Meilleures pratiques d'empilement de tolérance
L'empilement de tolérances, également connu sous le nom d'empilement de tolérances, fait référence à la combinaison de diverses tolérances de dimension de pièce. Après qu'une tolérance est identifiée sur la dimension d'une pièce , il est important de tester si cette tolérance fonctionnerait avec l'outil tolérances :soit l'extrémité supérieure, soit l'extrémité inférieure. Une pièce ou un assemblage peut être sujet à des imprécisions lorsque ses tolérances sont empilées de manière incorrecte.
L'importance des tolérances
Les tolérances influencent directement le coût et les performances d'un produit. Des tolérances plus serrées rendent une pièce usinée plus difficile à fabriquer et donc souvent plus chère. Dans cet esprit, il est important de trouver un équilibre entre la fabricabilité de la pièce, sa fonctionnalité et son coût.
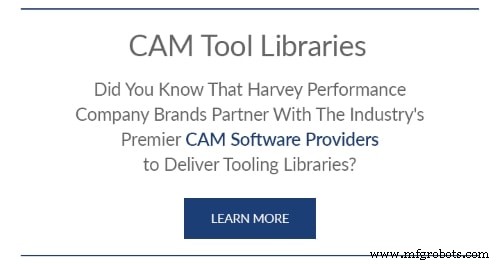
Conseils pour un empilement de tolérance réussi
Évitez d'utiliser des tolérances inutilement petites
Comme indiqué ci-dessus, des tolérances plus serrées entraînent un coût de fabrication plus élevé car la pièce est plus difficile à fabriquer. Ce coût plus élevé est souvent dû à la quantité accrue de pièces mises au rebut qui peut se produire lorsque les dimensions se révèlent hors tolérances. Le coût des porte-outils de haute qualité et de l'outillage avec des tolérances plus serrées peut également représenter une dépense supplémentaire.
De plus, des tolérances inutilement petites entraîneront des temps de fabrication plus longs, car plus de travail est nécessaire pour s'assurer que la pièce répond à des critères stricts pendant l'usinage et après l'usinage dans le processus d'inspection.
Attention à ne pas surdimensionner une pièce
Lorsqu'une tolérance supérieure et inférieure est étiquetée sur chaque caractéristique d'une pièce, le surdimensionnement peut devenir un problème. Par exemple, une fraise en bout à rayon d'angle avec des rayons d'angle droit et gauche peut avoir une tolérance de +/- 0,001", et le méplat entre eux a une tolérance de 0,002". Dans ce cas, la fenêtre de tolérance pour le diamètre de la fraise serait de +/- 0,004", mais elle est souvent mal calculée lors du dimensionnement de la pièce. De plus, placer une tolérance sur cette légende entraînerait une surdimensionnement, et donc la cote de référence "REF" doit être laissée pour prendre la place de la tolérance.
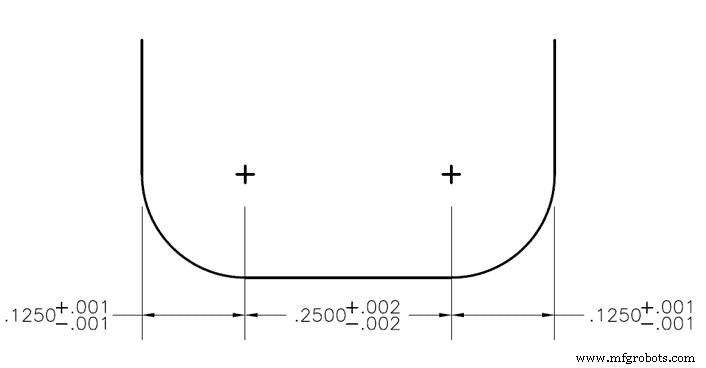
Utiliser l'analyse de tolérance statistique :
L'analyse statistique examine la probabilité que les trois tolérances soient inférieures ou supérieures à la largeur de fente dimensionnée, sur la base d'un écart type. Cette probabilité est représentée par une fonction de densité de probabilité normale, visible sur la figure 2 ci-dessous. En combinant toutes les probabilités des différentes pièces et dimensions dans une conception, nous pouvons déterminer la probabilité qu'une pièce ait un problème, ou échoue complètement, en fonction des dimensions et de la tolérance des pièces. Généralement, cette méthode d'analyse n'est utilisée que pour les assemblages avec quatre tolérances ou plus.
