Guide rapide pour sceller FDM avec Insight
Vous souhaitez donc qualifier ce nouveau design de produit qui retient le liquide mais redoutez le post-traitement requis ? Restez calme et perspicace.
Il semble y avoir une quantité infinie d'applications à mesure que la technologie de fabrication additive (AM) évolue. Néanmoins, ceux qui se tournent vers la FA pour le prototypage fonctionnel et les pièces d'utilisation finale continuent de faire le travail avec un cheval de bataille de 25 ans - la technologie de modélisation par dépôt de fusion (FDM). Un énorme 85% du marché est basé sur FDM et ce n'est pas une surprise. Il produit des pièces précises et fonctionnelles dans un large éventail de plastiques de production d'ingénierie.
Outre tous ses avantages, le FDM est également intrinsèquement poreux. Pour de nombreuses applications, cela n'entre pas du tout en jeu. Si vous faites du thermoformage, vous accepteriez ce défaut. Cependant, si vous essayez de retenir un gaz ou un liquide (à l'intérieur ou à l'extérieur), il s'agit d'une limitation flagrante. Ainsi, lorsque la porosité est un problème, commencer par le logiciel de traitement Insight est le meilleur moyen de garantir le succès de votre application.
La géométrie aura un impact considérable sur la technique ou les combinaisons de techniques nécessaires pour sceller la pièce à tester, puis l'utilisation finale. L'utilisation du logiciel Insight de Stratasys, inclus avec la gamme Fortus de Stratasys, est un moyen simple de résoudre les problèmes de porosité sur la plupart des géométries ; à l'inverse, certaines géométries complexes peuvent potentiellement nécessiter un post-traitement à forte intensité de main-d'œuvre. Donc, si vous êtes du genre frugal, vous devez vous efforcer de traiter les STL dès le départ avec un poing Ultem pour vous assurer que ces opérations manuelles ne sont pas nécessaires. Et devine quoi? Contrairement à la plupart des méthodes de post-traitement, cette stratégie ne modifiera pas la géométrie de la pièce.
Si vous connaissez déjà FDM, vous savez peut-être pourquoi la porosité est souvent nécessaire. Sinon, voici pourquoi :le modèle peut avoir des zones qui ne sont pas autoportantes, les supports doivent donc être retirés et dissous. La porosité naturelle permet à la solution soluble d'atteindre le matériau de support ainsi que de s'écouler de ces mêmes zones qui peuvent être cachées. En d'autres termes, la lixiviation est parfois utile. Gardez cela à l'esprit.
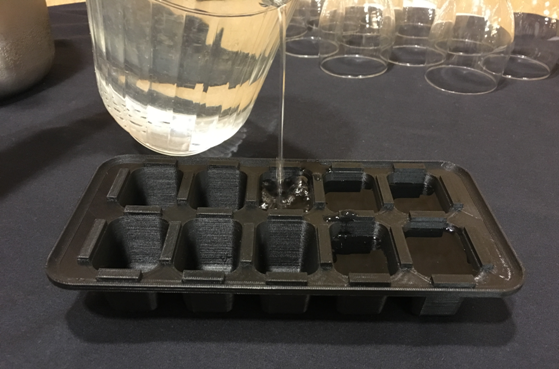
Sceller avec Insight
Avec Insight, vous avez la possibilité de contrôler voire d'éliminer le problème de porosité, en particulier avec des géométries simples. Cela est vrai tant que les exigences de l'application sont de maintenir un gaz ou un liquide autour des pressions atmosphériques. Il ne sera pas aussi efficace à des pressions/vide plus élevés, ou avec des géométries de pièces complexes.
La première étape concerne l'orientation de la construction sur la plate-forme. Cela nécessitera votre jugement et les besoins de l'application. La règle la plus importante est d'orienter la pièce de manière à ce que la plupart des surfaces soient orientées verticalement.
Une fois que vous avez déterminé l'orientation optimale, l'étape suivante consiste à ajouter plusieurs contours aux murs verticaux (image du bas). Fondamentalement, cette technique repose sur l'utilisation de contours supplémentaires et à son tour réduit ou élimine les rasters de ces couches. L'existence de trames au sein d'un modèle augmente le risque de fuite, en raison des entrefers qu'ils créent, comme indiqué ci-dessous (image du haut).
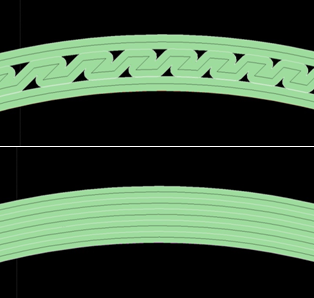
À partir de la barre d'outils Groupes, vous pouvez configurer les paramètres pour réduire les entrefers en suivant ces étapes :
- Déterminez l'épaisseur de votre paroi en mesurant à chaque couche, puis faites le calcul, de sorte que l'épaisseur de la paroi soit égale au nombre de contours multiplié par la largeur du contour. Vous pouvez sélectionner une gamme de couches qui ont les mêmes épaisseurs de paroi.
