époxy 2 composants pour une production accrue d'aérostructures composites via RTM
Ceci est le troisième de ma série de blogs sur les technologies que vous devriez consulter au CAMX 2019 (23-26 septembre, Anaheim, CA, États-Unis). Hexion (Columbus, Ohio, États-Unis) a développé un système à deux composants (2K) pour RTM d'aérostructures basé sur sa résine époxy Epikote System 600. L'introduction ci-dessous expliquera pourquoi ce développement est important. Après cela, je donne plus de détails sur ce nouveau système 2K et comment Hexion répond aux exigences des équipementiers de l'aérospatiale en matière d'assurance qualité in situ de la résine mélangée. En bas, je discute également de l'époxy 2K par infusion/RTM d'Hexion pour les applications ignifuges (FR).
Pourquoi des résines 2K pour RTM ?
Plus tôt cette année, j'ai écrit sur les programmes du spécialiste de l'outillage Alpex Technologies (Mils, Autriche) et de la filiale d'Airbus Composites Technology Center (CTC, Stade, Allemagne) pour produire des pièces d'avion en composite à l'aide du moulage par transfert de résine (RTM) . L'utilisation du RTM dans l'aérospatiale n'est pas nouvelle. Il y a et il y a eu une variété de pièces d'avions fabriquées à l'aide de RTM, y compris :
- Safran pour l'avion d'affaires Gulfstream G250 (Israel Aerospace Industries et North Coast Composites)
- Aubes et carter de soufflante pour le moteur d'avion à double flux LEAP (Albany Engineered Composites)
- Cadre de porte A350 (Airbus Helicopters Donauworth)
- Démonstration de porte passager A350 (Elbit Cyclone)
- Démonstration volet multispar A320 (Airbus Bremen)
- Matrix Composites a produit plus de 6 000 composants pour le F-22 à l'aide de RTM.
Cependant, la RTM dans les applications aérospatiales est traditionnellement un processus à basse pression avec des temps de cycle mesurés en heures. Les programmes d'Alpex et de CTC sont axés sur l'exploitation de l'automatisation, l'injection rapide et des temps de cycle de 15 à 20 minutes offert par RTM haute pression (HP-RTM). Dans mon article "HP-RTM pour la production en série d'aérostructures CFRP rentables", j'ai discuté de la question de l'utilisation de résines époxy à 2 composants (2K) par rapport à la norme actuelle d'utilisation de systèmes prémélangés à 1 composant (1K):
« Schiller [Jan Schiller, chef de projet CTC pour les systèmes de production et contact principal pour les technologies RTM] observe que tous les RTM précédents les structures d'avions n'ont utilisé que des systèmes 1K mélangé par le fournisseur, qui certifie ensuite le mélange et assume la responsabilité de s'assurer que la résine répond aux exigences de qualification. « Maintenant, nous envisageons des systèmes 2K, mais le défi est d'assurer la qualité du mixage ," il explique. Les systèmes 1K prémélangés nécessitent une expédition et un stockage à froid pour éviter toute réaction jusqu'au traitement de la pièce. Ainsi, les avantages des systèmes 2K incluent l'élimination de cette dépense ainsi qu'une plus grande réactivité pour un traitement plus rapide. »
« Un problème, cependant, est que l'assurance qualité (AQ) sera transférée du fournisseur de résine au fabricant de pièces. « Ce QA nécessite la détection du rapport de mélange et la qualité de résine mixte . Les deux sont nécessaires pour la qualification Airbus d'un nouveau matériau. Cela signifie donc des mesures des deux composants juste avant le mélange et de la résine après mélange . Aujourd'hui, nous n'avons que des capteurs avant la tête de mélange, indiquant la quantité de résine et de durcisseur dosée dans le mélange. Ce n'est pas suffisant pour la qualification. »
Hexion (Columus, Ohio, États-Unis), un leader dans le développement d'époxydes à durcissement rapide pour HP-RTM dans les composites automobiles (voir « HP-RTM à la hausse »), a annoncé en mars 2019 avoir développé un système 2K pour RTM de aérostructures à base de sa résine époxy Epikote System 600. J'ai interviewé Jean Rivière, leader du segment mondial de l'aérospatiale époxy d'Hexion, pour en savoir plus sur leur système 2K pour l'aérospatiale et sur la manière dont ils répondent à cette demande d'assurance qualité in situ de la résine mélangée.
Surmonter les limitations des systèmes 1K
« Tout comme avec le préimprégné, les systèmes 1K pour le RTM et l'infusion dans l'aérospatiale doivent être conservés au froid et avoir une durée de vie limitée », explique Rivière. « En utilisant un système époxy à 2 composants (2K), vous supprimez ces contraintes. Nous avons vu des résines époxy 2K et hautement réactives utilisées dans la fabrication de pales d'éoliennes et de structures automobiles. Alors pourquoi pas dans l'aérospatiale ?"
