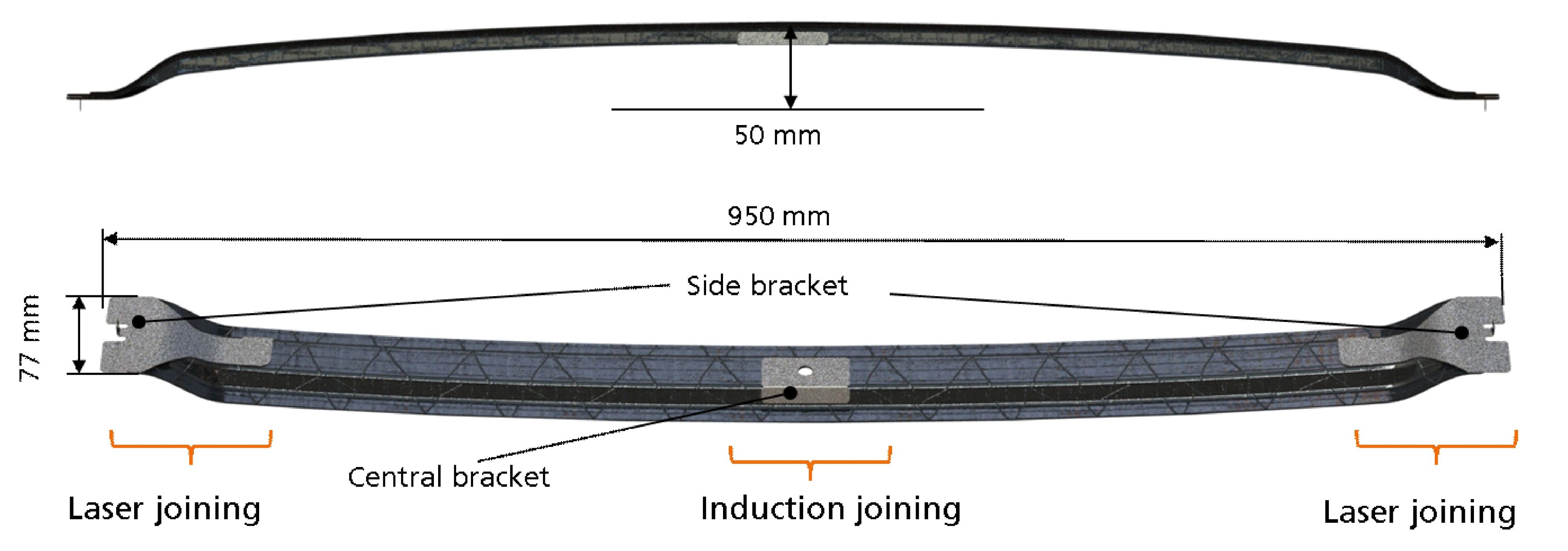
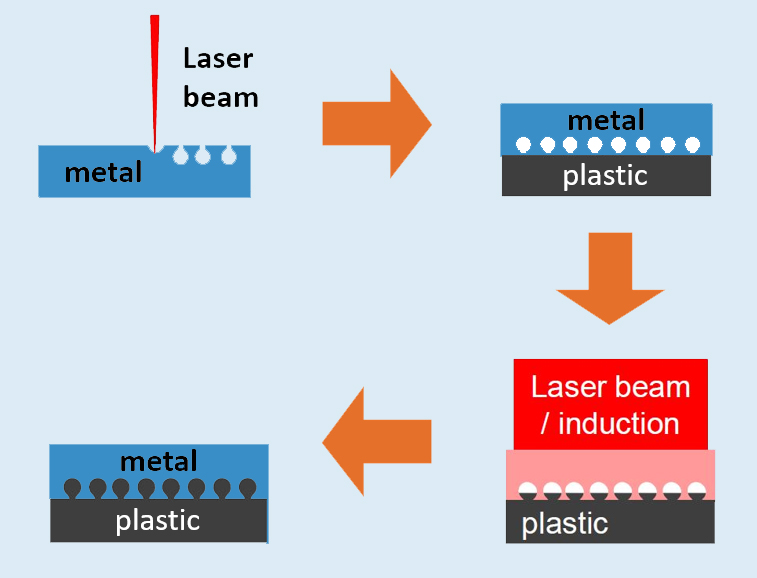
Fig. 1 Structuration de surface pour assemblage hybride
FlexHyJoin démontre l'assemblage par laser et par induction de supports en acier à un raidisseur de toit GF/PA6 estampé (en haut ). Ces joints hybrides reposent sur le traitement de surface des supports métalliques pour créer des contre-dépouilles, qui sont remplies de plastique fondu pendant les étapes du processus d'assemblage (en bas ).
Origine | IVW
La simple fusion de la matrice PA6 sur les supports en acier ne produirait pas une jointure suffisamment résistante pour répondre aux exigences structurelles. Ainsi, un traitement de surface au laser était nécessaire avant l'assemblage. « La surface des supports a été structurée par un laser pour créer des contre-dépouilles », explique Johannes Voithofer, chef de projet chez Fill Gesellschaft (Gurten, Autriche), qui a été chargé d'assembler et d'intégrer la cellule de production automatisée. « Les brackets traités sont posés sur la pièce composite. La chaleur et la pression sont ensuite appliquées lors de l'assemblage, provoquant l'écoulement de la matrice PA6 du composite dans les contre-dépouilles induites par le laser [voir Fig. 1]. Le processus de structuration a été développé par un autre partenaire, l'Institut Fraunhofer de technologie laser (ILT, Aix-la-Chapelle, Allemagne), et aboutit à une jonction métal-composite qui combine l'adhérence du matériau ainsi que le verrouillage mécanique.
Les pièces jointes sont ensuite transférées vers une station CND où elles sont scannées à la recherche de défauts à l'aide d'un type de thermographie. « Les projecteurs halogènes sont utilisés pour le chauffage modulé de la surface composite », explique Vitalij Popow, associé de recherche IVW et responsable du développement du FlexHyJoin NDT et du contrôle de processus. « Cela conduit à un champ de température oscillant au sein de la structure composite. Nous analysons la réponse thermique de la surface au fil du temps et identifions les défauts des joints. Les tests entièrement automatisés sont effectués dans la cellule de production pour chaque composant fabriqué. La validation du procédé a été réalisée sur environ 400 joints.
La cellule de production automatisée FlexHyJoin, telle qu'elle est actuellement configurée, exécute la structuration laser, l'assemblage et le CND en parallèle avec des temps de cycle de 81 secondes, 98-108 secondes et 100 secondes, respectivement, sans compter le temps de transfert robotique des pièces entre les stations. Voithofer dit que le temps de cycle par pièce hybride terminée est d'environ 140 secondes.
