Qu'est-ce que le processus de traitement thermique - types, méthodes, avantages
Dans cet article, nous allons apprendre qu'est-ce que processus de traitement thermique et aussi sur les différents types de procédés de traitement thermique en détail.
Qu'est-ce que le processus de traitement thermique ?
Traitement thermique fait référence à une combinaison de chauffage et de refroidissement d'un métal ou d'un alliage à l'état solide dans le but d'obtenir les propriétés souhaitées. Les changements de propriétés résultent de changements microstructuraux du matériau produit par les opérations de traitement thermique.
Le traitement thermique est le processus de chauffage et de refroidissement des métaux, en utilisant des méthodes spécifiques prédéterminées pour obtenir les propriétés souhaitées. Les métaux ferreux et non ferreux subissent un traitement thermique avant d'être utilisés. Au fil du temps, de nombreuses méthodes différentes ont été développées. Aujourd'hui encore, les métallurgistes s'efforcent constamment d'améliorer les résultats et la rentabilité de ces processus.
Pour cela, ils développent de nouveaux horaires ou cycles pour produire une variété de grades. Chaque programme fait référence à un taux différent de chauffage, de maintien et de refroidissement du métal. Ces méthodes, lorsqu'elles sont suivies méticuleusement, peuvent produire des métaux de différentes normes avec des propriétés physiques et chimiques remarquablement spécifiques.
Bases du traitement thermique
Bien que le fer et l'acier constituent la grande majorité des matériaux traités thermiquement, les alliages d'aluminium, de cuivre, de magnésium, de nickel et de titane peuvent également être traités thermiquement.
Les processus de traitement thermique nécessitent trois étapes de base. Ou nous pouvons dire que l'étape du traitement thermique est :
- Chauffage à une température spécifiée
- Maintien à cette température pendant la durée appropriée
- Refroidissement selon les méthodes prescrites
Les températures peuvent aller jusqu'à 2 400 °F et le temps à température peut varier de quelques secondes à 60 heures ou plus .
Dans le four, certains matériaux sont refroidis lentement, tandis que d'autres doivent être trempés . Traitement à -120 °F ou moins est requis pour certains procédés cryogéniques . L'eau, la saumure, les huiles, les solutions de polymères, les sels fondus, les métaux fondus et les gaz sont quelques exemples de milieux de trempe. Chacun a son propre ensemble de caractéristiques qui le rendent idéal pour des tâches spécifiques. 90 % des pièces, en revanche, sont trempées dans de l'eau, de l'huile, du gaz ou des polymères.
R. Étape de chauffage
Lors de la phase de chauffage, l'objectif principal est de s'assurer que le métal chauffe uniformément. Le chauffage lent assure un chauffage uniforme. Si vous chauffez le métal de manière inégale, une section peut se dilater plus rapidement qu'une autre, entraînant une section de métal déformée ou fissurée. Vous sélectionnez le taux de chauffage en fonction des facteurs suivants :
1. La conductivité thermique du métal : Les métaux à haute conductivité thermique chauffent plus rapidement que ceux à faible conductivité.
2. État du métal : Les outils et les pièces qui ont déjà été durcis ou sollicités doivent être chauffés à un rythme plus lent que les outils et les pièces qui ne l'ont pas été.
B. L'étape de trempage
Le but de l'étape de trempage est de maintenir le métal à la bonne température jusqu'à ce que la structure interne souhaitée prenne forme. La "période de trempage » fait référence à la durée pendant laquelle le métal est maintenu à la température appropriée. Vous aurez besoin de l'analyse chimique et de la masse du métal pour déterminer la durée correcte. La période de trempage pour les sections transversales inégales peut être déterminée en utilisant la plus grande section.
En général, vous ne devez pas faire passer la température du métal de la température ambiante à la température de trempage en une seule étape. Au lieu de cela, chauffez lentement le métal juste en dessous de la température à laquelle la structure va changer, puis maintenez-le jusqu'à ce que la température soit constante dans tout le métal. Après ce "préchauffage ", vous pouvez rapidement chauffer la température jusqu'à la température finale dont vous aurez besoin. Pour éviter le gauchissement, les pièces aux conceptions plus complexes peuvent nécessiter plusieurs couches de préchauffage.