Rivière explique qu'après avoir parlé à de nombreux clients à ce sujet, Hexion a compris la principale préoccupation - vous avez besoin d'une validation que le rapport de mélange est correct à tout moment avant l'injection dans le moule. Sans cela, vous courez un risque inacceptable pour l'équipementier », note-t-il. Il ajoute qu'auparavant, il n'y avait pas de demande pour le type de volumes de production observés dans les pales éoliennes et l'automobile. Aujourd'hui, cependant, Airbus et Boeing veulent dépasser les taux de production actuels tout en visant davantage de pièces composites par avion. « Alors maintenant, il est nécessaire de s'éloigner de la superposition de préimprégnés et d'opter pour un époxy 2K pour l'aérospatiale RTM ou l'infusion », explique Rivière.
Dans les schémas de la chaîne d'approvisionnement ci-dessous, la technologie 2K supprime non seulement les étapes de stockage à froid et de réchauffement, mais lève également les restrictions sur la taille des conteneurs de résine pour l'expédition. « Vous devez maintenir la masse de résine prémélangée à 20 litres et maintenir ces fûts à très basse température », explique Rivière, « sinon la résine peut commencer à réagir. Pour un système 2K, des fûts standard de 200 litres peuvent être expédiés sans restrictions de basse température. Donc, il y a moins de risques, pas de refroidissement puissant et moins de précautions nécessaires. »
