Le système de tissage automatisé cible les applications hautes performances et à volume élevé
Un obstacle de longue date à l'adoption généralisée des composites, notamment dans l'industrie automobile, est la nécessité d'une production en grand volume et des coûts inférieurs à ceux réalisables avec de nombreux types de processus de fabrication de composites. La start-up WEAV3D Inc. (Norcross, Géorgie, États-Unis) cherche à résoudre ces problèmes avec ses structures de treillis de renforcement composites thermoplastiques continues fabriquées dans un processus de tissage automatisé conçu pour être sans déchets, rentable et, selon WEAV3D Inc. , un catalyseur pour la production à haut volume.
Du concept à la commercialisation
Christopher Oberste, fondateur et PDG de WEAV3D Inc., a développé le concept initial de sa technologie tout en obtenant son doctorat. en science et ingénierie des matériaux au Georgia Institute of Technology (Georgia Tech, Atlanta) en 2014. Ses études en ingénierie des polymères et des fibres et un stage coopératif à GKN Aerospace North America (Tallassee, Ala., États-Unis) ont suscité un intérêt pour les thermoplastiques et des procédés à haut volume comme le moulage par compression et les composites aérospatiaux. Ce travail a conduit au développement de sa première itération pour un procédé de tissage automatisé à grande vitesse pour les structures en treillis de renfort composites thermoplastiques. Avec l'aide et le soutien de son doctorat. conseiller, le Dr Ben Wang, Oberste a demandé et reçu une subvention pour développer et commercialiser son idée de la Georgia Research Alliance et du programme Innovation Corps (NSF I-Corps) de la National Science Foundation.
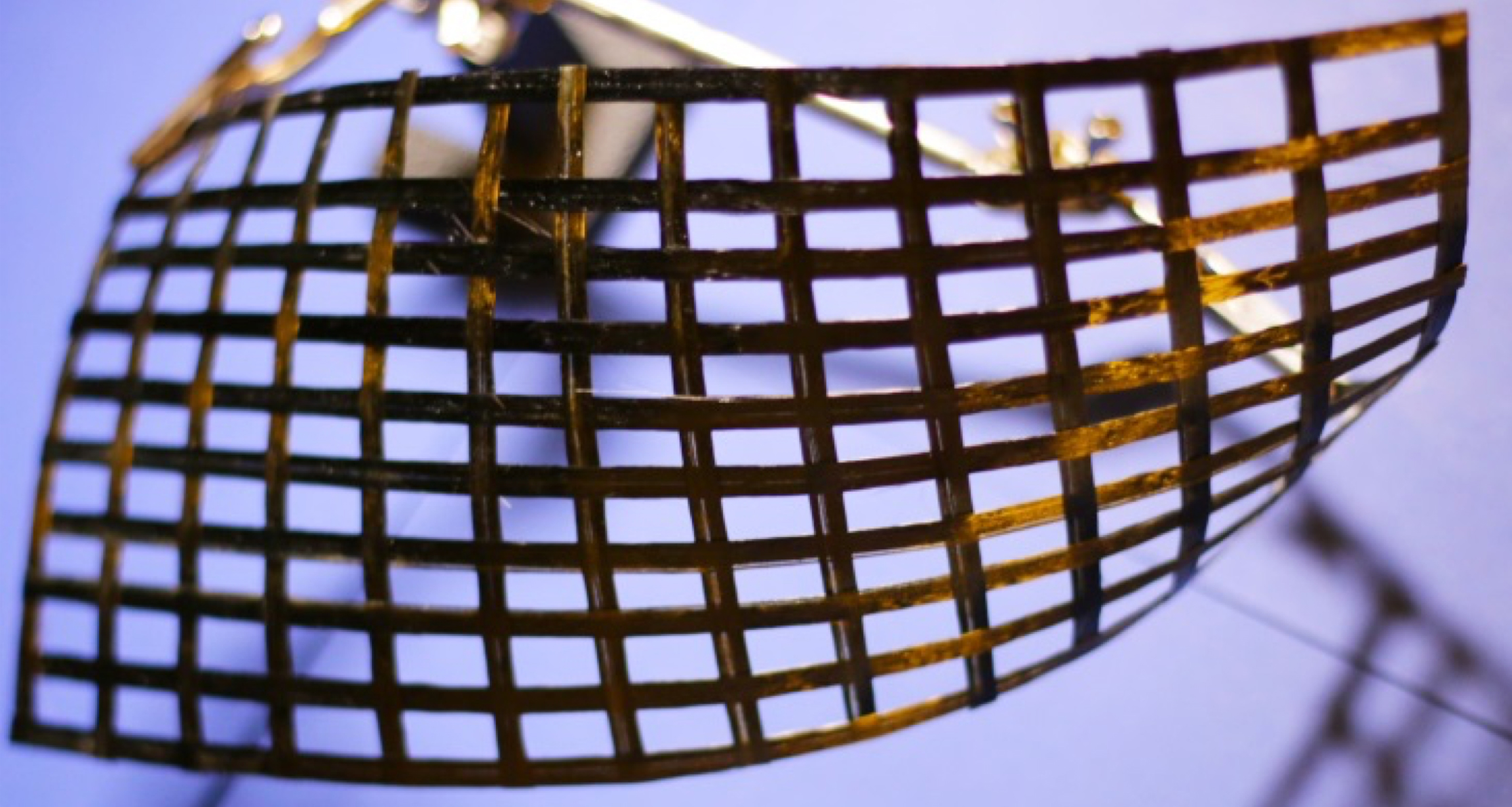
Au cours des deux années suivantes, Oberste a travaillé avec des étudiants en MBA et en droit pour commercialiser la technologie dans le cadre d'un programme de collaboration à Georgia Tech appelé TI:GER (Innovation technologique :générer des résultats économiques). D'ici 2017, avec un financement supplémentaire