Fig. 2 Permettre l'assemblage hybride à l'échelle industrielle
La cellule de production pilote FlexHyJoin comprend trois stations modulaires de structuration de surface, d'assemblage et de CND. Le robot de manutention unique de la cellule transfère les composants du tiroir de chargement vers chacune de ces stations, en plaçant les pièces hybrides finies dans un tiroir adjacent. Origine | IVW et remplissage
Structure laser
Le processus de structuration au laser produit des lignes avec des géométries en contre-dépouille sur la surface de jonction des supports métalliques. Pour FlexHyJoin, les contre-dépouilles mesuraient 75 micromètres de large et 215 micromètres de profondeur. Ces mesures, ainsi que le nombre de lignes et le motif global des lignes peuvent tous être personnalisés et, idéalement, sont adaptés pour répondre aux exigences de temps de pièce et de cycle.
« La position ainsi que le nombre de microstructures sur la surface d'assemblage peuvent être adaptés à la charge du composant », explique Stefan Weidmann, associé de recherche IVW et chef de l'équipe de développement de l'unité d'assemblage par induction FlexHyJoin. « La distance entre les microstructures peut être réduite dans les zones fortement chargées de la surface de jonction et augmentée dans les zones moins chargées pour permettre un processus de microstructuration efficace. »
La structuration est réalisée par ablation de la surface du support métallique à l'aide d'un laser à fibre monomode haute puissance fourni par IPG Photonics (Burbach, Allemagne). Ce laser YLR-1000-WC a une puissance maximale de 1 000 watts à une longueur d'onde d'émission de 1 070 nanomètres. "Nous avons utilisé le laser à fibre monomode pour le processus de microstructuration en raison de sa capacité de focalisation élevée, en maintenant une taille de spot d'environ 40 micromètres", explique Christoph Engelmann, chef d'équipe du traitement des polymères chez Fraunhofer ILT.
Le laser est contenu dans une tête optique montée sur un bras robotique ABB 1200. « À l'intérieur de la tête optique, nous avons deux miroirs galvanométriques pour dévier le faisceau dans un champ de travail de 240 millimètres sur 240 millimètres », détaille Engelmann. « De plus, il y a une lentille mobile pour suivre la hauteur z (z-shifter). Nous n'avons utilisé le robot que pour positionner la tête de balayage au-dessus des composants métalliques, puis le faisceau est dévié par les miroirs et la position z pour chaque ligne de la microstructure est adaptée par le z-shifter. Ainsi, il n'y a pas de mouvement de la tête pendant le traitement. De cette façon, nous sommes capables de traiter des pièces 2.5D, en restant dans la même position z pour chaque ligne discrète mais capable de s'ajuster entre les lignes. »
« Pour des raisons de sécurité, les unités de structuration et d'assemblage sont fermées », explique Voithofer, en notant les armoires noires dans la cellule de production pilote (Fig. 2). Ainsi, un portail/porte automatisé reste abaissé pendant les opérations laser, s'ouvrant pour le retrait des pièces finies et l'insertion de nouvelles.
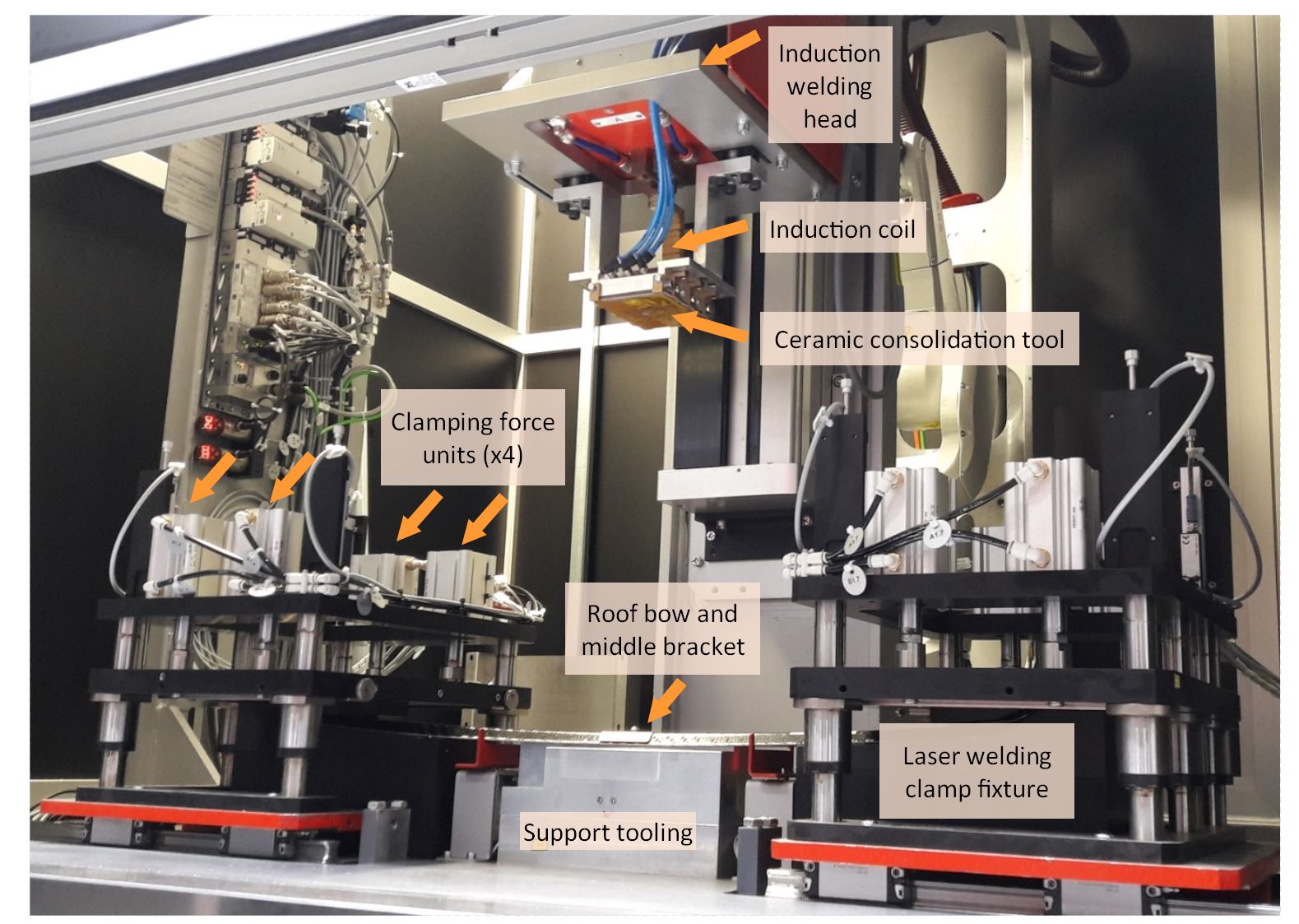
Fig. 3 Cellule d'induction et de jonction laser
Dans la cellule d'assemblage, l'assemblage par induction est utilisé pour fixer le support central tandis que l'assemblage au laser est utilisé pour joindre les supports latéraux à chaque extrémité de l'arc de toit composite. Origine | IVW et remplissage
Induction et assemblage laser
Adjacente à la cellule de structuration se trouve la cellule d'assemblage, qui comprend deux opérations distinctes :l'assemblage par induction du support central et l'assemblage laser des supports latéraux gauche et droit. « Pour les pièces plus grandes avec une complexité modérée comme le support central, l'assemblage par induction est une méthode d'assemblage plus appropriée », explique Weidmann. « Un outil de consolidation en céramique avec inducteur applique une pression sur la zone de jonction et est perméable au champ électromagnétique, ce qui permet un apport énergétique efficace dans le support métallique pour le chauffage. Ceci est pratique pour les formes plates, mais plus difficile pour les formes complexes, telles que la géométrie des supports latéraux. Ainsi, il était plus efficace d'utiliser l'assemblage au laser pour ceux-ci. Weidmann ajoute :« L'assemblage par induction est préférable pour les pièces de grande taille et de complexité modérée, tandis que l'assemblage au laser est plus approprié pour les pièces à haute complexité. »
Un trou percé dans le raidisseur de toit composite l'aligne sur le dessus de l'outillage de support, façonné pour correspondre à la courbure du raidisseur thermoformé. Un trou découpé au laser dans le support central le positionne sur le raidisseur de toit tandis que les supports latéraux sont alignés par leur forme qui correspond aux extrémités du raidisseur de toit.