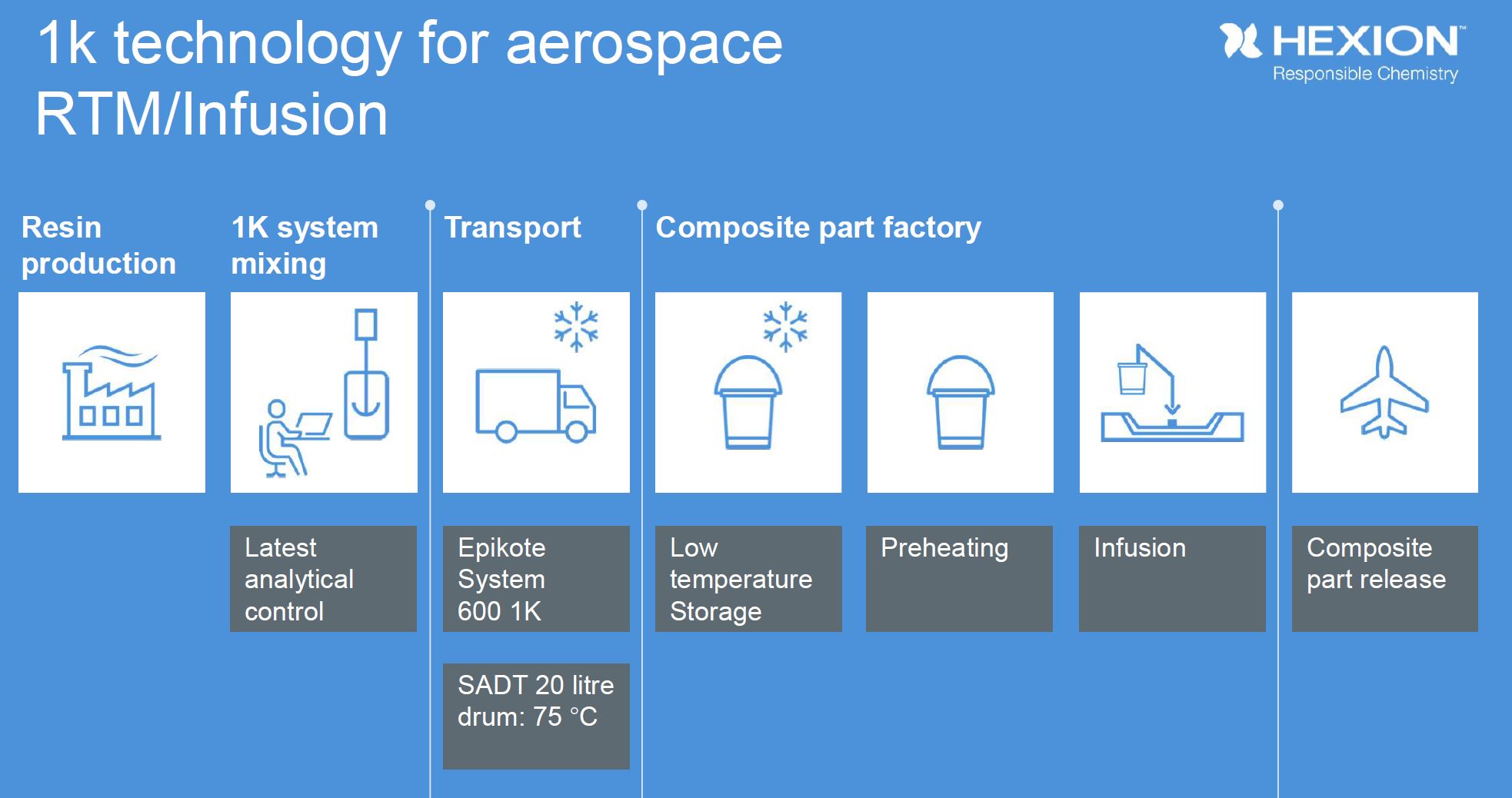
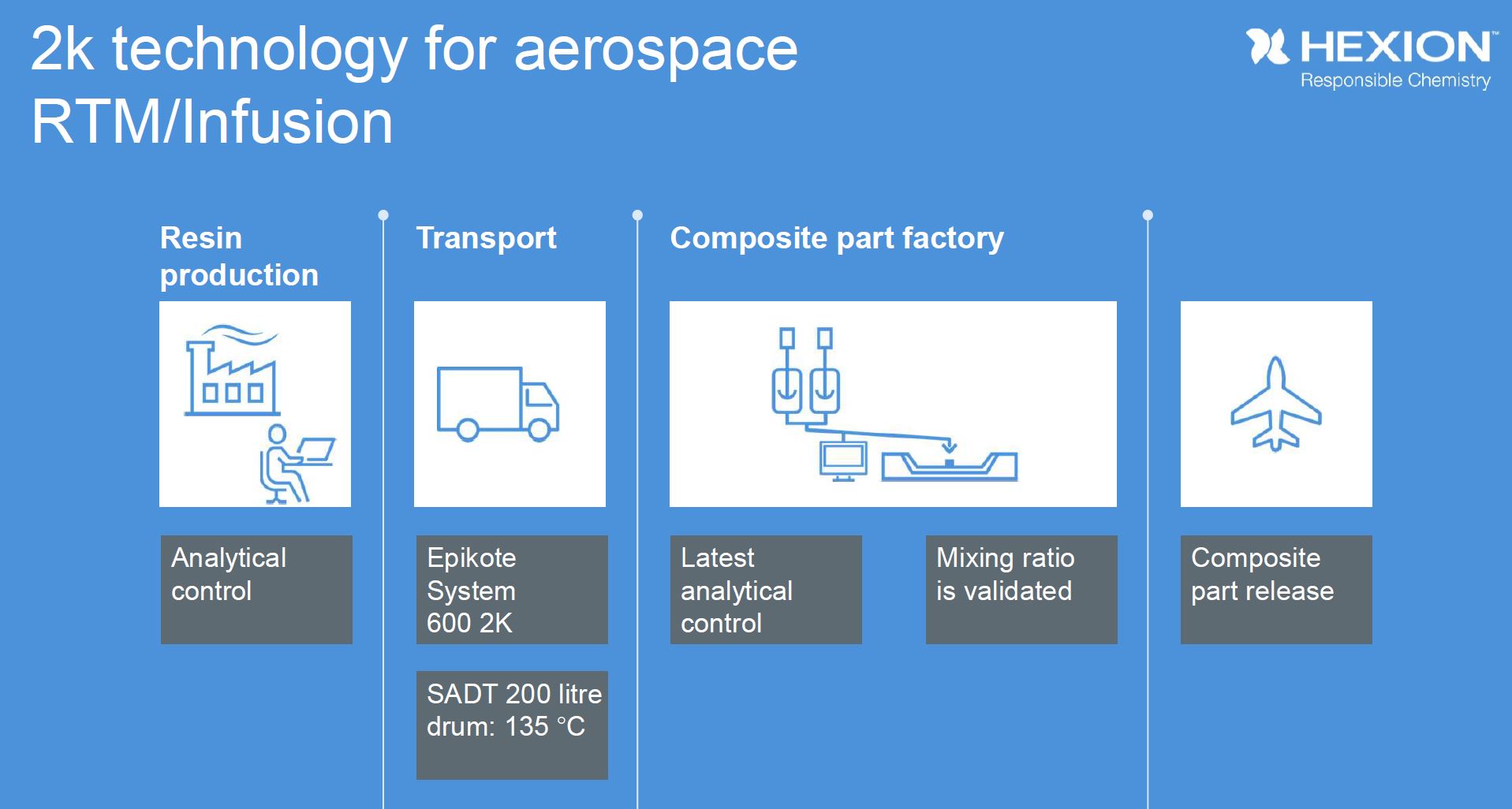
Les chaînes d'approvisionnement ci-dessus montrent comment le contrôle analytique change. Alors que seul un contrôle initial est effectué sur le site de fabrication pour les systèmes de résine 1K, le contrôle est mis en œuvre à plusieurs points de contrôle pour le système 2K. En plus du contrôle des composants A et B pendant la production en usine, le rapport de mélange A:B est également contrôlé numériquement dans l'équipement de mélange, de dosage et de distribution (MMD) et à nouveau juste avant l'injection de résine dans le moule. SOURCE | Hexion.
Contrôle analytique
Pour développer cette technologie 2K, Hexion a travaillé avec Hübers (Bocholt, Allemagne), un fabricant d'équipements de mélange, de mesure et de distribution (MMD), et Comosyst (Hurlach, Allemagne) qui détient une licence exclusive pour le procédé breveté d'assistance sous vide ( VAP) pour l'infusion. Hübers a une solide réputation pour les systèmes MMD hautes performances utilisés dans la fabrication de composants électriques et électroniques (par exemple, résine coulée et composants imprégnés pour transformateurs, etc.) tandis que Comosyst est un expert en injection et infusion de résine pour les applications Airbus, et ainsi , comprend ce que l'OEM de l'avion recherche en matière de traitement et d'assurance qualité (AQ) des résines mélangées.
