Électronique grand public :capots composites hybrides
SABIC a démontré dans une étude récente qu'une couverture d'un millimètre d'épaisseur pouvait répondre à toutes les spécifications de performances pertinentes de l'industrie pour les ordinateurs portables ou les tablettes très minces. Source, toutes les images | SABIC
L'électronique grand public est un marché dynamique avec des temps de cycle assez courts entre les générations de produits. À partir de leurs smartphones, montres intelligentes, tablettes et ordinateurs portables/ordinateurs portables, les consommateurs veulent des vitesses de fonctionnement plus rapides, des batteries plus durables, une plus grande durabilité et plus de fonctionnalités à un coût et un poids inférieurs. Pour répondre à la demande des consommateurs, les équipementiers demandent aux fournisseurs des matériaux offrant une esthétique et une liberté de conception élevées, une excellente résistance aux chocs et une rigidité élevée - ce qui implique la qualité sur ce marché - avec un faible poids et des sections de paroi minces. Ils veulent également des méthodes de traitement rentables et hautement reproductibles qui répondent à la demande de production mondiale de dizaines de millions d'unités par an. Ces pressions ont poussé le marché d'abord vers les métaux légers pour les couvercles/boîtiers et cadres, et le poussent maintenant vers des solutions en métal/composite et entièrement composites.
Une étude de faisabilité menée par SABIC (Bergen op Zoom, Pays-Bas) a impliqué l'utilisation de deux types de composites thermoplastiques pour produire une couverture pour ordinateur portable/tablette d'un millimètre d'épaisseur. L'étude a montré que la conception composite thermoplastique hybride pourrait être une solution viable pour le marché exigeant de l'électronique grand public.
Cas de test
Depuis 2012, SABIC a réalisé une série d'investissements pour développer ses propres rubans composites thermoplastiques renforcés de fibres unidirectionnelles (UD) (voir « Evoluer vers des renforts en fibres continues »), ce qui a étendu la compétence de base de l'entreprise en injection de fibres courtes et en fibres longues. matériaux thermoplastiques à fibres (LFT) et a permis à SABIC de se développer dans des composites thermoplastiques plus performants. En 2015, la société a acheté une participation majoritaire dans le fabricant de rubans Fiber Reinforced Thermoplastics BV (FRT, Lelystad, Pays-Bas) et en 2017, elle s'est associée et est devenue un investisseur minoritaire dans Airborne (La Haye, Pays-Bas), un fabricant de machines et développeur de traitement composite. lignes.
Comme SABIC et Airborne ont conçu et développé une technologie pour produire rapidement et à moindre coût des laminés à base de ruban thermoplastique de haute qualité en forme de filet pour les marchés à volume vraiment élevé (voir «Fabrication de composites thermoplastiques à grande vitesse et à haut débit»), l'équipe a commencé à chercher un cas de test. Ce démonstrateur serait un outil marketing important pour prouver les concepts de conception de stratifiés composites thermoplastiques produits à partir de rubans composites surmoulés avec des composés discontinus renforcés de fibres. Il serait également important de tester les outils d'ingénierie prédictive que l'équipe a développés pour les deux technologies des matériaux et de présenter le processus de fabrication à grande vitesse évoluant aux Pays-Bas.
« Nous avons décidé de nous spécialiser dans les applications électroniques grand public », explique Gino Francato, leader mondial des composites de SABIC. « Ce marché est très intéressant car il y a une réelle ambition de se tourner vers des matériaux légers pour rendre nos téléphones portables et ordinateurs portables plus légers et plus fins. Et comme ils en fabriquent des millions et des millions, nous avons décidé de relever le défi que proposait ce marché.
