Quelque chose que vous ne savez pas sur le moulage sous pression
Le moulage sous pression est un processus de moulage de métal , dont la caractéristique est d'appliquer une pression élevée au métal en fusion en utilisant une cavité de moule. Et les moules sont généralement usinés à partir d'alliages plus résistants. Le processus est similaire au moulage par injection. Pour permettre aux gens d'avoir une compréhension globale du moulage sous pression, la société JTR a organisé et résumé ce qu'est le moulage sous pression ? Quel est le processus de moulage sous pression? Quels sont les matériaux du moulage sous pression? Et d'autres questions, j'espère que vous pouvez avoir une compréhension complète de "moulage sous pression ".
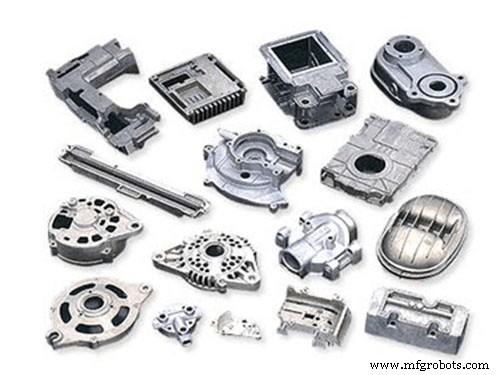
Définition de "Moulage sous pression"
Le moulage sous pression est une technique de moulage de précision qui utilise une contrainte élevée pour exiger du métal fondu dans un moule métallique et une moisissure aux formes complexes. Les étalements réalisés par moulage sous pression sont appelés moulages sous pression.
La plupart des moulages sous pression sont sans fer, comme le zinc, le cuivre, l'aluminium, le magnésium, le plomb, l'étain et les alliages plomb-étain ainsi que leurs alliages. Selon le type de moulage sous pression, un appareil de moulage sous pression à chambre froide ou un appareil de moulage sous pression à chambre chaude est nécessaire.
La résistance à la traction de ces matériaux est presque le double de celle des alliages coulés ordinaires, ce qui a une signification plus positive pour les roues, cadres et autres pièces automobiles en alliage d'aluminium qui devraient être produits avec des matériaux plus résistants et résistants aux chocs.
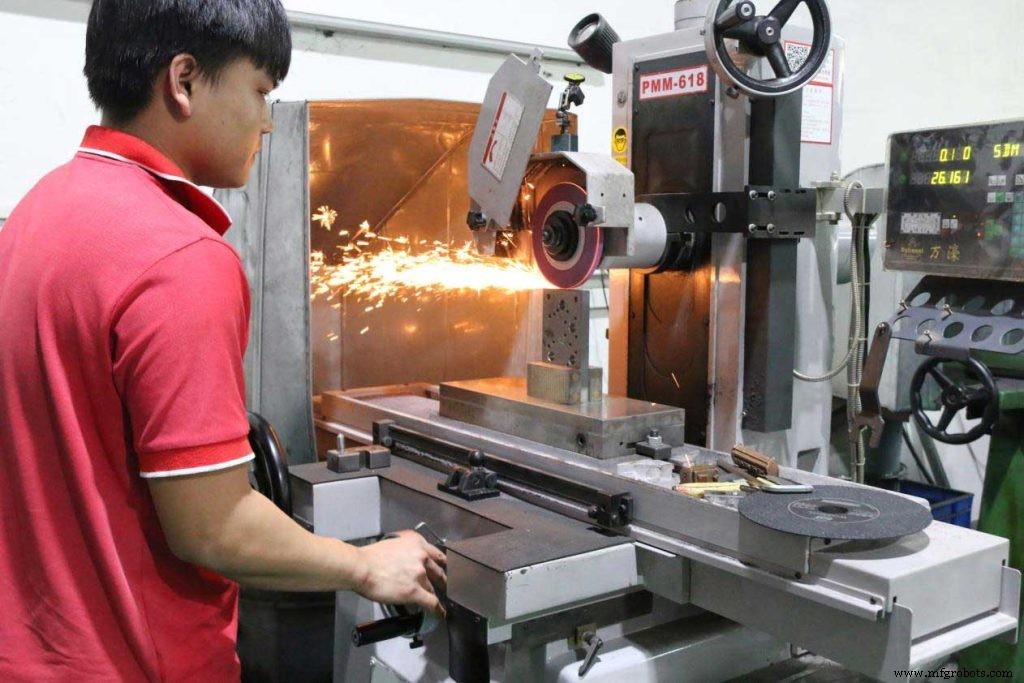
Processus de moulage sous pression
Le processus typique de moulage sous pression consiste principalement en 4 étapes, ou moulage sous pression à haute pression. Ces quatre étapes, y compris le travail de préparation du moule, le remplissage du matériau, l'injection et le décochage, sont également à la base de divers processus de moulage sous pression personnalisés.
