Utiliser des suscepteurs mobiles pour innover dans le soudage par induction thermoplastique
Le Groupe Institut de Soudure (IS Groupe, Villepinte, France) — littéralement « l'institut du soudage » de France — a plus de 100 ans d'expérience dans le soudage des métaux et s'impose aujourd'hui comme un leader dans le soudage des composites thermoplastiques. Comme indiqué dans CW Dossier 2018 « Soudure des composites thermoplastiques », IS Groupe et sa marque de composites Composite Integrity a développé le procédé de « soudage par induction dynamique » utilisé pour joindre des longerons de ruban unidirectionnel (UD) en fibre de carbone (CF)/polyéthercétonecétone (PEKK) et des peaux de fuselage dans le projet de démonstration « Arches TP » avec le fournisseur de rang 1 d'Airbus STELIA Aerospace (Toulouse, France) , qui a été dévoilé au salon du Bourget 2017.
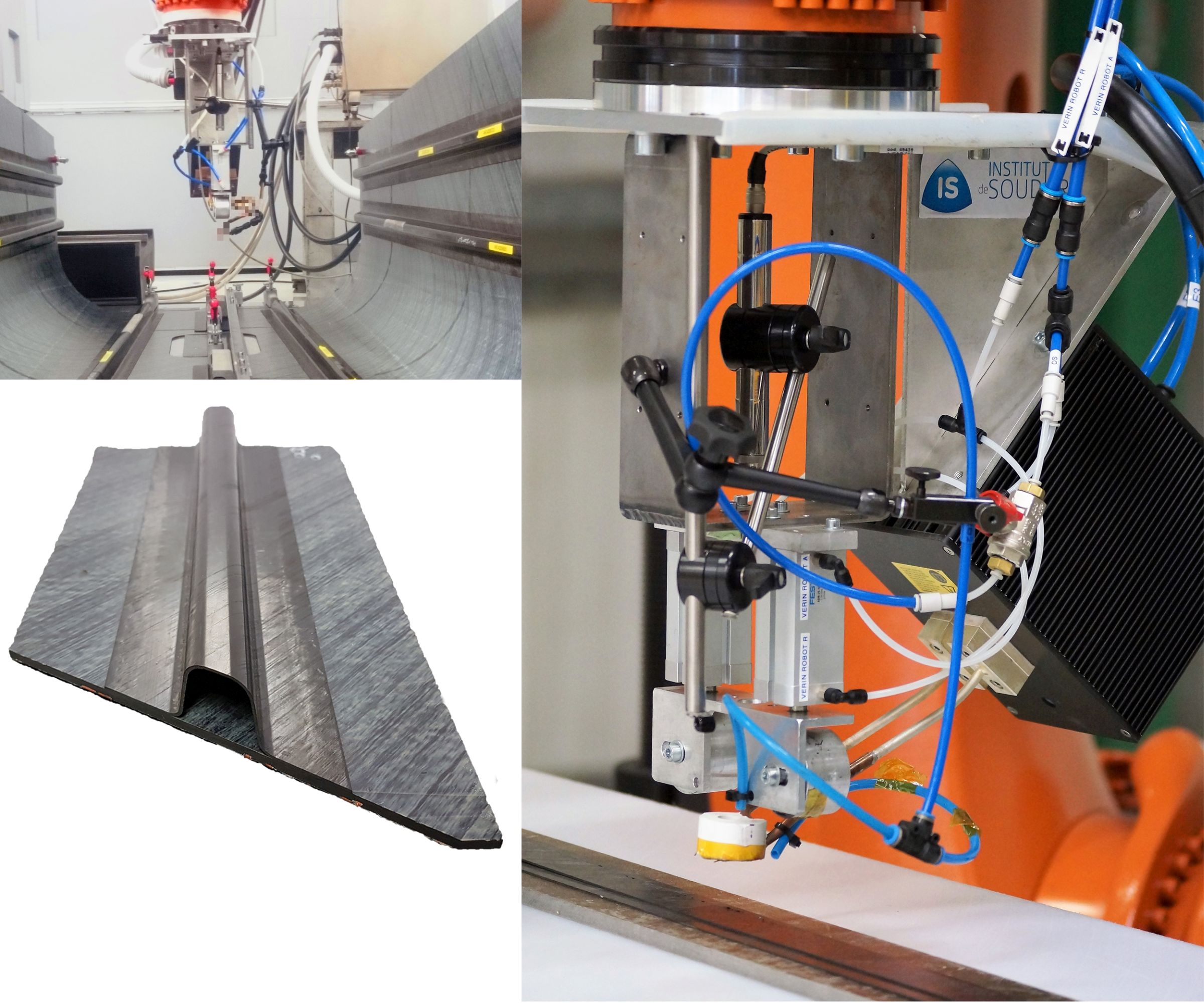
« C'est le début de notre développement avec le soudage par induction pour les pièces de structure aéronautique, explique Jérôme Raynal, directeur aéronautique &composites d'IS Groupe. « Bien que le procédé de soudage par induction dynamique que nous avons développé ait été un succès, il présentait certaines limitations concernant les performances dans le rayon du longeron collé et l'échauffement global du panneau car il n'y a pas de suscepteur à l'interface. »
Un suscepteur est un matériau placé entre les deux adhérents d'un joint composite thermoplastique soudé qui est chauffé par la bobine d'induction dans la tête de soudage. Le suscepteur peut être électriquement conducteur pour un chauffage résistif ou magnétique pour un chauffage par hystérésis, faisant fondre la matrice à l'interface de soudure qui est simultanément pressée pour