CETMA :R&D et innovation composites en Italie
Fondé en 1994, le Centro di Ricerche Europeo di Technologie, Design e Materiali (CETMA, Brindisi, Italie) est l'une des plus grandes organisations indépendantes de recherche et de technologie en Italie, avec une installation de 4 000 mètres carrés et 75 employés. Depuis plus de 20 ans, le CETMA a fortement investi dans les composites, se traduisant par un large éventail d'expertises :
- Conception et prototypage de composants
- Nouveaux processus composites
- Procédés de recyclage des composites et des plastiques
- Optimisation des processus pour le coût, la durabilité, le taux, etc.
- Surveillance des processus en temps réel
- Tests non destructifs (END)
- Surveillance de la santé structurelle (SHM) en temps réel et à distance pendant la production et le service
- Conseil REACH
- Estampage thermoplastique, moulage par compression continue (CCM) et moulage par compression préimprégné (PCM)
- Infusion de liquide, moulage par transfert de résine (RTM) et même RTM qualifié (SQRTM)
- Préimprégné hors autoclave (OOA)
- Soudage par induction
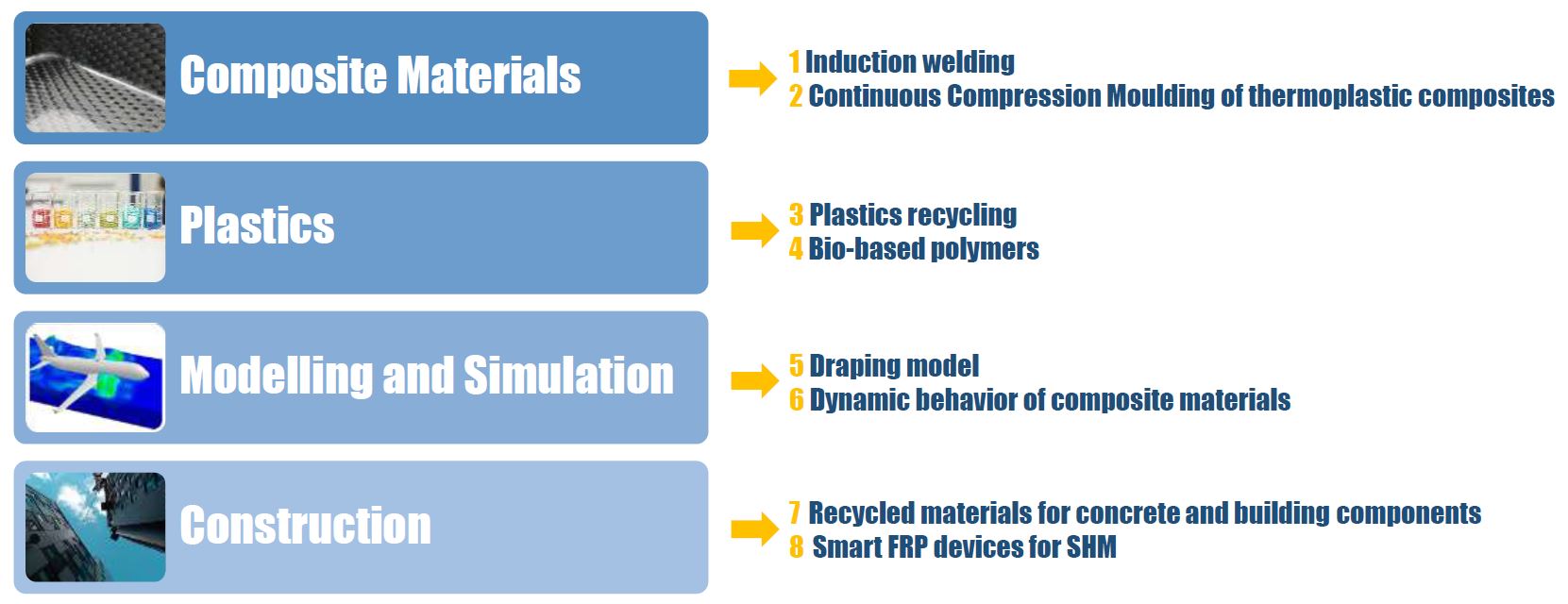
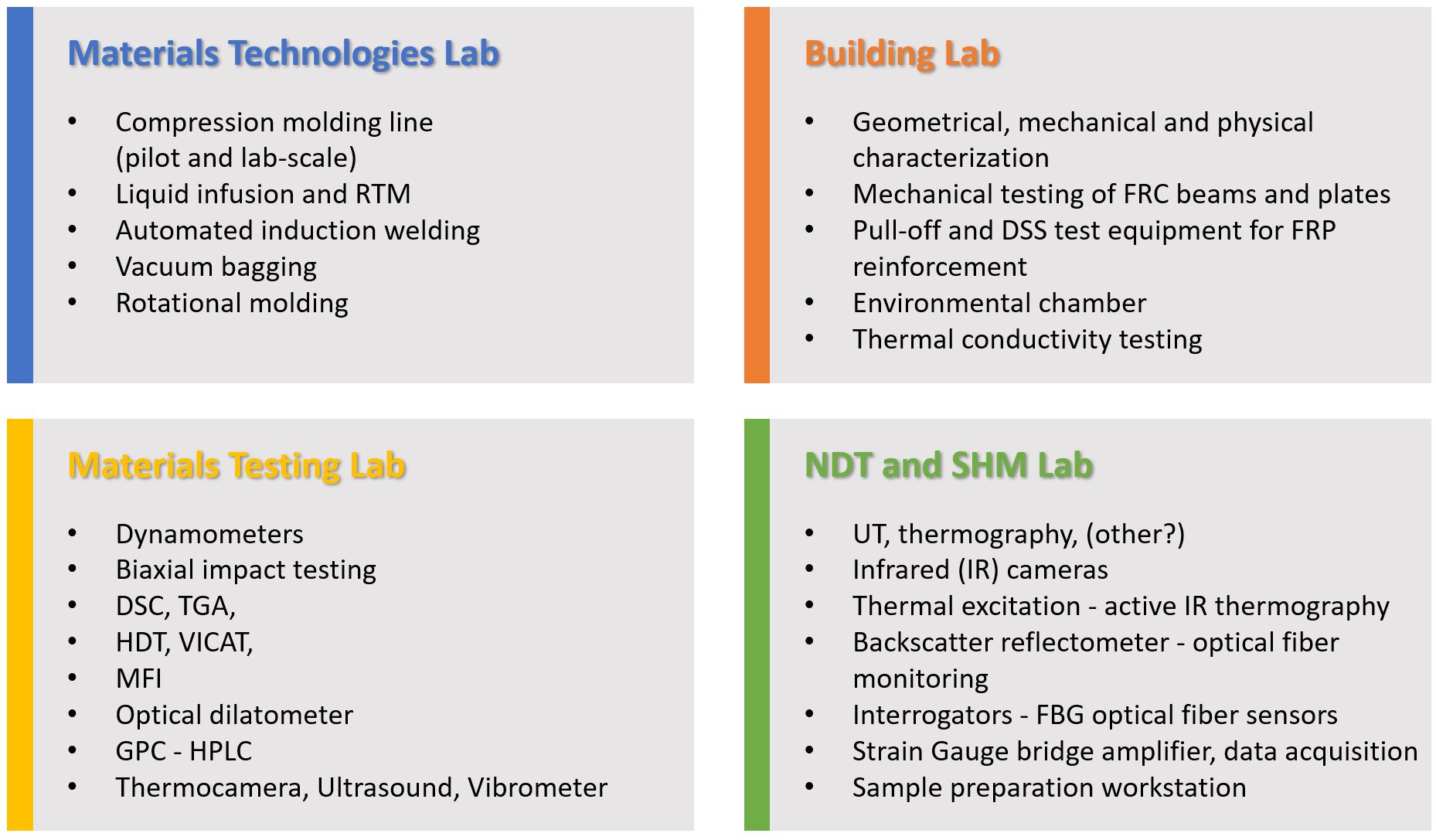
L'objectif principal du CETMA est d'accompagner les entreprises et l'innovation. Desservies par quatre laboratoires principaux, les activités composites du CETMA sont organisées au sein de son département Matériaux et Procédés Avancés (AMP) qui comprend également quatre pôles :
- Matériaux et caractérisation
- Technologies et processus
- Modélisation et simulation
- Diagnostics et surveillance de la santé structurelle
AMP emploie 30 personnes, dont des ingénieurs en matériaux, aéronautiques, civils et chimistes, ainsi qu'un chimiste, un spécialiste des matériaux, un architecte et de nombreux techniciens, conformément à sa croyance en des équipes multidisciplinaires.
Résistance des composites thermoplastiques
« Nous offrons une gamme complète de services dans les composites, note Alessandra Passaro, responsable du département AMP au CETMA, mais nos activités dans les matériaux thermoplastiques sont actuellement l'un de nos domaines prioritaires. Tous les différents types de polymères matriciels thermoplastiques ont été traités dans notre laboratoire. Nous avons commencé à travailler avec la fibre mélangée TWINTEX en 2004 et avec le moulage par compression à l'aide d'une simple presse il y a environ 15 ans. Aujourd'hui, nous avons développé des technologies brevetées de moulage par compression continue (CCM) et de soudage par induction. Nous avons analysé tous les matériaux composites thermoplastiques qui peuvent être utilisés dans ces procédés.
