Compression RTM pour la production des futures aérostructures
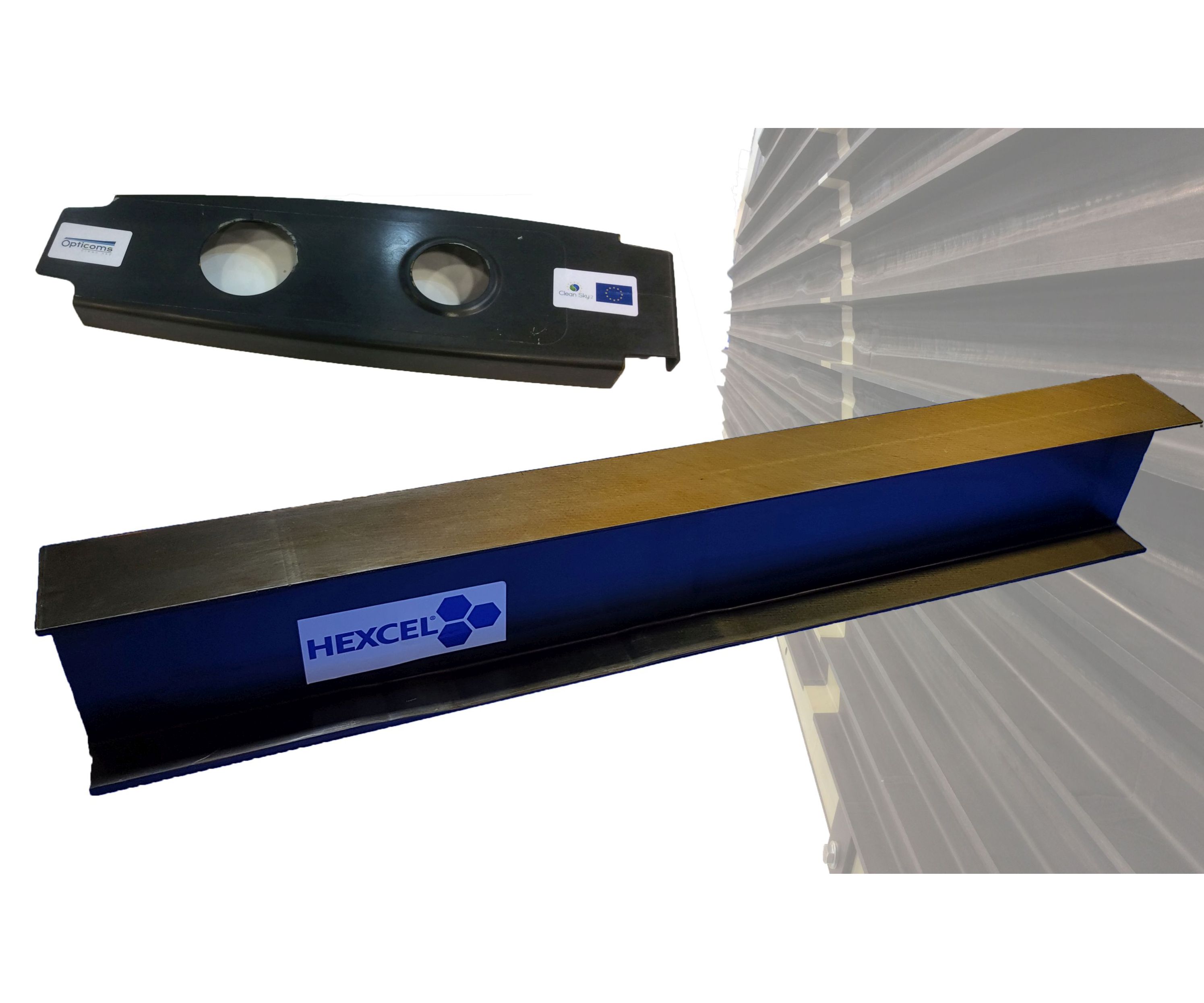
Les composites ont obtenu une place permanente dans les cellules des avions de ligne commerciaux, car ils permettent des structures légères et à haute résistance qui offrent des coûts de maintenance inférieurs à ceux du métal. Les projections actuelles pour la prochaine génération d'avions à fuselage large et étroit montrent une croissance continue des cellules composites, mais seulement si les matériaux et les processus peuvent atteindre des objectifs ambitieux de faible coût et de taux de production élevés. Bien que le préimprégné époxy durci à l'autoclave ait régné en maître dans les cellules en polymère renforcé de fibres de carbone (CFRP) à ce jour, les développeurs d'avions de nouvelle génération poursuivent activement les technologies hors autoclave (OOA) avec automatisation intégrée et inspection en ligne en tant que catalyseurs clés pour future production de l'Industrie 4.0.
Le fournisseur d'équipements et d'automatisation Techni-Modul Engineering (Coudes, France) et sa filiale américaine Composite Alliance Corp. (Dallas, Texas, États-Unis) se sont associés aux unités commerciales britanniques et françaises du fournisseur de matériaux avancés Hexcel (Stamford, Connecticut, États-Unis) pour démontrer la production automatisée d'OOA de nervures et de longerons en PRFC. Les pièces sont fabriquées avec un préformage automatisé de renforts en fibre de carbone sèche Hexcel et un procédé de moulage par transfert de résine par compression (C-RTM) qui offre une infiltration rapide de la résine époxy liquide Hexcel HexFlow RTM6 pour produire des pièces avec 60 % de volume de fibres et moins de 1 % de vides dans un cycle de 2,5 à 3,0 heures qui peut être mis à l'échelle pour produire plusieurs pièces pour une production à cadence élevée.
Développement de renforts secs
« Nous considérons le moulage composite liquide (LCM) comme une réponse au défi à trois volets pour réduire les coûts, être prêt pour la cadence et fournir des performances de structure primaire », explique Rémy Pagnac, Ingénieur support technique Hexcel pour le moulage de composites liquides. Hexcel a développé son tissu HiMax non serti (NCF) et ses matériaux en fibre de carbone unidirectionnelle HiTape (UD) pour répondre aux besoins de performance de la structure primaire lors de l'utilisation des processus LCM. HiMax permet de mettre en place rapidement de grandes structures plates telles que des peaux d'ailes, tandis que HiTape permet des layups sur mesure pour de grandes structures complexes avec un minimum de déchets. « Nous pouvons obtenir des propriétés équivalentes à celles des préimprégnés UD de dernière génération », ajoute Pagnac.
Hexcel s'est efforcé de réduire le volume et d'améliorer la drapabilité avec HiMax NCF, y compris un fil de maille fin 20 dTex. Les matériaux HiMax sont fabriqués dans l'ancienne usine Formax de Leicester, au Royaume-Uni, qu'Hexcel a acquise en 2016. Les multiaxiaux légers à remorquage étalés produits dans cette usine avaient déjà une longue histoire de fourniture de solutions pour des applications exigeantes telles que les yachts de course, les supercars et la Formule 1 voitures de course. Désormais, les matériaux NCF ont été utilisés dans un projet de démonstrateur d'aile réalisé par Airbus Defence and Space (Airbus DS, Cadix, Espagne) et Danobat (Elgoibar, Espagne) en utilisant la technologie Automated Dry Material Placement (ADMP) de ce dernier - un type de placement automatisé de fibres. (AFP) pour NCF (voir « Proving viability for dry fabrics infusion for large aerostructures ») — et dans le projet ZAero parrainé par Airbus pour les structures CFRP zéro défaut telles que les revêtements d'aile renforcés par des longerons (voir « Fabrication zéro défaut de pièces composites »).
Avec HiMax et HiTape, Hexcel intègre des couches de voile de filament thermoplastique mince et de faible poids surfacique qui agissent comme un liant, éliminant ainsi le besoin de liants en poudre traditionnellement utilisés dans les matériaux secs pour le préformage et le moulage liquide. Pour HiMax, ce voile est intercalé entre des plis NCF; pour HiTape, le voile est appliqué des deux côtés de l'uni-ruban en fibre de carbone. «Avec cela, vous n'avez pas besoin d'utiliser de liant en poudre pour maintenir les couches UD en place», explique Pagnac. « HiTape est calibré et n'est pas une bande refendue, il n'y a donc pas de fuzz et il y a moins de variation de largeur pour un traitement AFP amélioré. Le voile thermoplastique ajoute également de la ténacité au stratifié final, et nous avons démontré que nous pouvons atteindre des taux de dépôt de matériau élevés avec la prochaine génération de machines AFP. Dans un article SAMPE de mai 2015, Hexcel décrit une préforme à simple courbure fabriquée à l'aide de HiTape de 0,25 pouce de large appliqué avec une machine AFP Coriolis Composites (Quéven, France) équipée d'un laser à une vitesse de drapage de 1 mètre/seconde. Il a également travaillé avec l'équipement AFP d'Electroimpact (Mukilteo, Wash., États-Unis) pour démontrer des taux de dépôt allant jusqu'à 150 kilogrammes/heure pour une aérostructure de longeron pleine grandeur.