créer un joint lié par fusion avec une résistance très élevée. Comme expliqué dans l'article de janvier 2000, « Design of a Resistive Susceptor for Uniform Heating during Induction Bonding of Composites » de Bruce Fink, Shridhar Yarlagadda et John W. (Jack) Gillespie, les suscepteurs utilisés dans les composites thermoplastiques soudés par induction étaient initialement un métal écran ou grillage, parfois imprégné de polymère.
IS Groupe pensait que les problèmes initiaux rencontrés pouvaient être résolus avec plus de développement. « Nous avons entamé un nouveau cycle de réflexion interne », déclare Raynal. Cela comprenait des discussions avec le fournisseur de matériaux thermoplastiques (TP) Arkema (Colombes, France) qui a conclu un partenariat de développement. « Nous avons maintenant développé et co-breveté une nouvelle technologie avec Arkema appelée Innovative Solution for Welding (ISW) », ajoute Raynal.
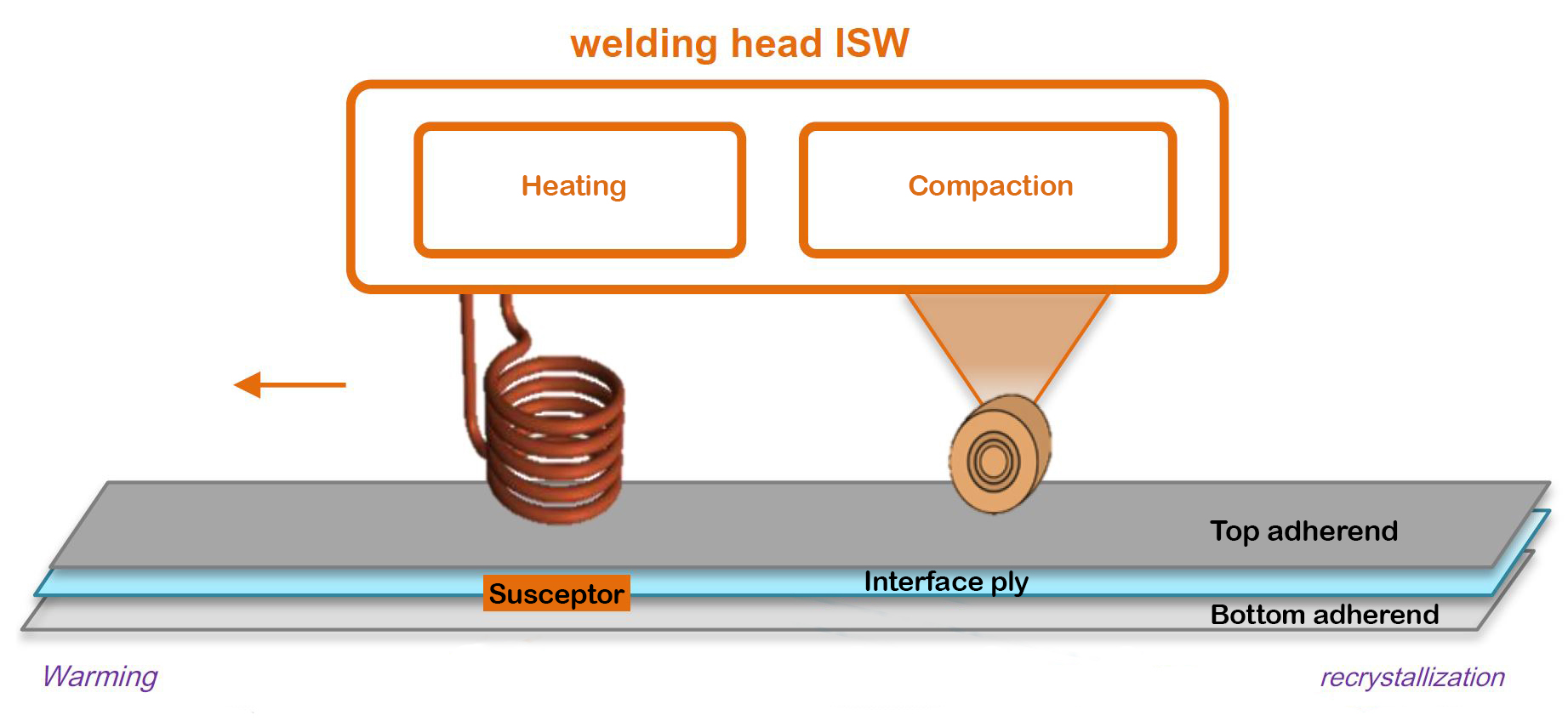
Bases ISW
« La base de l'ISW est d'utiliser un suscepteur pour chauffer l'interface de soudage, mais il s'agit d'un suscepteur mobile lié à la tête de soudage », explique Raynal. « Le suscepteur nous permet de localiser parfaitement la zone de chauffe au niveau de la soudure, mais la tête de soudage avec suscepteur se déplace pour qu'il ne reste rien dans l'interface pour perturber les propriétés de la structure soudée. Dans les premières itérations du soudage par induction, des suscepteurs à mailles métalliques étaient laissés dans la soudure, mais cela était considéré comme indésirable. Des techniques plus récentes ont été capables d'éliminer les suscepteurs parce que la fibre de carbone dans les stratifiés aérospatiaux courants est électriquement conductrice. Cela a également permis l'utilisation de matériaux en fibre de carbone comme suscepteurs.