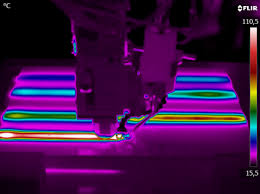
La ligne CCM permet de fabriquer des pièces à section constante en PPS, PEEK, PEKK ou PAEK. Mais en quoi le processus CETMA est-il différent de celui utilisé par des entreprises comme XELIS (Markdorf, Allemagne) et ATC Manufacturing (Post Falls, Idaho, États-Unis) ? (Voir les articles CW :« Moulage par compression de qualité aérospatiale » et « Accélération des composites thermoplastiques dans l'aérospatiale ».) Passaro explique : « Il y a des détails spécifiques dans la conception du moule que nous utilisons. Notre technologie est plus flexible en ce qui concerne les géométries et les matériaux de matrice qui peuvent être utilisés. Il est encore en développement. Bien que brevetée, la technologie est toujours en cours de développement et certains aspects sont exclusifs. La raison pour laquelle le CETMA a poursuivi le CCM ne l'est pas. « Nous avons constaté une utilisation et un besoin accrus de procédés continus de composites thermoplastiques », explique Passaro. « XELIS est une entreprise de produits, pas un fournisseur de machines. Nous sommes une organisation de R&D indépendante et investissons donc dans la technologie et la développons d'un point de vue différent. »
Un exemple de ceci est la simulation de processus étendue pour analyser la répartition de la température dans le moule. "Les résultats de la simulation nous permettent d'avoir une image complète de l'évolution de la température dans le matériau au fil du temps", explique-t-elle, "ce qui est très difficile à surveiller en ligne d'un côté, et pourtant c'est crucial pour minimiser les défauts dans le composite."
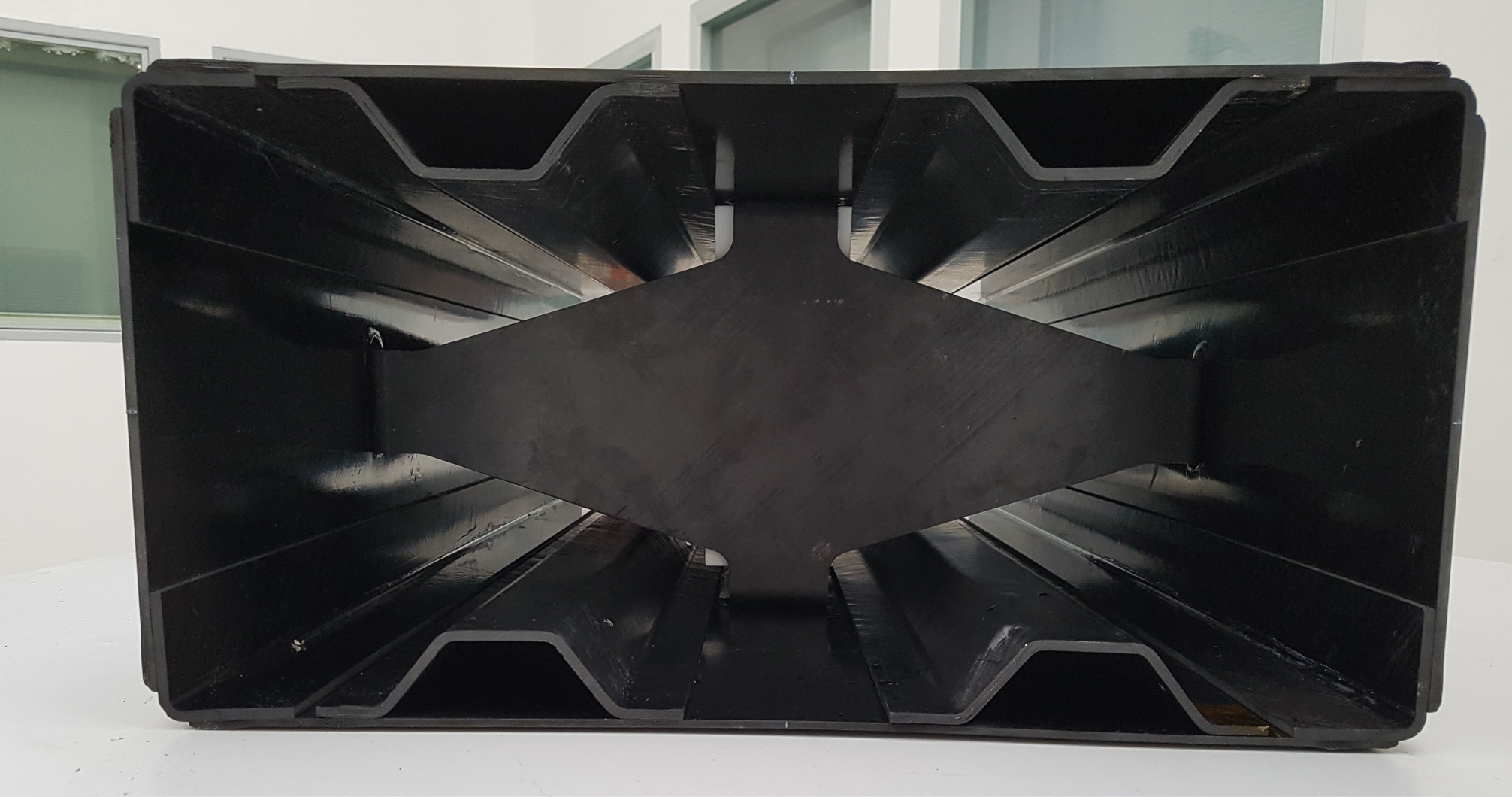
Soudage par induction pour assemblage
Un autre élément clé de l'expertise de CETMA en matière de composites thermoplastiques est la technologie brevetée de soudage par induction, qui comprend un système de contrôle et de refroidissement pour maintenir la chaleur dans la ligne de soudure. Le CETMA a utilisé la technologie avec son partenaire EURECAT (Barcelone, Espagne) pour assembler des profilés et des plaques CCM dans une poutre de quille composite thermoplastique pour un avion de type Airbus A320 dans le cadre du projet Clean Sky 2 KEELBEMAN. Mon blog de janvier 2020, « Advancing thermoplastique composites et RTM pour Clean Sky 2… », donne plus de détails sur ce projet ainsi que les détails de la soudure du CETMA.
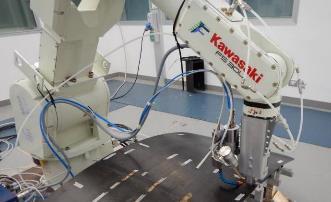
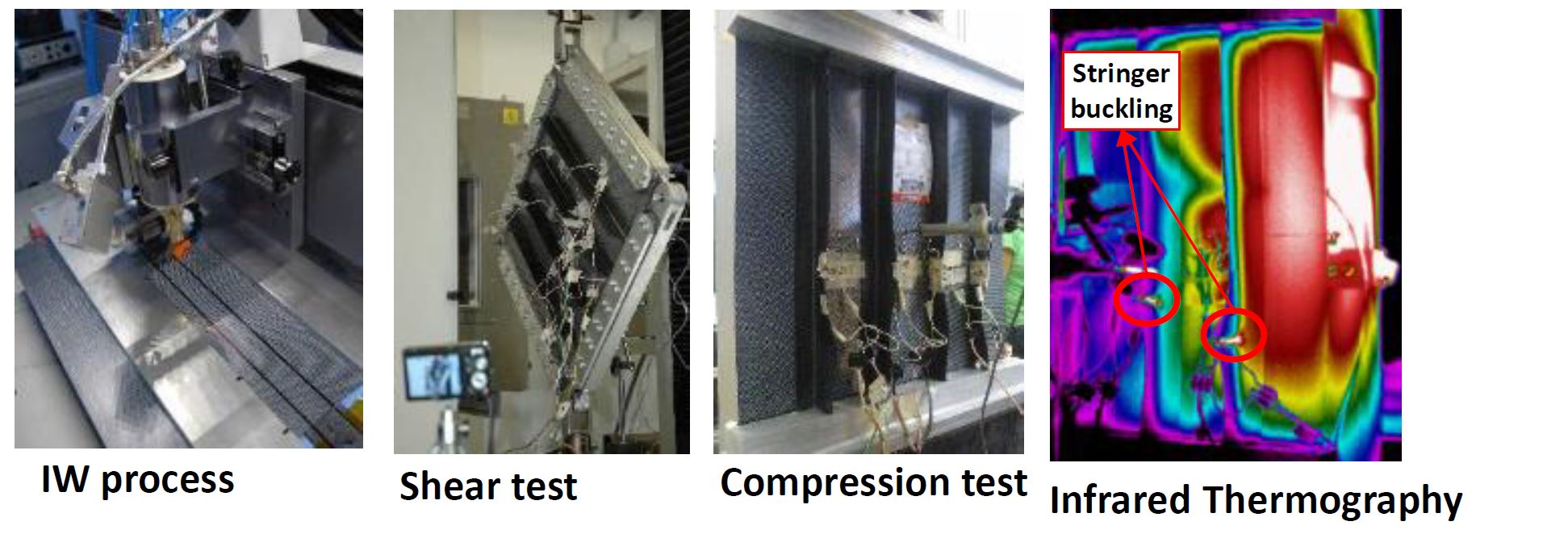
« Nous avons développé deux types de systèmes de soudage par induction », note Passaro. « L'un est une machine fixe pour les surfaces planes et l'autre est basé sur un robot pour les géométries 3D complexes. Les deux permettent des soudures continues à l'échelle industrielle sans nécessiter de matériaux supplémentaires dans la ligne de soudure, tout en offrant des performances d'adhérence très élevées dans les assemblages. »
Le CETMA a démontré le soudage par induction sur des stratifiés composites fabriqués à partir d'un tissu tissé en fibre de carbone et d'un ruban unidirectionnel (UD) ainsi que d'une gamme de matériaux de matrice :PPS, PEEK, PEI, PEKK, PP, PA6, PA12 et un hybride thermodurcissable époxy/PVB ( polyvinylbutyral) système thermoplastique.
