Capteurs de pression portables ultrasensibles basés sur des tissus enduits de nanofils d'argent
Résumé
Les capteurs de pression flexibles ont attiré une attention croissante en raison de leurs applications potentielles dans les systèmes portables de surveillance et de soins de la santé humaine. Ici, nous présentons une approche facile pour la fabrication d'un capteur de pression piézorésistif entièrement textile avec des tissus enduits de nanofils Ag intégrés. Il tire pleinement parti de l'effet synergique des contacts multi-niveaux fibre/fil/tissu, conduisant à une sensibilité ultra-élevée de 3,24 × 10 5 kPa −1 à 0–10 kPa et 2,16 × 10 4 kPa −1 à 10–100 kPa, respectivement. De plus, l'appareil a obtenu un temps de réponse/détente rapide (32/24 ms) et une stabilité élevée (> 1000 cycles de chargement/déchargement). Ainsi, un tel capteur de pression tout textile à hautes performances devrait être applicable dans les domaines des vêtements intelligents, de la surveillance de l'activité et des appareils de santé.
Introduction
Avec le développement récent de l'électronique portable, il existe une demande croissante de capteurs de pression flexibles dans une multitude d'applications, notamment les dispositifs e-skin, les systèmes de surveillance de la santé et les robots intelligents [1,2,3,4,5,6,7, 8]. Afin d'être utilisés de manière viable dans ces applications, les capteurs de pression doivent présenter d'excellentes performances de sensibilité, fournissant ainsi des informations exhaustives pour un diagnostic ou une analyse précis.
À ce jour, de nombreuses méthodes ont été développées pour améliorer les performances du capteur en optimisant les nanomatériaux, notamment les nanotubes de carbone (CNT) [1], les nanofeuillets de graphène [9], les nanofils métalliques [10,11,12,13,14,15,16 ,17,18,19], les polymères conducteurs [20] et leurs matériaux composites [21,22,23,24,25,26]. En particulier, le nanofil d'Ag (AgNW) a été largement exploré en tant que matériaux de détection ou charges conductrices dans les capteurs de pression en raison de ses excellentes propriétés électriques. Par exemple, Wang et al. a fabriqué un capteur de pression flexible basé sur le film PU rempli d'AgNW, offrant une sensibilité de 5,54 kPa −1 à la plage de pression inférieure à 30 Pa [27]. Ho et al. ont rapporté un capteur de pression transparent renforcé par des fissures constitué de deux films stratifiés de PDMS portant des canaux microfluidiques intégrés à AgNW [28]. Cependant, la plupart de ces capteurs ont été fabriqués à l'aide de substrats élastiques étanches à l'air, respirants et inconfortables à porter, limitant ainsi leurs applications pratiques.
Plus récemment, les capteurs de pression à base de textile ont attiré une attention croissante en raison de leur douceur, de leur respirabilité et de leur biocompatibilité, ce qui les rend durables et portables à long terme. Les AgNW ont été largement utilisés dans les capteurs de pression à base de textile en tant que couche sensible. Pour les capteurs à base de textile, une structure typique est constituée de circuits flexibles recouverts d'un tissu de conduction, et ils exploitent un changement de résistance de contact entre les circuits et les tissus. Lorsqu'une pression est appliquée, les deux films entrent en contact et un courant important est généré. Par exemple, Wei et al. ont démontré un capteur de pression portable avec la structure de deux feuilles de coton conductrices enduites d'AgNWs [29]. Zhou et al. ont conçu un capteur de pression avec une électrode textile imprimée et un tissu de coton enduit d'AgNW [30]. Cependant, la plage de pression est limitée pour la structure de ces capteurs. Ainsi, diverses conceptions de structure ont été proposées pour améliorer les performances des capteurs de pression. Zhong et al. a développé un capteur piézorésistif ultrasensible à haute flexibilité, composé de nanofibres POE et d'AgNW par une méthode de filtration facile. Les nanofibres sont répliquées sur des textiles en nylon à motifs avec différents espacements de fibres [12]. Malgré ces progrès, un capteur de pression entièrement textile avec une sensibilité et une conception de structure ultra-élevées est rarement signalé de loin.