"Le support central a été joint à l'aide de discontinu assemblage par induction. « Il s'agit essentiellement d'un assemblage par presse quasi-statique », explique Weidmann, « ce qui signifie simplement qu'il s'agit d'un processus statique, réalisant un assemblage surfacique en un seul endroit, mais il y a un mouvement dans la direction z car l'épaisseur du composite change légèrement en raison à la pression de consolidation appliquée lors de l'assemblage (d'induction). »
L'unité d'assemblage par induction contient un générateur haute fréquence KGR (Brandizzo, Italie) pour fournir un champ électrique alternatif à la bobine d'induction. La tête est déplacée via un moteur électrique et une broche (Fig. 3) de sorte que l'outil de consolidation en céramique appuie sur le support métallique. La bobine d'induction dans l'outil de consolidation fait chauffer le métal, ce qui fait fondre la matrice composite et crée le joint. « La pression est appliquée tout au long du chauffage et du refroidissement », note Weidmann.
L'assemblage au laser des supports latéraux commence simultanément à l'assemblage par induction. Deux dispositifs de serrage, situés de chaque côté de l'outillage de support, peuvent appliquer une force de serrage de 4 000 Newtons aux supports latéraux. « Le serrage est nécessaire pour minimiser l'écart entre les composants composites et métalliques », explique Voithofer. « Cela évite les vides dans le joint. » Une fois la force de serrage appliquée, la tête laser se met en position. Il est équipé d'un laser à diode LineBeam fourni par Leister Technologies (Kägiswil, Suisse). Johannes Eckstaedt de Leister explique que ce laser a une puissance de sortie maximale de 600 watts à une longueur d'onde d'émission de 980 nanomètres. Le faisceau est formé sur une ligne de 27 millimètres sur 1 millimètre par des lentilles optiques et est focalisé sur le support métallique. La tête laser est montée sur un bras robotisé qui lui permet de se déplacer le long de la surface profilée du support. « Nous avons défini des vitesses différentes pour chaque zone des supports afin d'obtenir une température d'assemblage homogène, réduisant ainsi la contrainte thermique pour les meilleurs résultats d'assemblage », explique Eckstaedt.
En général, l'assemblage au laser peut utiliser l'assemblage par transmission ou par conduction thermique. Pour l'assemblage par transmission laser, le composite à assembler doit être transparent pour la longueur d'onde sélectionnée du laser. Le laser traverse