Elle a également appliqué son expertise en modélisation et simulation informatique au procédé de soudage par induction. « Cela nous permet de prédire l'évolution de la température dans la zone d'assemblage pendant le soudage, fournissant une aide fondamentale pour optimiser les paramètres du processus », explique Passaro.

Projets de R&D Clean Sky 2 et composites
En plus de KEELBEMAN, le département AMP du CETMA est actuellement impliqué dans quatre autres projets Clean Sky 2.
TRINITI - Réservoirs d'azote haute pression thermoplastiques multi-matériaux pour avion (JTI-CS2-CFP09-2018-02). Le projet de deux ans, qui a débuté en 2019, vise à construire un prototype de réservoir d'avion pour le stockage à long terme d'azote à des fins de lutte contre les incendies. Diehl Aviation (Gilching et Dresde, Allemagne) est le responsable thématique du projet. Les partenaires incluent également le laboratoire de R&D aérospatial Novotech s.r.l. (Naples, Italie), Laboratoire d'essais de composites (Inverin, Co. Galway, Irlande). Le projet fabriquera des réservoirs composites thermoplastiques multi-matériaux grâce à une combinaison de processus tels que la co-extrusion pour former un revêtement/laminé multicouche et multifonctionnel, suivi d'une consolidation in situ (ISC) à l'aide d'un placement automatisé de fibres assisté par laser (AFP ). (Pour en savoir plus sur ISC AFP, voir «Consolidation des aérostructures composites thermoplastiques en place, partie 1 et partie 2».) L'un des objectifs de TRINITI est de réduire, voire d'éliminer les microfissures dans les environnements cryogéniques. Actuellement, le CETMA s'efforce d'identifier tous les matériaux thermoplastiques pouvant répondre aux exigences des récipients sous pression aérospatiaux.
RECHANGE - Grilles de plancher composites innovantes pour passagers et cargaisons à grande échelle pour les démonstrateurs au sol de barils de fuselage d'avions régionaux – (JTI-CS2-2017-CfP07-REG-01-14). Lancé en octobre 2018, ce projet de 18 mois vise à fabriquer des grilles de plancher de passagers et de fret à grande échelle en utilisant des composites thermoplastiques (TP) renforcés de fibres de carbone. La production hautement automatisée comprend le profilage progressif et le soudage par induction pour l'assemblage. L'objectif est de réduire le poids et les coûts récurrents par rapport aux solutions traditionnelles en métal et composites thermodurcissables. Les grilles de plancher composites seront assemblées dans les démonstrateurs de fuselage d'avions régionaux Clean Sky 2 pour des essais au sol et seront évaluées pour l'impact technique et économique ainsi que les performances de résistance aux flammes conformément à la réglementation FAR 25.583. Le leader du sujet est Leonardo tandis que le CETMA coordonne le projet en collaboration avec le fabricant de machines OMI S.r.l. (Fogliano Redipuglia, Italie).
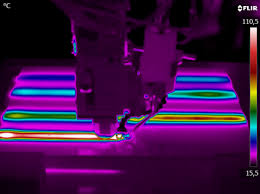
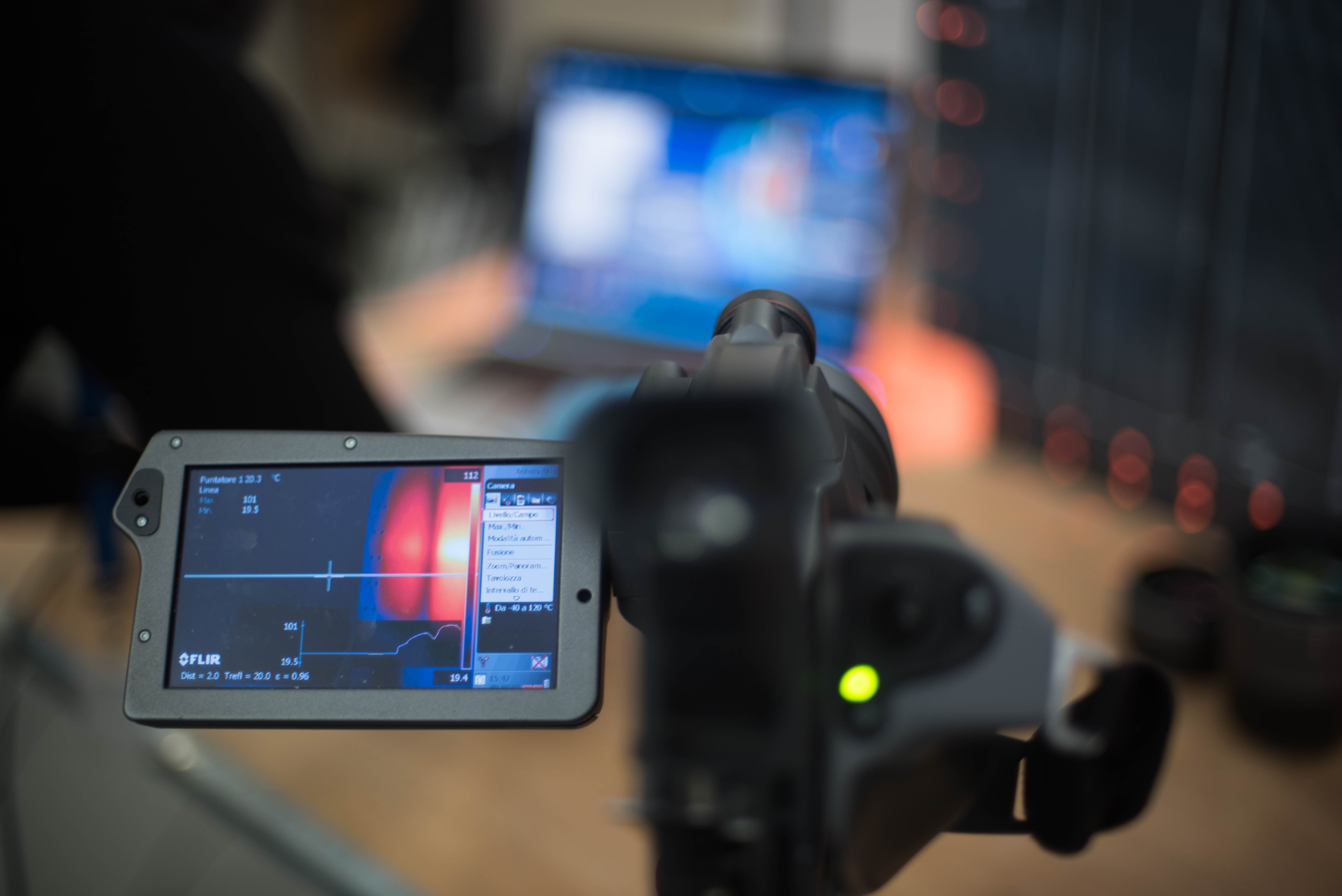
L'une des principales contributions du CETMA à SPARE est le développement de la thermographie infrarouge (IRT) pour la surveillance en ligne du profilage progressif. Ce processus soumet les rouleaux de stratifié composite TP à un compactage et à un chauffage jusqu'à ce que la température de traitement du matériau, la forme complexe et l'épaisseur de conception soient atteintes. "Cependant, il est important de s'assurer que les plis les plus internes subissent une fusion complète de la matrice et une consolidation", explique Passaro. « De plus, il existe une fenêtre de température étroite qui assure la fusion mais ne dégrade pas le polymère. L'IRT est une méthode sans contact qui mesure l'énergie thermique rayonnée à travers la surface de la pièce avec une grande précision. »
Le CETMA a utilisé des fenêtres en zinc sélénurium (ZnSe) pour regarder à l'intérieur des équipements fermés. Transparents aux ondes IR, ils fonctionnent à des températures allant jusqu'à 500°C. Deux de ces fenêtres ont été construites dans la ligne de profilage progressive du projet SPARE avec des caméras IRT suspendues au-dessus pour avoir une vue presque perpendiculaire du matériau traité. Un logiciel de contrôle modifiable a permis de surveiller, d'enregistrer et d'alarmer si les valeurs tombaient en dehors de la plage cible définie.