Ici, nous avons proposé une nouvelle stratégie pour la fabrication de capteurs de pression entièrement textiles. La solution AgNWs a été synthétisée, puis le tissu conducteur peut être fabriqué à l'aide d'une méthode de revêtement par immersion, qui a été réalisée en plongeant des morceaux de coton dans la dispersion AgNW. L'élément de détection actif contenait des cotons enduits d'AgNW à double couche avec une entretoise en maille de coton pour sécuriser le contact initial entre eux. La détection de pression est basée sur les changements du courant électrique dus au contact entre les couches de revêtement lors de la pression externe. Ce capteur de pression piézorésistif tout textile tire pleinement parti de l'effet synergique des contacts multi-niveaux fibre/fil/tissu, conduisant à la sensibilité ultra-élevée de 3,24 × 10 5 kPa −1 à 0–10 kPa et 2,16 × 10 4 kPa −1 à 10–100 kPa, respectivement. Pendant ce temps, le capteur de pression a obtenu un temps de réponse/relaxation rapide (32/24 ms) et une stabilité élevée (> 1000 cycles de chargement/déchargement). Ces appareils ont de nombreuses applications dans les vêtements intelligents, la surveillance des activités et les appareils de santé.
Section expérimentale
Matériaux et méthodes
La solution d'AgNWs a été synthétisée par méthode hydrothermale. Tout d'abord, la solution de PVP a été ajoutée dans EG; puis, le mélange a été agité pendant 20 min pour fabriquer la solution de PVP/EG. Par la suite, les solutions de AgNO3 /EG et NaCl/EG ont été préparés avec une méthode similaire. Deuxièmement, les solutions de AgNO3 /EG et NaCl/EG ont été ajoutés dans PVP/EG, et le mélange a été agité et transféré dans un chaudron de réaction. Troisièmement, la bouilloire a été chauffée à 140 °C pendant 2 h, puis à 160 °C pendant 30 min. Par la suite, la bouilloire a été naturellement refroidie à température ambiante. Les précipités obtenus ont été lavés et filtrés par centrifugation avec de l'acétone et de l'eau désionisée plusieurs fois pour former une poudre blanche. Enfin, les AgNW obtenus ont été dispersés par ultrasons dans de l'éthanol.
Fabrication du capteur de pression
Le capteur de pression tout textile a été fabriqué selon le procédé « trempage et séchage » [31] (Fig. 1). Tout d'abord, les tissus de coton ont été nettoyés avec du DI et de l'éthanol anhydre chacun pendant 15 min. Deuxièmement, les tissus ont été plongés dans la solution obtenue d'AgNWs pendant 20 min et suivis d'un séchage à 90 °C pendant 10 min (Fig. 1a). Ensuite, les électrodes de cuivre ont été fixées à la surface des tissus enduits d'AgNW avec de la pâte d'argent et séchées à 90 °C pendant 1 h. Pendant ce temps, les espaceurs en maille de coton avec différents diamètres de trous ont été fabriqués par un processus de gravure au laser (Fig. 1b). Enfin, le tissu de détection à double couche avec une entretoise en maille de coton insérée a été assemblé par un processus d'emballage face à face (Fig. 1c).
