Le guide d'usinage CNC ultime
L'usinage à commande numérique par ordinateur (CNC) est un processus de fabrication soustractif moderne, efficace et automatisé qui permet aux fabricants de fabriquer des pièces reproductibles de qualité constante à partir d'une large gamme de matériaux, y compris les plastiques, les métaux et les composites. Aujourd'hui, les pièces usinées CNC peuvent être trouvées dans une variété d'industries différentes, de l'aérospatiale à l'automobile en passant par le médical.
Les débuts des technologies CNC remontent à quelques points différents de l'histoire. Les premiers outils d'usinage modernes sont apparus en 1775 lorsque les industriels ont mis au point un outil d'alésage permettant aux fabricants de produire des cylindres de machines à vapeur avec des degrés d'exactitude et de précision plus constants.
Les ancêtres technologiques de l'informatique moderne sont cependant apparus plus tôt dans le siècle, émergeant de l'industrie textile. En 1725, Basile Bouchon a commencé à utiliser un système de trous perforés dans la bande de papier pour encoder les données. Des décennies plus tard, en 1805, Joseph Marie Jacquard a affiné le processus, remplaçant la bande de papier par des cartes perforées robustes. Lorsqu'elles étaient liées dans une séquence, les cartes perforées indiquaient comment le tissu était ajouté au métier à tisser, simplifiant le processus et fournissant l'un des premiers exemples de programmation. Cette machine, le métier Jacquard, est en quelque sorte l'ancêtre de nos solutions modernes d'informatique et d'automatisation.
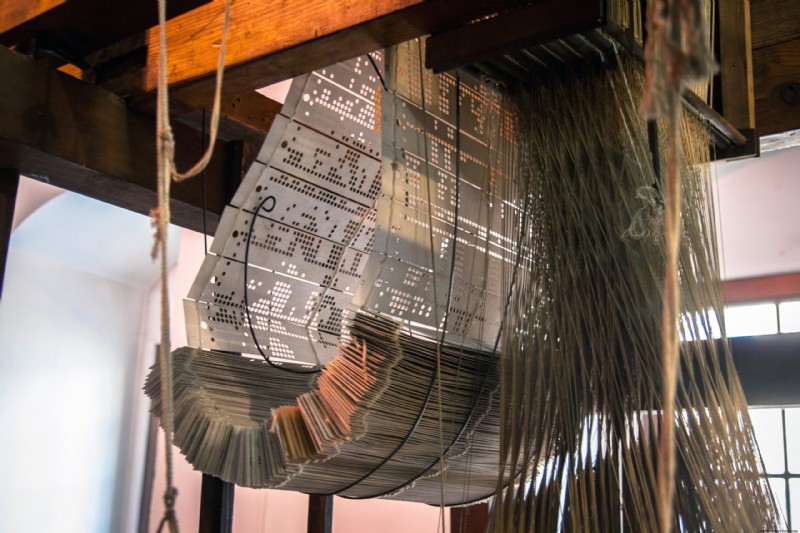
Ce guide sur tout ce qui concerne l'usinage CNC expliquera comment fonctionnent les processus d'usinage CNC modernes, y compris les options de matériaux, les considérations de conception, les inducteurs de coûts, etc. Continuez à lire ou cliquez ici pour télécharger le PDF.
Types d'usinage CNC
Aujourd'hui, plusieurs processus techniques sont inclus sous le parapluie de l'usinage CNC.
Usinage 3 axes :fraisage et tournage
Une fois que l'opérateur a entré les instructions d'usinage, les machines CNC à 3 axes effectueront les opérations d'entrée en utilisant des outils de coupe pour couper le long de trois axes :X (de gauche à droite), Y (avant vers arrière) et Z (haut et - vers le bas). Le fraisage CNC et le tournage CNC sont deux exemples courants d'usinage 3 axes.
Le fraisage CNC à 3 axes consiste à fixer le bloc de matériau - également appelé la pièce ou "l'ébauche" - avec un étau ou un banc de machine. Cela maintient la pièce à l'arrêt alors que les outils de coupe et les perceuses rotatives, attachés à une broche centrale, effectuent des coupes pour enlever le matériau et façonner le composant final. Les fraiseuses CNC à 3 axes sont faciles à programmer et à utiliser et peuvent être utilisées pour créer la plupart des pièces avec des conceptions géométriques simples.
Étant donné que les outils de coupe et les forets sont limités à trois axes, certaines caractéristiques de conception ou zones de l'ébauche peuvent être difficiles à terminer ou à atteindre (par exemple, des formes non conventionnelles ou des cavités profondes et étroites). Cependant, plusieurs configurations peuvent aider à orienter la pièce pour que les machines atteignent ces caractéristiques. Alors que presque tous les travaux d'usinage 3 axes ont plus d'une configuration par pièce, un trop grand nombre de configurations par pièce peut rapidement augmenter les coûts de production. Le traitement de pièces géométriquement complexes peut, par exemple, obliger les opérateurs à repositionner manuellement les pièces, ce qui peut avoir un impact sur la vitesse de traitement, augmenter les coûts de main-d'œuvre et créer davantage de possibilités d'erreur humaine.
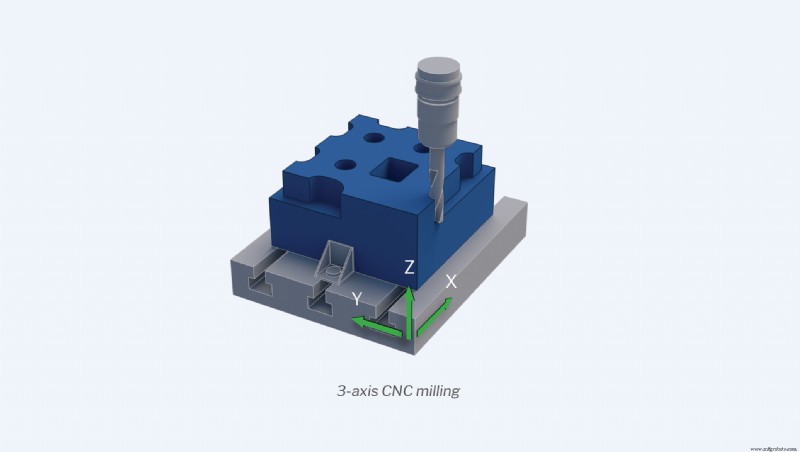
Le processus de tournage CNC fonctionne un peu différemment. L'ébauche est fixée à une broche rotative, et un tour façonne ensuite les périmètres intérieur et extérieur de la pièce ou perce des trous autour de l'axe central de la pièce. La restriction de conception la plus importante avec les tours CNC est qu'ils produisent toujours des pièces symétriques en rotation. Le procédé est donc idéal pour la fabrication de pièces telles que des vis, des bols ou des pieds de chaise. Pour ces types de pièces arrondies, les tours peuvent produire des pièces plus rapidement et à moindre coût que les fraiseuses CNC, en particulier lors de la production de pièces en gros volumes.
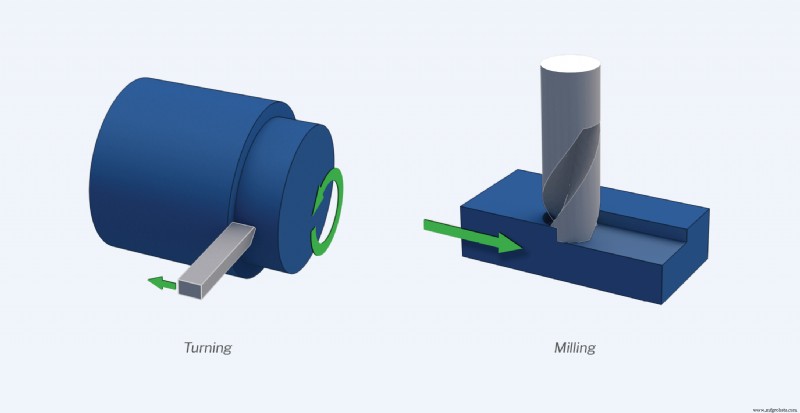
Usinage 5 axes ou multiaxes
Les processus d'usinage multi-axes permettent aux outils de coupe une plus grande liberté de mouvement pendant le fraisage ou le tournage de la pièce. Les procédés à 3 axes permettent soit à l'ébauche, soit à l'outil de coupe de tourner, mais pas les deux. En revanche, les processus à 5 axes permettent à la fois à la pièce et à l'outil de tourner et de se déplacer simultanément le long des axes X, Y et Z. L'usinage CNC 5 axes permet de gagner du temps et est idéal pour créer des pièces complexes et précises comme celles que l'on trouve dans les industries médicales, pétrolières et gazières et aérospatiales.
