Les modules OptiPath et Force de CGTech se révèlent complémentaires
Il y a trois ans, le développeur de logiciels Vericut CGTech s'est entretenu avec les programmeurs Don Lahr et Mike Triplett de l'atelier de travail aérospatial et médical Ultra Machining Company (UMC) au sujet de leur utilisation du module d'usinage basé sur les connaissances OptiPath de Vericut. Les hommes avaient récemment installé une mise à jour qui comprenait une personnalisation qu'ils avaient demandé à CGTech de faire en leur nom.
La demande d'amélioration - Vericut SCR #16986 - a simplifié les changements de vitesse d'alimentation grâce à des macro-variables accessibles à l'opérateur, a simplifié les configurations et a éliminé le besoin d'impliquer le bureau de programmation pour un simple ajustement de variable.
Lahr et Triplett sont toujours chez UMC aujourd'hui, tout comme Cory Mahn, un employé de 12 ans qui a rejoint le service de programmation peu de temps après la mise à jour de la personnalisation. À cette époque, il y avait eu des discussions sur le nouveau module Force de CGTech, un outil d'optimisation de trajectoire d'outil basé sur la physique censé réduire les temps de cycle de 25 % ou plus, mais UMC n'avait pas de plans imminents pour sa mise en œuvre.
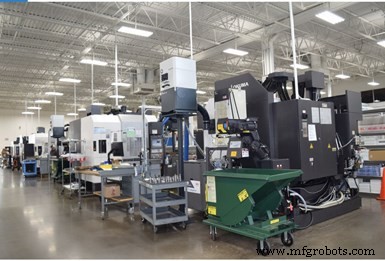
UMC, un atelier d'emplois aérospatiaux et médicaux à Monticello, Minnesota, abrite des dizaines de machines-outils CNC modernes. L'entreprise utilise Vericut de CGTech depuis plus de 15 ans.
Ces plans ont changé en février 2020, alors que l'entreprise a entrepris son premier test Force sur un travail assez long. "Nous avons réduit d'environ 10 % le temps de cycle sur ce numéro de pièce, ce qui a permis à l'entreprise d'économiser près de 13 000 $", déclare Lahr. Les résultats ont été suffisamment impressionnants pour que la haute direction accepte d'investir dans le logiciel. "Ce ne sont pas des économies aussi importantes que celles que nous avons réalisées depuis avec Force, mais cela a définitivement ouvert les yeux sur la valeur d'aller de l'avant."
La pièce en question est un composant médical en acier inoxydable 304L mesurant environ 2 × 3 × 0,5 pouce. Le plus grand outil UMC utilisé est une fraise en bout en carbure à quatre dents de 0,75 pouce, la plus petite de seulement 1/32 pouce, prenant des profondeurs de coupe axiales de 0,001 ou 0,002 pouce par passe. Lahr note que Force a fourni le plus d'avantages lors des opérations d'ébauche et de semi-finition, mais il ajoute que même avec de très petits outils tels que ceux décrits ci-dessus, cela a aidé à optimiser les trajectoires d'outils au point que la rupture de la fraise est tombée à zéro alors que le temps de cycle s'est souvent amélioré. . "Il y a aussi certainement un avantage pour la durée de vie de l'outil", ajoute-t-il.
Mises à jour du site et poussée d'automatisation
Les changements récents chez UMC ont également influencé la décision de l'entreprise de commencer à utiliser Force. L'entreprise en est encore à sa deuxième génération d'entreprise familiale, mais le nombre d'employés a doublé pour atteindre près de 200 personnes. Le nombre de machines-outils à commande numérique a également augmenté. Il existe maintenant une poignée de centres d'usinage verticaux à cinq axes Okuma M460V-5AX, une paire de centres d'usinage verticaux à quatre axes MB-46VAE d'Okuma et trois centres d'usinage à cinq axes Matsuura MX-520 - deux avec des piscines de palettes à quatre stations. /P>
En raison de la pénurie de main-d'œuvre qualifiée, UMC et d'autres ateliers de travail constatent que l'entretien automatisé des machines devient de plus en plus important d'année en année.
Malgré l'augmentation des effectifs, l'automatisation des ateliers est en hausse. "Il est difficile de trouver des travailleurs qualifiés, nous avons donc ajouté des robots à certains de nos tours et fraiseuses", explique Mahn. "Cela offre la possibilité de fonctionner avec peu de surveillance ou même sans surveillance dans certains cas, même si la taille de nos lots est assez petite. Nous avons également amélioré notre serrage sur certaines machines et effectuons le préréglage d'outils hors ligne. »
Comparaison d'OptiPath et de Force
Au moment d'écrire ces lignes, la société a optimisé 20 références différentes avec Force. Jusqu'à présent, les améliorations du temps de cycle ont varié de 3 à 28 %, mais Lahr s'empresse de souligner qu'UMC récupérera son investissement trois ou quatre fois au cours de la première année.