« Nous avons décidé de commencer par quelque chose de relativement complexe, mais pas trop complexe », explique Scott Davis, scientifique du personnel de SABIC et technologie d'application mondiale. Le capot supérieur d'un ordinateur portable très fin ou même d'une tablette – que l'équipe espérait pouvoir éventuellement traduire en composants de smartphone – semblait un bon point de départ. « Nous travaillions avec une géométrie globale simple, un rectangle, qui devait toujours conserver une haute esthétique et offrir beaucoup de complexité sur sa face B, y compris les fonctionnalités de fixation », poursuit Davis. « Nous devions garder le couvercle très mince, tout en répondant aux exigences de déflexion difficiles courantes dans l'industrie. Et, bien sûr, nous devions livrer un produit très cohérent via un nouveau processus de fabrication complexe. »
Comme ils ne travaillaient pas avec une conception client réelle et ne créaient que la housse de protection d'un écran, ils ont utilisé une géométrie générique. En fait, note Davis, lorsqu'ils ont commencé à découper des outils d'injection pour le développement interne, ils ne savaient même pas s'ils fabriqueraient une couverture pour tablette ou ordinateur portable, la couverture a donc été conçue pour fonctionner pour l'un ou l'autre. « Il y avait de nombreux défis à relever pour préparer une solution composite pour une production en grand volume », ajoute Davis. « En fait, il se passait beaucoup de choses simultanément – le développement de bandes, le développement de stratifiés et le développement de processus – et nous ne pouvions pas attendre que toutes ces choses soient finalisées pour commencer notre outillage, c'est ainsi que nous nous sommes retrouvés avec cette conception. » Une fois la conception de base terminée, l'équipe s'est concentrée sur d'autres détails, tels que le meilleur moyen de réaliser une barrière, les types de chevauchements nécessaires entre l'insert stratifié et le composé de surmoulage, comment gérer le placement automatisé à l'intérieur de l'outil, comment gérer le coefficient de ( linéaire) discordance de dilatation thermique (CLTE ou CTE) entre les deux composites et comment créer une pièce facilement reproductible.
Répondre à des exigences exigeantes
L'objectif était de développer un revêtement supérieur d'un millimètre d'épaisseur offrant une rigidité élevée et satisfaisant à toutes les exigences de performance et d'esthétique, en particulier le test de déviation du point central appliqué régulièrement sur les housses d'ordinateurs portables pour évaluer les charges nécessaires pour endommager l'écran sous-jacent. Les exigences de charge/déflexion varient selon l'OEM, l'appareil et le modèle, mais généralement pas plus de 3 à 5 millimètres de déflexion sont autorisés sous 40 à 120 Newtons de pression - une situation qui simule les charges exercées par un doigt ou un coude enfoncé dans le couvercle comme un utilisateur humain se lève. Dans de nombreuses industries, la stratégie pour réussir de tels tests consisterait à augmenter l'épaisseur de la section, mais ce marché valorise les conceptions plus minces qui libèrent de l'espace pour des batteries plus grandes et d'autres composants sans augmenter la taille ou le poids de l'appareil. Par conséquent, l'équipe a dû utiliser une stratégie de conception différente pour éviter d'endommager l'écran, à savoir la sélection de matériaux plus rigides (via un insert stratifié) et l'utilisation de la géométrie (par exemple, des nervures via un surmoulage par injection). Mais, d'abord, ils devaient spécifier les matériaux.
L'un de ces matériaux, le polycarbonate (PC), est déjà largement utilisé dans cette industrie pour les couvercles et autres composants, en raison de son excellente esthétique et de sa haute résistance aux chocs. Les plus grandes faiblesses du polymère sont la résistance chimique et les rayures de surface, mais le revêtement, la peinture ou les combinaisons des deux appliqués à la plupart des revêtements surmontent généralement ces problèmes potentiels.
« Parce que les ordinateurs ultralégers sont si minces, l'espace de l'emballage à l'intérieur est vraiment précieux, donc les déflexions et la mécanique deviennent vraiment critiques », souligne Francato. « Alors que vous voudriez utiliser du verre [renforcement] du point de vue des coûts, nous avons dû utiliser du carbone [fibre] pour obtenir la rigidité dont nous avions besoin. » En conséquence, tous les stratifiés à base de ruban évalués étaient des variantes de polycarbonate renforcé de fibres de carbone - des qualités alors en cours de développement avec la filiale FRT de SABIC.
