Faire fondre et couler du métal
Du four de coulée au moule
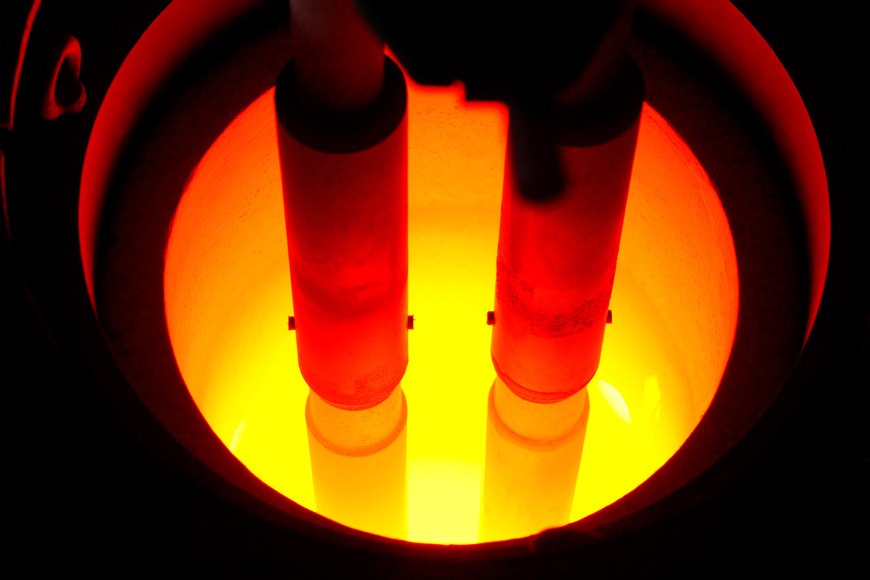
Les fonderies sont dramatiques. D'énormes fournaises, incandescentes de chaleur, transforment des morceaux de métal en liquides ardents qui coulent. Lorsqu'ils sont prêts, leur contenu est versé dans des louches en attente au milieu d'une pluie d'étincelles. Les travailleurs guident le flux de métal du four au moule derrière des écrans thermiques, se protégeant contre les dangers de la température et des matériaux. L'étage de la fonderie est l'endroit où le design devient réel, dans un processus extraordinaire qui crée des objets du quotidien. Les innovations dans la création et le maintien des températures requises pour différents alliages font partie de l'évolution de la métallurgie. Le travail de fonte et de coulage du métal ressemble à des scènes tirées des livres d'histoire, mais c'est là que se déroulent certaines des activités scientifiques les plus intéressantes.
La fabrication de métal coulé repose sur des fours qui peuvent devenir suffisamment chauds pour amener les métaux à l'état liquide. La première fusion de minerais dans l'histoire de l'humanité a été le plomb et l'étain :ces métaux mous peuvent être fondus à la chaleur du feu de cuisine. Pour créer des métaux plus solides, les métallurgistes avaient besoin de quelque chose de plus que la flamme du bois.
Haute chaleur et progrès humain
L'âge du bronze dépendait de la force du cuivre. Le cuivre a peut-être d'abord été fondu accidentellement dans un four à poterie, qui chauffe au moins 200°C de plus qu'un feu de camp. Le manque de trace écrite de cette époque rend difficile d'être sûr. À l'âge du bronze, des fours ressemblant à des fours étaient utilisés pour extraire divers composants élémentaires de la roche qui fondait à différentes températures, le cuivre étant le prix le plus élevé pour fabriquer du laiton et du bronze de qualité.