- Configurer des groupes personnalisés pour chaque épaisseur et ajoutez les couches aux groupes. Au sein de chaque groupe, vous pourrez contrôler le nombre de contours et leurs largeurs respectives.
- Sélectionnez les Lien Contours caractéristique et ajoutez un léger entrefer contour à contour négatif dans la mesure du possible. Cette fonctionnalité créera des parcours d'outils continus en éliminant les points de départ et d'arrêt entre chaque contour.
Dans cet exemple, affiché dans les paramètres d'un groupe personnalisé, j'ai une épaisseur de paroi de 0,100. J'ai utilisé cinq (5) contours avec une largeur de contour de 0,020. J'ai aussi le Link Contour case cochée et lui a donné un entrefer de -0,001. Alternativement, vous pouvez appliquer Largeur de contour et Lien Contours globalement si cela répond à vos besoins via la Configuration du parcours d'outil menu.
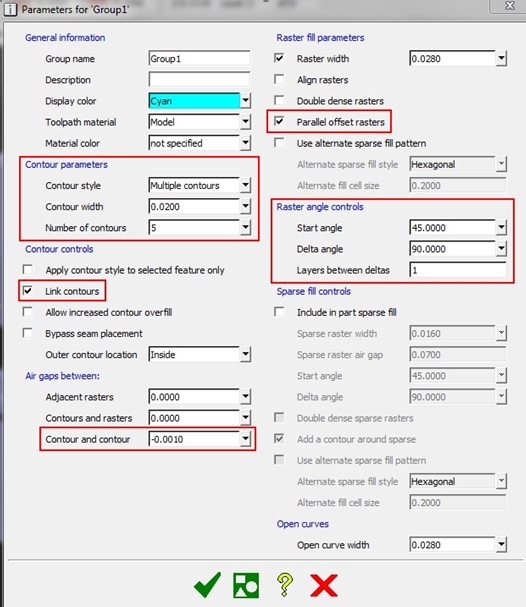
Remarque : La modification de certains de ces paramètres peut faire varier votre temps de fabrication et votre utilisation des matériaux. La meilleure pratique consiste à lancer un « drapeau vert » comme contrôle et à prendre note du temps et du matériel estimés avant de modifier les paramètres.
Ensuite, nous examinerons les rasters, car vous aurez probablement des zones qui en auront besoin. Par défaut, les contrôles d'angle raster sont définis pour commencer à 45° et alterner par delta de 90° (voir ci-dessus). Ces zones de retournement alternées laissent des chemins ou des trous d'air à travers les couches, c'est-à-dire les triangles noirs où les trames rencontrent les bords intérieurs des contours.
En sélectionnant Décalage parallèle Rasters, Insight modifiera trois paramètres.
- Varie le nombre de contours sur chaque couche afin de masquer les retournements de raster. Cela s'appliquera toujours même si vous avez déjà configuré plusieurs contours.
- Positionne les parcours d'outil raster parallèlement aux couches adjacentes (0° delta).
- Décale les parcours d'outils des rasters afin qu'ils recouvrent les jointures des couches précédentes.
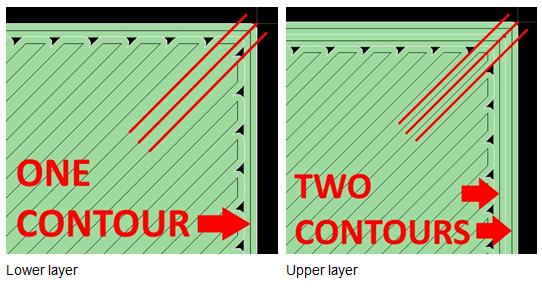
Alors ça scelle l'affaire. Cela devrait vous donner un excellent point de départ pour le traitement des STL en vue des applications d'étanchéité FDM.
Voici un article sur d'autres techniques de post-traitement qui feront passer le scellement au niveau supérieur. Mais soyez prudent, car ils affecteront votre géométrie.
Tags :Technologie FDM, Thermoformage, Ultem
impression en 3D
- Fraisage – Un guide rapide
- Java 8 - Guide rapide
- Guide rapide du parallélisme GD&T
- Un guide rapide de la presse à froid
- Un guide rapide de la boîte de vitesses planétaire
- Un guide rapide de la machine de presse servo
- Un guide rapide du dérouleur d'engrenages
- Un guide rapide de l'axe de tour CNC
- Un guide rapide des mandrins électriques