de Megawatt Ventures et un prix de l'Université des technologies propres du Département de l'énergie des États-Unis, Oberste et le co-fondateur Lewis Motion, un ancien pilote d'hélicoptère de la Garde côtière américaine, ont fondé WEAV3D Inc. ; aujourd'hui, l'entreprise emploie trois personnes à temps plein et quatre à temps partiel.
Compte tenu des antécédents d'Oberste et de Motion dans l'aérospatiale, le plan initial était de qualifier les matériaux composites thermoplastiques de WEAV3D en tant que structures de renforcement dans les composants aérospatiaux. Cependant, Oberste explique que dans le cadre de la subvention NSF I-Corps, lui et son équipe ont dû réaliser une série de 100 entretiens avec des clients potentiels de l'industrie, ce qui les a amenés à prendre une direction différente. «Nous avons fait beaucoup d'entretiens de découverte dans l'aérospatiale… mais nous avons entendu à maintes reprises que le chemin pour les startups qui se lancent dans l'aérospatiale, en particulier avec un nouveau processus de fabrication, est très difficile. Le temps d’adoption est vraiment long, et c’est très cher. De nombreuses entreprises meurent avant même d'avoir pu arriver sur le marché », explique-t-il.
Après avoir parlé à des entreprises d'autres secteurs, Oberste et son équipe ont décidé de se concentrer sur les marchés de l'automobile et de la construction. Il dit:«Une fois que nous avons commencé à parler aux gens [dans l'automobile], nous avons réalisé qu'il y avait un très gros besoin non satisfait dans cet espace, en ce sens que les gens de l'automobile ont une demande pressante de réduction de poids, mais ils sont également sensibles au prix. . Ils nous ont dit que la plupart des procédés de fabrication de composites conventionnels disponibles n'étaient pas en mesure de fournir le volume dont ils avaient besoin aux coûts qu'ils voulaient. À partir de là, Oberste a entrepris de faire évoluer sa technologie pour en faire une solution habilitante pour la production de pièces composites en grand volume à faible coût.