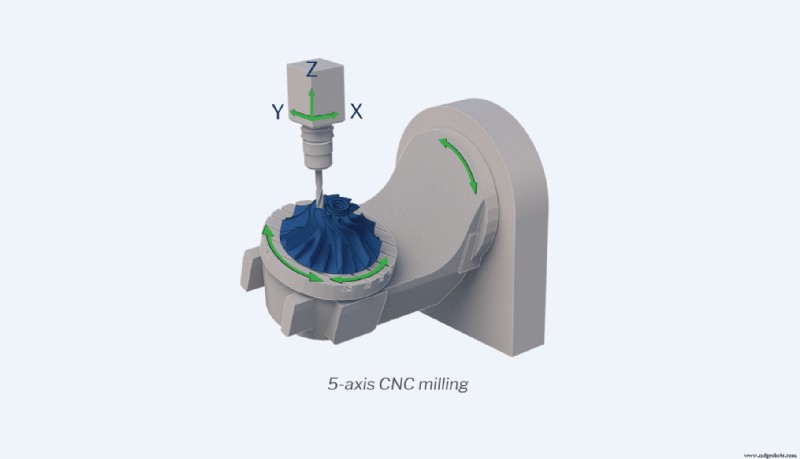
La famille d'usinage CNC multi-axes comprend trois procédés :
- Fraisage CNC 5 axes indexé : Lors des opérations de fraisage 5 axes indexés, non seulement les outils de coupe peuvent se déplacer le long des trois axes linéaires, mais entre les opérations, la table d'usinage et la tête d'outil peuvent pivoter dans deux directions. L'avantage le plus remarquable du fraisage 5 axes est qu'il n'est plus nécessaire de régler manuellement les ébauches entre les opérations de coupe, ce qui permet de créer des composants aux géométries complexes avec plus de précision et d'efficacité. L'usinage 5 axes indexé est idéal pour fabriquer des composants tels que des boîtiers, des gabarits et des fixations. Le processus se situe quelque part entre le fraisage CNC 3 axes et l'usinage CNC continu 5 axes (voir ci-dessous) en termes de vitesse, de précision et de capacité à gérer des géométries complexes.
- Fraisage CNC 5 axes continu : Les fraiseuses CNC à 5 axes continus peuvent déplacer et faire pivoter simultanément l'outil de coupe et la pièce à usiner lors de chaque opération, ce qui permet la fabrication de pièces aux géométries extrêmement complexes et aux surfaces lisses. Bien qu'il s'agisse de la forme d'usinage CNC la plus coûteuse par pièce, le coût du fraisage CNC continu à 5 axes est généralement compensé par l'amélioration de la finition de surface, de la vitesse et de la stabilité dimensionnelle.
- Usinage fraisage-tournage avec outillage motorisé : Le fraisage-tournage combine des éléments de tours CNC avec des outils de fraisage. La pièce est fixée à une broche rotative tandis que les outils de coupe enlèvent la matière de l'ébauche. En combinant les éléments des machines de tour CNC avec des outils de fraisage, la CNC de fraisage-tournage offre des niveaux élevés de précision et de polyvalence géométrique, ce qui la rend idéale pour créer des pièces avec des symétries de rotation lâches, telles que des arbres à cames ou des compresseurs centrifuges.
Choisir le bon type d'usinage CNC
Lors de la sélection d'un processus de fabrication pour votre pièce, vous devrez évaluer s'il convient mieux à l'usinage 3 axes ou 5 axes. En règle générale, les pièces aux conceptions plus simples peuvent être fabriquées rapidement et à moindre coût à l'aide de machines à 3 axes, tandis que les machines à 5 axes sont plus adaptées pour créer des pièces géométriquement complexes avec une vitesse et une précision accrues.
Si vous avez un budget limité ou si vous avez seulement besoin de couper une surface plane, les machines à 3 axes sont la solution. En plus d'être plus abordables, les machines 3 axes sont plus simples à programmer, vous n'aurez donc pas à supporter les coûts de travail avec des programmeurs et opérateurs 5 axes coûteux. De plus, le temps de préparation est plus court avec l'usinage 3 axes.
Si vous avez besoin de produire une pièce plus profonde ou avec une géométrie complexe, vous voudrez utiliser l'usinage 5 axes. L'utilisation de machines à 5 axes vous permet d'usiner la pièce de tous les côtés sans nécessiter de rotation manuelle. Avec l'usinage 5 axes, vous obtiendrez des rendements plus élevés, une plus grande précision et une plus grande liberté de mouvement, ainsi que la possibilité de fabriquer des pièces plus grandes plus rapidement.
Matériaux CNC courants
L'un des avantages de l'usinage CNC est que le procédé est compatible avec de nombreux matériaux différents, les plastiques et les métaux étant les deux familles de matériaux les plus courantes. Voici quelques-uns des plastiques et des métaux que vous êtes susceptible de rencontrer.
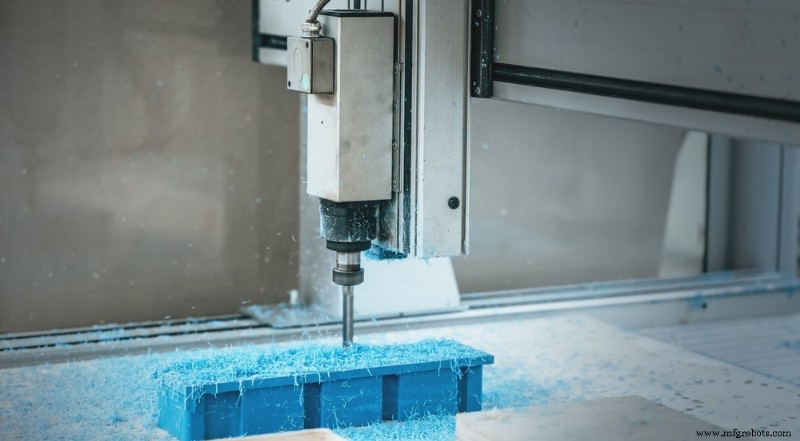
Polymères hautes performances
- Acrylonitrile butadiène styrène (ABS) : L'ABS est un thermoplastique technique résistant aux chocs avec d'excellentes propriétés mécaniques. Solide et rigide tout en conservant une certaine flexibilité, l'ABS se distingue par sa résistance mécanique, sa bonne isolation et sa résistance à l'abrasion et aux contraintes.
- Polyéthylène haute densité (HDPE) : L'un des polymères thermoplastiques les plus polyvalents, le HDPE est un matériau flexible et facile à traiter qui est très résistant à la fissuration sous contrainte, aux produits chimiques et aux agents corrosifs, même à basse température. Il offre également une excellente résistance aux chocs. Le PEHD est couramment utilisé pour fabriquer des bouteilles en plastique, des bouchons, des joints, des isolants, des tuyaux et de nombreux autres produits.
- Polyéthylène basse densité (LDPE) : Principalement utilisé pour créer des orthèses et des prothèses, ce plastique résistant et flexible est facile à souder et à sceller à chaud. Bien qu'il offre une bonne résistance chimique, le LDPE n'est pas idéal pour les applications nécessitant une rigidité, une résistance structurelle élevée ou une résistance aux températures élevées.
- Polyamide (PA) ou Nylon : Les nylons sont une famille de plastiques à faible frottement qui sont bien adaptés pour remplacer les composants métalliques, comme les roulements ou les bagues, en raison de leur combinaison unique d'élasticité, de rigidité et de raideur. Les nylons peuvent être renforcés avec une gamme d'additifs pour créer des propriétés matérielles et chimiques spécifiques ou combinés avec d'autres plastiques pour des performances et des caractéristiques matérielles accrues.
- Polyamide (PA) ou Nylon 30 % GF : Les fibres de verre, l'un des additifs les plus courants pour les plastiques techniques, augmentent considérablement la résistance et la rigidité des pièces en nylon. Malheureusement, ces fibres augmentent également la fragilité du matériau et ne sont donc recommandées que pour les applications qui n'impliquent pas de contrainte ou de déflexion à fort impact.
- Polycarbonate (PC) : Ce plastique est largement utilisé pour un certain nombre de raisons :il est solide tout en étant léger, c'est un bon isolant électrique et il est naturellement résistant à la chaleur. Le PC est intrinsèquement transparent et translucide et absorbe bien les pigments. De plus, le PC résiste aux acides dilués, aux huiles et aux graisses, mais est sensible à l'usure par les hydrocarbures et aux rayons UV.
- Polyétheréthercétone (PEEK) : Polymère haute performance doté d'une combinaison unique de propriétés mécaniques, le PEEK est résistant aux produits chimiques, à l'usure, au fluage, à la fatigue, aux liquides et à la température. En plus d'être recyclable et biocompatible, ce matériau est également léger, solide et insoluble dans tous les solvants courants. Semblable au nylon, le PEEK peut remplacer le métal dans l'usinage CNC. Les applications courantes de ce matériau comprennent les pistons, les pièces critiques de moteurs d'avion et les seringues dentaires. Il s'agit notamment de l'un des plastiques d'usinage CNC les plus chers du marché.