Fig. 1 Compression RTM
En C-RTM, la préforme sèche est placée dans un moule RTM, mais le moule n'est que partiellement fermé, laissant un espace entre la préforme sèche et la surface supérieure du moule. Le vide est ensuite appliqué, la résine est injectée et la presse ferme l'espace dans le moule, poussant la résine liquide vers le bas dans la préforme dans la direction z sur toute la pièce. Origine | Hexcel

Adaptation du C-RTM pour l'aérospatiale
Le C-RTM a été introduit pour la première fois avec le RTM haute pression (HP-RTM) pour les composites automobiles. Comme avec le RTM conventionnel, le C-RTM consiste à placer une préforme en fibre sèche dans un moule en métal assorti, à injecter de la résine liquide dans la préforme, puis à appliquer de la chaleur et de la pression à l'aide d'une presse actionnée. En C-RTM, cependant, le moule n'est que partiellement fermé, laissant un espace entre la préforme sèche et la surface supérieure du moule (Fig. 1). Le vide est ensuite appliqué, une dose précise de résine mélangée est injectée et la presse ferme l'espace dans le moule, forçant la résine liquide à descendre dans la préforme dans la direction z sur toute la pièce. « C'est beaucoup plus rapide que d'injecter la résine dans le plan à travers la pièce », explique Thomas Chevallet, ingénieur procédés de Techni-Modul Engineering.
Techni-Modul Engineering a vu une opportunité d'adapter C-RTM pour l'aérospatiale dans le cadre de son rôle de partenaire dans le projet Clean Sky 2 « Optimized Composite Structures » (OPTICOMS). Organisé au sein du Work Package B-1.2 (« Structures composites plus abordables »), OPTICOMS vise à réduire les coûts de production des petits avions (par exemple, les avions de ligne régionaux) via des structures intégrées et une fabrication automatisée, en explorant à la fois les méthodes de préimprégné et de résine liquide. OPTICOMS a conçu un démonstrateur d'aile composite comprenant une aile supérieure à trois longerons, réalisée sous la forme d'une structure intégrée en un seul coup. L'aile à grande échelle (Fig. 2) fait partie d'un démonstrateur de technologie innovante (ITD) AIRFRAME pour évaluer et faire évoluer les technologies vers le niveau de maturité technologique (TRL) 6 pour les avions de nouvelle génération en production à partir de 2025. Israel Aerospace Industries (Lod, Israël) a été sélectionné comme coordinateur d'OPTICOMS en juillet 2016. Le consortium comprend également l'équipementier de petits avions Piaggio Aerospace (Savone, Italie), Techni-Modul Engineering et les fournisseurs d'équipements AFP Coriolis Composites et Danobat.
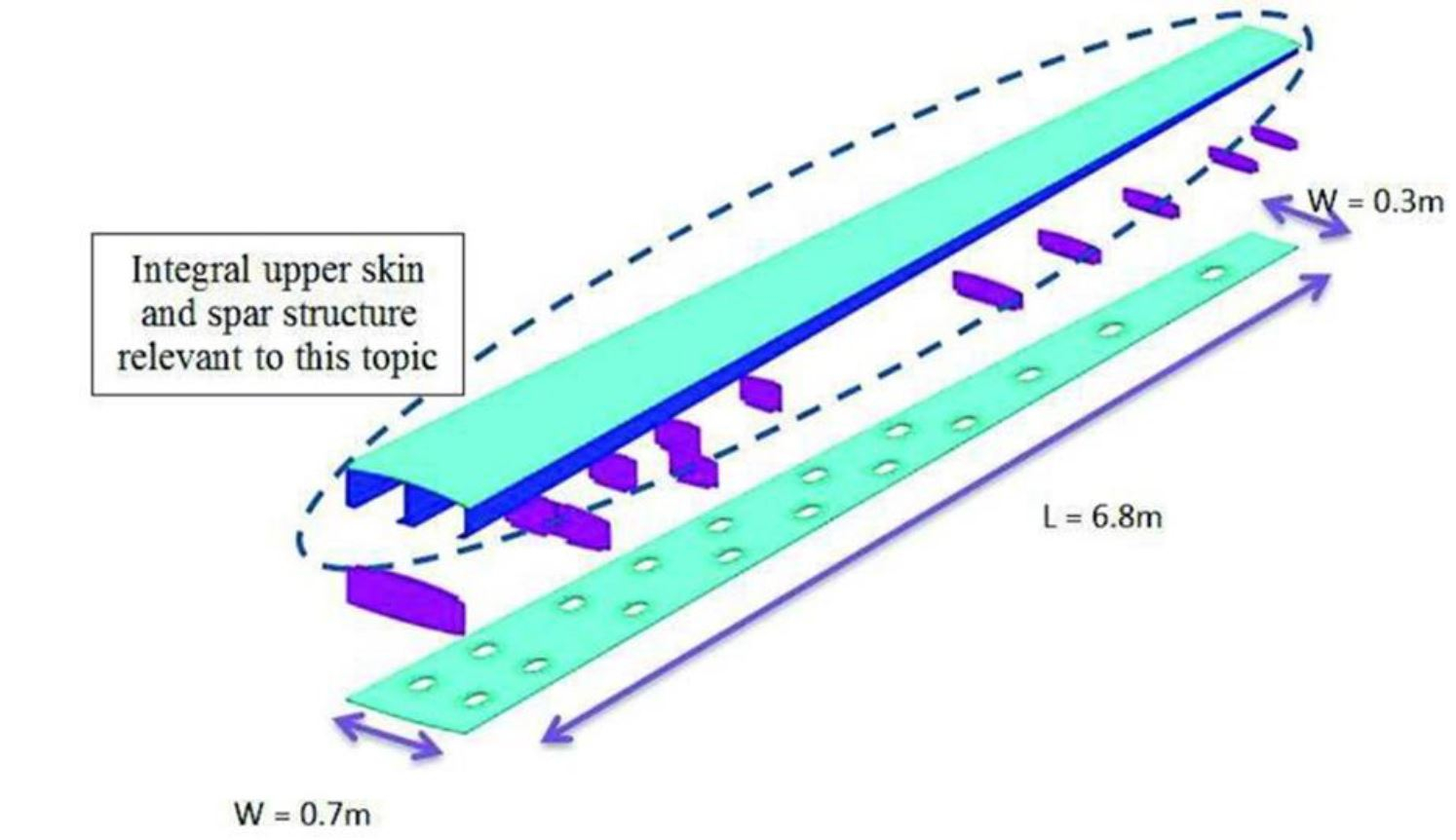
Fig. 2 nervure Clean Sky 2 OPTICOMS
Techni-Modul est partenaire du projet Clean Sky 2 « Optimized Composite Structures » (OPTICOMS) qui a conçu un démonstrateur d'aile composite comprenant un bas d'aile, plusieurs nervures et un haut d'aile à trois longerons. Ce dernier est produit comme une structure intégrée dans un processus unique. Le démonstrateur sera évalué pour les avions de nouvelle génération en production à partir de 2025. Origine | Ciel propre 2
« C-RTM était bien connu dans l'industrie », explique Chevallet, « mais avec HP-RTM, une grosse presse est encore nécessaire. Notre développement consistait à adapter le C-RTM pour une injection rapide utilisant des pressions plus faibles, permettant une production moins coûteuse de pièces aérospatiales avec des exigences très strictes pour un volume de fibres élevé, un alignement de fibres et de faibles vides. Le temps d'injection de la nervure d'aile de 0,7 mètre de long sur 0,2 mètre de large dans le projet OPTICOMS a été réduit de 40 à cinq minutes. Dans un programme de test distinct pour une poutre en I mesurant 900 millimètres de long et 150 millimètres de haut, le temps d'injection a été réduit d'une heure à moins de cinq minutes.

« Cette réduction du temps d'injection offerte par le C-RTM serait encore plus importante pour des pièces de grandes dimensions telles que des ailes pleines ou des pales de rotor d'hélicoptère », ajoute Chevallet. Il note que le C-RTM permet également l'injection de résines à haute viscosité ainsi que des systèmes d'injection à basse pression et des presses à plus faible tonnage, ce qui réduit les coûts. « La pression du moule pendant le C-RTM n'est que de 6 bars, ce qui est bien inférieur à ce qui est utilisé en HP-RTM », explique Chevallet. « Le processus permet d'obtenir des composites de qualité aérospatiale, mais fonctionne bien pour les grandes pièces minces et les petites pièces de forme complexe. »
Préformage automatisé
Bien que l'injection de résine et le moulage OOA plus rapides et moins coûteux soient des éléments clés de cette approche pour une production d'aérocomposites plus abordable, la chaîne de processus nécessite encore plusieurs étapes pour la découpe et la superposition des matériaux et le préformage. « Pour nous, OPTICOMS était aussi une question d'automatisation », explique Chevallet. Techni-Modul Engineering a fourni non seulement un système d'injection C-RTM pour le projet OPTICOMS, mais également un robot pick-and-place et une machine de formage à chaud (HDF), le tout intégré dans une cellule de production entièrement automatisée.