C. Étape de refroidissement
Pendant la phase de refroidissement, vous voudrez ramener le métal à température ambiante, mais il existe différentes façons de le faire selon le type de métal. Il peut nécessiter un milieu de refroidissement, tel qu'un gaz, un liquide, un solide ou une combinaison de ceux-ci. La vitesse de refroidissement est déterminée par le métal et le milieu utilisé pour le refroidissement. Par conséquent, les options de refroidissement que vous choisissez ont un impact significatif sur les propriétés souhaitées du métal.
Trempe est le refroidissement rapide du métal dans l'air, l'huile, l'eau, la saumure ou un autre milieu. La plupart des métaux qui sont durcis sont refroidis rapidement avec la trempe, de sorte que la trempe est généralement associée au durcissement; cependant, la trempe ou un autre refroidissement rapide n'entraîne pas toujours un durcissement. Le cuivre, par exemple, est recuit par trempe à l'eau, et les autres métaux sont durcis par refroidissement lent.
Objectif du traitement thermique
Cependant, ceux-ci servent un ou plusieurs des objectifs suivants :
- Améliorer l'usinabilité
- Soulage les tensions internes.
- Améliorer les propriétés mécaniques telles que la ductilité, la résistance, la dureté, la ténacité, etc.
- Modifiez la taille du grain.
- Augmente la résistance à la chaleur et à la corrosion.
- Modifier les propriétés électriques et magnétiques.
- Modifier la composition chimique.
- Éliminer les gaz
Avantages du traitement thermique
Après traitement thermique, les matériaux sont :
- Produit plus durable.
- L'acier devient plus dur, plus fort.
- Plus facile à souder.
- Devient plus flexible.
- Augmente sa résistance à l'usure.
- Augmentation de la durée de vie globale de la pièce.
Le traitement thermique est effectué pour diverses raisons. Certaines procédures ramollissent le métal, tandis que d'autres le durcissent. Ils peuvent également avoir un impact sur la conductivité électrique et thermique de ces matériaux.
Certaines méthodes de traitement thermique soulagent les contraintes causées par les processus de travail à froid précédents. D'autres ajoutent des propriétés chimiques souhaitables aux métaux. Le choix de la meilleure méthode est finalement déterminé par le type de métal et les propriétés requises.
Une pièce métallique peut être soumise à plusieurs traitements thermiques dans certains cas. Certains superalliages utilisés dans l'industrie aéronautique, par exemple, peuvent subir jusqu'à six étapes de traitement thermique différentes pour être optimisés pour l'application.
Types de processus de traitement thermique
Les finalités de traitement thermique précitées peuvent être servies par un ou plusieurs des procédés de traitement thermique suivants :
3. Durcissement
4. Trempe
5. Cémentation :
a.) Carburation
b.) Cyanure
c.) Nitruration
6. Durcissement superficiel
a.) Trempe par induction
b.) Trempe à la flamme
7. Revêtement diffusant
1. Recuit
Recuit est l'une des opérations les plus importantes largement utilisées dans le traitement thermique de l'acier.
Le recuit est un traitement thermique en métallurgie et en science des matériaux qui modifie les propriétés physiques et parfois chimiques d'un matériau pour augmenter sa ductilité et réduire sa dureté, le rendant plus maniable. Cela implique de chauffer un matériau au-dessus de sa température de recristallisation, de maintenir cette température pendant une durée appropriée, puis de refroidir.
Le but du recuit est d'obtenir un ou plusieurs des effets suivants :
- Adoucir l'acier.
- Améliorer l'usinabilité.
- Augmenter ou restaurer la ductilité et la ténacité.
- Soulage les tensions internes.
- Réduire ou éliminer l'inhomogénéité structurelle.
- Affiner la granulométrie
- Préparez l'acier pour le traitement thermique ultérieur.
2. Normalisation
Normaliser est un processus de traitement thermique utilisé pour rendre un métal plus ductile et plus résistant après qu'il a été durci thermiquement ou mécaniquement. La normalisation est le processus consistant à chauffer un matériau à une température élevée, puis à le laisser refroidir à température ambiante en l'exposant à de l'air à température ambiante après qu'il a été chauffé. Ce chauffage et ce refroidissement lent modifient la microstructure du métal, abaissant sa dureté et augmentant sa ductilité.