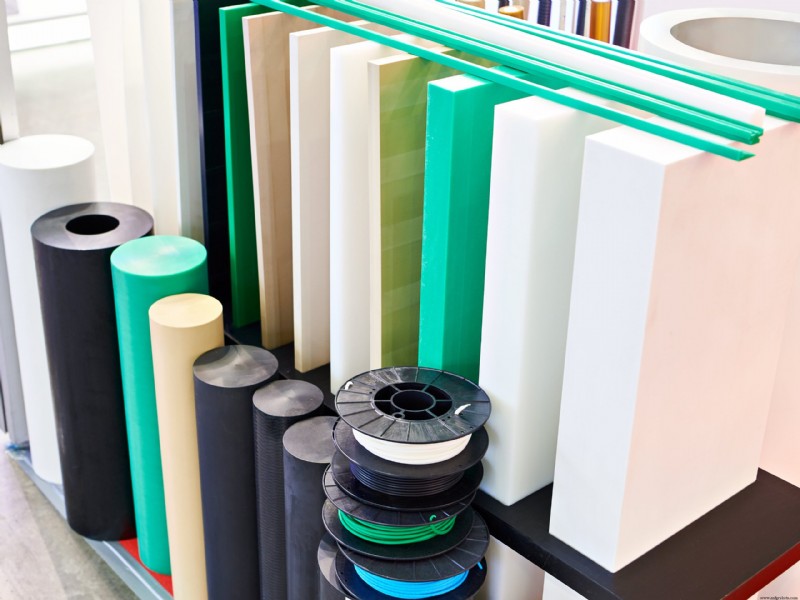
- Polyétherimide (PEI) : Communément appelé ULTEM®, le PEI est un plastique haute performance et un agrafe de fabrication. Non seulement le PEI est solide et facile à utiliser, mais il résiste également aux produits chimiques et aux flammes, et peut supporter des températures extrêmement élevées sans perdre ses propriétés électriques stables. Pour cette raison, le PEI est généralement utilisé pour créer des produits tels que des circuits imprimés, des lunettes, des équipements de préparation et de stérilisation des aliments et des pièces d'avion. C'est l'un des rares polymères thermoplastiques amorphes disponibles dans le commerce qui conserve son intégrité mécanique à des températures élevées.
- Polyméthacrylate de méthyle (PMMA) : Le PMMA est un polymère thermoplastique rigide souvent appelé acrylique ou verre acrylique. Extrêmement incassable, ce matériau robuste et léger est translucide et résistant aux intempéries et aux rayons UV, ce qui le rend idéal pour les applications à faible contrainte telles que les serres, les couvercles des phares et des clignotants de voiture ou les panneaux solaires. Cependant, il est important de noter que le PMMA est sensible à la chaleur élevée, aux chocs, à l'usure et à l'abrasion, et qu'il a tendance à se fissurer sous de lourdes charges.
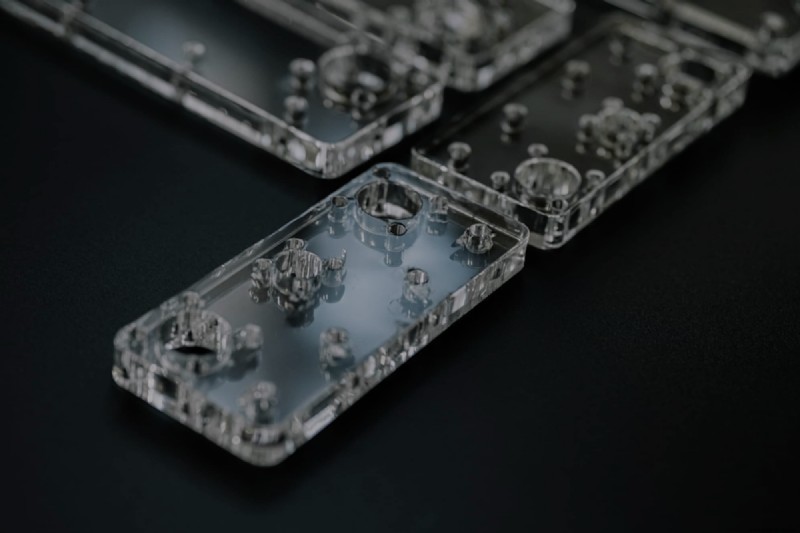
- Polyoxyméthylène (POM) : Communément connu sous le nom d'acétal ou par son nom de marque, Delrin®, ce thermoplastique semi-cristallin de qualité technique offre une excellente stabilité dimensionnelle, une rigidité et un faible frottement. En raison de ces propriétés, l'acétal est souvent utilisé pour créer des pièces très précises utilisées dans des applications nécessitant une résistance élevée, une durabilité et une large plage de températures de fonctionnement (-40 °C à 120 °C).
- Polypropylène (PP) : Ce plastique économique est léger, hautement résistant aux produits chimiques dans les environnements corrosifs et résistant à la plupart des solvants organiques, agents dégraissants et électrolytes. Comparé au LDPE et au HDPE, le PP a une résistance aux chocs inférieure mais offre une meilleure résistance à la traction.
- Polytétrafluoroéthylène (PTFE) : Le PTFE, communément appelé Teflon®, est un polymère polyvalent apprécié pour ses propriétés mécaniques. Résistant aux produits chimiques, à la température, à la lumière, aux rayons UV, à l'eau, aux intempéries, à la fatigue et à l'adhérence, le PTFE se trouve couramment dans les revêtements des poêles antiadhésives, mais est également utilisé dans les semi-conducteurs, les joints et même certaines applications médicales. Bien que le PTFE soit l'un des plastiques les plus résistants à la corrosion, il est sensible au fluage et à l'abrasion.
- Chlorure de polyvinyle (PVC) : Le PVC est l'un des plastiques les plus anciens au monde. Blanc et rigide, le PVC est une alternative au caoutchouc abordable qui est très demandée depuis des décennies. Bénéficiant d'une forte résistance à la lumière, aux produits chimiques et à la corrosion, le PVC est un matériau populaire dans les secteurs de la santé, de l'informatique, des transports, du textile et de la construction.
- Polyéthylène à poids moléculaire ultra élevé (UHMW) : Plastique résistant, polyvalent et hautement usinable, l'UHMW peut être utilisé pour créer des pièces avec une résistance élevée à l'abrasion et à l'usure, une durabilité et de faibles coefficients de frottement. L'UHMW n'est généralement pas adapté aux applications à forte charge ou aux conditions dépassant 80 à 100 °C.
Métaux
Les aciers et les aciers inoxydables, les aluminiums et les métaux doux comme le laiton, le bronze, le titane et le cuivre sont parmi les métaux usinables les plus populaires. Alors que les aciers et les aluminiums sont les plus couramment usinés, chaque famille de métaux offre un ensemble différent de propriétés physiques et de prix.
- Aluminium : Les aluminiums sont des métaux doux, de faible densité et non magnétiques qui sont beaucoup plus faciles à usiner que l'acier. En raison de leur faible résistance à la traction, ces métaux sont souvent alliés à d'autres matériaux afin d'accentuer les propriétés physiques souhaitées. Les aluminiums pèsent généralement environ 1/3 du poids de l'acier, ce qui signifie qu'ils offrent un meilleur rapport résistance/poids. Cela peut être utile pour alléger les pièces. Ils sont également de bien meilleurs conducteurs thermiques et électriques que les aciers.
- Acier : Les aciers sont des métaux à base de fer qui ont été alliés avec du carbone et d'autres métaux, notamment du manganèse, du phosphore ou du soufre. Les aciers ont tendance à être plus solides et plus durables que les aluminiums. Cependant, ils sont également plus lourds et plus difficiles à usiner sans utiliser de carbure ou d'autres outils spécialisés, ce qui peut augmenter les coûts de production.
- Acier inoxydable : La principale différence entre les aciers et les aciers inoxydables est que ce dernier est allié au chrome plutôt qu'au carbone. Alors que les aciers standard sont sensibles à la rouille et à la corrosion lorsqu'ils sont exposés à l'humidité et à l'oxygène, la teneur en chrome des aciers inoxydables crée une couche passive d'oxyde de chrome à la surface du métal, empêchant le fer à l'intérieur de s'oxyder davantage. Cela inhibe également la capacité des aciers à conduire l'électricité. Les aciers inoxydables peuvent être alliés à d'autres métaux (y compris le molybdène, le nickel ou le titane) pour augmenter la résistance d'une pièce à la corrosion et à la chaleur.