Il existe des preuves que les humains utilisaient du fer avant l'âge du fer. Cependant, ces objets étaient faits de fer travaillé qui était littéralement tombé du ciel - le fer météorique est sous une forme relativement pure par rapport au fer terrestre. Il pourrait être chauffé et travaillé tel qu'il a été trouvé. Le véritable âge du fer a commencé, cependant, lorsque les gens ont compris comment extraire le fer utile des minerais, ce qui nécessite une fusion à des états mous, ressemblant à de la tire, presque liquides ou liquides. Cette avancée s'est produite dans différentes parties du globe à des moments différents, mais a impliqué l'invention de fours à fleurs et une lente construction des connaissances sur la métallurgie des ferreux. Les fours Bloomery permettent au fer d'être suffisamment chaud pour être travaillé vers la pureté, plutôt que d'amener le métal à l'état fondu, mais ils ont contribué à la lente découverte de la chimie du fer. C'est une chose de faire fondre du fer :pour fabriquer un métal solide et utilisable, il faut un bon ajout de carbone, et les fours à fleurs étaient dépendants du carbone. Lorsque les fours devenaient suffisamment chauds pour faire fondre le fer, les métallurgistes devaient également développer leur compréhension des fondants, qui sont des additifs utilisés pour aider à purifier le métal final en empêchant la formation d'oxyde.
Les progrès apportés par la combinaison innovante du four et de la chimie se sont poursuivis tout au long de l'histoire humaine. L'avancée métallurgique a évidemment inauguré les âges du bronze et du fer en fonction de leur nom. La révolution industrielle nous a fait entrer dans l'âge de l'acier. Le moteur à combustion, les chemins de fer et les pratiques de construction modernes ne seraient pas possibles sans une avancée importante appelée le procédé Bessemer, qui fait barboter de l'oxygène à travers l'acier en fusion permettant des températures plus élevées et des temps de production plus rapides, permettant la production en série d'acier de qualité.
Fusion contre fusion
La fusion est le processus d'élimination d'un élément métallique des minerais extraits. La plupart des métaux se trouvent sous forme de veines dans les roches ou de parties d'autres éléments. La fusion est la première étape de l'extraction. La fusion est ce qui se fait avec des alliages métalliques ou des métaux purs. La ferraille est fondue, le minerai est fondu. La fonte brute est constituée de lingots de fer brut créés à partir de la fusion du minerai de fer.
Hauts-fourneaux
Les hauts fourneaux, qui sont de très hauts fourneaux injectés de gaz sous pression, sont utilisés pour la fusion. Les hauts fourneaux produisent principalement des lingots d'un alliage intermédiaire, comme la fonte brute. Ces lingots sont ensuite expédiés vers des fonderies impliquées dans la fabrication.
Les fonderies de fabrication prennent des alliages et des additifs et les font fondre pour fabriquer des nuances spécifiques de métal coulé dans d'autres types de fours de fusion.
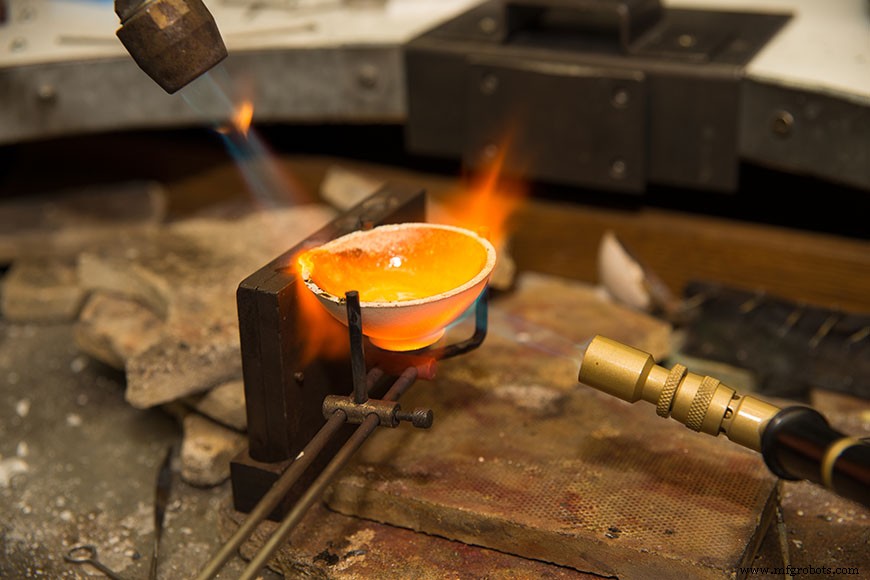
Types de fours de fusion de fonderie
Traditionnellement, les fours à cubilot et à creuset étaient les moyens les plus courants de forger des métaux pour la coulée; De nos jours, les fours à arc électrique et à induction sont courants.