ensuite le composite, frappe la surface métallique du support et le chauffe. Cependant, cette méthode n'a pas été utilisée dans le démonstrateur FlexHyJoin car le stratifié organofeuille du raidisseur de toit n'était pas transparent au laser. Au lieu de cela, la méthode alternative d'assemblage par conduction thermique a été utilisée. Cela applique simplement le laser directement sur la surface métallique, qui conduit la chaleur à travers le matériau de base métallique vers le composite, faisant fondre la matrice PA6 à 220-300 °C et créant le joint. « En raison de la conductivité thermique élevée des supports en acier, la chaleur du laser se propage rapidement, rejoignant efficacement les supports latéraux », explique Voithofer.
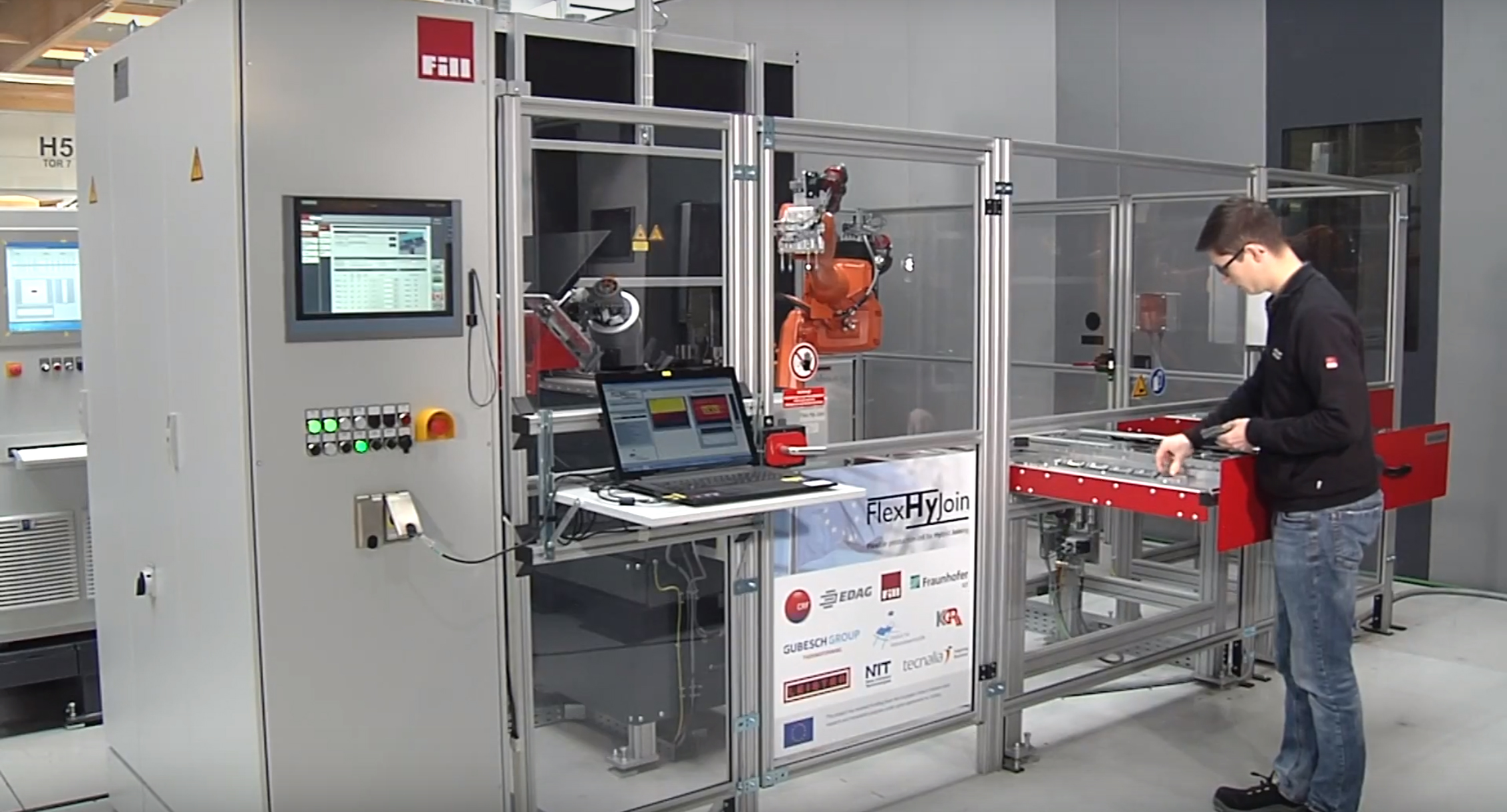
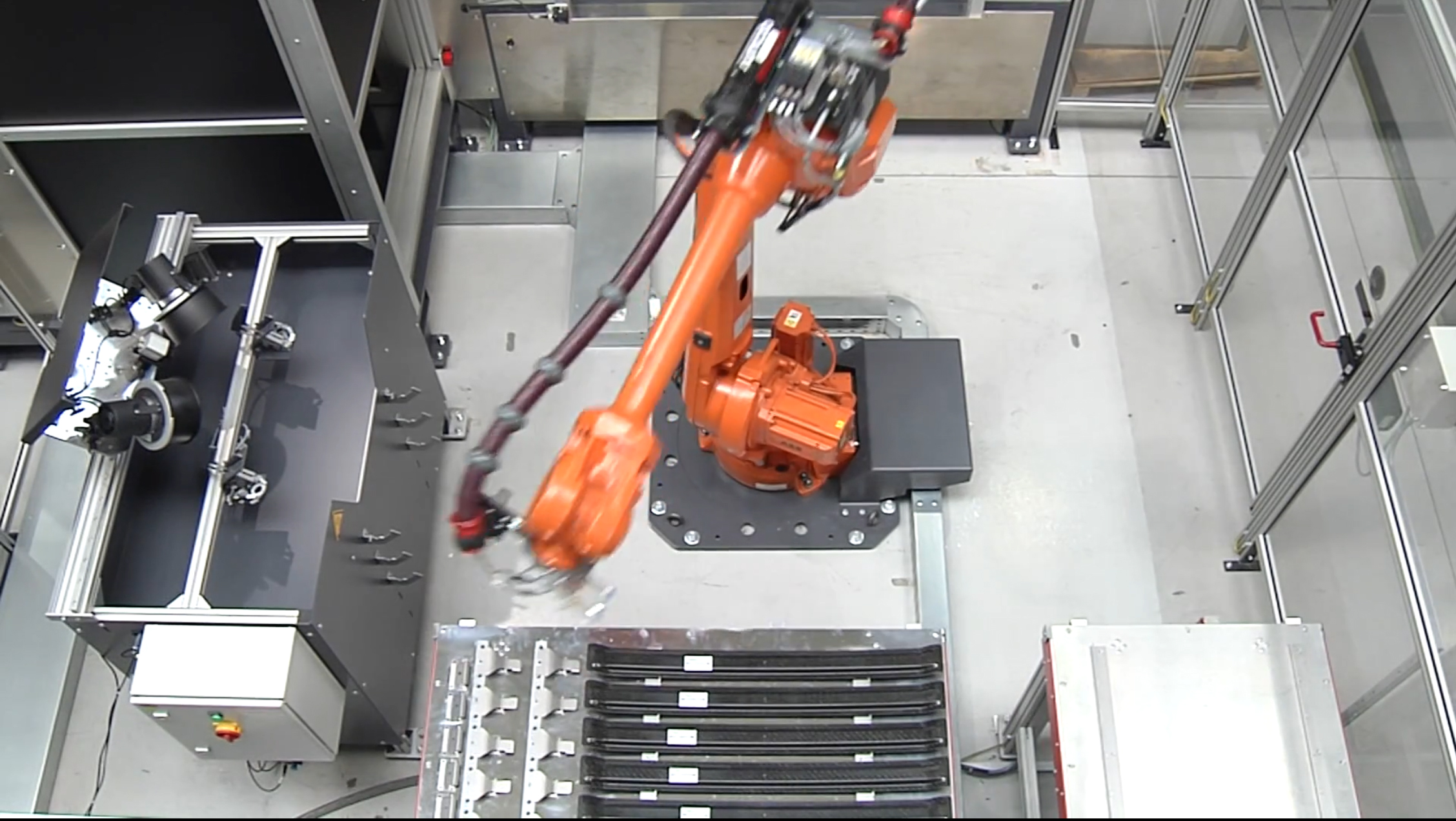
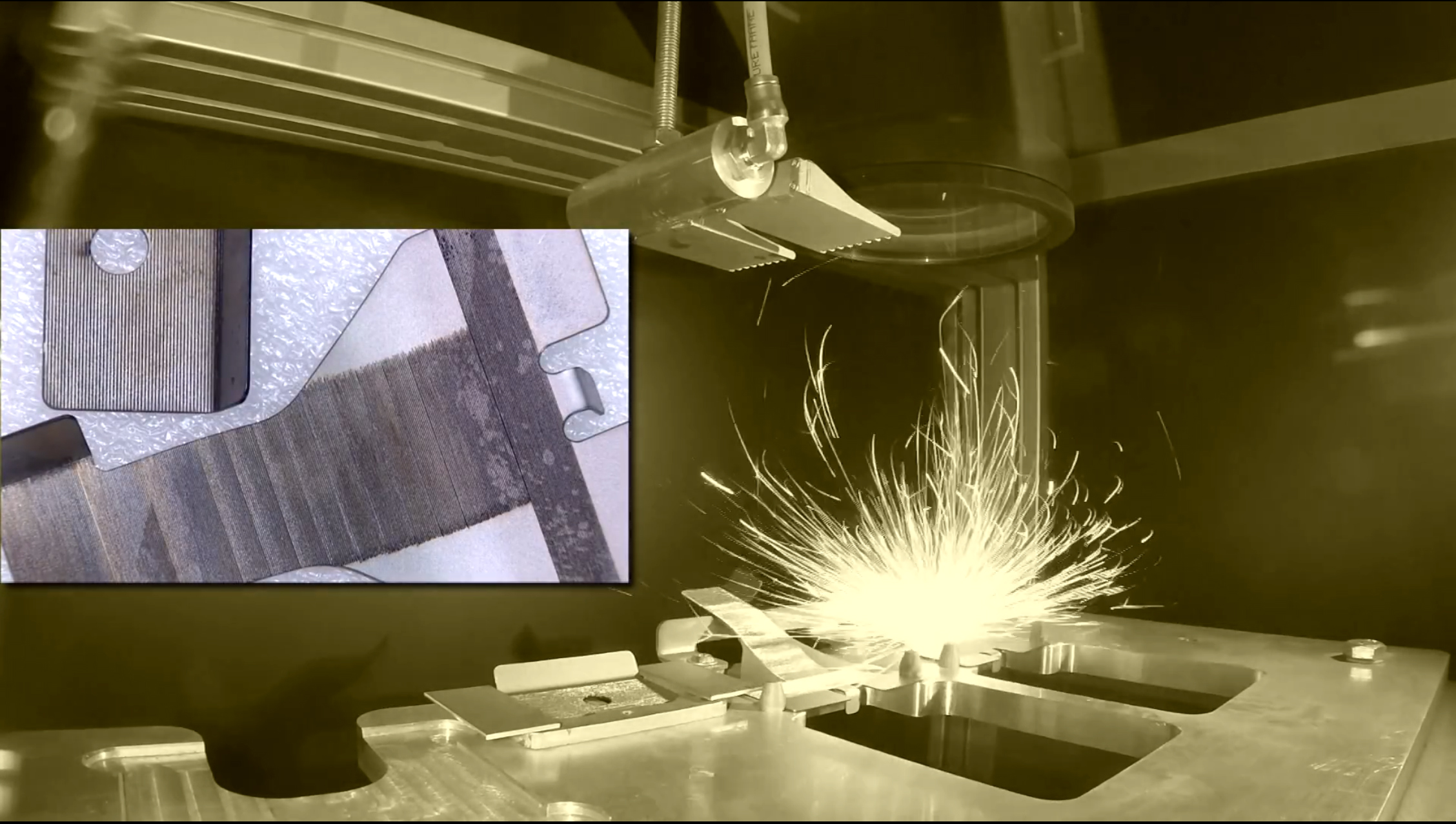
Étape 3. À l'intérieur de la cellule de structuration, un laser à fibre haute puissance crée des contre-dépouilles dans la surface du support à joindre dans le raidisseur de toit composite.
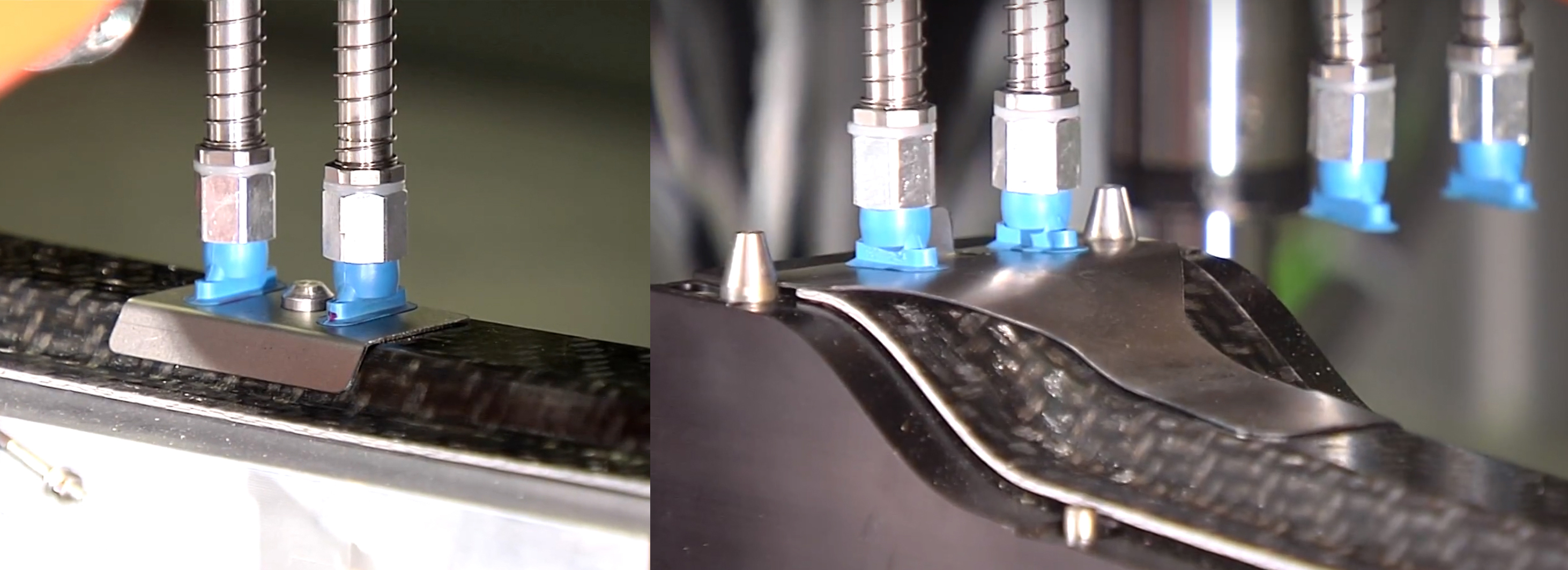
Étape 5. Le robot retourne dans la cellule de structuration, récupère les brackets traités et les pose, côté structuré vers le bas, sur la voûte de toit TPC.