Lorsque l'acier est froid, la structure est déformée et le métal peut être cassant et peu fiable. La structure interne d'une pièce forgée travaillée à chaud peut également être déformée du fait d'un travail à très basse température. On voit également qu'une température de finition variable se traduira par une structure variable pour des pièces forgées de même teneur en carbone. De même, si une pièce moulée est coulée à une température quelque peu indéfinie et se refroidit à des vitesses différentes dans différentes parties, elle peut ne pas être fiable. La normalisation est donc particulièrement utilisée pour les éléments suivants
Le but de la normalisation est d'obtenir un ou plusieurs des effets suivants :
- Pour éliminer la structure à gros grains.
- Pour éliminer les contraintes internes pouvant avoir été causées par le travail
- Pour améliorer les propriétés mécaniques de l'acier
En plus de tous ces usages, il peut être utilisé pour augmenter dans une certaine mesure la résistance des aciers moyennement carbonés (par rapport aux aciers recuits), pour améliorer l'usinabilité des aciers bas carbone, pour améliorer la structure des soudures, etc.
3. Durcissement
L'opération de durcissement s'applique à tous les outils et à certaines pièces de machines importantes destinées à un service particulièrement intensif ainsi qu'à toutes les pièces de machines en acier allié.
Les finalités de la trempe avec revenu ultérieur sont :
2. Pour améliorer la résistance, l'élasticité, la ductilité et la ténacité.
Le processus consiste à :
1. Chauffer l'acier à une température supérieure au point critique.
2. Maintien à cette température pendant une période considérable.
3. Trempe (changement rapide) en bain d'eau, d'huile ou de sel fondu.
4. Trempe
Tempérer , en métallurgie, processus d'amélioration des propriétés d'un métal, en particulier de l'acier, en le chauffant à une température élevée, mais inférieure au point de fusion, puis en le refroidissant, généralement à l'air. Le processus durcit en réduisant la fragilité et les contraintes internes.
Lorsqu'une pièce d'acier est retirée du milieu de trempe, comme déjà indiqué, elle est dure, cassante et aura des contraintes internes sévères inégalement réparties en plus d'autres caractéristiques défavorables. En général, le revenu restaure la ductilité et réduit la dureté et entraîne une certaine diminution de la dureté. Les principaux objets de la trempe sont donc les suivants :
- Pour stabiliser la structure du métal.
- Pour réduire les contraintes internes produites lors du chauffage précédent.
- Pour réduire une partie de la dureté produite lors du durcissement et pour augmenter la ductilité du métal.
- Pour donner au métal huit conditions structurelles combinées à la ténacité et à la résistance aux chocs.
Le traitement de revenu nécessite :
- Réchauffage de l'acier après durcissement à des températures inférieures au point Ac1 (ligne psk sur la fig 6.6
- Tenir le bit pendant un temps considérable.
- Refroidissement lent. Il est souhaitable que la température de l'acier soit maintenue pendant au moins 4 à 5 minutes pour chaque millimètre de la section.
5. Cémentation
R. Carburation
La plus ancienne méthode connue pour produire une surface dure sur l'acier est la cémentation ou carburation . L'acier utilisé à cette fin est généralement un acier à faible teneur en carbone d'environ 0,15 % de carbone, qui ne répond pas de manière appréciable au traitement thermique. Au cours du processus, la couche externe est convertie en un acier à haute teneur en carbone avec une teneur en carbone allant de 0,9 à 1,2 % de carbone. S'il reçoit un traitement thermique approprié, il aura une surface extrêmement dure à l'extérieur et un noyau souple et ductile.
B. Cyanure
Cyanure est un processus de production de surface dure sur des aciers à faible ou moyenne teneur en carbone en immergeant l'acier dans un bain de sel fondu contenant du cyanure maintenu à 800 ° C à 900 ° C, puis en trempant l'acier dans de l'eau ou de l'huile. La dureté produite par ce traitement est due à la présence de composés d'azote ainsi que de carbone dans la couche superficielle.