Une autre partie de la solution ISW consiste à utiliser une matrice TP pure ou une couche à faible volume de fibres à l'interface de soudure pour augmenter le flux de résine. La température de fusion et la viscosité de cette couche d'interface peuvent être ajustées et peuvent également être fonctionnalisées pour fournir une conductivité électrique ou une isolation pour empêcher la corrosion galvanique, par exemple entre la fibre de carbone et l'aluminium ou l'acier.
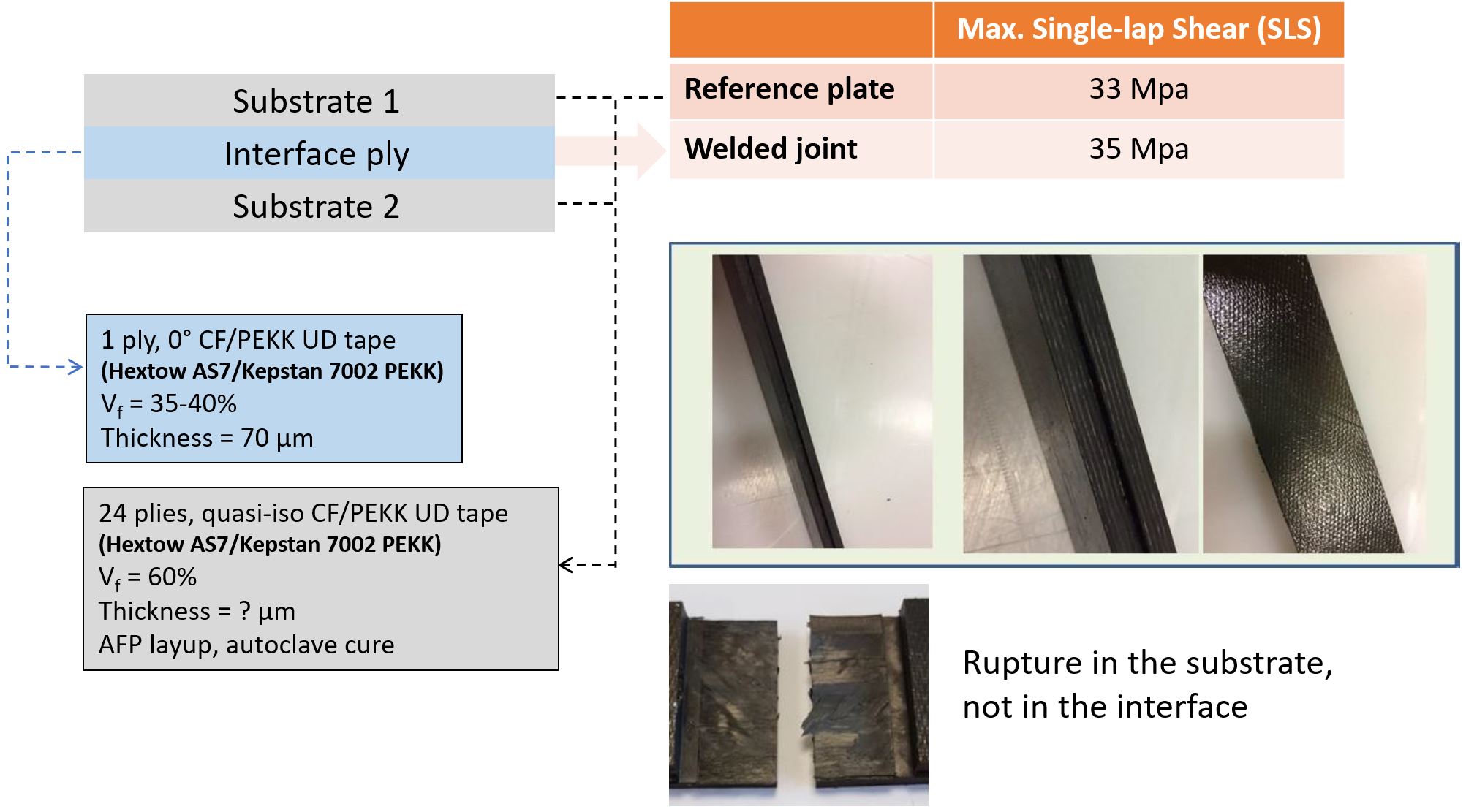
Résultats ISW
« Nous nous retrouvons avec un coefficient conjoint de 80 à 90 %, précise Raynal. Le coefficient de joint correspond à la résistance de la soudure et est utilisé avec le métal, les plastiques et les composites. « Lors d'essais de cisaillement à un seul tour de deux plaques préconsolidées soudées ensemble à l'aide d'ISW, nous avons atteint 80 à 90 % des propriétés des plaques de référence non soudées et consolidées en autoclave. Ces essais ont utilisé du ruban UD fabriqué avec de la fibre de carbone Hextow AS7 (Hexcel, Stamford, Connecticut, États-Unis) et Arkema Kepstan 7002 PEKK.
Raynal dit que l'ISW peut être utilisé pour souder tout type de matrice :PE, PA, PEKK, PEEK, ainsi que des composites thermoplastiques renforcés de fibres de carbone, de verre ou d'aramide. « Nous avons également montré qu'il n'y avait aucun problème à souder des composants dotés d'un treillis en cuivre pour la protection contre la foudre (LSP), ce qui est essentiel pour la production d'aérostructures », ajoute-t-il. ISW est conçu pour être entièrement automatisé avec la tête de soudage attachée à un bras robotique à 6 axes.
Contrôle de la température