Le lubrifiant est pulvérisé dans la cavité du moule tout au long de la procédure de préparation. En plus d'aider à gérer le niveau de température du moule, le lubrifiant peut également aider à la libération de la coulée. Le moule peut alors être fermé, ainsi que le métal en fusion infusé dans le moule à haute pression, qui varie de 10 à 175 MPa environ.
Une fois le métal en fusion rempli, la pression est maintenue jusqu'à ce que la coulée se solidifie. Le poteau de presse après cela pousse tous les moulages, et aussi, parce qu'il peut y avoir plusieurs cavités dans un moule, il peut y avoir plusieurs moulages par moulage.
Le processus de chute du sable nécessite la séparation des résidus, y compris les ouvertures de moules, les canaux, les portes et les bavures. Le processus est généralement effectué en pressant le moulage à travers une matrice de garniture spéciale. D'autres façons de faire tomber du sable comprennent le sciage et le ponçage. Si la porte est fragile, vous pouvez battre le casting directement, ce qui peut économiser des ressources humaines. L'excédent de matrice de coulée peut être réutilisé après la fusion.
L'injection à haute pression permet un remplissage très rapide du moule, de sorte que l'ensemble du moule peut être rempli de métal en fusion avant qu'une pièce ne se solidifie. De cette manière, même les pièces à parois minces difficiles à remplir peuvent être suffisamment remplies et les discontinuités de surface de la pièce moulée sous pression peuvent être évitées.
Cependant, cela provoque en outre un emprisonnement d'air, car il est difficile pour l'air de s'échapper lors du remplissage rapide du moule. Placer des évents sur la ligne de séparation peut réduire ce problème, mais des processus vraiment précis peuvent également laisser de la porosité dans le centre de coulée. Une fois que la plupart des pièces sont moulées sous pression, elles peuvent être traitées par le service de finition de surface pour compléter certaines structures qui ne peuvent pas être complétées par moulage, comme le perçage et le polissage.
Les défauts peuvent être inspectés une fois le décochage terminé. Les défauts les plus courants sont la stagnation (remplissage insuffisant de la solution). Ces défauts peuvent être provoqués par un niveau de température inadéquat du moule ou du métal en fusion, une contamination par le métal, ainsi que peu d'évents, un excès de lubrifiant, etc. Les marques d'écoulement sont des marques laissées sur la surface de coulée par des défauts de porte, des angles vifs ou un excès de substance lubrifiante.
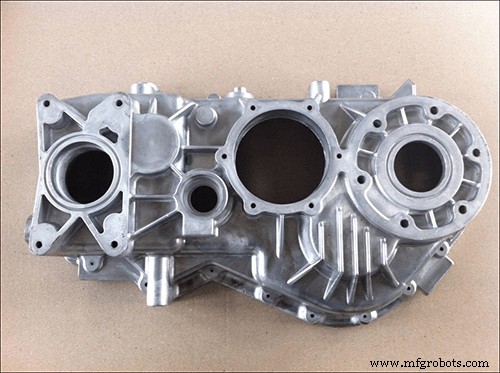
Métal pour moulage sous pression
Les métaux utilisés dans le moulage sous pression comprennent principalement le zinc, le cuivre, l'aluminium, le magnésium, le plomb, l'étain et les alliages plomb-étain, bien que le moulage sous pression soit rare mais viable. Des aciers de coulée sous pression beaucoup plus uniques sont constitués de ZAMAK, d'alliages aluminium-zinc, ainsi que des normes de l'American Aluminium Association :AA380, AA384, AA386, AA390, ainsi que du magnésium AZ91D. Les caractéristiques du moulage sous pression de nombreux métaux sont conformes à :
Zinc : Le métal le plus facile à mouler sous pression, rentable pour fabriquer de petits composants, facile à revêtir, haute résistance à la compression, plasticité et durée de vie durable.
Aluminium :Légèreté, stabilité dimensionnelle élevée lors de la fabrication de pièces moulées complexes et à parois minces, forte résistance à la corrosion, bonnes propriétés mécaniques, conductivité thermique et électrique élevée et haute résistance à haute température
Magnésium : Facile à usiner, rapport résistance/poids élevé, le plus léger parmi les métaux moulés sous pression couramment utilisés
Cuivre :Dureté élevée, forte résistance à la corrosion, meilleures propriétés mécaniques des métaux de moulage sous pression couramment utilisés, résistance à l'usure et résistance proche de l'acier.