« Le contrôle analytique entre en jeu après que les composants A et B de l'époxy ont été mélangés précisément par l'équipement Hübers et se préparent à être introduits dans le moule », explique Rivière. Les tubes noirs entre le système Hübers MMD et la configuration de perfusion VAP sous vide dans l'image ci-dessous sont un élément clé de ce système de contrôle analytique. « C'est là que nous avons un appareil d'analyse qui contrôle le rapport de mélange en temps réel », explique Rivière. « Nous avons démontré une mesure du rapport de mélange toutes les 12 secondes, mais une mesure plus fréquente est également possible. En effet, la technologie permet un contrôle continu du rapport de mélange, qui est signalé et enregistré. »
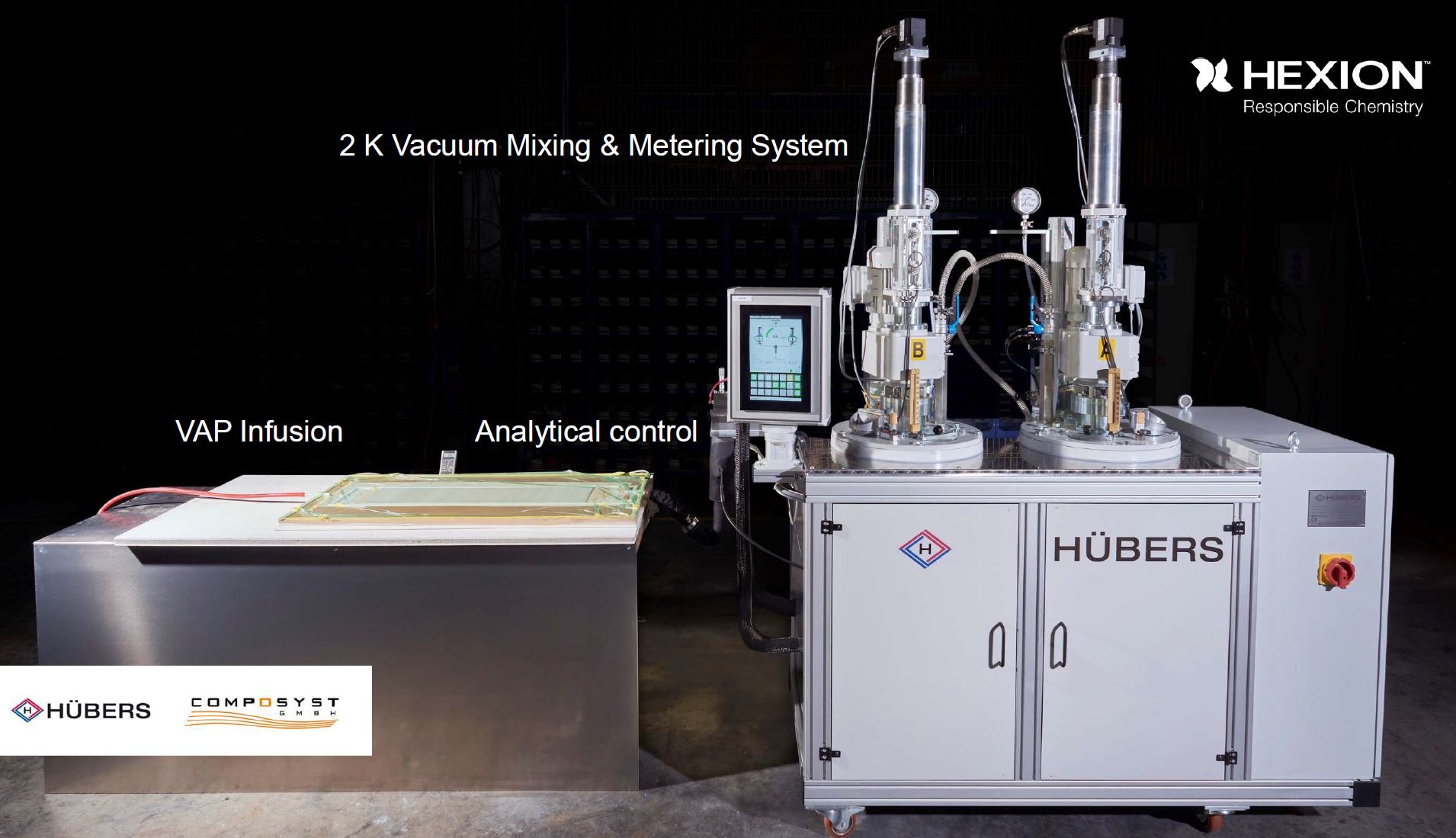
Notez le tube noir entre l'équipement Hübers MMD et la configuration d'infusion VAP où Hexion a développé une mesure en ligne du rapport de mélange de résine avant l'injection. SOURCE | Hexion
« Avec ce système, poursuit-il, il y a un double contrôle :le contrôle normal dans l'unité MMD et notre contrôle analytique de pré-injection en haut. Tout d'abord, Rivière souligne que les machines Hübers MMD sont réputées pour leur précision et leur exactitude. « Ils ont un double système de pompage pour les deux composants et doivent maintenir la précision du volume et de la température ainsi que le rapport de mélange pour les applications auxquelles ils alimentent. Notre système ajoute ensuite une deuxième mesure après le mélange et juste avant l'injection où vous pouvez définir des cibles pour les alarmes. Si le rapport de mélange mesuré n'atteint pas les objectifs et déclenche l'alarme, le système évacuera alors la résine mélangée dans un récipient séparé, en contournant le moule afin qu'elle ne soit pas introduit dans la partie infusée. « Il est alors possible de récupérer le procédé et de poursuivre l'injection », note Rivière.
