Production automatisée d'aérocomposites :moulage liquide ou thermoplastique soudé ?
Alors que les équipementiers et les fournisseurs explorent les matériaux et les processus qui permettront la prochaine génération d'avions, deux approches différentes sont démontrées. Le premier est le moulage liquide de préformes en fibres sèches vu, par exemple, dans la ligne de moulage par transfert de résine (RTM) à haut débit de Spirit AeroSystem (Prestwick, Écosse) pour les spoilers d'Airbus A320 et également dans le programme Wing of Tomorrow (WOT) dirigé par Airbus. qui utilise le placement automatisé de tissus non sertis (NCF) et l'infusion de résine liquide, suivi d'un durcissement hors autoclave (OOA) dans un four (voir « La ligne RTM automatisée à haut débit pour l'aérospatiale fournit des spoilers de nouvelle génération » et « Mise à jour :l'aile inférieure skin, Wing of Tomorrow” respectivement.)
Le second est constitué de composites thermoplastiques (TPC) présentés, par exemple, dans le démonstrateur de fuselage multifonctionnel Clean Sky 2 (MFFD), où des peaux raidies sont créées à l'aide d'un placement automatisé de fibres - consolidées in situ pour la moitié supérieure et consolidées à l'autoclave pour la moitié inférieure. moitié — suivi d'un assemblage par soudage. Ces programmes utilisent l'automatisation pour augmenter le taux de production et la qualité tout en réduisant les coûts. Mais comment se comparent-ils ?
L'Institut des structures et de la conception du Centre aérospatial allemand (DLR) exploite le Centre de technologie de production légère (ZLP) à Augsbourg. Parmi ses nombreux projets de fabrication de composites, PROTEC NSR et Fast Lane RPB présentent une opportunité unique de comparer, respectivement, une cloison à pression arrière thermodurcissable (RPB) moulée liquide pour l'Airbus A350 bi-couloir avec un RPB thermoplastique pour l'Airbus monocouloir A320. Les deux projets ont travaillé avec le fournisseur de niveau 1 de ces structures, Premium Aerotec Group (PAG, Augsbourg, Allemagne), et ont démontré l'automatisation tout en évaluant la durée et le coût du cycle.
cloison TS moulée liquide
« Nous avons commencé il y a de nombreuses années avec PAG dans le projet AZIMUT pour analyser les processus manuels de fabrication de composites », explique le Dr Lars Larsen, responsable des technologies d'assemblage et d'assemblage chez ZLP Augsburg. « Notre première solution d'automatisation était destinée au layup, puis nous avons travaillé à automatiser davantage d'opérations. » L'objectif principal de PROTEC NSR était de prendre ces solutions spécialisées pour la production de RPB et de les intégrer dans un seul processus automatisé, explique le Dr Marcin Malecha, chef de projet pour PROTEC NSR chez DLR.
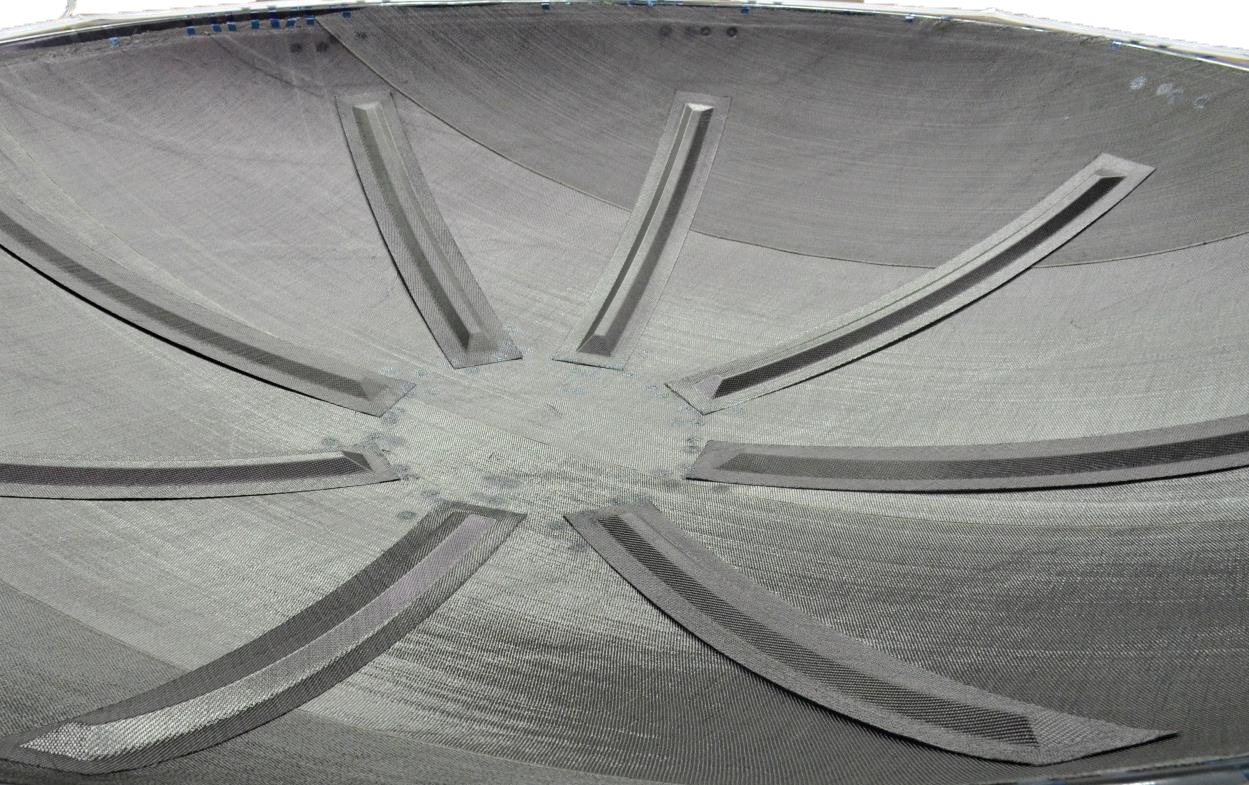
Préforme et pinces. Les étapes du processus de création de la préforme sèche ensachée sous vide sont illustrées à la figure 1 ci-dessous. Celui-ci a été infusé avec de la résine époxy RTM6 à l'aide du procédé breveté Airbus (VAP), qui utilise une membrane semi-perméable pour une porosité réduite. Le drapage de la préforme comprenait deux ensembles de 16 plis jusqu'à 5 mètres de long utilisant toute la largeur de 1,27 mètre du tissu en fibre de carbone satiné à 5 harnais. Entre ces deux ensembles, 25 pièces de renforcement de forme complexe mesuraient jusqu'à 1,5 mètres sur 2,5 mètres. Huit limons ont été placés sur le dessus.