C. Nitruration
Nitruration est un processus de production d'une couche de surface dure sur des aciers alliés uniquement, la nitruration consiste essentiellement à chauffer l'acier dans une atmosphère de gaz ammoniac à une température de 500°C à 650°C sans autre traitement thermique. L'ammoniac est dissocié et l'azote naissant se combine avec les éléments de l'acier pour former des nitrures. Ces nitrures donnent une dureté extrême à la surface. Une couche de surface dure généralement de 0,2 à 0,4 mm de profondeur est produite en 50 heures.
La nitruration est la dernière opération après le processus de mise en forme et de traitement thermique. Ainsi après forgeage, la suite des opérations est :(a) durcissement à l'huile de 850°C à 900°C, (b) revenu de 600 °C à 650 °C, (c) usinage d'ébauche, (d) stabilisation (pour éliminer les contraintes internes) à 525 °C à 550 °C, (e) l'usinage final et finalement, (f) nitruration.
La nitruration est utilisée sur de nombreuses pièces d'usure de moteurs automobiles, d'avions et de moteurs diesel, ainsi que sur de nombreuses pièces diverses telles que les arbres de pompe, les jauges, les matrices d'étirage, les engrenages, les embrayages et les mandrins. Son utilisation est limitée par les dépenses nécessaires au traitement et le boîtier relativement fin obtenu.
6. Durcissement de surface
R. Trempe par induction
Induction le chauffage s'est avéré satisfaisant pour de nombreuses opérations de durcissement superficiel telles que requises sur les zones d'appui des vilebrequins, des arbres à cames, des arbres d'essieu et des surfaces d'usure similaires. Elle diffère de la pratique courante de la cémentation en ce que l'analyse de l'acier de surface n'est pas modifiée, la trempe étant réalisée par un chauffage et une trempe extrêmement rapides de la surface d'usure qui n'ont aucun effet sur l'âme intérieure. La dureté obtenue en trempe par induction est la même que celle obtenue en traitement conventionnel et dépend de la teneur en carbone.
B. Durcissement à la flamme
Le processus de durcissement de l'acier en le chauffant avec la flamme d'un chalumeau oxyacétylénique est connu sous le nom de durcissement à la flamme qui, comme le processus de trempe par induction, est basé sur un chauffage rapide et une trempe de la surface par l'eau. La flamme est dirigée vers la partie souhaitée sans chauffer efficacement le reste de l'œuvre pour l'affecter. Les avantages en faveur de son application sont les suivants :
- Parce qu'il chauffe rapidement, le chauffage à la flamme est pratique lorsque la dureté n'est requise que pour une profondeur limitée, le reste conservant sa ténacité et sa ductilité d'origine.
- Le chauffage à la flamme rend possible et pratique le durcissement d'une partie ou de la totalité d'une pièce trop grande ou trop peu pratique pour être placée dans un four.
- Le temps nécessaire au chauffage est moindre avec le chauffage à la flamme qu'avec un four
7. Revêtement de diffusion
Revêtement diffusant , ou cémentation métallique , est le processus d'imprégnation de la surface de l'acier avec de l'aluminium, du chrome, du silicium, du bore, du béryllium et d'autres éléments.
Le revêtement par diffusion est réalisé en chauffant et en maintenant des pièces en acier en contact direct avec l'un des éléments ci-dessus qui peut être à l'état solide, liquide ou gazeux. Ce processus confère un certain nombre de propriétés précieuses à l'acier, parmi lesquelles une résistance élevée à la chaleur, à la corrosion et à l'usure. Dans de nombreux cas, l'acier soumis à un revêtement par diffusion peut être utilisé comme substitut d'un acier fortement allié.
Diagramme de phases
Chaque alliage métallique a son propre diagramme de phase. Comme indiqué précédemment, le traitement thermique est effectué conformément à ces schémas. Ils décrivent les changements structurels qui se produisent à différentes températures et compositions chimiques.
Prenons l'exemple du diagramme de phase fer-carbone car c'est le plus connu et le plus enseigné dans les universités.