- Métaux mous : Les métaux tendres comme le laiton, le bronze, le titane et le cuivre offrent une large gamme de caractéristiques physiques attrayantes pour des applications spécifiques. Cependant, les métaux mous - en particulier ceux à forte teneur en cuivre - peuvent en fait être plus difficiles à usiner en raison de la ductilité élevée du cuivre. L'usinage de métaux doux peut contribuer à une accumulation de chaleur accrue sur le site de coupe, à une plus grande usure de l'outil et à un grippage (une accumulation de gomme sur le tranchant de l'outil). Le titane, en particulier, est également moins rigide que les autres métaux et nécessite donc une prise serrée sur la pièce à usiner pour assurer précision et exactitude. Tous ces facteurs peuvent contribuer à augmenter les coûts d'usinage des métaux tendres.
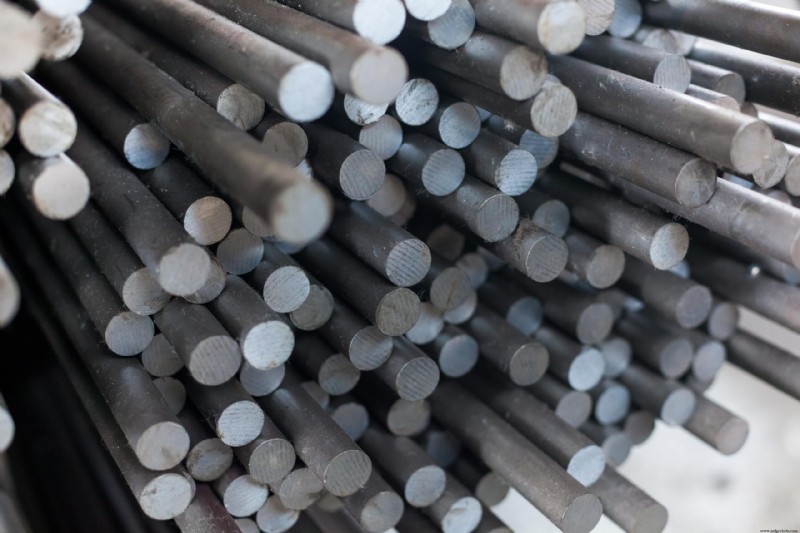
Finitions de surface CNC et post-traitement
Une fois qu'une pièce ou un composant a été usiné, il peut devoir subir un ou plusieurs processus de finition. Ces processus peuvent être utilisés pour éliminer les défauts esthétiques, améliorer l'apparence d'un produit, fournir une force et une résistance supplémentaires, ajuster la conductivité électrique, etc. Les processus de finition courants pour les pièces usinées sont l'anodisation, le revêtement en poudre et le grenaillage. Cependant, il est également courant de laisser les pièces usinées ou fraisées lorsque d'autres finitions ne sont pas nécessaires.
Options de finition CNC courantes
- Anodisation (aluminium) : L'anodisation est un processus électrochimique dans lequel des alliages d'aluminium ou de titane sont immergés dans un bain électrolytique afin d'épaissir la couche d'oxyde naturelle d'une pièce usinée pour la rendre plus dense, électriquement non conductrice et plus durable. Les finitions anodisées promettent également un bon contrôle dimensionnel, ce qui les rend mieux utilisées dans les applications d'ingénierie hautes performances, en particulier pour les cavités internes et les petites pièces. L'anodisation offre l'une des finitions les plus esthétiques pour les pièces usinées CNC, mais son prix est plus élevé.
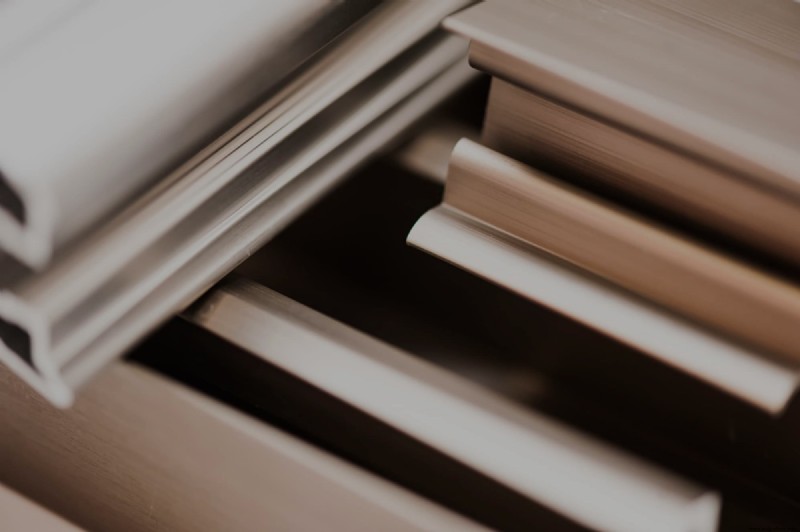
- Grenaillage (métal ou plastique) : Le grenaillage utilise un système d'air sous pression pour tirer des millions de billes de verre sur la pièce, ce qui élimine efficacement les marques d'outils et les imperfections, et peut être utilisé pour créer une finition de surface granuleuse, mate ou satinée. Le grenaillage n'ajoute aucune propriété chimique ou mécanique et, contrairement au revêtement en poudre qui ajoute de la matière à une pièce, il s'agit d'une finition réductrice, ce qui signifie que le processus enlève de la matière de la pièce. Ceci est une considération importante si votre pièce a des tolérances strictes. Le grenaillage est l'une des finitions de surface les plus abordables mais doit être exécuté manuellement. La taille et la qualité des perles affecteront également la finition finale.
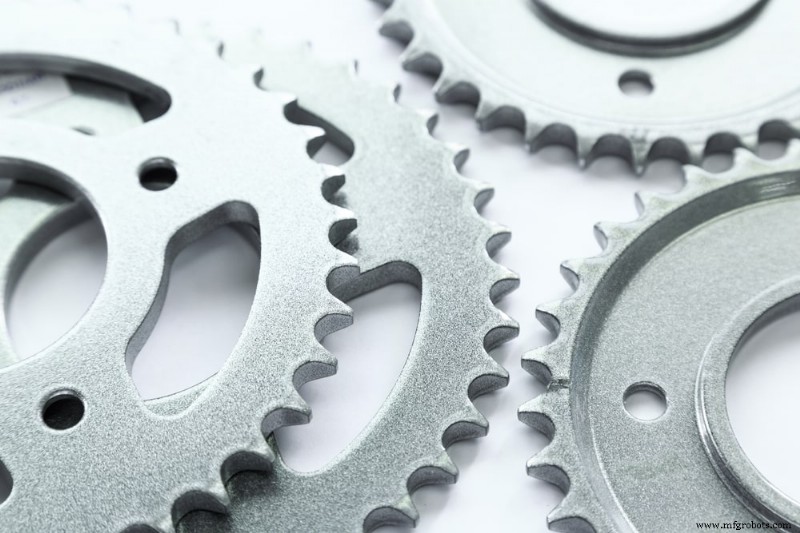
- Oxyde noir (acier, acier inoxydable, cuivre) : Ce processus de traitement électrochimique ou chimique crée de l'oxyde de fer noir à la surface des métaux ferreux. Aussi appelé noircissement, oxydation ou passivation noire, ce procédé ne se contente pas de déposer une couche d'oxyde noir à la surface du métal. Au contraire, la réaction chimique entre le fer dans le métal et la solution saline oxydante crée un oxyde de fer appelé magnétite, qui a un aspect noir mat. Ce processus améliore la stabilité dimensionnelle et l'aspect esthétique de la pièce tout en réduisant la réflexion lumineuse de la surface, ce qui est important pour les pièces utilisées dans des applications impliquant des rayonnements. L'acier noir oxydant peut également aider à affûter des outils tels que des pointes de tournevis et des forets.
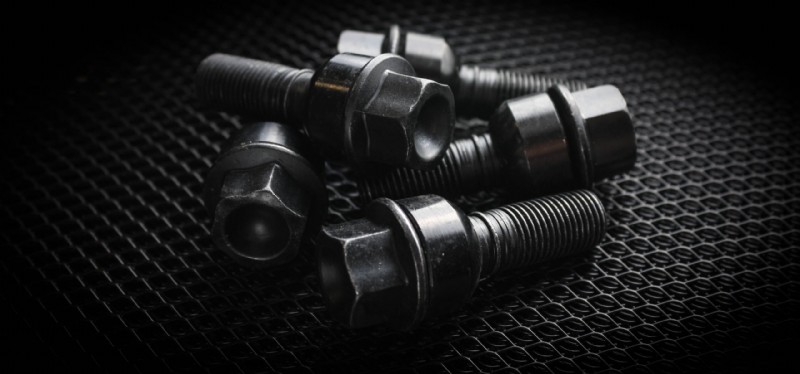
- Revêtement en poudre (tous métaux) : Le revêtement en poudre est similaire à la peinture au pistolet. La pièce usinée reçoit une couche d'apprêt pour la protéger contre la corrosion. Ensuite, la pièce est « peinte » avec un revêtement en poudre sèche à l'aide d'un pistolet de pulvérisation électrostatique et durcie dans un four chauffé à au moins 200 °C. Plusieurs couches peuvent être appliquées pour augmenter l'épaisseur de la finition, ce qui crée une fine couche protectrice sur la pièce qui est solide, résistante à l'usure et esthétique. Ce processus peut être combiné avec le grenaillage pour augmenter la résistance à la corrosion de la pièce et créer une plus grande uniformité de texture et d'apparence. Contrairement à l'anodisation, une finition thermolaquée est compatible avec tous les métaux, est moins cassante et offre une plus grande résistance aux chocs. Cependant, le revêtement en poudre donne généralement moins de contrôle dimensionnel qu'une finition anodique et n'est pas recommandé pour une utilisation dans de petits composants ou des surfaces internes. Le prix plus élevé du revêtement en poudre peut également rendre les grandes séries de production coûteuses.