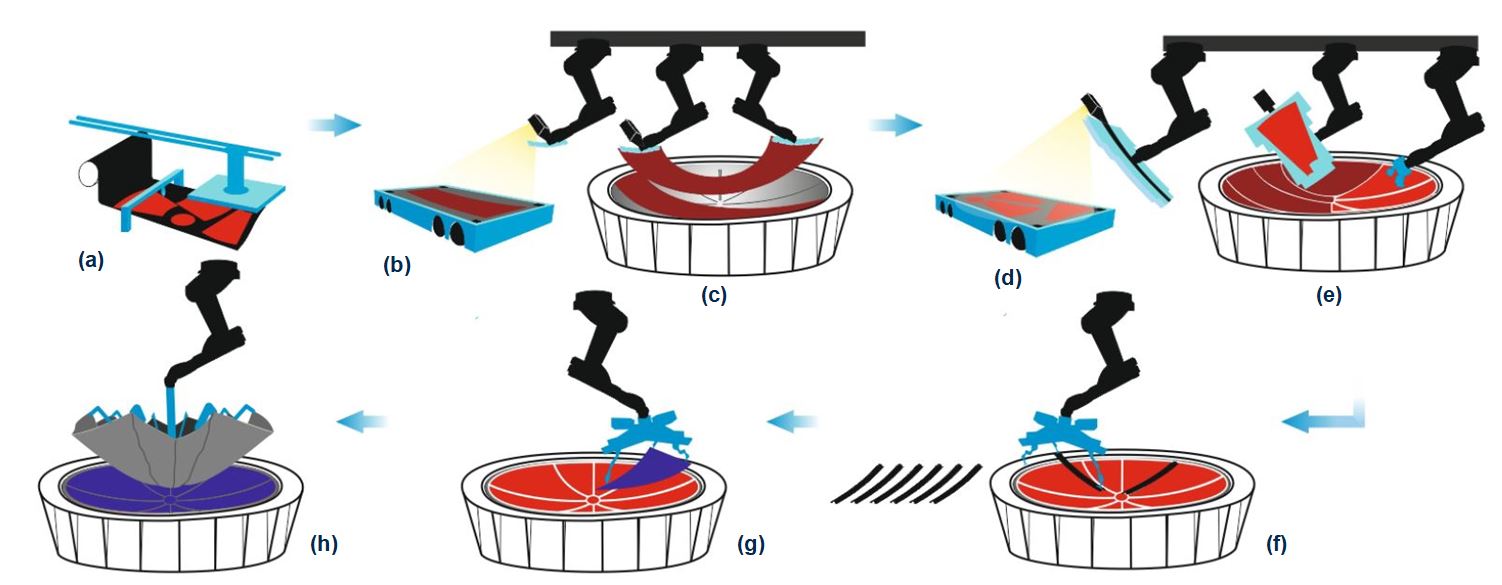
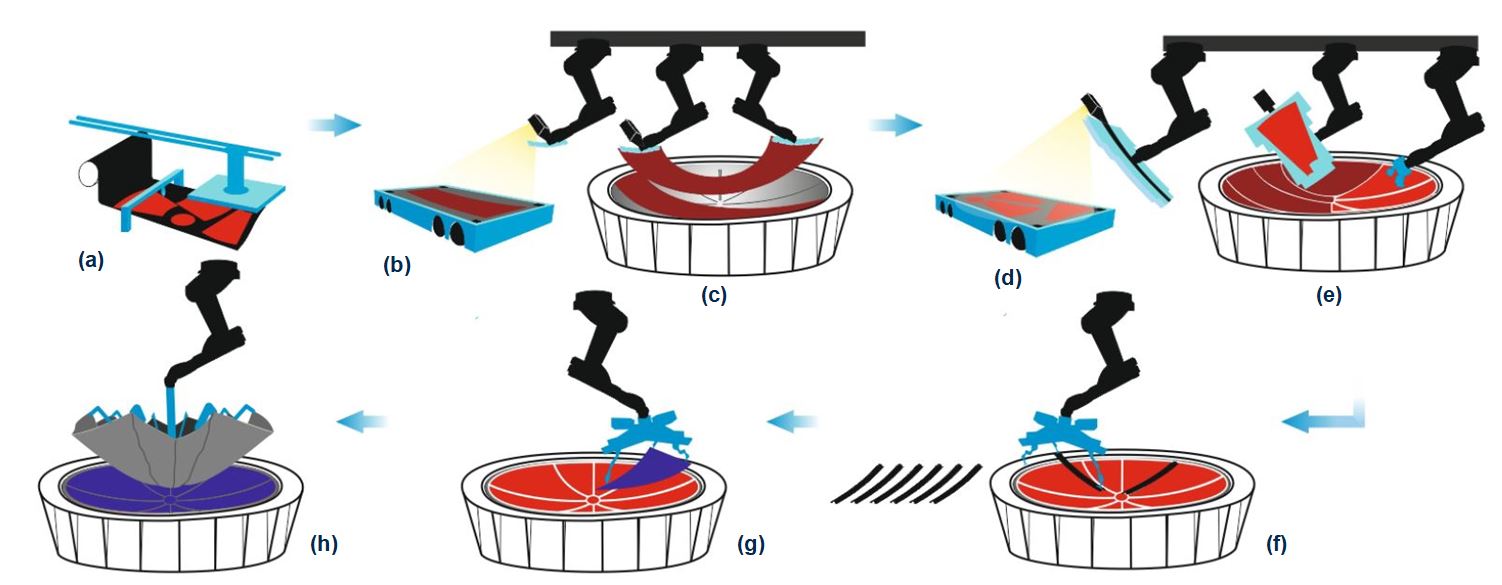
« Développer des outils et des pinces capables d'atteindre la précision nécessaire pour le drapage et la manipulation a été l'un des plus grands défis », note Larsen. Cela était en partie dû au mélange complexe de plis qui nécessitait trois mécanismes de drapage différents :
- Application de matière pleine largeur directement à partir du rouleau qui doit s'adapter à la forme du moule.
- Drapage de plis structurels de grandes coupes où deux robots collaborent, un par bord de tissu, pour saisir et créer la géométrie cible du moule pour assurer une conformation sans plis avant la pose.
- Adaptation pour les petits plis façonnés jusqu'à 1,5 sur 2,5 mètres .