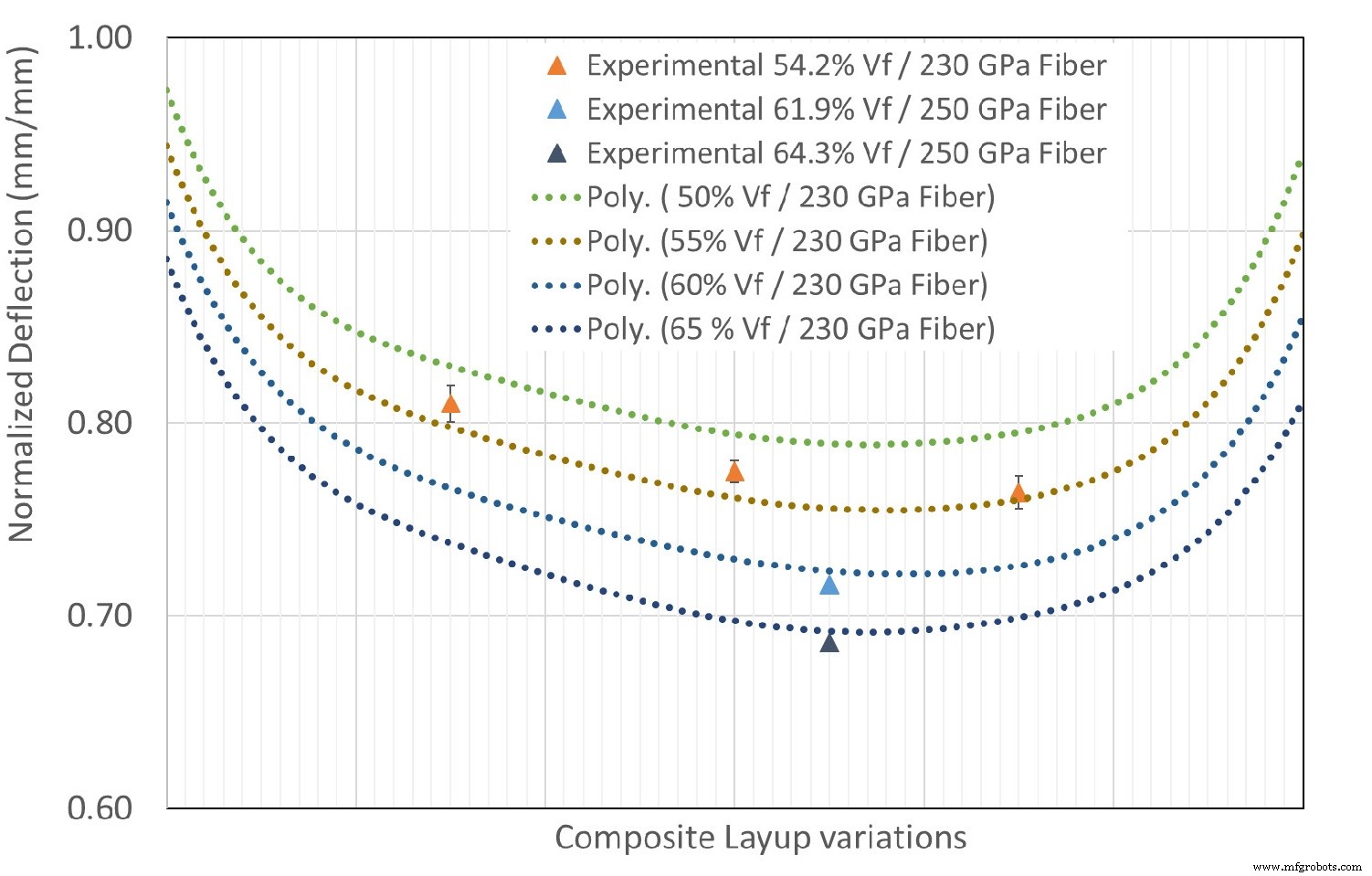
SABIC a développé des modèles prédictifs pour simuler le type et l'architecture des stratifiés (avec et sans composés de surmoulage) par rapport aux performances des pièces moulées et rapporte qu'une forte corrélation entre les prédictions et les résultats expérimentaux a été obtenue. On dit que les outils d'ingénierie prédictive accélèrent le développement des matériaux.
Le composé de surmoulage nécessitait une approche différente. Initialement, la stratégie consistait à utiliser un composé LFT à fibres plus longues, mais pour un certain nombre de raisons, notamment des exigences esthétiques élevées, la taille des pièces et la stratégie de blocage, les composés à fibres courtes répondaient mieux aux exigences du projet. Un autre problème était le type de fibre à utiliser. « Les composés d'injection à court de carbone sont vraiment difficiles à travailler et ont toujours une haute esthétique », poursuit Francato, « donc pour notre matériau de surmoulage, nous avons examiné des grades renforcés de verre court. » La filiale de SABIC LNP Engineering Plastics, Inc. (Exton, Pennsylvanie, États-Unis) propose de nombreuses qualités de fibre de verre/PC avec une bonne esthétique et une bonne rigidité qui sont populaires parmi les équipementiers d'appareils, c'est pourquoi l'équipe s'est concentrée sur celles-ci.
