Le système de découpe préimprégné réduit les déchets et accélère l'assemblage du jet d'affaires suisse
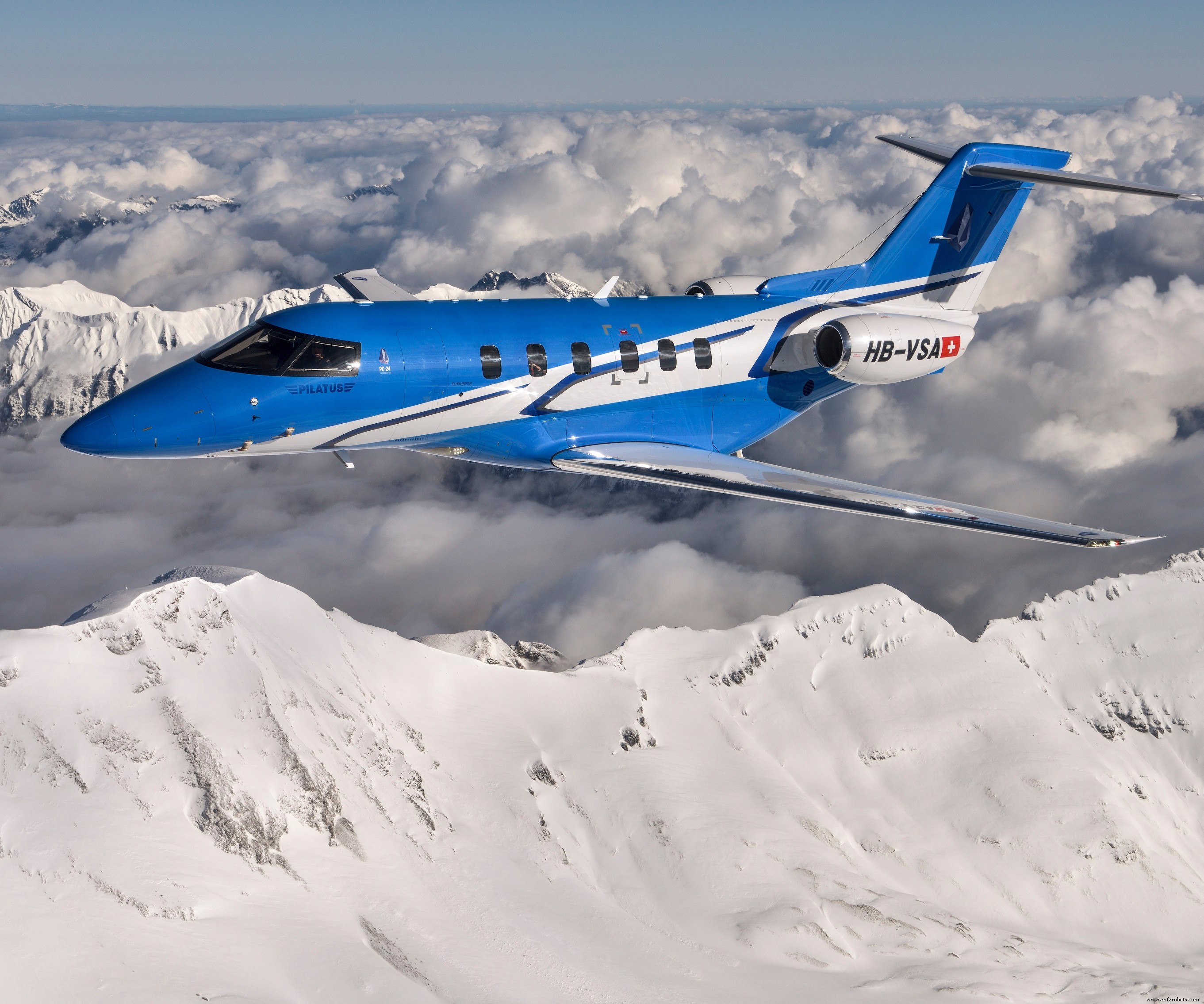
Source | Zünd
Grâce aux composants en fibre de carbone et de verre, le PC-24 L'avion d'affaires, fabriqué par Pilatus Aircraft AG (Stans, Suisse), affiche un poids de base de seulement 5,3 tonnes (moins de 12 000 livres), ce qui lui permet de décoller et d'atterrir sur des pistes courtes, non pavées ou en gravier habituellement réservées aux avions à turbopropulseurs. En fait, le PC-24 est capable de décoller sur une piste aussi courte que 890 mètres (2 920 pieds) et ne nécessite que 720 mètres (2 362,2 pieds) pour atterrir.