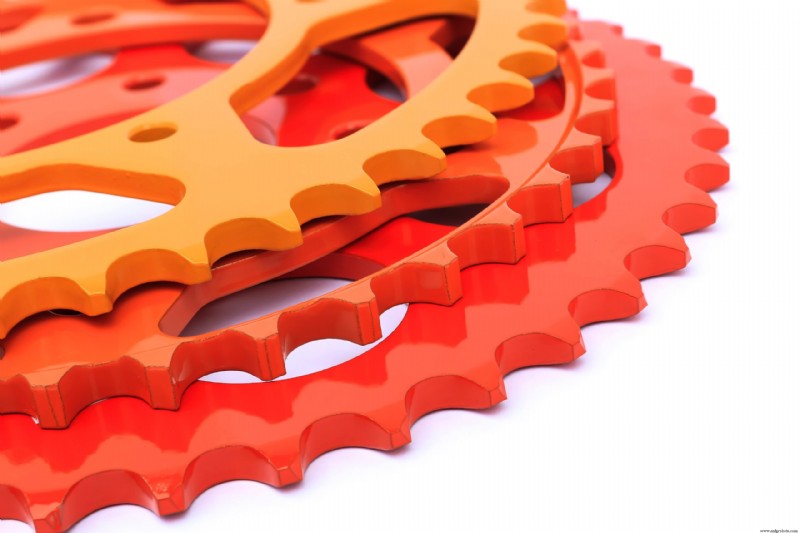
- Comme usiné (métal ou plastique) : Ne pas appliquer de processus de finition aux pièces usinées est appelé une finition "as-usined" ou "as-milled". La pièce aura des marques d'outils et des imperfections petites mais visibles. Les pièces usinées ont les tolérances dimensionnelles les plus strictes et sont extrêmement abordables à produire car le post-traitement n'est pas nécessaire. Ceci est idéal pour les applications dans lesquelles l'intégrité dimensionnelle importe plus que l'esthétique. Cependant, il est important de noter que sans finition supplémentaire ou revêtement protecteur, la dureté de surface des pièces usinées les rend susceptibles de se couper, de s'érafler et de se rayer.
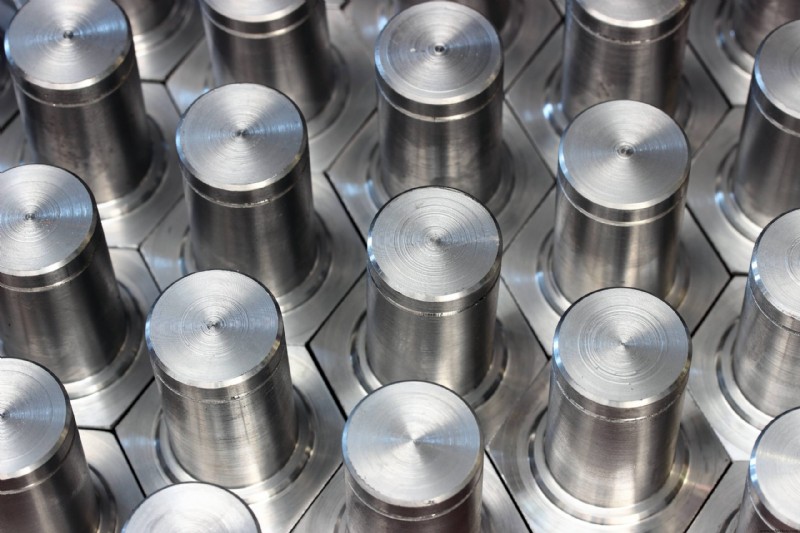
Choisir les bons matériaux et la bonne finition
La sélection des matériaux et des options de post-traitement pour votre pièce dépend fortement de la manière et de l'endroit où votre pièce sera utilisée. Les principales considérations d'utilisation finale pour la sélection du matériau de votre pièce et de la finition de surface incluent :
- Facteurs environnementaux : Les conditions environnementales de l'application d'utilisation finale d'une pièce donnée jouent un rôle important dans la détermination des matériaux et des traitements idéaux. Des facteurs tels que la chaleur, le froid, les flammes, les rayons UV, l'exposition à des produits chimiques ou l'autoclavage, etc., doivent être pris en compte afin d'assurer la viabilité de la pièce.
- Facteurs électriques : Qu'une pièce nécessite des propriétés conductrices ou isolantes est une autre considération critique. Knowing your part should conduct electricity, you may select a conductive material like copper, whereas a material like Nylon 66 would be appropriate when searching for a good insulator.
- Mechanical factors: Parts intended to endure heavy loads, wear, or other external forces need to be made from materials that can withstand those forces. Identifying the most desirable or necessary properties for a part — such as flexibility, impact resistance, tensile or compressive strength — can help teams pinpoint which materials make the best fit.
- Cosmetic considerations: While aesthetics can be of secondary priority for some parts, this is not the case for many consumer products. Some parts or applications may require materials with particular cosmetic options when it comes to color, transparency, or surface finish.
- Tolerances: Some degree of variation between parts is expected in manufacturing, and dimensional tolerances refer to the range of acceptable variation that viable parts must fall within. Tighter tolerances are more labor-intensive and costly to achieve repeatedly but may be necessary based on how a component is used.
Designing for CNC machining
Designing a high-quality part that will perform as expected is only half the challenge. You must also be able to machine the part in an efficient and cost-effective way. Design for manufacturability (DFM) is the process framework that helps integrate how a part will be made with the part design. DFM is critical to manufacturing and affects everything from production timelines and costs to operational efficiency and the quality of the part itself. The most common design considerations for CNC machining include:
Deep pockets:
Features like deep or narrow pockets and slots require longer tools to machine properly. However, longer cutting tools are more prone to breaking and are often less precise due to machining vibrations, or chatter. Deep features also typically require several cuts to machine properly, which increases both machining time and production costs — especially since smaller tools will likely be necessary to complete the finishing passes. If slots or deep pockets must be machined, aim to either reduce the depth of the feature as much as possible or increase the area of the pocket’s cross-section. The depth of a pocket or slot should be no more than 3x the diameter of the smallest tool needed.
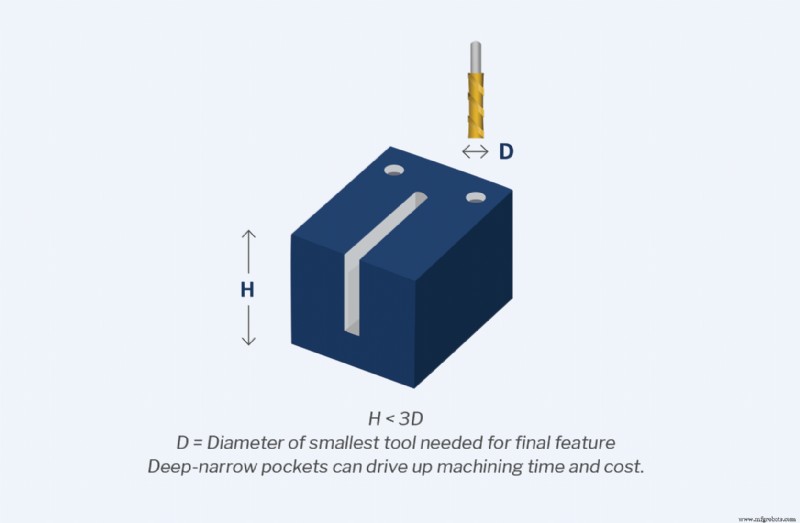
Narrow regions:
Narrow features limit the size of viable cutting tools. This can present a challenge for manufacturers because of how susceptible long, small-diameter tools are to chatter and breakage. Just as with deep features, narrow regions should be no less than 3x the diameter of the smallest cutting tool. Minimizing the depth of these features allows you to use shorter, larger-diameter cutting tools, which helps to reduce machine chatter.