Bien que le PC entièrement amorphe soit moins sujet au gauchissement que les polymères semi-cristallins, l'équipe s'inquiétait toujours des différences CLTE entre les rubans en fibre de carbone UD hautement renforcés et anisotropes et les qualités de surmoulage de fibres de verre courtes plus isotropes et discontinues à des charges de fibres inférieures. « Dans des murs aussi minces, il y a très peu de marge d'erreur, donc les légères différences dans le CLT étaient des choses que nous devions soigneusement considérer », explique Davis. « Et cela ne touche même pas à tous les problèmes normaux qui vous préoccupent lors du moulage par injection, comme les emplacements des portes, les motifs de remplissage, les pressions d'emballage et les lignes de tricot. Tous ces facteurs ont été simulés et vérifiés par des tests physiques. »
Une fois les matériaux choisis, les ingénieurs de SABIC ont effectué plusieurs itérations de remplissage de moules, d'analyse structurelle et de simulation de gauchissement pour évaluer les combinaisons de stratification, de géométrie et de matériaux afin d'optimiser la rigidité pour le test de charge/déflexion, ainsi que d'autres exigences de performance et de coût. La société affirme avoir développé des outils de modélisation de composites complets et précis (disponibles pour les clients et fonctionnant dans des codes de structure et de traitement communs) qui peuvent rapidement modéliser et simuler l'architecture du stratifié, la composition du composé de surmoulage et diverses options de traitement et d'outillage par rapport aux performances des pièces telles que moulées. Ces outils sont censés atteindre une forte corrélation entre les prédictions et les performances mesurées et sont idéaux pour accélérer le développement de matériaux personnalisés.