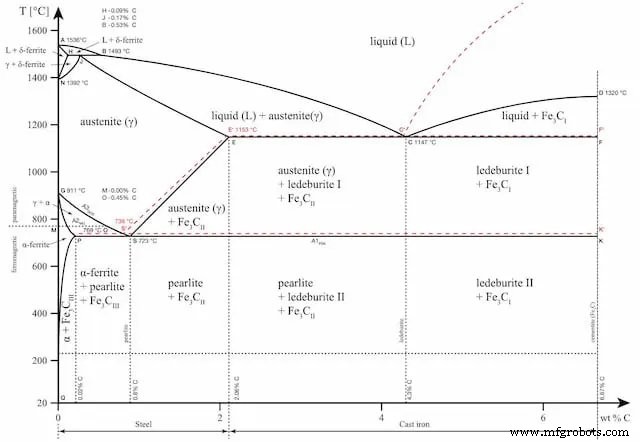
Le diagramme de phase fer-carbone est un outil utile pour connaître le comportement au traitement thermique de divers aciers au carbone. L'axe des x représente la teneur en carbone de l'alliage, tandis que l'axe des y représente la température.
Notez que la limite à laquelle l'acier devient de la fonte est de 2,14 % de carbone.
Le diagramme représente diverses régions où le métal peut être trouvé dans divers micro-états tels que l'austénite, la cémentite et la perlite. Ces zones sont désignées par les limites A1, A2, A3 et Acm. Lorsque la valeur de température ou de teneur en carbone passe par ces interfaces, des changements de phase se produisent.
- A1 :la limite supérieure de la phase cémentite/ferrite.
- A2 :La limite où le fer perd son magnétisme. La température à laquelle un métal perd son magnétisme est également appelée température de Curie.
- A3 :L'interface qui sépare la phase Austénite + Ferrite de la phase austénite γ (Gamma).
- Acm :L'interface qui sépare l'Austénite γ du champ Austénite + Cémentite.
Le diagramme de phase est un outil important pour déterminer si le traitement thermique sera bénéfique ou non. Chaque structure apporte des qualités différentes au produit final, et le traitement thermique est choisi en conséquence.
Étapes du processus de traitement thermique
En termes simples, le traitement thermique consiste à chauffer le métal, à le maintenir à cette température, puis à le refroidir. Au cours du processus, la pièce métallique subira des modifications de ses propriétés mécaniques. En effet, la température élevée modifie la microstructure du métal. Et la microstructure joue un rôle important dans les propriétés mécaniques d'un matériau.
Le résultat final dépend de nombreux facteurs différents. Ceux-ci incluent le temps de chauffage, le temps de maintien de la pièce métallique à une certaine température, la vitesse de refroidissement, les conditions environnantes, etc. Les paramètres dépendent de la méthode de traitement thermique, du type de métal et de la taille de la pièce.
Au cours de ce processus, les propriétés du métal changeront. Parmi ces propriétés figurent la résistance électrique, le magnétisme, la dureté, la ténacité, la ductilité, la fragilité et la résistance à la corrosion.
Chauffage
- Pièces métalliques mises au four
- Pièces de moteur à réaction entrant dans un four
- Comme nous en avons déjà discuté, la microstructure des alliages changera pendant le traitement thermique. Le chauffage est effectué selon un profil thermique prescrit
- Un alliage peut exister dans l'un des trois états différents lorsqu'il est chauffé. Il peut s'agir d'un mélange mécanique, d'une solution solide ou d'une combinaison des deux.
- Un mélange mécanique est analogue à un mélange de béton où le ciment lie le sable et le gravier ensemble. Le sable et le gravier sont toujours visibles sous forme de particules distinctes. Avec les alliages métalliques, le mélange mécanique est maintenu par le métal de base.
- En revanche, dans une solution solide, tous les composants sont mélangés de manière homogène. Cela signifie qu'ils ne peuvent pas être identifiés individuellement, même au microscope.
- Chaque état apporte des qualités différentes. Il est possible de changer l'état par chauffage selon le diagramme de phases. Le refroidissement, cependant, détermine le résultat final. Il est possible que l'alliage se retrouve dans l'un des trois états, en fonction uniquement de la méthode.
Tenir
- Pendant la phase de maintien, ou trempage , le métal est maintenu à la température atteinte. La durée dépend de l'exigence.
- Par exemple, la cémentation ne nécessite que des changements structurels à la surface du métal afin d'augmenter la dureté de surface. Dans le même temps, d'autres méthodes nécessitent des propriétés uniformes. Dans ce cas, la période de détention est plus longue.