Peu de temps après le lancement d'OPTICOMS en 2016, CAC, filiale de Techni-Modul Engineering, a remporté le prix ACE Equipment and Tooling Innovation Award dans la catégorie fabrication pour sa cellule de préformage 3D automatisée au CAMX 2016 (26-29 septembre, Anaheim, Californie, États-Unis). Capable de produire des préformes 3D à partir de fibres sèches ou de préimprégnés, la cellule utilisait des ventouses à vide pour prélever, placer et plier les plis coupés sur un moule de préforme chauffé. Techni-Modul Engineering et CAC ont développé un logiciel pour préparer les plis découpés de matériaux 2D pour la mise en forme de surfaces complexes et développables. Cette cellule a été développée plus avant dans OPTICOMS et le projet de test I-beam.
Étape 1
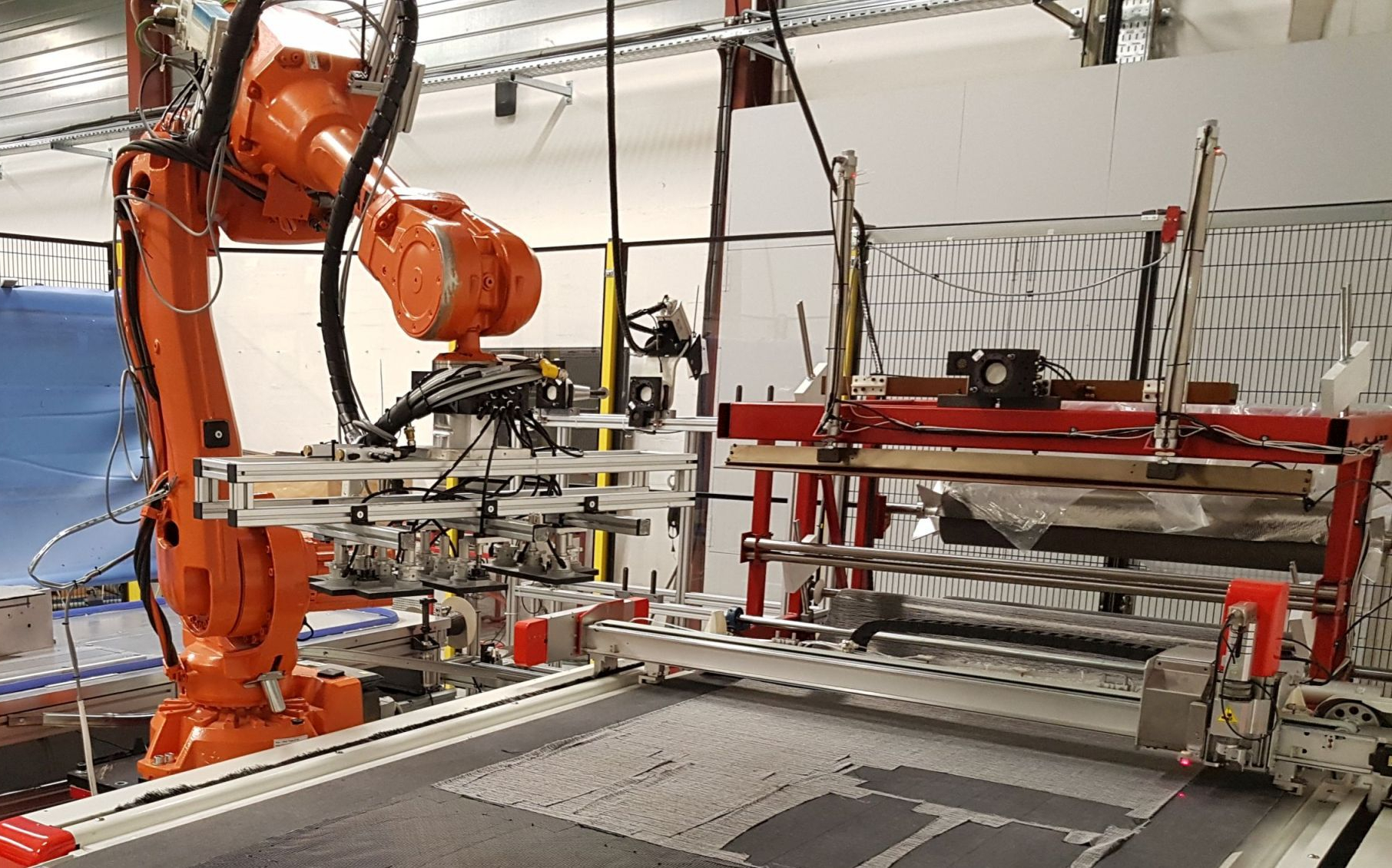
Source, toutes les images d'étape | Techni-Modul Ingénierie
Au sein de la cellule automatisée Techni-Modul Engineering, un robot pick-and-place retire les plis d'un cutter automatisé et les applique à un outil de préformage chauffé.
Étape 2

Les outils de préformage reposent sur une table de compactage avec une membrane sous vide réutilisable à charnière (bleue, à gauche) utilisée pour terminer un dégrossissage chauffé tous les 5 à 8 plis pendant le drapage.
Étape 3
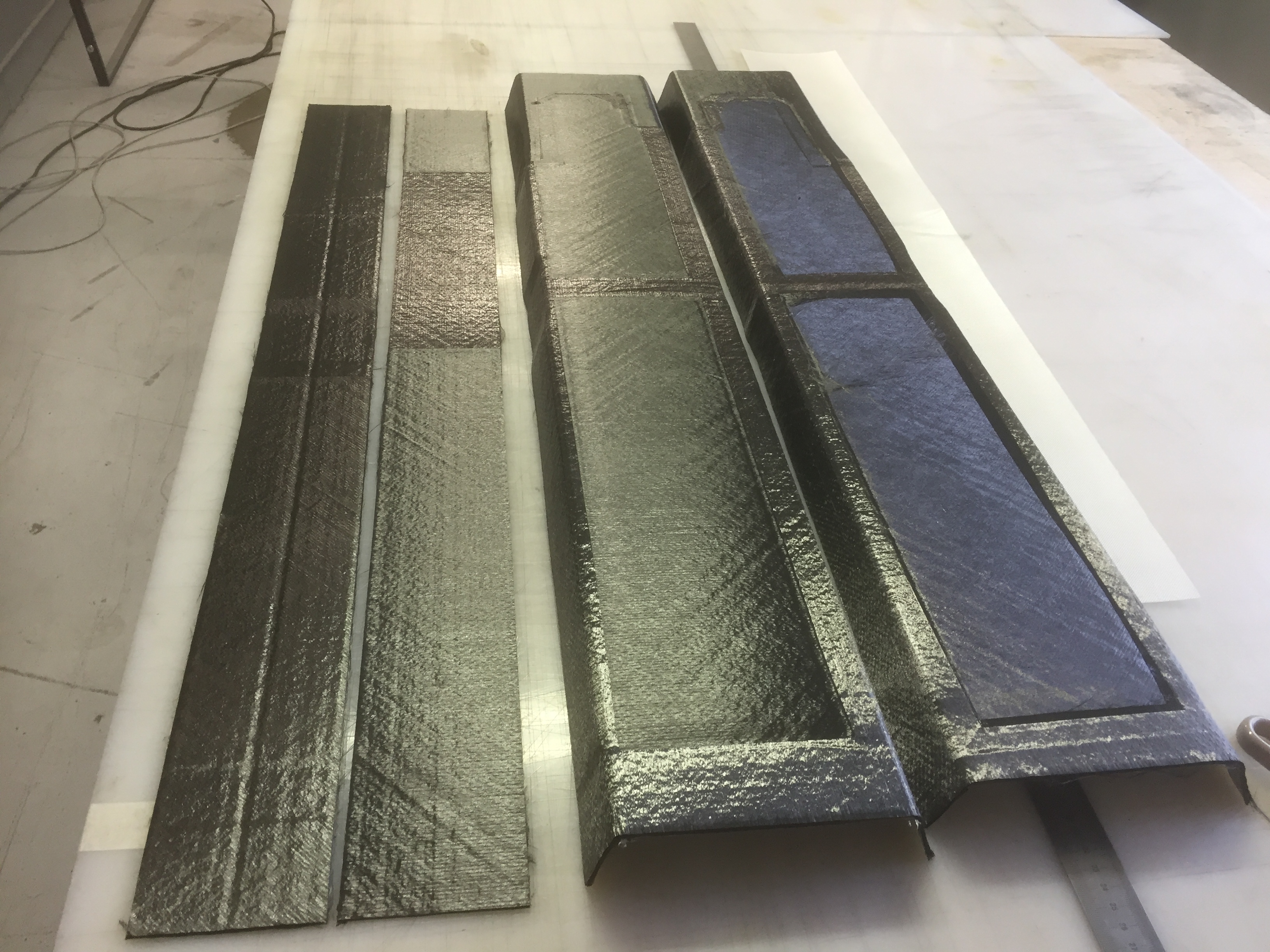
Chaque cycle de préformage de longerons produit une préforme de poutre en C (deux comprennent l'âme de la poutre en I) et une préforme de semelle plate. Deux ensembles requis pour chaque longeron de poutre en I sont affichés ici.
Étape 4
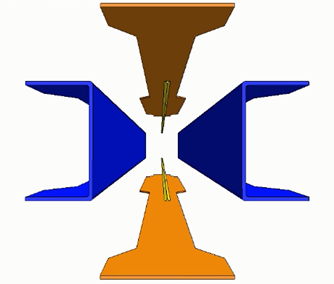
Les quatre préformes de longerons en I sont placées dans le moule RTM, le vide est appliqué et l'injection de résine est terminée en 5 minutes.