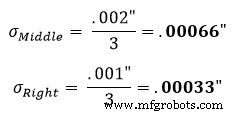
Avant de démarrer une analyse de tolérance statistique, vous devez calculer ou choisir un facteur de distribution de tolérance. La distribution standard est 3 . Cela signifie que la plupart des données (ou dans ce cas les tolérances) seront à moins de 3 écarts-types de la moyenne. Les écarts types de toutes les tolérances doivent être divisés par ce facteur de distribution de tolérance pour les normaliser d'une distribution de 3 à une distribution de 1 . Une fois cela fait, la somme des racines au carré peut être prise pour trouver l'écart type de l'assemblage.
Pensez-y comme une tasse de café préparée avec 3 grains de tailles différentes. Afin de préparer une délicieuse tasse de café, vous devez d'abord broyer tous les grains à la même taille afin qu'ils puissent être ajoutés au filtre à café. Dans ce cas, les grains sont les écarts-types, le broyeur est le facteur de distribution de tolérance et le filtre à café est l'équation racine carrée. Cela est nécessaire car certaines tolérances peuvent avoir des facteurs de distribution différents en fonction de l'étroitesse de la plage de tolérance.
La méthode d'analyse statistique est utilisée s'il est nécessaire que la fente ait une largeur de 0,500" avec une tolérance de +/- 0,003", mais il n'y a pas besoin de rayons (0,125") et de plat (0,250") ) pour être exact tant qu'ils tiennent dans l'emplacement. Dans cet exemple, nous avons 3 tolérances bilatérales avec leurs écarts types déjà disponibles. Puisqu'ils sont bilatéraux, l'écart type par rapport à la moyenne serait simplement quelle que soit la valeur de tolérance + ou -. Pour les rayons extérieurs, ce serait 0,001" et pour la région plate du milieu, ce serait 0,002".
Pour cet exemple, trouvons l'écart type (σ) de chaque section à l'aide de l'équation 1. Dans cette équation représente l'écart type.

L'hypothèse standard est qu'une tolérance de pièce représente une distribution normale +/- 3. Par conséquent, le facteur de distribution sera de 3. En utilisant l'équation 1 dans la partie gauche de la figure 1, nous constatons que son écart type corrigé équivaut à :
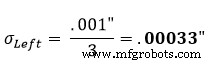
Ceci est ensuite répété pour les sections du milieu et de droite :
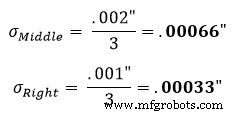
Après avoir obtenu ces écarts-types, nous saisissons les résultats dans l'équation 2 pour trouver l'écart-type de la zone de tolérance. L'équation 2 est connue sous le nom d'équation racine somme carrée.
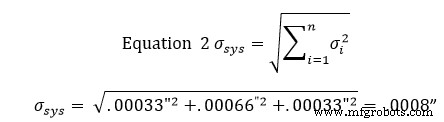
À ce stade, cela signifie que 68 % des emplacements seront dans une tolérance de +/- 0,0008". Multiplier cette tolérance par 2 se traduira par une fenêtre de confiance de 95 %, où la multiplier par 3 se traduira par une fenêtre de confiance de 99 %.
68 % des créneaux seront à +/- 0,0008"
95 % des créneaux seront à +/- 0,0016"
99 % des créneaux seront à +/- 0,0024"
Ces fenêtres de confiance sont standard pour un ensemble distribué normal de points de données. Une distribution normale standard peut être vue dans la figure 2 ci-dessus.