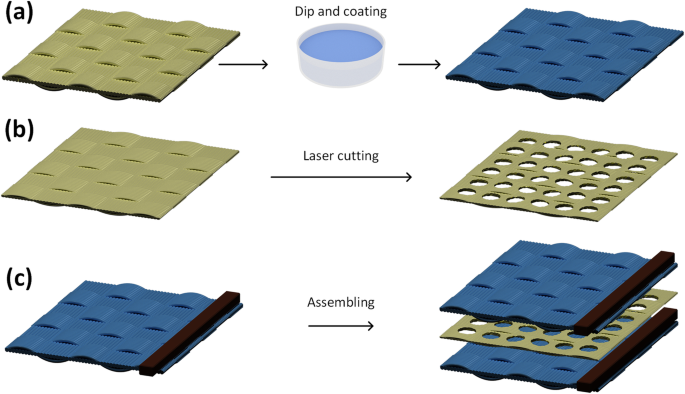
Processus de fabrication du capteur de pression tout textile. un Le processus de préparation du coton enduit AgNW. b Le processus de fabrication du coton intercalaire en maille. c Le processus d'assemblage du capteur de pression
Caractérisation
Les images de microscopie électronique à balayage (MEB) des surfaces de tissu revêtues d'AgNW ont été prises via un GeminiSEM 500 (ZEISS, New York, Amérique) à 5 kV. La réponse actuelle des capteurs de pression a été enregistrée à l'aide d'un compteur source numérique (Keithley 4200, Amérique) et mesurée à l'aide d'un dynamomètre numérique (SJS-500V, Chine).
Résultats et discussion
La figure 2 montre des images SEM de la morphologie du tissu enduit d'AgNWs avec un grossissement différent. Comme le montre la figure 2a, les fils du coton étaient naturellement stratifiés avec une structure poreuse. La surface la plus externe du tissu est recouverte d'AgNWs (Fig. 2b), sur lesquels des nanofils sont uniformément enroulés sur les fibres. En particulier, entre les fils voisins, il existe des espacements vides qui sont comblés par les réseaux conducteurs AgNW attachés (Fig. 2c). A noter, des fils longs et uniformes ont été observés entre les fils adjacents, et le diamètre moyen de AgNW est d'environ 55 nm. Sur la figure 2d, les AgNW sont formés de manière homogène dans la zone principale de la surface du fil, tout en étant déconnectés à un moment donné en raison de la mauvaise adhérence. De plus, la distance entre les nanofils collés sur le fil individuel est relativement plus grande que celle des nanofils entre les fils voisins.
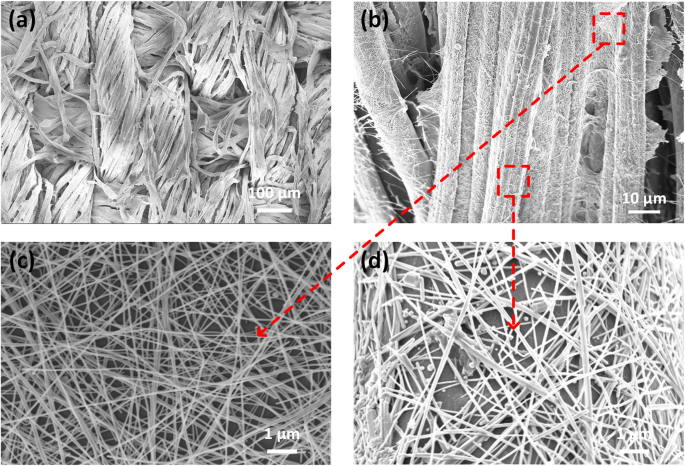
La morphologie des tissus enduits d'AgNWs. un –d Les images SEM de la morphologie de surface du tissu enduit d'AgNWs avec différentes positions d'AgNWs et différents grossissements, dans lesquels c est l'image SEM des AgNWs entre les fils et d les AgNWs enduits sur la fibre unique
De plus, la densité des AgNW à la surface des tissus a été ajustée par les temps des cycles de revêtement par immersion. Le tissu enduit d'AgNWs avec 1 cycle de trempage et 5 cycles de trempage a été montré sur la figure S1 et la figure 2d, respectivement. Par rapport à celui à haute densité, les espacements des mailles de nanofils d'un cycle d'immersion sont passés de moins de 1 à 2 à 4 μm.