Ceux qui connaissent l'optimisation des trajectoires d'outils se demandent peut-être :si UMC utilisait déjà OptiPath, pourquoi investirait-il dans Force ? Après tout, les deux produits promettent des temps de cycle plus courts et une durée de vie de l'outil améliorée, et résolvent tous les deux les problèmes de déviation de la fraise, de broutage dans les coins et d'événements d'usinage indésirables similaires. Cela signifie-t-il que l'investissement d'UMC dans OptiPath était un gaspillage d'argent ? Pas du tout, explique Gene Granata, chef de produit chez CGTech pour Vericut.
"Force et OptiPath sont des produits différents qui utilisent des approches d'optimisation différentes, mais chacun se complète", déclare-t-il. « OptiPath, par exemple, ne mesure pas les forces de coupe. Au lieu de cela, il utilise soit une méthode volumétrique d'optimisation, soit une méthode qui mesure l'épaisseur des copeaux. La force mesure également l'épaisseur des copeaux, mais dispose de contrôles et d'équilibrages supplémentaires, notamment la surveillance des forces de coupe ou de la puissance de la broche, et prédit la déviation de l'outil. Dans les deux cas, l'enlèvement de matière est maintenu constant en ajustant la vitesse d'avance et en subdivisant les mouvements de la trajectoire d'outil selon les besoins afin de maintenir des conditions d'usinage quasi idéales pour chaque outil."
Différents outils pour différentes situations
En fin de compte, les deux logiciels ont leurs propres cas d'utilisation optimaux. Granata suggère d'utiliser Force dans les matériaux durs et difficiles à usiner, où de légers pics instantanés de charges d'outils peuvent entraîner de gros problèmes avec les fraises et les broches de la machine. D'autre part, il recommande OptiPath pour les métaux mous comme l'aluminium, l'acier doux et la fonte grise où l'objectif principal est de nettoyer le matériau aussi rapidement que possible (plutôt que de maintenir une charge de copeaux constante), ou pour les situations dans lesquelles la coupe de l'outil les conditions ne s'approchent jamais des niveaux dangereux de force de coupe ou de puissance de la broche.
Selon Granata, de nombreux clients OptiPath continuent d'utiliser leurs stratégies OptiPath éprouvées lorsqu'ils commencent à utiliser l'optimisation Force, en particulier avec des matériaux plus durs ou difficiles à usiner, et utilisent OptiPath lors de la découpe avec certains outils qui favorisent cette méthode d'optimisation. Cela dit, il souligne qu'il n'y a pas d'approche unique en matière de programmation.
"Cela dépend des stratégies que les utilisateurs préfèrent", dit-il. "Si vous êtes un utilisateur avancé d'OptiPath, vous seriez probablement plus enclin à ajouter l'optimisation Force à votre licence OptiPath et à invoquer les deux. Vous pouvez alors choisir, sur une base outil par outil, à utiliser. Les programmeurs peuvent même changer de stratégie au cours d'un parcours d'outil pour obtenir l'optimisation la plus efficace. Les deux sont complémentaires pour offrir le plus de stratégies d'optimisation possible."
Les expériences de l'équipe de programmation d'UMC semblent étayer cette théorie. Mahn note que Force a encore réduit le temps de cycle de 5 à 6 % en moyenne sur les tâches que l'équipe exécutait auparavant via OptiPath. Comme avantage secondaire, Mahn et Lahr ont également découvert que Force réduisait leur temps de programmation global. "Avec Force, nous n'avons pas besoin d'être aussi précis avec la création de trajectoires d'outils dans notre logiciel de FAO", déclare Lahr. "Peut-être que le plus gros ajustement pour moi a été de laisser Force faire son travail. Cela suggérera souvent une vitesse d'alimentation qui est au moins le double de celle que j'aurais utilisée, mais si vous la laissez aller, Force le fait bien. »
Équipement industriel
- Rutronik :SoC et modules sans fil multiprotocoles de Redpine Signals
- Timken va acquérir les roulements QM et la transmission de puissance
- Fabrication additive avec des composites dans l'aérospatiale et la défense
- Success Story :ROI rapide et croissance de l'entreprise
- Trois étapes pour gérer le risque fournisseur et la force majeure
- Top 5 des caractéristiques distinctives d'une équipe experte et leader de fabricants de moules
- Tour d'outillage
- Tour CNC
- Une société de télécommunications et de services Internet, WBL Services, déploie Fluke Connect®