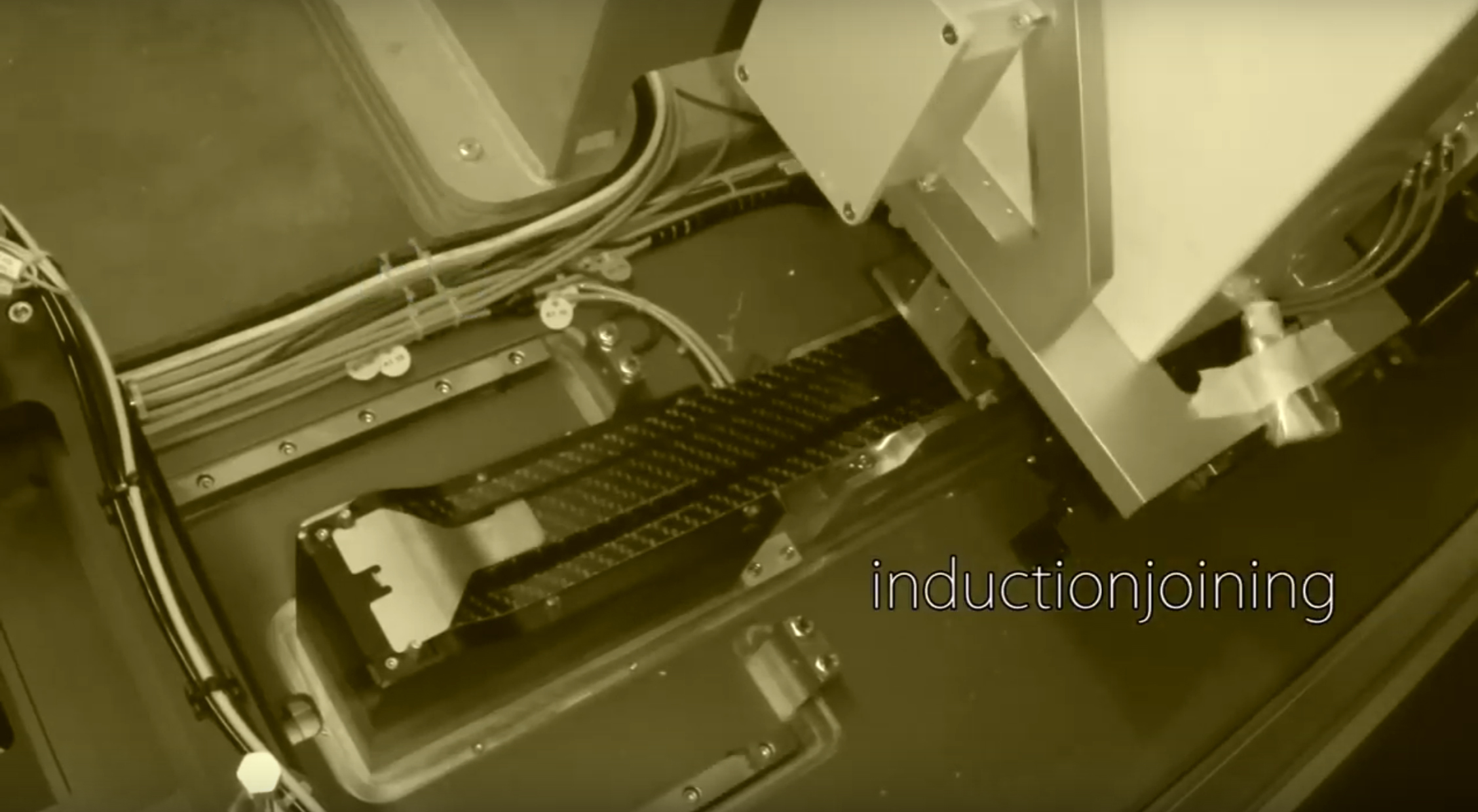
Étape 6. Le robot place ensuite des unités de serrage sur les trois supports. L'unité de jonction par induction s'abaisse sur le support central. La bobine d'induction fait chauffer le support métallique, faisant fondre la matrice PA6 du composite sous-jacent.
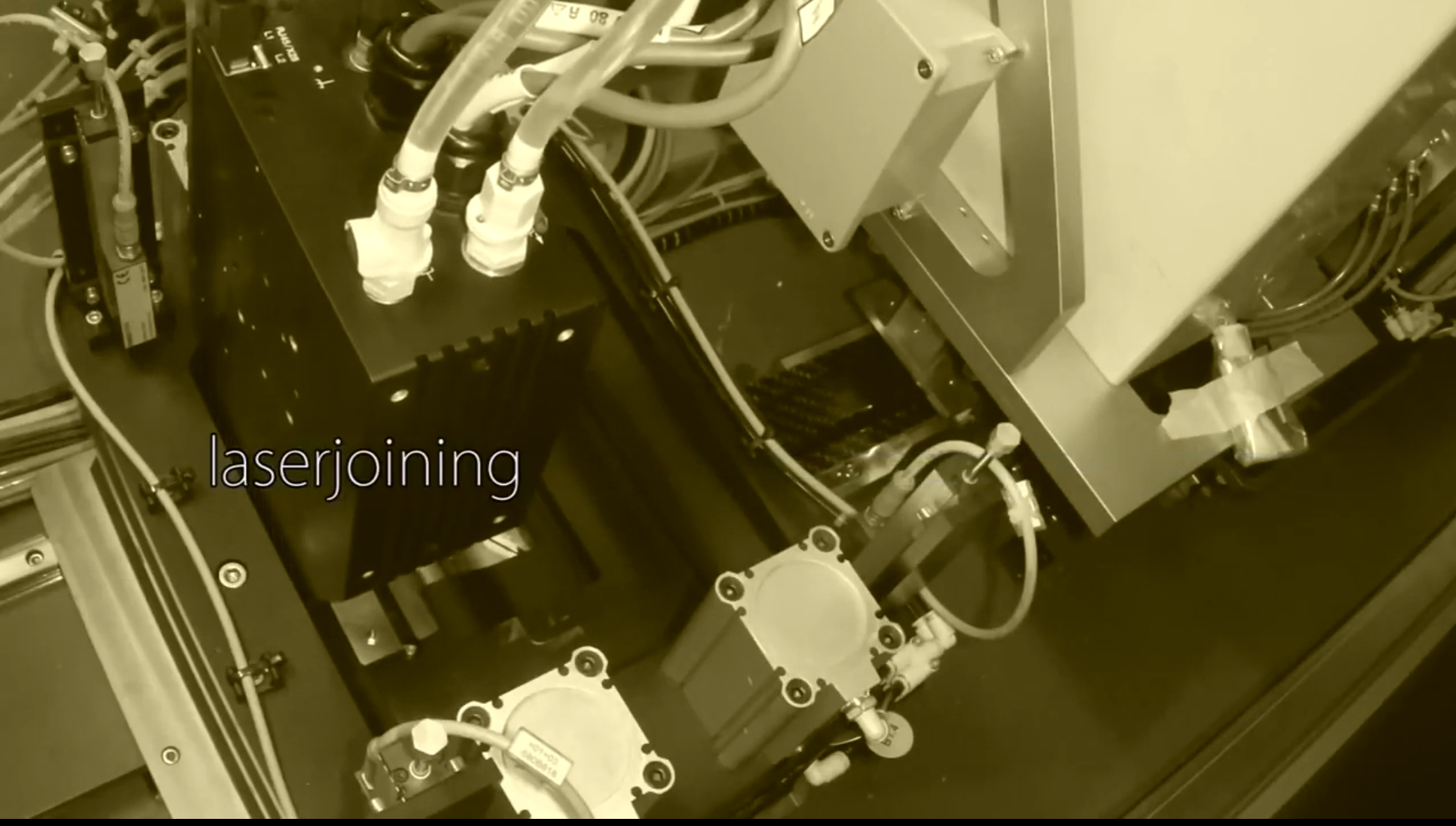
Étape 7. Pendant que l'assemblage par induction est terminé, l'unité d'assemblage laser est abaissée pour joindre les supports de gauche puis de droite. Le laser chauffe le métal, provoquant la fusion de la matrice PA6 sous-jacente dans les contre-dépouilles, créant un joint à haute résistance.