Étape 5
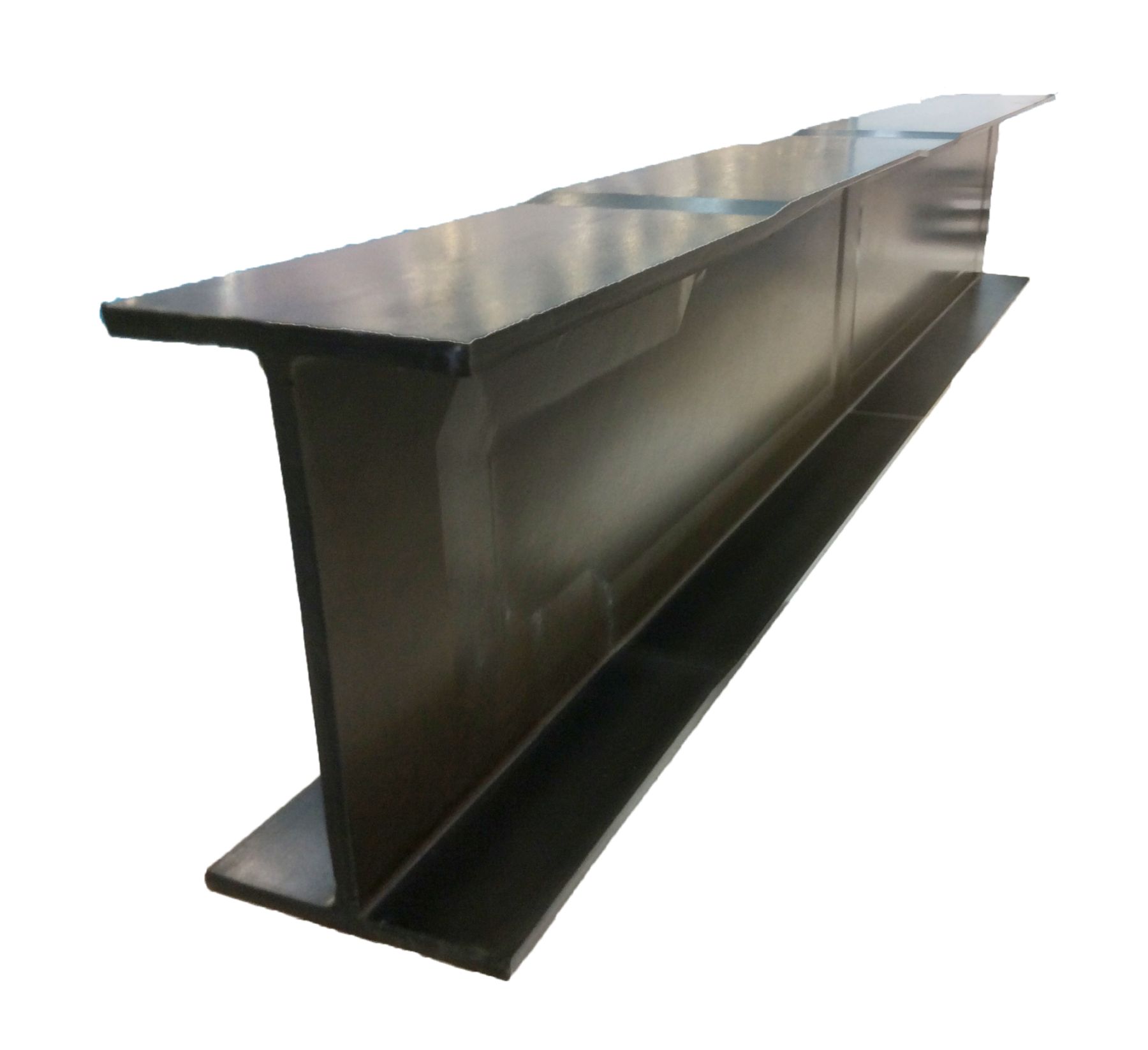
Après un durcissement de 90 minutes, le limon est démoulé et le flash de résine est coupé pour un cycle partiel complet de 4,5 heures.

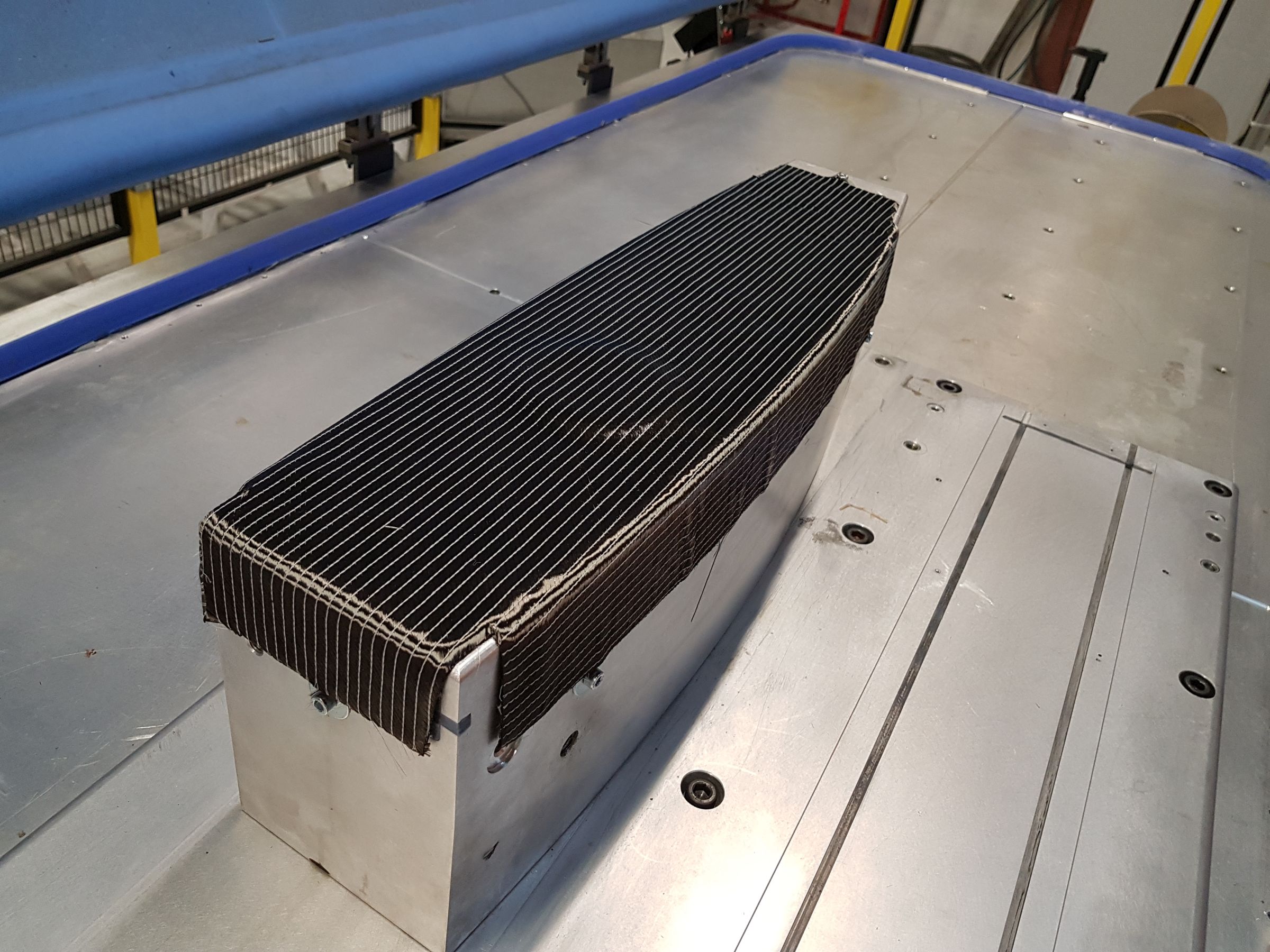
Un robot place des plis coupés sur l'outil de préforme chauffé. Tous les 5 à 8 plis, un dégrossissage chauffé est effectué pour compacter la préforme.

Avant le dégrossissage, un film antiadhésif bleu est appliqué.