La composition du tissu revêtu d'AgNWs a également été étudiée par spectroscopie à rayons X à dispersion d'énergie (EDS), comme illustré dans l'encart de la figure S2. En plus des teneurs en C et O attribuées principalement au coton, l'élément Ag a également été observé, indiquant la répartition des AgNW sur le coton.
Le principe de détection du capteur de pression est illustré sur la figure 3a, et les images SEM en coupe transversale du capteur avec différentes pressions sont illustrées sur les figures 3b-e. À l'état de déchargement, la résistance initiale est importante, ce qui est causé par les AgNW sans contact sur les tissus (Fig. 3b). Une fois la pression appliquée, les contacts croissants à l'échelle des fibres des nanofils sur les tissus adjacents ont contribué à une diminution de la résistance (Fig. 3c). De plus, lorsque les nanofils sur les tissus étaient complètement en contact, la pression continue chargée sur les fibres augmentait alors les contacts à l'échelle du fil. Comme le montre la Fig. 3d, la longueur des fils en Y direction sont réduites d'environ 200 à 160 μm, confirmant la compression entre les fils. D'après les images SEM en coupe, les AgNW se sont formés à la fois sur la surface du fil et à l'intérieur des fils adjacents (Fig. S3). Lorsque la pression était appliquée et que les fils étaient comprimés, les AgNW à l'intérieur des fils pouvaient entrer en contact et réduire davantage la résistance du capteur. Avec l'augmentation de la pression de chargement, les tissus voisins ont été comprimés (Fig. 3e); les contacts à l'échelle du tissu ont encore réduit la résistance du capteur en raison de la zone de contact accrue entre les tissus de parement. À ce stade, l'épaisseur totale des tissus à double couche a été réduite de 600 à 350 µm. Par conséquent, la détection de pression des capteurs a été déterminée par l'effet synergique du contact multi-échelle fibre/fil/tissu. Ces images SEM en coupe ont confirmé le mécanisme de détection de pression.
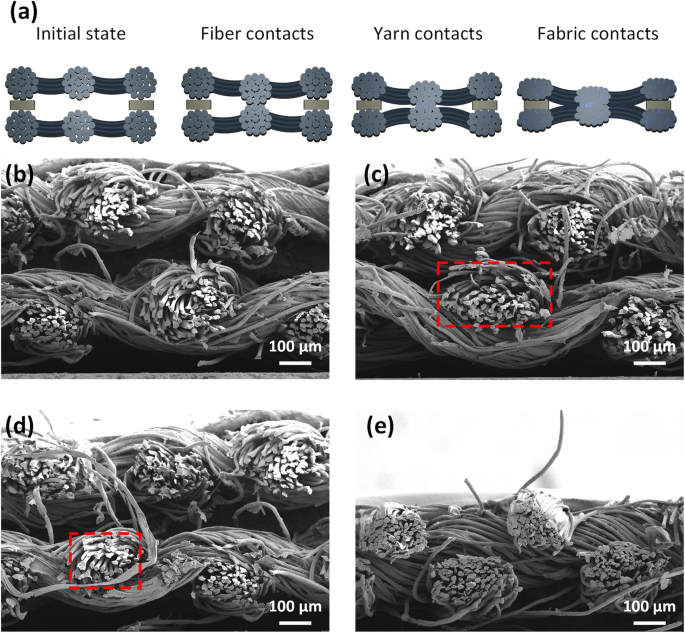
Le principe de détection du capteur de pression. un Illustration schématique de la détection de pression. b –e Les images SEM en coupe du tissu enduit d'AgNWs sous différentes pressions
L'influence de la flexion sur la morphologie de la surface des tissus revêtus d'AgNWs a été étudiée par des images SEM en coupe transversale illustrées à la Fig. S4. Avec la faible déformation en flexion, il n'y a pas de problème évident de fissure et de décollement du réseau AgNWs sur les tissus (Fig. S4b) par rapport à l'état initial (Fig. S4a). Afin d'étudier plus avant l'influence de la déformation par flexion, les images SEM de tissus enduits d'AgNWs avec des cycles de flexion 500 fois ont été prises et présentées sur la figure S5. La figure S5 montre de nombreux points délaminés susceptibles de provoquer une dégradation du dispositif. Ce résultat indique que la stabilité du tissu enduit d'AgNWs doit encore être améliorée à l'avenir.