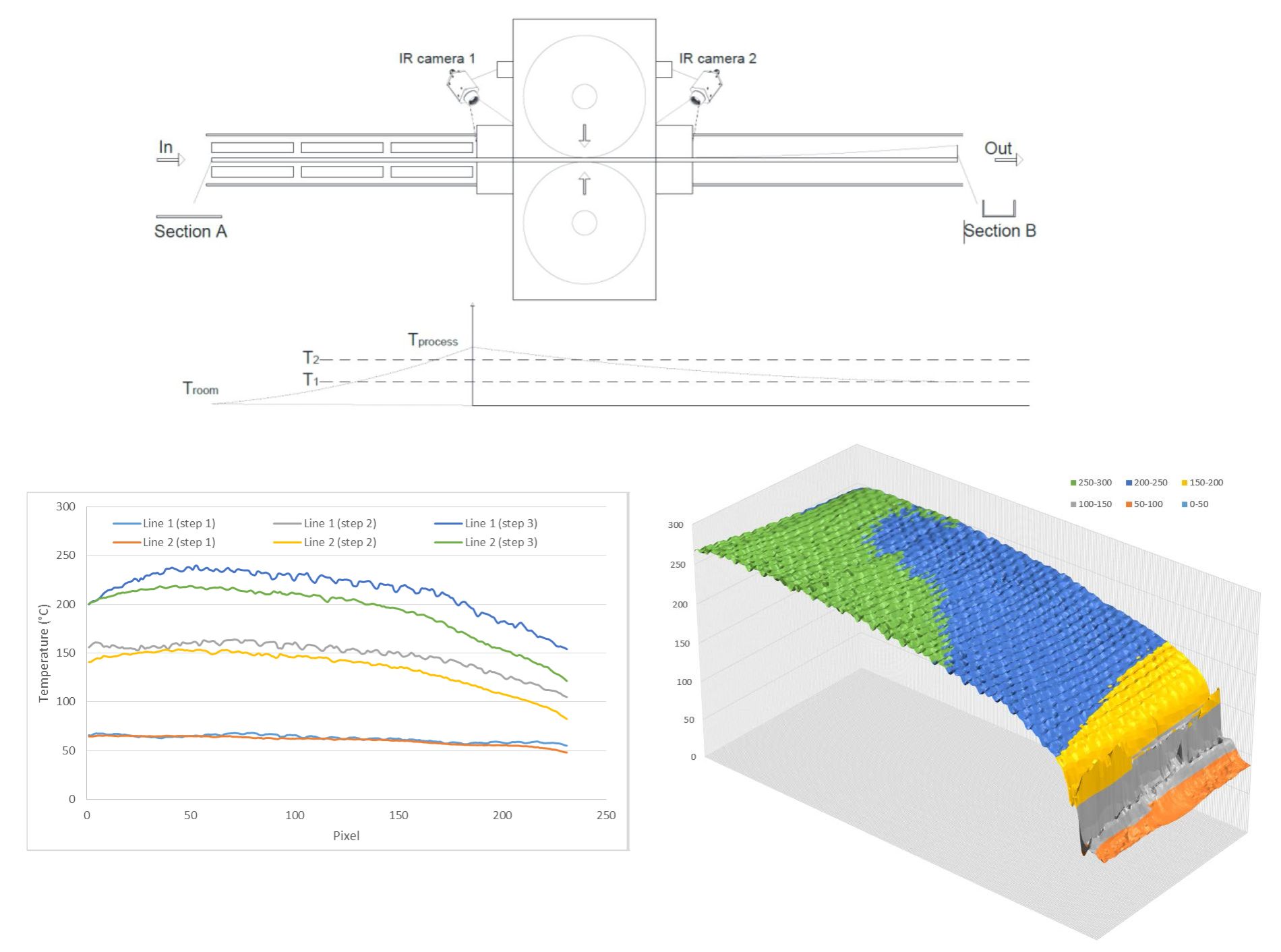
L'uniformité de la température du matériau à travers la section transversale du profil a été évaluée aux deux points limites - la ligne 1 est proche de l'étape de chauffage et la ligne 2 est plus loin dans le processus de formage. Chacune a été divisée en 3 étapes successives (Fig. 19) :phase initiale (étape 1), processus de formage démarré (étape 2) et formage à vitesse réduite (étape 3). L'IRT a montré que la température sur les bords extérieurs du stratifié était inférieure à celle de la zone centrale, ce qui entraîne un chauffage et des propriétés mécaniques inégaux. Une représentation 3D des températures de surface enregistrées par IRT (Fig. 20) a fourni une aide visuelle pour mieux comprendre la distribution de la température.
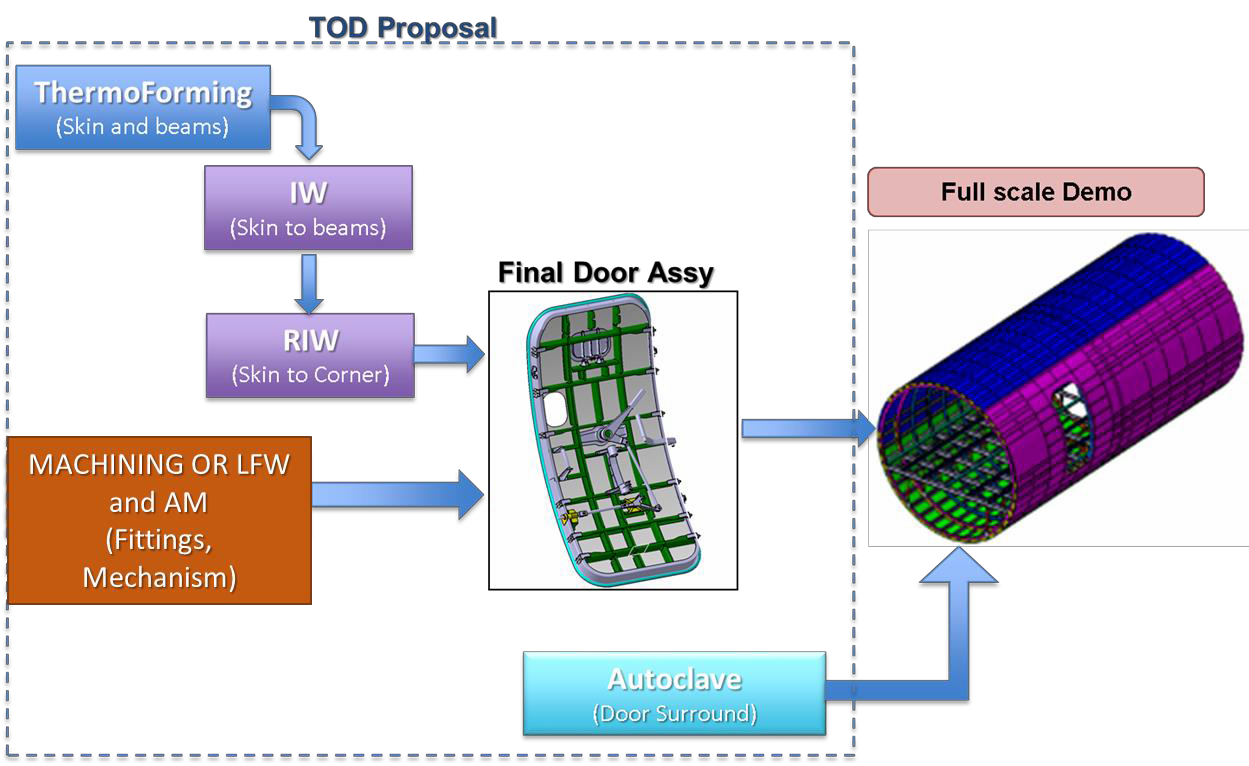
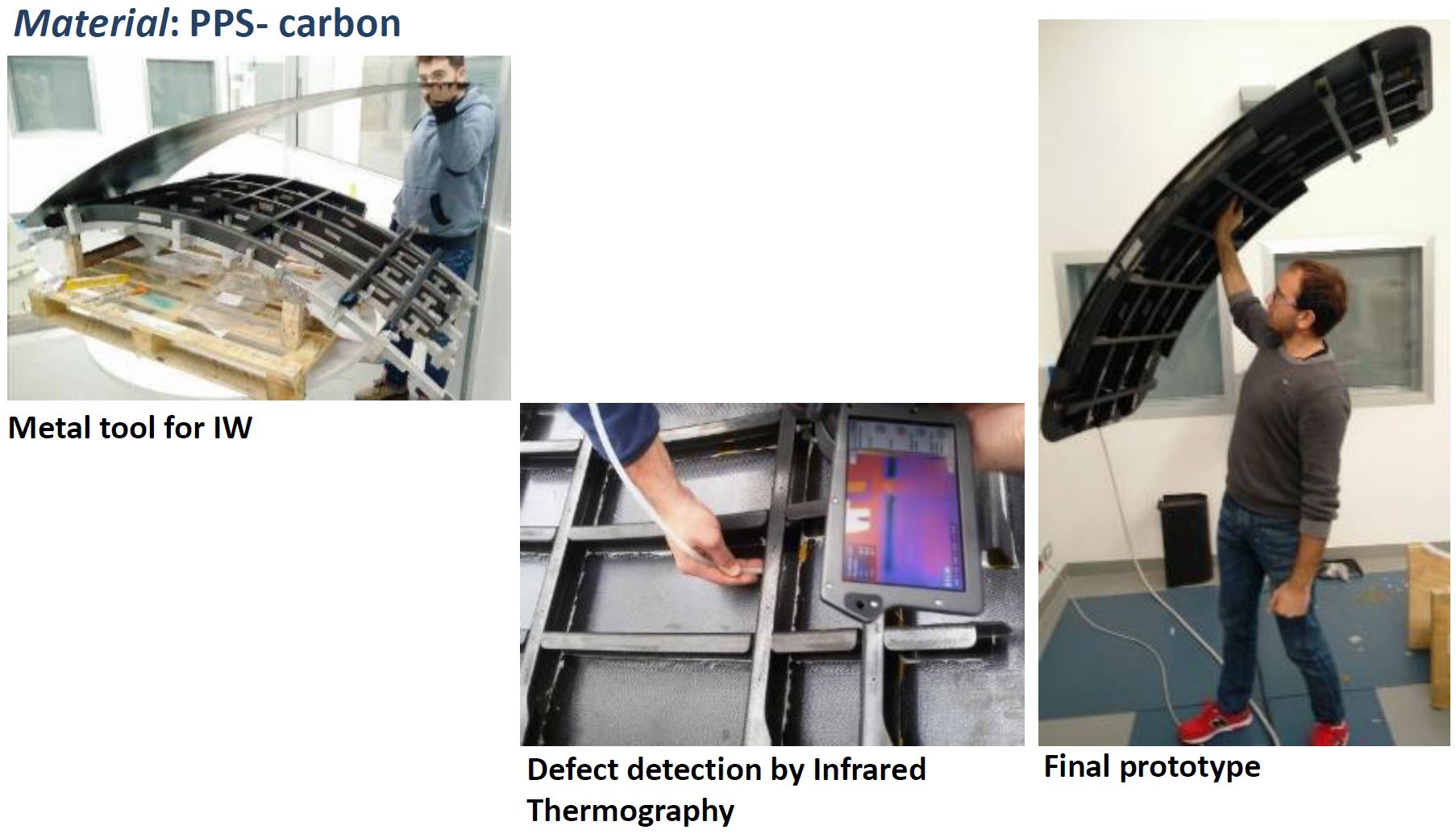
TOD – Thermoplastique sur les portes (JTI-CS2-2017-CfP07-REG-01-12). TOD vise à développer et valider la production et l'assemblage rapides d'une porte en composite thermoplastique à grande échelle (y compris les sous-structures de fuselage) pour un avion régional. TOD fait partie de la Clean Sky 2 Regional Aircraft IADP (Innovative Aircraft Demonstrator Platform), qui porte l'intégration des technologies développées dans la première phase de Clean Sky Green Regional Aircraft ITD (Innovative Technology Demonstrator) à un niveau supérieur de complexité et de maturité via deux bancs d'essais volants et trois grands démonstrateurs au sol intégrés. Dirigé par Leonardo, le CETMA travaillera avec les partenaires du projet The Welding Institute (TWI, Cambridge, Royaume-Uni) et l'aérospatiale de niveau 1 et la société d'ingénierie/industrialisation DEMA (Design Manufacturing SpA, Somma Vesuviana, Italie).