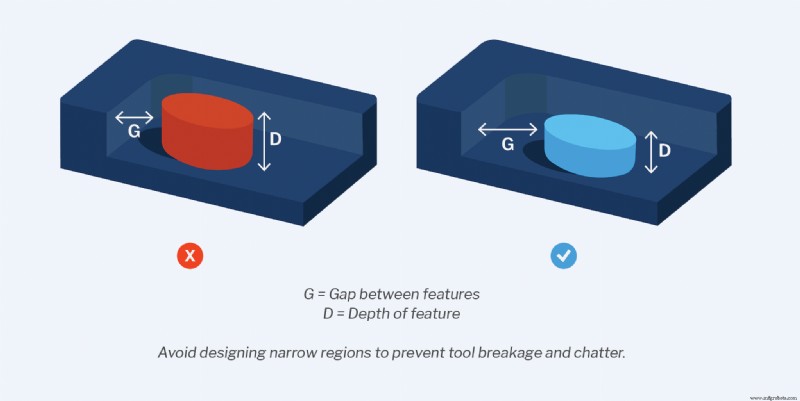
Sharp internal corners:
CNC end mills are circular, which makes it difficult to machine sharp internal corners because the bits will leave behind a corner radius. While there are methods of machining sharp internal corners, these processes tend to be costly. In general, sharp internal corners should be avoided for machined parts. Internal corner radii should also be larger than the radius of the intended cutting tool. By designing internal radii to be larger than the cutting tool, the machine can create a smooth transition between walls. In contrast, an internal radius that is the same size as the cutting tool will force the machine to make a sudden change in direction, resulting in a less smooth finish.
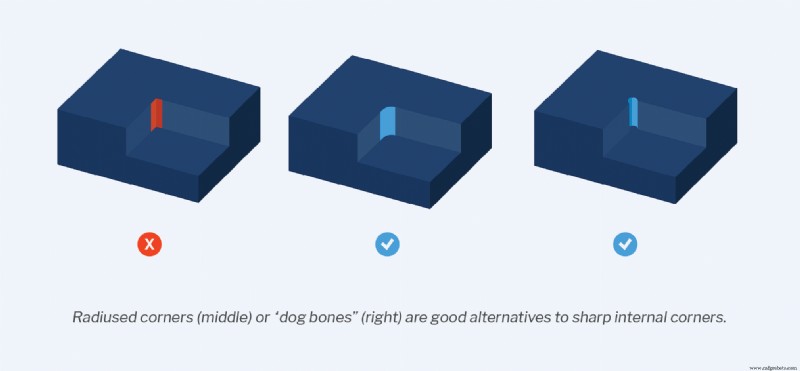
Inaccessible features:
Features like counterbores — those that open inside another pocket or pockets with negative drafts — can pose a significant challenge for production teams. These design features take considerably more time to machine because of how difficult it can be to allow the cutting tool access. It’s critical to ensure that cutting tools can freely access all of a part’s features without being blocked by any other feature.
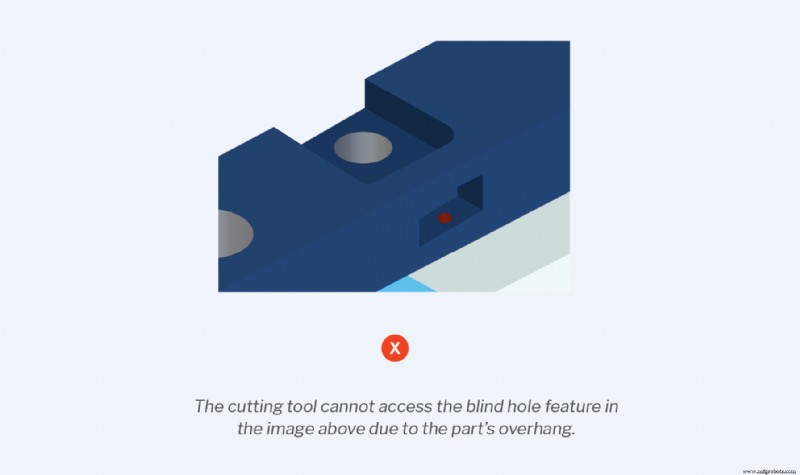
Outside fillets:
Outside fillets, or rounded corners along the top edge of pockets, bosses, slots, and other features, require custom cutting tools supported by a precise machining setup — a pairing that can quickly become expensive. Beveling or chamfering the outside edges can help avoid these costs.
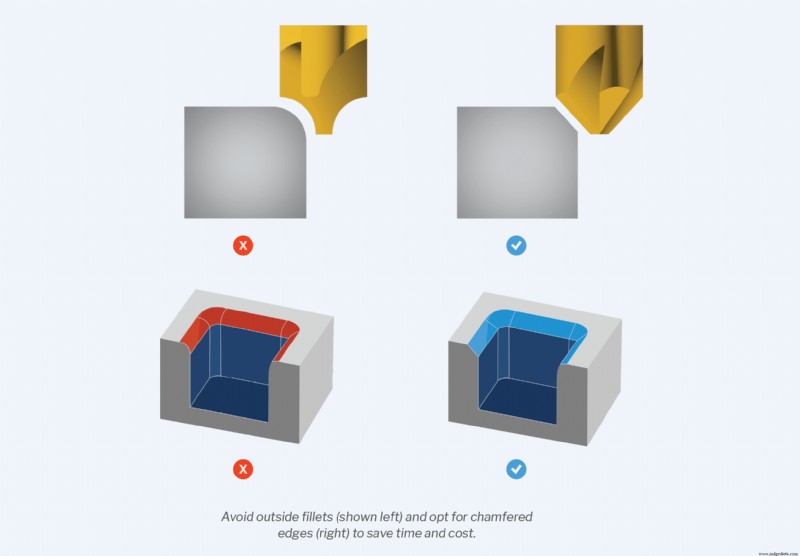
Wall thickness:
Thin walls can create issues for metal and plastic parts alike and should be avoided wherever possible. Thin metal walls are more prone to chatter, for instance, which negatively impacts the accuracy of the part and its surface finish. Plastic parts with thin walls are also more likely to warp or soften. The minimum wall thickness for metal parts should be 0.03” (0.762mm) and 0.06” (1.524mm) for plastic parts.
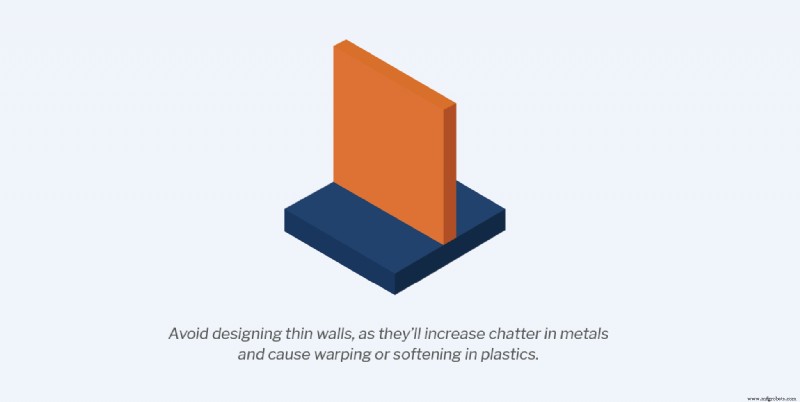
Flat-bottomed holes:
Holes with flat bottoms are not only difficult to machine, but they also tend to create difficulties for any subsequent operations. In general, product teams should avoid blind holes with flat bottoms in favor of standard twist drills, which create holes with cone-shaped bottoms.
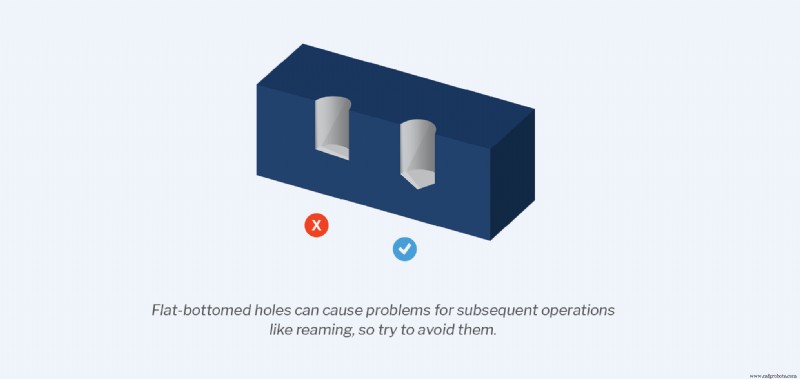
Threaded parts:
When machining internal or external threads, there are a few different design considerations.
For internal threads:
- Include a countersink at the end of internal threads.
- Reduce the number of threads whenever possible. Most of a part’s stress actually falls on the first three threads, so increasing the number
- of threads produces diminishing returns.
- Use standard forms and sizes.