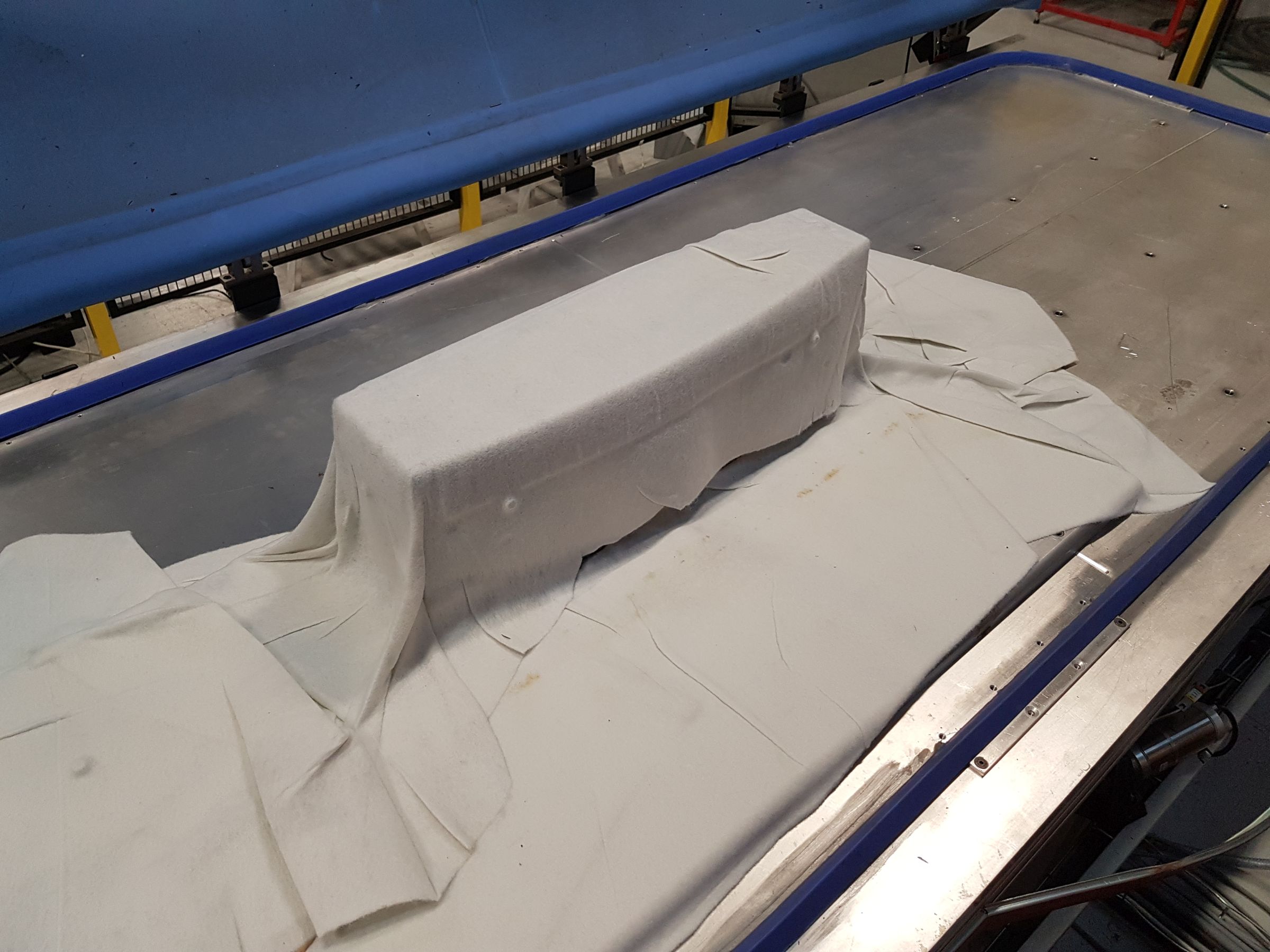
Le reniflard est utilisé pour extraire l'air à travers la préforme.
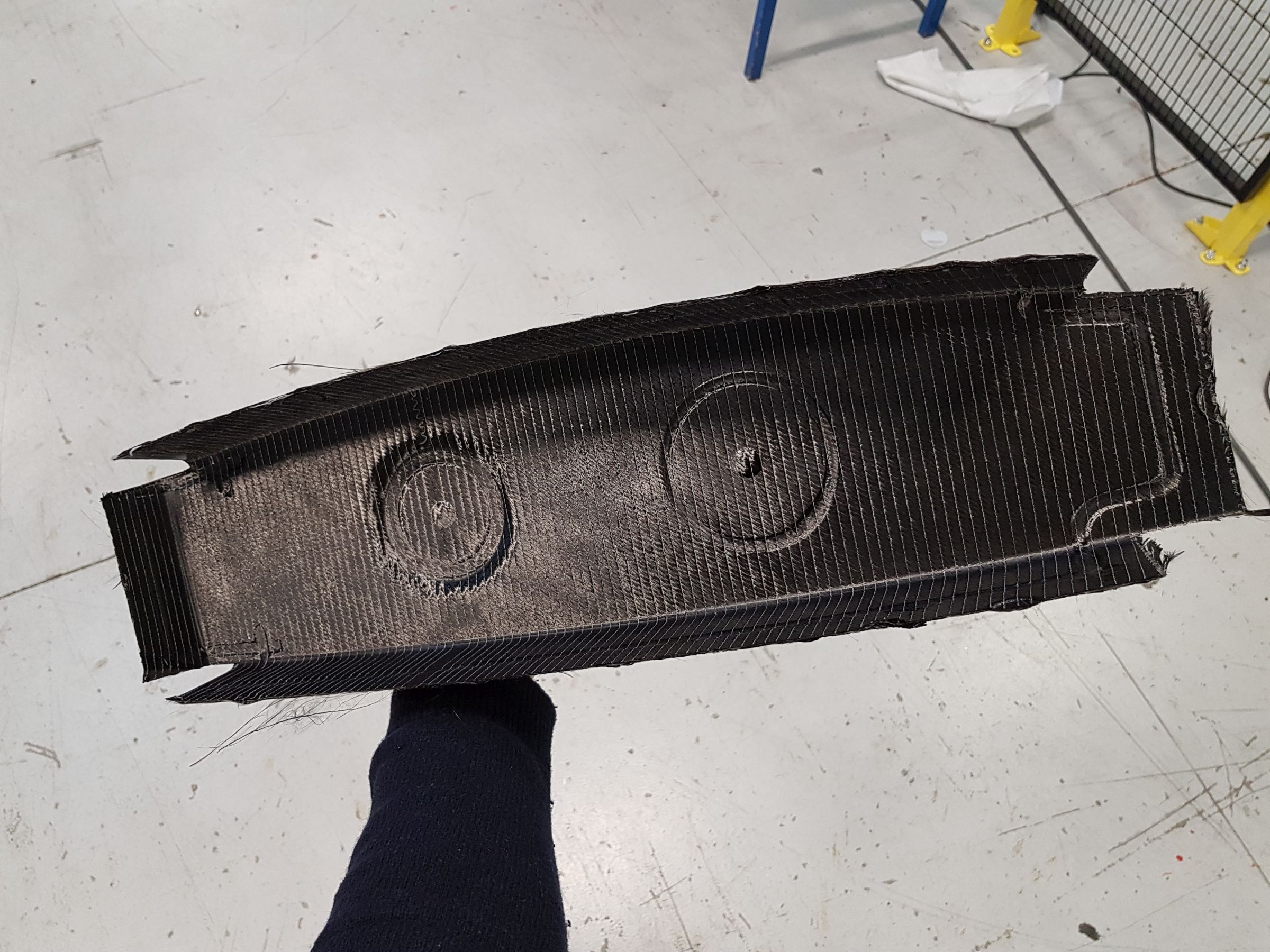
Après le dégrossissage final, la préforme est refroidie sur l'outil et les découpes sont découpées (ci-dessous).