Le résultat est le concept Rebar for Plastics de WEAV3D. À l'aide d'un processus de tissage et de consolidation automatisé, WEAV3D fabrique des structures en treillis composites thermoplastiques dimensionnellement ajustables conçues pour être facilement intégrées en tant que matériau de renforcement dans une pièce en plastique ou en béton par moulage par compression, surmoulage par injection ou d'autres processus courants à haut volume. Sur la base de modèles de simulation, Oberste affirme que cette approche permet la production de pièces automobiles avec des performances comparables à celles de la tôle d'acier ou d'aluminium, mais qui sont plus légères et 30 à 75 % moins chères à produire par rapport aux pièces composites formées par organosheet, pose automatisée de ruban ( ATL) ou des processus de drapage à la main.
Le processus WEAV3D
Le processus WEAV3D commence avec des rubans thermoplastiques unidirectionnels (UD) prêts à l'emploi. Oberste dit que le processus peut gérer n'importe quel type de thermoplastique et de fibre de renforcement :« Notre point idéal pour la plupart des travaux que nous avons effectués dans l'automobile et la construction se situe dans le polypropylène [PP], le polycarbonate [PC], le polyéthylène téréphtalate [PET] ou espace polyamide [PA]. Nous sommes également très agnostiques en termes de fibres de renforcement, bien que les fibres de verre et de carbone soient bien sûr les plus populaires. » Il dit que l'équipe a également effectué des travaux avec des rubans métalliques conducteurs et fait des recherches sur les rubans avec des fibres optiques intégrées.