Fours à creuset
Les fours à creuset sont la forme la plus basique de four à métaux. Un creuset est un récipient fait d'un matériau qui peut supporter des températures incroyablement élevées, souvent en céramique ou en un autre matériau réfractaire. Il est placé dans la source de chaleur comme un pot pourrait s'asseoir dans un feu. Le creuset est rempli, ou chargé, de métal et d'additifs. À l'ère moderne, les fours à creuset sont encore utilisés par les bijoutiers, les amateurs de basse-cour, certaines fonderies non ferreuses et les fonderies effectuant de très petits travaux par lots. Les creusets peuvent aller d'une très petite tasse où les métaux sont fondus au chalumeau, comme cela pourrait être fait chez un bijoutier, à de grands récipients contenant 50 livres de matériau. Les creusets plus grands sont souvent placés à l'intérieur d'un four semblable à un four et peuvent être soulevés pour être versés ou avoir du matériau versé par le haut.
Cubilots
Les cubilots sont longs, en forme de cheminée et remplis de coke de charbon et d'autres additifs. Le combustible à l'intérieur de la coupole est allumé et lorsque le four est suffisamment chaud, la fonte brute et la ferraille sont ajoutées directement. Le processus de fusion du fer autour du coke et des additifs ajoute du carbone et d'autres éléments et produit différentes qualités de fer et d'acier. Les cubilots ne sont généralement plus utilisés dans la production, car les méthodes à arc électrique et à induction sont plus efficaces pour produire la chaleur nécessaire. Cependant, il y a des endroits où la tradition maintient les cubilots en marche, comme dans cette vidéo de Da Shu Hua, où les fondeurs chinois jettent du fer en fusion contre un mur pour créer des étincelles spectaculaires pour accueillir la nouvelle année.
Fours à arc électrique
(EAF) est entré en service à la fin des années 1800. Les électrodes font passer le courant électrique à travers le métal à l'intérieur du four, ce qui est plus efficace que l'ajout de chaleur externe lors de la fusion de volumes élevés en une seule fois. Un grand EAF utilisé dans la production d'acier peut contenir jusqu'à 400 tonnes. Une «charge» de cet acier est souvent constituée de fer lourd comme des dalles et des poutres, de ferraille déchiquetée provenant de voitures et d'autres recyclages, et de lingots de fonte provenant d'une fonderie.
Une fois le réservoir rempli, des électrodes sont placées dans le métal et un arc électrique passe entre elles. Lorsque le métal commence à fondre, les électrodes peuvent être poussées plus loin dans le mélange ou séparées pour créer un arc plus grand. De la chaleur et de l'oxygène peuvent être ajoutés pour accélérer le processus. Au fur et à mesure que le métal en fusion commence à se former, la tension peut être augmentée, car les scories créées sur le métal agissent comme une couverture protectrice pour le toit et les autres composants de l'EAF.
Quand tout est fondu, tout le four est basculé, pour décharger le métal liquide dans une poche en dessous. Parfois, les poches elles-mêmes peuvent être des fours EAF plus petits, chargés de maintenir le métal chaud avant de le couler.
Fours à induction
travailler avec des champs magnétiques plutôt qu'avec des arcs électriques. Le métal est chargé dans un creuset entouré d'un puissant électroaimant en cuivre bobiné. Lorsque le four à induction est allumé, la bobine crée un champ magnétique à inversion rapide par l'introduction d'un courant alternatif. Au fur et à mesure que le métal fond, l'électroaimant crée des tourbillons dans le liquide qui agitent automatiquement le matériau. La chaleur dans un four à induction est créée par l'excitation des molécules dans le fer lui-même, ce qui signifie que tout ce qui entre dans le creuset est exactement ce qui en sort :il n'y a pas d'ajout d'oxygène ou d'autres gaz dans le système. Cela signifie moins de variables à contrôler lors de la fusion, mais cela signifie également qu'un four à induction ne peut pas être utilisé pour affiner l'acier. Ce qui entre, sort. Comme un four EAF, les fours à induction déchargent souvent en basculant dans les poches en dessous.
Les fours à induction sont très courants et sont simples à utiliser lorsqu'ils reçoivent des intrants de haute qualité. Les modèles courants peuvent produire 65 tonnes d'acier à chaque charge.