L'analyse de tolérance statistique ne doit être utilisée que pour les assemblages comportant plus de 4 pièces tolérancées. De nombreux facteurs n'ont pas été pris en compte dans cette simple analyse. Cet exemple concernait 3 dimensions bilatérales dont les tolérances étaient représentatives de leurs écarts-types par rapport à leurs moyennes. Dans l'analyse de tolérance statistique standard, d'autres variables entrent en jeu telles que les angles, le faux-rond et le parallélisme, qui nécessitent des facteurs de correction.
Saviez-vous que les marques Harvey Performance Company s'associent aux principaux fournisseurs de logiciels de caméras du secteur pour proposer des bibliothèques d'outils ?
Cliquez ici pour en savoir plus
Utiliser l'analyse du pire cas :
L'analyse du pire cas consiste à additionner toutes les tolérances d'une pièce pour trouver la tolérance totale de la pièce. Lors de l'exécution de ce type d'analyse, chaque tolérance est définie sur sa limite la plus grande ou la plus petite dans sa plage respective. Cette tolérance totale peut ensuite être comparée aux limites de performance de la pièce pour s'assurer que l'assemblage est correctement conçu. Ceci est généralement utilisé pour une seule dimension (un seul plan, donc aucun angle impliqué) et pour les assemblages avec un petit nombre de pièces.
L'analyse du pire des cas peut également être utilisée lors du choix de l'outil de coupe approprié pour votre travail, car la tolérance de l'outil peut être ajoutée à la tolérance des pièces pour le pire des cas. Une fois ce scénario identifié, le machiniste ou l'ingénieur peut effectuer les ajustements appropriés pour maintenir la pièce dans les dimensions spécifiées sur l'impression. Il convient de noter que le pire scénario se produit rarement dans la production réelle. Bien que ces analyses puissent être coûteuses pour la fabrication, elles offrent une tranquillité d'esprit aux machinistes en garantissant que tous les assemblages fonctionneront correctement. Souvent, cette méthode nécessite des tolérances serrées car l'empilement total dans les conditions maximales est la principale caractéristique utilisée dans la conception. Des tolérances plus strictes augmentent les coûts de fabrication en raison de l'augmentation de la quantité de grattage, du temps de production pour l'inspection et du coût de l'outillage utilisé sur ces pièces.
Exemple de pire scénario dans le contexte de la figure 1 :
Trouvez la limite de spécification inférieure.
Pour le rayon du coin gauche
.125" – .001" =.124"
Pour la section plate
.250" – .002" =.248"
Pour le rayon du coin droit
.125" – .001" =.124"
Ajoutez tous ces éléments à la limite de spécification inférieure :
.124" + .248" + .124" =.496"
Trouvez la limite de spécification supérieure :
Pour le rayon du coin gauche
.125" + .001" =.126"
Pour la section plate
.250" + .002" =.252"
Pour le rayon du coin droit
.125" + .001" =.126"
Ajoutez tous ces éléments à la limite de spécification inférieure :
.126" + .252" + .126" =.504"
Soustrayez les deux et divisez cette réponse par deux pour obtenir la tolérance du pire cas :
(Limite supérieure - Limite inférieure)/2 =0,004"
Par conséquent, le pire scénario de cet emplacement est de 0,500" +/- 0,004".
commande numérique par ordinateur
- Meilleures pratiques pour la surveillance synthétique
- Meilleures pratiques commerciales natives du cloud
- Meilleures pratiques de gestion des risques d'arrêt
- Best of…Meilleures pratiques en matière de moulage par injection
- Cinq bonnes pratiques en matière de télématique des transports
- Meilleures pratiques de gestion des câbles robotiques
- Meilleures pratiques pour assurer la sécurité des excavatrices
- Circuit imprimé Power Plane :bonnes pratiques
- Meilleures pratiques de marketing de fabrication pour 2019