Il dit que le système de contrôle analytique post-mélange et pré-injection d'Hexion fournit un enregistrement indépendant pour la traçabilité et peut également être intégré dans l'unité MMD, en fonction des besoins du client. Rivière note que l'unité Hübers MMD effectue également un dégazage complet de la résine, ce qui est requis par l'industrie électronique, où il ne peut y avoir aucun vide ou porosité dans les composants de l'application. « Ce système permet également un contrôle portable de la pression sur le moule en gérant le flux de la résine à des niveaux élevés ou faibles », précise-t-il. "Vous pouvez obtenir une très bonne imprégnation avec ce type de contrôle, et vous pouvez également raccourcir le temps de processus d'infusion tout en répondant aux exigences de qualité aérospatiale en termes de porosité et de volume de fibre."
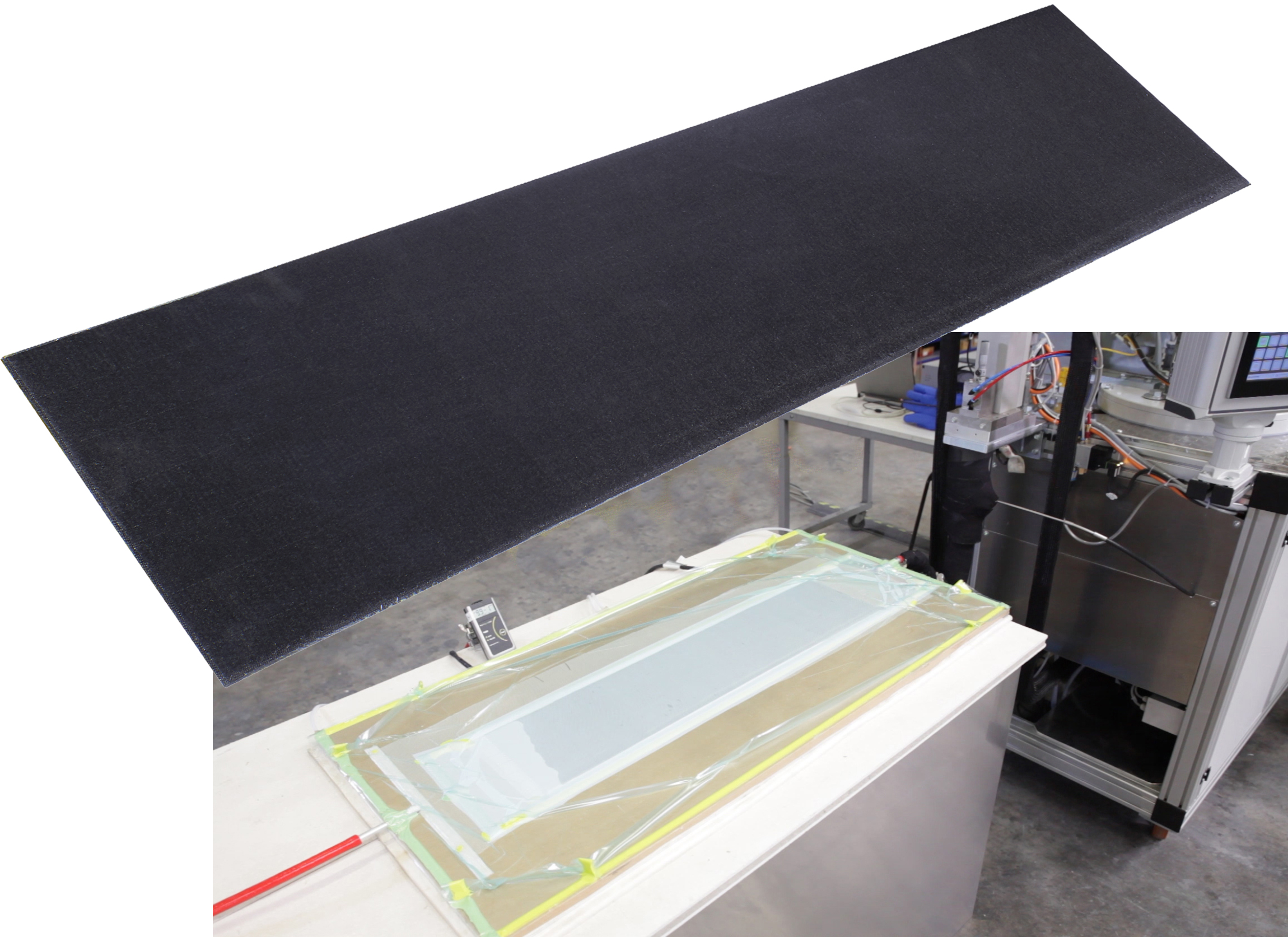
Photos montrant la configuration d'infusion à l'aide de l'équipement Hübers MMD et du contrôle analytique Hexion 2K et d'un stratifié UD en fibre de carbone de 2 centimètres d'épaisseur préparé à l'aide de cette configuration, atteignant plus de 60 % de volume de fibres. SOURCE | Hexion
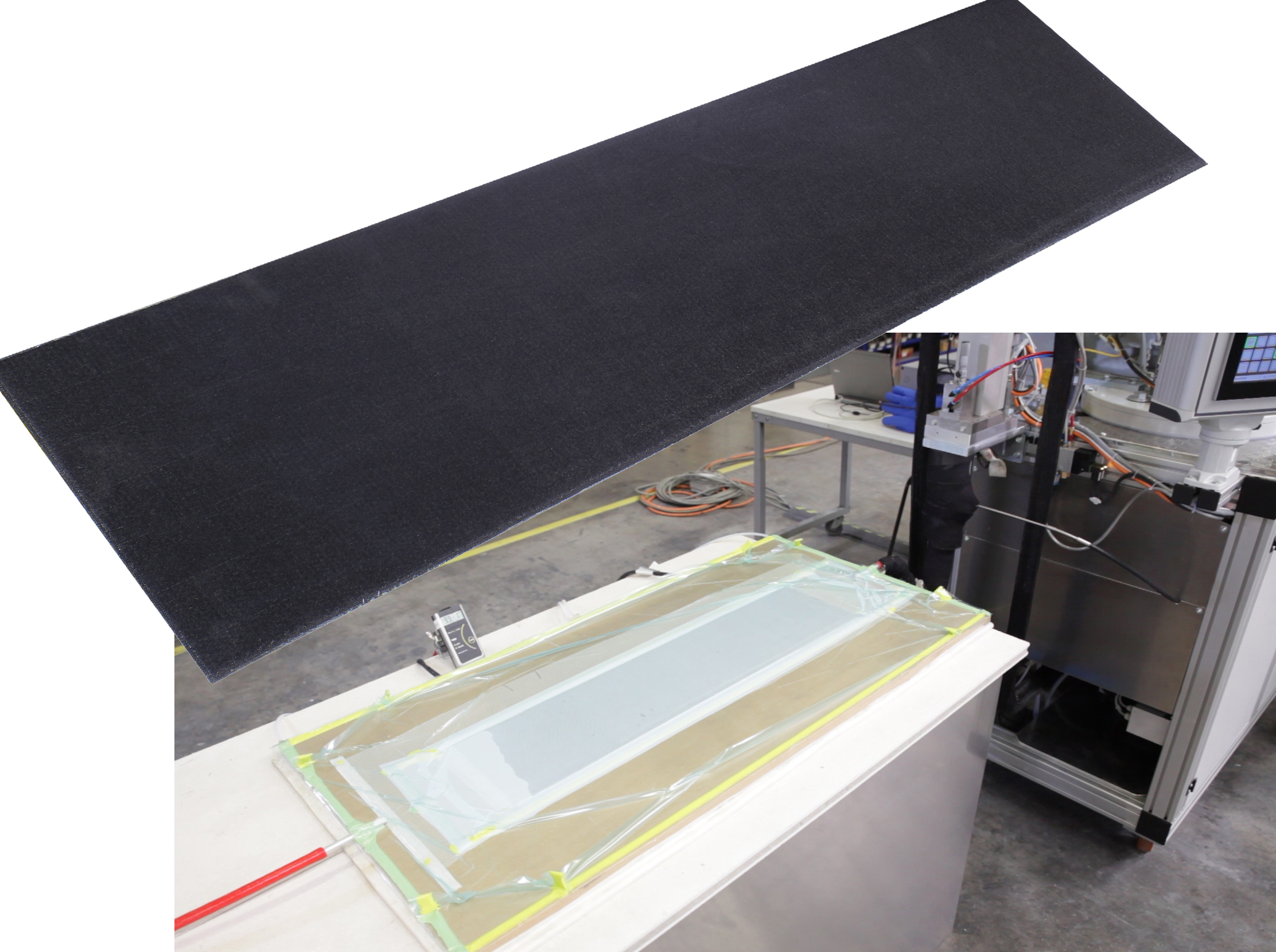
Meilleure fenêtre de traitement
