Rubans thermoplastiques renforcés de fibre de carbone PAN à base de textile
Un défi de longue date dans l'industrie des composites avancés est de trouver des moyens de produire de la fibre de carbone à moindre coût afin que toutes les industries qui souhaitent utiliser ce renfort composite précieux et efficace puissent le faire. Les coûts de la fibre de carbone ont considérablement baissé grâce à des décennies de travail pour améliorer la productivité via la chimie des précurseurs, l'innovation des machines, l'amélioration des processus et plus encore.
L'utilisation de précurseurs alternatifs au polyacrylonitrile (PAN) conventionnel de qualité aérospatiale est un domaine très prometteur. Par exemple, le US Dept. of Energy (DOE, Washington, DC, US) et le Oak Ridge National Laboratory (ORNL, Oak Ridge, Tenn., US) ont développé des méthodes pour produire de la fibre de carbone à partir de précurseurs alternatifs allant des polymères à la lignine. , au charbon.
Précurseurs alternatifs
L'un des précurseurs les plus prometteurs, et le plus proche de la commercialisation, est le PAN à base de textile, qui est similaire à la fibre utilisée pour produire des pulls en acrylique. Comme d'autres précurseurs alternatifs étudiés par ORNL, la fibre de carbone PAN (TCF) à base de textile est différente de la fibre de carbone PAN spécialisée dans l'aérospatiale à plusieurs égards.
L'une des différences est que le précurseur de PAN à base de textile, car il est destiné à être utilisé dans l'industrie textile (pensez aux rideaux, aux vêtements, aux tissus d'ameublement), est fourni dans un format de remorquage large qui est intrinsèquement moins coûteux que celui spécialisé de qualité aérospatiale. Précurseur du PAN. Lors de la production de fibre de carbone, cela a pour effet d'augmenter le débit et de réduire les coûts de conversion par rapport à la fibre PAN conventionnelle. Il a également tendance à produire une fibre de remorquage beaucoup plus grande - de l'ordre de 300K à 450K sur la ligne à l'installation de technologie de fibre de carbone de l'ORNL contre 3K à 50K typique de la fibre de carbone PAN conventionnelle. De plus, alors qu'il faut plus de temps pour traiter le précurseur du TCF, car il ne contient pas d'accélérateurs de réaction comme le PAN conventionnel et est généralement exécuté à des températures plus basses (en fonction de la nécessité d'équilibrer le temps de séjour et la température), le fait que beaucoup plus de fibres peuvent être traités à un moment donné et que la consommation d'énergie est plus faible en poids ou en volume permet de réduire les coûts. En fait, l'ORNL estime qu'environ 60 % d'économies d'énergie totales pour la conversion de la fibre optique et environ 50 % d'économies de coûts sont possibles.
Cela offre à son tour la possibilité de produire des fibres moins coûteuses en quantités inhabituellement importantes et de les utiliser pour fabriquer des produits avec une empreinte carbone plus faible. Dans des secteurs tels que l'automobile/le transport terrestre, l'électronique grand public, les articles de sport, le bâtiment/la construction et l'énergie éolienne, le TCF est un renforcement attrayant car les applications ont tendance à être axées sur la rigidité, par rapport aux applications axées sur la résistance dans l'aérospatiale. Notamment, les industries non aérospatiales pourraient potentiellement consommer beaucoup de fibres.
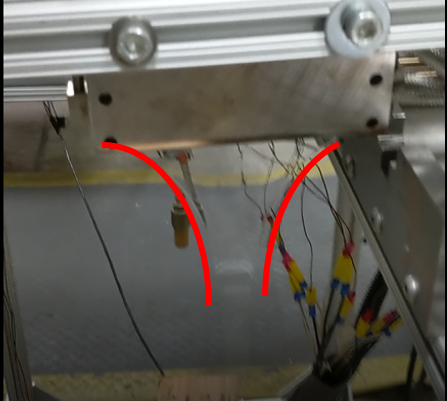
Cependant, le TCF est toujours un produit différent de la fibre de carbone PAN conventionnelle, des travaux sont donc nécessaires non seulement pour mieux caractériser cette fibre, mais aussi pour trouver des moyens de la convertir et de l'utiliser. Parce qu'il peut être traité dans une bande de remorquage ultra-large, ce précurseur nécessite des modifications de l'équipement de traitement tout au long du processus de production de fibres. Cela modifie également la modification de la surface et l'emballage post-production, et cela affectera, bien sûr, les processus de conversion allant de la fabrication de rubans et de tissus aux préimprégnés et aux préformes.
Reconnaissant toutes les façons dont le TCF peut résoudre le problème de coût/disponibilité de la fibre de carbone d'une part, mais crée également de nouveaux problèmes dans la façon de manipuler, convertir et emballer ce matériau d'autre part, l'Institute for Advanced Composites Manufacturing Innovation (IACMI, Knoxville , Tenn., États-Unis) a travaillé sur un certain nombre de projets de recherche financés par les membres au cours des trois dernières années pour résoudre ces problèmes. Un projet intéressant a examiné les moyens de convertir le TCF à bande de remorquage ultra-large en rubans composites thermoplastiques.