L'approche proposée comprend l'optimisation et la validation du thermoformage pour les processus de fabrication et d'assemblage de composants tels que le soudage par induction (IW) et le soudage d'implants résistifs (RIW), qui permettent de réduire le poids en éliminant les attaches mécaniques. TOD fera également progresser l'automatisation de l'industrie 4.0 et la surveillance en ligne pour prendre en charge la production à haut débit de pièces de haute qualité (zéro défaut) avec un contrôle de processus robuste. Les avantages attendus incluent :
- Réduction de poids minimale de 15 %
- Réduction des déchets et rebuts de 10 % grâce aux capteurs et à la surveillance en ligne
- Jusqu'à 75 % d'économies d'énergie par rapport au traitement en autoclave standard
- Coûts récurrents réduits grâce à une fabrication intelligente adaptative (flexibilité accrue, diminution du coût des outils de ligne complète)
- Amélioration des émissions de CO2 lors de la fabrication et de l'exploitation des avions plus légers.
Le CETMA est impliqué dans de nombreux autres projets de développement. Un exemple est NHYTE (Nouvelles aérostructures composites thermoplastiques hybrides fabriquées par Out of Autoclave Continuous Automated Technologies) qui vise à démontrer des aérostructures intégrées innovantes fabriquées à partir de matériaux matriciels thermoplastiques hybrides dotés de capacités multifonctionnelles.
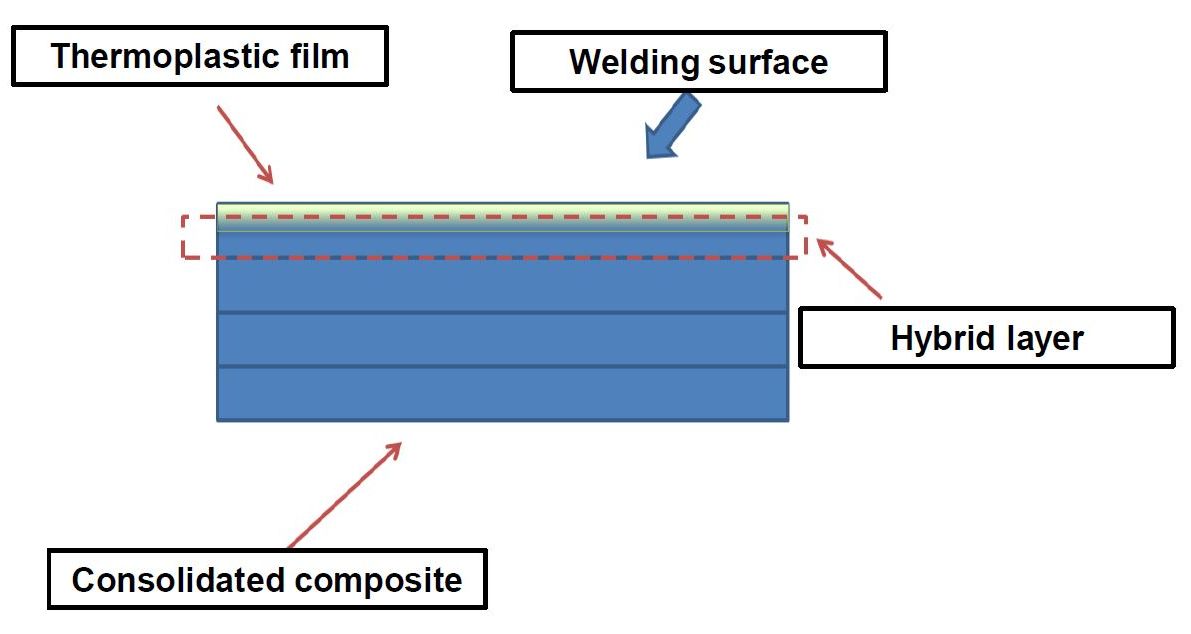
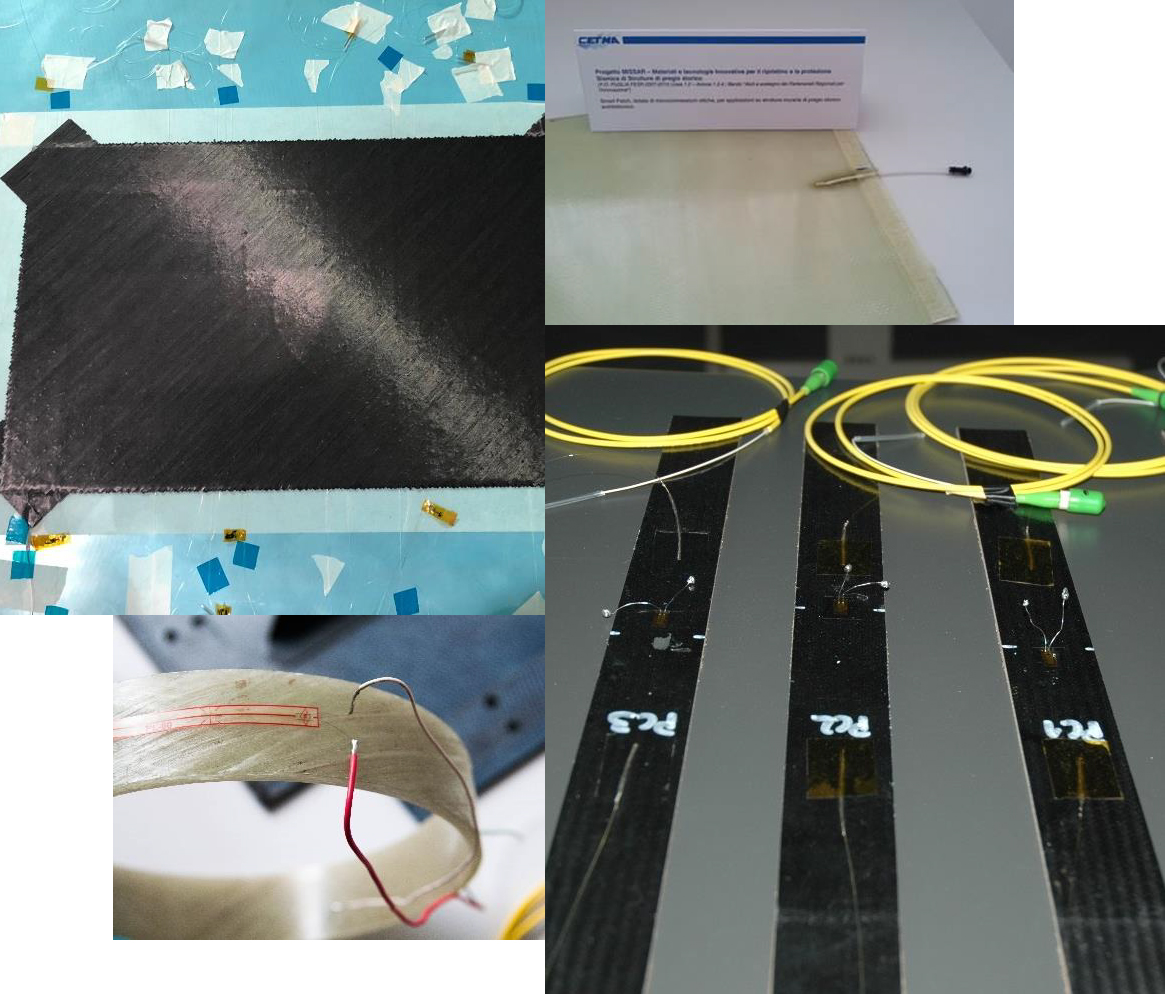
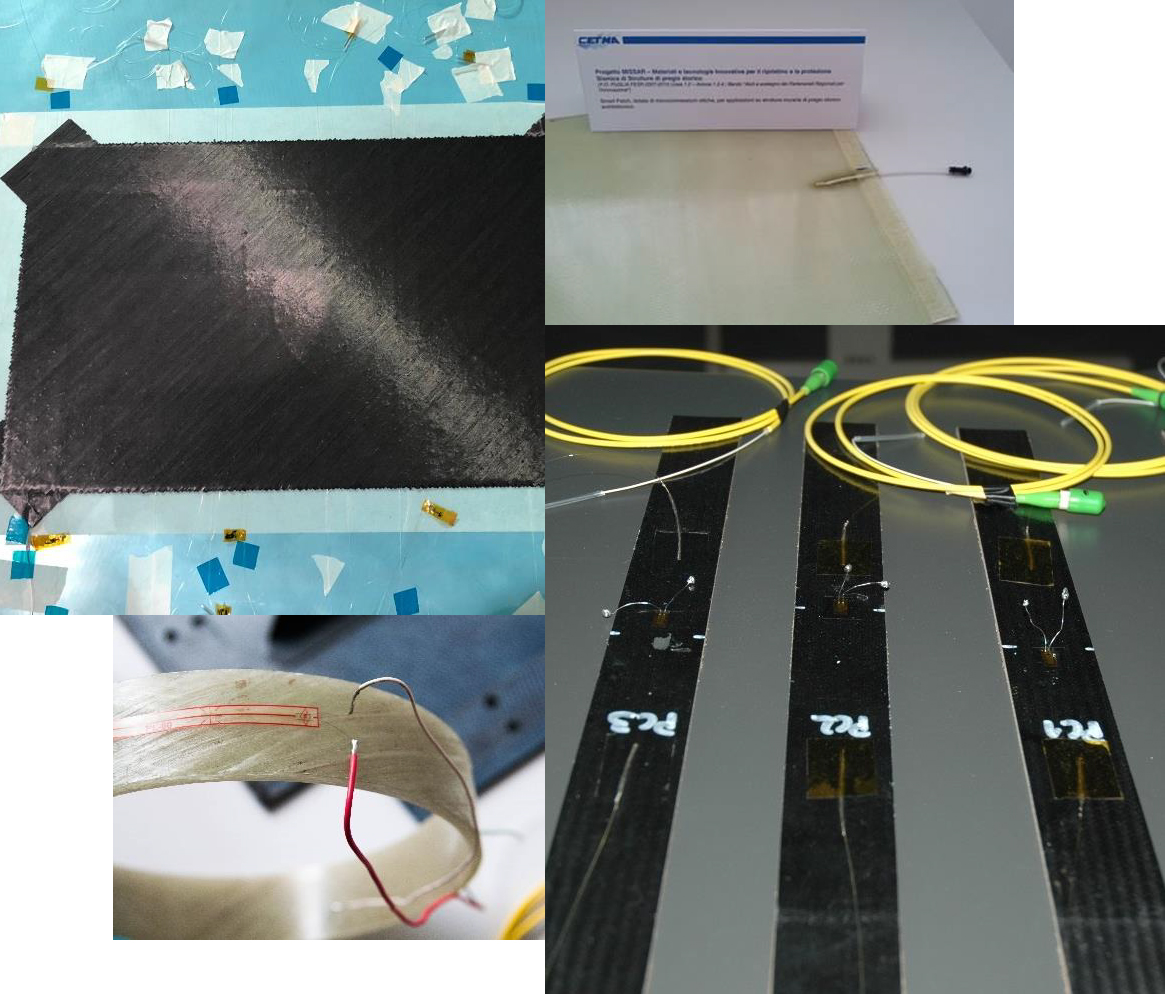
Financé dans le cadre du programme Horizon 2020 et dirigé par NOVOTECH (Naples, Italie), NHYTE a commencé en septembre 2018 et devait se terminer en janvier 2020. Le matériau hybride haute performance est basé sur un préimprégné commercial en fibre de carbone/PEEK avec un PEI amorphe ajouté. films pour permettre la consolidation in-situ avec placement automatisé des fibres (ISC AFP) puis l'assemblage via la technologie de soudage par induction brevetée de CETMA. Le CETMA a achevé une vaste campagne de caractérisation comprenant des tests physico-mécaniques et virtuels du matériau composite hybride et de la configuration du procédé de soudage par induction.