« Parce que le mélange se fait avec un mélangeur statique et dans un court laps de temps juste avant l'injection, le mélange de résine offre une durée de vie en pot plus longue (jusqu'à 40 % par rapport à 1K)", note Rivière . Cela offre une meilleure fenêtre de traitement et nous avons produit des stratifiés épais en fibre de carbone avec 60% de volume de fibre. Les performances mécaniques des systèmes 2K par rapport aux systèmes 1K sont les mêmes car la chimie est la même. Nous pensons que ce sera un processus plus fiable et la valeur complète est lorsque vous connectez le contrôle de mélange à la configuration d'injection de résine. »
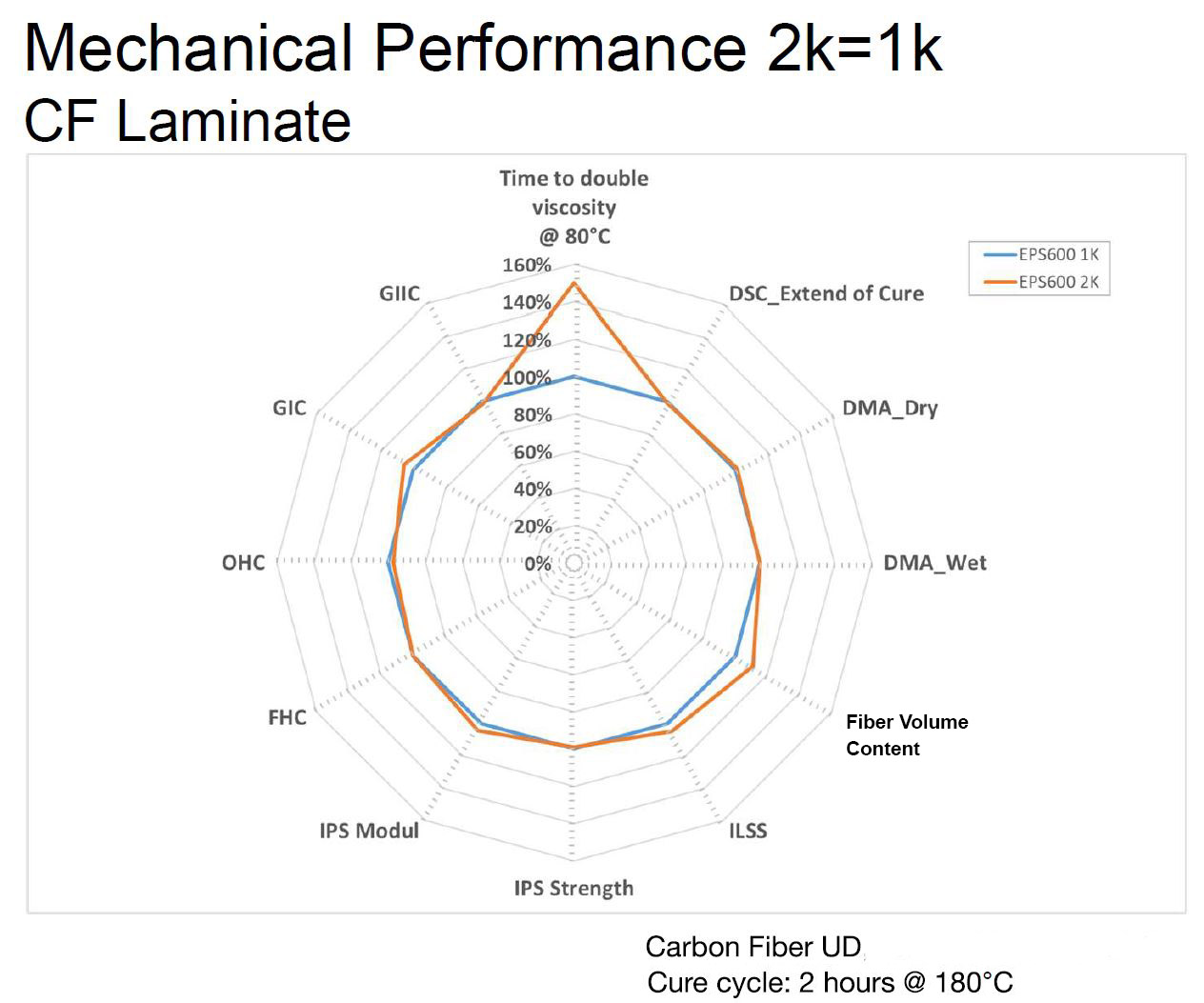
SOURCE | Hexion
Hexion présentera des informations détaillées sur son système 2K Epikote 600 pour RTM et son époxy EPON FlameX pour répondre aux exigences FST (incendie, fumée et toxicité) des avions (voir ci-dessous) dans le théâtre CAMX sur le sol de l'exposition :
- Nouvelle technologie 2K pour la fabrication d'époxy aérospatiale
Mardi 24 septembre — 11h00-11h25 - Systèmes époxy FlameX pour les applications de sécurité incendie
Mardi 24 septembre — 11h30 – 11h55
Vous pouvez également obtenir plus de détails sur le stand Hexion Y24.
EPON FlameX époxy pour infusion/RTM de composites résistants au feu
Hexion a également développé un époxy à 2 composants pour l'infusion/RTM de pièces qui doivent répondre aux exigences de résistance au feu (FR) et de flamme, fumée, toxicité (FST). Destiné à remplacer les préimprégnés phénoliques par un moulage époxy liquide, les moteurs de ce développement incluent :