- Opt for coarse threads to keep costs low.
For external threads:
- Include a chamfer in all screw designs.
- Avoid terminating near the shoulder of areas with large diameters.
- Turned external threads should have a relief groove.
- Use shorter external threads unless the part specifically calls for high thread strength.
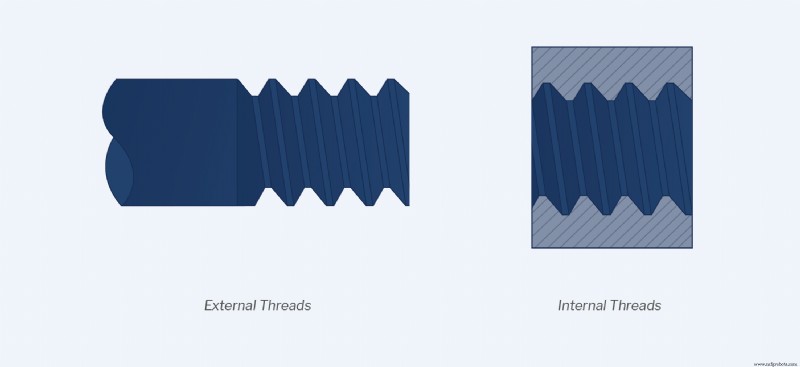
Drill entrances and exits:
If the surface of a workpiece is not perpendicular to the axis of a drill, the drill tip will wander when it comes into contact with the material. To minimize uneven exit burrs and streamline the burr-removal process, ensure that hole features have start and end faces that are perpendicular to the drill axis.
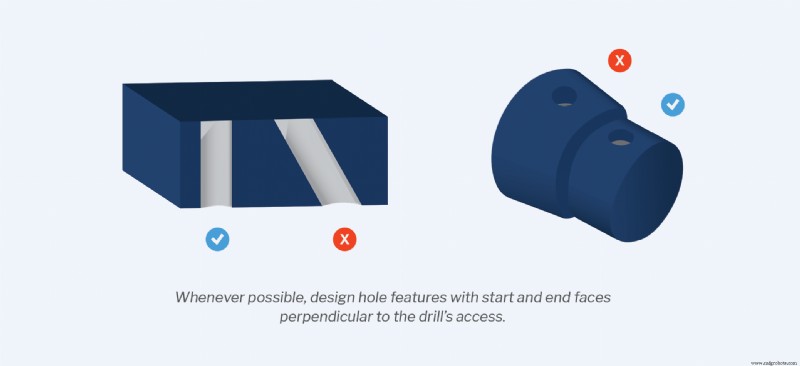
A checklist for reducing costs
1. Keep parts simple
Parts with complex designs or manufacturing processes can have a number of downstream effects. Complexity can increase machining time and cost, introduce opportunities for error, and make it difficult for end-users to understand the exact use of components or parts. Separating which characteristics and design features are vital to the viability of the part from those that are desirable yet non-critical helps remove unnecessary complexity from a part’s design and machining operations.
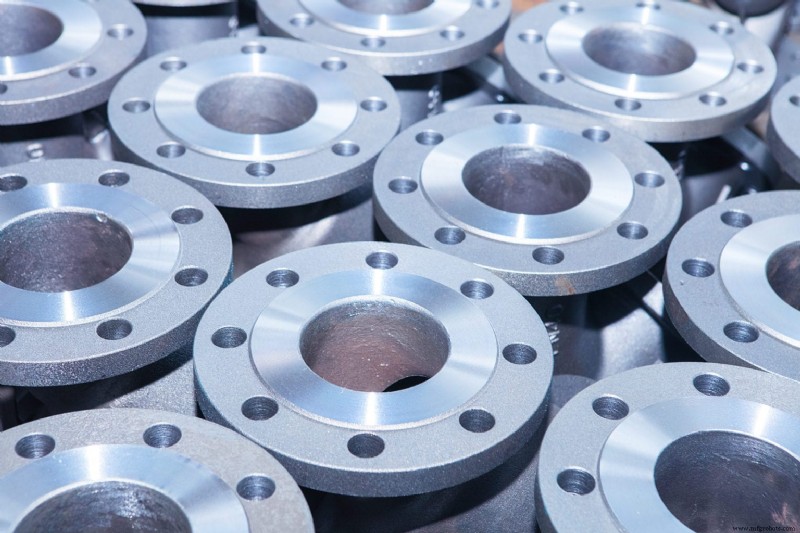
2. Design with tool geometry and setup orientation in mind
While most CNC machining jobs require more than one setup orientation, you’ll want to keep the number of orientations per part to a minimum. For example, if you need to flip a workpiece three times for the cutting tools to be able to access all of the features, this is going to increase costs because each setup requires re-mounting the part, zero-ing the machine to establish the correct axes, and running a new G-code program. 5-axis machines are going to be more capable in this aspect as they can reach more features without requiring multiple setups, though this is dependent on the geometry of a particular part.
Minimizing the number of cutting tools required is another way to reduce costs. As much as possible, try to keep radii consistent so that fewer tools are needed to machine internal corners. Likewise, avoid very small details where possible. Smaller cutting tools aren’t able to cut as deep into the workpiece and are also more prone to breaking. Typically, the smallest internal features that can be machined are 0.0394” (1mm), though holes can go as small as 0.0197” (0.5mm).
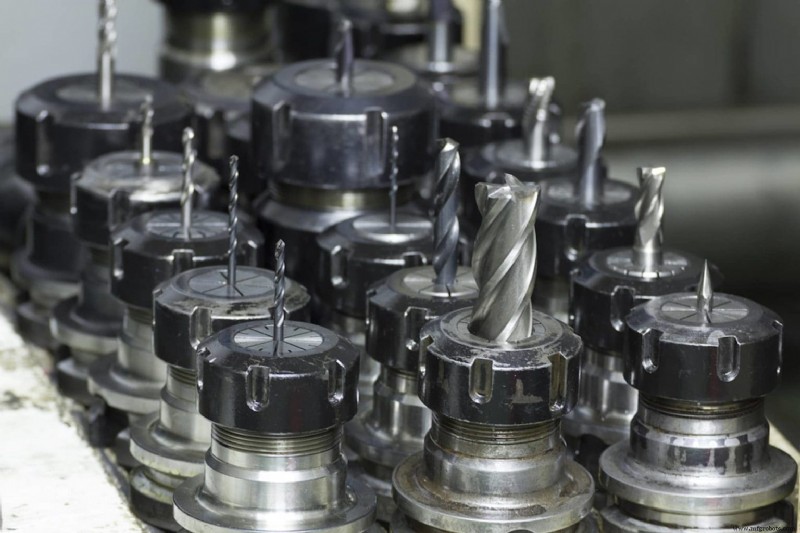
Choose your critical dimensions thoughtfully. Not every dimension requires inspection or is critical to the viability of the part, so focus your attention on those that are most essential. Determining how precise specific features need to be will allow you to adjust tolerances accordingly, reduce costs, and streamline the manufacturing process. Make sure that tolerances are still within machineable limits, adhere to given standards, and account for tolerance stacking.
Avoid over-dimensioning your part, as well. Unclear part drawings defeat the purpose of geometric dimensioning and tolerancing, which is to clarify and streamline communication. At Fast Radius, we recommend that you align drawing datums with the CNC coordinate system, as using consistent datum reference frames between machining and measurement systems is more likely to ensure parts are accurately located.
If possible, ensure all datums — points, surfaces, or axes used as references for measurement — reference the same setup. If a datum was machined in a previous setup, it becomes more difficult to hold tight tolerances after a setup change. Finally, be conscious about your datums. Choosing reference datums that are easy to measure from will ease manufacturing.
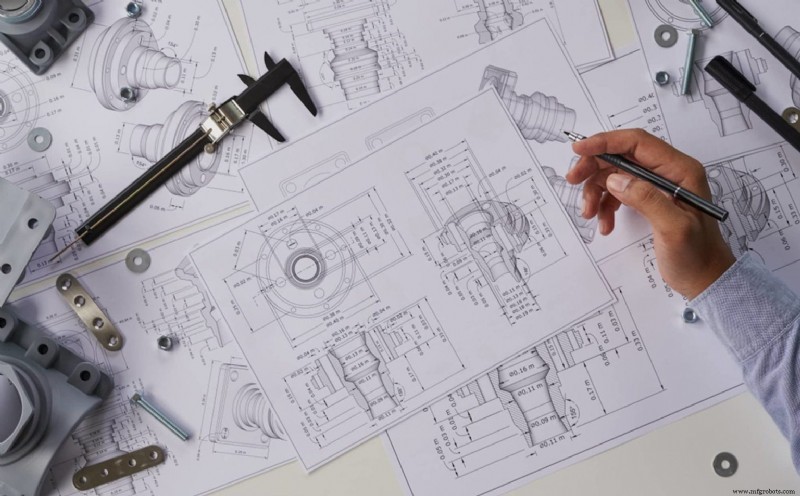
Similar to balancing your tolerances, strategically applying the right inspection levels can help reduce costs and optimize the production processes. Typical inspection options may include a visual inspection of the part, checking part dimensions using hand tools, or a first article inspection (FAI) where the first manufactured part is checked to ensure all requirements have been met. More in-depth inspections require more time and labor, which increases manufacturing costs.