"Pour les robots coopérants, nous avons développé des effecteurs terminaux qui contiennent six modules reliés par des articulations sphériques", explique Larsen. « Cela permet à l'effecteur final de se déformer, d'une manière similaire à un serpent, en se conformant à la géométrie cible du moule. Les dispositifs de chauffage intégrés activent le liant dans le tissu pendant qu'il est transporté et façonné, maintenant sa forme 3D et sa position une fois placé. »
Drapage et placement automatisés
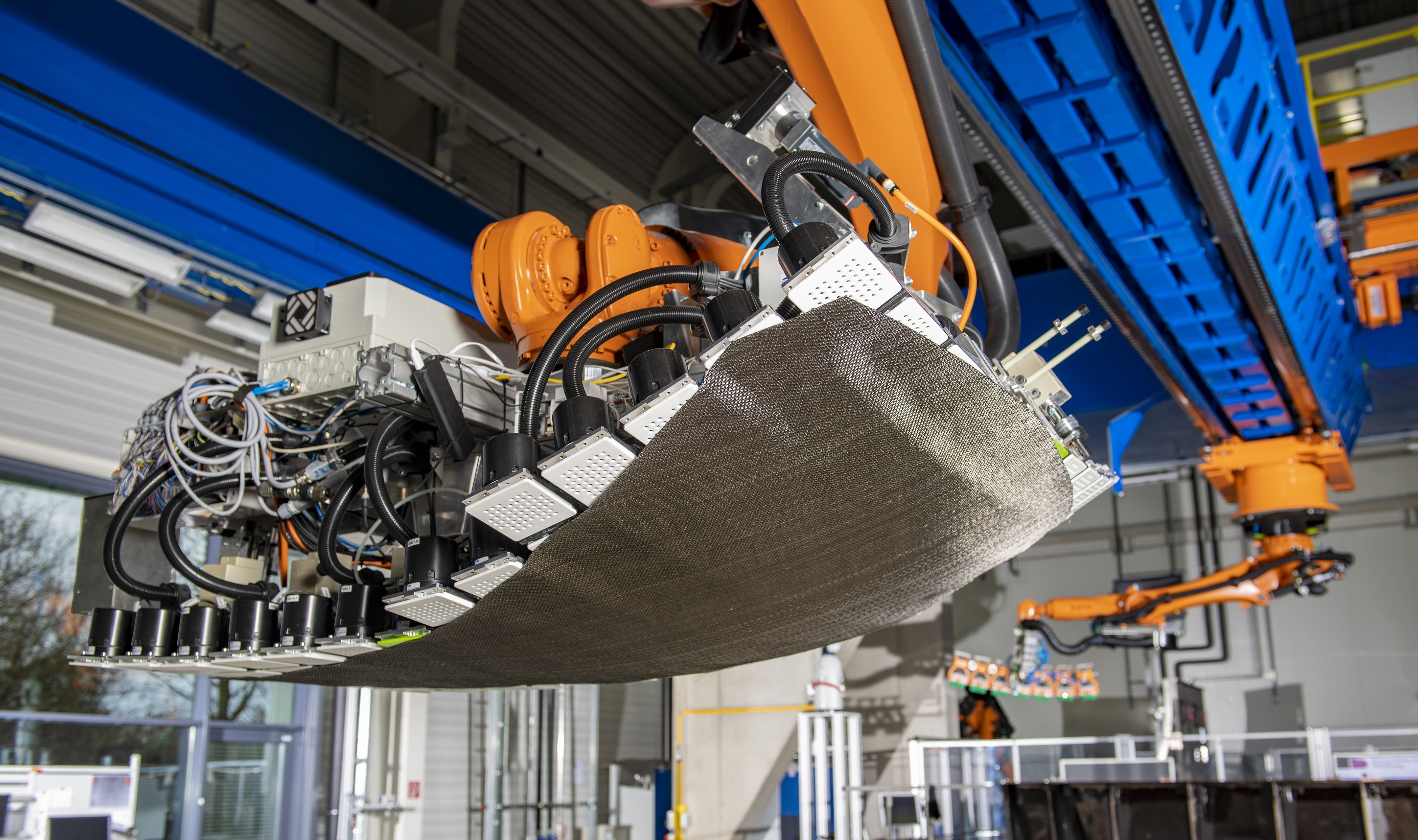
L'effecteur final est doté d'une pince qui utilise 127 modules équipés d'une aspiration sous vide pour prélever des plis de tissu coupés, les transformer ensuite en une forme 3D, puis les chauffer avant de les placer dans le moule. Crédit photo :Institut des structures et de la conception du Centre aérospatial allemand (DLR)
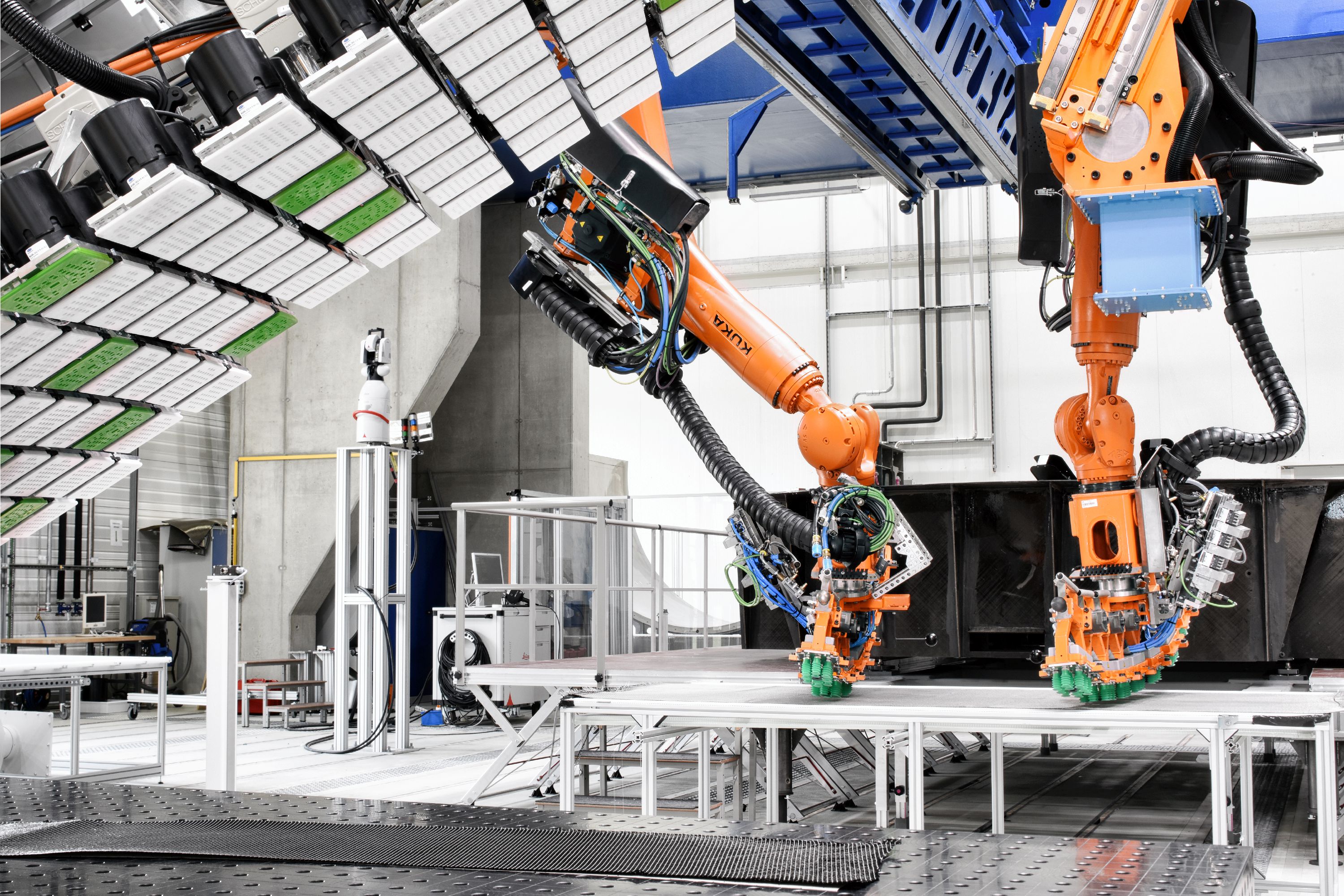
Ici, on peut voir à la fois le préhenseur à 127 modules (à gauche) et les robots collaborateurs (en arrière-plan). Crédit photo :Institut des structures et de la conception du Centre aérospatial allemand (DLR)
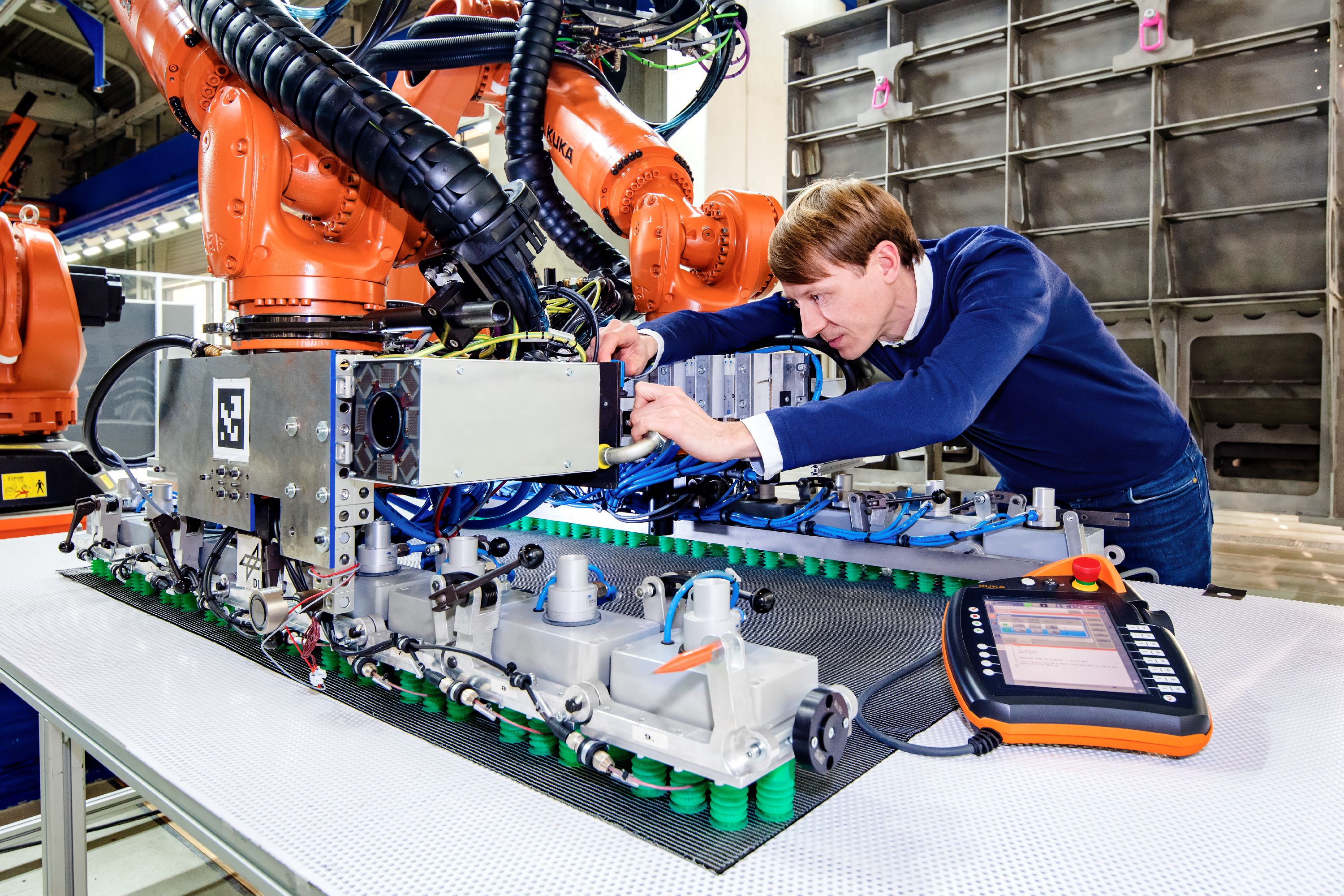