- Augmentation des cadences de production
- Réglementation REACH pour les systèmes sans halogène et non phénoliques
- Résines plus résistantes et plus résistantes que les résines phénoliques cassantes
- Coût compétitif avec les phénoliques mais beaucoup moins cher que les thermoplastiques.
Le système EPON FlameX d'Hexion n'utilise pas d'additifs halogènes ou particulaires pour obtenir une résistance au feu, mais intègre plutôt cette performance dans le squelette moléculaire de la résine. Il n'y a pas de filtrage des particules pendant l'infusion. La résine s'infuse bien avec une viscosité de 250 cps à 60-70 °C (140-158 °F) et durcit en 1,5 heures à 150 °C (302 °F). Une post-polymérisation autoportante ou à l'aide d'un outil à 180 °C est recommandée pour des propriétés structurelles maximales.
Les pièces fabriquées avec ce système passent les étapes suivantes sans revêtements ni mesures FR supplémentaires :
- Brûlure verticale des années 60 FAR25.853(a)
- Toxicité de la fumée BSS7239
- Densité de fumée BSS7238
Il passera également le dégagement de chaleur OSU 65/65, dans certaines configurations avec un gel coat ou un revêtement intumescent certifié. Ceci n'est requis que pour les pièces qui peuvent être touchées pendant le roulage, le décollage et l'atterrissage de l'avion.