Increasing the number of parts that you inspect will also increase the cost of production, so it’s important that you select the right sampling plan to ensure confidence across the entire order. At Fast Radius, our default sampling rate is based on ANSI ASQ Z1.4 Level 2.
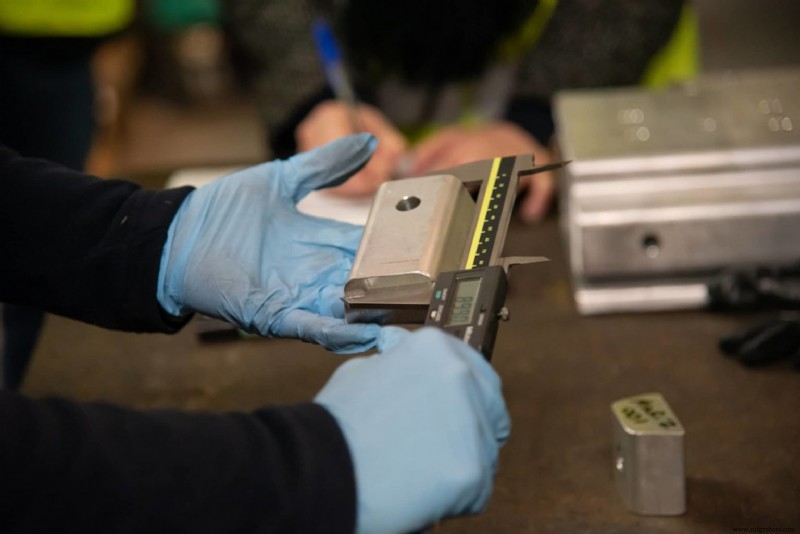
5. Design to common stock sizes
Designing parts to common stock sizes can help streamline the manufacturing process by minimizing the amount of material that needs to be removed from the workpiece. For example:if it’s acceptable for a part surface to retain its stock finish — that is, if the surface can be rougher than 125 μin Ra — and it does not need to be machined, you have an opportunity to reduce machining time without sacrificing part quality.
This is why knowing the common stock sizes for various materials is important. Metals, for instance, are typically available in a number of stock forms, including sheets, rods, bars, or tubes, which can be purchased according to dimensions like length, width, thickness, and diameter.
Keep in mind that metric sizes are more commonly available in Asia, while imperial sizes are more commonly available in the U.S.
6. Minimize deformation risk
Removing a large amount of material from a workpiece can cause the material to deform. This requires additional processing during machining to prevent deformation, leading to higher costs. Plastics have a higher risk of deformation than metals.
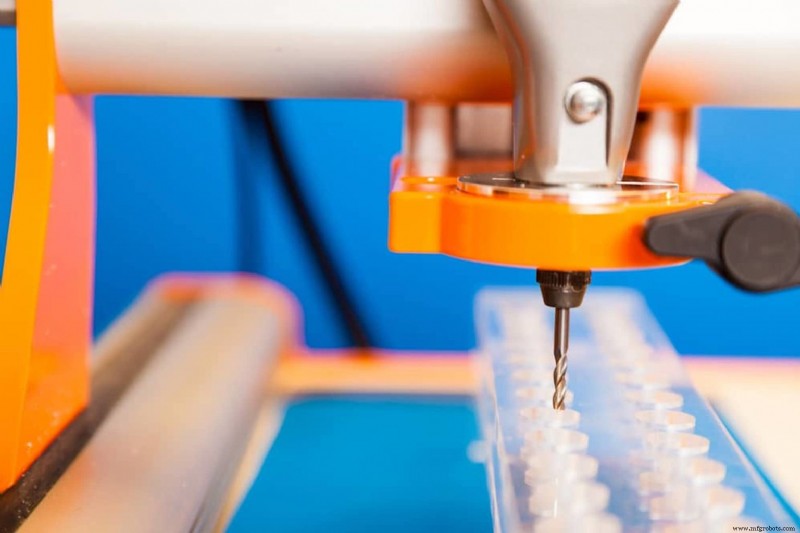
7. Choose your material carefully
The material you pick has a significant impact on the overall cost of your part. For example, metals are generally more expensive than plastics. Avoid over-engineering your parts and consider whether a specific grade or material certificate is required for the part. If a generic material can fulfill the part’s requirements or multiple materials can be accepted, select the less expensive material to keep costs low.
The machinability of the material should also be taken into consideration. Steels, for example, are typically more difficult to machine, which leads to higher costs because steel parts take longer to machine and increase wear-and-tear on cutting tools.

Common applications for CNC machining
Many industries rely on CNC machining processes to produce reliable, accurate parts that meet precise specifications and regulatory requirements, including the aerospace, automotive, medical device, electronics, and commercial parts manufacturing sectors.
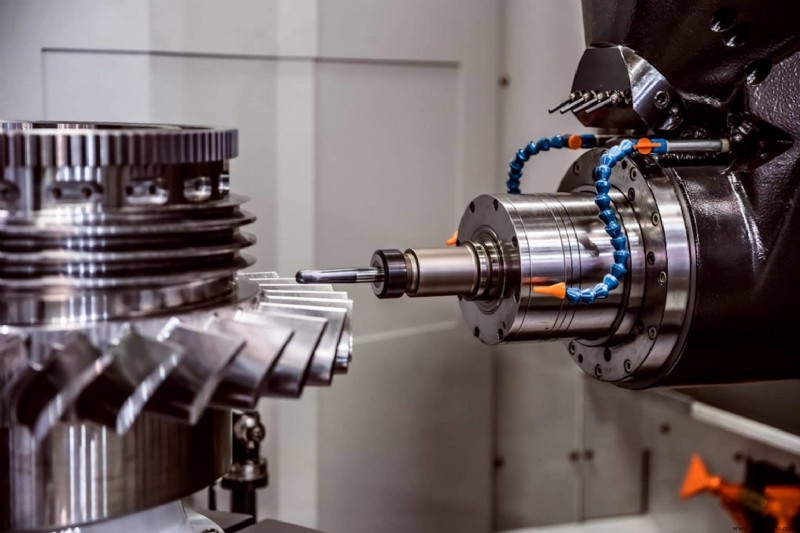
Aerospace parts are held to high quality, testing, and regulatory standards in order to ensure proper function, fit, and safety. CNC machining is an excellent fit for creating plastic and metal parts with extremely tight tolerances that satisfy the aerospace manufacturer’s need for an incredible degree of precision and a range of highly specialized parts. The same is true for automotive components.
CNC machining can also be used to create a variety of medical devices, from implants to surgical implements to components for medical electronics.
Care and precision are critical when producing these sorts of devices and tools, as they are held to additional safety standards and requirements. Semiconductors and electronics components also have incredibly stringent precision requirements and tolerance standards, given their size and complexity. As a process, CNC machining has few material limitations, allowing it to be used with conductive materials like silicon. Many commercial parts — from aluminum castings and extrusions to steel and plastic parts — can also be machined.
Another common application for CNC machining is tooling, or the process of creating the various components, tools, machinery, and master patterns that will be used in production. Tooling is an integral part of every manufacturing and molding process and encompasses items like molds, jigs, and fixtures.
Starting your CNC machining project with Fast Radius
At Fast Radius, we make it simple and straightforward to get quality parts through our CNC machining service. To get started, visit os.fastraidus.com, upload your part designs, and you’ll receive instant DFM feedback. The site also allows you to manage designs and orders from a single, intuitive interface.
When you choose Fast Radius, you’re choosing to work with a seasoned group of experts. You’ll receive the full support of our team of engineers, customer success managers, account executives, and others across the business. We’ll also leverage options for domestic and international CNC machining to ensure that your project is carried out as efficiently as possible, without sacrificing quality.
Contact us today to experience the Fast Radius difference or click here to download our comprehensive guide as a PDF.
Prêt à fabriquer vos pièces avec Fast Radius ?
Commencez votre devisTechnologie industrielle
- Le guide essentiel de l'usinage CNC 5 axes
- Usinage CNC dans l'industrie automobile
- Qu'est-ce que l'AIaaS ? Le guide ultime de l'IA en tant que service
- Électricité froide :guide ultime sur les bases
- Traçage de circuit :le guide ultime
- Le coût de l'usinage CNC
- Le guide complet de la fraiseuse CNC à 5 axes
- L'avenir de l'usinage CNC
- Usinage CNC 5 axes :le guide complet