Faire des vagues avec l'automatisation des tours
En tant que fierté de l'État de Badger, Mercury Marine est localement connu simplement sous le nom de "Merc". Les racines de 81 ans de cette icône américaine lui confèrent une riche histoire, ce qui en fait la fierté de la communauté et un favori du public nautique. Pendant ce temps, son succès fait de Merc l'envie de ses concurrents. Mercury Marine est l'un des principaux fabricants mondiaux de tous les types de systèmes de propulsion marine, une division de 2,6 milliards de dollars de Brunswick Corp. qui emploie plus de 5 200 personnes sur plusieurs sites dans le monde.
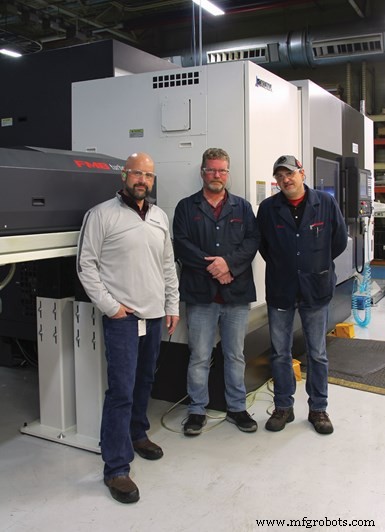
Jason Noworatzky, Bill Cusick et Chris Erke ( L-R) font partie de l'équipe qui produit tous les engrenages et arbres des moteurs inboard et hors-bord Mercury Marine utilisés dans le monde entier.
Plus de 80 ans de développement innovant de moteurs de bateaux ont fait de Fond du Lac, dans le Wisconsin, un lieu extrêmement réputé pour ses prouesses en ingénierie et son excellence en matière de production. Le campus tentaculaire d'aujourd'hui le long de l'Interstate 41 comprend plus de 2,5 millions de pieds carrés d'espace qui contient toutes sortes de disciplines d'ingénierie et de fabrication ainsi que les quelque 3 300 personnes qui font que tout cela se produise.
Dans l'usine 4, tous les engrenages et arbres sont produits pour tous les moteurs inboard et hors-bord de Mercury Marine fabriqués dans ses usines à travers le monde. Cette entreprise massive comprend des arbres de transmission, des arbres de transmission, des arbres de direction, des engrenages avant, des engrenages arrière et des pignons pour tous les moteurs inboard et sterndrive MerCruiser, les sterndrives MerCruser Alpha et Bravo, les moteurs diesel Mercury et les sterndrives diesel, le Mercury SportJet et tous les moteurs hors-bord. L'homme responsable de l'équipe d'ingénieurs de fabrication, d'ingénieurs industriels et de programmeurs requis pour cette lourde tâche est Jason Noworatzky, directeur de l'ingénierie de l'usine 4. Pour tout ce qui concerne le processus de fabrication des arbres et des engrenages, M. Noworatzky et son équipe créent et établissent les procédures de fabrication et de qualité ainsi que les dépenses en capital nécessaires pour produire les pièces efficacement et, surtout, pour répondre aux spécifications strictes de Mercury. . Ensuite, ils sélectionnent les meilleures machines et automatisations en fonction de la vitesse, du coût de la main-d'œuvre et de la perfection des pièces. "La qualité :nous construisons le processus autour de cela", déclare M. Noworatzky.
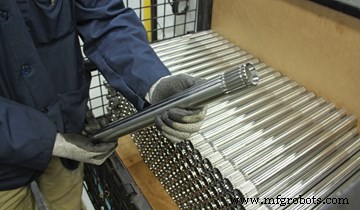
Cette section de l'arbre de direction pour les moteurs hors-bord de l'entreprise était à l'origine produit dans une cellule de cinq machines avec deux opérateurs, mais est maintenant géré par un tour à deux tourelles et deux broches qui est combiné avec un ravitailleur de barres et un déchargeur.
L'un des composants nécessitant une main-d'œuvre particulièrement importante est une section creuse d'arbres de direction utilisés dans les moteurs hors-bord Mercury Marine. Le procédé précédent était une cellule multi-machines. Le démarrage du processus a été un tour monobroche avec une tourelle unique et une poupée mobile avec un ravitailleur de barres. Il serait ensuite transporté vers une autre machine pour une opération de perceuse à colonne. Ensuite, les pièces ont été déplacées vers une autre machine pour une opération de rectification sans centre, puis transportées vers une opération de taillage final. Cette méthode de production de pièces a été utilisée pendant des décennies. « Je suis ici depuis 25 ans, et cela a toujours été fait de cette façon », explique Bill Cusick, ingénieur de fabrication. Ce précédent processus de cellules multi-machines utilisait deux opérateurs.