Plomb et étain : Une densité élevée et une précision dimensionnelle extrêmement élevée peuvent être utilisées comme composants spéciaux de protection contre la corrosion. Pour des raisons de santé publique, cet alliage ne peut pas être utilisé dans les équipements de transformation et de stockage des aliments. Les alliages de plomb, d'étain et d'antimoine (parfois avec un peu de cuivre) peuvent faire du lettrage à la main dans l'impression typographique et le bronzage.
Métal | Section transversale minimale | Angle de dépouille minimal |
Alliage d'aluminium | 0,89 mm (0,035 pouce) | 1:100 (0,6 °) |
Laiton et bronze | 1,27 mm (0,050 pouce) | 1:80 (0,7°) |
Alliage de magnésium | 1,27 mm (0,050 pouce) | 1:100 (0,6 °) |
Alliage de zinc | 0,63 mm (0,025 pouce) | 1:200 (0,3°) |
Les limites de masse supérieures pour le moulage sous pression avec de l'aluminium, du cuivre, du magnésium et du zinc sont respectivement de 70 lb (32 kg), 10 lb (4,5 kg), 44 lb (20 kg) et 75 lb (34 kg).
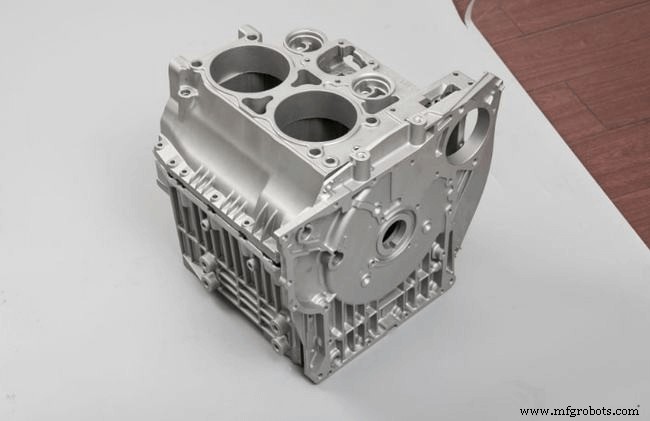
Avantages et inconvénients du moulage sous pression
Avantages du moulage sous pression
Les avantages du moulage sous pression incluent que les pièces moulées peuvent avoir une excellente précision dimensionnelle.
Habituellement, cela dépend du matériau de coulée. Par rapport à d'autres procédés de moulage, le moulage sous pression produit des pièces avec des surfaces lisses et un rayon de congé d'environ 1 à 2,5 microns. Le moulage sous pression peut produire des pièces avec des épaisseurs de paroi d'environ 0,75 mm, par rapport à un flacon ou à des moulages en moule permanent. Il peut couler directement des pièces de structures internes, telles que des gaines de fil, des éléments chauffants, des surfaces d'appui à haute résistance. Les autres avantages incluent la réduction ou l'évitement de l'usinage secondaire des pièces, la vitesse de production des pièces moulées, la résistance à la traction des pièces moulées (résistance jusqu'à 415 MPa) et la capacité de couler des métaux à haut débit.
Inconvénients du moulage sous pression
Le plus gros inconvénient du moulage sous pression est son coût élevé. Le prix des équipements de moulage sous pression (machines de moulage sous pression) et des moules et composants liés aux moules est relativement élevé par rapport aux autres méthodes de moulage. Par conséquent, la fabrication par moulage sous pression n'a une valeur économique élevée que lors de la production de pièces en série.
Parmi les autres inconvénients, citons:le procédé de moulage sous pression ne convient qu'aux métaux relativement fluides et la masse de coulée doit être comprise entre 30 grammes et 10 kilogrammes. Il y aura toujours des vides dans le dernier lot de pièces moulées dans le moulage sous pression normal. Par conséquent, aucun traitement thermique ou soudage ne peut être effectué car le gaz dans l'entrefer va se dilater sous l'action de la chaleur, provoquant des micro-défauts internes et un décollement de la surface.