Pour les robots collaborateurs, des effecteurs terminaux ont été développés qui contiennent six modules reliés par des articulations sphériques. Crédit photo :Institut des structures et de la conception du Centre aérospatial allemand (DLR)

Chaque robot ramasse un bord du grand pli de tissu. Ils travaillent ensuite ensemble pendant qu'ils transportent le pli pour créer la géométrie cible requise avant de placer le tissu dans le moule. Crédit photo :Institut des structures et de la conception du Centre aérospatial allemand (DLR)
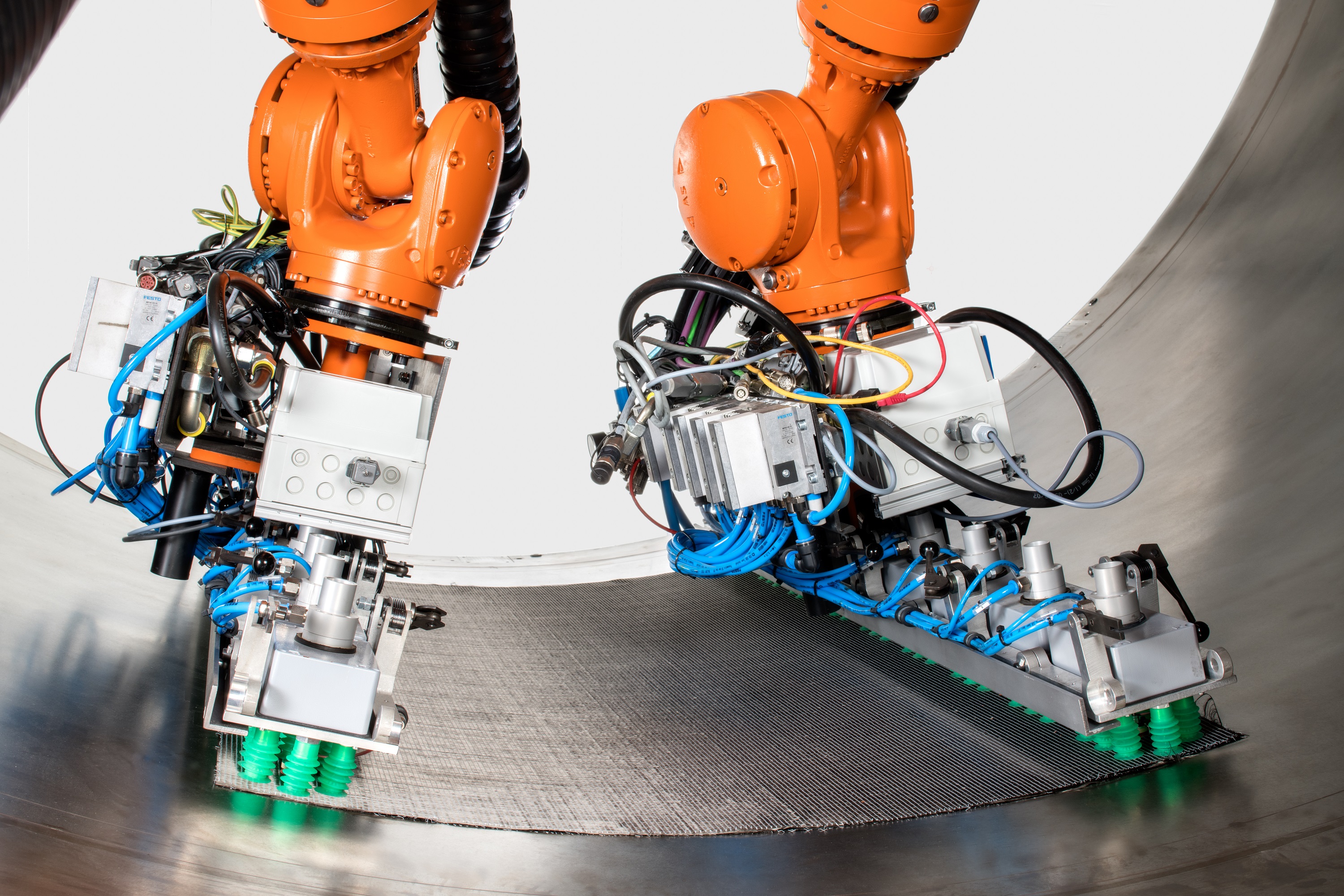
Crédit photo :Institut des structures et de la conception du Centre aérospatial allemand (DLR)
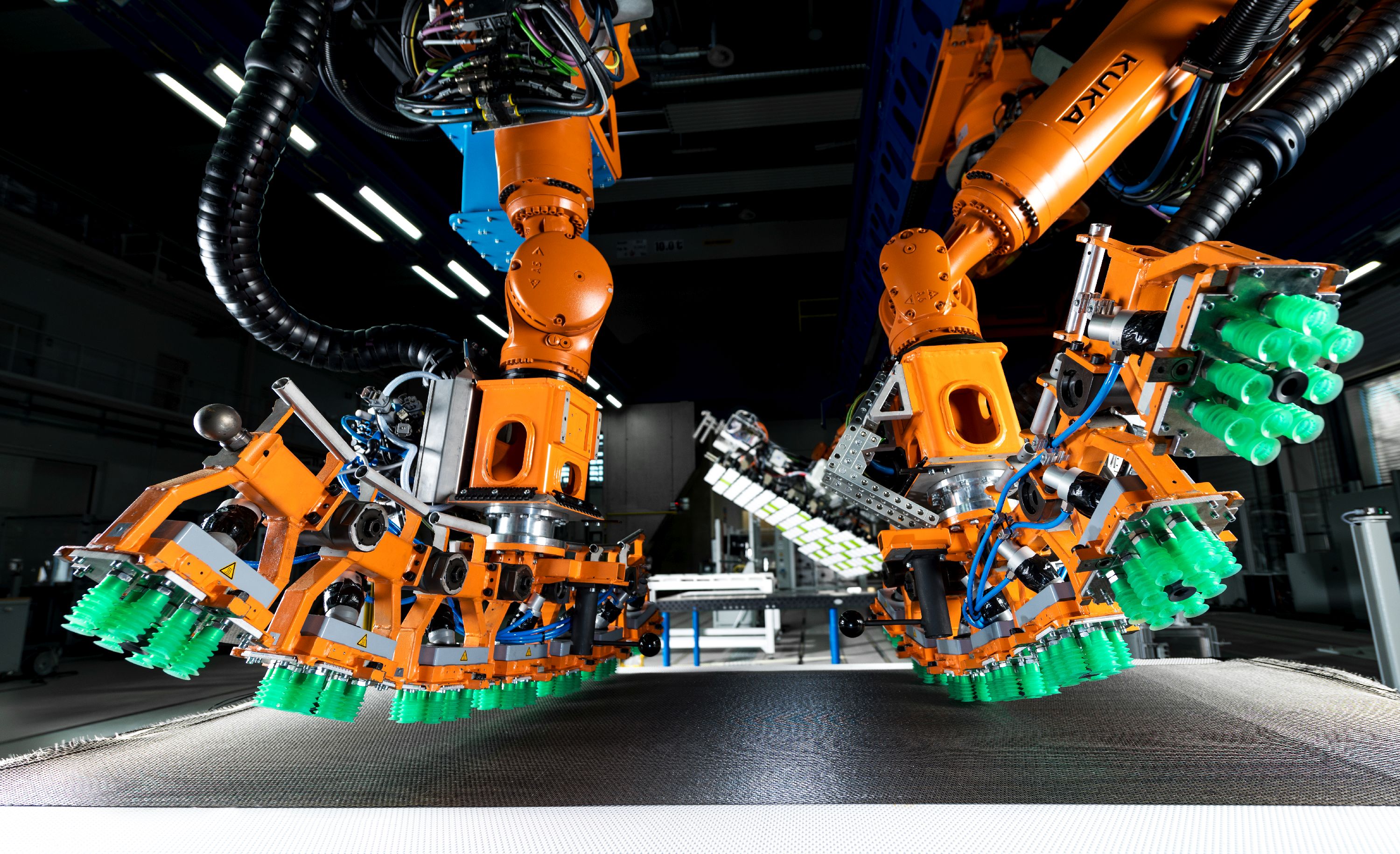
Gros plan sur les effecteurs finaux du robot collaboratif. Crédit photo :Institut des structures et de la conception du Centre aérospatial allemand (DLR)
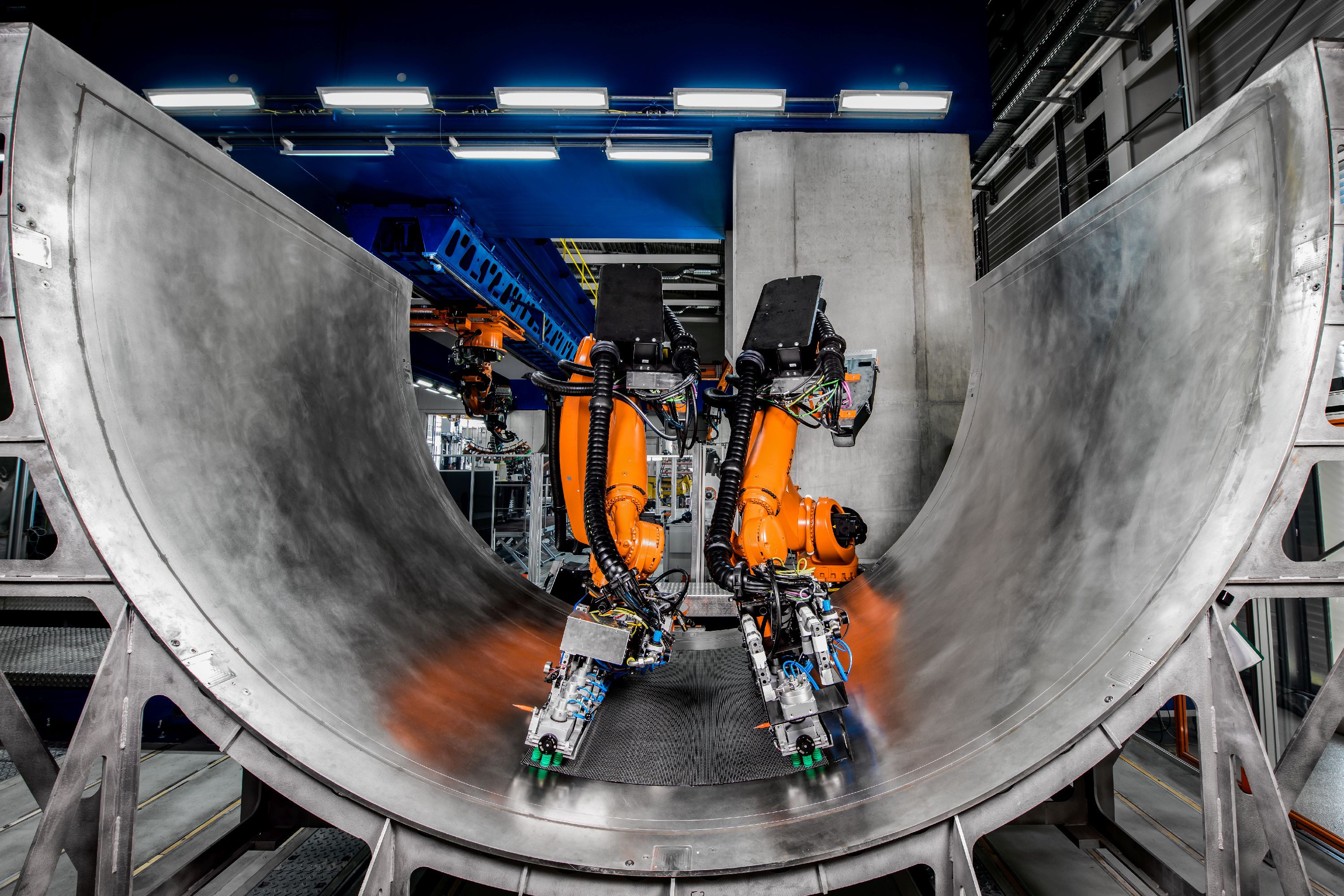
Ce système initialement développé par le DLR pour une cloison de pression arrière d'A320 a maintenant également été démontré pour un panneau de fuselage et est conçu pour être flexible pour une variété de grandes aérostructures, sur la base de leurs fichiers de conception numériques, sans réapprendre les robots. Crédit photo :Institut des structures et de la conception du Centre aérospatial allemand (DLR)