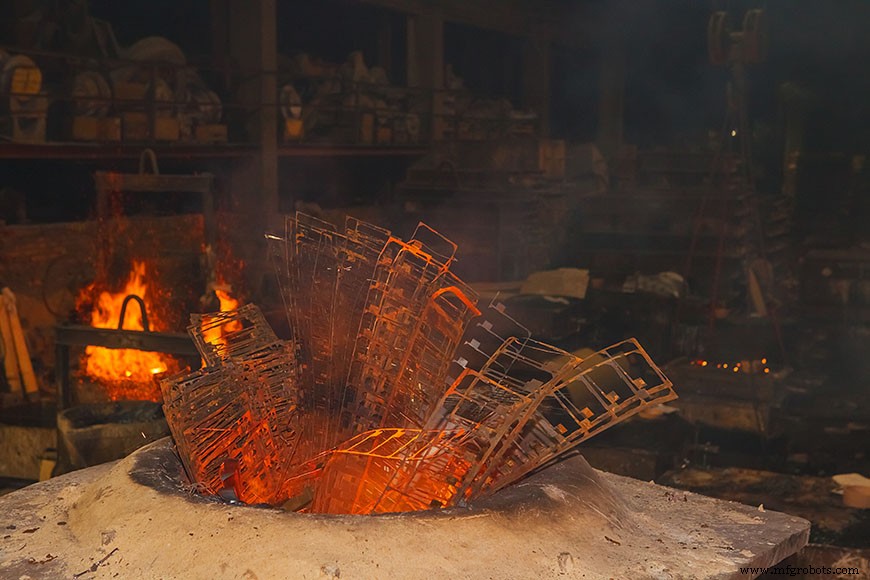
Tous les fours de la fonderie sont confrontés à un ennemi mortel :la vapeur. L'eau, même en petite quantité, peut provoquer des éclaboussures ou des explosions. Par conséquent, tous les ferrailles et ferroalliages, ainsi que tous les outils utilisés dans la production, doivent être secs avant utilisation. La ferraille ne doit pas avoir de zones fermées dans lesquelles de l'eau ou de la vapeur peuvent avoir été emprisonnées. Même les outils utilisés par les fondeurs doivent être exempts de condensation ou d'humidité. De nombreuses fonderies disposent d'un four de séchage pour s'assurer que la ferraille et les outils sont parfaitement secs avant que quoi que ce soit ne touche le four de coulée.
Louches de coulée
Une fois le métal fondu, il doit être introduit dans le moule. Dans les petites fonderies, tout cela peut se produire en une seule étape :un creuset basculant ou amovible peut transporter le métal du four vers le sable. Cependant, cela n'est pas pratique lorsqu'un four contient plusieurs tonnes de métal. Généralement, dans la fabrication ferreuse, les poches transfèrent de plus petites portions de la masse fondue du four principal.
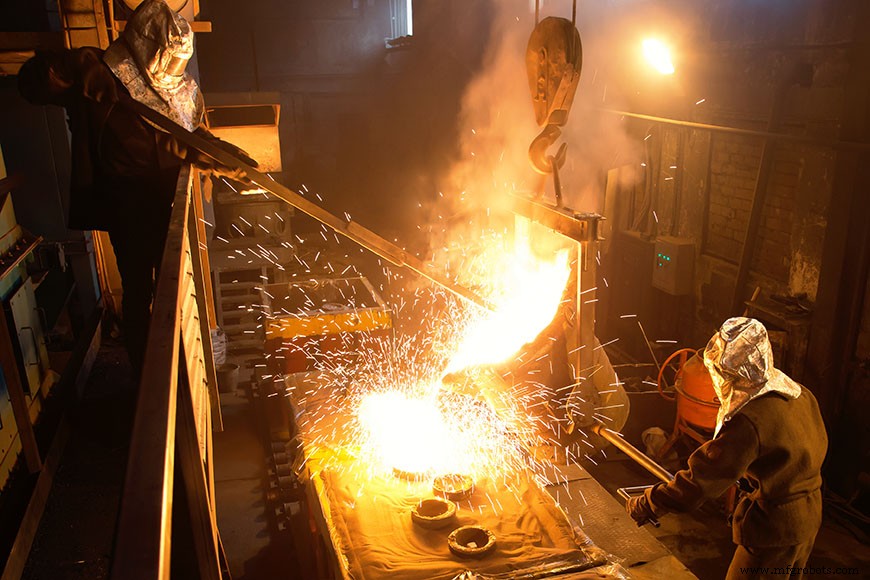
Dans ces systèmes, une poche peut amener le métal directement dans le moule. Cependant, une poche de transfert peut amener le liquide vers un réservoir de rétention ou un four secondaire. Les louches de traitement sont un autre type disponible, utilisées pour briser la fonte en portions, comme un boulanger pourrait séparer une pâte de base pour l'utiliser comme base pour d'autres recettes. Par exemple, la fonte liquide peut avoir des agents ajoutés dans la poche de traitement pour donner au carbone une forme sphérique plutôt qu'en flocons, créant ainsi un métal plus malléable appelé fonte ductile.