Pilatus a commencé à utiliser des pièces en fibre de carbone dès le début de son histoire de fabrication d'avions, en commençant par ses premiers composants en plastique renforcé de fibre de carbone (PRFC) et en plastique renforcé de fibre de verre (PRF) pour le PC-6 Avion universel en métal de Porter. Les quelques composants composites sur le PC-6 , qui a décollé pour la première fois en 1959 et a connu une production d'environ 500 avions avant d'être remplacé par son successeur le PC-12 , ont été mis en place à la main. PC-6 l'assemblage nécessitait donc une main-d'œuvre expérimentée et des tolérances élevées pour les pièces.
En revanche, le dernier type d'avion de la société, le PC-24 , se compose de nombreuses pièces, dont beaucoup sont fraisées avec des tolérances de la plage Mμ. Le PC-24 utilise des composites principalement pour les revêtements intérieurs et extérieurs. Les carters du moteur et les extrémités des ailes sont également en fibre de carbone, ainsi que les trappes de train d'atterrissage, les conduits d'air, divers tuyaux, couvercles et bords de fuite sur les ailes.
Non seulement le PC-24 inclure plus de composants composites que le PC-6 fait en 1959, mais l'assemblage est beaucoup plus rapide maintenant, rendu possible, dit Pilatus, grâce aux progrès des technologies de production. La clé de ceci est la réduction permanente des coûts, l'optimisation de la productivité et la capacité de mettre en œuvre des technologies de production modernes.
Les systèmes de découpe numériques de préimprégnés font partie de cette tendance. Pilatus fait confiance aux systèmes de coupe Zünd (Altstätten, Suisse) depuis des années et a ajouté en 2019 un système de coupe préimprégné Zünd G3 L-2500. Le système G3 monocouche coupe les matériaux pour les composants respectifs dans un processus largement automatisé, puis étiquette les pièces coupées avec un module à jet d'encre intégré.
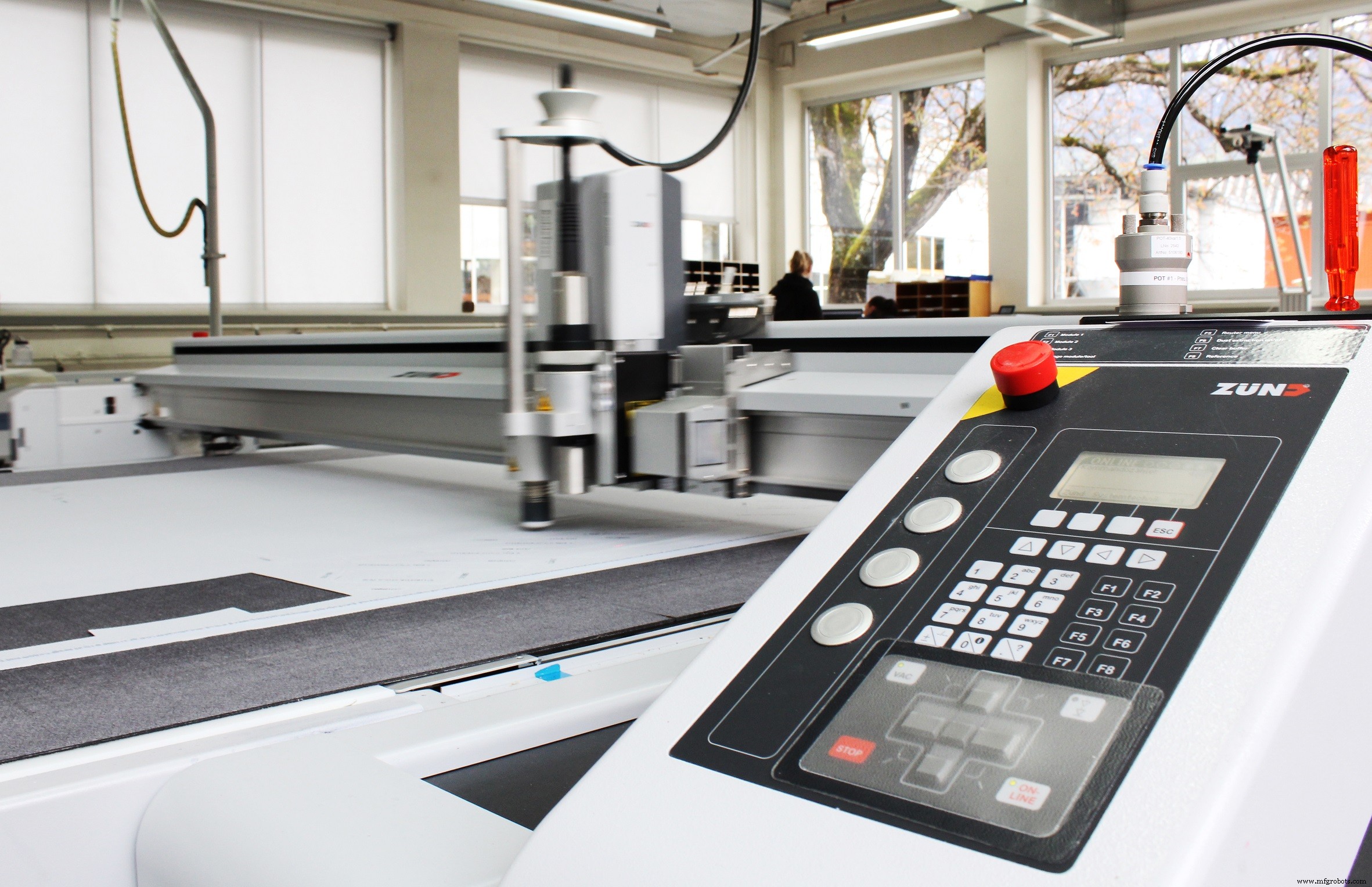
Source | Zünd