Précédent SuivantPour les petits plis façonnés jusqu'à 1,5 sur 2,5 mètres, un deuxième type de préhenseur a été développé qui utilise 127 modules équipés d'une aspiration sous vide pour le ramassage. "Cette pince saisit le matériau dans un état 2D, puis le plie selon la géométrie cible", explique Malecha. « Il doit décider lequel des 127 modules il tiendra ferme et lequel il laissera glisser pour transformer le pli 2D en une forme 3D. Donc, c'est très similaire à la façon dont les mains travaillent pour draper. Nous avons fait de nombreuses expériences et acquis de l'expérience sur où tenir et où sortir. La force peut être ajustée en fonction de l'intensité de l'adhérence des modules sur le matériau. »
Inspection en ligne. Des capteurs optiques dans les pinces modulaires ont surveillé le processus de drapage. Après avoir placé un pli, un effecteur final combinant un Leica T-Scan (Hexagon Manufacturing, Cobham, Royaume-Uni) et un système de mesure d'angle de fibre basé sur une caméra de Profactor (Steyr, Autriche) vérifie la qualité. "Nous avons d'abord mesuré les angles des fibres et comparé au fichier CAO", explique Malecha, "puis nous avons mesuré les bords de chaque pièce et vérifié sa position par rapport au fichier CAO."