Moulage sous pression à chambre chaude et moulage sous pression à chambre froide
Il existe deux manières différentes de fabriquer des pièces en moulage sous pression :moulage sous pression en chambre chaude et moulage sous pression en chambre froide . Dans les deux processus de fabrication, les moules sont pulvérisés avec un agent de démoulage avant le processus de coulée pour garantir que les pièces coulées par la suite peuvent être facilement retirées des moules. Cependant, la masse fondue n'est pas versée directement dans la cavité du moule mais d'abord versée dans la cavité de coulée de la machine de coulée sous pression. De là, l'alliage est pressé dans le moule par un piston (appelé groupe de coulée) à travers un ou plusieurs canaux. La différence entre les deux processus est la structure de la chambre de coulée, comme décrit ci-dessous.
Moulage sous pression en chambre chaude
Dans le moulage sous pression à chambre chaude, son bain de métal est un état fondu de métal liquide semi-liquide qui remplit le moule sous pression. Les avantages de ce système comprennent une vitesse de cycle élevée (environ 15 cycles par minute), une facilité d'automatisation et une facilité de fusion du métal. Les inconvénients comprennent l'incapacité de couler sous pression des métaux avec des points de fusion plus élevés et l'incapacité de couler sous pression de l'aluminium, ce qui entraînerait le fer hors du bain en fusion. Ainsi, les machines de coulée sous pression à chambre chaude sont généralement utilisées pour les alliages de zinc, d'étain et de plomb. De plus, le moulage en matrice à chambre chaude est difficile à utiliser pour le moulage sous pression de grandes pièces moulées, qui sont généralement le moulage sous pression de petites pièces moulées.
Moulage sous pression en chambre froide
Le moulage sous pression à chambre froide peut être utilisé lors du moulage sous pression de métaux qui ne peuvent pas être utilisés dans le processus de moulage sous pression à chambre chaude, notamment les alliages d'aluminium, de magnésium, de cuivre et de zinc à teneur plus élevée en aluminium. Le métal doit d'abord être fondu dans un creuset séparé dans ce processus. Une quantité de métal en fusion est ensuite transférée dans une chambre ou buse d'injection non chauffée. Ces métaux sont injectés dans le moule par pression hydraulique ou mécanique.
Le plus gros inconvénient de ce procédé est le long temps de cycle dû à la nécessité de transférer le métal en fusion dans la chambre froide. Les machines de moulage sous pression à chambre froide sont également divisées en types verticaux et horizontaux. Les machines de moulage sous pression verticales sont généralement de petites machines, tandis que les machines de moulage sous pression horizontales ont différents modèles.
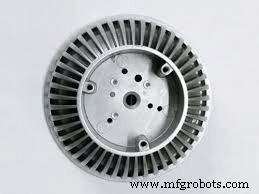
Domaines d'application du moulage sous pression
Le moulage sous pression est principalement utilisé pour la production de masse, c'est-à-dire pour couler de nombreuses pièces du même type. Une qualité de moulage élevée est obtenue malgré la haute pression utilisée dans le processus de fabrication. Le procédé de moulage sous pression est particulièrement adapté à la production de pièces très fines (jusqu'à 1 mm) (légères).
Le plus souvent, les composants moulés sous pression tels que les roues, les blocs-cylindres, les culasses, les corps de soupapes et les collecteurs sont fabriqués pour l'industrie automobile. De plus, d'autres industries utilisent le moulage sous pression :
- Aéronautique
- Appareils électroménagers
- Meubles
- Outils électriques
- Produits électroniques
- Mécanique
- Technologie d'éclairage
À l'avenir, les fonderies s'intéresseront à d'autres industries telles que les véhicules électriques. Cela offre un grand potentiel pour les pièces moulées en métal léger.
Choisissez une entreprise de moulage sous pression de confiance
Le moulage sous pression est largement utilisé dans la fabrication depuis le 19ème siècle. En tant que principal fournisseur de services de moulage sous pression en Chine, JTR fournit à ses clients des solutions complètes de moulage sous pression depuis de nombreuses années. Un service de moulage sous pression de haute qualité est la clé de notre rentabilité. Donc, si vous avez besoin de mettre en œuvre votre conception, vous pouvez nous contacter. Vous avez juste besoin de compléter la conception ou la créativité, et nous ferons le reste.
Technologie industrielle
- 6 choses que vous ne saviez pas sur l'impression 3D
- 5 faits amusants sur le moulage sous pression
- Ce que vous devez savoir sur la certification CMMC
- Tout ce que vous devez savoir sur le moulage des métaux
- Tout ce que vous devez savoir sur le condensateur MFD
- Ce que vous devez savoir sur le moulage de métal
- 5 choses que vous ne saviez pas sur le titane
- Tout ce que vous devez savoir sur le travail des métaux
- Tout ce que vous devez savoir sur le contreplaqué