Les louches peuvent être très petites et soulevées par les ouvriers de la fonderie ou elles peuvent contenir plusieurs tonnes de métal et nécessiter un support mécanique. Les plus grandes poches sont déplacées dans une fonderie par un chariot-poche ou par un pont roulant ou un système de chenilles.
Les louches de toutes sortes sont conçues pour protéger le travailleur des éclaboussures, des flammes ou des étincelles lors du versement. Certaines louches se déversent sur la lèvre supérieure, ou un bec verseur, et doivent être inclinées :elles ont souvent des engrenages qui permettent au fondeur de contrôler soigneusement la vitesse de coulée. D'autres louches ont leur bec verseur au fond du seau et le versement est contrôlé en retirant et en remplaçant un bouchon.
Mélange d'alliages
Les alliages métalliques sont constitués de mélanges d'éléments qui sont normalisés par une formule qui précise les pourcentages de chaque type ainsi que les étapes de sa fabrication. Les fours de fusion et les poches de traitement d'une fonderie sont l'endroit où ces types d'alliages sont créés pour les moulages.
Les fonderies se spécialisent souvent soit dans les alliages ferreux, qui contiennent du fer, soit dans des alliages non ferreux spécifiques, comme les métaux précieux, les alliages à base de cuivre ou d'aluminium.
Les alliages ferreux se trient en fer et en acier. Les alliages de fonte comprennent la fonte grise, qui comprend du silicium, et la fonte ductile, qui a un type de carbone sphérique. Les nuances d'acier moulé sont définies par les pourcentages de carbone et d'autres additifs dans le mélange. L'acier inoxydable est un acier qui contient du chrome, pour aider à prévenir la rouille par passivation.
Les alliages non ferreux incluent tous les autres métaux, il n'est donc pas surprenant qu'il y ait une spécialisation supplémentaire dans les fonderies non ferreuses. Certains endroits sont spécialisés dans le zinc, d'autres dans l'aluminium ; d'autres travaillent principalement avec des alliages à base de cuivre comme le laiton et le bronze. Cependant, il y a croisement. Si une fonderie particulière travaille à la fois avec du bronze et de l'aluminium, par exemple, elle se spécialisera probablement dans certaines nuances de chacun.
Quels que soient les alliages avec lesquels une fonderie travaille, le principe de fabrication de métal en fusion et de coulée dans des vides pour le façonner est le même. Une idée devient réalité au moment où le métal coule dans un moule.
Previous Post:CoreMakingMetal Casting ProcessNext Post:Shakeout and Cleaning
Métal
- Coulage au sable :processus et caractéristiques | Secteurs | Métallurgie
- Qu'est-ce qu'un métal ferreux ? – Un guide complet
- Chrome métal :éléments, propriétés et utilisations
- Qu'est-ce que la fonte ? - Définition, propriétés et utilisations
- Qu'est-ce que le traitement thermique ? - Processus et méthodes
- Qu'est-ce que la tôle? - Définition, types et utilisations
- Qu'est-ce que la coulée de métal ? - Définition, types et processus
- Qu'est-ce que la Corrosion ? - Définition et prévention
- Comprendre les alliages métalliques et la limite d'élasticité