La machine pilote à grande échelle de WEAV3D est standardisée pour traiter une bande de 25 millimètres de large ou de 1 pouce de large, bien qu'Oberste indique que la machine peut gérer des bandes aussi petites que 5 millimètres (0,2 pouce) de large avec l'utilisation d'adaptateurs, et plus larges bandes avec réoutillage. Sur la machine actuelle, des treillis peuvent être produits jusqu'à 1,5 mètre de large (60 pouces) et jusqu'à cinq couches d'épaisseur, à n'importe quelle longueur requise par l'application.
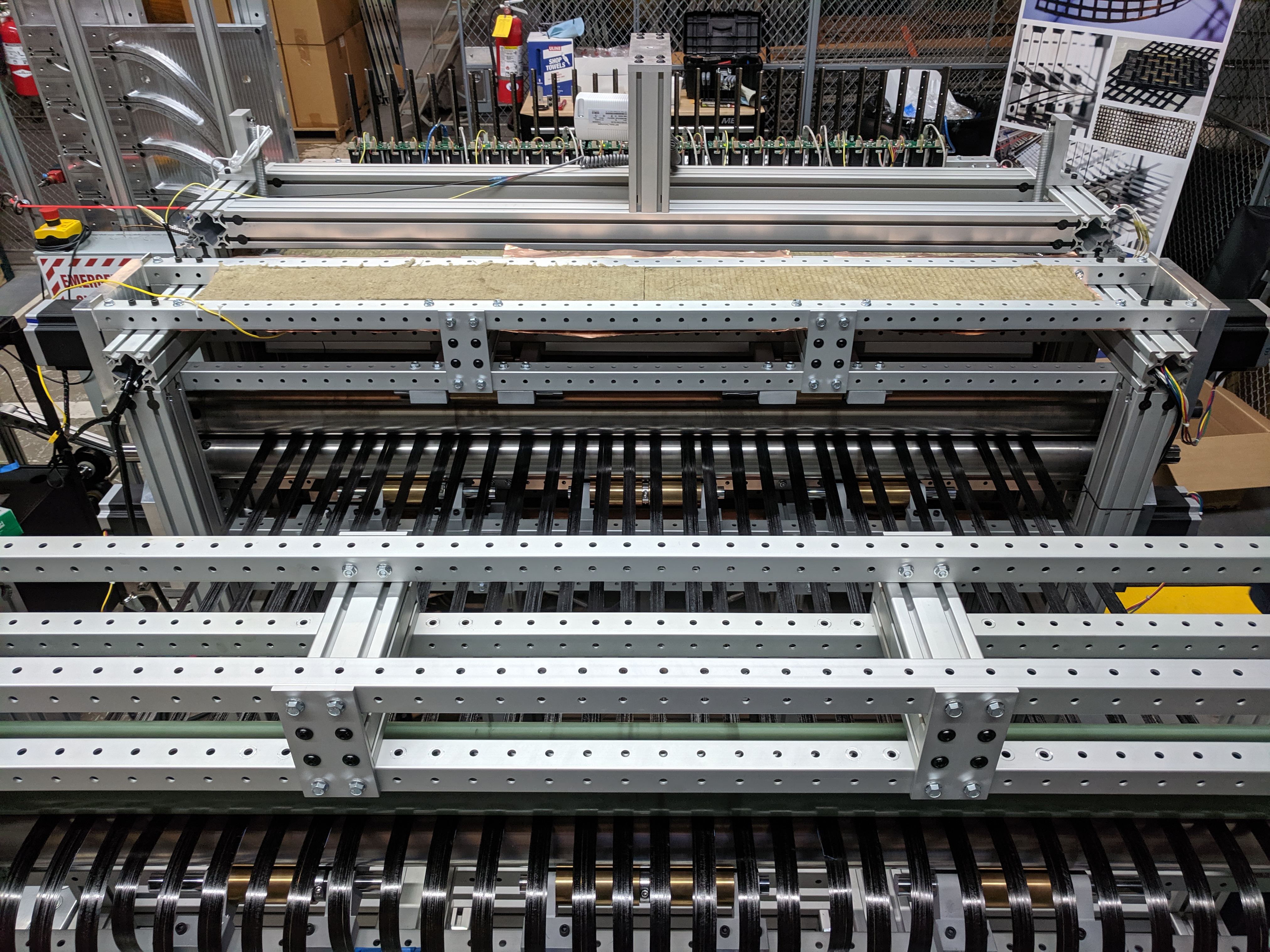
Le dépôt de brevet de la société en novembre 2017 décrit le système WEAV3D comme « une machine permettant de fabriquer en continu un composite tissé avec une géométrie de tissu interne contrôlable ». À partir de bobines chargées sur la machine, les bandes UD sont enfilées dans un ensemble de têtes de chaîne contrôlables indépendamment. Chaque tête contient plusieurs canaux de bande, formant une foule de chaîne, un espace entre les bandes de chaîne pour les bandes dans le sens de la trame à enfiler. Une pile de dispositifs d'insertion distribue des rubans unidirectionnels dans le sens de la trame à travers la foule de chaîne pour former un tissage composite. Le treillis tissé est ensuite tiré sous une source de lumière infrarouge (IR) puis à travers des rouleaux de compression pour consolider et lier les couches de rubans ensemble aux points d'entrelacement. Selon les exigences du client, la structure résultante est fournie sous forme de feuille plate ou de rouleau, ou WEAV3D propose des services supplémentaires de coupe et de préformage.