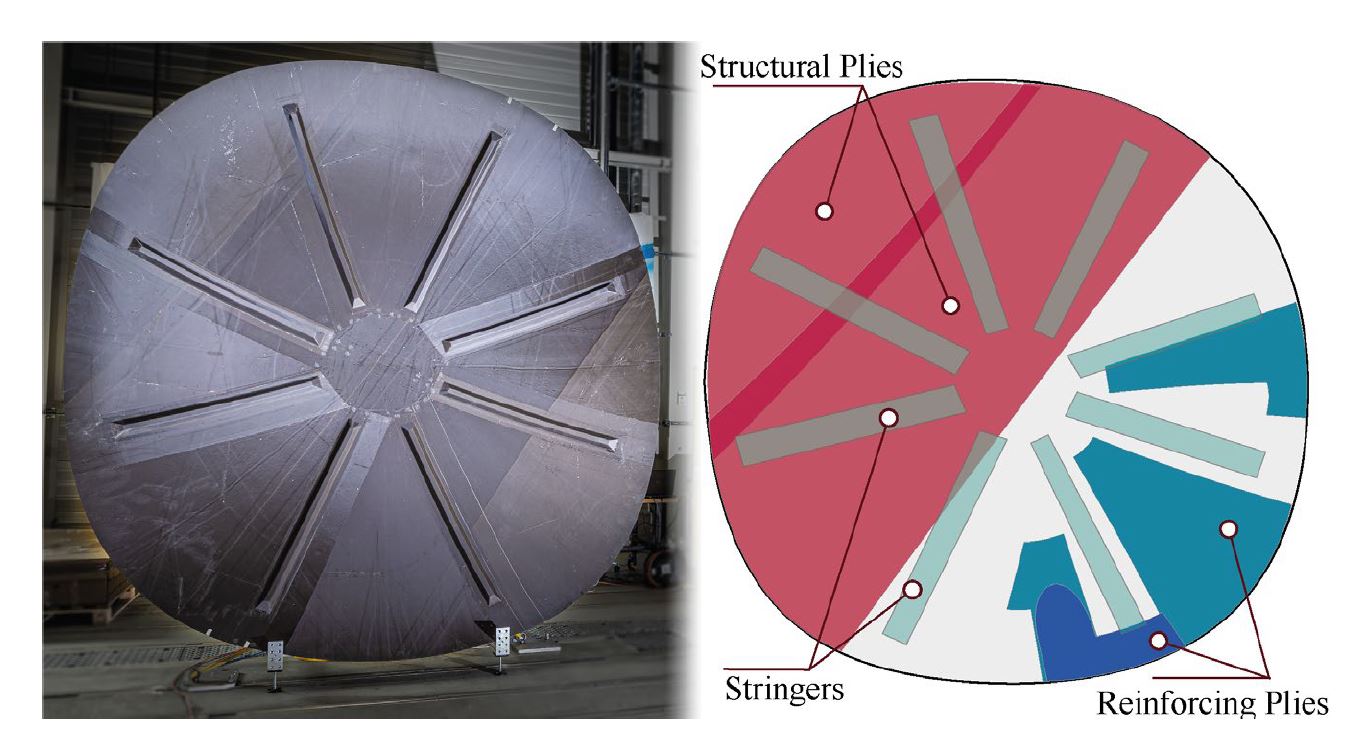
Longueurs et mise sous vide. Après avoir terminé la préforme, huit raidisseurs (longerons) ont été fixés sur le dessus. Pour cette tâche, le Multi Kinematic Gripper a été développé et a également été utilisé pour appliquer les matériaux auxiliaires du sac sous vide. Cette pince comprend trois petits robots indépendants à 6 degrés de liberté (DOF) et un bras rigide, tous montés sur la bride centrale d'un robot industriel à 6 degrés de liberté. Les matériaux auxiliaires d'ensachage sous vide - pli pelable, film antiadhésif perforé et supports d'écoulement de résine (matériaux auxiliaires côté outil) - ont été prédécoupés et pré-assemblés, conçus pour l'endroit où ils ont été placés. "Ils n'avaient pas besoin d'être drapés, juste placés", note Malecha. La membrane semi-perméable préfabriquée a été appliquée de manière semi-automatique via un effecteur terminal avec un mécanisme "en forme de parapluie", tandis que le placement du ruban adhésif et du sac sous vide extérieur restait manuel mais pouvait également être automatisé.
Durée et coût du cycle. Pour Malecha, le plus grand défi consistait à construire le système d'exécution de fabrication (MES) modulaire basé sur l'intelligence artificielle (IA) pour surveiller et contrôler la chaîne de processus. « Nous avons dû construire des systèmes de gestion de données qui pourraient rassembler des processus assez différents, puis les commander via le MES via un port d'échange de données », explique-t-il. « Nous pouvons les utiliser au fur et à mesure de nos besoins, ce qui permet une plus grande flexibilité et une utilisation plus large par rapport à un ordre de fabrication strict. »
La technologie PROTEC NSR a été validée en fabriquant un démonstrateur grandeur nature en janvier 2019 et en atteignant un niveau de maturité de TRL 5-6 à la mi-2019. Par rapport à l'état de l'art actuel de PAG, cette chaîne de processus automatisée réduit le temps de cycle d'application du tissu enroulé de 58 % et le prélèvement et le placement des plis coupés de 50 %. Les coûts de fabrication de ces opérations ont été réduits de 11,5% et 31%, respectivement.