Pilatus traite environ cinq rouleaux de préimprégné par jour (environ 90 mètres carrés), soit environ 90 000 mètres carrés par an, le taux de consommation augmentant régulièrement à mesure que de plus en plus de composants CFRP et GFRP sont utilisés dans les avions de l'entreprise. Pilatus fait confiance à la découpe numérique Zünd depuis plus de 15 ans, en commençant par une découpeuse de la série PN. La demande croissante de composants en fibre de carbone a commencé à dépasser la capacité, ce qui a conduit à l'ajout d'un Zünd G3 L-2500 en 2019. Une fois la découpe terminée, les pièces sont assemblées et mises en chambre froide jusqu'à un traitement ultérieur. Les structures composites Pilatus peuvent comprendre jusqu'à 350 plis de préimprégné.
Un autre facteur du succès de Pilatus a été l'accent mis sur l'augmentation de la productivité. Selon Patrick Rohrer, chef de projet de l'approvisionnement des systèmes chez Pilatus, « Lorsqu'il s'agit de matériaux coûteux tels que la fibre de carbone ou de verre, l'efficacité et l'optimisation des matériaux sont toujours une préoccupation. Nous nous efforçons constamment d'augmenter l'utilisation et de réduire ainsi les déchets, d'autant plus que nous avons encore peu d'options de recyclage. »
L'entreprise affirme avoir réduit les taux de déchets de 30 % à 20 %, et elle cite les fonctionnalités d'imbrication efficaces du logiciel Zünd's Cut Center - ZCC comme un facteur important de ce succès. Les différents plis d'une pièce sont imbriqués statiquement, ce qui signifie que les plis individuels d'une pièce sont imbriqués dans la quantité demandée selon la commande . L'imbrication dynamique, c'est-à-dire lorsque les couches individuelles de pièces de plusieurs commandes sont imbriquées et combinées dans un seul fichier de coupe, peut également être utilisée chaque fois que cela est logique. Cela, dit Zünd, augmente encore le degré d'utilisation de la matière première.
fibre
- Comment fonctionne la découpe au jet d'eau ?
- 5 avantages de la découpe au jet d'eau
- Découpe au jet d'eau et au laser :quelle est la différence ?
- Comment optimiser efficacement la machine de découpe au jet d'eau ?
- Que faut-il considérer avant d'acheter une machine de découpe au jet d'eau abrasive ?
- La solution réduit les éruptions système pour Solvay
- La fiabilité réduit les pertes de temps, de talents et de ressources
- Usinage et découpe au jet d'eau abrasif
- L'automatisation de votre système de découpe laser est-elle adaptée à votre application ?