Finalement, il est devenu évident que les machines de ces cellules devraient être remplacées. À la recherche d'une solution moderne, M. Cusick a étudié des machines nouvelles et modernes. « La technologie a finalement rattrapé son retard, de sorte que nous pouvions désormais utiliser tous les processus dans une seule machine », note M. Cusick. "Nous n'avions plus besoin de les faire fonctionner sur les anciennes machines à tailler."
Chris Erke, programmeur senior, intervient sur la question de la qualité. "Il est difficile de maintenir la position et le faux-rond d'une machine à l'autre au lieu de tout faire dans une seule machine où vous pouvez la contrôler."
Un juste équilibre
"Une grande partie de ce déménagement pour nous a été la qualité", a déclaré M. Cusick. "Cela signifie fait dans une seule machine." L'équipe a dû trouver un juste équilibre entre la capacité et les capacités des machines, le nombre de machines et les besoins de production prévus. Après avoir créé une sorte de tableau de bord, une solution l'a emporté. M. Cusick s'est rendu chez le revendeur de machines-outils local de confiance de l'entreprise, Morris Midwest, et a entamé un dialogue concernant le remplacement des anciennes cellules à cinq machines. "Nous avons créé un SOW (énoncé des travaux) qui expliquait que nous voulions un tour qui effectuera notre processus d'usinage complet", explique M. Cusick. "Nous avions une assez bonne idée de ce que nous pensions que cela impliquerait pour obtenir le temps de cycle nécessaire lors de l'ajout des opérations supplémentaires."
M. Cusick et M. Erke ont fait savoir à Morris Midwest qu'ils pensaient qu'un tour à deux tourelles et deux broches, combiné à un ravitailleur de barres et à un déchargeur, fonctionnerait. "Avec les nouvelles technologies, nous ne pensions pas que ce serait un problème de le produire, donc il va à une extrémité et sort fini", remarque M. Erke. "Nous savions à peu près comment le faire complètement, mais Morris Midwest a sélectionné la bonne machine, a fait toute l'ingénierie et a géré tous les écoulements."
La montée de Frankenlathe
En 2017, la première nouvelle cellule combinée ravitailleur de barres/tour/déchargeur a été livrée à l'usine 4. En raison de sa taille et de ses capacités, le nouveau Okuma LT3000 EX a été affectueusement surnommé "Frankenlathe". Peu de temps après, une deuxième cellule (une réplique exacte du numéro un) a été positionnée à côté de la première et a rapidement été appelée "Bride of Frankenlathe" par le personnel du magasin.
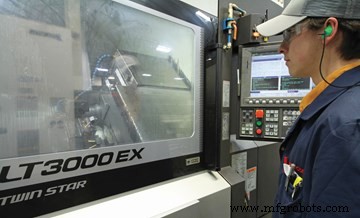
Trois tours Okuma LT3000 EX, avec ravitailleurs de barres et déchargeurs, ont été ajoutés pour gérer la production des arbres.
Les "Frankenlathes" sont tous deux flanqués des machines d'Edge Technologies qui font du processus un véritable avantage technologique unique. L'automatisation utilisée dans cette configuration actuelle était la pièce manquante nécessaire pour produire la pièce "one-and-done" avec la qualité requise. L'Okuma LT3000 EX est un tour à architecture ouverte, un centre de tournage à deux broches très flexible dans la classe des mandrins de 8 pouces. Cette machine bibroche horizontale multifonctions intègre les fonctions tour et fraisage/perçage sur toutes les tourelles.
Les deux premières cellules étaient équipées de ravitailleurs FMB Turbo 5-65. Ce sont des unités de style magazine qui alimentent des barres aussi longues que 12 pieds et comportent des canaux remplis d'huile qui créent un effet de roulement hydrodynamique autour des barres tournantes pour un fonctionnement fluide. La capacité de stockage du magasin est de 11 pouces sur les unités standard. Avec la longueur de pièce et le temps de cycle de cette section d'arbre, l'Okuma peut traiter pas mal de pieds linéaires de tubes pendant un quart de travail, alors Edge Technologies a ajouté le Edge BarLift, un système de chargement de magasin étendu qui comprend 28 pouces supplémentaires de stock pour fonctionnement plus long sans que l'opérateur ait besoin de charger manuellement le chargeur.