La figure 4a montre les courbes courant-tension du capteur de pression sous différentes pressions. Lorsque la pression appliquée augmentait de 0 à 100 kPa, la résistance du capteur diminuait. De plus, la réponse du capteur était stable et conforme à la loi d'Ohm [32]. Le courant du capteur de pression est représenté sur la figure 4b, qui est relativement constant sous différentes pressions appliquées, révélant que la réponse du capteur est stable pour différentes pressions. Par conséquent, les résultats fournissent une excellente stabilité électrique pour l'application potentielle du capteur de pression.
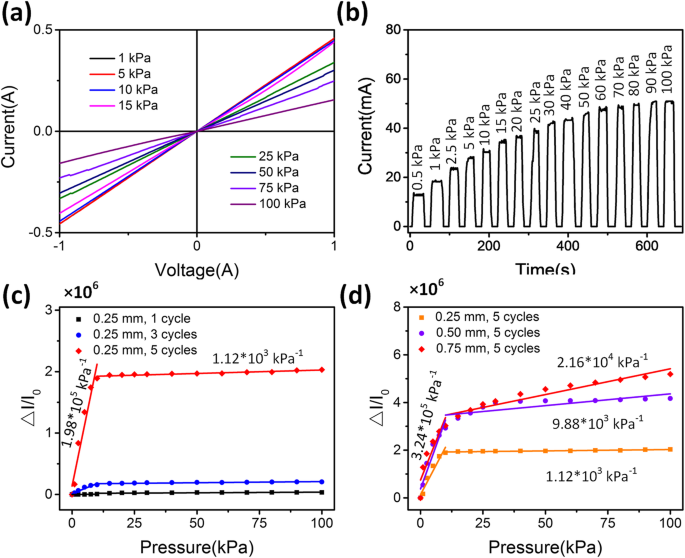
Performances des capteurs de pression. un Courbes I-V du capteur de pression avec différentes pressions appliquées. b La réponse actuelle du capteur sous différentes pressions. c , d La comparaison des performances des capteurs de pression avec différents cycles de revêtement par immersion et diamètres de trous de maille
Pour étudier les performances des capteurs de pression, le courant relatif change (ΔI /Je 0 ) en fonction de la pression avec les différents cycles de revêtement par immersion AgNWs et les diamètres des trous de maille ont été montrés dans les Fig. 4c, d. Ici, la sensibilité du capteur de pression a été définie comme S =(ΔJe /Je 0 )/P , où P désigne la pression appliquée. À un diamètre de trou de maille de 0,25 mm, la sensibilité du capteur de pression dépendait fortement des cycles de revêtement par immersion d'AgNW. La sensibilité des capteurs a été améliorée de 2,12 × 10 3 kPa −1 à 1,98 × 10 5 kPa −1 dans la plage de 0 à 10 kPa lorsque les cycles de revêtement par immersion sont passés de 1 à 5. De plus, la sensibilité s'est améliorée de 764 à 1,12 × 10 3 kPa –1 à 10–100 kPa. L'amélioration de la sensibilité avec des cycles de revêtement par immersion élevés est principalement attribuée à l'augmentation des densités AgNWs.