Prêt pour les heures de grande écoute
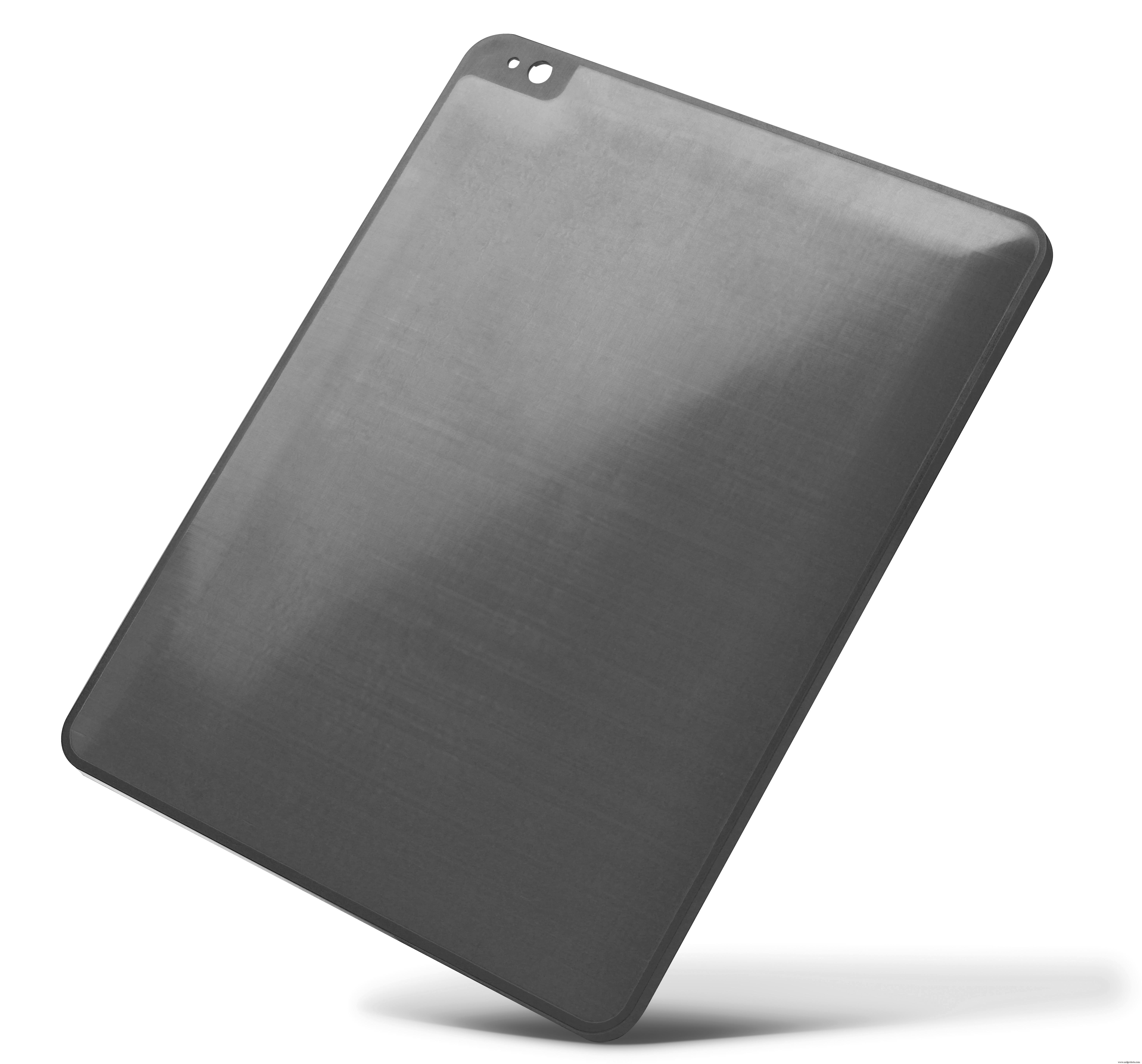
Face avant de la couverture finale pour ordinateur portable/tablette, qui a été produite à l'aide d'un insert stratifié à base de ruban de polycarbonate renforcé de fibres de carbone surmoulé avec un composé de verre court/polycarbonate-copolymère, une combinaison qui répondait à toutes les exigences mécaniques et esthétiques pertinentes dans un 1- pièce d'un millimètre d'épaisseur.
Le démonstrateur final comprend un insert stratifié produit à partir de sept couches de rubans de développement en fibre de carbone/PC UDMAX (fraction volumique de 55 % de fibres), puis consolidé, rogné, préformé et rogné à nouveau jusqu'à la forme finale du filet, avant d'être surmoulé par injection avec 40 % de fibres. -fraction pondérale THERMOCOMP D452 fibre de verre courte/copolymère PC (une qualité optimisée pour un débit élevé et une haute esthétique et déjà largement utilisée dans ce segment). La combinaison produit une couverture avec une rigidité et une résistance élevées à une masse et une épaisseur de section faibles tout en incluant de nombreux détails de conception 3D, des caractéristiques de fixation et une bonne esthétique, exploitant ainsi le meilleur de chaque matériau. La couverture aurait passé tous les tests requis par l'industrie et est actuellement en cours d'évaluation par les fabricants d'équipements d'origine.