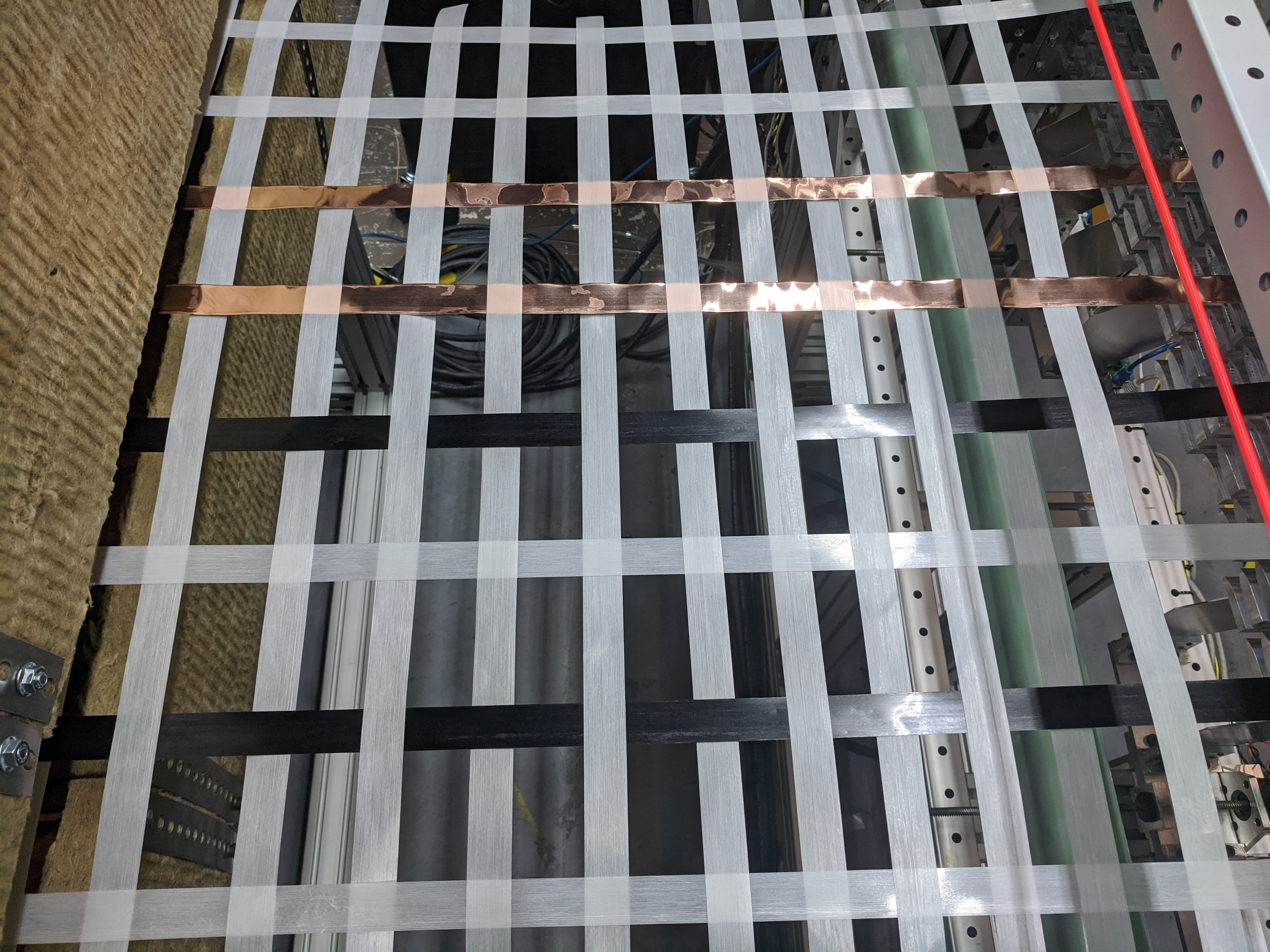
L'un des avantages les plus importants du processus de WEAV3D, selon Oberste, est le haut niveau d'accordabilité de la structure en treillis pour différentes applications. Cela comprend le mélange de différents matériaux à différents endroits, ainsi que l'ajustement de la densité, ou de la distance entre les bandes, de la structure en treillis. « Nous pouvons vraiment optimiser la structure du réseau pour les exigences du produit final tout en minimisant les coûts globaux. »
Une fois livrés au client, les treillis peuvent être intégrés dans des composants en béton polymère, ou moulés par compression, thermoformés ou surmoulés par injection pour former une pièce composite automobile finale. Le processus WEAV3D peut également s'adapter à différents niveaux de complexité. Oberste explique que pour des pièces relativement simples, « ce treillis peut être associé