Entretien d'experts :Duncan McCallum, PDG de Digital Alloys, sur l'impression Joule et l'avenir de l'impression 3D sur métal
L'essor de l'impression 3D métal au cours de la dernière année a été bien documenté. Avec l'arrivée rapide de nouveaux acteurs sur le marché, Digital Alloys est l'une des entreprises qui contribuent à cette évolution. Fondée en 2017, Digital Alloys a développé sa technologie brevetée d'impression Joule pour la fabrication additive métallique à grande vitesse. La technologie promet des vitesses de production plus rapides, des coûts inférieurs et des pièces de haute qualité rivalisant avec la fabrication conventionnelle. Après avoir obtenu avec succès un tour de table de 12,9 millions de dollars de série B cette année, la société semble certainement en bonne voie pour perturber le marché de l'impression 3D métal.
Nous nous sommes entretenus avec le PDG de Digital Alloys, Duncan McCallum, pour en savoir plus sur Joule Printing et ses réflexions sur l'avenir de l'impression 3D métal.
Les alliages numériques ont récemment fait la une des journaux avec l'annonce de deux nouveaux brevets pour sa technologie d'impression Joule. Pourriez-vous expliquer comment fonctionne la technologie ?
Tout d'abord, je vais commencer par le problème que nous résolvons :il n'y a tout simplement pas beaucoup de bonnes options aujourd'hui si vous souhaitez utiliser l'impression 3D pour la production. En effet, les systèmes sont trop lents, les coûts de production sont trop élevés et les processus sont trop complexes. Cela rend difficile l'obtention de pièces métalliques de haute qualité constante.
La façon dont nous résolvons ces problèmes passe par l'impression Joule. La technologie utilise du fil, qui est peu coûteux par rapport à la poudre et à d'autres matériaux. Le fil est placé dans un système de mouvement de précision avec une alimentation de fil de précision. La pointe du fil est ensuite déplacée à l'endroit de la pièce où l'on veut commencer une ligne d'impression afin qu'elle touche la pièce. La pointe du fil est ensuite fondue en plaçant un courant à travers le fil dans la partie en contact. En physique, cela s'appelle chauffage par résistance ou chauffage par joule - c'est comme la bobine d'un grille-pain.
Quels sont les avantages de la technologie d'impression Joule ?
Lorsque vous utilisez le chauffage par joule, vous chauffez le métal de l'intérieur. Comme il n'y a pas de constante de temps thermique, vous pouvez chauffer le métal très rapidement avec une très faible énergie. Cela signifie qu'il n'y a pas de limite de vitesse thermodynamique; nous sommes capables d'imprimer à la vitesse à laquelle nous pouvons nous déplacer avec précision et exactitude. Notre objectif est de 5 ou 10 kg/heure d'ici la fin de l'année. Avec une vitesse très élevée et des coûts de matières premières faibles, les coûts de production globaux sont considérablement réduits.
De plus, vous pouvez mesurer exactement ce qui se passe dans le bain de fusion - vous savez exactement où il se trouve, combien de métal y pénètre et combien de chaleur est appliquée. Nous utilisons tous ces paramètres pour le contrôler en temps réel, c'est donc un système serré en boucle fermée, ainsi que pour capturer les données de processus pour les analyser hors ligne.
Le résultat est un système qui peut imprimer du métal à une vitesse extrêmement rapide et de haute qualité, suffisamment bon marché pour être moins cher que la fabrication conventionnelle pour de nombreuses applications.
Comment l'impression Joule se compare-t-elle aux autres systèmes de FA en métal sur le marché ?
Il y a 3 autres catégories de technologie à considérer. Le premier, qui est le plus populaire, est la fusion sur lit de poudre. Avec la fusion sur lit de poudre, vous étalez de la poudre métallique en une couche mince et la faites fondre avec un laser ou un faisceau d'électrons.