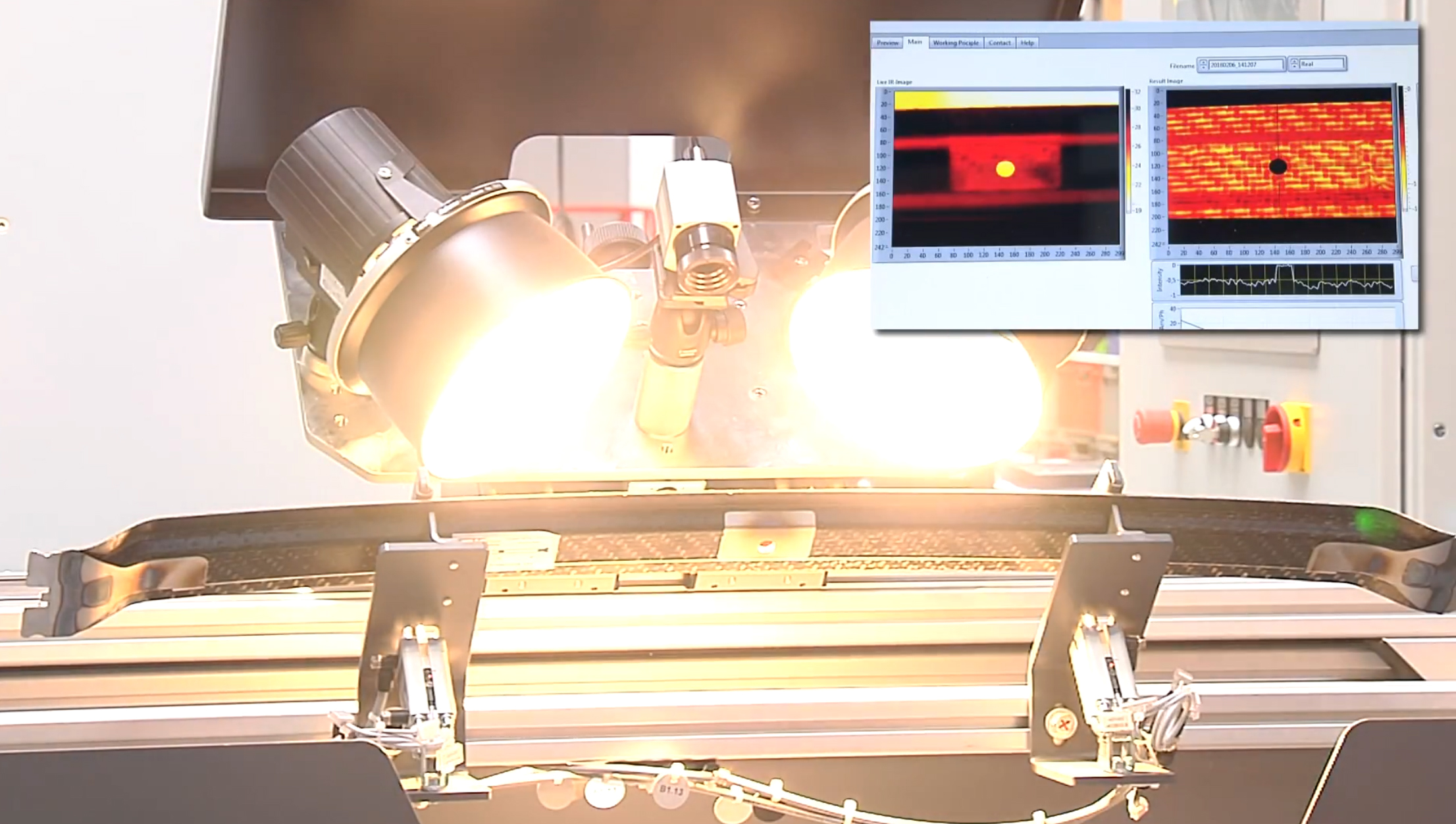
Contrôle des processus de connexion
La méthode de base pour contrôler les deux processus d'assemblage consiste à mesurer la température et le temps par rapport à un ensemble de paramètres optimisés qui ont été définis par des tests. « Par conséquent, nous avons produit des échantillons de test d'assemblage avec différents paramètres et effectué des tests mécaniques pour chaque ensemble de paramètres à l'aide de configurations de test spéciales. Pour le support latéral, une combinaison d'un test de cisaillement et d'un test de pelage a été développée, et pour le support central, nous avons utilisé un test de charge de pression, comparable à un test de cisaillement, mais vous poussez au lieu de tirer, afin d'obtenir une charge de cisaillement dans la zone de jonction », explique Popow. La mise en place de ces tests spéciaux a été conçue en collaboration avec EDAG Engineering GmbH (EDAG, Fulda, Allemagne), qui a également effectué l'analyse des résultats des tests. Suite à cette procédure, le meilleur ensemble de paramètres pour les processus d'assemblage a été identifié puis utilisé dans la cellule de production pilote.
« Le processus d'assemblage par induction a été calibré à l'avance », explique Weidmann. « Nous savons que nous atteignons la température d'assemblage après environ 30 secondes, mais nous mesurons également la température in situ pour des raisons de sécurité afin d'éviter une surchauffe. » Un pyromètre, qui mesure à distance le rayonnement d'une surface, a été utilisé pour mesurer un point chaud connu dans la zone de jonction par induction. « Mais il ne peut pas fournir de mesures précises de la jonction laser en raison du niveau élevé de lumière irradiée et de chaleur in situ », explique-t-il. Cependant, des capteurs de contact pourraient être utilisés sur le côté composite des zones de jonction laser, bien qu'ils ne soient pas applicables au processus de jonction par induction car ils sont généralement en métal et s'échaufferaient par induction et fausseraient la mesure.
« Les zones chauffées de tous les joints sont également couvertes par l'outil de sertissage et les dispositifs de serrage », note Weidmann. « Ainsi, nous avons validé le changement d'épaisseur du composant dû à la pression et à la chaleur avant et après l'assemblage en tant que méthode d'assurance qualité. » Cette variation d'épaisseur est mesurée par un capteur de distance intégré à l'outil de positionnement du raidisseur de toiture (également représenté sur la Fig. 3). « Lorsque nous pressons les pièces ensemble, le capteur de distance est déplacé », explique-t-il. « Lorsque nous appliquons de la chaleur et une pression d'assemblage, le polymère de matrice fondu s'écoule dans les cavités de la structuration laser et est légèrement expulsé de la zone d'assemblage jusqu'à ce que le joint refroidisse. Cela conduit à un changement d'épaisseur qui est enregistré par le capteur de distance. Weidmann et l'équipe IVW ont corrélé cette distance à la qualité de la pièce. "Un changement d'épaisseur - en d'autres termes, un compactage - supérieur à 0,1 millimètre signifie que la qualité du joint est bonne", note Weidmann.