De plus, la dépendance du diamètre du trou a ensuite été caractérisée. Les capteurs de pression avec 5 cycles de revêtement par immersion présentaient des sensibilités améliorées avec des diamètres croissants, qui sont passés de 1,12 × 10 3 , 9,88 × 10 3 , à 2,16 × 10 4 kPa –1 dans la plage de pression de 10 à 100 kPa, respectivement. L'amélioration de la sensibilité a été principalement attribuée à l'augmentation de la zone de contact à travers les trous plus grands. Cependant, une fois que le diamètre a dépassé 1 mm avec 4 cycles, l'interface initiale des tissus de parement a entraîné plus de contact à l'état de déchargement, diminuant ainsi considérablement la résistance de contact entre les tissus (Fig. S6). De plus, lorsque l'épaisseur du coton intercalaire est modifiée, les performances des capteurs se dégradent (Fig. S7). Le capteur avec une épaisseur inférieure montre une diminution de ∆I /Je 0 en raison de la mise en contact des tissus de parement à l'état initial (Fig. S7a). De plus, une épaisseur plus élevée réduit le contact des tissus. Lorsque l'épaisseur du coton intercalaire augmentait à 1 mm, les AgNW sur les tissus n'étaient pas en contact jusqu'à ce que la pression dépasse 10 kPa (Fig. S7c).
Notamment, le capteur de pression présentait clairement deux segments de courant linéaires; la sensibilité augmente fortement dans la plage des basses pressions et augmente progressivement dans la plage des hautes pressions. Selon le principe de détection mentionné ci-dessus, dans la plage de basse pression, le contact AgNWs adjacent joue un rôle important dans l'augmentation du courant. De plus, lorsque la pression est augmentée à 10-15 kPa, les AgNW sur l'interface étaient complètement en contact. Les changements actuels étaient principalement déterminés par la résistance de contact entre les fils et les tissus, qui était relativement stable. Le contact entre le fil et les écailles du tissu a joué un rôle plus important dans le mécanisme de détection lors de cycles de revêtement par immersion de 5 fois et d'un diamètre de 0,75 mm en améliorant la sensibilité et la plage linéaire. Par conséquent, le diamètre de 0,75 mm (Fig. 4d) présentait une sensibilité plus élevée et une plage linéaire plus large en raison d'un contact accru [33, 34].
La réponse dynamique du dispositif a été étudiée sous des cycles de pression de chargement/déchargement. Le capteur a montré une réponse immédiate aux pressions cycliques. La réponse résolue en temps a été analysée pour quantifier les temps de réponse et de relaxation (Fig. 5a). Les temps de réponse et de relaxation mesurés étaient respectivement de 32 et 24 ms. Les performances du capteur sous pression différentielle sont également étudiées et illustrées à la Fig. S8. Le capteur a clairement distingué une pression subtile de 50 Pa, indiquant les excellentes performances du capteur. Le ΔJe /Je 0 avec une pression appliquée de 10 kPa avec 1000 cycles de chargement a été utilisé pour vérifier la répétabilité du dispositif (Fig. 5b). Les résultats montrent l'excellente stabilité des capteurs de pression. De plus, la perméabilité à l'air du coton normal et du coton enduit d'AgNW a été étudiée. Bien que la perméabilité à l'air ait été réduite de 787,3 à 252,6 mm/s, cette valeur est encore beaucoup plus élevée que celles récemment rapportées [35, 36]. Ce résultat a démontré que les capteurs de pression portables basés sur des tissus enduits de nanofils d'argent conservent une bonne perméabilité à l'air en raison de leur porosité élevée.