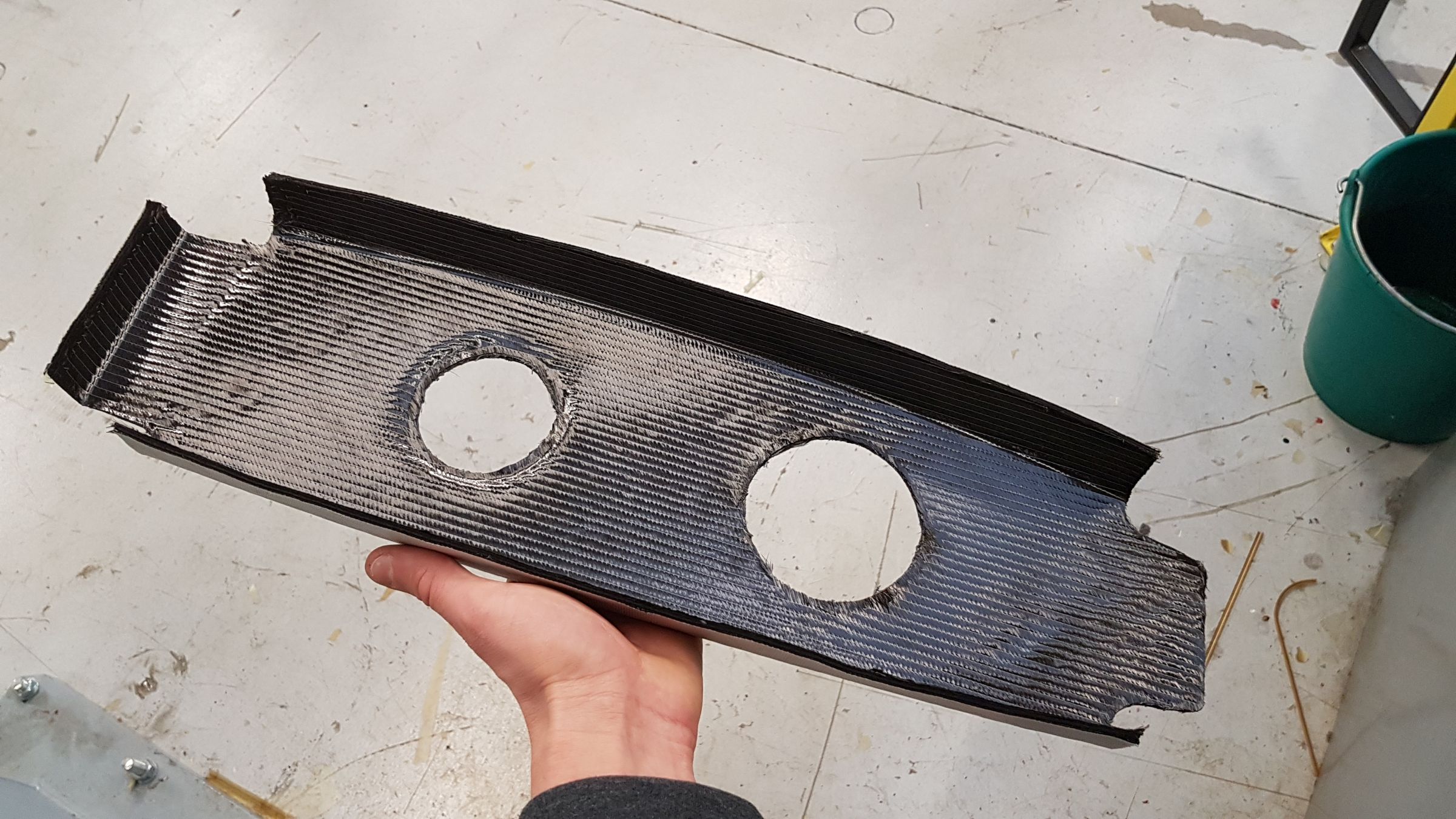
« Nous avons automatisé l'empilage manuel classique des plis à l'aide d'un pick and place robotisé », précise Chevallet. "Le robot récupère les plis d'un coupeur automatisé et les transfère vers l'outil de préforme chauffé qui se trouve sur une table de compactage [étapes 1 et 6]." Une couche pelable (film bleu à l'étape 6), un reniflard (matériau blanc à l'étape 6) et une membrane sous vide réutilisable à charnière (bleu clair à gauche aux étapes 2 et 6) sont appliqués, suivis d'un aspirateur et de la chaleur pour préformer et éliminer l'air du empilement textile (formage drapé à chaud, HDF) tout en fondant les voiles thermoplastiques minces pour créer une préforme compactée.
« Le nombre de plis que vous pouvez compacter à la fois dépend des matériaux et de la forme de la pièce », explique Chevallet. « Pour les pièces à faible courbure, comme une peau d'aile, vous pouvez éventuellement compacter tous les 50 plis. La nervure OPTICOMS, cependant, a des angles de 90 degrés, et le longeron de la poutre en I de test a des formes en T, vous devez donc faire attention à ne pas former de plis dans les plis pendant le préformage. Il ajoute que des formes aussi complexes peuvent nécessiter un compactage tous les 5 à 8 plis, mais peuvent tout de même faire partie d'un processus industrialisé à grand volume :plis empilés, HDF 2 minutes compactage, rouvrir et empiler à nouveau, suivi de cycles de compactage répétés avec un refroidissement final de la préforme sur l'outil avant transfert dans le moule RTM.
« Notre cellule automatisée peut placer à une cadence de 15 secondes par pli », note Chevallet. « Le drapage de la nervure OPTICOMS, avec moins de 20 plis au total, a été réalisé en 20 minutes. » La pose de la poutre en I a été plus longue :45 minutes en raison de sa forme complexe et de son empilement de stratifiés, y compris des variations d'épaisseur de 1,2 à 6 millimètres. "C'est encore beaucoup plus rapide que les processus manuels et réduit le risque d'erreur, augmente la répétabilité et la qualité tout en réduisant les coûts", ajoute-t-il.
Étape 7
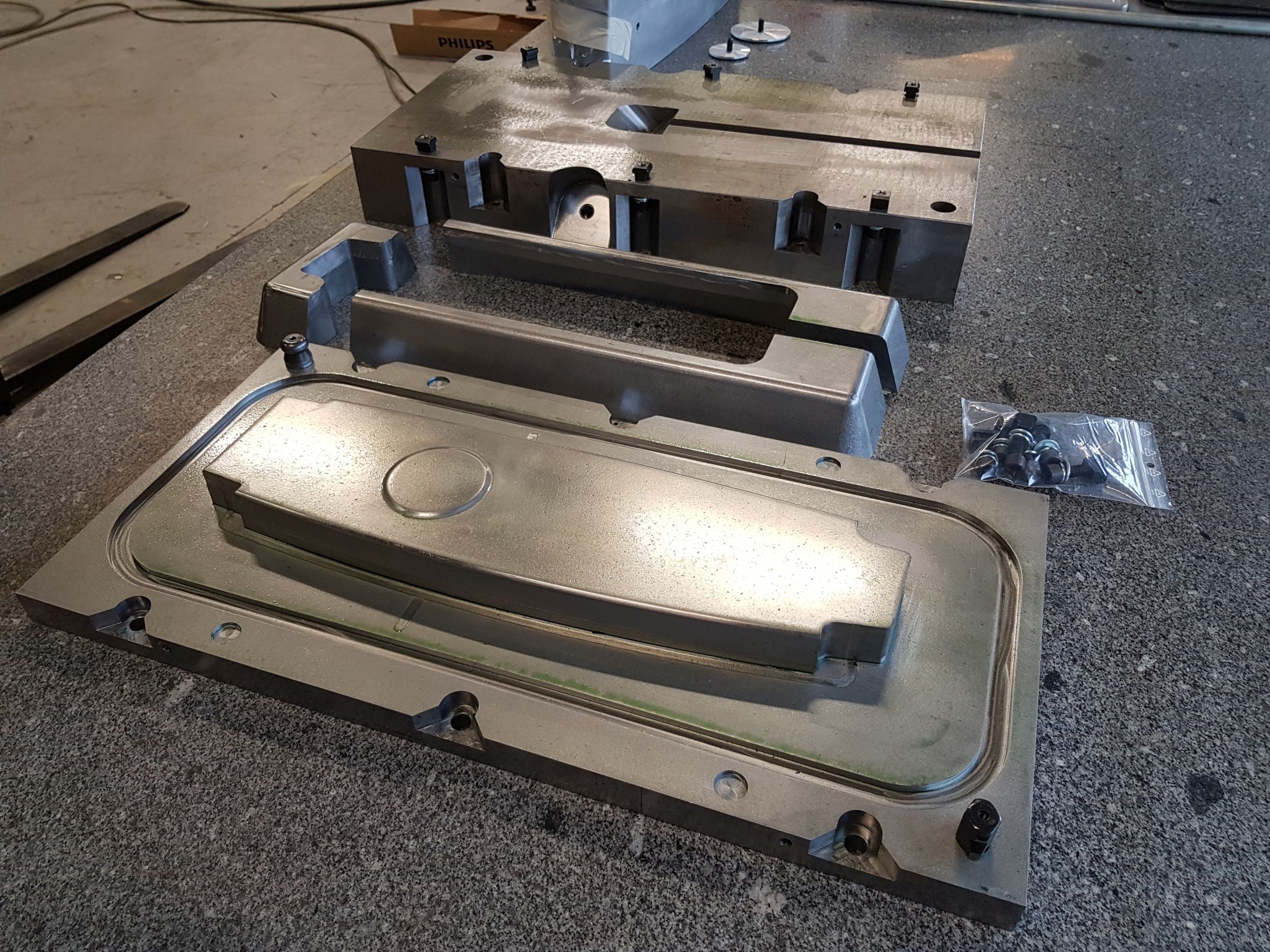
L'outil RTM pour la nervure OPTICOMS comprend plusieurs pièces.