RPB thermoplastique
« Ce projet a débuté en 2018 avec le PAG et l'Institut für Verbundwerkstoffe (IVW, Kaiserslautern, Allemagne) pour montrer ce qui est possible avec les composites thermoplastiques dans les grandes pièces et les structures primaires », explique le Dr Stefan Jarka, chef de projet pour Fast Lane RPB et expert en technologies de soudage chez ZLP Augsburg. « Un RPB n'est pas vraiment primaire, car les exigences mécaniques ne sont pas aussi élevées qu'une aile ou un fuselage, mais il montre ce qui est possible pour de grandes structures plates et légèrement incurvées. En seulement quatre mois, nous avons développé un démonstrateur A320 RPB comme exemple de conversion d'une structure en aluminium existante en composites thermoplastiques. »
Ce démonstrateur a utilisé un tissu en fibre de carbone (CF) Cetex/une feuille organique en polysulfure de phénylène (PPS) (Toray Advanced Composites, Nijverdal, Pays-Bas) et un soudage par résistance. Un élément résistif entre les deux surfaces à souder génère de la chaleur et reste dans la structure soudée. GKN Fokker (Hoogeveen, Pays-Bas) utilise cette technique depuis des décennies pour produire des trappes de train d'atterrissage et des bords d'attaque fixes. Pour cet A320 RPB, l'équipe ZLP a utilisé un élément résistif CF au lieu d'un grillage en acier inoxydable conventionnel.
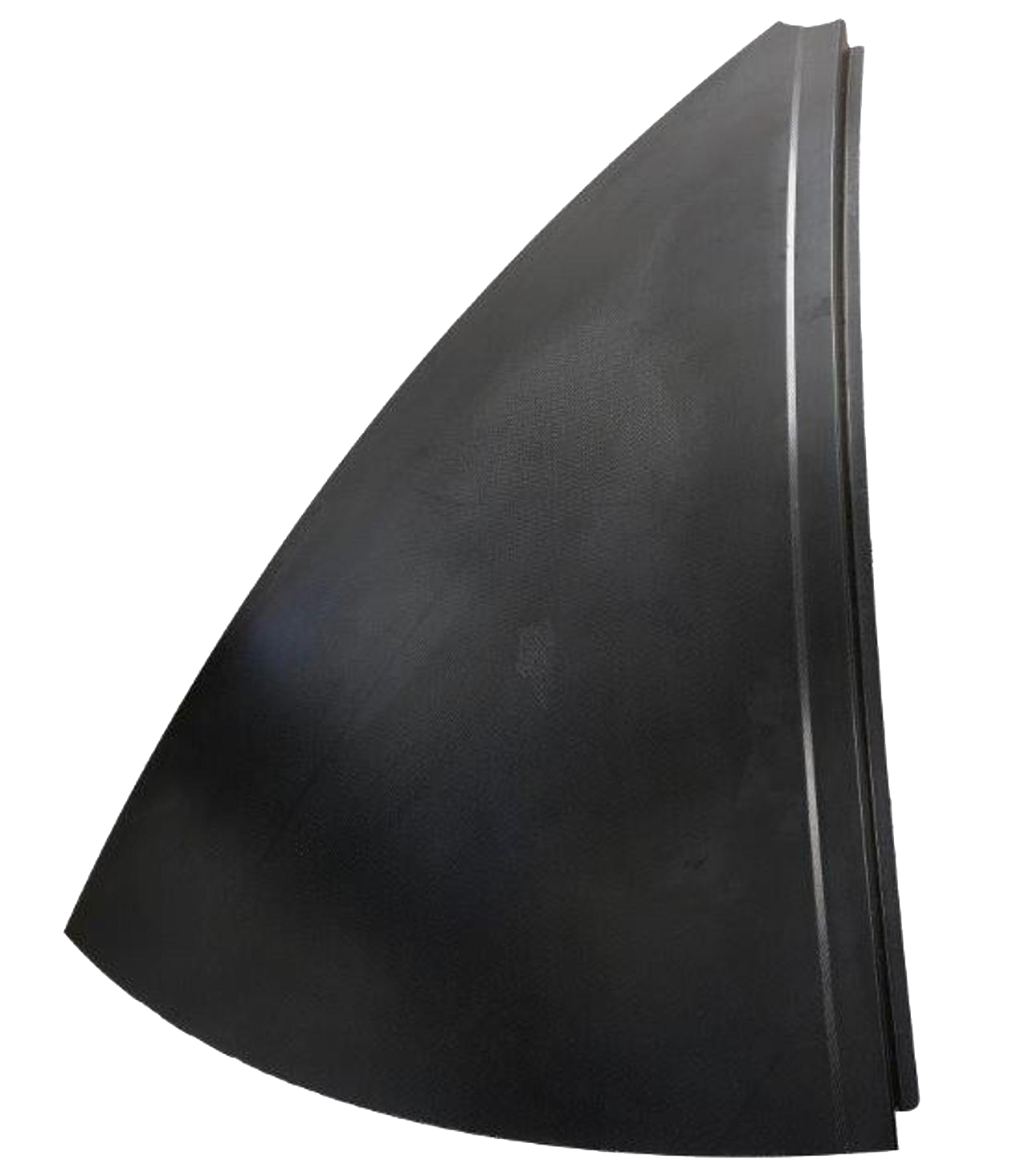
« Le composite thermoplastique RPB devait être au même prix ou moins cher, mais le matériau est beaucoup plus cher », note Larsen. Ainsi, la réduction des coûts de production due à l'automatisation était essentielle, tout comme l'utilisation de huit sections de pétales identiques. « Ces sections étaient nécessaires pour former la forme à double courbure de la pièce », explique Jarka. « Le thermoformage en une seule pièce nécessiterait une presse de très grande taille qui serait trop chère. Ainsi, huit sections plus petites ont été moulées à la presse par l'IVW à l'aide d'un outillage métallique adapté et nous les avons assemblées à l'aide d'un soudage automatisé. Le niveau d'automatisation du formage à la presse des thermoplastiques est plus élevé que celui des composites thermodurcissables. Vous utilisez principalement des outils métalliques adaptés, la température élevée mais constante étant le principal problème, mais cela rend également le cycle de presse automatisé très rapide. »
Les étapes globales du processus du démonstrateur RPB sont illustrées à la Fig. 2. « Le processus de soudage que nous avons utilisé n'était pas nouveau », explique Jarka, « mais a dû être développé large] coutures pour la pièce de 3 mètres de diamètre et intègrent un système de contrôle qualité. Les composants ont d'abord été fixés dans la bonne position à l'aide d'un gabarit de positionnement, puis de l'énergie électrique a été appliquée pour générer le plastique fondu dans la zone de soudure. »
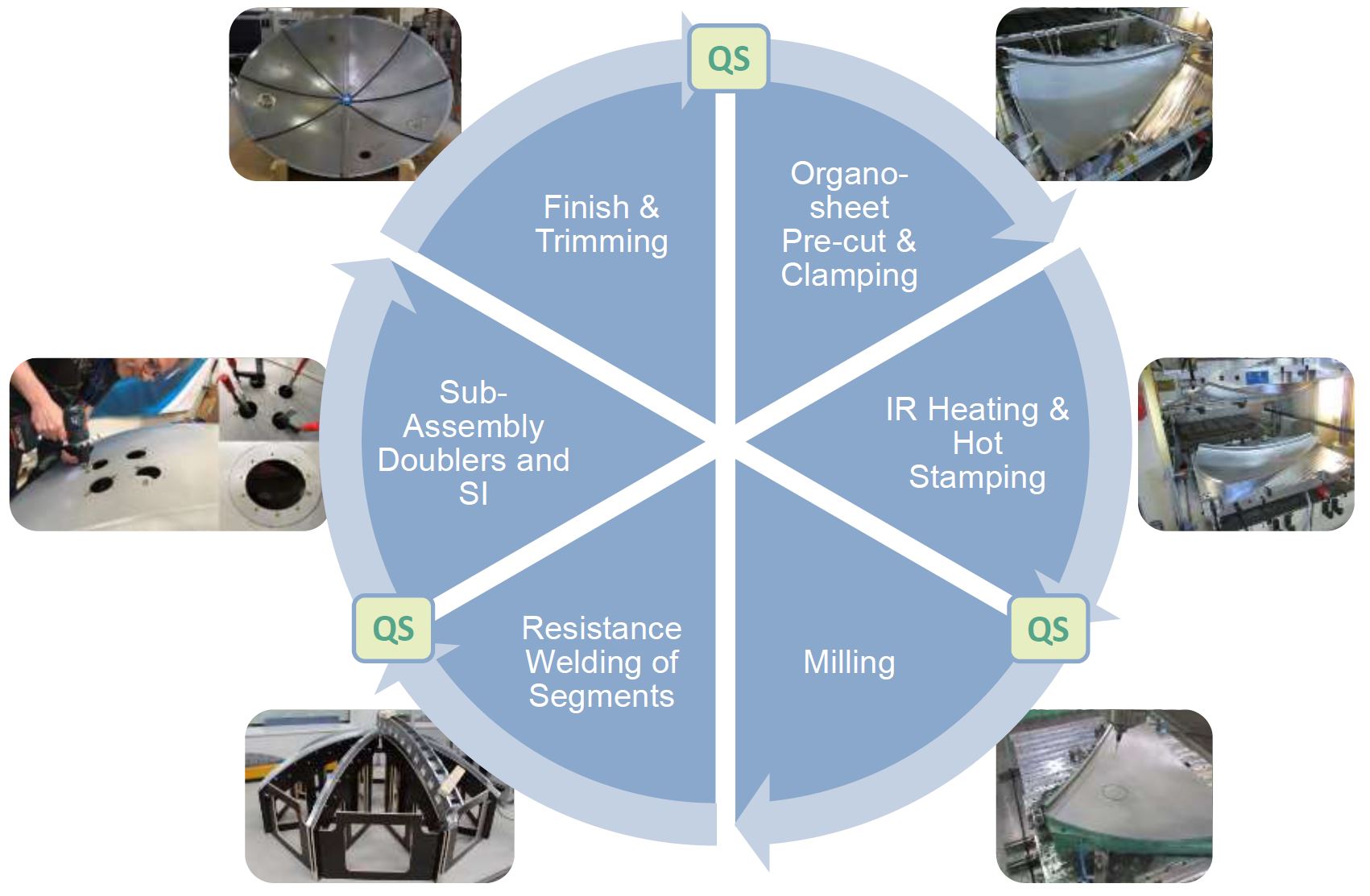
Fig. 2. Étapes du processus RPB thermoplastique
Étapes du processus utilisées pour produire huit sections (en bas) de feuille organique CF/PPS formée par tampon qui ont ensuite été assemblées par soudage par résistance pour former une cloison de démonstration A320. Crédit photo :Institut des structures et de la conception du Centre aérospatial allemand (DLR)
Intégrer le contrôle qualité. « Nous avons essayé la thermographie, activée à la fois par lampe flash et par ultrasons, mais ce n'est pas si facile de mesurer la zone de soudage avec cela », explique Jarka. « La thermographie est très rapide, mais elle ne vous dit pas facilement si vous avez une bonne consolidation. » Au lieu de cela, ils ont utilisé un banc d'essai standard pour fabriquer plusieurs échantillons soudés, mesurant le courant, la tension et la température. « Nous les avons ensuite inspectés avec des tests par ultrasons (UT) et avons établi des corrélations entre les paramètres de processus et une bonne consolidation », explique Larsen. « Si nous avons de bons paramètres, alors nous avons une bonne partie. Nous avons également construit une simulation de processus pour comparer les données que nous obtenons pendant le soudage avec la ligne de base initiale que nous avons établie. »