à un procédé de laminage puis thermoformé, tout comme une étape de coformage. Pour les pièces moyennement complexes, nous pouvons faire du coformage ou du préformage en moulage par compression, qu'il s'agisse de moulage par compression thermoplastique ou de moulage par compression SMC. Et puis pour les pièces très complexes, nous pouvons en fait préformer le treillis dans la forme qu'il doit avoir, le placer dans un outil, puis effectuer un surmoulage par injection sur cette pièce. »
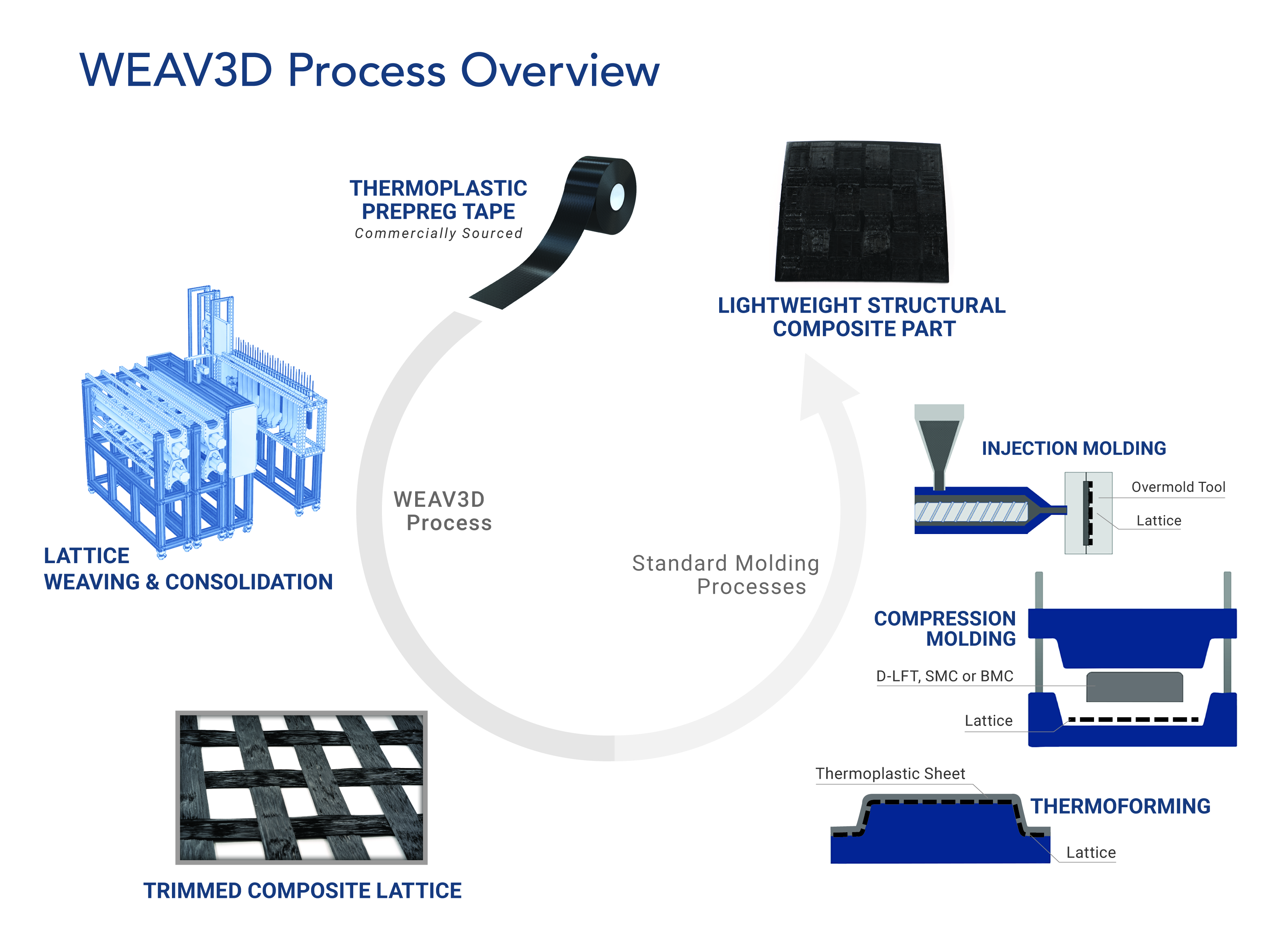
« Notre objectif principal dans l'écosystème des composites est de changer la donne pour la production à haut volume », ajoute-t-il. Le volume exact dépend de l'application, mais Oberste estime que pour les pièces en treillis dimensionnées pour le renforcement des panneaux de porte automobiles, les machines de WEAV3D peuvent produire entre 200 000 et 500 000 unités par an.