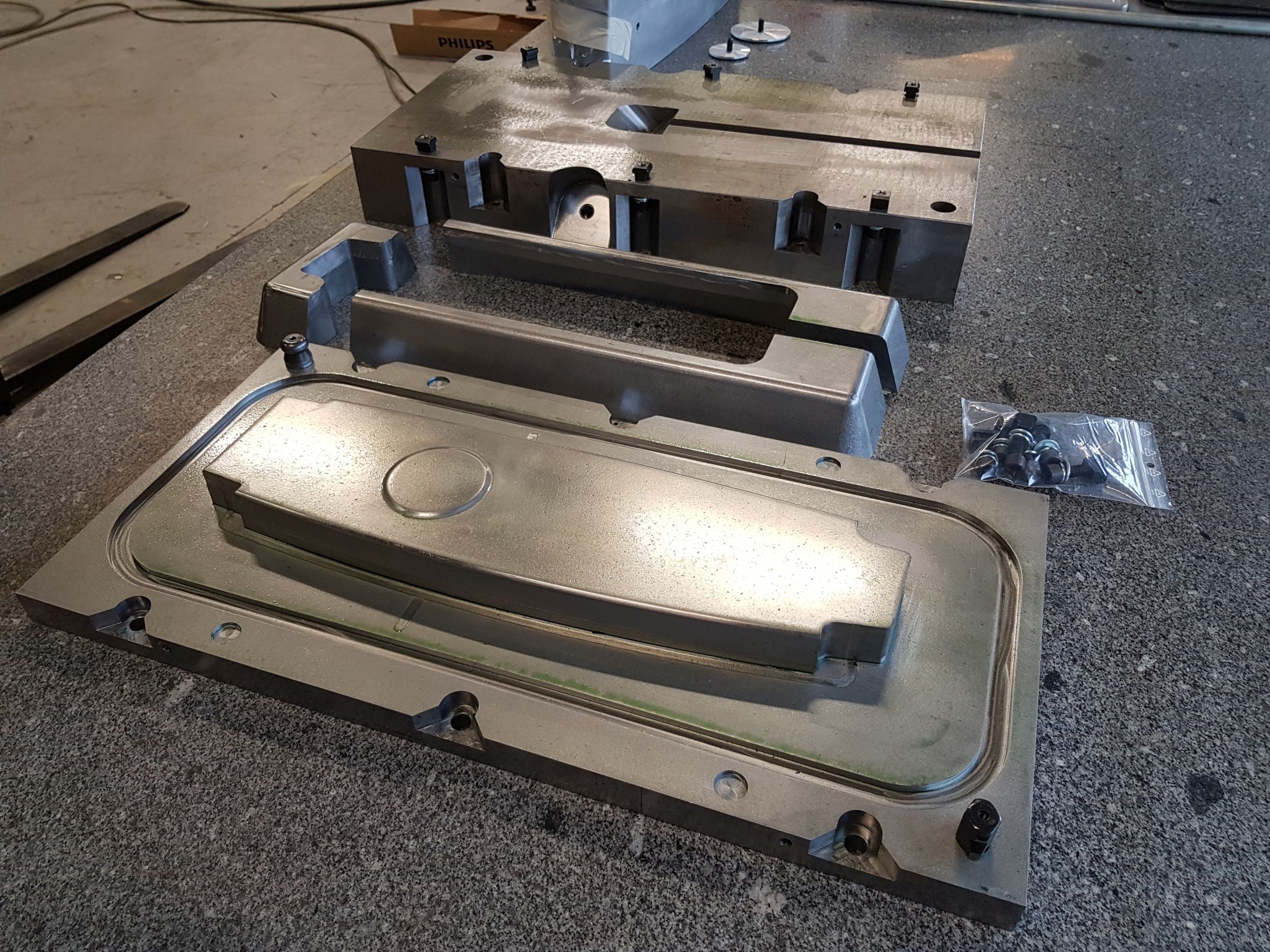
Étape 8
La préforme de nervure est placée dans l'outil RTM.
Étape 9
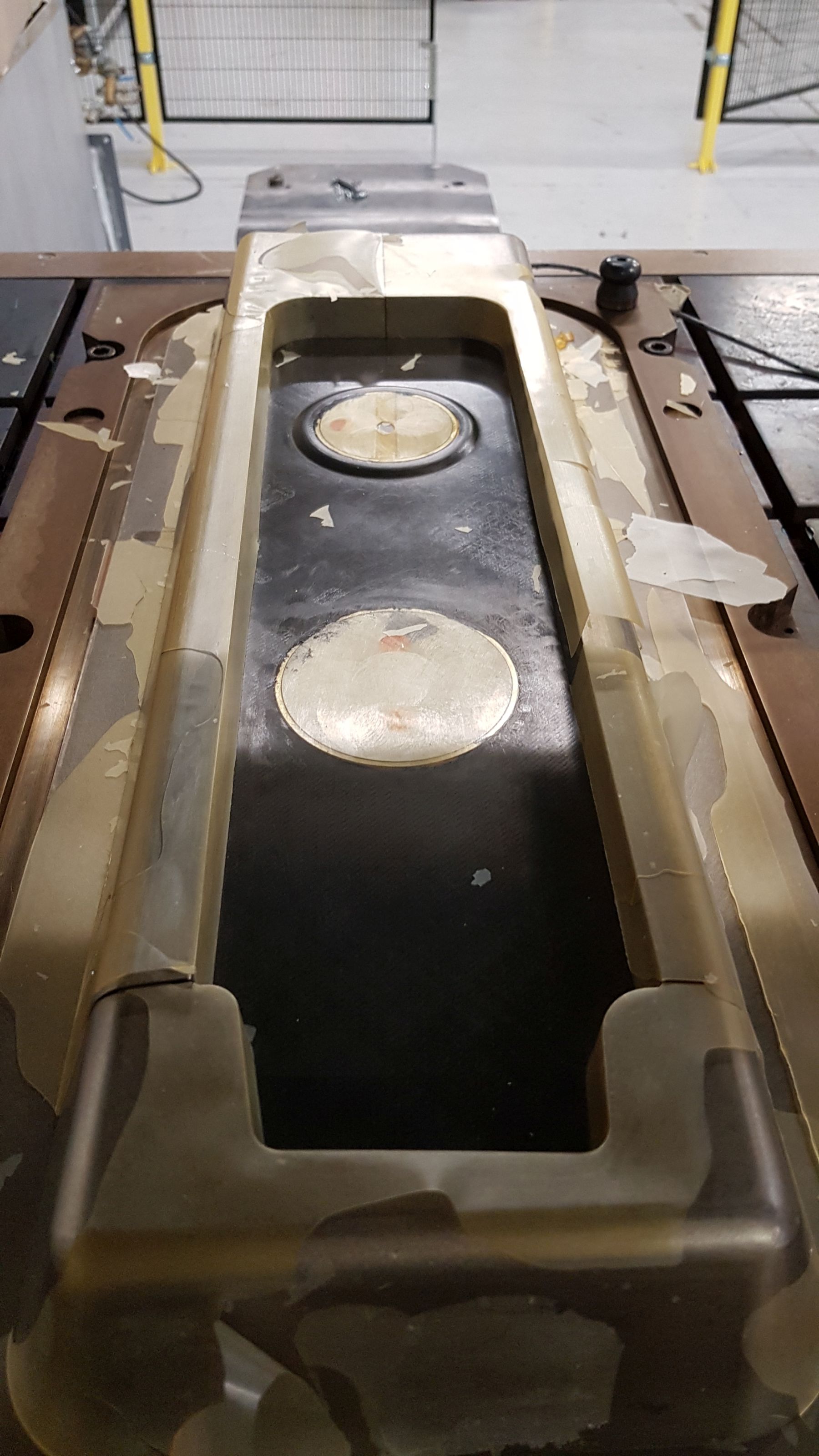
Le vide est appliqué, la résine est injectée et s'infiltre dans la préforme, suivie d'un durcissement de 90 minutes. Ici, la presse a été ouverte pour révéler la partie durcie.
Étape 10
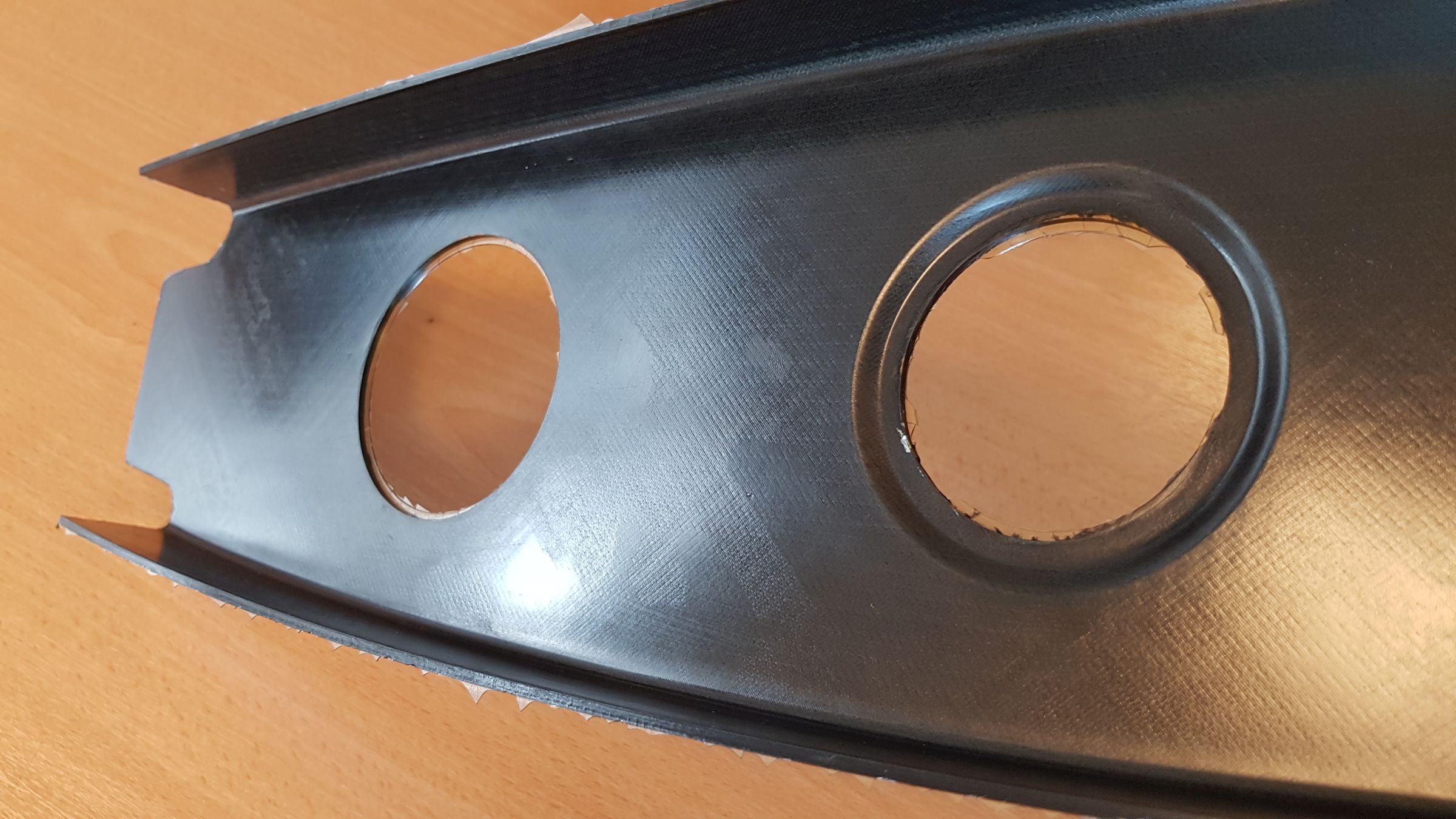
Une fois le démoulage terminé, le flash de résine sera retiré pour un cycle partiel complet de 4 heures.