Recyclage de la fibre de carbone
Un autre domaine clé pour le CETMA est le recyclage. Le CIRCÉ Le projet vise à utiliser les déchets de préimprégné générés lors de la fabrication de pièces composites en les recyclant dans un composé de moulage par compression, qui sera ensuite utilisé pour mouler des inserts d'orteils pour chaussures de sécurité. Le CETMA caractérisera cette matière première secondaire et développera un modèle numérique pour prédire les performances structurelles des inserts de chaussures. Ce modèle aidera à analyser et à vérifier le comportement à l'impact pour répondre aux réglementations de sécurité, les résultats étant utilisés pour affiner et finaliser la conception des inserts d'orteils. L'équipe de projet italienne comprend Base Protection (Barletta), le fabricant de pièces composites pour sports mécaniques/automobiles HP Composites (Ascoli Piceno), le spécialiste des machines et des lignes de production Elks Group (Ascoli Piceno) et Petroceramics (Stezzano).
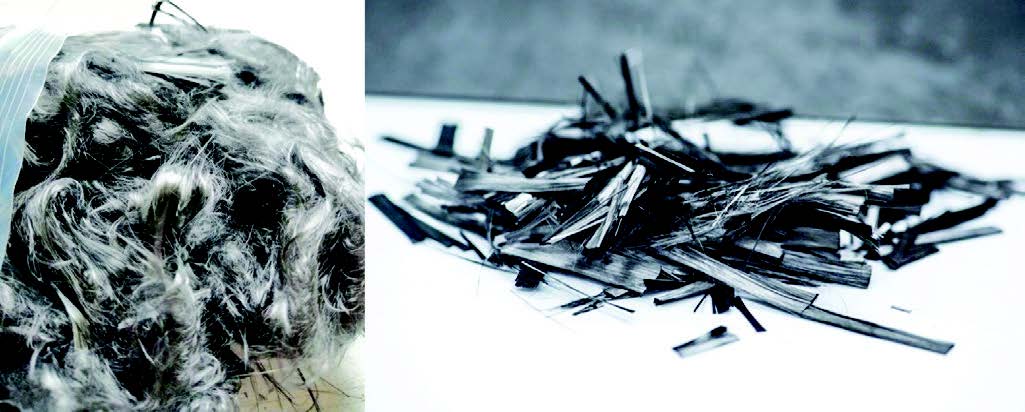
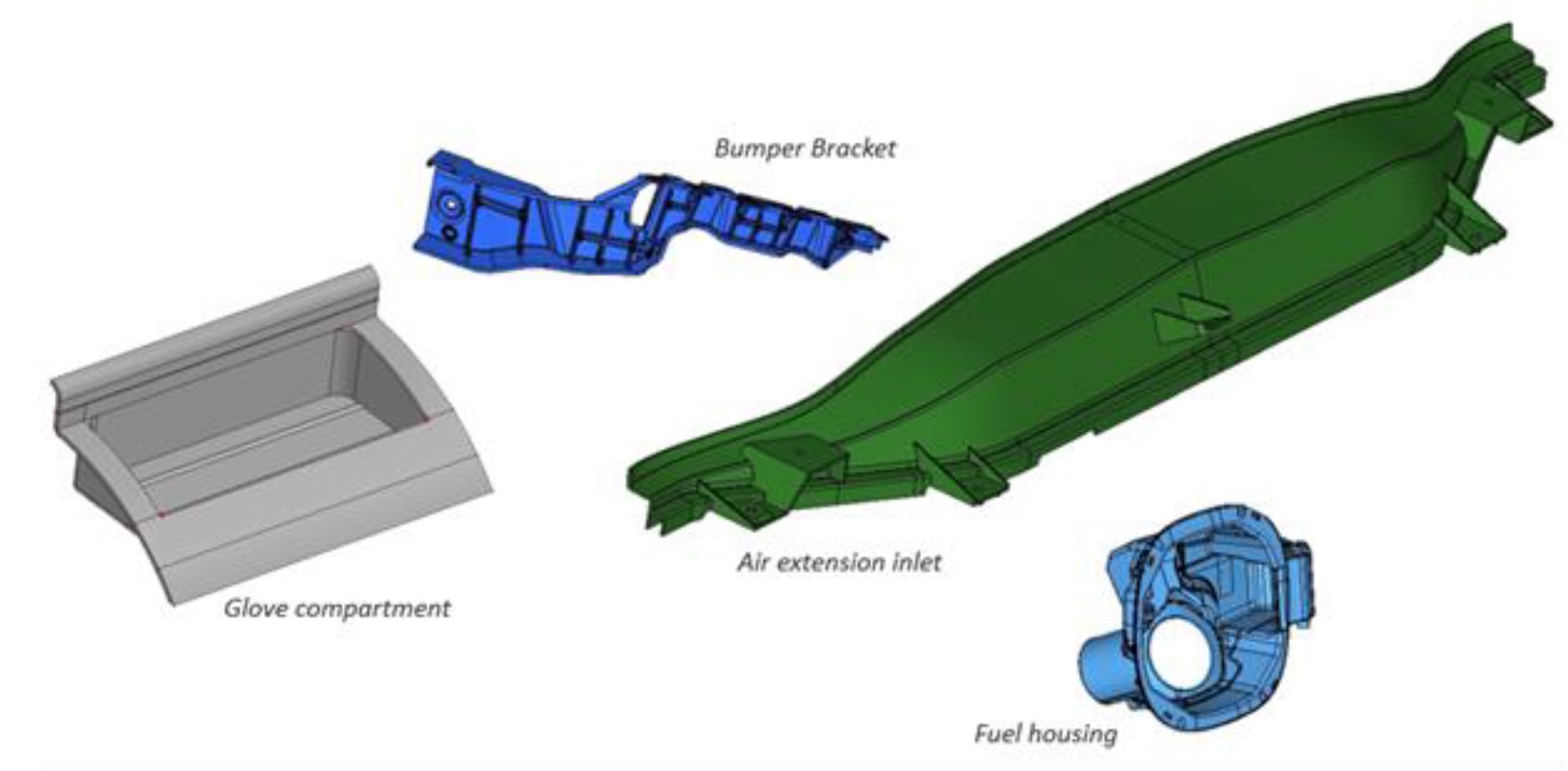
Le plus gros investissement du CETMA dans le recyclage à ce jour a peut-être été réalisé via le programme REVALUE projet visant les fibres de carbone recyclées pour des composites à haute VALEUR. Financé par l'Institut européen d'innovation et de technologie (EIT, Budapest, Hongrie), l'objectif du projet REVALUE est de prendre de la fibre de carbone recyclée (RCF) fournie par le principal producteur ELG Carbon Fiber (Coseley, Royaume-Uni) en utilisant la pyrolyse et de la combiner avec polymères thermoplastiques vierges et recyclés pour remplacer les matériaux actuels utilisés par Centro Ricerche Fiat (CRF, Turin, Italie) pour la production de composants automobiles sélectionnés.