De plus, le produit WEAV3D a également présenté des propriétés mécaniques améliorées lors du renforcement d'une pièce composite ou plastique. « La combinaison d'un réseau WEAV3D avec des plastiques à fibres courtes ou des composites à fibres longues existants peut augmenter considérablement la résistance, la rigidité et la ténacité du produit obtenu », déclare Oberste, bien qu'il ajoute que la quantité d'augmentation varie considérablement selon les matériaux spécifiques utilisés et la conception de une partie particulière. « Dans certaines applications, ces performances accrues permettent de réduire considérablement l'épaisseur des pièces ou les nervures, ce qui se traduit par un poids réduit. »
Tranchées en béton armé :première application commerciale
Au cours des premières années, la start-up s'est concentrée sur la production d'une méthode de fabrication et de matériaux adaptés à l'industrie automobile en particulier, bien qu'Oberste ait des idées sur la façon dont cette technologie pourrait être utilisée dans les composants intérieurs de l'aérospatiale commerciale, les avions de défense sans pilote, le rail, le fret transports et applications maritimes.
Cependant, pour sa première application commerciale annoncée en novembre 2020, WEAV3D a commencé avec le marché de la construction, en utilisant des renforts en fibre de verre/PET pour un système de tranchées en béton polymère fabriqué par Oldcastle Infrastructure (Atlanta, Géorgie, États-Unis).
Le système de tranchées d'Oldcastle, utilisé pour acheminer les câbles de services publics dans les zones urbaines, les gares ou les usines industrielles, doit pouvoir supporter des charges de 16 000 livres provenant de véhicules passant dessus. Auparavant, la tranchée était renforcée par des cages en fil d'acier soudées sur mesure et encastrées dans le béton. Cependant, selon Oberste, ces cages en acier étaient à la fois coûteuses à fabriquer sur mesure et, comme Oldcastle fabrique des tranchées de plusieurs tailles différentes, les cages en acier n'étaient pas toujours aux dimensions correctes pour renforcer correctement les trous de drainage de la tranchée. « Avec notre processus, parce que nous pouvons vraiment optimiser le treillis pour les exigences de l'application, nous avons pu ajuster la géométrie du treillis - par exemple, pour nous assurer que nous avons ajouté un renforcement autour des trous de drainage au fond de la tranchée et un renforcement au extrémités de la tranchée afin qu'elle soit protégée contre les chocs lors de la manipulation », dit-il.
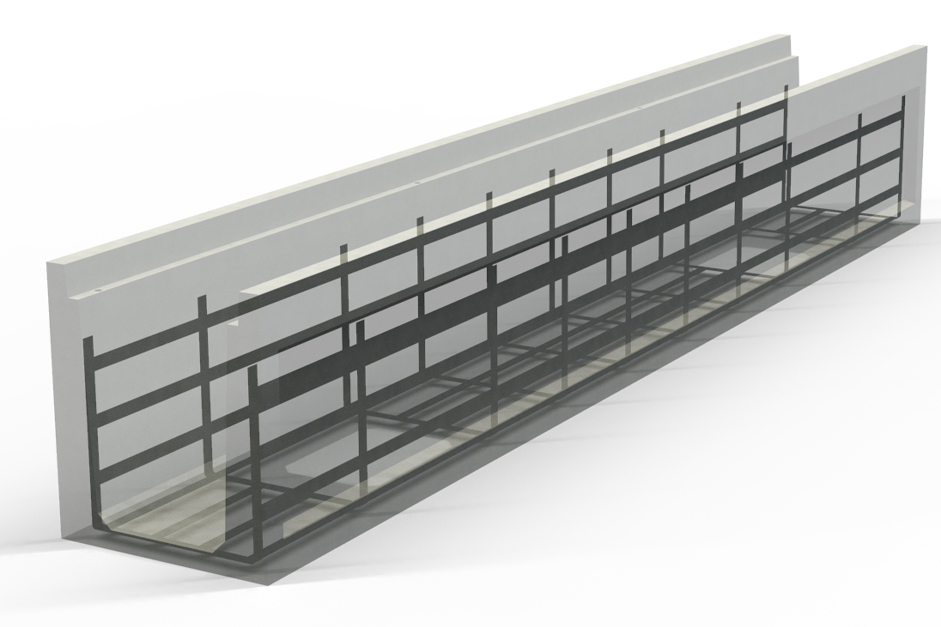
En outre, l'un des aspects les plus difficiles du projet, selon Oberste, était d'identifier un matériau de ruban thermoplastique qui pourrait former une liaison adhésive avec le béton polymère, plutôt que de s'appuyer uniquement sur une interface mécanique, comme c'est le cas avec la cage en acier. renforts. Le matériau polyéthylène téréphtalate glycol (PETG) sélectionné par WEAV3D forme une véritable interface adhésive entre les deux matériaux, ce qui facilite le transfert des contraintes et diminue le risque de fracture. "Même si une fracture se produit", ajoute-t-il, "cette fracture est beaucoup moins susceptible de se propager à travers la structure car elle doit surmonter cette interface adhésive."