Comme expliqué dans l'article de Kirk/Yarlagadda/Gillespie ci-dessus, un problème courant avec les suscepteurs à mailles métalliques soumis à un champ magnétique est la distribution de température non uniforme résultante dans la pièce à souder. « Nous contrôlons cela en utilisant un suscepteur pour faire fondre uniquement l'interface de soudure », explique Raynal. « Nous captons la température avec un pyromètre laser qui mesure en fait le bord du suscepteur sur le côté. Ainsi, nous connaissons exactement la température à l'interface. Nous utilisons également le refroidissement pour aider à gérer la température et assurer une cristallisation suffisante du matériau thermoplastique tout au long de la soudure. »
Essais de soudure lisse-peau STELIA
Le fournisseur de rang 1 d'Airbus, STELIA (Toulouse, France), est l'un des premiers clients de ce développement du soudage par induction. IS Groupe et Arkema ont réalisé pour STELIA une étude spécifique pour souder un longeron 7 plis CF/PEKK sur une peau 14 plis avec treillis cuivre pour la protection contre la foudre (LSP). L'objectif final est de souder des structures de 30 mètres de long, avec des sections droites et à double courbe. Les composants ont été fabriqués à l'aide d'un ruban UD de 194 g/m² comprenant de la fibre de carbone Tenax HST45 (Teijin, Osaka, Japon) et du Kepstan 7002 PEKK. STELIA a spécifié une soudure homogène avec des performances mécaniques> 85 % du matériau de référence consolidé en autoclave et sans dégradation des propriétés thermiques ou mécaniques des supports. Il a également demandé un processus robuste en ce qui concerne le changement d'épaisseur de l'adhésif. Des tests chimiques et de propriétés sur les composants soudés ont été effectués par IS Groupe.