Réduire les coûts
L'intérêt pour les rubans composites thermoplastiques s'est accru dans de nombreuses industries, mais ces produits ont tendance à être coûteux, car un équipement et un savoir-faire spécialisés sont nécessaires pour imprégner avec succès toute fibre avec des résines thermoplastiques prépolymérisées, de poids moléculaire élevé et de haute viscosité par rapport à leurs homologues thermodurcissables à faible viscosité n'ayant pas réagi. Il n'est que trop facile de produire des bandes avec beaucoup de vides et une mauvaise humidification des fibres, se terminant par des pièces finales qui non seulement ont l'air affreuses, mais présentent également un risque de défaillance prématurée.
Le Dr Uday Vaidya, professeur et président du gouverneur pour la fabrication de composites avancés, Université du Tennessee-Knoxville (UTK, Knoxville, Tennessee, États-Unis) et directeur de la technologie de l'IACMI (CTO), a collaboré à des programmes de composites thermoplastiques depuis le début des années 2000 avec George Husman, président de Husman Consulting Inc. (Cape Coral, Floride, États-Unis) et directeur à la retraite et CTO de Zoltek Co. Inc. (St. Louis, Mo., États-Unis). Leurs nombreuses interactions ont conduit à l'idée de l'imprégnation en ligne de fibres de carbone conventionnelles à mèches lourdes (24K à 50K) pour produire des rubans composites thermoplastiques à l'arrière de la ligne de production de fibres. La production de rubans immédiatement après la production de fibres éliminerait une étape de processus intermédiaire distincte et tous les frais d'expédition et de manutention que cela implique. On espère que cela contribuera à réduire les coûts des bandes et des pièces fabriquées à partir de ces bandes.
La réalisation de ce concept a nécessité un développement à la fois du processus et de l'équipement pour fabriquer des rubans thermoplastiques renforcés de fibres de carbone dans différentes tailles de câble. Vaidya et Husman ont déposé un brevet provisoire en collaboration avec la Fondation de recherche de l'Université du Tennessee (UTRF, Knoxville, Tennessee, États-Unis) en 2018 couvrant un processus de production en ligne de rubans thermoplastiques renforcés avec jusqu'à 50K de fibre de carbone. L'année suivante, Vaidya et son équipe UTK ont étendu ce travail pour inclure l'imprégnation thermoplastique du TCF ultra large bande (300K à 450K remorquage) avec un deuxième dépôt.
Bandes TCF TP
Comme on pouvait s'y attendre, les défis techniques à relever ne manquent pas. L'alimentation et la manipulation de la fibre ont nécessité une modification importante de l'équipement, car le TCF a tendance à être plus large et à impliquer plus de filaments que la fibre de carbone conventionnelle. Il est également sujet au comportement caténaire pendant l'étape d'imprégnation des fibres de la production de ruban. Cela signifie qu'une onde sinusoïdale se forme lorsque les câbles alimentent la matrice d'imprégnation, provoquant une séparation inégale des câbles et leur entrée dans la matrice sous différentes tensions, ce qui conduit à des rubans qui se tordent, se déforment et humidifient mal les fibres.
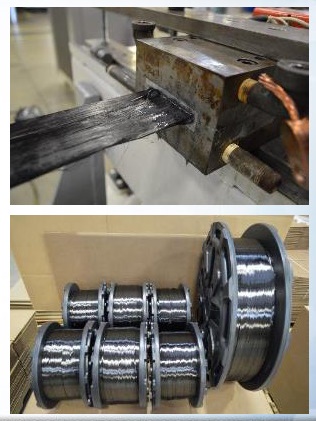
« Trouver un moyen de maintenir un équilibre entre la tension des fibres et la flexibilité s'est avéré très difficile et a demandé beaucoup de travail », explique Vaidya. « Notre équipe a compris à quel point il était important de maintenir l'intégrité du câble afin d'étendre les filaments et d'obtenir un degré élevé de mouillage, ce qui, bien sûr, est essentiel pour produire des rubans de qualité. »
Ensuite, il y avait le problème de la taille. Les bandes de remorquage TCF sont fortement dimensionnées pour aider la fibre à se déplacer en douceur du cantre à la matrice d'imprégnation où elle est mouillée avec de la résine pour produire du ruban. Cependant, une fois à la filière, des recherches antérieures avaient montré que pour obtenir un bon mouillage avec des thermoplastiques à viscosité plus élevée, la présence d'encollage empêchait en fait l'imprégnation, ce qui rendait très souhaitable l'élimination de l'encollage. Des essais et des erreurs ont finalement conduit l'équipe à développer une technique pour brûler l'encollage juste avant que les câbles n'entrent dans la filière d'imprégnation.