Contrôle intelligent
Une autre caractéristique clé de la cellule de préformage automatisée de Techni-Modul Engineering est son système de contrôle intégré. Appelé SMART CONTROL, son épine dorsale est un système de caméra et un logiciel multi-usage qui compare les images prises pendant le traitement à la base de données CAO de la pièce, permettant la reconnaissance de la forme de la préforme, le contrôle de l'orientation des fibres, le positionnement des plis et la détection des défauts et des débris d'objets étrangers (FOD ). Le retour SMART CONTROL indique au robot comment ramasser et placer les plis dans le bon ordre et au bon moment, mais alerte également l'opérateur de la cellule lorsqu'il détecte des erreurs. « Le système peut être configuré pour que l'opérateur retire ensuite manuellement le pli et redémarre le système pour le remplacer », explique Chevallet, « ou nous pouvons travailler avec le client pour créer une solution automatisée pour éliminer les plis défectueux et corriger les erreurs. » /P>
Les mêmes images optiques utilisées pour détecter les bords et les contours des plis sont également utilisées pour contrôler l'orientation des fibres. Chevallet concède que si la pièce est très grande (par exemple, 2 mètres de long contre 200 sur 200 millimètres), « vous aurez peut-être besoin d'un appareil photo prenant des photos [d'une] position verticale plus élevée pour détecter les bords des plis, puis vous rapprocher de la partie pour vérifier l'orientation des fibres. Vous calibrez cette séquence pour chaque type de pièce. Pour détecter les rides et les FOD, il existe une base de données de différents défauts que vous pouvez ajouter à celle-ci, de sorte que l'algorithme d'apprentissage en profondeur s'améliore avec le temps. L'idée est d'avoir un système adaptatif. »
Durée du cycle et production future
Les préformes pour la nervure OPTICOMS ont été réalisées en HiMax, et le longeron en I a utilisé HiTape. Le système de résine pour les deux était l'époxy liquide HexFlow RTM6 à un composant (1K) d'Hexcel, qui a un cycle de durcissement de 90 à 120 minutes à 180°C. Ce durcissement est l'étape la plus longue dans les temps de cycle de la pièce pour la nervure OPTICOMS et le longeron de poutre en I d'essai, comme on peut le voir dans le tableau 1.
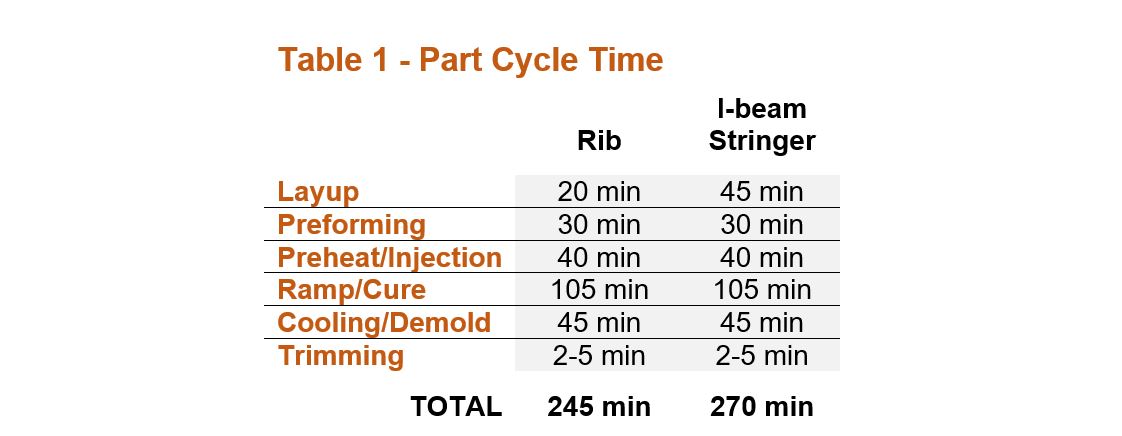
Origine | Techni-Modul Ingénierie
À ce jour, il s'agit du seul époxy qualifié pour le RTM des structures aérospatiales. Cependant, l'intérêt augmente pour qualifier les systèmes à deux composants qui sont mélangés à la tête d'injection, offrant une flexibilité accrue du cycle de durcissement et évitant le besoin d'expédition et de stockage réfrigérés nécessaires pour empêcher une réaction prématurée du RTM6 prémélangé.
Airbus Helicopters (Donauworth, Allemagne) a collaboré avec Alpex Technologies (Mils, Autriche) dans le cadre du projet SPARTA pour démontrer un procédé HP-RTM utilisant une version à deux composants de HexFlow RTM6 pour obtenir des polymérisations de 30 minutes à 180 °C pour une porte A350 cadre, qui est une structure primaire de forme complexe mesurant 2 mètres de haut, 200 à 250 millimètres de large et 8 à 10 millimètres d'épaisseur (voir « HP-RTM pour la production en série d'aérostructures CFRP rentables »). Airbus a également fait la démonstration d'une nervure CFRP de 1,5 mètre sur 0,5 mètre fabriquée à l'aide de HP-RTM par sa filiale Composite Technology Center (CTC, Stade, Allemagne), réalisant des cycles de moulage de 20 minutes pour des pièces avec 60 % de volume de fibres et moins de 2 % de vides. Au cours de la dernière année, CTC a travaillé avec un certain nombre de fournisseurs de niveau pour faire la transition des pièces préimprégnées à la main vers HP-RTM pour l'A320. Cependant, les systèmes de résine 2K doivent être qualifiés pour la production d'aérostructures, et CTC est préoccupé par la capacité d'assurer en permanence la qualité du mélange des systèmes de résine 2K in situ. Alpex utilise des capteurs dans le moule de Netzsch (Selb, Allemagne) et Kistler (Winterthur, Suisse) pour y parvenir, et d'autres solutions sont en cours de développement (voir « Époxy en 2 parties pour une production accrue d'aérostructures composites »).
Même sans systèmes 2K, des volumes de production plus élevés peuvent être possibles. Les cadres de porte du projet SPARTA ont été retirés après le durcissement initial de 30 minutes à 180 °C et post-durcis hors de la presse, sous vide pour éliminer les contraintes thermiques et garantir les propriétés mécaniques. Selon Bernhard Rittenschober, responsable R&D d'Alpex, cela nécessite des jeux d'outils supplémentaires, mais une seule presse et unité d'injection. Il explique que le coût supplémentaire de l'outil est compensé par un coût de processus et de presse inférieur et peut être récupéré rapidement, même avec un faible volume de 500 à 1 000 pièces/an.
« La principale réalisation de ces démonstrateurs est la capacité de fabriquer des aérostructures primaires avec une courte injection de résine par rapport aux processus RTM aérospatiaux conventionnels, où il a été difficile et long d'infiltrer de la résine dans de si grandes pièces avec des renforts en fibre de carbone UD », explique Pagnac . « Nous ne sommes qu'au début de ce que nous pouvons réaliser avec ce type de préformage automatisé intelligent et de traitement C-RTM », ajoute Chevallet. « Il a le potentiel d'atteindre la production plus rentable et durable de structures de peau intégrées aux raidisseurs envisagée pour les futurs avions. »
Résine
- matériaux d'impression 3D pour les voyages dans l'espace ?
- Henkel propose une plate-forme de matériaux pour la fabrication additive
- Matériaux :technologie de production en nid d'abeille léger au K 2019
- Matériaux :polyamide haute température ignifuge pour l'impression 3D
- Préparer un avenir autonome
- Trelleborg annonce un nouveau distributeur pour les matériaux d'outillage
- Arkema Inc. construit une usine de production de PEKK aux États-Unis
- 10 matériaux les plus solides pour l'impression 3D
- Matériaux pour composants Invar 36