IS Groupe et Arkema ont pu répondre aux exigences de STELIA en atteignant> 85 % des performances de cisaillement simple (SLS) et de résistance au cisaillement interlaminaire (ILSS) par rapport aux stratifiés de référence consolidés en autoclave. Il n'y a pas eu de déballage ni de dégradation des stratifiés des composants ou du maillage LSP. Le seul domaine où ils ont échoué est la vitesse. STELIA a demandé une vitesse de soudage ≥ 1 mètre/minute. "Actuellement, nous sommes à 0,3 mètre (10 pouces) par minute", concède Raynal, "mais nous continuons à travailler vers cette vitesse cible." Y a-t-il une limite d'épaisseur de substrat qui peut être soudée ? « Nous pouvons souder des épaisseurs typiques des structures aérospatiales et avons soudé des composants de 5 millimètres d'épaisseur à un substrat de 5 millimètres. »
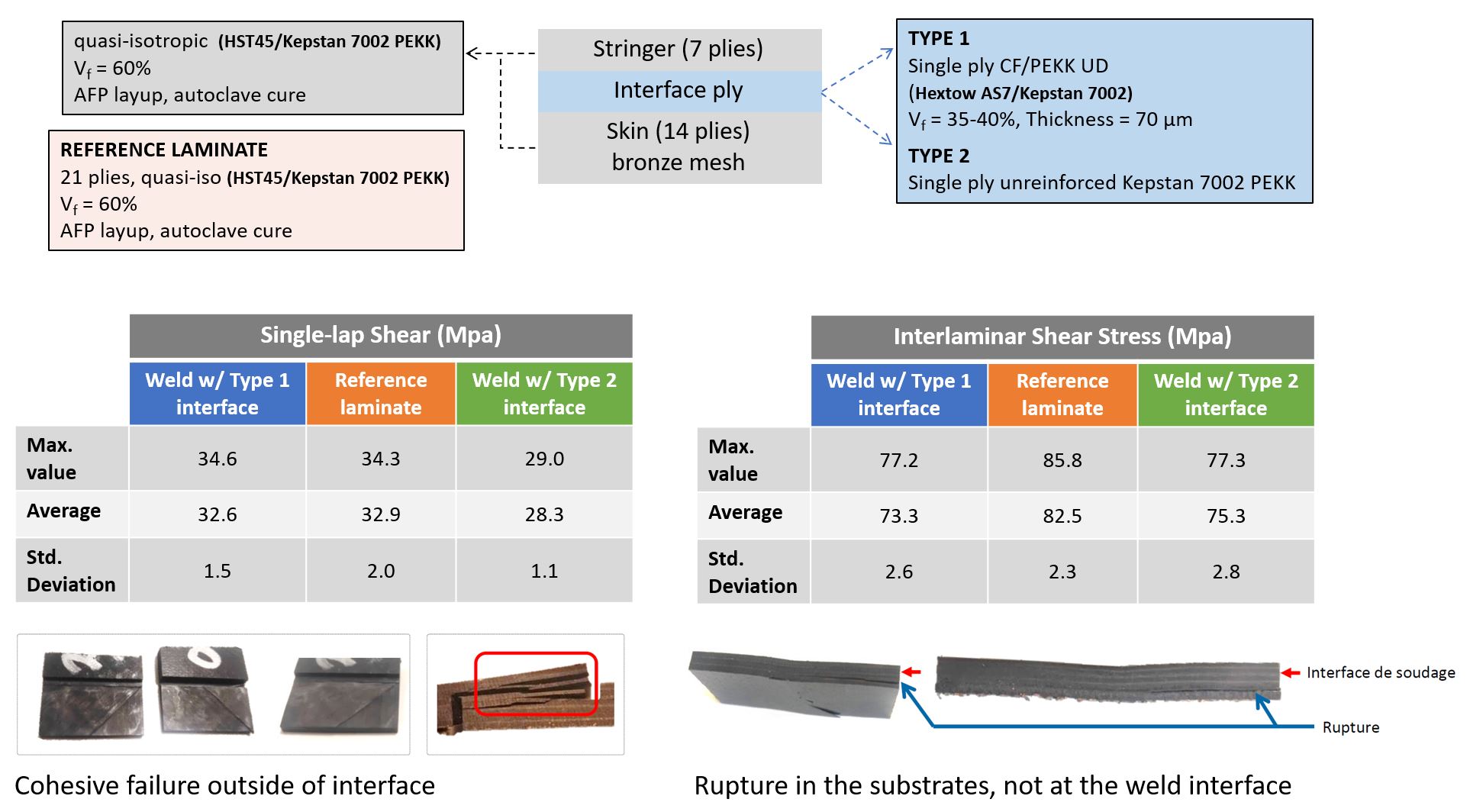
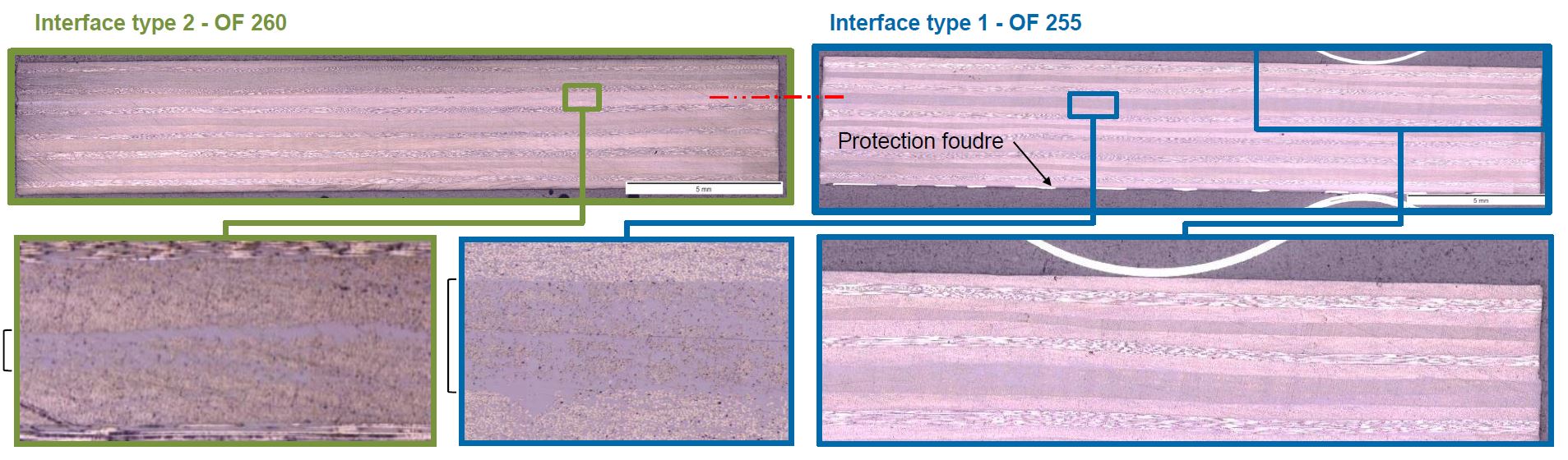
Partenariat Arkema, opportunités et défis
Pourquoi travailler avec Arkema ? « Parce qu'il y a une relation entre la technologie et les matériaux, explique Raynal. « Par exemple, les matériaux à l'interface et leur fraction volumique font la différence. Nous sommes des spécialistes du process, mais nous avions besoin de travailler en étroite collaboration avec un partenaire pour les matériaux. Ce développement conjoint était nécessaire pour optimiser complètement la technologie de soudage. »
IS Groupe et Arkema sont copropriétaires de la technologie ISW et ont protégé cette technologie par un solide portefeuille de brevets qui comprend déjà cinq demandes de brevets français et internationaux. ISW peut être utilisé avec n'importe quelle matrice composite thermoplastique, et IS Groupe démontre la technologie à travers des programmes qu'il a avec des entreprises en Europe et aux États-Unis, y compris Latécoère (Toulouse, France) et Collins Aerospace Aerostructures (Chula Vista, Californie, États-Unis).