Le défi de la fusion sur lit de poudre est que les poudres sont très chères et qu'une grande quantité est gaspillée au cours du processus, ce qui entraîne des coûts de matériaux très élevés. Vous êtes également limité dans la vitesse à laquelle vous pouvez faire fondre la poudre :puisque vous la chauffez de haut en bas, vous devez attendre que la chaleur traverse la poudre. C'est presque comme faire cuire une dinde - un processus qui prend toujours quelques heures. Vous ne pouvez pas aller plus vite avec une plus grande chaleur car vous ruinerez l'extérieur de la dinde. De même, dans la fusion sur lit de poudre, vous vaporisez simplement la poudre. Dans l'ensemble, il s'agit d'un moyen assez coûteux et complexe de fabriquer une pièce.
La deuxième catégorie est le jet de liant. Les systèmes de jet de liant s'attaquent au problème de vitesse. Ils utilisent une poudre de qualité inférieure, donc moins chère, mais le matériau reste beaucoup plus cher qu'un fil. Les systèmes projettent de la colle couche par couche pour construire ce qu'on appelle une partie verte. Une partie verte est généralement constituée de 20% de colle. La colle doit ensuite être enlevée à l'aide d'un bain chimique et la pièce mise dans un four et frittée. En faisant cela, vous espérez réduire la pièce de 20 % pour obtenir un métal à pleine résistance et à pleine densité.
Ce processus fonctionne assez bien pour les petites pièces minces (plus petites que le baseball). Mais si les parois de votre pièce sont plus épaisses qu'environ 1 centimètre, vous ne pouvez pas rétrécir à pleine densité car vous ne pouvez pas transporter suffisamment de chaleur dans la pièce. De plus, essayer de réduire de 20 % des murs plus épais est un grand changement de dimension, il est donc difficile de maintenir la précision dimensionnelle. Le résultat net est que cette technologie ne fonctionne pas vraiment bien pour les pièces dont les parois sont plus épaisses que 1 centimètre, ou pour les pièces plus grandes.
La troisième catégorie que les gens considèrent est le dépôt d'énergie directe, en particulier les systèmes à base de fil. Bien que ces systèmes utilisent un fil, il s'agit généralement d'un fil épais, généralement de 3 millimètres de diamètre. Vous faites ensuite fondre le fil avec un laser, un faisceau d'électrons ou un arc, comme le soudage à l'arc.
Bien que ces systèmes puissent atteindre des vitesses d'impression assez élevées, le défi est la résolution. Étant donné que le métal goutte ou pulvérise dans la ligne d'impression, vous vous retrouvez avec une ligne d'impression beaucoup plus grosse que le fil. Cela signifie que vous ne pouvez imprimer que des pièces grossières et à faible résolution. De plus, la géométrie de la pièce est limitée car il est difficile d'imprimer des zones en surplomb lorsque le métal en fusion est égoutté ou pulvérisé. Les machines DED ont également tendance à être chères car vous avez besoin de beaucoup de puissance pour faire fondre le métal de cette manière. Ces systèmes sont donc généralement utilisés pour de très grandes pièces, comme la taille d'une cellule, mais ne sont pas tout à fait adaptés aux exigences de haute résolution.
L'impulsion derrière la technologie d'impression Joule était donc de résoudre tous ces problèmes ?
Oui. Pour résoudre les problèmes de vitesse, de coût de production et de qualité.
Outre les problèmes de vitesse, de coût et de qualité des pièces, quels sont les autres défis auxquels sont confrontées les entreprises souhaitant adopter l'impression 3D métal pour la production ?
La question se pose de savoir quelles technologies correspondent le mieux à quelles applications. Il est important d'être clair sur le problème que vous essayez de résoudre et de choisir le bon outil pour résoudre ce problème.
C'est comme la fabrication classique :chaque pièce métallique n'est pas fabriquée de la même manière. Certaines choses sont usinées, d'autres sont forgées ou embouties ou coulées. Il n'y a pas d'approche unique pour chaque problème. L'impression 3D métal est la même.
Comment voyez-vous l'impression 3D métal évoluer au cours des 5 prochaines années ?
Si aujourd'hui l'impression 3D métal est une industrie d'environ 2 milliards de dollars, j'imagine qu'elle deviendra une industrie de 30 milliards de dollars dans 5 ans.