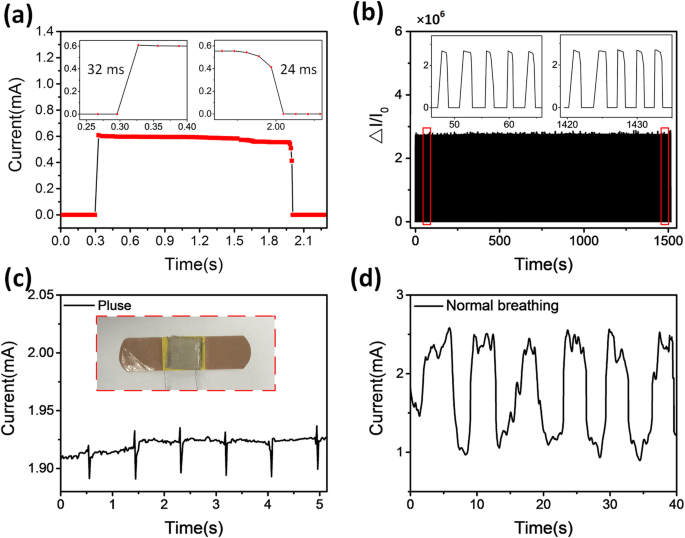
un Temps de réponse/libération de l'appareil. b Le test de cyclage de l'appareil sous une pression de 10 kPa. c Signal de pouls au poignet de l'utilisateur humain. d Le signal actuel répond à la respiration sous respiration normale
En raison de la flexibilité naturelle des tissus et de la haute sensibilité des capteurs, le capteur de pression était portable et capable de détecter des signaux mécaniques tels que le pouls physiologique et la fréquence respiratoire. Tout d'abord, le dispositif a été fixé au poignet à l'aide d'un pansement adhésif pour surveiller la pression pulsée. La figure 5c présente les données enregistrées en temps réel, dans lesquelles les fréquences cardiaques mesurées étaient ≈ 72 battements min –1 . De plus, le capteur était également attaché à un masque pour détecter les états de respiration. La figure 5d indique que la fréquence respiratoire normale de 10 respirations par minute d'un adulte et une onde de type carré pour une respiration normale. De plus, la largeur de la bande d'ondes indiquait le temps de respiration maintenu. Ces résultats suggèrent que le capteur de pression avec une sensibilité et une supériorité élevées a un grand potentiel dans les applications d'appareils de santé portables.
Conclusion
Dans ce travail, les AgNWs ont été fabriqués par méthode hydrothermale, et la morphologie a été caractérisée et analysée. Un capteur de pression entièrement textile a été fabriqué en insérant une entretoise en maille de coton entre les cotons enduits d'AgNW à double couche. Grâce à l'effet collectif des contacts multi-échelles fibre/fil/tissu, le capteur a une sensibilité extrêmement élevée (3,24 × 10 5 kPa −1 à 0–10 kPa et 2,16 × 10 4 kPa −1 à 10-100 kPa, respectivement), un temps de réponse/récupération rapide (32/24 ms), une stabilité élevée (1000 cycles) et une large plage de pression (0-100 kPa). La surveillance des signaux physiologiques tels que la pression pulsée a été démontrée avec succès. Avec une méthode de fabrication simple et efficace, un tel capteur de pression ultrasensible favorisera une large application dans le développement de prochaine génération de vêtements intelligents, de surveillance d'activité et d'appareils de santé.
Disponibilité des données et des matériaux
Les auteurs déclarent que les matériaux et les données sont à la disposition des lecteurs, et toutes les conclusions tirées dans ce manuscrit sont basées sur les données qui sont toutes présentées et montrées dans cet article.
Abréviations
- CNT :
-
Nanotubes de carbone
- AgNW :
-
Nanofil d'Ag
- PVP :
-
polyvinylpyrrolidone
- Ex. :
-
Éthylène glycol
- NaCl :
-
Chlorure de sodium
- DI :
-
Eau déminéralisée
- SEM :
-
Microscope électronique à balayage
- EDS :
-
Spectroscopie à rayons X à dispersion d'énergie
Nanomatériaux
- Capteur de gaz portable pour la surveillance de la santé et de l'environnement
- Q&R :Fabrication ultra-rapide de capteurs portables
- De minuscules capteurs quantiques observent la transformation des matériaux sous pression
- La percée du capteur de pression souple résout les goulots d'étranglement les plus difficiles dans les domaines
- Capteur à base de graphite pour dispositifs médicaux portables
- Les capteurs portables détectent les fuites de gaz
- Ce gant Touchy-Feely détecte et cartographie les stimuli tactiles
- Un appareil alimente des capteurs portables grâce au mouvement humain
- Le nouveau patch cutané nous rapproche du moniteur de santé portable tout-en-un