Pour Arkema, l'accent est mis sur le PEKK, a déclaré Raynal, notant son alliance stratégique avec Hexcel en 2018 pour développer des rubans CF/thermoplastiques pour les futurs avions, en mettant l'accent sur la réduction des coûts et des vitesses de production plus rapides pour ses clients. Dans le cadre de ce partenariat, un laboratoire commun de R&D est en cours de création en France.
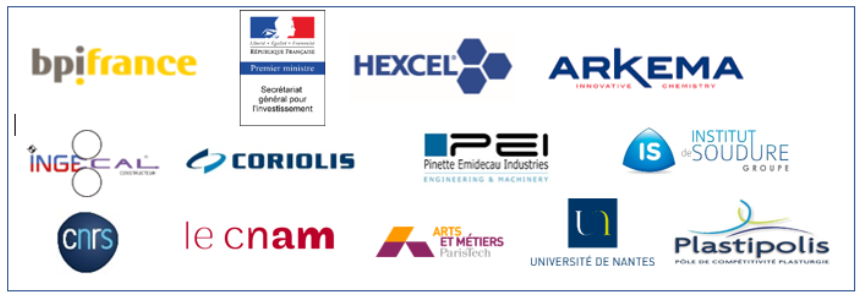
Les composites intégrés hautement automatisés pour la réalisation de structures adaptables à 13,5 millions d'euros et 48 mois (HAICoPAS) s'inscrit dans la continuité de l'alliance stratégique Arkema-Hexcel. Cette collaboration entièrement française comprend IS Groupe, ainsi que le concepteur de machines sur mesure Ingecal (Chassieu), Coriolis Composites (Quéven), Pinette Emidecau Industries (Chalon Sur Saône) et un consortium de laboratoires universitaires. HAICoPAS optimisera la conception et la fabrication de matériaux pour la production de pièces composites afin d'atteindre un coût compétitif à grande vitesse. Il vise également à développer une technologie plus productive pour le placement/la superposition de matériaux composites et un nouveau système d'assemblage de pièces finales par soudage avec contrôle qualité en ligne.
Les applications ciblées comprennent les structures primaires d'avions, les pièces structurelles pour l'industrie automobile et les pipelines pour l'industrie pétrolière et gazière. Les avantages de recyclabilité et de durabilité fournis par les matériaux thermoplastiques sont également importants pour ces marchés et seront démontrés et quantifiés dans HAICoPAS.
« L'un des avantages que nous pouvons offrir avec ISW est une réduction de plus de 50 % de la puissance électrique requis par rapport à notre procédé de soudage dynamique par induction de 2017 », précise Raynal. « Avec l'induction conventionnelle, vous avez besoin d'une puissance élevée pour chauffer la surface. Mais avec un suscepteur à l'interface, la surface que vous chauffez est beaucoup plus petite, nécessitant beaucoup moins d'énergie. Il note que cela aide également à éviter le décompactage dans le rayon des longerons. « Si vous chauffez trop, vous pouvez ramollir le matériau dans le rayon et permettre aux fibres de bouger ici. Ainsi, il suffit de chauffer parfaitement uniquement la zone de contact pour les substrats soudés sans chauffer le rayon. Avec ISW, ce n'est pas un problème. »
Il y a quand même des problèmes thermiques. « Avec les formes plates, le contrôle thermique est simple, mais il devient plus difficile avec la complexité accrue des formes », explique Raynal. « Pour 2020, l'objectif principal est de poursuivre le développement et de réaliser le soudage des longerons sur peau à une échelle représentative. Notre objectif est également d'introduire la technologie dans de nouveaux programmes de développement d'avions. »
Pour plus de détails, voir Composite Integrity au JEC World 2020, Hall 5, Stand N89.
Résine
- Les 5 principaux avantages du soudage par induction
- C# en utilisant
- Covestro intensifie ses investissements dans les composites thermoplastiques
- Lancement des mélanges maîtres thermoplastiques renforcés de graphène
- Solvay augmente la capacité des composites thermoplastiques
- Composites thermoplastiques chez Oribi Composites :CW Trending, épisode 4
- Soudage de composites thermoplastiques
- Ce qui manque aux municipalités si elles n'utilisent pas les inspections mobiles
- Prévenir les problèmes et les défauts de soudage en utilisant des métaux vérifiés