Automatisation et temps de cycle. « L'ensemble du processus a été très rapide, à l'échelle des pièces automobiles », explique Jarka. « Nous avons atteint le TRL 3 lors de notre examen de 2019 et avons depuis atteint le TRL 4. Nous atteindrons le TRL 6 d'ici la fin de 2021. » Avant la pandémie, PAG avait indiqué qu'il mettrait le RPB thermoplastique en production d'ici 2021. Bien que l'avenir soit maintenant moins clair, le RPB thermoplastique est toujours considéré comme permettant le «fuselage de demain», réduisant le poids de 41 à 35 kilogrammes, processus et le temps d'assemblage de 75 % et le coût global des pièces de plus de 10 %.
Comparaison des composites TS et TP
« Les processus thermoplastiques sont si rapides que vous pouvez être moins cher que l'aluminium et même atteindre un taux de production de 100 avions par mois », explique Jarka. « Le RPB est une bonne application pour le soudage thermoplastique mais aussi pour l'automatisation », explique Malecha. « Le RPB à fibres sèches et moulées en liquide est plus coûteux à automatiser. »
"Mais cette automatisation est intéressante car vous pourriez obtenir de réels gains en automatisant seulement certains des sous-processus", explique Larsen. « Par exemple, avec l'automatisation des auxiliaires, nous pourrions terminer l'ensachage sous vide en une heure environ, soit environ 10 fois plus rapidement que le processus manuel. Cependant, il concède que le coût est un obstacle majeur à la mise en œuvre d'une telle amélioration. « Le coût des outils numériques, des robots et du développement est trop élevé pour une seule pièce, comme le RPB. Mais si nous pouvions développer une approche modulaire où vous pourriez utiliser ce système pour de nombreuses pièces, alors ce coût pourrait être réparti plus largement, le rendant abordable lorsqu'il est calculé avec un temps et une main-d'œuvre réduits. ZLP a en effet atteint cet objectif, comme expliqué dans CW Article de juillet 2020 :"Composites 4.0 :transformation numérique, production adaptative, nouveaux paradigmes."
"Il n'y a pas encore beaucoup de comparaisons entre les structures composites thermodurcissables et thermoplastiques", explique Malecha. "Mais nous commençons à comparer les procédés thermodurcissables et thermoplastiques." Il note que le prochain objectif est de montrer que les lignes de soudure thermoplastiques ont les propriétés requises pour les ailes et les fuselages d'avions. Et cette performance doit également être démontrée pour les grandes ailes moulées liquides intégrées, par exemple. C'est exactement ce que les programmes MFFD et WOT ont entrepris d'accomplir. Et nous attendons leurs résultats, ainsi que ceux de nombreux autres projets Clean Sky 2 et EC, pour montrer les prochaines étapes.
Résine
- Blog :Moulage par injection de caoutchouc de silicone liquide
- Technologie de production de panneaux en nid d'abeille thermoplastique EconCore
- Karl Mayer lance une ligne de production de rubans thermoplastiques UD
- INEOS Styrolution va construire un site de production pour le composite thermoplastique StyLight
- La technologie de production Herone remporte le JEC Innovation Award
- Thermoplastiques surmoulés thermodurcissables, cycle de 2 minutes, une cellule
- LANXESS étend sa capacité de production de composites thermoplastiques renforcés de fibres continues
- Airtech lance des matériaux d'ensachage sous vide haute température pour le moulage thermoplastique
- Procédé Finex pour la production de fonte liquide