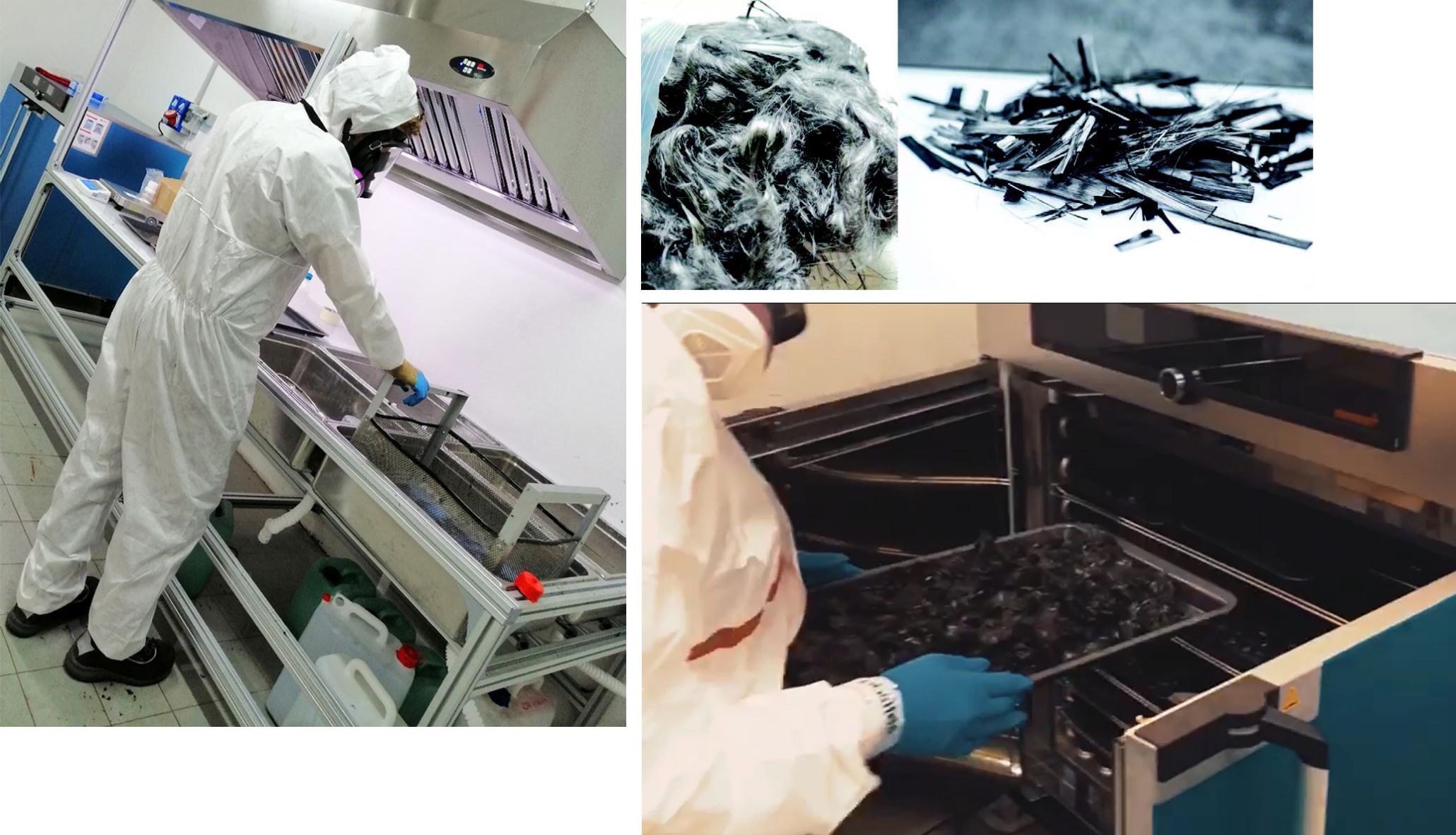
Cependant, comme indiqué dans le magazine JEC Composites de janvier-février 2020 article, « Nouvelle formulation de dimensionnement pour les fibres de carbone recyclées » par Alessandra Passaro, et. al., le RCF produit par pyrolyse n'a pas d'ensimage, ce qui rend les fibres cassantes sujettes à de fréquentes ruptures lors de la manipulation ainsi qu'à la séparation des câbles de fibres en filaments, ce qui donne une forme enchevêtrée et « duveteuse » avec une faible densité apparente. Dans le cadre de REVALUE, le CETMA a développé une formulation spécifique d'encollage pour RCF, compatible avec le polypropylène (PP) vierge ou recyclé et le PA6. Il a ensuite évalué la capacité de dimensionnement pour améliorer la transformabilité du RCF et augmenter l'interface avec les matrices thermoplastiques sélectionnées.
Pour ce faire, le CETMA a développé une installation pilote de dimensionnement du RCF, capable d'appliquer le dimensionnement en kilogrammes et, en même temps, d'évaluer l'effet des principaux paramètres sur le processus de dépôt. L'usine comprend trois stations principales :traitement d'encollage et lavage des fibres; manipuler les fibres sèches avant et après traitement; et sécher les fibres au four. Quatre kilogrammes de RCF peuvent être traités par jour en cycle continu.
Les RCF calibrées du CETMA ont ensuite été utilisées par le centre de recherche français CEA et le compoundeur français SUEZ pour produire un mélange de moulage à partir de polymères thermoplastiques vierges et recyclés. La caractérisation physico-chimique des composés a été achevée et la capacité du dimensionnement CETMA à améliorer les performances mécaniques finales des composites a été vérifiée.
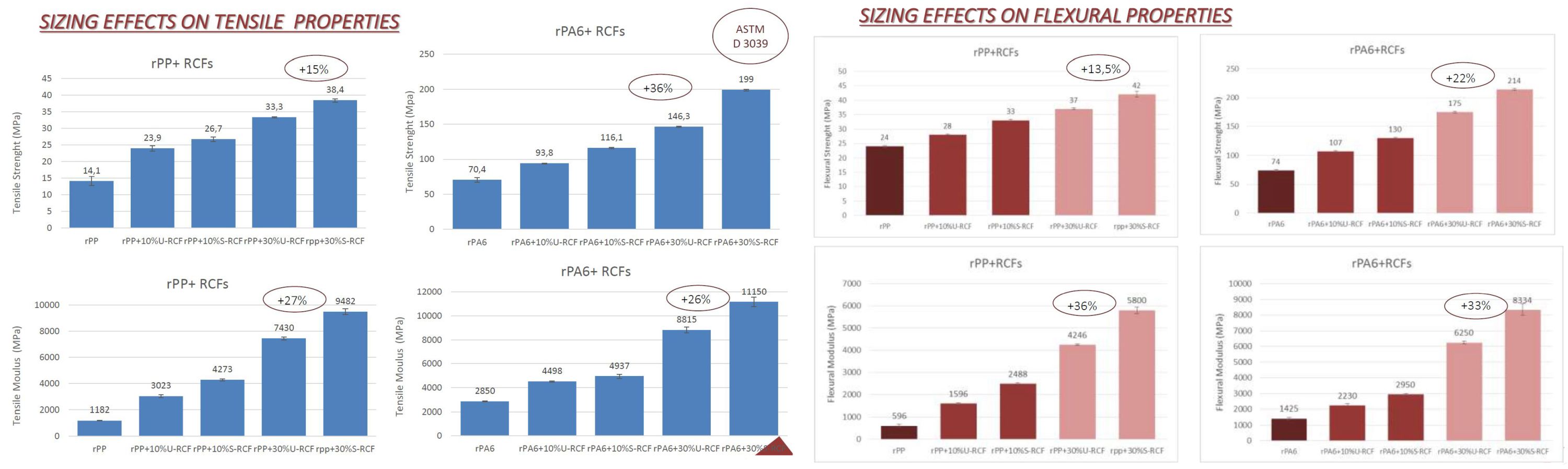
Les composés de moulage innovants RCF ont ensuite été utilisés pour mouler par injection des composants semi-structurels automobiles qui sont actuellement fabriqués avec du PP ou du PA6 renforcé de fibres de verre. Au-delà de l'avantage évident du recyclage et de la réutilisation des matériaux, la réduction du poids des véhicules, de la consommation de carburant et des émissions de CO2 a également été démontrée.
