La fibre de carbone et la fabrication additive améliorent les performances des chaussures à crampons Pleko
Le coureur de demi-fond vénitien Miro Buroni a créé et développé Pleko, une chaussure de piste d'athlétisme personnalisée (ou chaussure à crampons) avec le soutien du fabricant italien de vêtements de sport et de chaussures Diadora (Vénétie, Italie) pour l'analyse historique et la technologie CRP (Modène, Italie) pour la fabrication de la semelle extérieure, de la semelle intermédiaire et du bord-côte à l'aide de son Windform Matériau composite SP chargé de fibres de carbone et procédé de frittage laser sélectif par fusion sur lit de poudre (PBF).
Un scan 3D du pied d'un athlète, suivi d'une analyse biomécanique de l'acte de courir et de marcher grâce au scan 3D du pied, a permis aux entreprises de modéliser la chaussure en fonction des besoins d'un individu en termes de structure du pied et de performance athlétique. "De plus, le scan et l'analyse biomécanique nous ont permis de comprendre le meilleur placement du "système de traction" sous la semelle extérieure, les "pins" ” dit Miro Buroni.
Le processus de fabrication additive a été choisi pour construire la structure de support de Pleko, ainsi que la gamme de matériaux composites Windform SP Top-Line de CRP Technology, qui ont fourni à Buroni de solides caractéristiques mécaniques, telles que la résistance à la déformation et la flexibilité, les « bonnes caractéristiques pour l'athlétisme chaussures de piste."
« Windform SP », explique Buroni, « garantit une excellente résistance même dans des épaisseurs très minces ; cette caractéristique m'a permis de créer des chaussures à crampons avec un enveloppement parfait du pied qui facilite une augmentation du confort et des performances améliorées. »
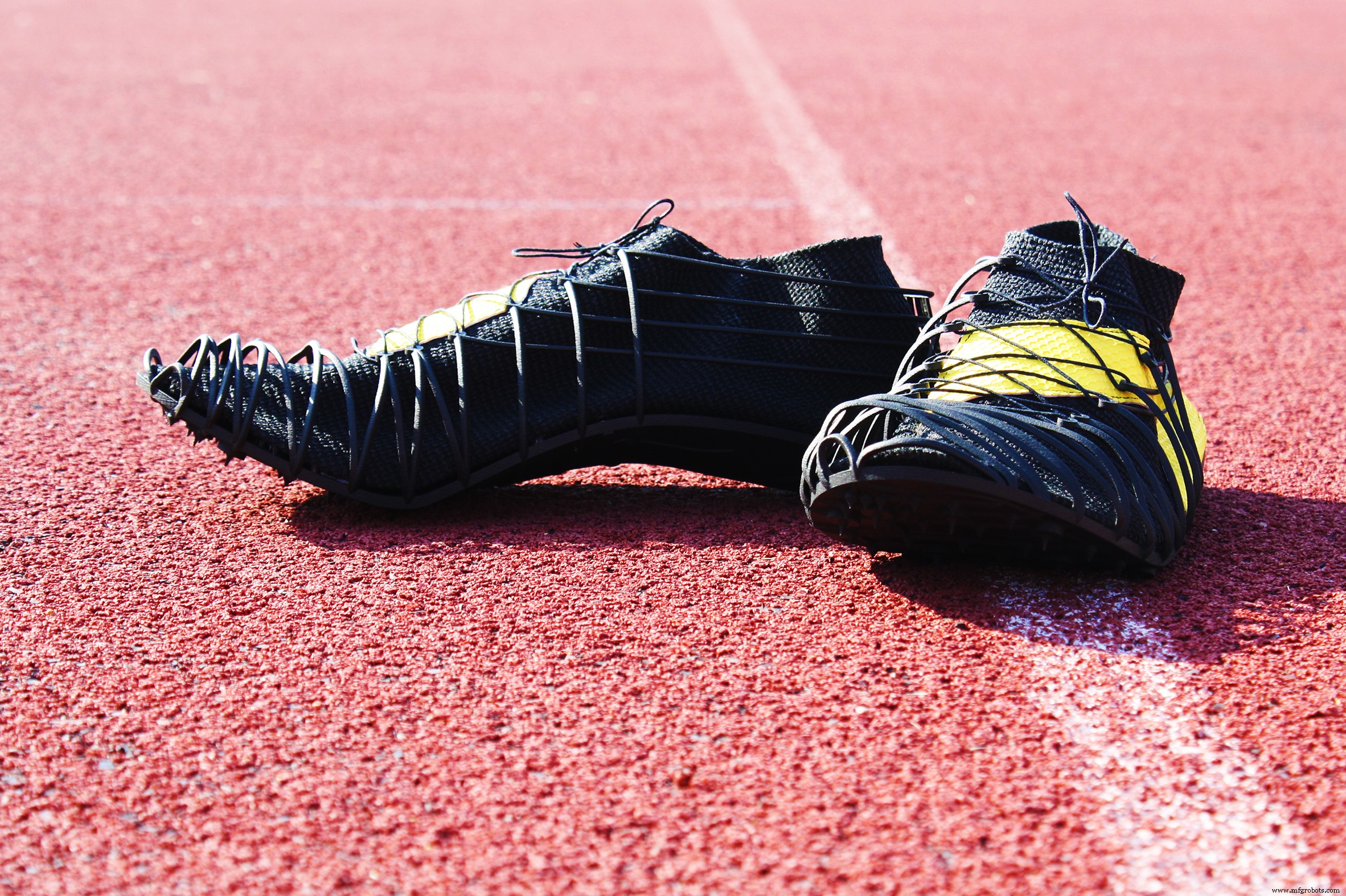
CFRP a fabriqué la semelle extérieure, la semelle intermédiaire, les nervures et les broches de Pleko en une seule unité. Les nervures, note Buroni, proviennent de sous la semelle extérieure, en correspondance avec les lignes d'effort maximal pendant la course sur piste. Ils sont chargés de transporter l'énergie cinétique libérée par le mouvement biomécanique pendant la course sur piste, et d'empêcher sa dispersion. Grâce à eux, la structure Windform SP est également capable d'embrasser le pied de l'athlète « comme une cage » pour faciliter l'amélioration de la technique de course.
« Grâce aux picots sous la semelle extérieure, la « cage » de Windform SP permet à l'athlète de développer le plus de force possible, sans perdre d'énergie. J'ai positionné les épingles les plus profondes dans les points de pression supérieure des pieds contre le sol. J'ai également mis des crampons plus petits dans d'autres parties de la semelle extérieure :ces crampons sont également essentiels à la stabilité des chaussures de course », explique Buroni.
Dans l'ensemble, Buroni se dit satisfait des résultats obtenus. "Les technologies de conception et de fabrication, combinées au Windform SP et à ses caractéristiques mécaniques, ont rendu les chaussures de piste Pleko très innovantes, amenant l'ensemble du projet au plus haut niveau de personnalisation et de spécialisation", conclut-il.
fibre
- Comparaison des méthodes de fabrication courantes de pièces en fibre de carbone
- 5 produits surprenants en fibre de carbone
- La fibre de carbone peut-elle être recyclée ?
- Avantages des chaussures en fibre de carbone
- La fibre de carbone dans les applications aérospatiales
- La fibre de carbone dans les applications automobiles
- Comment est fabriquée la fibre de carbone ?
- La fibre de carbone Split Tow améliore les performances du SMC
- Le ruban UD en fibre de carbone/polypropylène offre une flexibilité de fabrication