« Nous avons fait la démonstration de bacs suspendus qui nécessitent actuellement 10 à 12 heures pour être fabriqués à l'aide de procédés de préimprégné phénolique conventionnels, mais qui peuvent être produits en 90 à 120 minutes par infusion ou RTM à l'aide du système FlameX », déclare Nathan Bruno, spécialiste des applications époxy et du développement de produits chez Hexion. . "En outre, parce qu'il n'y a pas de charges, il a une densité inférieure à celle des époxy FR chargés."
Les applications incluent les intérieurs d'avions, les zones de fret, les toilettes, les cuisines et les composants de sièges, ainsi que les intérieurs marins, ferroviaires et architecturaux.
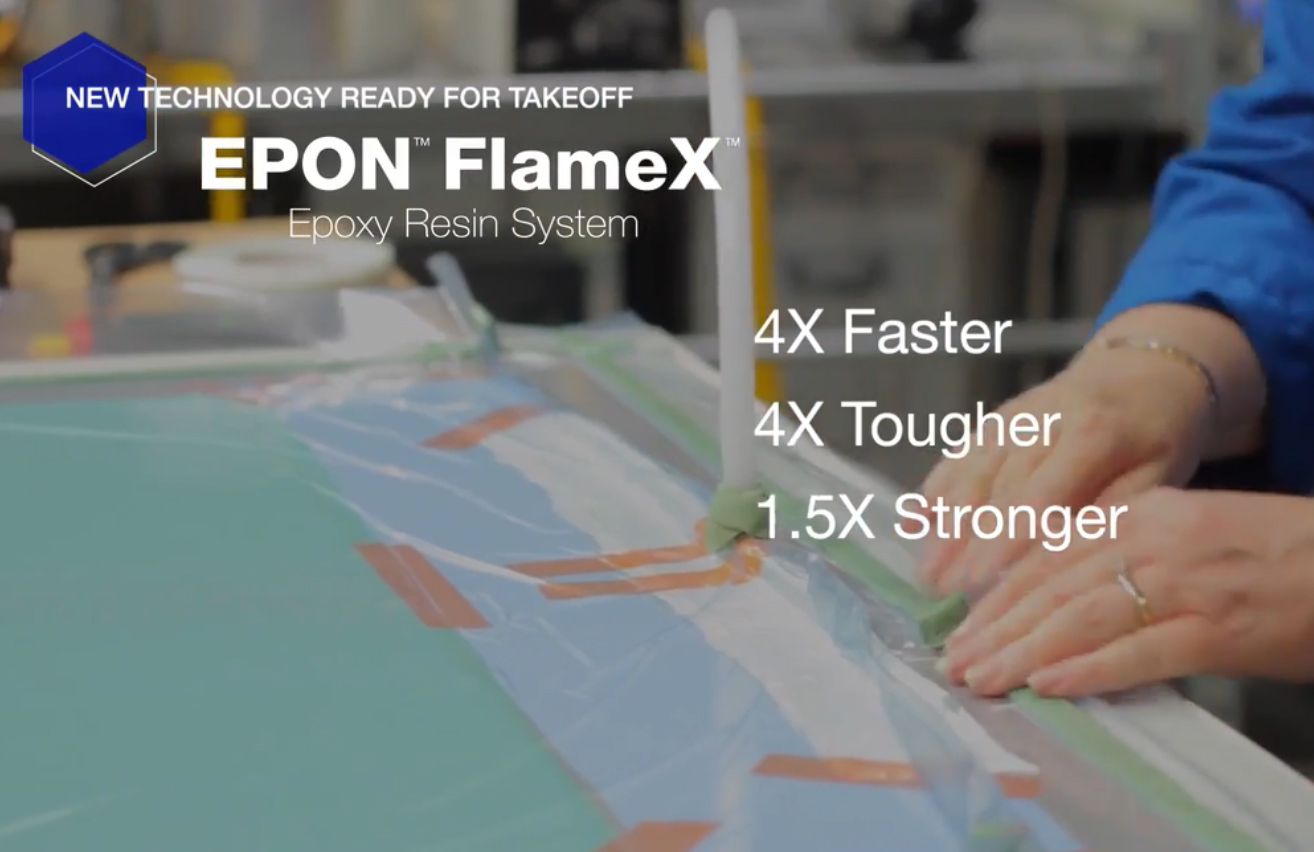
Résine
- Lanxess ajoute deux nouvelles lignes de production pour les matériaux composites Tepex
- Composés de purge pour la production d'emballages en polyoléfine à paroi mince
- Les utilisations de la résine époxy pour l'art gagnent en popularité
- Broetje-Automation élargit le portefeuille AFP pour la production composite en série
- INEOS Styrolution va construire un site de production pour le composite thermoplastique StyLight
- Total Composite Solutions (TCS) lance une solution de préimprégné époxy pour l'aérospatiale
- Hexion présente une solution époxy à deux composants pour la production de composites aérospatiaux
- Techsil lance un adhésif époxy transparent pour substrats composites
- Rhodes Interform fabrique une presse composite pour AMRC