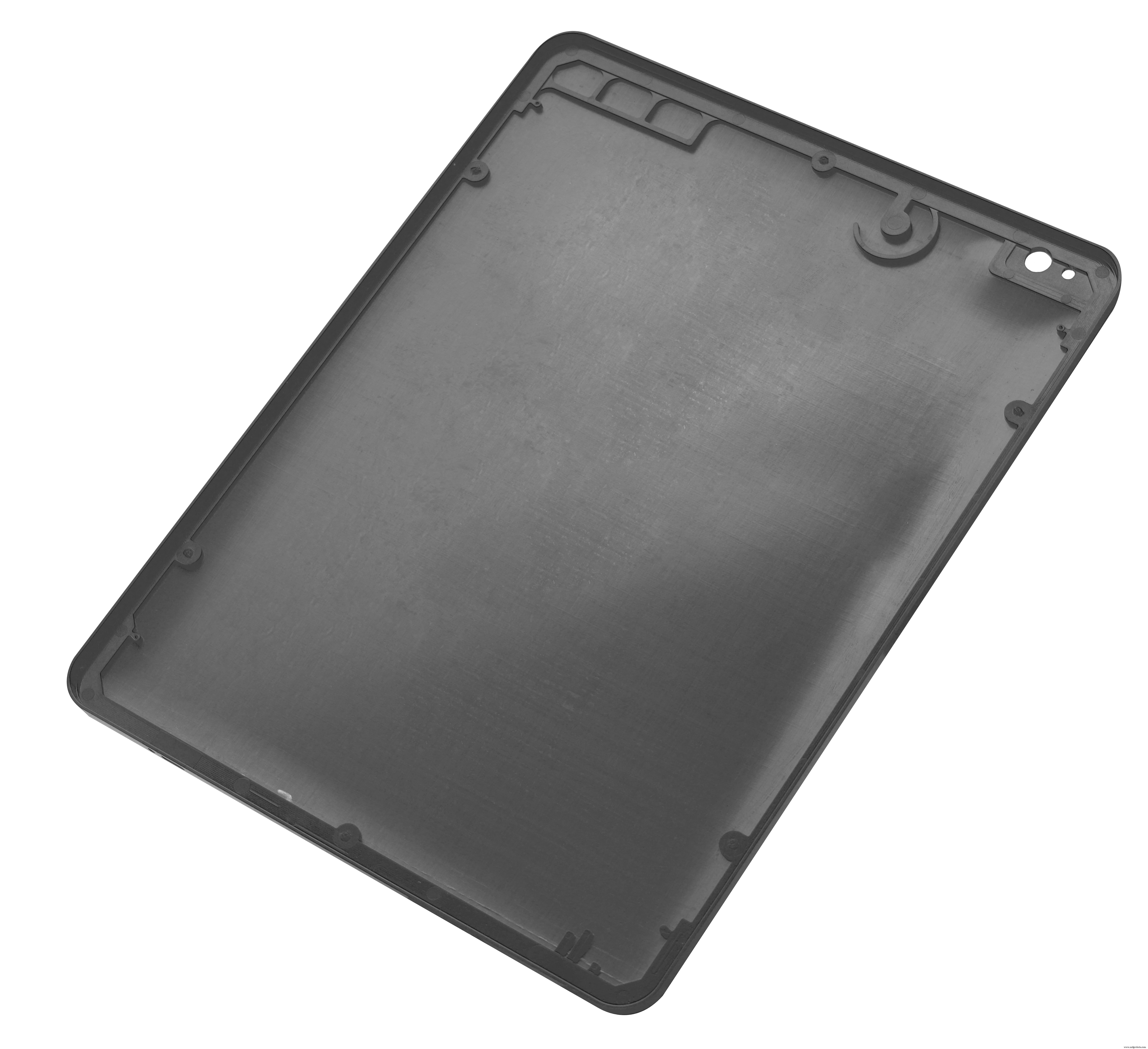
Verso de la couverture finie.
Le travail entre Airborne et SABIC a également porté ses fruits pour les objectifs de marché de l'électronique grand public de SABIC. Le partenariat a été annoncé en 2018, et cette année, des détails supplémentaires ont été fournis sur ce que les deux sociétés appellent leur ligne de fabrication de composites numériques, qui peut produire quatre inserts stratifiés consolidés en forme de filet à partir de bandes composites thermoplastiques par minute ou 1,5 million de stratifiés par an à partir de une seule ligne de production. Le système est dit flexible (en termes d'architecture de stratification et de matériaux) et rapide. À partir de 2020, Airborne utilisera la ligne pour fabriquer des stratifiés à usage commercial dans l'électronique grand public, devenant une ressource qui, espèrent les deux sociétés, augmentera considérablement la pénétration des composites thermoplastiques dans ce segment hautement compétitif et en évolution rapide.
fibre
- Matériaux :graphite flexible monocouche pour l'électronique grand public
- Solvay augmente la capacité des composites thermoplastiques
- La roue en thermoplastique prend la route difficile
- Fraunhofer met en service des cellules de production automatisées Engel pour la R&D sur les composites thermoplastiques
- Les bandes thermoplastiques continuent de montrer un potentiel pour les aérostructures composites
- INEOS Styrolution va construire un site de production pour le composite thermoplastique StyLight
- Xenia présente des composés composites thermoplastiques CF/PP
- composite thermoplastique TenCate qualifié NIAR NCAMP
- Composite + métal :technologie hybride à profil creux