C'est grâce aux 3 énormes avantages de l'impression 3D :d'une part, vous pouvez gagner beaucoup de temps car vous pouvez passer directement d'une conception à une pièce sans construire d'outillage. Deuxièmement, vous pouvez réaliser des géométries intéressantes que vous ne pouvez pas faire autrement avec la fabrication conventionnelle. Troisièmement, si vous choisissez la bonne technologie pour la bonne application, vous pouvez réduire considérablement les coûts de production.
Quel rôle jouera Digital Alloys dans cette évolution ?
Les alliages numériques joueront un rôle énorme. Nous sommes moins chers que la fabrication conventionnelle pour une très grande catégorie de pièces. Cela signifie que vous pouvez utiliser notre technologie pour réduire vos coûts de production sans reconcevoir votre pièce ou apporter d'autres modifications. Et c'est très attrayant pour les clients.
Quels secteurs d'activité ciblez-vous avec l'impression Joule ?
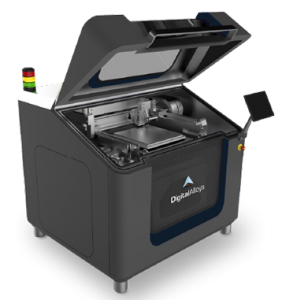
Nous commençons en tant que fournisseur de pièces imprimées, avec l'objectif d'expédier nos imprimantes début 2020. Dans nos premières applications, nous nous concentrons sur les domaines où nous pouvons réduire les coûts de production par rapport à la fabrication conventionnelle. Cela est particulièrement vrai pour les pièces usinées à partir de métaux difficiles à couper, tels que le titane, l'acier à outils, les alliages de nickel et l'acier inoxydable.
L'impression Joule vous permet d'imprimer une pièce de forme quasi nette qui élimine les rebuts et l'usinage de dégrossissage, générant de nombreuses économies. Un exemple d'application est celui des pièces en titane utilisées dans l'aérospatiale, les dispositifs médicaux et dans l'industrie maritime. Une deuxième application est l'outillage, car les aciers à outils sont très difficiles à couper. Mais avec l'impression 3D, vous pouvez ajouter des canaux de refroidissement aux outils, par exemple un insert de moulage sous pression avec des canaux de refroidissement internes qui vous permettent de refroidir l'outil plus rapidement et de réduire le temps de cycle. Nos clients pour ceux-ci sont l'automobile, les produits de consommation et l'aérospatiale.
En ce qui concerne la fabrication additive, y a-t-il une tendance qui vous passionne le plus ?
Le passage du prototypage à la production. C'est certainement la plus grande tendance du moment.
À quoi ressemble l'avenir des alliages numériques ?
Nous construirons notre première usine en 2019. Travailler dans la production, ce n'est pas seulement une question de technologie. Vous devez savoir comment embaucher et former des opérateurs, construire une chaîne d'approvisionnement, comment faire l'assurance qualité, la certification, assurer l'approbation réglementaire, etc. Nous le ferons en premier, ce qui permettra à nos clients de suivre plus facilement. Après cela, nous prévoyons de commencer à expédier nos imprimantes début 2020.
Vous pouvez en savoir plus sur Digital Alloys sur https://www.digitalalliages.com/.
impression en 3D
- La transformation numérique et l'avenir de l'industrie du papier
- Entretien avec un expert :Spencer Wright de pencerw.com et nTopology
- Entretien d'experts :Guillaume de Calan, PDG de Nanoe, sur l'avenir de l'impression 3D céramique
- Entretien d'experts :John Kawola, président d'Ultimaker, sur l'avenir de l'impression 3D
- Entretien d'experts :Rush LaSelle de Jabil sur l'avenir de la fabrication additive
- Entretien d'experts :Nanci Hardwick, PDG de MELD Manufacturing, sur la réalisation du potentiel de la fabrication additive métallique
- L'automatisation et l'avenir de la fabrication numérique ?
- L'avenir de l'impression 3D dans la fabrication
- L'impression 3D est-elle l'avenir de la fabrication ?