Pour prédire avec précision la rhéologie de la résine et l'alimentation en polymère à travers la matrice d'imprégnation et faire un bon ruban, de nouveaux travaux de simulation et de validation étaient nécessaires. L'équipe s'est concentrée sur la production de rubans TCF avec du polypropylène (PP) ainsi que du polyamide 6 (PA6), deux thermoplastiques largement utilisés dans l'automobile pour leur ténacité et leur prix abordable. L'équipe a utilisé le logiciel de conception de matrices d'extrusion PolyXtrue de Plastic Flow LLC (Hancock, Michigan, États-Unis), qui est basé sur le modèle Williams-Landel-Ferry (WLF) et a fourni une excellente corrélation avec les résultats de rhéologie et de taux de cisaillement mesurés.
La conception de la matrice elle-même était un autre domaine de recherche important, en particulier lorsque l'équipe est passée des câbles standard de 12K à 50K, puis aux câbles TCF ultra large bande. À ce stade, la matrice a dû être complètement repensée et un processus en deux étapes adapté. Au cours de la première étape, la fibre est imprégnée; au cours de la deuxième étape, des angles de rupture optimisés pour les broches de tension/imprégnation - qui contrôlent la tension à laquelle la fibre de carbone est tirée, la fraction de poids de fibre (FWF), ainsi que le contrôle de la qualité - sont définis afin d'obtenir les propriétés souhaitées dans les bandes terminées. À l'heure actuelle, l'équipe a produit 30 à 50 % de bandes FWF en PP et en PA6, même avec les câbles les plus lourds.
Pour refroidir rapidement les bandes après la sortie de la filière, un système de refroidissement par air post-imprégnation a été développé. L'équipe a même dû élaborer une méthode pour récupérer les bandes terminées sur des cantres/bobines, en raison de la largeur des produits et des défis de l'utilisation en aval de ces bandes.
Vaidya indique que l'équipe se concentre actuellement sur l'intégration électronique, qui comprend la construction d'une interface utilisateur graphique formelle et le développement d'un système basé sur un contrôleur logique programmable (PLC). En fin de compte, l'objectif de l'équipe est de développer un module de production de ruban thermoplastique qui peut être ajouté à l'arrière d'une ligne de production de TCF ou de fibre de carbone conventionnelle pour faciliter la production de rubans thermoplastiques secondaires/intermédiaires.
« Notre équipe a été confrontée à de nombreux défis techniques, mais nous avons également réalisé quelques réalisations », explique Vaidya. « Il a été difficile de manipuler une bande de remorquage aussi large et d'imprégner avec succès - et rapidement - les fibres pour obtenir des rubans thermoplastiques de qualité sans vides. Cependant, notre équipe a exploré un certain nombre de paramètres de processus, y compris plusieurs itérations de conception de matrice; simulations d'écoulement de polymère à travers la filière ; et divers aspects de l'alimentation en fibres, de la tension et du préchauffage. Non seulement nous avons prouvé certaines des revendications de notre brevet, mais nous avons également atteint des vitesses de ligne d'imprégnation de 12 pieds/minute [3,7 mètres/minute] tout en produisant des rubans en polypropylène à 30 % FWF et PA6. »
Étapes suivantes
Vaidya dit que les protections de la propriété intellectuelle entourant cette technologie de bande ont été déposées auprès de la UT Research Foundation – une avec des fibres traditionnelles 24K et 50K et une avec des fibres à remorquage large. La commercialisation, dit-il, se concentrera sur l'imprégnation en ligne dans une ligne de fibre de carbone. "Cela réduira considérablement le post-traitement et s'adaptera facilement, ce qui réduira encore le coût global de l'intermédiaire", dit-il.
Comment ces bandes pourraient-elles être appliquées? Vaidya dit que les options sont nombreuses :« Par exemple, le matériau peut être coupé en fibres longues, utilisé dans la matière première de pultrusion, l'enroulement filamentaire de grand réservoir, le surmoulage (similaire à une feuille organique) dans le moulage par compression, les feuilles dans les processus hybrides - par exemple , avec LFT [thermoplastique à fibres longues], SMC [composé de moulage en feuille] et d'autres matériaux synergiques. Cela ouvre une gamme de types de produits qui bénéficieraient d'améliorations de la rigidité, d'une résistance aux chocs élevée et d'une aptitude au traitement améliorée telles que les formes, les étirages et les pliages, le recyclage et les chimies réversibles.
Les applications, dit-il, incluent l'automobile, les camions, les éoliennes, les infrastructures (ponts), la construction, les articles de sport, les produits marins et offshore. « L'intermédiaire thermoplastique en fibre de carbone à remorquage large peut désormais offrir des possibilités d'envisager la fibre de carbone là où elle était trop chère auparavant », conclut Vaidya.
Résine
- Fibre de carbone
- Qu'est-ce que la fibre de carbone ?
- Plastique renforcé de fibres de carbone (CFRP)
- Ruban unidirectionnel thermoplastique en fibre de carbone à base de PPS
- Le consortium cible des solutions pour les structures composites thermoplastiques en fibre de carbone
- Impression 3D de composites avec fibre continue
- Fabrication de pièces IM plus solides avec des matériaux renforcés de fibres et remplis
- Feutre en carbure de silicium renforcé de fibres de carbone SIGRASIC®
- Fibres courtes en carbure de silicium renforcé de fibres de carbone SIGRASIC®