- Le temps de trempage dépend également du type de matériau et de la taille de la pièce. Les pièces plus grandes nécessitent plus de temps lorsque l'objectif est d'avoir des propriétés uniformes. Il faut juste plus de temps pour que le cœur d'une grande pièce atteigne la température requise.
Refroidissement
- Une fois l'étape de trempage terminée, le métal doit être refroidi de la manière prescrite. A ce stade également, des changements structurels se produisent. Une solution solide lors du refroidissement peut rester la même, devenir un mélange mécanique complètement ou partiellement, en fonction de divers facteurs.
- Différents fluides tels que la saumure, l'eau, l'huile ou l'air forcé contrôlent la vitesse de refroidissement. La séquence des milieux de refroidissement nommés ci-dessus est dans l'ordre décroissant du taux effectif de refroidissement. La saumure absorbe la chaleur le plus rapidement, tandis que l'air est le plus lent.
- Il est également possible d'utiliser des fours dans le processus de refroidissement. L'environnement contrôlé permet une grande précision lorsqu'un refroidissement lent est nécessaire.
Quels métaux conviennent au traitement thermique ?
Bien que les métaux ferreux représentent la majorité des matériaux traités thermiquement, les alliages de cuivre, de magnésium, d'aluminium, de nickel, de laiton et de titane peuvent également être traités thermiquement.
Environ 80 % des métaux traités thermiquement sont des nuances d'acier différentes. La fonte, l'acier inoxydable et diverses qualités d'acier à outils sont tous des métaux ferreux qui peuvent être traités thermiquement.
Les métaux ferreux sont généralement soumis à des processus tels que le durcissement, le recuit, la normalisation, la relaxation des contraintes, la cémentation, la nitruration et le revenu.
Les méthodes de traitement thermique telles que le recuit, le vieillissement et la trempe sont utilisées sur le cuivre et les alliages de cuivre.
L'aluminium convient au recuit, au traitement thermique en solution, au vieillissement naturel et artificiel et à d'autres méthodes de traitement thermique. Le traitement thermique de l'aluminium est un processus précis. La portée du processus doit être établie et il doit être soigneusement contrôlé à chaque étape pour s'assurer que les caractéristiques souhaitées sont atteintes.
Évidemment, tous les matériaux ne sont pas adaptés aux différents types de traitement thermique. De même, un seul matériau peut ne pas bénéficier de toutes les méthodes. Par conséquent, chaque matériau doit être étudié séparément afin d'obtenir le résultat souhaité. Le point de départ consiste à utiliser des diagrammes de phase et les informations disponibles sur les effets des méthodes susmentionnées.
Traitement thermique des aciers
Le traitement thermique de l'acier est le chauffage et le refroidissement des métaux pour modifier leurs propriétés physiques et mécaniques sans les faire changer de forme. Le traitement thermique est une méthode de renforcement des matériaux, mais il peut également être utilisé pour modifier les propriétés mécaniques telles que la formabilité, l'usinage, etc.
L'application la plus courante est la métallurgie, mais le traitement thermique des métaux peut également être utilisé dans la production de verre, d'aluminium, d'acier et de divers autres matériaux.
Nous avons essayé de couvrir tous les aspects du traitement thermique en commençant par le processus de traitement thermique, puis les types de processus de traitement thermique, y compris les méthodes telles que le recuit, la cémentation, la trempe, la normalisation et bien d'autres. Nous avons également discuté des avantages et des inconvénients du processus de traitement thermique.
Si vous avez aimé l'article, veuillez le partager avec vos amis.
Technologie industrielle
- Qu'est-ce que l'anticrénelage ? 6 types et méthodes différents
- Qu'est-ce que l'estampage ? - Types, fonctionnement et application
- Qu'est-ce que le casting ? - Définition | Types de coulée
- Qu'est-ce que le forgeage ? - Définition, processus et types
- Qu'est-ce que le placage métallique ? - Définition, types et avantages
- Qu'est-ce que la galvanisation ? - Définition, méthodes, processus
- Qu'est-ce que le traitement thermique ? - Processus et méthodes
- Qu'est-ce que la coulée de métal ? - Définition, types et processus
- Qu'est-ce qu'un numéro de manche ?