END en ligne
IVW a développé une autre méthode d'assurance qualité :les tests de thermographie en ligne. « Pour l'assurance qualité, l'objectif principal était de voir les propriétés dans la zone de jointure », explique Popow. « Mais c'était très difficile, nous avons donc effectué une thermographie du côté composite des joints une fois la pièce terminée. »
IVW a choisi une technique de thermographie active appelée thermographie verrouillée, car elle offre un meilleur rapport signal/bruit que les autres méthodes actives (par exemple, la thermographie à phase pulsée) et peut également inspecter les défauts plus profonds. "L'idée de base est de mettre de la chaleur dans le composite, qui conduit ensuite dans la zone de jointure et retourne à la surface", explique Popow. « Avec la thermographie de verrouillage, le composant est excité avec une fréquence définie sur plusieurs périodes. Nous analysons ensuite cette réponse dans le temps. Si vous avez des zones entre la surface composite et la zone de jointure qui ne sont pas homogènes en raison d'un vide ou d'un défaut, cela se verra dans la réponse thermique. »
La réponse thermique est capturée sous forme d'image. Les points qui composent ces images sont des pixels, abréviation d'éléments d'image. Chaque pixel est aussi un point de mesure. Ainsi, le signal de température pour chaque pixel sur toute la zone d'inspection est analysé. "En conséquence, vous obtenez des informations d'amplitude et de phase pour chaque pixel, et le logiciel reconstruit ensuite cela en une image, qui peut être inspectée visuellement", ajoute-t-il. Mais il a également fourni de grands ensembles de mesures pour les 126 pièces testées. « Nous avons corrélé ces résultats d'END avec les résultats des tests mécaniques effectués par EDAG », explique Popow. Son équipe a également testé la zone de jointure après avoir retiré les supports, c'est-à-dire des tests destructifs. "Nous avons ainsi corrélé trois ensembles de résultats de test et pouvons désormais identifier les zones de liaison à faible résistance par rapport à haute résistance à partir de l'analyse visuelle des résultats de la thermographie", dit-il.
Cellule intégrée pour la production de masse
L'une des plus grandes réalisations de FlexHyJoin, selon Weidmann, est d'intégrer toutes les unités technologiques, chacune développée par un partenaire de projet différent, dans une ligne de production automatisée et optimisée. Voithofer, celui qui intègre l'équipement chez Fill, explique que « chaque ensemble d'équipement qui nous est expédié utilisait un contrôleur différent. J'ai dû concevoir un automate maître pour contrôler toutes les différentes unités de traitement. Cela comprenait les boîtiers laser et le robot de manipulation de la cellule, qui ont été fournis par Fill. "Il était également très difficile de faire fonctionner toutes ces étapes de processus ensemble, car elles prennent des durées différentes", ajoute-t-il.
Voithofer a commencé par développer une architecture pour chaque unité de traitement et robot, en considérant comment les positionner pour le meilleur flux. « Notre concept était de garder les trois stations — structuration, assemblage et CND — modulaires, dans trois boîtiers distincts », explique-t-il. « De cette façon, nous pourrions extraire des unités individuelles et les utiliser lors de salons professionnels ou d'autres projets de démonstration, puis les retourner. Ainsi, la cellule de travail est modulaire, mais intégrée. »
Les décennies d'expérience de Fill dans ce type d'intégration de systèmes pour la production de composites en série ont permis de réaliser ce que Popow considère comme le plus grand exploit de FlexHyJoin :passer de l'échelle du laboratoire à l'échelle industrielle. « Nous sommes le premier consortium à réaliser un procédé comme celui-ci, qui convient à la production en série de composites liés au métal », dit-il. « Ce processus peut être utilisé pour de nombreuses pièces automobiles telles que les biellettes stabilisatrices, les pare-chocs et les portes », note Voithofer. "Il existe de nombreuses pièces composites qui se connectent à des pièces métalliques dans un BIW léger."
Adaptation pour plusieurs industries
Cependant, quelques modifications sont nécessaires avant que la cellule ne soit mise en production en série. « Nous ne conserverions plus la structuration et l'assemblage laser dans des boîtiers séparés, mais les combinerions en un seul », explique Voithofer. « Cela éliminerait le besoin d'ouvrir et de fermer les portes de l'enceinte entre ces processus, réduisant ainsi le temps de cycle. » Il relierait également toutes les stations de manière linéaire sur une bande transporteuse. La ligne fonctionnerait ainsi en continu, les pièces étant récupérées et remises sur le convoyeur pour chaque station avant de sortir de la cellule prêtes à être assemblées dans un BIW. Cela réduirait encore le temps de cycle. De plus, des tiroirs agrandis capables d'alimenter des centaines de pièces permettraient à la ligne de fonctionner pendant des équipes entières sans avoir besoin de réapprovisionnement.
Bien que cette cellule de production pilote ait été ciblée pour l'industrie automobile, Popow note qu'elle peut être facilement adaptée à l'aérospatiale, aux produits de sport/de consommation et aux applications industrielles. "C'était en fait l'une des principales directives", explique Weidmann, "qu'il doit pouvoir assembler différentes géométries et pièces. Le seul changement devrait être l'outil de compactage par assemblage par induction, les dispositifs de serrage pour l'assemblage au laser et l'outillage de support. Les parties principales de la cellule devraient rester les mêmes. Il note qu'IVW a également démontré l'assemblage hybride de titane et d'acier à des composites organofeuilles tissés en fibre de carbone/sulfure de polyphénylène (PPS) et développe actuellement des démonstrations de polyétheréthercétone (PEEK) et de polyéthercétonecétone (PEKK). « Cela nécessite simplement d'adapter les processus d'assemblage à des températures plus élevées et de redéfinir les paramètres de processus optimaux », explique Weidmann. "La cellule est ouverte à une variété de matériaux, y compris l'aluminium et le cuivre ainsi que d'autres systèmes matriciels composites thermoplastiques tels que le polypropylène et le polyéthylène."
« Les partenaires du projet ont bien travaillé ensemble et sont ravis d'aller plus loin dans le développement », note-t-il. "Nous pensons que ce type de production est très prometteur, et la réponse que nous avons reçue de l'industrie jusqu'à présent montre qu'il existe une variété d'entreprises qui voient également cette promesse."
Résine
- Solvay augmente la capacité des composites thermoplastiques
- Synthèse et étude des caractéristiques optiques des structures sphériques hybrides Ti0.91O2/CdS
- Impédance de surface des métasurfaces/structures hybrides en graphène
- Fraunhofer met en service des cellules de production automatisées Engel pour la R&D sur les composites thermoplastiques
- L'importance de la sélection de résine
- Le DLR Institute of Structures and Design augmente la maturité des structures de fuselage en composite thermoplastique
- Le consortium cible des solutions pour les structures composites thermoplastiques en fibre de carbone
- Composite de bardage architectural dévoilé
- Composite + métal :technologie hybride à profil creux