En dehors de REVALUE, CETMA a également développé et évalué le dimensionnement pour RCF dans plusieurs processus composites, y compris le moulage par compression, l'infusion sous vide et le RTM, montrant des propriétés améliorées dans tous les cas.
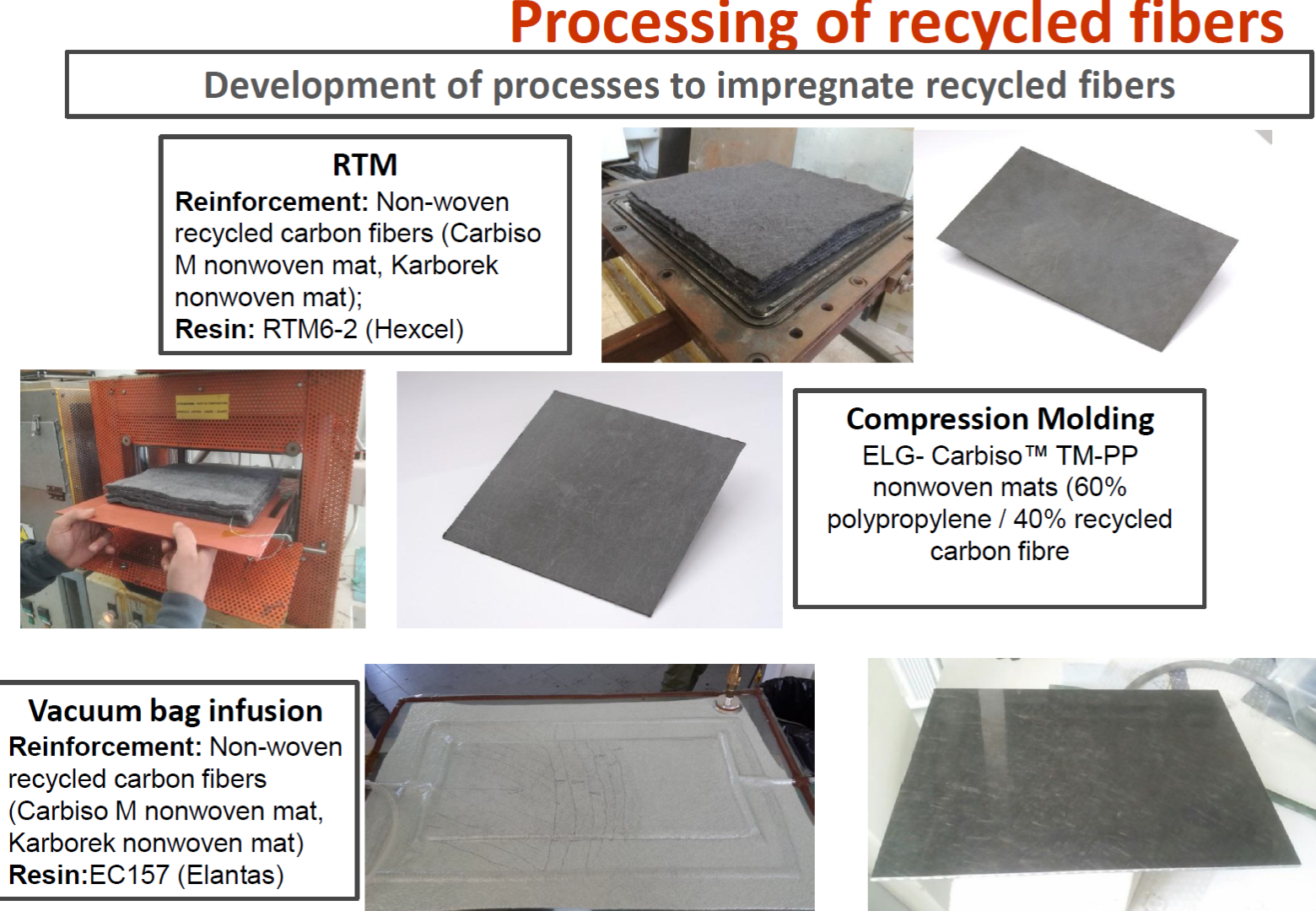
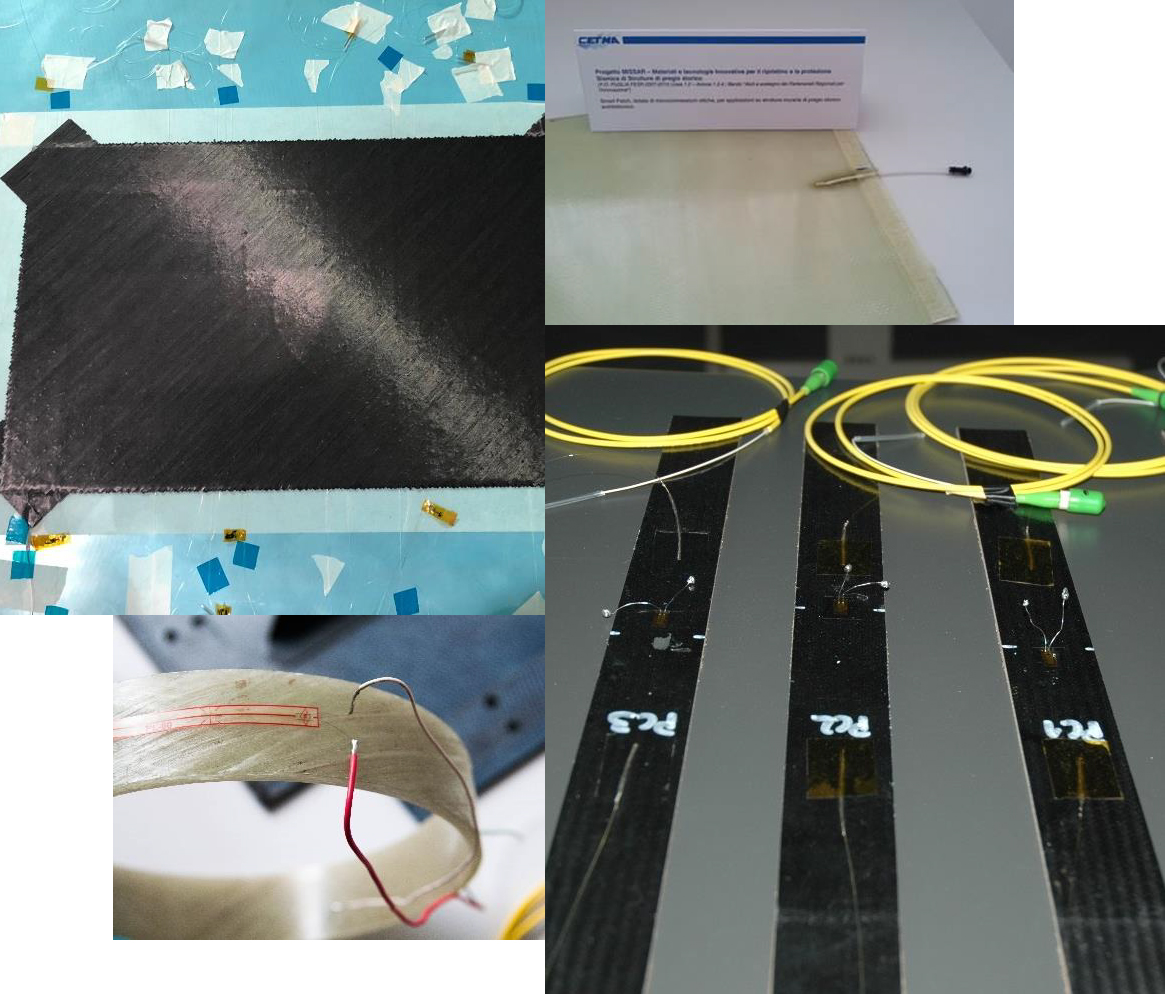
Surveillance de la santé structurelle (SHM)
Ce dernier domaine clé de l'activité des composites pour le CETMA est également une priorité croissante dans l'industrie. «Nous avons de nombreuses années d'expérience dans l'application de SHM pour les applications de construction et de bâtiment», note Passaro. « Et nous avons également beaucoup travaillé avec SHM dans les composites. Nous savons que cela sera important pour les applications futures et nous sommes intéressés à continuer à travailler avec les fabricants de composites et l'industrie pour faire avancer cette technologie.
Résine
- Personnalisation des capteurs à ultrasons pour l'optimisation et le contrôle des processus composites
- Composites One et IACMI organisent un atelier de deux jours
- Mesure de la température à l'intérieur des composites et des lignes de liaison
- TPAC et TPRC développent un procédé de recyclage des composites thermoplastiques
- L'additif PES augmente la résistance à la rupture et aux microfissures dans les composites époxy
- SABIC et Nottingham Spirk s'associent pour accélérer le développement de l'innovation
- Au service du monde des composites en Israël et aux États-Unis
- Défis de coupe :composites à matrice mixte et composites renforcés de fibres
- ABB Robotics :Innovation technologique et R&D robotique