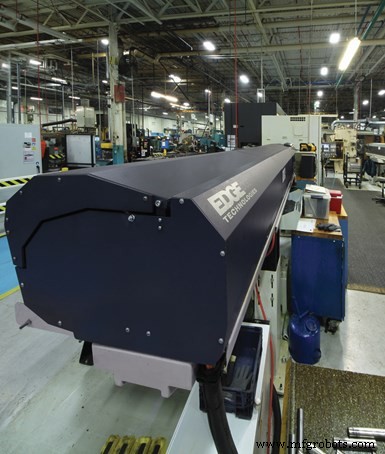
Le FMB Turbo 5-65 12 pieds les ravitailleurs de barres de style magazine comportent des canaux remplis d'huile qui créent un effet de bering hydrodynamique autour des barres tournantes pour un fonctionnement en douceur.
"Nous avons peut-être eu un ou deux tours équipés d'un déchargeur dans le passé, mais c'est de loin la plus grande étape sur le produit le plus courant sur lequel nous avons fait (un déchargeur)", déclare M. Noworatzky. « Nous ne pouvons pas laisser tomber cette pièce car cela endommagerait les cannelures. La pièce terminée a des exigences de finition de surface."
Les cellules un et deux ont été installées en 2017 et étaient équipées des unités FleXsys LE (Load/Extract) d'Edge Technologies pour le processus de déchargement des pièces. Cette unité est conçue pour l'automatisation de pièces plus grandes, en particulier les travaux à arbre long. Il est conçu pour alimenter et rétracter les barres coupées à la longueur de la pièce (jusqu'à 2,5 pouces de diamètre et 37 pouces de long) pour la production avec des tours CNC monobroches. Le stock de tubes de 12 pieds est introduit dans la broche principale d'Okuma avec le FMB Turbo 5-65.
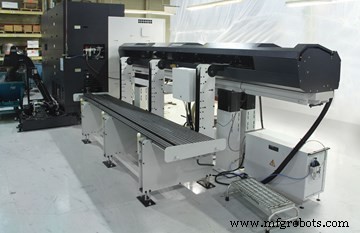
Le système de chargement de magasin étendu Edge BarLift comprend un 28 pouces supplémentaires de stock pour un fonctionnement plus long sans intervention de l'opérateur.
Frankenlathe 3 :L'essor de l'automatisation
La troisième cellule est arrivée fin 2019 avec le nouveau Rebel 80 Servo Unloader, le système d'extraction automatique de pièces le plus récemment développé par Edge Technologies pour extraire des pièces d'un diamètre compris entre 8 et 80 mm. Il s'agit d'une unité plus polyvalente que la version précédente qui fonctionne sur les cellules un et deux. Les anciennes unités n'avaient pas de système de contrôle qui communiquerait avec le tour comme le font les ravitailleurs de barres FMB. Une programmation supplémentaire du FleXsys LE était nécessaire. Bien que les unités aient bien fonctionné une fois qu'elles ont été ajustées, Mercury Marine a demandé à Edge Technologies de fournir une configuration de déchargeur mise à jour qui corrigerait cette lacune. Le développement du Rebel 80 Servo Unloader était la réponse. Edge avait travaillé sur le nouveau déchargeur et avait fait du problème de communication une priorité principale pour l'installation Mercury. Désormais, sur la troisième cellule, l'Okuma LT3000 EX, le ravitailleur de barres FMB et le déchargeur Edge communiquent et fonctionnent tous comme une seule machine avec une optimisation de type Industrie 4.0.
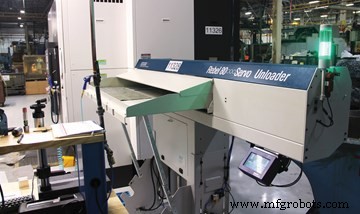
Alors que les deux premiers tours étaient équipés de FleXsysLE déchargeurs, conçus pour l'automatisation de pièces plus grandes, le troisième Okuma est équipé du déchargeur servo Rebel 80, conçu pour extraire des pièces de 8 à 80 mm de diamètre et doté de capacités de communication optimisées avec le ravitailleur de barres et la machine-outil.
Le déchargeur servo Rebel 80 propose plusieurs façons de retirer les pièces avec différentes méthodes de fixation de l'extracteur à la pièce pour la tirer de la sous-broche. Ces dispositifs sont appelés effecteurs terminaux. Les mécanismes d'effecteur d'extrémité disponibles comprennent des pinces à barre pour la préhension du diamètre extérieur, des pinces à expansion ID, des pinces à trois points pour le diamètre extérieur, des doigts d'alimentation, des pinces angulaires, des électroaimants pour les matériaux ferromagnétiques et des solutions techniques spéciales pour les pièces profilées et de forme irrégulière.