WEAV3D produit les treillis conçus pour cette application sous la forme d'une préforme en U, qu'Oldcastle place ensuite dans un moule de coulée où du béton polymère est coulé dessus, suivi d'un durcissement et d'un démoulage pour produire la structure finale en béton armé.
Dans le domaine de la construction, WEAV3D envisage d'étendre ses réseaux à d'autres applications de béton polymère telles que les boîtiers et les couvercles. En octobre 2020, WEAV3D, dans le cadre d'une proposition conjointe avec l'Université Western Ontario et la société d'ingénierie structurelle Entuitive, a reçu une subvention du Conseil national de recherches en sciences et en génie du Canada pour mener des recherches évaluant l'utilisation des treillis de WEAV3D comme renforcement dans le ciment Portland traditionnel. à base de béton également. L'objectif est de développer des treillis pouvant être utilisés comme renforts pour les dalles et les façades des bâtiments non résidentiels, explique Oberste.
WEAV3D de nouvelle génération :vitesses automobiles
Une version de nouvelle génération de la machine WEAV3D, conçue pour répondre aux besoins de la fabrication automobile, est en cours de développement grâce au financement de la recherche de la NSF. Oberste dit qu'il sera probablement mis en ligne en 2022. Les améliorations du nouveau système visent à tripler la vitesse de production du système actuel, y compris le remplacement des rouleaux de chauffage et de compression IR par un soudage par ultrasons plus efficace.
Dans le même temps, Oberste et son équipe ont entamé des discussions avec des constructeurs de niveau 1 et des équipementiers américains et européens de l'industrie automobile sur l'utilisation des produits WEAV3D pour renforcer les panneaux en plastique, allant des composants intérieurs aux hayons des camionnettes. « L'un des objectifs est d'ajouter un treillis en tant que squelette structurel dans les composants en plastique moulé afin d'améliorer leur résistance et leur rigidité et de remplacer les supports et raidisseurs métalliques sur lesquels les concepteurs s'appuient actuellement », explique Oberste. WEAV3D travaille également sur des articles de démonstration de panneaux de carrosserie automobile et d'autres composants pour présenter les avantages du matériau.
Résine
- Portwell :le système 19" cible les applications de mur vidéo
- Système de surveillance à domicile/hôtel avec contrôles automatisés
- Composites hautes performances en Israël
- EconCore octroie une licence à Fynotej pour les applications automobiles NA et les avancées dans les thermoplastiques hautes performances (HPT)
- Solvay lance un ruban en fibre de carbone hautes performances pour les applications pétrolières et gazières offshore
- Système d'étalonnage pour le placement automatisé des fibres
- Lasers hautes performances de nouvelle génération
- Intégrateurs de systèmes d'emballage automatisés
- Système de tri des colis et des paquets automatisé par l'IA