Pour protéger les finitions des pièces, dans le cas des cannelures de l'arbre de direction, le plateau en V d'extraction place doucement les arbres sur la surface du magasin, qui est recouverte d'un matériau non métallique. La table inclinée est réglable, ce qui permet au déchargeur de "décharger facilement" les pièces de grand diamètre.
Le déchargeur servo Rebel 80 est doté d'une voie de décalage axial qui permet à l'unité de glisser facilement loin du tour pour les changements de chemise de broche et l'accès de maintenance à l'arrière du tour. Il est équipé d'un pendentif télécommandé et d'une commande conversationnelle qui dispose d'un écran tactile et d'une programmation pilotée par menu. La commande stocke également un nombre illimité de programmes de pièce.
La troisième cellule a également bénéficié d'une avancée dans la technologie des embarreurs. Le FMB Turbo 5-65 était équipé en modèle A, avec le nouveau système de canal de guidage à réglage automatique. Les canaux de guidage en polyuréthane s'ajustent automatiquement au diamètre approprié, permettant à un canal de guidage de faire fonctionner des diamètres de barre de 5 mm à 65 mm. Cette fonctionnalité donne à Mercury Marine la possibilité de passer rapidement à différents diamètres d'arbre sans changement de jeu de canaux de guidage. Cette conception facilite les configurations rapides pour une production juste à temps.
Outre l'augmentation de la qualité des pièces, ces cellules présentent l'avantage de réduire les coûts de main-d'œuvre et offrent une meilleure utilisation de l'espace au sol. Idéalement, M. Noworatzky aurait une ardoise vierge pour reconfigurer son plancher de production comme il le souhaite. Il explique que les deux choses qui motivent son équipe sont de combiner les opérations et d'essayer de partager le travail.
À l'avenir, M. Noworatzky estime que l'ajout d'automatisation, comme les ravitailleurs de barres et les déchargeurs qui ont été utilisés avec ces tours, deviendra la norme. "Je ne prévois pas de nouvelles cellules qui n'auront pas un certain type d'automatisation. Qu'il s'agisse d'un robot FANUC, d'un système de portique, d'un ravitailleur de barres ou de déchargeurs. Il prédit que ce sera quelque chose pour minimiser la quantité de travail nécessaire pour faire un travail. "Le travail est une prime", conclut M. Noworatzky.
En raison de l'expertise technique plus élevée requise pour faire fonctionner des cellules comme celles-ci, Mercury Marine propose des cours au personnel pour améliorer leurs compétences. "Cela nécessite que vous ayez un niveau d'opérateur plus élevé", déclare M. Noworatzky. Pour ce faire, Mercury envoie ses opérateurs dans un collège communautaire local où ils s'inscrivent à des cours d'usinage de niveau 1 et 2. Une fois terminé, ils peuvent tester pour recevoir la certification NIMS.
Mercure Marine | mercuremarine.com
Technologies de pointe | 314-692-8388 | edgetechnologies.com
À propos de l'auteur
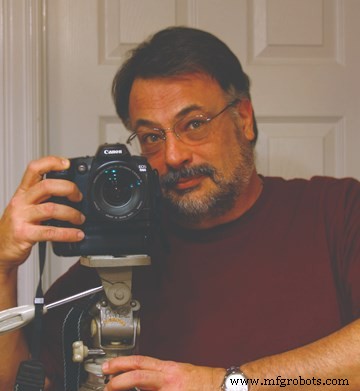
Kévin Shults
Kevin Shults est un professionnel de la publicité et du design. Il a 24 ans d'expérience dans l'industrie de la machine-outil, dont les 20 dernières en tant que directeur du marketing pour un équipementier de l'industrie de l'usinage de précision. Contactez M. Shults à [email protected].
Équipement industriel
- Gagner de l'argent avec le routeur CNC
- Évolution de l'automatisation des tests avec l'intelligence artificielle
- Automatisation de l'entreprise avec des plates-formes low-code
- Améliorer l'expérience client avec l'automatisation intelligente
- Tour standard avec commandes à écran tactile
- Tour avec CNC
- Tour CNC avec système de guidage linéaire hydrostatique
- Tour d'outils en groupe avec base en polymère--SNK
- Contrôle des caractéristiques du tour à banc incliné avec graphiques de vérification